Page 5657 of 6000
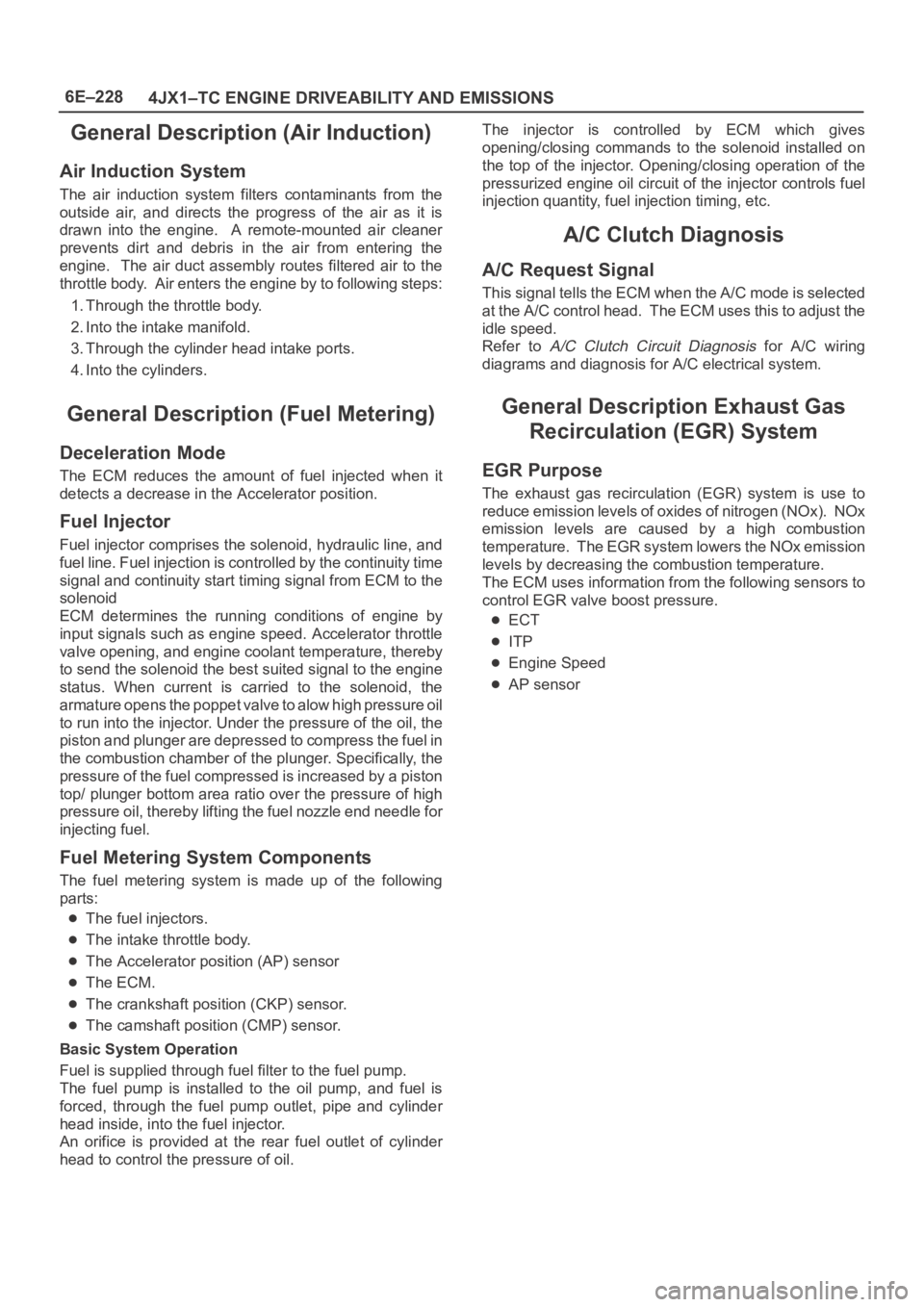
6E–228
4JX1–TC ENGINE DRIVEABILITY AND EMISSIONS
General Description (Air Induction)
Air Induction System
The air induction system filters contaminants from the
outside air, and directs the progress of the air as it is
drawn into the engine. A remote-mounted air cleaner
prevents dirt and debris in the air from entering the
engine. The air duct assembly routes filtered air to the
throttle body. Air enters the engine by to following steps:
1. Through the throttle body.
2. Into the intake manifold.
3. Through the cylinder head intake ports.
4. Into the cylinders.
General Description (Fuel Metering)
Deceleration Mode
The ECM reduces the amount of fuel injected when it
detects a decrease in the Accelerator position.
Fuel Injector
Fuel injector comprises the solenoid, hydraulic line, and
fuel line. Fuel injection is controlled by the continuity time
signal and continuity start timing signal from ECM to the
solenoid
ECM determines the running conditions of engine by
input signals such as engine speed. Accelerator throttle
valve opening, and engine coolant temperature, thereby
to send the solenoid the best suited signal to the engine
status. When current is carried to the solenoid, the
armature opens the poppet valve to alow high pressure oil
to run into the injector. Under the pressure of the oil, the
piston and plunger are depressed to compress the fuel in
the combustion chamber of the plunger. Specifically, the
pressure of the fuel compressed is increased by a piston
top/ plunger bottom area ratio over the pressure of high
pressure oil, thereby lifting the fuel nozzle end needle for
injecting fuel.
Fuel Metering System Components
The fuel metering system is made up of the following
parts:
The fuel injectors.
The intake throttle body.
The Accelerator position (AP) sensor
The ECM.
The crankshaft position (CKP) sensor.
The camshaft position (CMP) sensor.
Basic System Operation
Fuel is supplied through fuel filter to the fuel pump.
The fuel pump is installed to the oil pump, and fuel is
forced, through the fuel pump outlet, pipe and cylinder
head inside, into the fuel injector.
An orifice is provided at the rear fuel outlet of cylinder
head to control the pressure of oil.The injector is controlled by ECM which gives
opening/closing commands to the solenoid installed on
the top of the injector. Opening/closing operation of the
pressurized engine oil circuit of the injector controls fuel
injection quantity, fuel injection timing, etc.
A/C Clutch Diagnosis
A/C Request Signal
This signal tells the ECM when the A/C mode is selected
at the A/C control head. The ECM uses this to adjust the
idle speed.
Refer to
A/C Clutch Circuit Diagnosis for A/C wiring
diagrams and diagnosis for A/C electrical system.
General Description Exhaust Gas
Recirculation (EGR) System
EGR Purpose
The exhaust gas recirculation (EGR) system is use to
reduce emission levels of oxides of nitrogen (NOx). NOx
emission levels are caused by a high combustion
temperature. The EGR system lowers the NOx emission
levels by decreasing the combustion temperature.
The ECM uses information from the following sensors to
control EGR valve boost pressure.
ECT
ITP
Engine Speed
AP sensor
Page 5658 of 6000
6E–229 4JX1–TC ENGINE DRIVEABILITY AND EMISSIONS
Fuse and Relay Panel (Underhood Electrical Center) RHD
035RW109
Page 5659 of 6000
6E–230
4JX1–TC ENGINE DRIVEABILITY AND EMISSIONS
Fuse and Relay Panel (Underhood Electrical Center) LHD
035RW108
Page 5660 of 6000
ENGINE EXHAUST 6F – 1
ENGINE EXHAUST
CONTENTS
CAUTION: Exhaust system components must have
enough clearance from the underbody to prevent
overheating of the floor pan and possible damage to the passenger compartment, insulation and trim
materials.
General Description . . . . . . . . . . . . . . . . . . 6F–2
Hangers . . . . . . . . . . . . . . . . . . . . . . . . . 6F–2
Gasket . . . . . . . . . . . . . . . . . . . . . . . . . . 6F–2
On-Vehicle Service . . . . . . . . . . . . . . . . . . . 6F–3
Front Exhaust Pipe . . . . . . . . . . . . . . . . . 6F–3Center Exhaust Pipe . . . . . . . . . . . . . . . . 6F–5
Exhaust Silencer . . . . . . . . . . . . . . . . . . . 6F–6
Rear Exhaust Pipe . . . . . . . . . . . . . . . . . 6F–7
Page 5661 of 6000
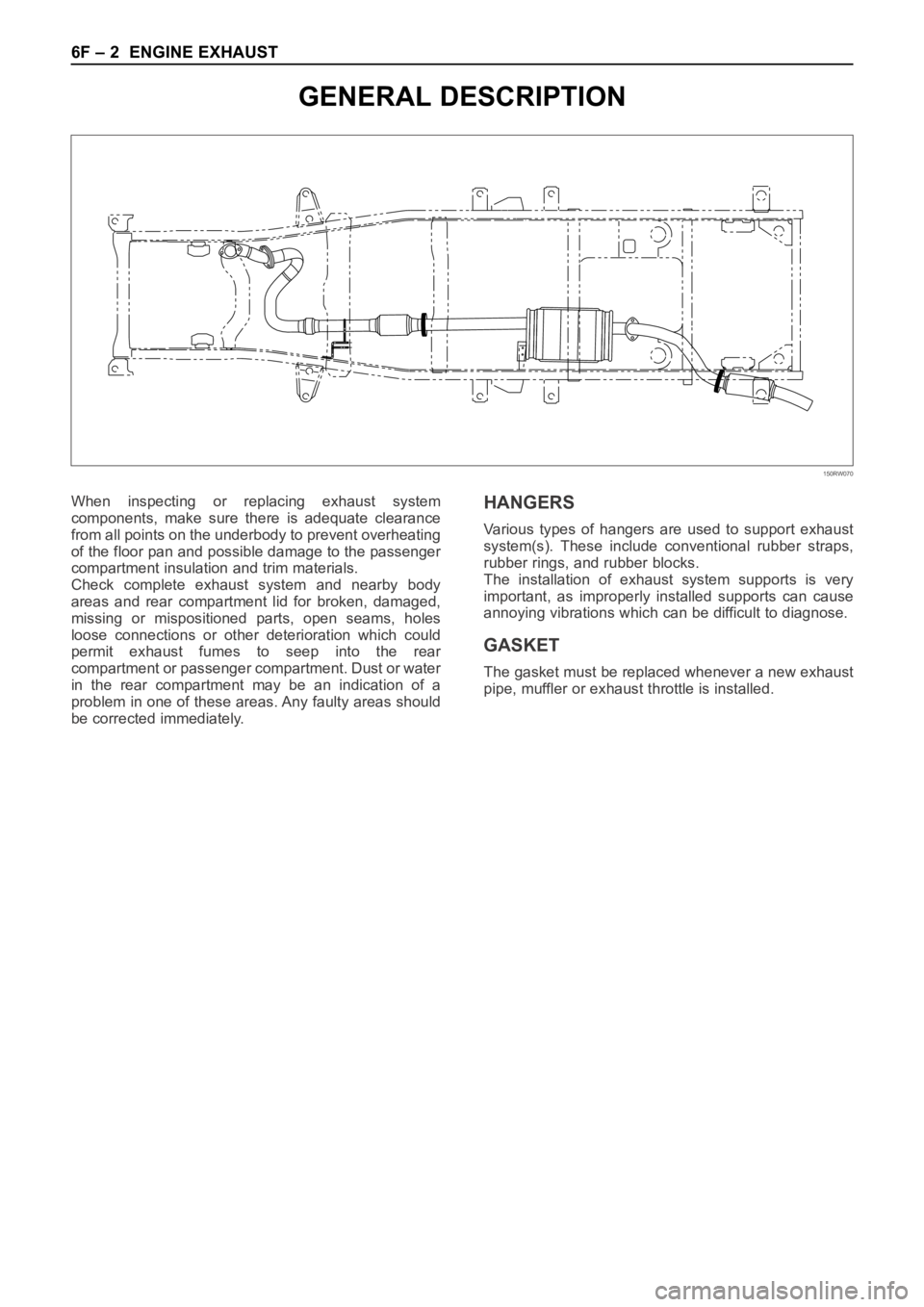
6F – 2 ENGINE EXHAUST
GENERAL DESCRIPTION
150RW070
When inspecting or replacing exhaust system
components, make sure there is adequate clearance
from all points on the underbody to prevent overheating
of the floor pan and possible damage to the passenger
compartment insulation and trim materials.
Check complete exhaust system and nearby body
areas and rear compartment lid for broken, damaged,
missing or mispositioned parts, open seams, holes
loose connections or other deterioration which could
permit exhaust fumes to seep into the rear
compartment or passenger compartment. Dust or water
in the rear compartment may be an indication of a
problem in one of these areas. Any faulty areas should
be corrected immediately.HANGERS
Various types of hangers are used to support exhaust
system(s). These include conventional rubber straps,
rubber rings, and rubber blocks.
The installation of exhaust system supports is very
important, as improperly installed supports can cause
annoying vibrations which can be difficult to diagnose.
GASKET
The gasket must be replaced whenever a new exhaust
pipe, muffler or exhaust throttle is installed.
Page 5662 of 6000
ENGINE EXHAUST 6F – 3
ON-VEHICLE SERVICE
FRONT EXHAUST PIPE
Rattles and noise vibrations in the exhaust system are
usually caused by misalignment of parts. When aligning
the system, leave all bolts or nuts loose until all parts
are properly aligned; then tighten, working from front to
rear.
1. Check connections for looseness or damage,
especially for exhaust gas leakage.
2. Check clamps and rubbers for weakness, cracks or
damage.3. If any part of the converter heat shield is damaged
or dented to the extent that it contacts the catalyst,
repair or replace.
4. Check for dents or damage and for any holes or
cracks caused by corrosion.
3
2 1
Legend
(1) Front exhaust pipe
(2) Center exhaust pipe
(3) Mounting rubber
150RW071
Page 5663 of 6000
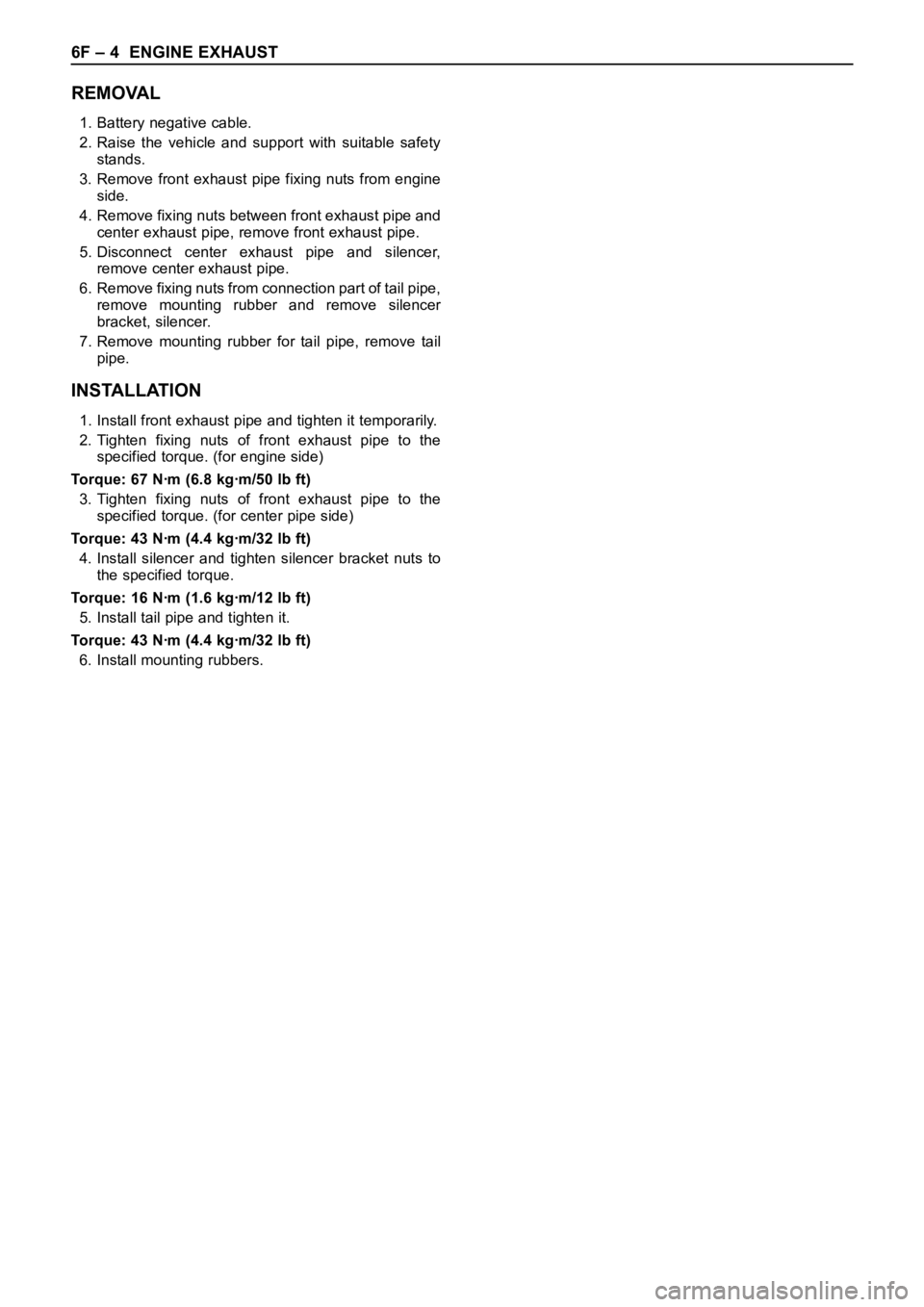
6F – 4 ENGINE EXHAUST
REMOVAL
1. Battery negative cable.
2. Raise the vehicle and support with suitable safety
stands.
3. Remove front exhaust pipe fixing nuts from engine
side.
4. Remove fixing nuts between front exhaust pipe and
center exhaust pipe, remove front exhaust pipe.
5. Disconnect center exhaust pipe and silencer,
remove center exhaust pipe.
6. Remove fixing nuts from connection part of tail pipe,
remove mounting rubber and remove silencer
bracket, silencer.
7. Remove mounting rubber for tail pipe, remove tail
pipe.
INSTALLATION
1. Install front exhaust pipe and tighten it temporarily.
2. Tighten fixing nuts of front exhaust pipe to the
specified torque. (for engine side)
Torque: 67 Nꞏm (6.8 kgꞏm/50 lb ft)
3. Tighten fixing nuts of front exhaust pipe to the
specified torque. (for center pipe side)
Torque: 43 Nꞏm (4.4 kgꞏm/32 lb ft)
4. Install silencer and tighten silencer bracket nuts to
the specified torque.
Torque: 16 Nꞏm (1.6 kgꞏm/12 lb ft)
5. Install tail pipe and tighten it.
Torque: 43 Nꞏm (4.4 kgꞏm/32 lb ft)
6. Install mounting rubbers.
Page 5664 of 6000
ENGINE EXHAUST 6F – 5
CENTER EXHAUST PIPE
REMOVAL
1. Battery negative cable.
2. Raise the vehicle and support with suitable safety
stands.
3. Remove mounting rubber.
4. Remove fixing nuts from silencer side.
5. Remove fixing nuts from front exhaust pipe.
6. Remove center exhaust pipe assembly.
INSTALLATION
1. Place center exhaust pipe in the original position
then tighten fixing nuts temporarily.
2. Install mounting rubber.
3. Tighten front exhaust pipe side nuts to the specified
torque.
Torque : 43 Nꞏm (4.4 kgꞏm/32 lb ft)
4. Tighten silencer side nuts to the specified torque.
Torque : 43 Nꞏm (4.4 kgꞏm/32 lb ft)
3
2 1
Legend
(1) Front Exhaust Pipe
(2) Center Exhaust Pipe
(3) Mounting Rubber
150RW071