Page 3537 of 6000
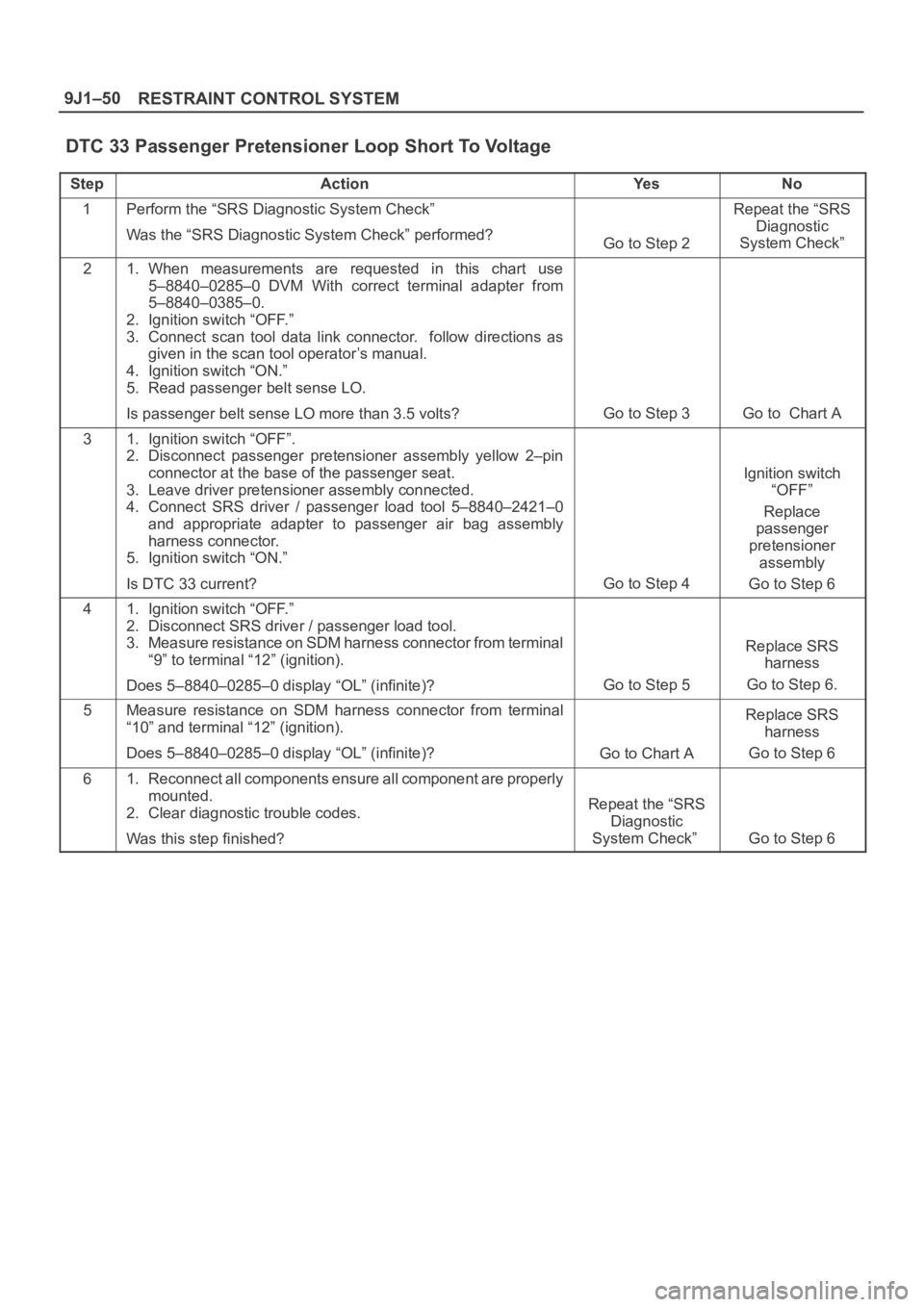
RESTRAINT CONTROL SYSTEM 9J1–50
DTC 33 Passenger Pretensioner Loop Short To Voltage
StepActionYe sNo
1Perform the “SRS Diagnostic System Check”
Was the “SRS Diagnostic System Check” performed?
Go to Step 2
Repeat the “SRS
Diagnostic
System Check”
21. When measurements are requested in this chart use
5–8840–0285–0 DVM With correct terminal adapter from
5–8840–0385–0.
2. Ignition switch “OFF.”
3. Connect scan tool data link connector. follow directions as
given in the scan tool operator’s manual.
4. Ignition switch “ON.”
5. Read passenger belt sense LO.
Is passenger belt sense LO more than 3.5 volts?
Go to Step 3Go to Chart A
31. Ignition switch “OFF”.
2. Disconnect passenger pretensioner assembly yellow 2–pin
connector at the base of the passenger seat.
3. Leave driver pretensioner assembly connected.
4. Connect SRS driver / passenger load tool 5–8840–2421–0
and appropriate adapter to passenger air bag assembly
harness connector.
5. Ignition switch “ON.”
Is DTC 33 current?
Go to Step 4
Ignition switch
“OFF”
Replace
passenger
pretensioner
assembly
Go to Step 6
41. Ignition switch “OFF.”
2. Disconnect SRS driver / passenger load tool.
3. Measure resistance on SDM harness connector from terminal
“9” to terminal “12” (ignition).
Does 5–8840–0285–0 display “OL” (infinite)?
Go to Step 5
Replace SRS
harness
Go to Step 6.
5Measure resistance on SDM harness connector from terminal
“10” and terminal “12” (ignition).
Does 5–8840–0285–0 display “OL” (infinite)?
Go to Chart A
Replace SRS
harness
Go to Step 6
61. Reconnect all components ensure all component are properly
mounted.
2. Clear diagnostic trouble codes.
Was this step finished?
Repeat the “SRS
Diagnostic
System Check”
Go to Step 6
Page 3538 of 6000
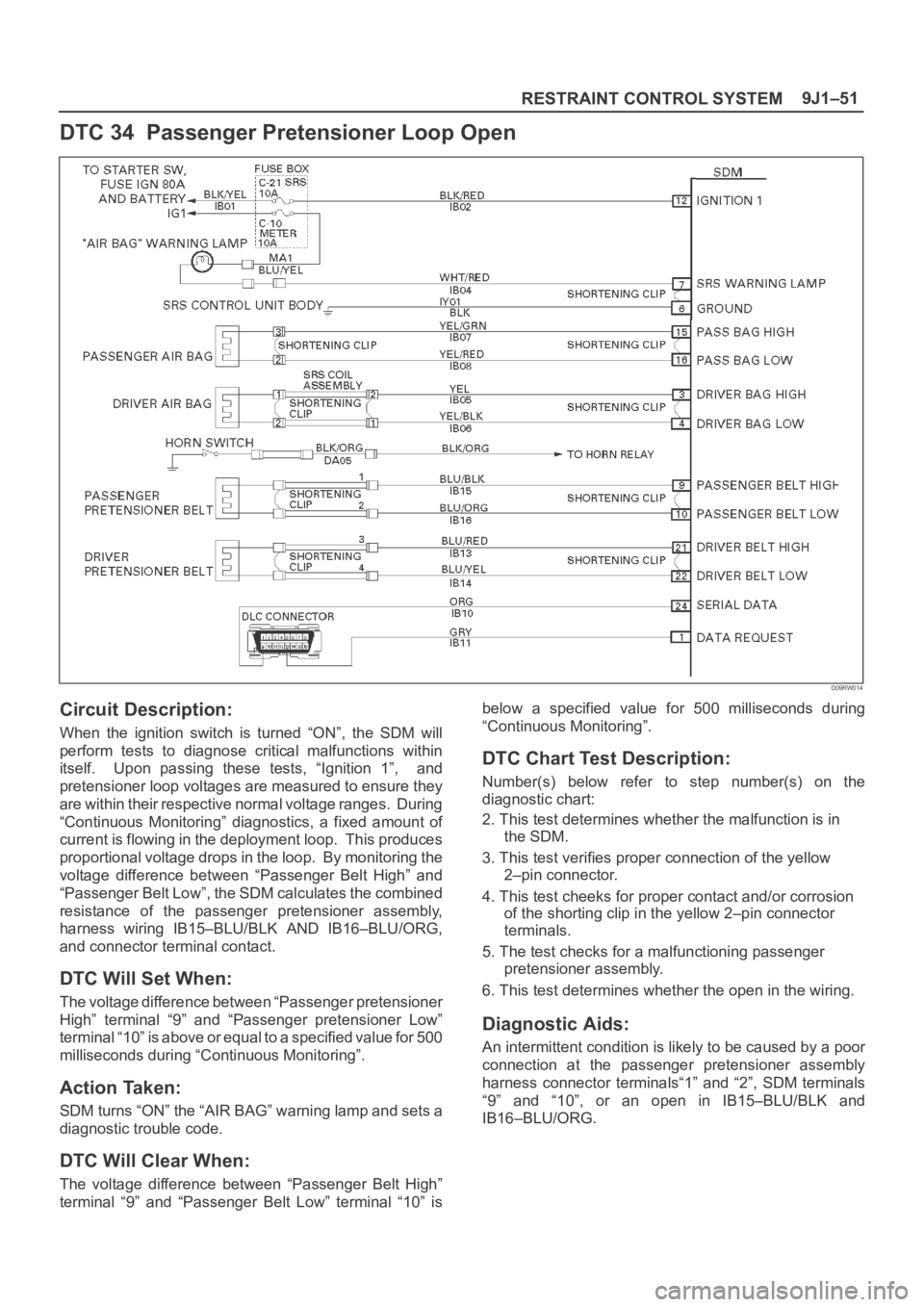
9J1–51
RESTRAINT CONTROL SYSTEM
DTC 34 Passenger Pretensioner Loop Open
D09RW014
Circuit Description:
When the ignition switch is turned “ON”, the SDM will
perform tests to diagnose critical malfunctions within
itself. Upon passing these tests, “Ignition 1”, and
pretensioner loop voltages are measured to ensure they
are within their respective normal voltage ranges. During
“Continuous Monitoring” diagnostics, a fixed amount of
current is flowing in the deployment loop. This produces
proportional voltage drops in the loop. By monitoring the
voltage difference between “Passenger Belt High” and
“Passenger Belt Low”, the SDM calculates the combined
resistance of the passenger pretensioner assembly,
harness wiring IB15–BLU/BLK AND IB16–BLU/ORG,
and connector terminal contact.
DTC Will Set When:
The voltage difference between “Passenger pretensioner
High” terminal “9” and “Passenger pretensioner Low”
terminal “10” is above or equal to a specified value for 500
milliseconds during “Continuous Monitoring”.
Action Taken:
SDM turns “ON” the “AIR BAG” warning lamp and sets a
diagnostic trouble code.
DTC Will Clear When:
The voltage difference between “Passenger Belt High”
terminal “9” and “Passenger Belt Low” terminal “10” isbelow a specified value for 500 milliseconds during
“Continuous Monitoring”.
DTC Chart Test Description:
Number(s) below refer to step number(s) on the
diagnostic chart:
2. This test determines whether the malfunction is in
the SDM.
3. This test verifies proper connection of the yellow
2–pin connector.
4. This test cheeks for proper contact and/or corrosion
of the shorting clip in the yellow 2–pin connector
terminals.
5. The test checks for a malfunctioning passenger
pretensioner assembly.
6. This test determines whether the open in the wiring.
Diagnostic Aids:
An intermittent condition is likely to be caused by a poor
connection at the passenger pretensioner assembly
harness connector terminals“1” and “2”, SDM terminals
“9” and “10”, or an open in IB15–BLU/BLK and
IB16–BLU/ORG.
Page 3539 of 6000
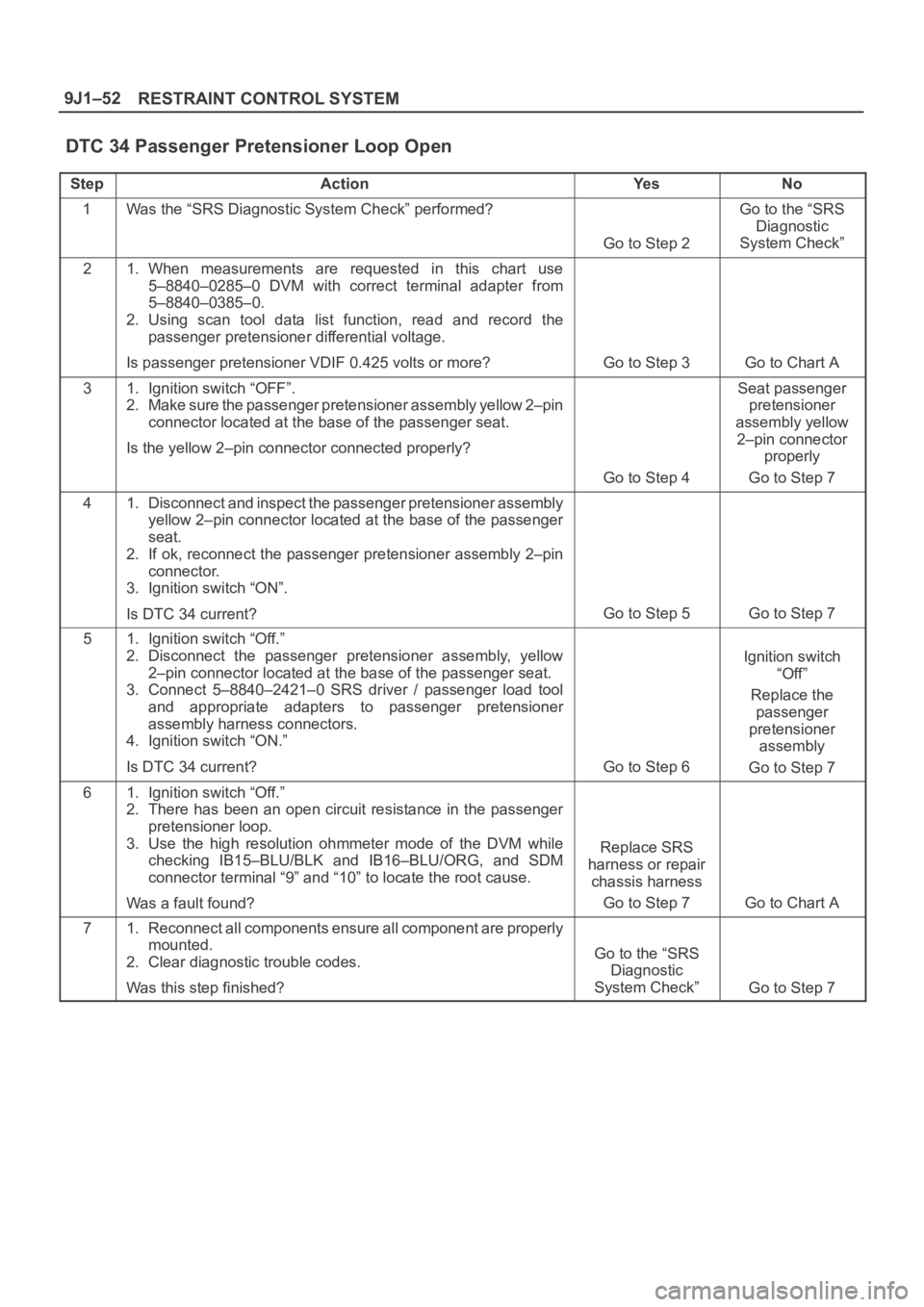
RESTRAINT CONTROL SYSTEM 9J1–52
DTC 34 Passenger Pretensioner Loop Open
StepActionYe sNo
1Was the “SRS Diagnostic System Check” performed?
Go to Step 2
Go to the “SRS
Diagnostic
System Check”
21. When measurements are requested in this chart use
5–8840–0285–0 DVM with correct terminal adapter from
5–8840–0385–0.
2. Using scan tool data list function, read and record the
passenger pretensioner differential voltage.
Is passenger pretensioner VDIF 0.425 volts or more?
Go to Step 3Go to Chart A
31. Ignition switch “OFF”.
2. Make sure the passenger pretensioner assembly yellow 2–pin
connector located at the base of the passenger seat.
Is the yellow 2–pin connector connected properly?
Go to Step 4
Seat passenger
pretensioner
assembly yellow
2–pin connector
properly
Go to Step 7
41. Disconnect and inspect the passenger pretensioner assembly
yellow 2–pin connector located at the base of the passenger
seat.
2. If ok, reconnect the passenger pretensioner assembly 2–pin
connector.
3. Ignition switch “ON”.
Is DTC 34 current?
Go to Step 5Go to Step 7
51. Ignition switch “Off.”
2. Disconnect the passenger pretensioner assembly, yellow
2–pin connector located at the base of the passenger seat.
3. Connect 5–8840–2421–0 SRS driver / passenger load tool
and appropriate adapters to passenger pretensioner
assembly harness connectors.
4. Ignition switch “ON.”
Is DTC 34 current?
Go to Step 6
Ignition switch
“Off”
Replace the
passenger
pretensioner
assembly
Go to Step 7
61. Ignition switch “Off.”
2. There has been an open circuit resistance in the passenger
pretensioner loop.
3. Use the high resolution ohmmeter mode of the DVM while
checking IB15–BLU/BLK and IB16–BLU/ORG, and SDM
connector terminal “9” and “10” to locate the root cause.
Was a fault found?
Replace SRS
harness or repair
chassis harness
Go to Step 7
Go to Chart A
71. Reconnect all components ensure all component are properly
mounted.
2. Clear diagnostic trouble codes.
Was this step finished?
Go to the “SRS
Diagnostic
System Check”
Go to Step 7
Page 3540 of 6000
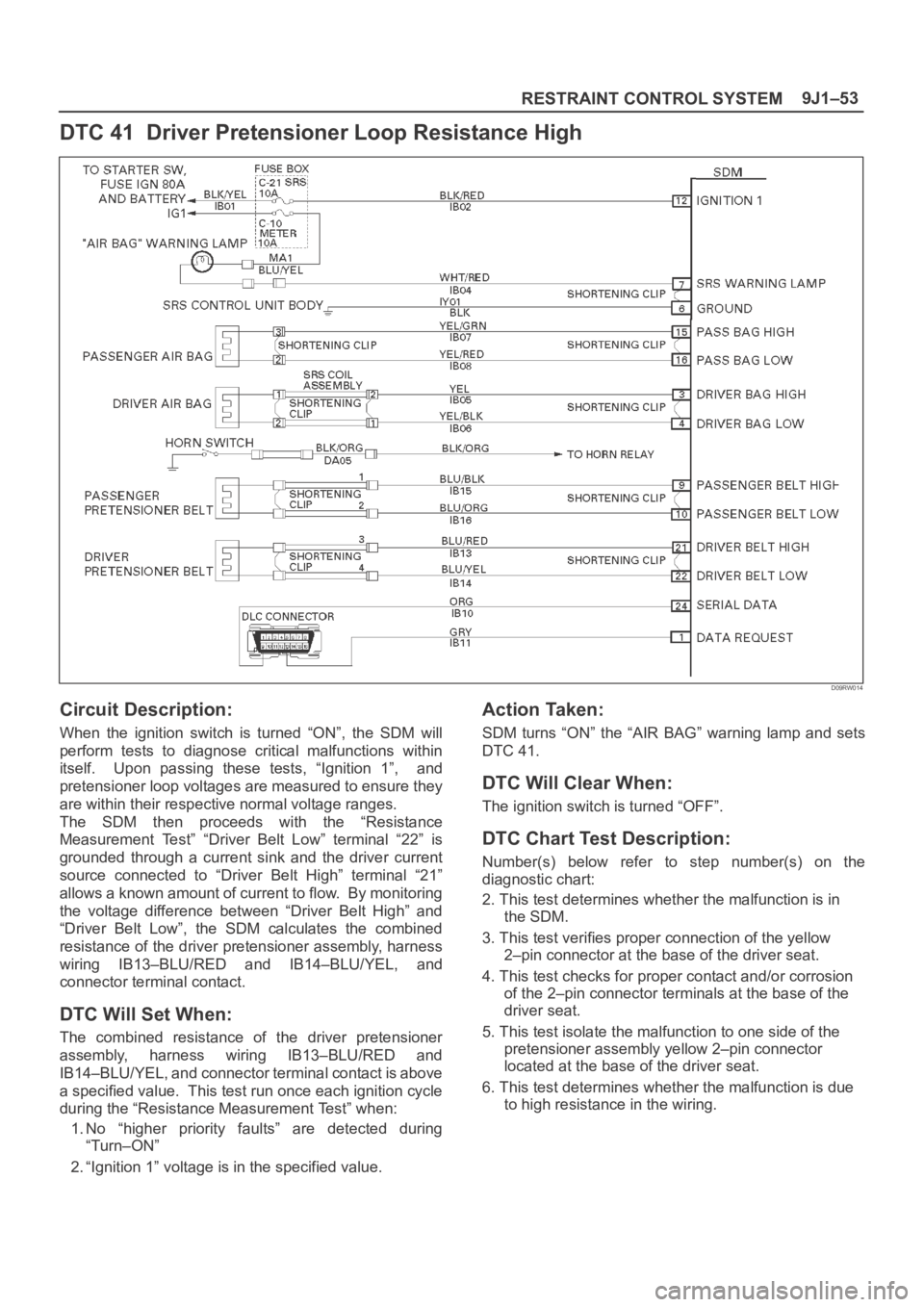
9J1–53
RESTRAINT CONTROL SYSTEM
DTC 41 Driver Pretensioner Loop Resistance High
D09RW014
Circuit Description:
When the ignition switch is turned “ON”, the SDM will
perform tests to diagnose critical malfunctions within
itself. Upon passing these tests, “Ignition 1”, and
pretensioner loop voltages are measured to ensure they
are within their respective normal voltage ranges.
The SDM then proceeds with the “Resistance
Measurement Test” “Driver Belt Low” terminal “22” is
grounded through a current sink and the driver current
source connected to “Driver Belt High” terminal “21”
allows a known amount of current to flow. By monitoring
the voltage difference between “Driver Belt High” and
“Driver Belt Low”, the SDM calculates the combined
resistance of the driver pretensioner assembly, harness
wiring IB13–BLU/RED and IB14–BLU/YEL, and
connector terminal contact.
DTC Will Set When:
The combined resistance of the driver pretensioner
assembly, harness wiring IB13–BLU/RED and
IB14–BLU/YEL, and connector terminal contact is above
a specified value. This test run once each ignition cycle
during the “Resistance Measurement Test” when:
1. No “higher priority faults” are detected during
“Turn–ON”
2. “Ignition 1” voltage is in the specified value.
Action Taken:
SDM turns “ON” the “AIR BAG” warning lamp and sets
DTC 41.
DTC Will Clear When:
The ignition switch is turned “OFF”.
DTC Chart Test Description:
Number(s) below refer to step number(s) on the
diagnostic chart:
2. This test determines whether the malfunction is in
the SDM.
3. This test verifies proper connection of the yellow
2–pin connector at the base of the driver seat.
4. This test checks for proper contact and/or corrosion
of the 2–pin connector terminals at the base of the
driver seat.
5. This test isolate the malfunction to one side of the
pretensioner assembly yellow 2–pin connector
located at the base of the driver seat.
6. This test determines whether the malfunction is due
to high resistance in the wiring.
Page 3541 of 6000
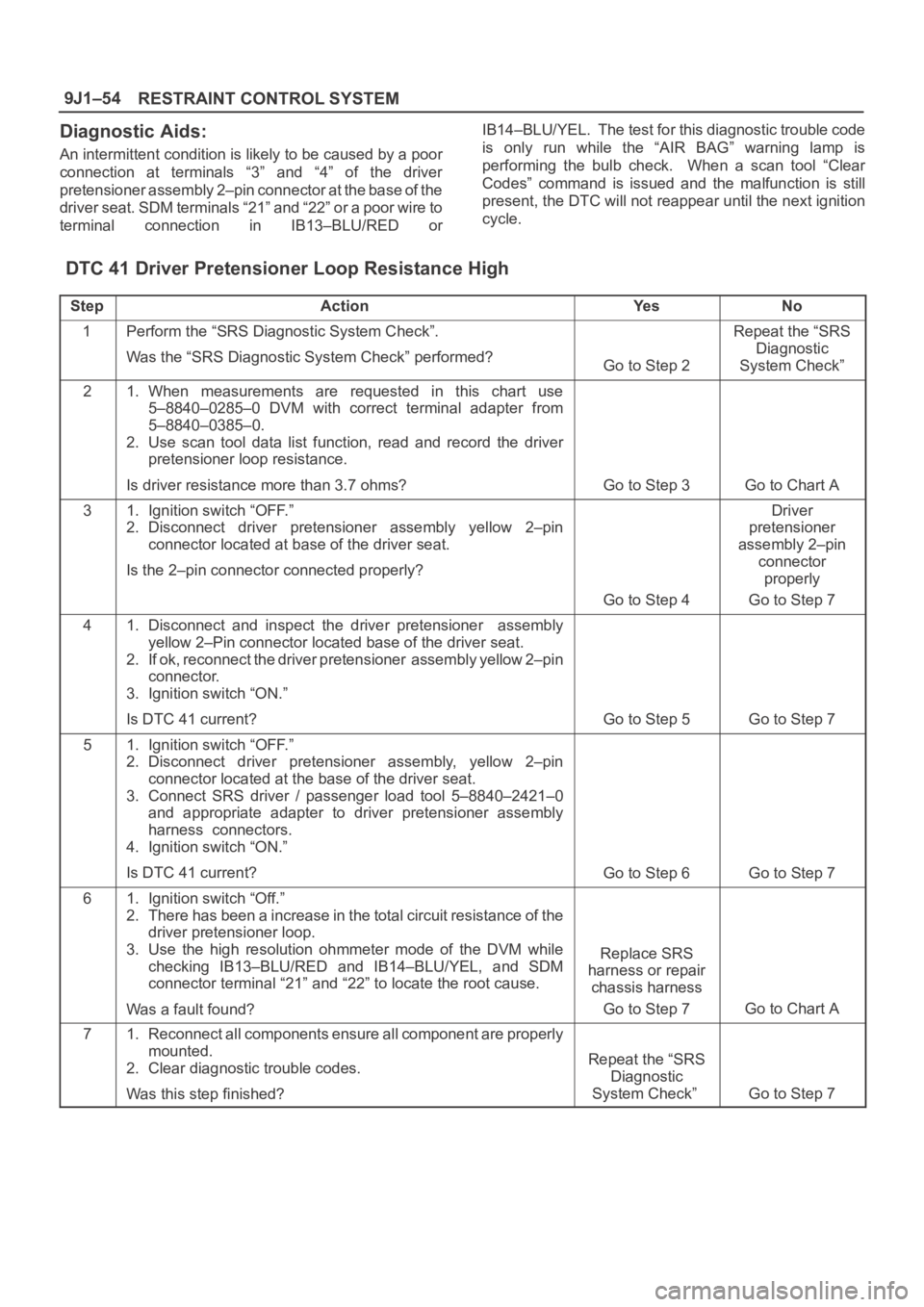
RESTRAINT CONTROL SYSTEM 9J1–54
Diagnostic Aids:
An intermittent condition is likely to be caused by a poor
connection at terminals “3” and “4” of the driver
pretensioner assembly 2–pin connector at the base of the
driver seat. SDM terminals “21” and “22” or a poor wire to
terminal connection in IB13–BLU/RED orIB14–BLU/YEL. The test for this diagnostic trouble code
is only run while the “AIR BAG” warning lamp is
performing the bulb check. When a scan tool “Clear
Codes” command is issued and the malfunction is still
present, the DTC will not reappear until the next ignition
cycle.
DTC 41 Driver Pretensioner Loop Resistance High
StepActionYe sNo
1Perform the “SRS Diagnostic System Check”.
Was the “SRS Diagnostic System Check” performed?
Go to Step 2
Repeat the “SRS
Diagnostic
System Check”
21. When measurements are requested in this chart use
5–8840–0285–0 DVM with correct terminal adapter from
5–8840–0385–0.
2. Use scan tool data list function, read and record the driver
pretensioner loop resistance.
Is driver resistance more than 3.7 ohms?
Go to Step 3Go to Chart A
31. Ignition switch “OFF.”
2. Disconnect driver pretensioner assembly yellow 2–pin
connector located at base of the driver seat.
Is the 2–pin connector connected properly?
Go to Step 4
Driver
pretensioner
assembly 2–pin
connector
properly
Go to Step 7
41. Disconnect and inspect the driver pretensioner assembly
yellow 2–Pin connector located base of the driver seat.
2. If ok, reconnect the driver pretensioner assembly yellow 2–pin
connector.
3. Ignition switch “ON.”
Is DTC 41 current?
Go to Step 5Go to Step 7
51. Ignition switch “OFF.”
2. Disconnect driver pretensioner assembly, yellow 2–pin
connector located at the base of the driver seat.
3. Connect SRS driver / passenger load tool 5–8840–2421–0
and appropriate adapter to driver pretensioner assembly
harness connectors.
4. Ignition switch “ON.”
Is DTC 41 current?
Go to Step 6Go to Step 7
61. Ignition switch “Off.”
2. There has been a increase in the total circuit resistance of the
driver pretensioner loop.
3. Use the high resolution ohmmeter mode of the DVM while
checking IB13–BLU/RED and IB14–BLU/YEL, and SDM
connector terminal “21” and “22” to locate the root cause.
Was a fault found?
Replace SRS
harness or repair
chassis harness
Go to Step 7
Go to Chart A
71. Reconnect all components ensure all component are properly
mounted.
2. Clear diagnostic trouble codes.
Was this step finished?
Repeat the “SRS
Diagnostic
System Check”
Go to Step 7
Page 3542 of 6000
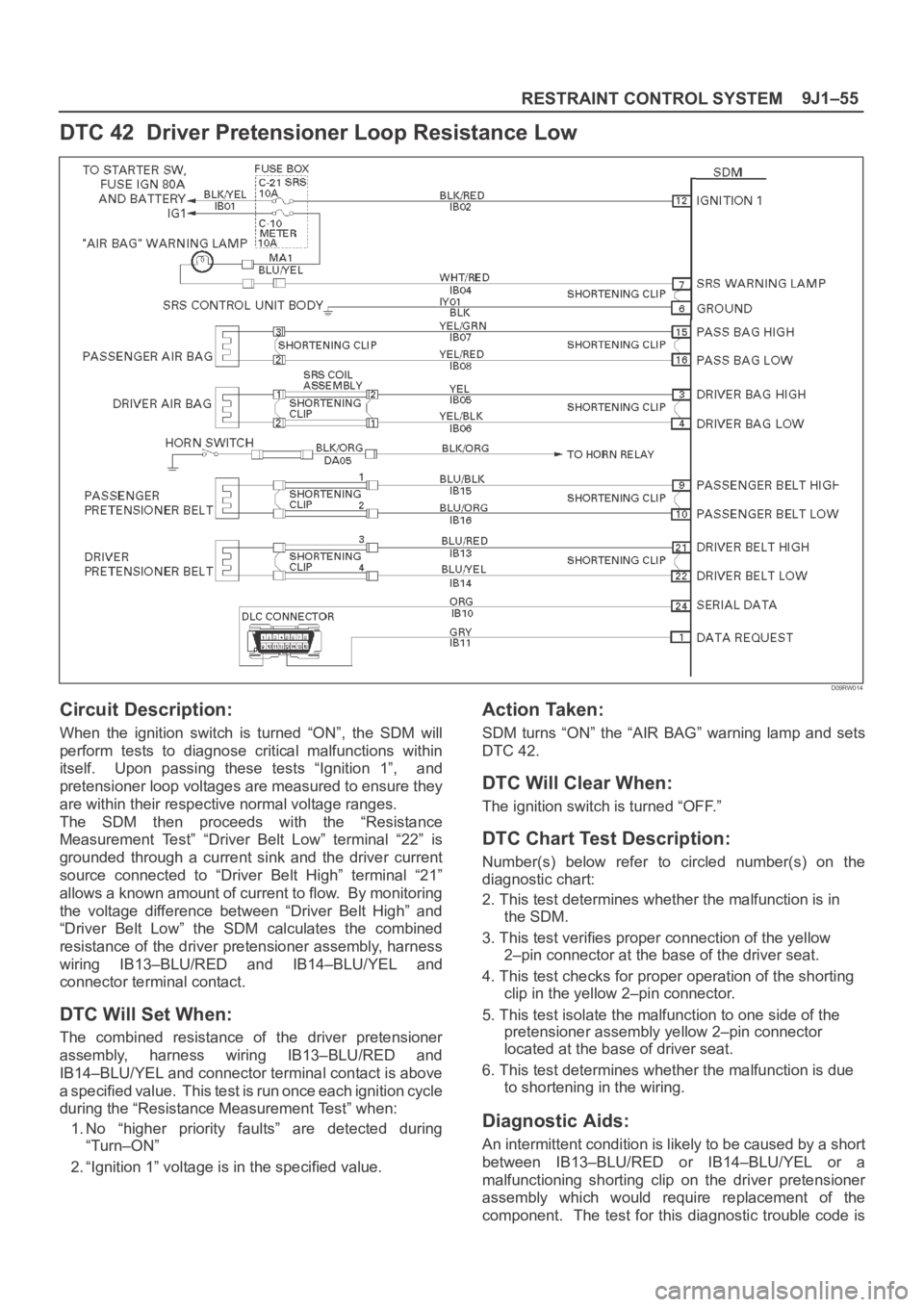
9J1–55
RESTRAINT CONTROL SYSTEM
DTC 42 Driver Pretensioner Loop Resistance Low
D09RW014
Circuit Description:
When the ignition switch is turned “ON”, the SDM will
perform tests to diagnose critical malfunctions within
itself. Upon passing these tests “Ignition 1”, and
pretensioner loop voltages are measured to ensure they
are within their respective normal voltage ranges.
The SDM then proceeds with the “Resistance
Measurement Test” “Driver Belt Low” terminal “22” is
grounded through a current sink and the driver current
source connected to “Driver Belt High” terminal “21”
allows a known amount of current to flow. By monitoring
the voltage difference between “Driver Belt High” and
“Driver Belt Low” the SDM calculates the combined
resistance of the driver pretensioner assembly, harness
wiring IB13–BLU/RED and IB14–BLU/YEL and
connector terminal contact.
DTC Will Set When:
The combined resistance of the driver pretensioner
assembly, harness wiring IB13–BLU/RED and
IB14–BLU/YEL and connector terminal contact is above
a specified value. This test is run once each ignition cycle
during the “Resistance Measurement Test” when:
1. No “higher priority faults” are detected during
“Turn–ON”
2. “Ignition 1” voltage is in the specified value.
Action Taken:
SDM turns “ON” the “AIR BAG” warning lamp and sets
DTC 42.
DTC Will Clear When:
The ignition switch is turned “OFF.”
DTC Chart Test Description:
Number(s) below refer to circled number(s) on the
diagnostic chart:
2. This test determines whether the malfunction is in
the SDM.
3. This test verifies proper connection of the yellow
2–pin connector at the base of the driver seat.
4. This test checks for proper operation of the shorting
clip in the yellow 2–pin connector.
5. This test isolate the malfunction to one side of the
pretensioner assembly yellow 2–pin connector
located at the base of driver seat.
6. This test determines whether the malfunction is due
to shortening in the wiring.
Diagnostic Aids:
An intermittent condition is likely to be caused by a short
between IB13–BLU/RED or IB14–BLU/YEL or a
malfunctioning shorting clip on the driver pretensioner
assembly which would require replacement of the
component. The test for this diagnostic trouble code is
Page 3543 of 6000
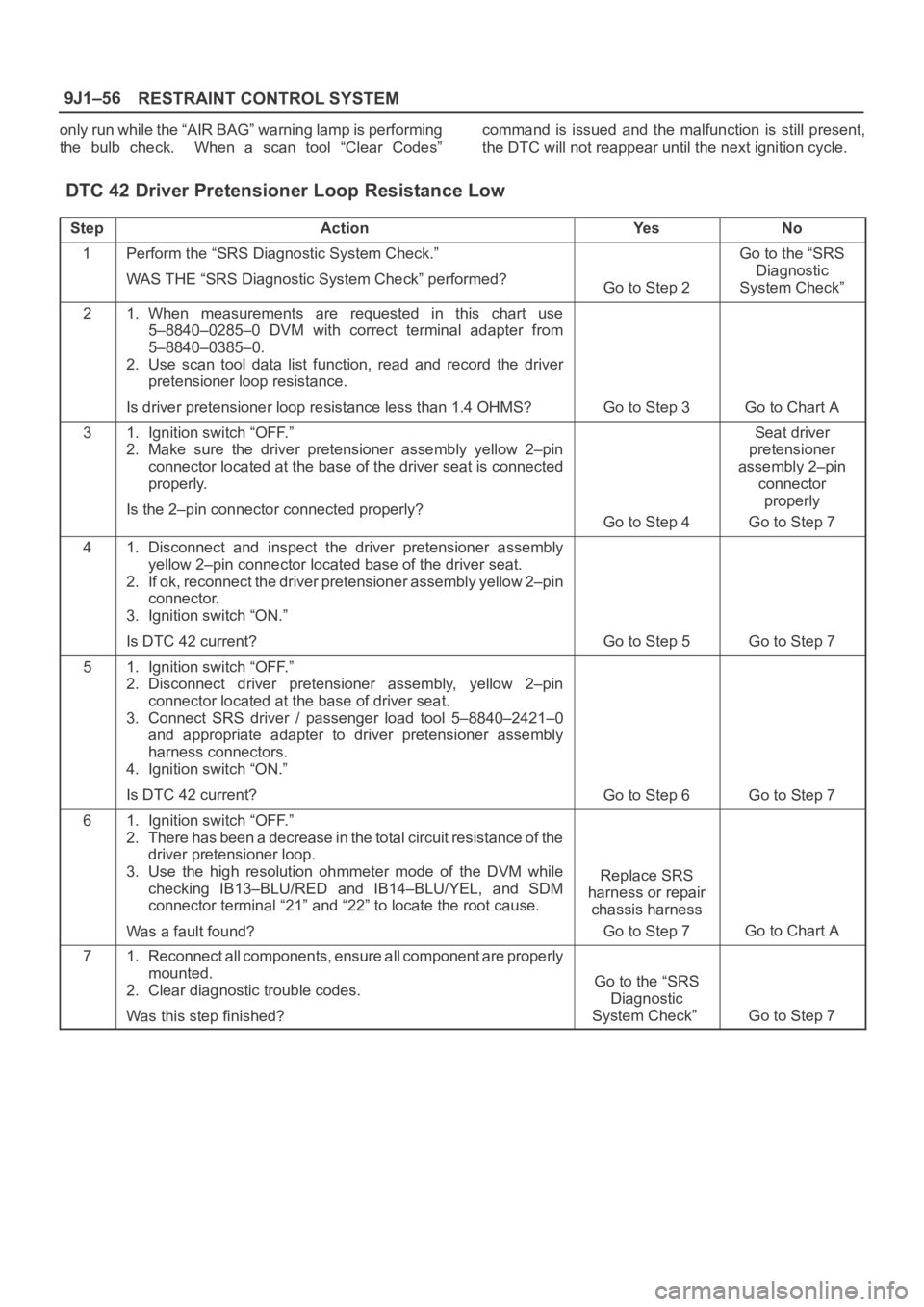
RESTRAINT CONTROL SYSTEM 9J1–56
only run while the “AIR BAG” warning lamp is performing
the bulb check. When a scan tool “Clear Codes”command is issued and the malfunction is still present,
the DTC will not reappear until the next ignition cycle.
DTC 42 Driver Pretensioner Loop Resistance Low
StepActionYe sNo
1Perform the “SRS Diagnostic System Check.”
WAS THE “SRS Diagnostic System Check” performed?
Go to Step 2
Go to the “SRS
Diagnostic
System Check”
21. When measurements are requested in this chart use
5–8840–0285–0 DVM with correct terminal adapter from
5–8840–0385–0.
2. Use scan tool data list function, read and record the driver
pretensioner loop resistance.
Is driver pretensioner loop resistance less than 1.4 OHMS?
Go to Step 3Go to Chart A
31. Ignition switch “OFF.”
2. Make sure the driver pretensioner assembly yellow 2–pin
connector located at the base of the driver seat is connected
properly.
Is the 2–pin connector connected properly?
Go to Step 4
Seat driver
pretensioner
assembly 2–pin
connector
properly
Go to Step 7
41. Disconnect and inspect the driver pretensioner assembly
yellow 2–pin connector located base of the driver seat.
2. If ok, reconnect the driver pretensioner assembly yellow 2–pin
connector.
3. Ignition switch “ON.”
Is DTC 42 current?
Go to Step 5Go to Step 7
51. Ignition switch “OFF.”
2. Disconnect driver pretensioner assembly, yellow 2–pin
connector located at the base of driver seat.
3. Connect SRS driver / passenger load tool 5–8840–2421–0
and appropriate adapter to driver pretensioner assembly
harness connectors.
4. Ignition switch “ON.”
Is DTC 42 current?
Go to Step 6Go to Step 7
61. Ignition switch “OFF.”
2. There has been a decrease in the total circuit resistance of the
driver pretensioner loop.
3. Use the high resolution ohmmeter mode of the DVM while
checking IB13–BLU/RED and IB14–BLU/YEL, and SDM
connector terminal “21” and “22” to locate the root cause.
Was a fault found?
Replace SRS
harness or repair
chassis harness
Go to Step 7
Go to Chart A
71. Reconnect all components, ensure all component are properly
mounted.
2. Clear diagnostic trouble codes.
Was this step finished?
Go to the “SRS
Diagnostic
System Check”
Go to Step 7
Page 3544 of 6000
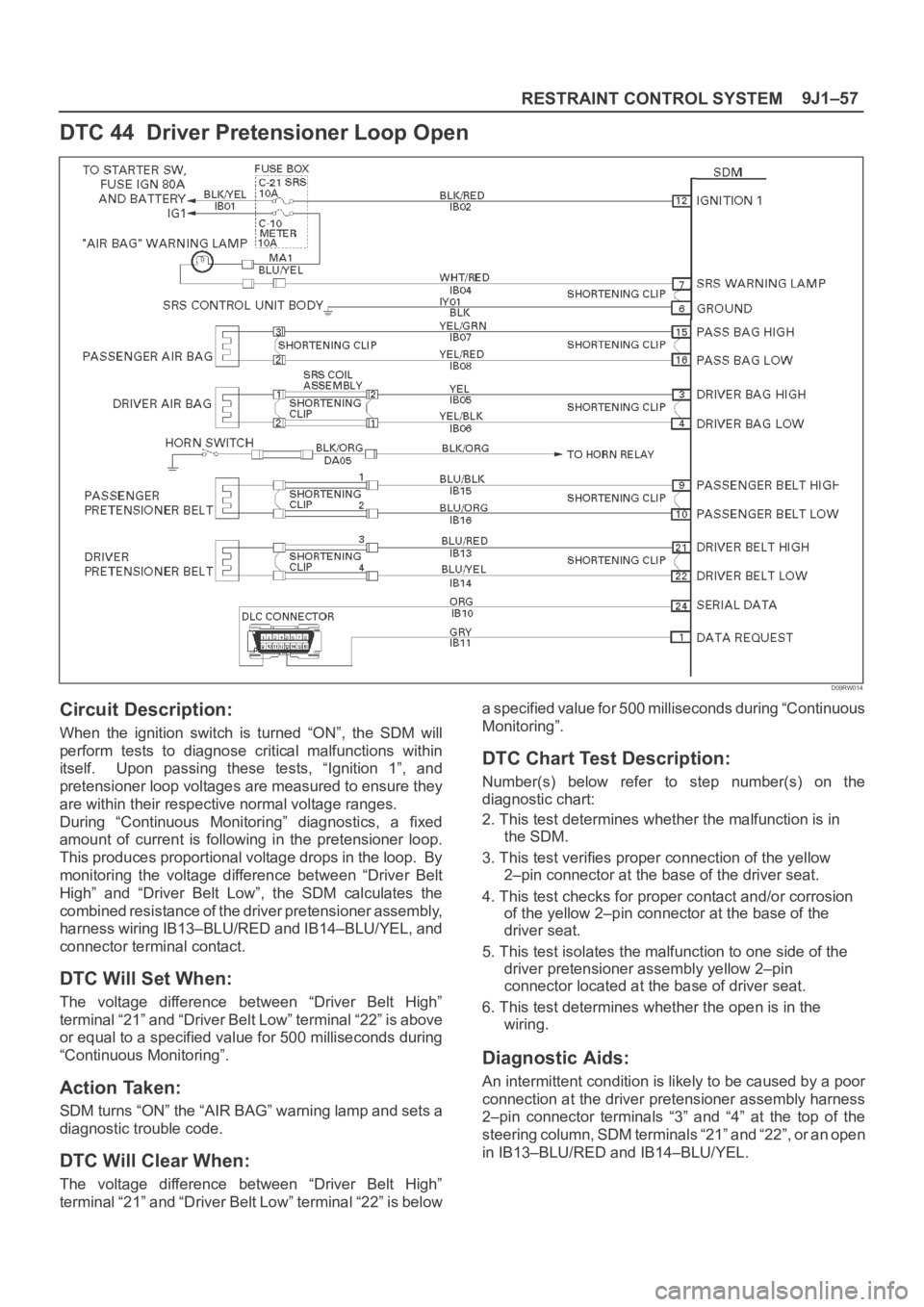
9J1–57
RESTRAINT CONTROL SYSTEM
DTC 44 Driver Pretensioner Loop Open
D09RW014
Circuit Description:
When the ignition switch is turned “ON”, the SDM will
perform tests to diagnose critical malfunctions within
itself. Upon passing these tests, “Ignition 1”, and
pretensioner loop voltages are measured to ensure they
are within their respective normal voltage ranges.
During “Continuous Monitoring” diagnostics, a fixed
amount of current is following in the pretensioner loop.
This produces proportional voltage drops in the loop. By
monitoring the voltage difference between “Driver Belt
High” and “Driver Belt Low”, the SDM calculates the
combined resistance of the driver pretensioner assembly,
harness wiring IB13–BLU/RED and IB14–BLU/YEL, and
connector terminal contact.
DTC Will Set When:
The voltage difference between “Driver Belt High”
terminal “21” and “Driver Belt Low” terminal “22” is above
or equal to a specified value for 500 milliseconds during
“Continuous Monitoring”.
Action Taken:
SDM turns “ON” the “AIR BAG” warning lamp and sets a
diagnostic trouble code.
DTC Will Clear When:
The voltage difference between “Driver Belt High”
terminal “21” and “Driver Belt Low” terminal “22” is belowa specified value for 500 milliseconds during “Continuous
Monitoring”.
DTC Chart Test Description:
Number(s) below refer to step number(s) on the
diagnostic chart:
2. This test determines whether the malfunction is in
the SDM.
3. This test verifies proper connection of the yellow
2–pin connector at the base of the driver seat.
4. This test checks for proper contact and/or corrosion
of the yellow 2–pin connector at the base of the
driver seat.
5. This test isolates the malfunction to one side of the
driver pretensioner assembly yellow 2–pin
connector located at the base of driver seat.
6. This test determines whether the open is in the
wiring.
Diagnostic Aids:
An intermittent condition is likely to be caused by a poor
connection at the driver pretensioner assembly harness
2–pin connector terminals “3” and “4” at the top of the
steering column, SDM terminals “21” and “22”, or an open
in IB13–BLU/RED and IB14–BLU/YEL.