Page 4233 of 6000
4C–27 DRIVE SHAFT SYSTEM
412RS019
412RS020
Legend
(1) Outer Case
(2) Circlip
(3) Open Ends
18. Install bellows. Adjust the air pressure within the
bellows by inserting a screwdriver or equivalent, so
that it equals atmospheric pressure.
412RW053
19. Install Band. After installation, check that the bellows
is free from distortion.
Page 4234 of 6000
4C–28
DRIVE SHAFT SYSTEM
Shift On The Fly System
Shift On The Fly System and Associated Parts
412RW004
Legend
(1) Filler Plug
(2) Bolt
(3) Oil Seal
(4) Snap Ring(External)
(5) Inner Shaft Bearing
(6) Snap Ring(Internal)
(7) Inner Shaft(8) Needle Bearing
(9) Clutch Gear
(10) Sleeve
(11) Housing
(12) Front Axle Drive Shaft (LH side)with Bracket
(13) Bolt
(14) Actuator Assembly
(15) Bolt
Disassembly
1. Remove filler plug and gasket, drain oil.
2. Loosen mounting bracket fitting bolts and remove
front axle drive shaft from front axle case.3. Remove Actuator Assembly and draw out actuator
ASM.
4. Remove housing.
5. Remove sleeve.
6. Remove clutch gear.
Page 4235 of 6000
4C–29 DRIVE SHAFT SYSTEM
7. Remove snap ring from front axle case by using snap
ring pliers.
412RW017
8. Take out inner shaft from front axle case.
9. Remove snap ring from inner shaft by using snap ring
pliers.
412RW016
10. Remove inner shaft bearing by using a remover
5–8840–2197–0 and press.
NOTE: Be careful not to damage the shaft.
412RW015
11. Remove needle bearing from inner shaft by using a
remover 5–8840–0027–0 and sliding hammer
5–8840–0084–0.
NOTE: Be careful not to damage the shaft.
412RS045
12. Remove oil seal from front axle case.
NOTE: Be careful not to damage the front axle case.
Page 4236 of 6000
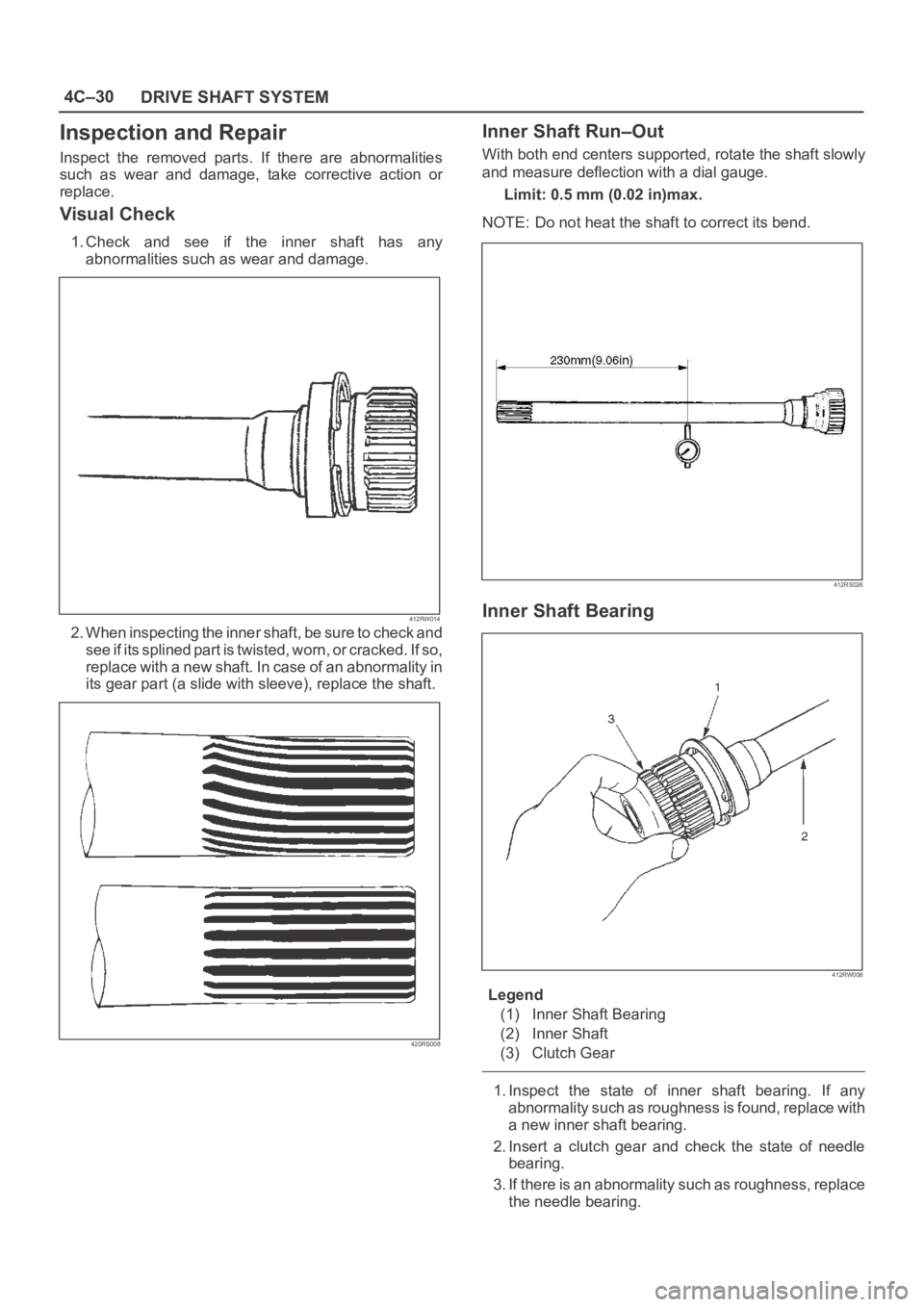
4C–30
DRIVE SHAFT SYSTEM
Inspection and Repair
Inspect the removed parts. If there are abnormalities
such as wear and damage, take corrective action or
replace.
Visual Check
1. Check and see if the inner shaft has any
abnormalities such as wear and damage.
412RW014
2. When inspecting the inner shaft, be sure to check and
see if its splined part is twisted, worn, or cracked. If so,
replace with a new shaft. In case of an abnormality in
its gear part (a slide with sleeve), replace the shaft.
420RS008
Inner Shaft Run–Out
With both end centers supported, rotate the shaft slowly
and measure deflection with a dial gauge.
Limit: 0.5 mm (0.02 in)max.
NOTE: Do not heat the shaft to correct its bend.
412RS026
Inner Shaft Bearing
412RW006
Legend
(1) Inner Shaft Bearing
(2) Inner Shaft
(3) Clutch Gear
1. Inspect the state of inner shaft bearing. If any
abnormality such as roughness is found, replace with
a new inner shaft bearing.
2. Insert a clutch gear and check the state of needle
bearing.
3. If there is an abnormality such as roughness, replace
the needle bearing.
Page 4237 of 6000
4C–31 DRIVE SHAFT SYSTEM
Sleeve Condition
Check and see that there is no wear, damage, or cracking
in the sleeve.
NOTE: Close inspection of the groove and inner gear are
required because those are important parts.
Sleeve Function
412RW011Operate the sleeve with the inner shaft combined with the
clutch gear. If roughness is felt, replace the sleeve.
NOTE: Gear oil should be applied to the contact surface
of gear.
Check the width of sleeve center groove.
Limit: 7.1 mm (0.28 in) max.
412RW022
Clutch Gear Condition
Check and see that there is no wear, damage, cracking,
or any other abnormality in the clutch gear.
Clutch Gear Function
412RW010If there is an abnormality such as roughness when
operated in combination with sleeve, replace the clutch
gear.
NOTE: When inspecting, gear oil should be applied to the
contact surface of gear.
Clutch Gear Journal Diameter
Make sure of the size illustrated.
Limit: 36.98 mm (1.456 in) min.
412RW009
Page 4238 of 6000
4C–32
DRIVE SHAFT SYSTEM
Actuator
Check and see that there is no damage, cracking, or other
abnormality.
Functional Check
412RW021
412RW013
412RW007Disconnect the shift position switch and make sure of
function with a vacuum of –400 mmHg applied to Ports A
and B, in accordance with the table below.
State
Port APort BFunction
C–400 mmHgA/PE
DA/P–400 mmHgF
If there is an abnormality, replace the actuator as an
assembly.
NOTE:
1. If the actuator works under –400mmHg or less, there
is no functional problem.
2. Be careful not to permit the entry of water or dust into
the ports of the actuator.
Dimensional Check
Measure illustrated sizes 1, 2, and 3.
Limit
1=64.3 mm (2.53 in) max.
2=6.7 mm (0.26 in) min.
3=6.7 mm (0.26 in) min.
Page 4239 of 6000
4C–33 DRIVE SHAFT SYSTEM
412RS037
Reassembly
1. Install the new oil seal which has been immersed in
differential gear oil, by using an oil seal installer
5–8840–2407–0 and grip 5–8840–0007–0.
412RS043
2. Force a new needle bearing into inner shaft by using a
installer 5–8840–2408–0 and grip 5–8840–0007–0.
412RS051
3. Place a new snap ring(internal) in inner shaft.
Force a new inner shaft bearing into the inner shaft by
using a installer 5–8840–2197–0 and press.
412RS044
4. Install snap ring(external).
NOTE: Be careful not to damage the inner shaft.
5. Clean the housing contact surface of the front axle
case and insert inner shaft assembly into the front
axle case.
Page 4240 of 6000
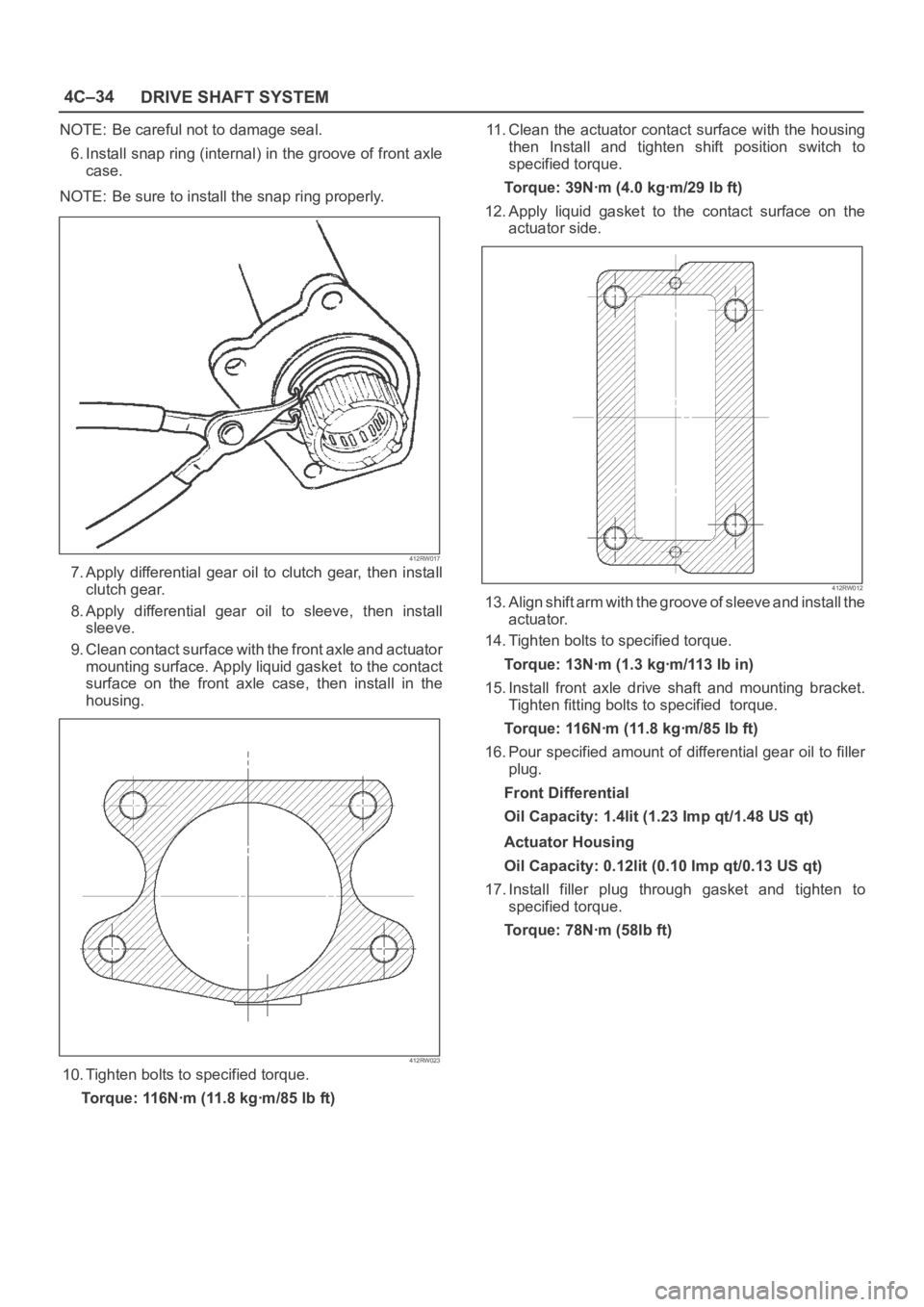
4C–34
DRIVE SHAFT SYSTEM
NOTE: Be careful not to damage seal.
6. Install snap ring (internal) in the groove of front axle
case.
NOTE: Be sure to install the snap ring properly.
412RW017
7. Apply differential gear oil to clutch gear, then install
clutch gear.
8. Apply differential gear oil to sleeve, then install
sleeve.
9. Clean contact surface with the front axle and actuator
mounting surface. Apply liquid gasket to the contact
surface on the front axle case, then install in the
housing.
412RW023
10. Tighten bolts to specified torque.
Torque: 116Nꞏm (11.8 kgꞏm/85 lb ft)11. Clean the actuator contact surface with the housing
then Install and tighten shift position switch to
specified torque.
Torque: 39Nꞏm (4.0 kgꞏm/29 lb ft)
12. Apply liquid gasket to the contact surface on the
actuator side.
412RW012
13. Align shift arm with the groove of sleeve and install the
actuator.
14. Tighten bolts to specified torque.
Torque: 13Nꞏm (1.3 kgꞏm/113 lb in)
15. Install front axle drive shaft and mounting bracket.
Tighten fitting bolts to specified torque.
Torque: 116Nꞏm (11.8 kgꞏm/85 lb ft)
16. Pour specified amount of differential gear oil to filler
plug.
Front Differential
Oil Capacity: 1.4lit (1.23 Imp qt/1.48 US qt)
Actuator Housing
Oil Capacity: 0.12lit (0.10 Imp qt/0.13 US qt)
17. Install filler plug through gasket and tighten to
specified torque.
To r q u e : 7 8 N ꞏm ( 5 8 l b f t )