Page 1809 of 6000
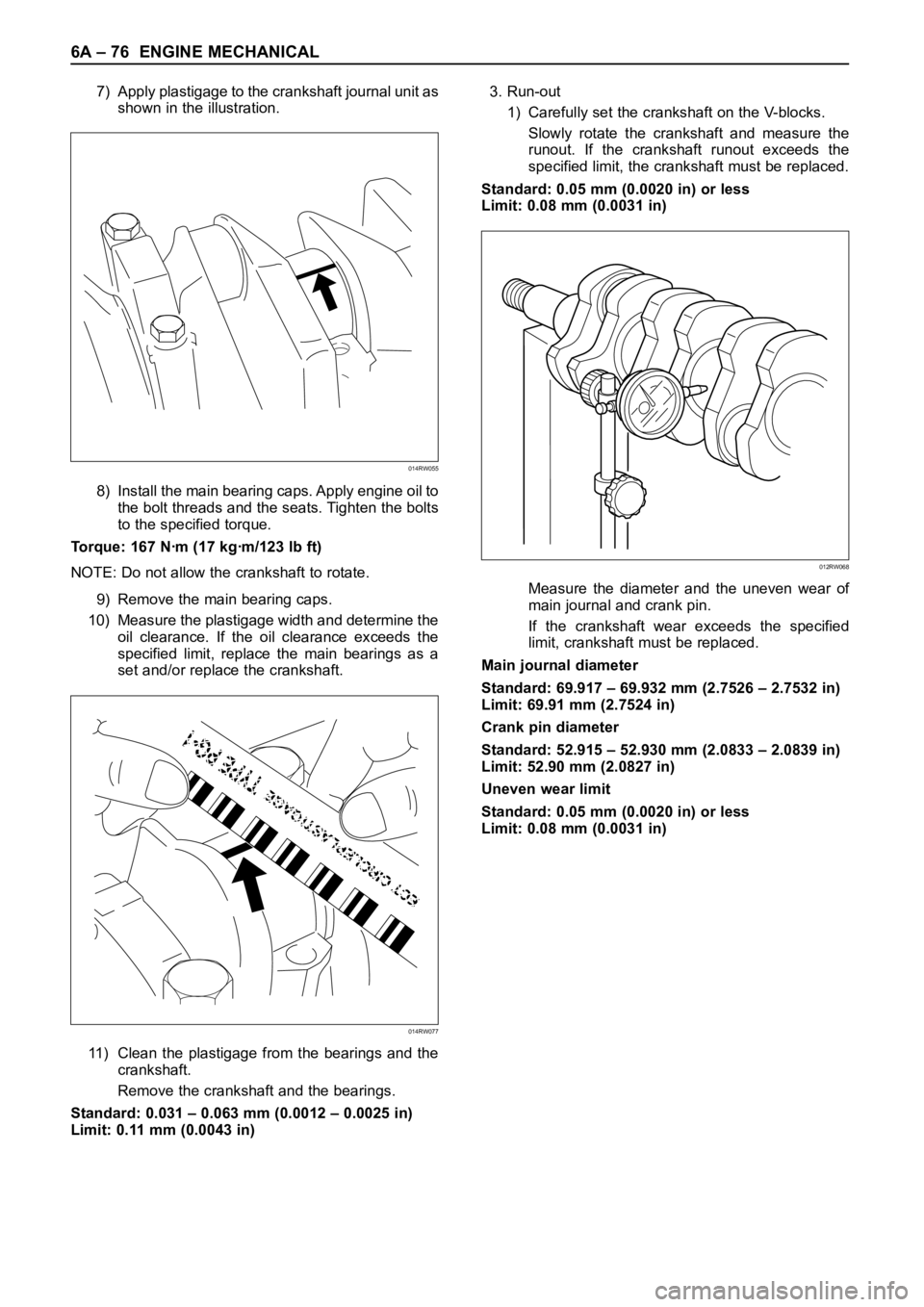
6A – 76 ENGINE MECHANICAL
7) Apply plastigage to the crankshaft journal unit as
shown in the illustration.
8) Install the main bearing caps. Apply engine oil to
the bolt threads and the seats. Tighten the bolts
to the specified torque.
Torque: 167 Nꞏm (17 kgꞏm/123 lb ft)
NOTE: Do not allow the crankshaft to rotate.
9) Remove the main bearing caps.
10) Measure the plastigage width and determine the
oil clearance. If the oil clearance exceeds the
specified limit, replace the main bearings as a
set and/or replace the crankshaft.
11) Clean the plastigage from the bearings and the
crankshaft.
Remove the crankshaft and the bearings.
Standard: 0.031 – 0.063 mm (0.0012 – 0.0025 in)
Limit: 0.11 mm (0.0043 in)3. Run-out
1) Carefully set the crankshaft on the V-blocks.
Slowly rotate the crankshaft and measure the
runout. If the crankshaft runout exceeds the
specified limit, the crankshaft must be replaced.
Standard: 0.05 mm (0.0020 in) or less
Limit: 0.08 mm (0.0031 in)
Measure the diameter and the uneven wear of
main journal and crank pin.
If the crankshaft wear exceeds the specified
limit, crankshaft must be replaced.
Main journal diameter
Standard: 69.917 – 69.932 mm (2.7526 – 2.7532 in)
Limit: 69.91 mm (2.7524 in)
Crank pin diameter
Standard: 52.915 – 52.930 mm (2.0833 – 2.0839 in)
Limit: 52.90 mm (2.0827 in)
Uneven wear limit
Standard: 0.05 mm (0.0020 in) or less
Limit: 0.08 mm (0.0031 in)
014RW055
014RW077
012RW068
Page 1810 of 6000
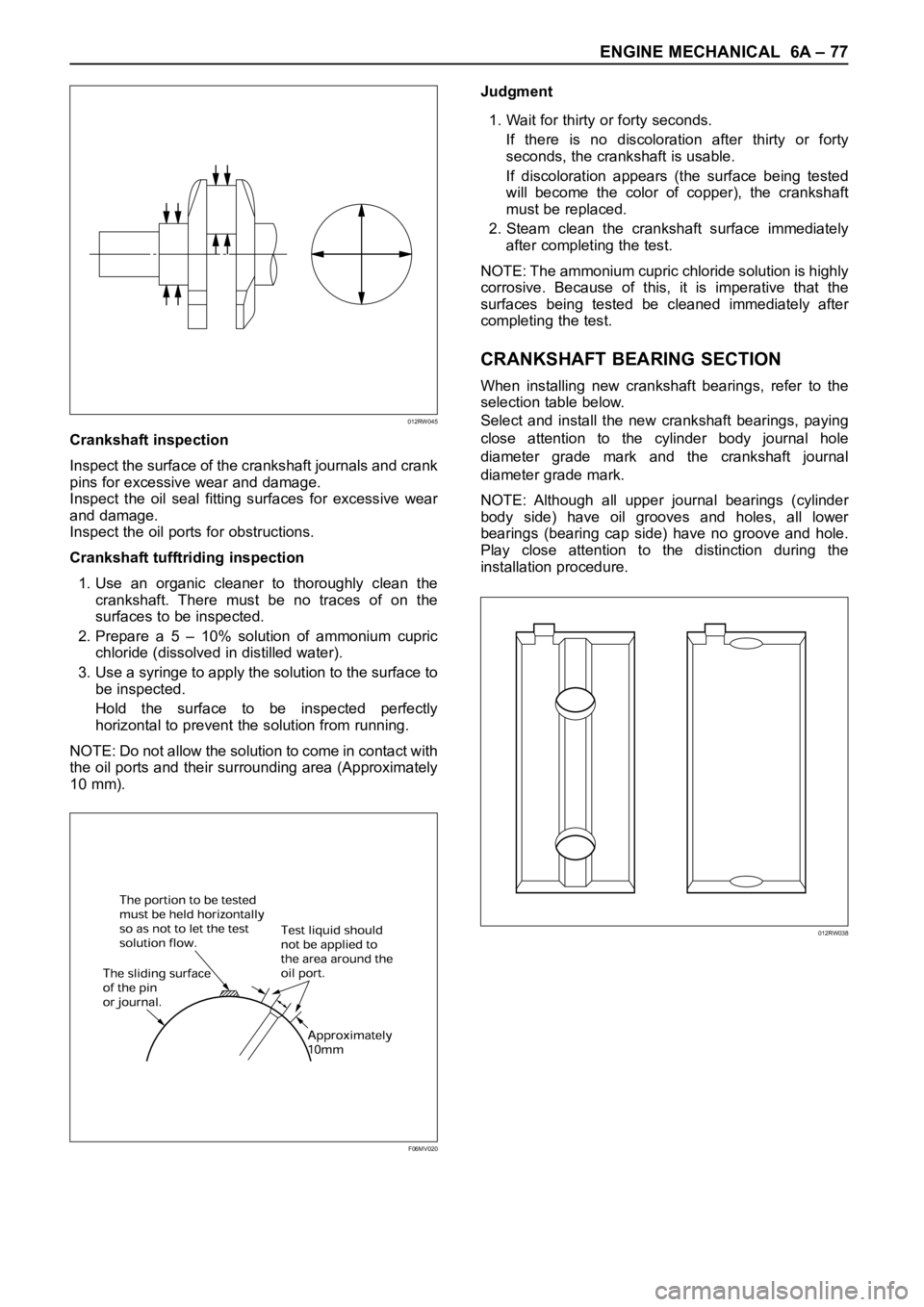
ENGINE MECHANICAL 6A – 77
Crankshaft inspection
Inspect the surface of the crankshaft journals and crank
pins for excessive wear and damage.
Inspect the oil seal fitting surfaces for excessive wear
and damage.
Inspect the oil ports for obstructions.
Crankshaft tufftriding inspection
1. Use an organic cleaner to thoroughly clean the
crankshaft. There must be no traces of on the
surfaces to be inspected.
2. Prepare a 5 – 10% solution of ammonium cupric
chloride (dissolved in distilled water).
3. Use a syringe to apply the solution to the surface to
be inspected.
Hold the surface to be inspected perfectly
horizontal to prevent the solution from running.
NOTE: Do not allow the solution to come in contact with
the oil ports and their surrounding area (Approximately
10 mm).Judgment
1. Wait for thirty or forty seconds.
If there is no discoloration after thirty or forty
seconds, the crankshaft is usable.
If discoloration appears (the surface being tested
will become the color of copper), the crankshaft
must be replaced.
2. Steam clean the crankshaft surface immediately
after completing the test.
NOTE: The ammonium cupric chloride solution is highly
corrosive. Because of this, it is imperative that the
surfaces being tested be cleaned immediately after
completing the test.
CRANKSHAFT BEARING SECTION
When installing new crankshaft bearings, refer to the
selection table below.
Select and install the new crankshaft bearings, paying
close attention to the cylinder body journal hole
diameter grade mark and the crankshaft journal
diameter grade mark.
NOTE: Although all upper journal bearings (cylinder
body side) have oil grooves and holes, all lower
bearings (bearing cap side) have no groove and hole.
Play close attention to the distinction during the
installation procedure.
012RW045
F06MV020
012RW038
Page 1811 of 6000
6A – 78 ENGINE MECHANICAL
Crankshaft Bearing Bore Grade Mark Position
Crankshaft bearing bore grade marks
1or 2are
stamped on the rear right hand side of the cylinder
body.
Example:
No. 1 Bearing No. 2 Bearing No. 3 Bearing No. 4 Bearing No. 5 Bearing
Housing Housing Housing Housing Housing
Legend
(1) No. 1 Main bearing bore grade
(2) No. 2 Main bearing bore grade
(3) No. 3 Main bearing bore grade
(4) No. 4 Main bearing bore grade
(5) No. 5 Main bearing bore gradeCrankshaft Journal Grade Mark Position
The crankshaft journal grade marks (1 or –) are
stamped on each crankshaft journal wave.
The crankshaft journal and bearing clearance must be
the same for each position after installation of the
crankshaft and the crankshaft bearings.
Legend
(1) Crankshaft journal outside diameter grade
12112
1
11122 234 5
1
2
3
4
5
012RW114
1
015RW078
012RW069
Page 1812 of 6000
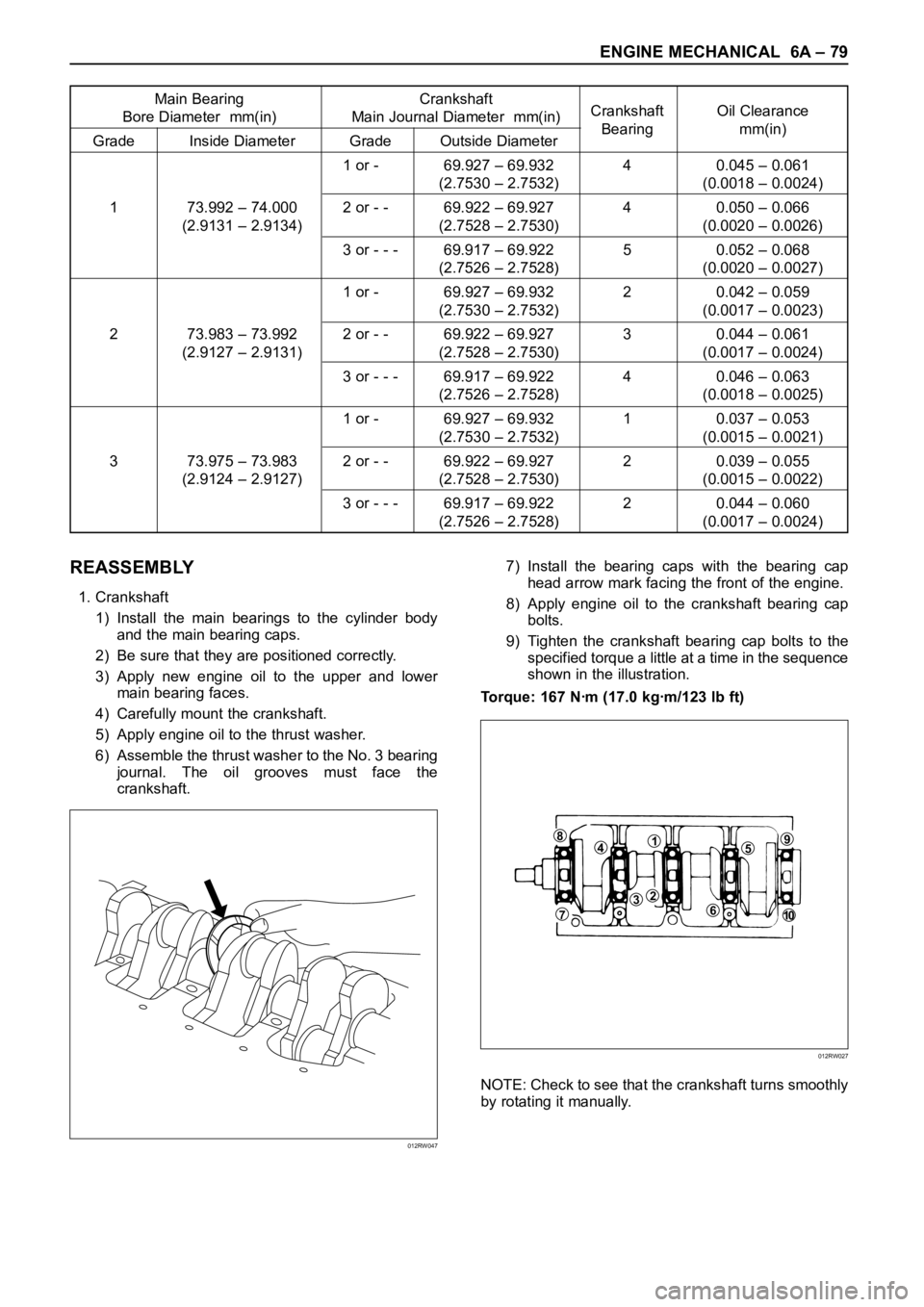
ENGINE MECHANICAL 6A – 79
Main Bearing Crankshaft
Bore Diameter mm(in) Main Journal Diameter mm(in)Crankshaft Oil Clearance
Grade Inside Diameter Grade Outside DiameterBearing mm(in)
1 or - 69.927 – 69.932 4 0.045 – 0.061
(2.7530 – 2.7532) (0.0018 – 0.0024)
1 73.992 – 74.000 2 or - - 69.922 – 69.927 4 0.050 – 0.066
(2.9131 – 2.9134) (2.7528 – 2.7530) (0.0020 – 0.0026)
3 or - - - 69.917 – 69.922 5 0.052 – 0.068
(2.7526 – 2.7528) (0.0020 – 0.0027)
1 or - 69.927 – 69.932 2 0.042 – 0.059
(2.7530 – 2.7532) (0.0017 – 0.0023)
2 73.983 – 73.992 2 or - - 69.922 – 69.927 3 0.044 – 0.061
(2.9127 – 2.9131) (2.7528 – 2.7530) (0.0017 – 0.0024)
3 or - - - 69.917 – 69.922 4 0.046 – 0.063
(2.7526 – 2.7528) (0.0018 – 0.0025)
1 or - 69.927 – 69.932 1 0.037 – 0.053
(2.7530 – 2.7532) (0.0015 – 0.0021)
3 73.975 – 73.983 2 or - - 69.922 – 69.927 2 0.039 – 0.055
(2.9124 – 2.9127) (2.7528 – 2.7530) (0.0015 – 0.0022)
3 or - - - 69.917 – 69.922 2 0.044 – 0.060
(2.7526 – 2.7528) (0.0017 – 0.0024)
REASSEMBLY
1. Crankshaft
1) Install the main bearings to the cylinder body
and the main bearing caps.
2) Be sure that they are positioned correctly.
3) Apply new engine oil to the upper and lower
main bearing faces.
4) Carefully mount the crankshaft.
5) Apply engine oil to the thrust washer.
6) Assemble the thrust washer to the No. 3 bearing
journal. The oil grooves must face the
crankshaft.7) Install the bearing caps with the bearing cap
head arrow mark facing the front of the engine.
8) Apply engine oil to the crankshaft bearing cap
bolts.
9) Tighten the crankshaft bearing cap bolts to the
specified torque a little at a time in the sequence
shown in the illustration.
Torque: 167 Nꞏm (17.0 kgꞏm/123 lb ft)
NOTE: Check to see that the crankshaft turns smoothly
by rotating it manually.
012RW047
84159
610
237
012RW027
Page 1813 of 6000
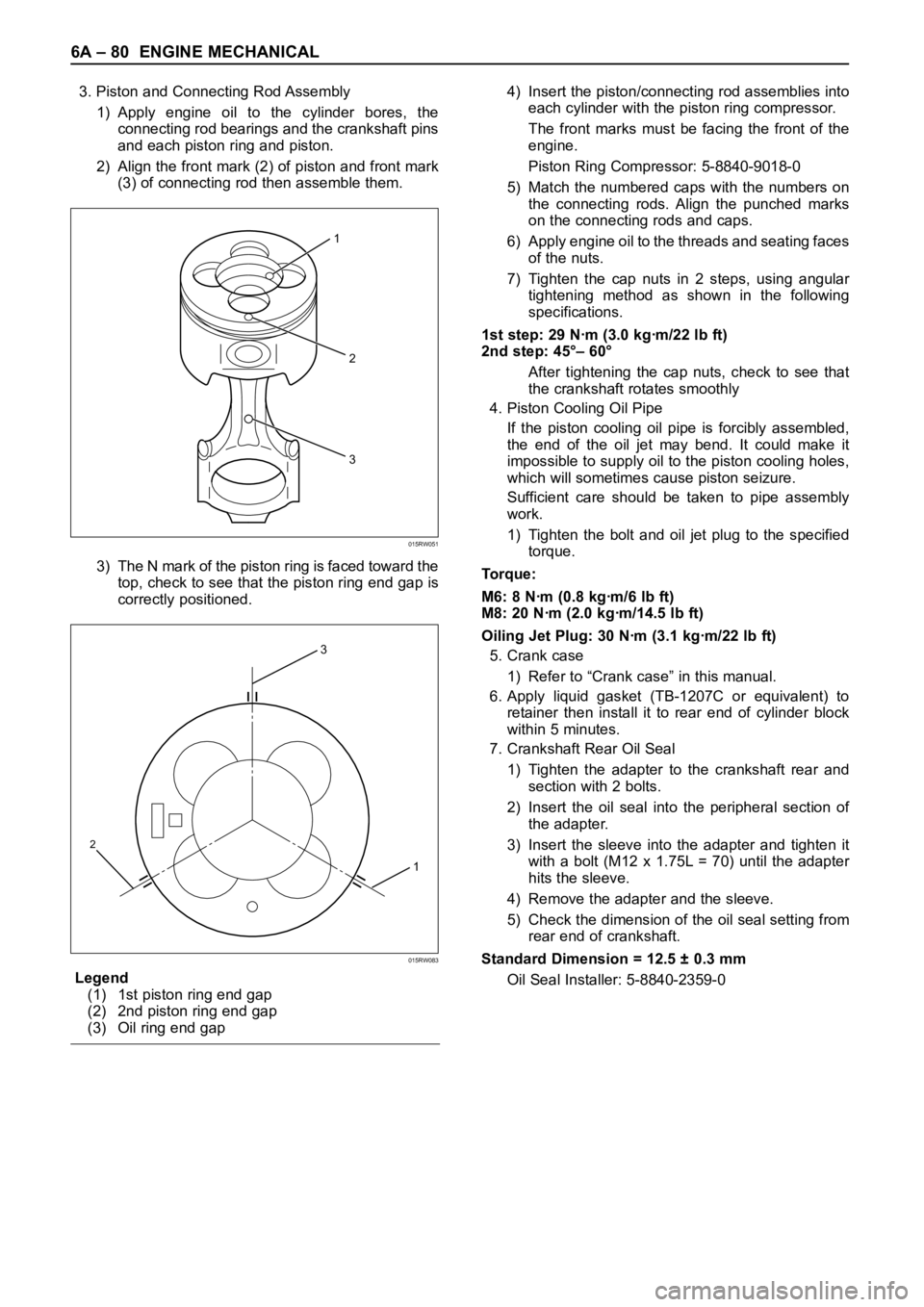
6A – 80 ENGINE MECHANICAL
3. Piston and Connecting Rod Assembly
1) Apply engine oil to the cylinder bores, the
connecting rod bearings and the crankshaft pins
and each piston ring and piston.
2) Align the front mark (2) of piston and front mark
(3) of connecting rod then assemble them.
3) The N mark of the piston ring is faced toward the
top, check to see that the piston ring end gap is
correctly positioned.
Legend
(1) 1st piston ring end gap
(2) 2nd piston ring end gap
(3) Oil ring end gap4) Insert the piston/connecting rod assemblies into
each cylinder with the piston ring compressor.
The front marks must be facing the front of the
engine.
Piston Ring Compressor: 5-8840-9018-0
5) Match the numbered caps with the numbers on
the connecting rods. Align the punched marks
on the connecting rods and caps.
6) Apply engine oil to the threads and seating faces
of the nuts.
7) Tighten the cap nuts in 2 steps, using angular
tightening method as shown in the following
specifications.
1st step: 29 Nꞏm (3.0 kgꞏm/22 lb ft)
2nd step: 45°– 60°
After tightening the cap nuts, check to see that
the crankshaft rotates smoothly
4. Piston Cooling Oil Pipe
If the piston cooling oil pipe is forcibly assembled,
the end of the oil jet may bend. It could make it
impossible to supply oil to the piston cooling holes,
which will sometimes cause piston seizure.
Sufficient care should be taken to pipe assembly
work.
1) Tighten the bolt and oil jet plug to the specified
torque.
Torque:
M6: 8 Nꞏm (0.8 kgꞏm/6 lb ft)
M8: 20 Nꞏm (2.0 kgꞏm/14.5 lb ft)
Oiling Jet Plug: 30 Nꞏm (3.1 kgꞏm/22 lb ft)
5. Crank case
1) Refer to “Crank case” in this manual.
6. Apply liquid gasket (TB-1207C or equivalent) to
retainer then install it to rear end of cylinder block
within 5 minutes.
7. Crankshaft Rear Oil Seal
1) Tighten the adapter to the crankshaft rear and
section with 2 bolts.
2) Insert the oil seal into the peripheral section of
the adapter.
3) Insert the sleeve into the adapter and tighten it
with a bolt (M12 x 1.75L = 70) until the adapter
hits the sleeve.
4) Remove the adapter and the sleeve.
5) Check the dimension of the oil seal setting from
rear end of crankshaft.
Standard Dimension = 12.5 ± 0.3 mm
Oil Seal Installer: 5-8840-2359-0
2
3
1
015RW051
3
1
2
015RW083
Page 1814 of 6000
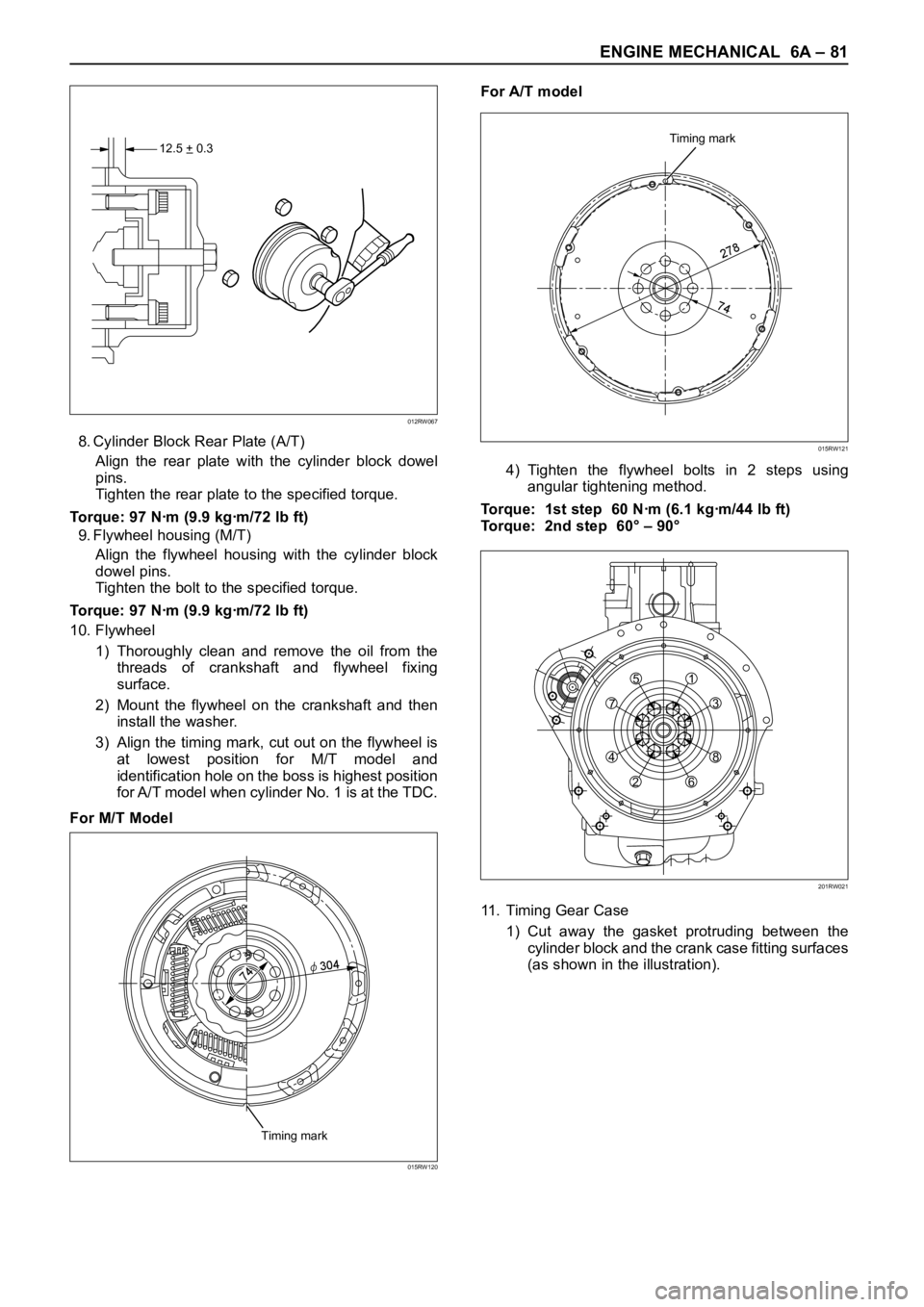
ENGINE MECHANICAL 6A – 81
8. Cylinder Block Rear Plate (A/T)
Align the rear plate with the cylinder block dowel
pins.
Tighten the rear plate to the specified torque.
Torque: 97 Nꞏm (9.9 kgꞏm/72 lb ft)
9. Flywheel housing (M/T)
Align the flywheel housing with the cylinder block
dowel pins.
Tighten the bolt to the specified torque.
Torque: 97 Nꞏm (9.9 kgꞏm/72 lb ft)
10. Flywheel
1) Thoroughly clean and remove the oil from the
threads of crankshaft and flywheel fixing
surface.
2) Mount the flywheel on the crankshaft and then
install the washer.
3) Align the timing mark, cut out on the flywheel is
at lowest position for M/T model and
identification hole on the boss is highest position
for A/T model when cylinder No. 1 is at the TDC.
For M/T ModelFor A/T model
4) Tighten the flywheel bolts in 2 steps using
angular tightening method.
Torque: 1st step 60 Nꞏm (6.1 kgꞏm/44 lb ft)
Torque: 2nd step 60° – 90°
11. Timing Gear Case
1) Cut away the gasket protruding between the
cylinder block and the crank case fitting surfaces
(as shown in the illustration).
12.5 + 0.3–
012RW067
Timing mark
2
78
74
015RW121
Timing mark
7
4φ
304
015RW120
751
3
8
6 2 4
201RW021
Page 1815 of 6000
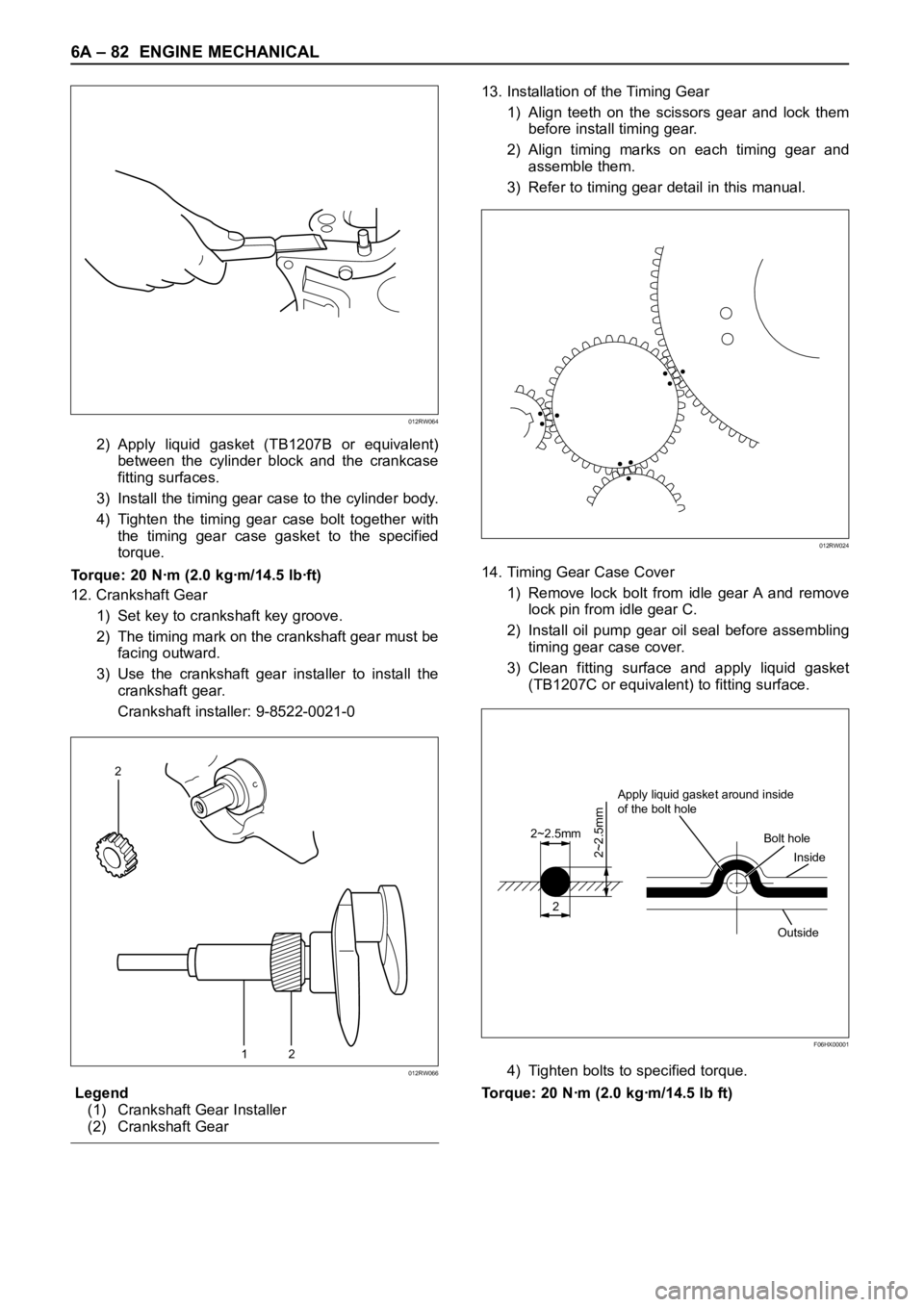
6A – 82 ENGINE MECHANICAL
2) Apply liquid gasket (TB1207B or equivalent)
between the cylinder block and the crankcase
fitting surfaces.
3) Install the timing gear case to the cylinder body.
4) Tighten the timing gear case bolt together with
the timing gear case gasket to the specified
torque.
Torque: 20 Nꞏm (2.0 kgꞏm/14.5 lbꞏft)
12. Crankshaft Gear
1) Set key to crankshaft key groove.
2) The timing mark on the crankshaft gear must be
facing outward.
3) Use the crankshaft gear installer to install the
crankshaft gear.
Crankshaft installer: 9-8522-0021-0
Legend
(1) Crankshaft Gear Installer
(2) Crankshaft Gear13. Installation of the Timing Gear
1) Align teeth on the scissors gear and lock them
before install timing gear.
2) Align timing marks on each timing gear and
assemble them.
3) Refer to timing gear detail in this manual.
14. Timing Gear Case Cover
1) Remove lock bolt from idle gear A and remove
lock pin from idle gear C.
2) Install oil pump gear oil seal before assembling
timing gear case cover.
3) Clean fitting surface and apply liquid gasket
(TB1207C or equivalent) to fitting surface.
4) Tighten bolts to specified torque.
Torque: 20 Nꞏm (2.0 kgꞏm/14.5 lb ft)
12
2
012RW066
2
2~2.5mm
2~2.5mm
Apply liquid gasket around inside
of the bolt hole
Bolt hole
Inside
Outside
F06HX00001
012RW024
012RW064
Page 1816 of 6000
15. Crankshaft Front Oil Seal
1) Set oil seal with special tool.
2) Install front oil seal to timing gear case cover.
Crankshaft Front Oil Seal Installer: 5-8840-2061-0
3) Remove special tool and check oil seal position
from front surface of timing gear case.
Oil Seal Position: 0.5 – 2.5 mm (0.0197 – 0.0984 in)
16. Cylinder Head
1) Refer to “Cylinder head” in this manual.
ENGINE MECHANICAL 6A – 83
015RW074