Page 577 of 3371
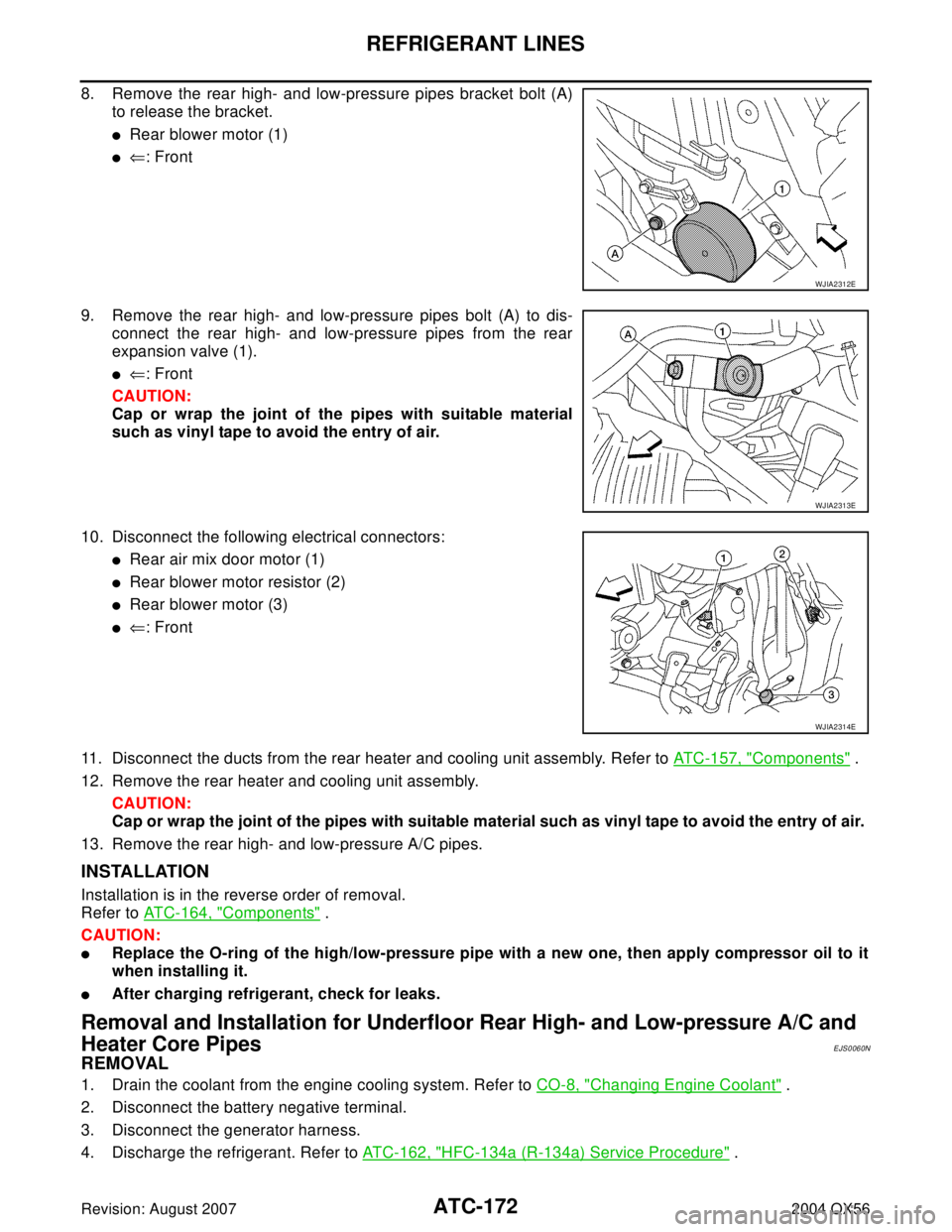
ATC-172
REFRIGERANT LINES
Revision: August 20072004 QX56
8. Remove the rear high- and low-pressure pipes bracket bolt (A)
to release the bracket.
Rear blower motor (1)
⇐: Front
9. Remove the rear high- and low-pressure pipes bolt (A) to dis-
connect the rear high- and low-pressure pipes from the rear
expansion valve (1).
⇐: Front
CAUTION:
Cap or wrap the joint of the pipes with suitable material
such as vinyl tape to avoid the entry of air.
10. Disconnect the following electrical connectors:
Rear air mix door motor (1)
Rear blower motor resistor (2)
Rear blower motor (3)
⇐: Front
11. Disconnect the ducts from the rear heater and cooling unit assembly. Refer to ATC-157, "
Components" .
12. Remove the rear heater and cooling unit assembly.
CAUTION:
Cap or wrap the joint of the pipes with suitable material such as vinyl tape to avoid the entry of air.
13. Remove the rear high- and low-pressure A/C pipes.
INSTALLATION
Installation is in the reverse order of removal.
Refer to ATC-164, "
Components" .
CAUTION:
Replace the O-ring of the high/low-pressure pipe with a new one, then apply compressor oil to it
when installing it.
After charging refrigerant, check for leaks.
Removal and Installation for Underfloor Rear High- and Low-pressure A/C and
Heater Core Pipes
EJS0060N
REMOVAL
1. Drain the coolant from the engine cooling system. Refer to CO-8, "Changing Engine Coolant" .
2. Disconnect the battery negative terminal.
3. Disconnect the generator harness.
4. Discharge the refrigerant. Refer to ATC-162, "
HFC-134a (R-134a) Service Procedure" .
WJIA2312E
WJIA2313E
WJIA2314E
Page 578 of 3371
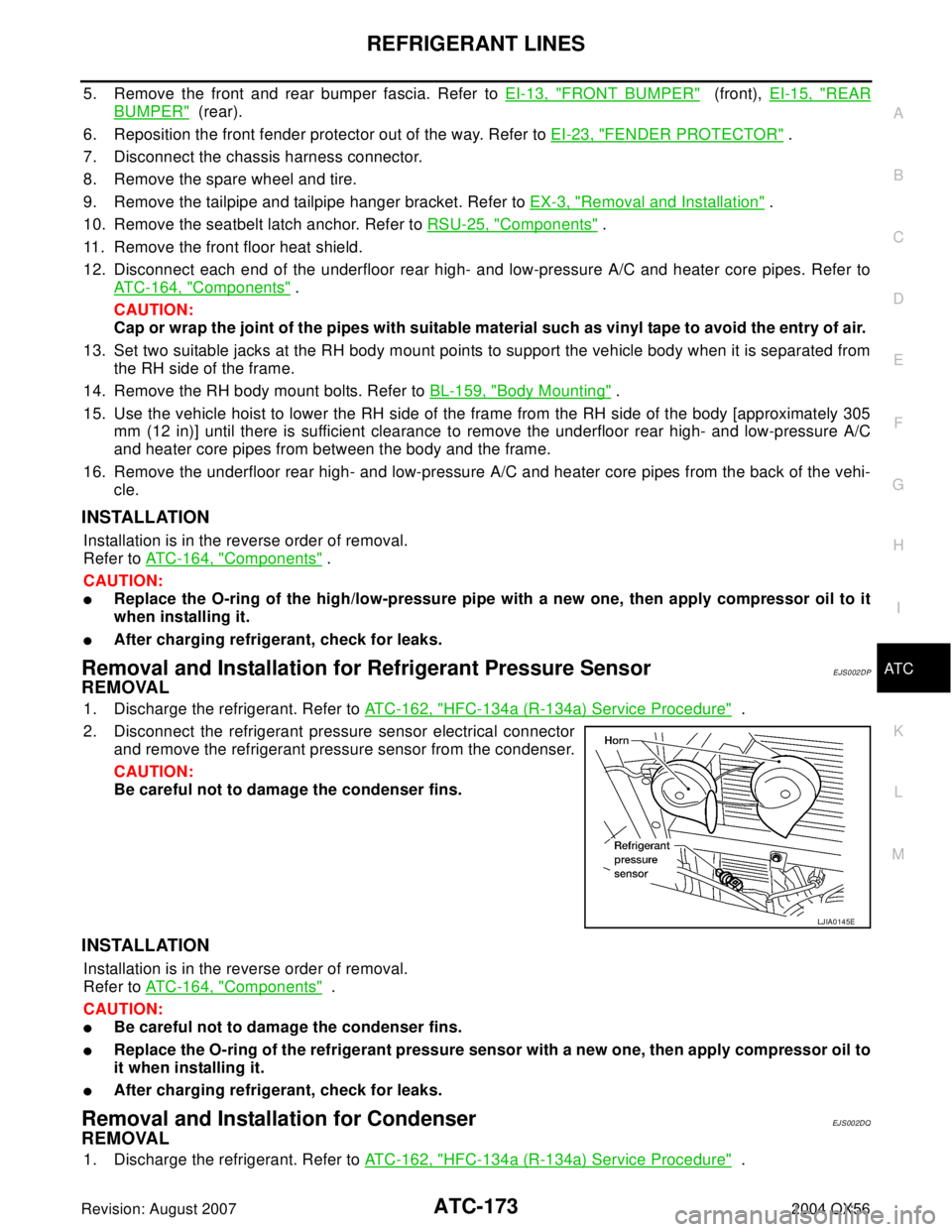
REFRIGERANT LINES
ATC-173
C
D
E
F
G
H
I
K
L
MA
B
AT C
Revision: August 20072004 QX56
5. Remove the front and rear bumper fascia. Refer to EI-13, "FRONT BUMPER" (front), EI-15, "REAR
BUMPER" (rear).
6. Reposition the front fender protector out of the way. Refer to EI-23, "
FENDER PROTECTOR" .
7. Disconnect the chassis harness connector.
8. Remove the spare wheel and tire.
9. Remove the tailpipe and tailpipe hanger bracket. Refer to EX-3, "
Removal and Installation" .
10. Remove the seatbelt latch anchor. Refer to RSU-25, "
Components" .
11. Remove the front floor heat shield.
12. Disconnect each end of the underfloor rear high- and low-pressure A/C and heater core pipes. Refer to
ATC-164, "
Components" .
CAUTION:
Cap or wrap the joint of the pipes with suitable material such as vinyl tape to avoid the entry of air.
13. Set two suitable jacks at the RH body mount points to support the vehicle body when it is separated from
the RH side of the frame.
14. Remove the RH body mount bolts. Refer to BL-159, "
Body Mounting" .
15. Use the vehicle hoist to lower the RH side of the frame from the RH side of the body [approximately 305
mm (12 in)] until there is sufficient clearance to remove the underfloor rear high- and low-pressure A/C
and heater core pipes from between the body and the frame.
16. Remove the underfloor rear high- and low-pressure A/C and heater core pipes from the back of the vehi-
cle.
INSTALLATION
Installation is in the reverse order of removal.
Refer to ATC-164, "
Components" .
CAUTION:
Replace the O-ring of the high/low-pressure pipe with a new one, then apply compressor oil to it
when installing it.
After charging refrigerant, check for leaks.
Removal and Installation for Refrigerant Pressure SensorEJS002DP
REMOVAL
1. Discharge the refrigerant. Refer to ATC-162, "HFC-134a (R-134a) Service Procedure" .
2. Disconnect the refrigerant pressure sensor electrical connector
and remove the refrigerant pressure sensor from the condenser.
CAUTION:
Be careful not to damage the condenser fins.
INSTALLATION
Installation is in the reverse order of removal.
Refer to ATC-164, "
Components" .
CAUTION:
Be careful not to damage the condenser fins.
Replace the O-ring of the refrigerant pressure sensor with a new one, then apply compressor oil to
it when installing it.
After charging refrigerant, check for leaks.
Removal and Installation for CondenserEJ S00 2DQ
REMOVAL
1. Discharge the refrigerant. Refer to ATC-162, "HFC-134a (R-134a) Service Procedure" .
LJIA0145E
Page 579 of 3371
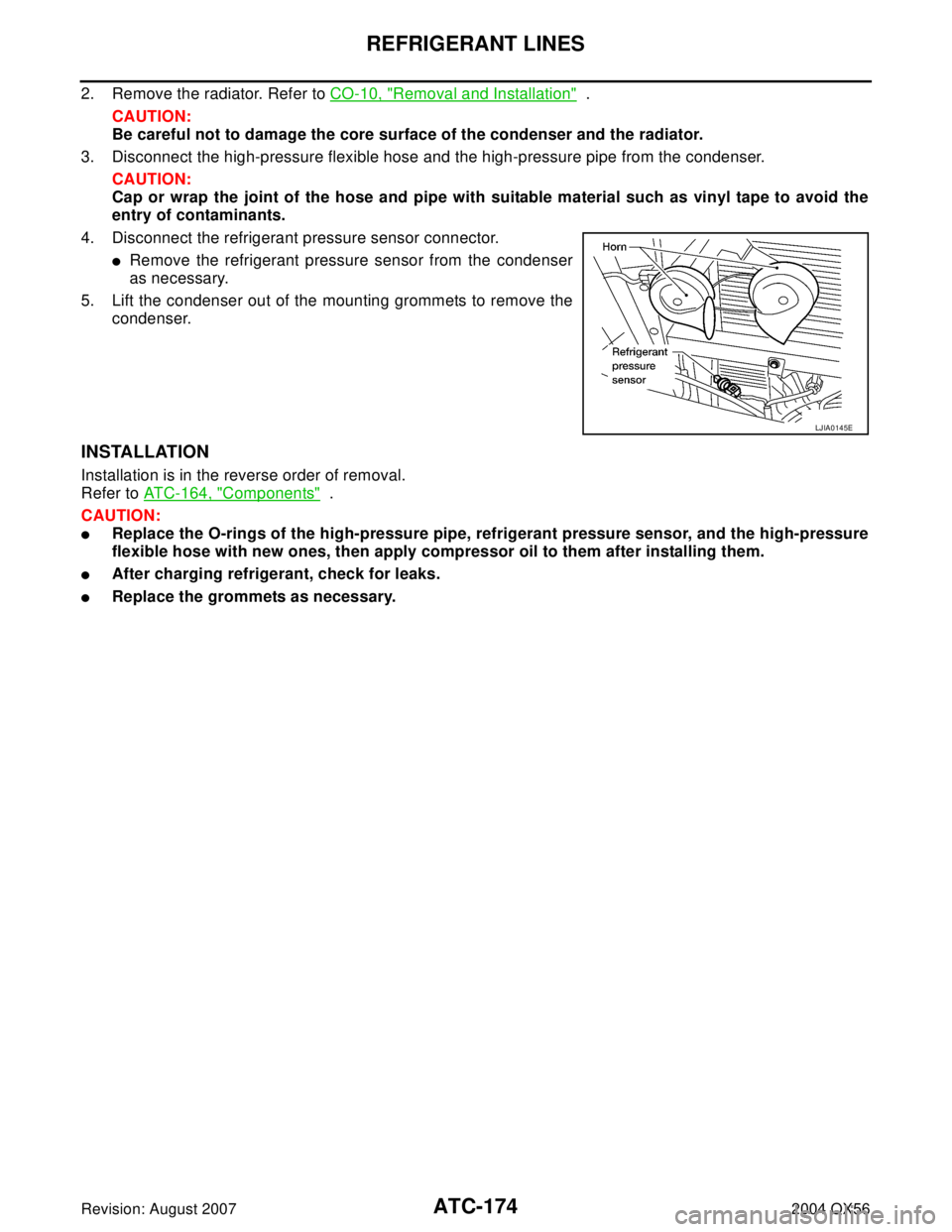
ATC-174
REFRIGERANT LINES
Revision: August 20072004 QX56
2. Remove the radiator. Refer to CO-10, "Removal and Installation" .
CAUTION:
Be careful not to damage the core surface of the condenser and the radiator.
3. Disconnect the high-pressure flexible hose and the high-pressure pipe from the condenser.
CAUTION:
Cap or wrap the joint of the hose and pipe with suitable material such as vinyl tape to avoid the
entry of contaminants.
4. Disconnect the refrigerant pressure sensor connector.
Remove the refrigerant pressure sensor from the condenser
as necessary.
5. Lift the condenser out of the mounting grommets to remove the
condenser.
INSTALLATION
Installation is in the reverse order of removal.
Refer to ATC-164, "
Components" .
CAUTION:
Replace the O-rings of the high-pressure pipe, refrigerant pressure sensor, and the high-pressure
flexible hose with new ones, then apply compressor oil to them after installing them.
After charging refrigerant, check for leaks.
Replace the grommets as necessary.
LJIA0145E
Page 580 of 3371
REFRIGERANT LINES
ATC-175
C
D
E
F
G
H
I
K
L
MA
B
AT C
Revision: August 20072004 QX56
Removal and Installation for Front EvaporatorEJS002DR
Front Heater and Cooling Unit Assembly
REMOVAL
1. Remove the front heater core. Refer to ATC-148, "FRONT HEATER CORE" .
LJIA0138E
1. Heater core cover 2. Heater core pipe bracket 3. Heater core
4. Upper bracket 5. Upper heater and cooling unit case 6. A/C evaporator
7. Lower heater and cooling unit case 8. Blower motor 9. Variable blower control
Page 581 of 3371
ATC-176
REFRIGERANT LINES
Revision: August 20072004 QX56
2. Remove the defroster mode door arm.
3. Separate the heater core and cooling unit case.
4. Remove the evaporator.
INSTALLATION
Installation is in the reverse order of removal.
CAUTION:
Replace the O-rings on the low-pressure flexible hose and the high-pressure pipe with new ones.
Apply compressor oil to the O-rings before installing them.
Removal and Installation for Rear EvaporatorEJS002DS
Rear Heater and Cooling Unit Assembly
LJIA0135E
1. Front cover 2. Evaporator and heater core case 3. Evaporator
4. Side cover 5. Heater core 6. Rear blower motor
7. Blower motor case 8. Rear blower motor resistor
Page 582 of 3371
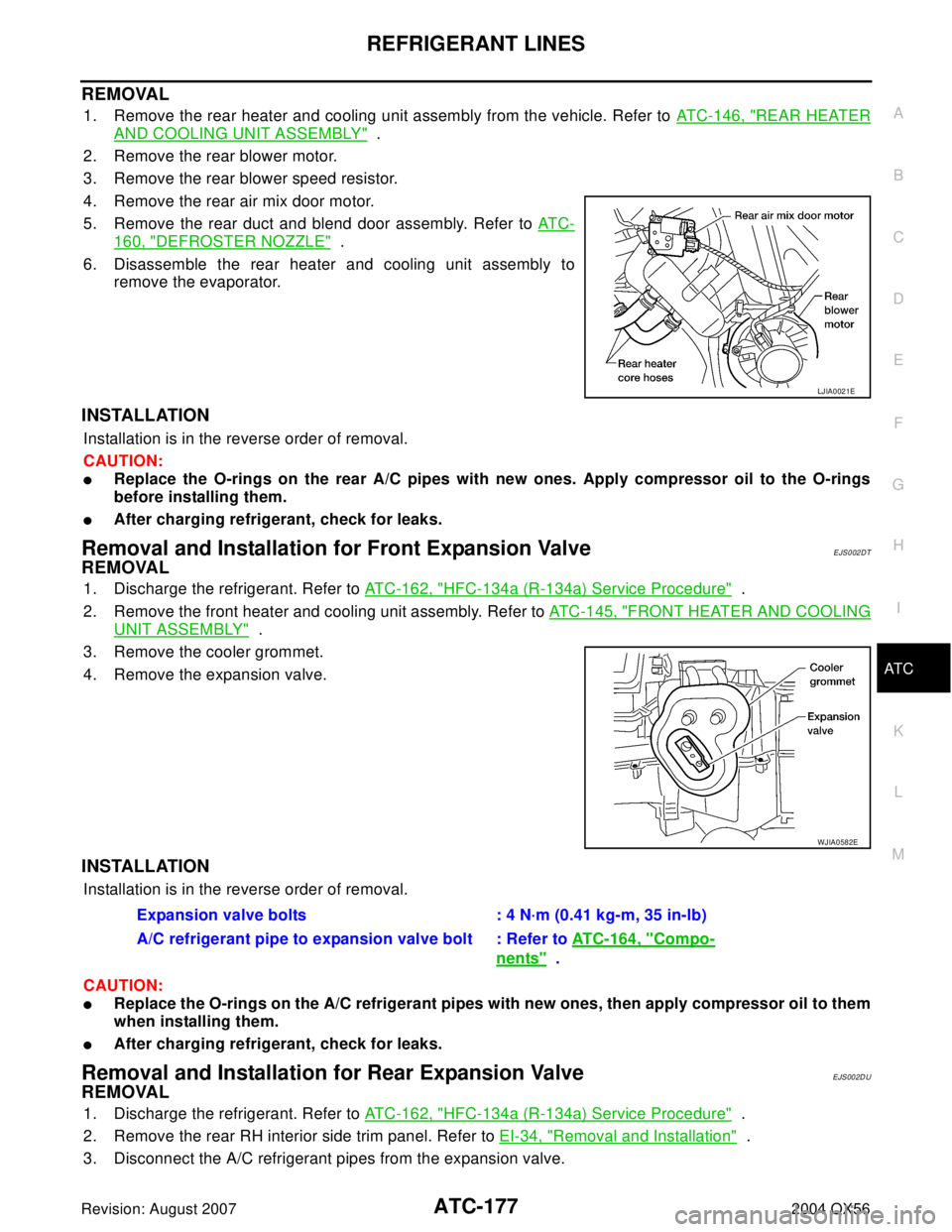
REFRIGERANT LINES
ATC-177
C
D
E
F
G
H
I
K
L
MA
B
AT C
Revision: August 20072004 QX56
REMOVAL
1. Remove the rear heater and cooling unit assembly from the vehicle. Refer to ATC-146, "REAR HEATER
AND COOLING UNIT ASSEMBLY" .
2. Remove the rear blower motor.
3. Remove the rear blower speed resistor.
4. Remove the rear air mix door motor.
5. Remove the rear duct and blend door assembly. Refer to AT C -
160, "DEFROSTER NOZZLE" .
6. Disassemble the rear heater and cooling unit assembly to
remove the evaporator.
INSTALLATION
Installation is in the reverse order of removal.
CAUTION:
Replace the O-rings on the rear A/C pipes with new ones. Apply compressor oil to the O-rings
before installing them.
After charging refrigerant, check for leaks.
Removal and Installation for Front Expansion ValveEJS002DT
REMOVAL
1. Discharge the refrigerant. Refer to ATC-162, "HFC-134a (R-134a) Service Procedure" .
2. Remove the front heater and cooling unit assembly. Refer to ATC-145, "
FRONT HEATER AND COOLING
UNIT ASSEMBLY" .
3. Remove the cooler grommet.
4. Remove the expansion valve.
INSTALLATION
Installation is in the reverse order of removal.
CAUTION:
Replace the O-rings on the A/C refrigerant pipes with new ones, then apply compressor oil to them
when installing them.
After charging refrigerant, check for leaks.
Removal and Installation for Rear Expansion ValveEJS002DU
REMOVAL
1. Discharge the refrigerant. Refer to ATC-162, "HFC-134a (R-134a) Service Procedure" .
2. Remove the rear RH interior side trim panel. Refer to EI-34, "
Removal and Installation" .
3. Disconnect the A/C refrigerant pipes from the expansion valve.
LJIA0021E
WJIA0582E
Expansion valve bolts : 4 N·m (0.41 kg-m, 35 in-lb)
A/C refrigerant pipe to expansion valve bolt : Refer to ATC-164, "
Compo-
nents" .
Page 583 of 3371
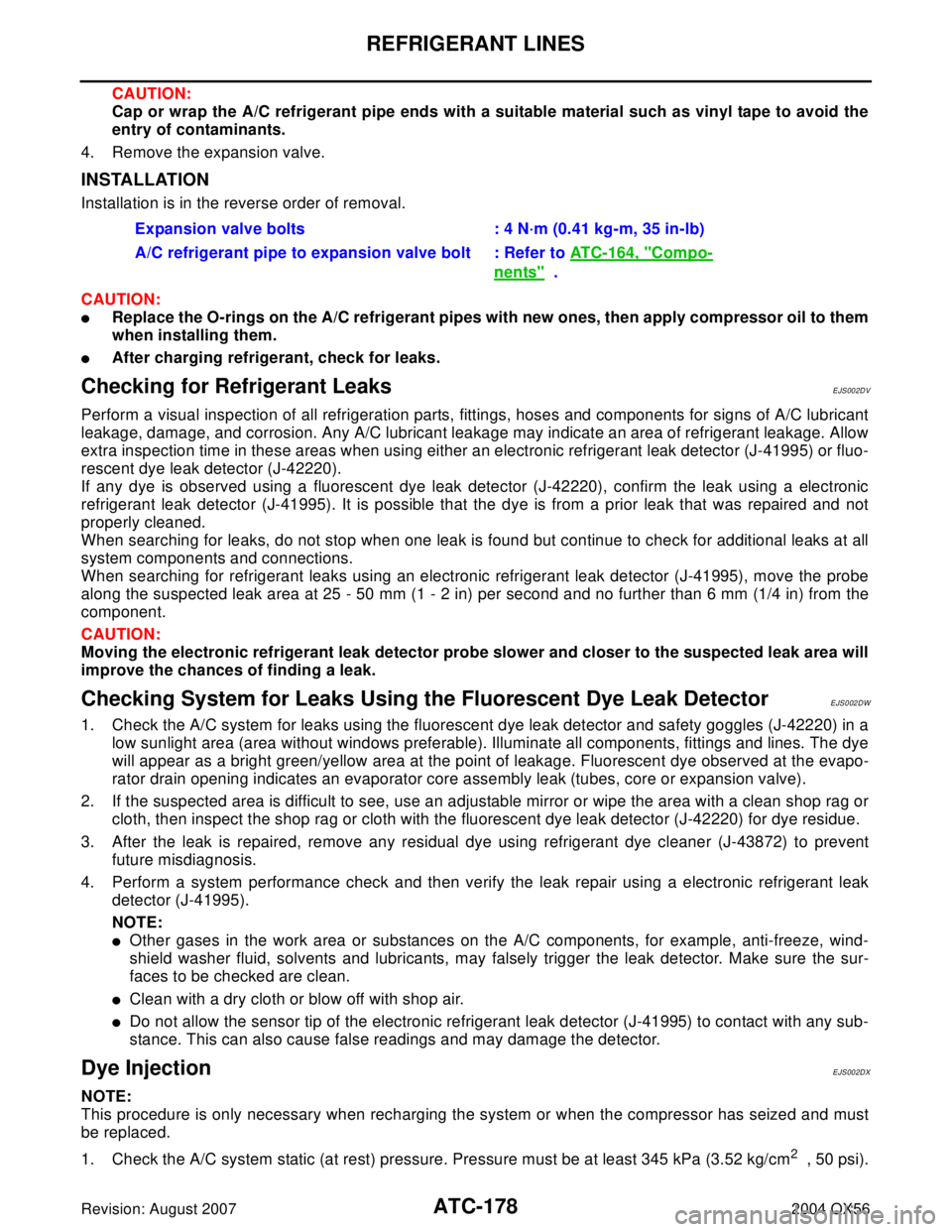
ATC-178
REFRIGERANT LINES
Revision: August 20072004 QX56
CAUTION:
Cap or wrap the A/C refrigerant pipe ends with a suitable material such as vinyl tape to avoid the
entry of contaminants.
4. Remove the expansion valve.
INSTALLATION
Installation is in the reverse order of removal.
CAUTION:
Replace the O-rings on the A/C refrigerant pipes with new ones, then apply compressor oil to them
when installing them.
After charging refrigerant, check for leaks.
Checking for Refrigerant LeaksEJS002DV
Perform a visual inspection of all refrigeration parts, fittings, hoses and components for signs of A/C lubricant
leakage, damage, and corrosion. Any A/C lubricant leakage may indicate an area of refrigerant leakage. Allow
extra inspection time in these areas when using either an electronic refrigerant leak detector (J-41995) or fluo-
rescent dye leak detector (J-42220).
If any dye is observed using a fluorescent dye leak detector (J-42220), confirm the leak using a electronic
refrigerant leak detector (J-41995). It is possible that the dye is from a prior leak that was repaired and not
properly cleaned.
When searching for leaks, do not stop when one leak is found but continue to check for additional leaks at all
system components and connections.
When searching for refrigerant leaks using an electronic refrigerant leak detector (J-41995), move the probe
along the suspected leak area at 25 - 50 mm (1 - 2 in) per second and no further than 6 mm (1/4 in) from the
component.
CAUTION:
Moving the electronic refrigerant leak detector probe slower and closer to the suspected leak area will
improve the chances of finding a leak.
Checking System for Leaks Using the Fluorescent Dye Leak DetectorEJS002DW
1. Check the A/C system for leaks using the fluorescent dye leak detector and safety goggles (J-42220) in a
low sunlight area (area without windows preferable). Illuminate all components, fittings and lines. The dye
will appear as a bright green/yellow area at the point of leakage. Fluorescent dye observed at the evapo-
rator drain opening indicates an evaporator core assembly leak (tubes, core or expansion valve).
2. If the suspected area is difficult to see, use an adjustable mirror or wipe the area with a clean shop rag or
cloth, then inspect the shop rag or cloth with the fluorescent dye leak detector (J-42220) for dye residue.
3. After the leak is repaired, remove any residual dye using refrigerant dye cleaner (J-43872) to prevent
future misdiagnosis.
4. Perform a system performance check and then verify the leak repair using a electronic refrigerant leak
detector (J-41995).
NOTE:
Other gases in the work area or substances on the A/C components, for example, anti-freeze, wind-
shield washer fluid, solvents and lubricants, may falsely trigger the leak detector. Make sure the sur-
faces to be checked are clean.
Clean with a dry cloth or blow off with shop air.
Do not allow the sensor tip of the electronic refrigerant leak detector (J-41995) to contact with any sub-
stance. This can also cause false readings and may damage the detector.
Dye InjectionEJS002DX
NOTE:
This procedure is only necessary when recharging the system or when the compressor has seized and must
be replaced.
1. Check the A/C system static (at rest) pressure. Pressure must be at least 345 kPa (3.52 kg/cm
2 , 50 psi). Expansion valve bolts : 4 N·m (0.41 kg-m, 35 in-lb)
A/C refrigerant pipe to expansion valve bolt : Refer to ATC-164, "
Compo-
nents" .
Page 584 of 3371
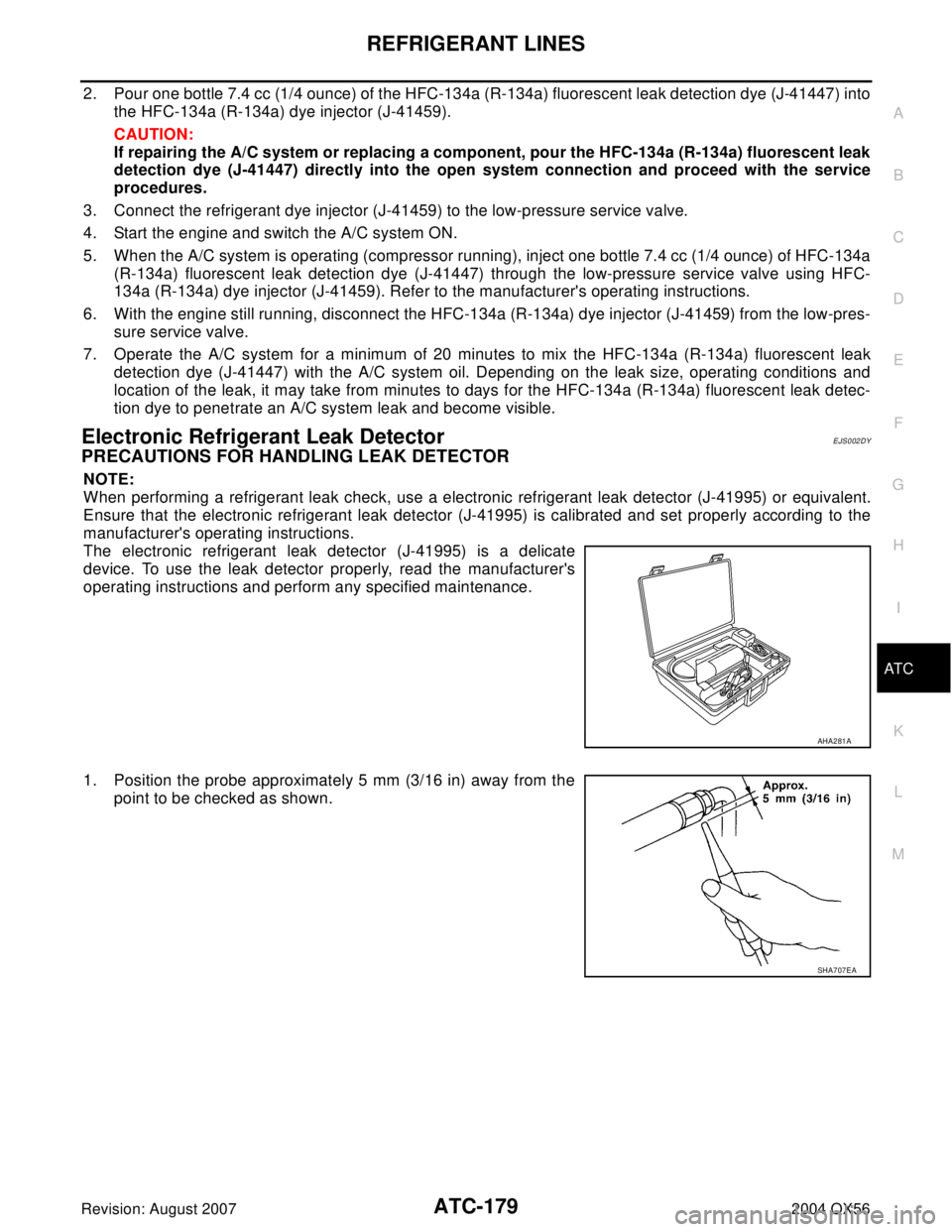
REFRIGERANT LINES
ATC-179
C
D
E
F
G
H
I
K
L
MA
B
AT C
Revision: August 20072004 QX56
2. Pour one bottle 7.4 cc (1/4 ounce) of the HFC-134a (R-134a) fluorescent leak detection dye (J-41447) into
the HFC-134a (R-134a) dye injector (J-41459).
CAUTION:
If repairing the A/C system or replacing a component, pour the HFC-134a (R-134a) fluorescent leak
detection dye (J-41447) directly into the open system connection and proceed with the service
procedures.
3. Connect the refrigerant dye injector (J-41459) to the low-pressure service valve.
4. Start the engine and switch the A/C system ON.
5. When the A/C system is operating (compressor running), inject one bottle 7.4 cc (1/4 ounce) of HFC-134a
(R-134a) fluorescent leak detection dye (J-41447) through the low-pressure service valve using HFC-
134a (R-134a) dye injector (J-41459). Refer to the manufacturer's operating instructions.
6. With the engine still running, disconnect the HFC-134a (R-134a) dye injector (J-41459) from the low-pres-
sure service valve.
7. Operate the A/C system for a minimum of 20 minutes to mix the HFC-134a (R-134a) fluorescent leak
detection dye (J-41447) with the A/C system oil. Depending on the leak size, operating conditions and
location of the leak, it may take from minutes to days for the HFC-134a (R-134a) fluorescent leak detec-
tion dye to penetrate an A/C system leak and become visible.
Electronic Refrigerant Leak DetectorEJS002DY
PRECAUTIONS FOR HANDLING LEAK DETECTOR
NOTE:
When performing a refrigerant leak check, use a electronic refrigerant leak detector (J-41995) or equivalent.
Ensure that the electronic refrigerant leak detector (J-41995) is calibrated and set properly according to the
manufacturer's operating instructions.
The electronic refrigerant leak detector (J-41995) is a delicate
device. To use the leak detector properly, read the manufacturer's
operating instructions and perform any specified maintenance.
1. Position the probe approximately 5 mm (3/16 in) away from the
point to be checked as shown.
AHA2 81 A
SHA707EA