Page 529 of 6000
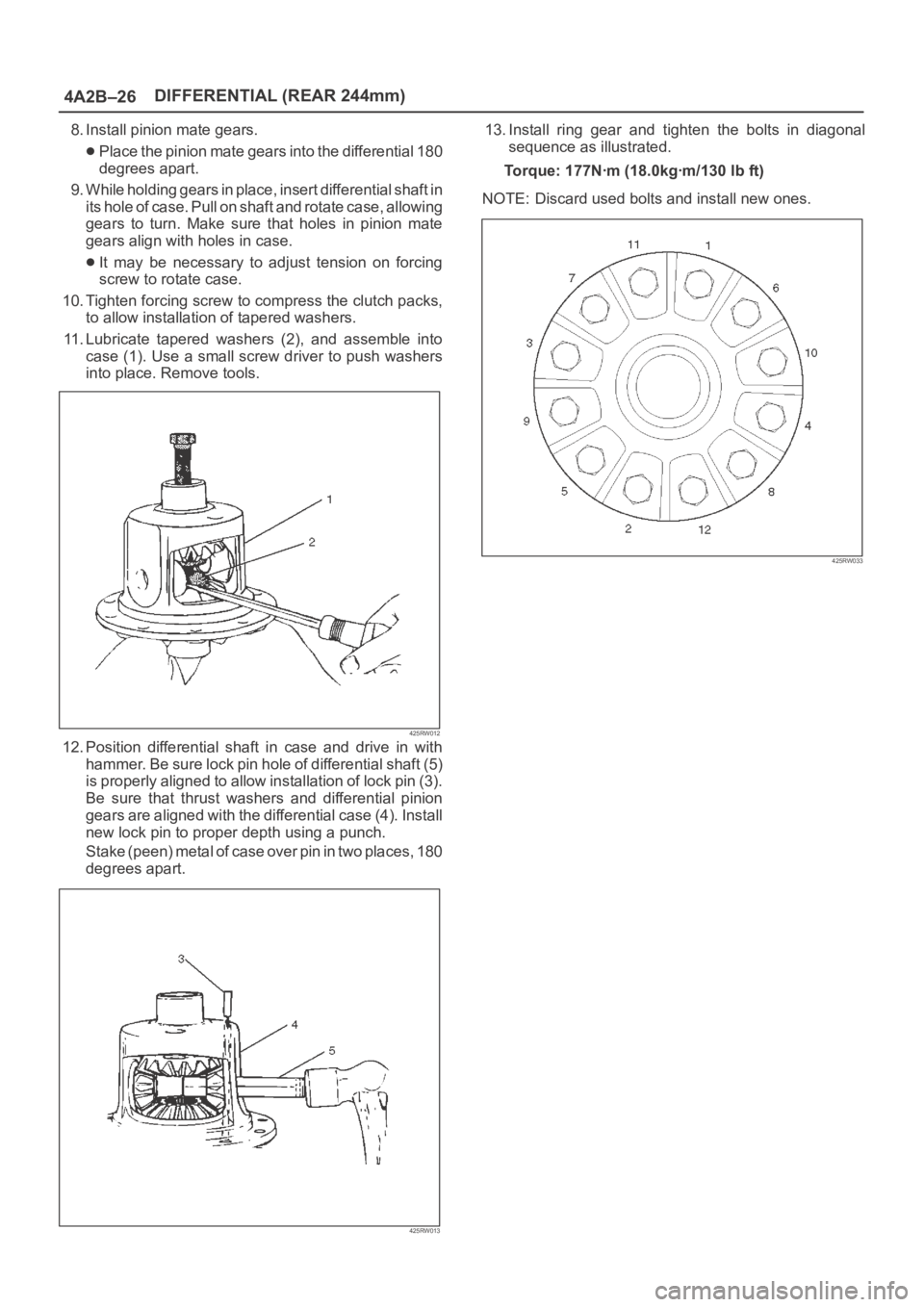
4A2B–26DIFFERENTIAL (REAR 244mm)
8. Install pinion mate gears.
Place the pinion mate gears into the differential 180
degrees apart.
9. While holding gears in place, insert differential shaft in
its hole of case. Pull on shaft and rotate case, allowing
gears to turn. Make sure that holes in pinion mate
gears align with holes in case.
It may be necessary to adjust tension on forcing
screw to rotate case.
10. Tighten forcing screw to compress the clutch packs,
to allow installation of tapered washers.
11. Lubricate tapered washers (2), and assemble into
case (1). Use a small screw driver to push washers
into place. Remove tools.
425RW012
12. Position differential shaft in case and drive in with
hammer. Be sure lock pin hole of differential shaft (5)
is properly aligned to allow installation of lock pin (3).
Be sure that thrust washers and differential pinion
gears are aligned with the differential case (4). Install
new lock pin to proper depth using a punch.
S t a k e ( p e e n ) m e t a l o f c a s e o v e r p i n i n t w o p l a c e s , 1 8 0
degrees apart.
425RW013
13. Install ring gear and tighten the bolts in diagonal
sequence as illustrated.
Torque: 177Nꞏm (18.0kgꞏm/130 lb ft)
NOTE: Discard used bolts and install new ones.
425RW033
Page 530 of 6000
DIFFERENTIAL (REAR 244mm)
4A2B–27
Main Data and Specifications
General Specifications
Rear axle
Ty p eBanjo, Semi–floating
Rear axle Size244 mm (9.61 in)
Gear typeHypoid
Gear ratio (to 1)4.100(6VE1 with A/T)
4.300(6VE1 with M/T,4JX1)
Differential typeTwo pinion
Lubricant GradeGL–5: (Standard differential)
GL–5, LSD: (Limited slip differential)
Locking Differential Lubricant80W90 GL–5
(USE Limited Slip Differential Gear Lubricant or Friction
Modifier Organic Additive)
Capacity3.0 liter (2.6 Imp qt/3.2 US qt)
Page 531 of 6000
4A2B–28DIFFERENTIAL (REAR 244mm)
Torque Specifications
E04RW019
Page 532 of 6000
DIFFERENTIAL (REAR 244mm)
4A2B–29
Special Tools
ILLUSTRATIONTOOL NO.
TOOL NAME
5–8840–2294–0
(J–39210)
Installer; Axle shaft inner
seal
5–8840–0133–0
(J–8614–01)
Pinion flange holder
5–8840–2165–0
(J–37263)
Installer; Pinion oil seal
5–8840–2029–0
(J–42832)
Holding fixture
5–8840–0003–0
(J–3289–20)
Holding fixture base
5–8840–2587–0
(J–42379)
Remover; Bearing
ILLUSTRATIONTOOL NO.
TOOL NAME
5–8840–2576–0
(J–8107–3)
Adapter; Side bearing
plug
5–8840–0008–0
(J–8611–01)
Installer; Outer bearing
outer race
5–8840–0007–0
(J–8092)
Grip
5–8840–2571–0
(J–42831)
Installer; Inner bearing
outer race
5–8840–2575–0
(J–42824)
Pilot;Outer
5–8840–0127–0
(J–21777–43)
Nut & Stud
Page 533 of 6000
4A2B–30DIFFERENTIAL (REAR 244mm)
ILLUSTRATIONTOOL NO.
TOOL NAME
5–8840–2573–0
(J–42827)
Pilot;Inner
5–8840–2572–0
(J–42826)
Gage plate
5–8840–0126–0
(J–8001)
Dial indicator
5–8840–2577–0
(J–42825)
Disc (2 required)
5–8840–0128–0
(J–23597–1)
Arbor
5–8840–2574–0
(J–42828)
Installer; Pinion bearing
ILLUSTRATIONTOOL NO.
TOOL NAME
5–8840–2293–0
(J–39209)
Punch; End nut lock
5–8840–2570–0
(J–42829)
Installer; Side bearing
5–8840–2323–0
(J–39602)
Remover; Outer bearing
5–8840–2586–0
(J–39858)
Clutch pack unloading
tool kit Includes
Screw cap, Cap and
Forcing screw
Page 534 of 6000
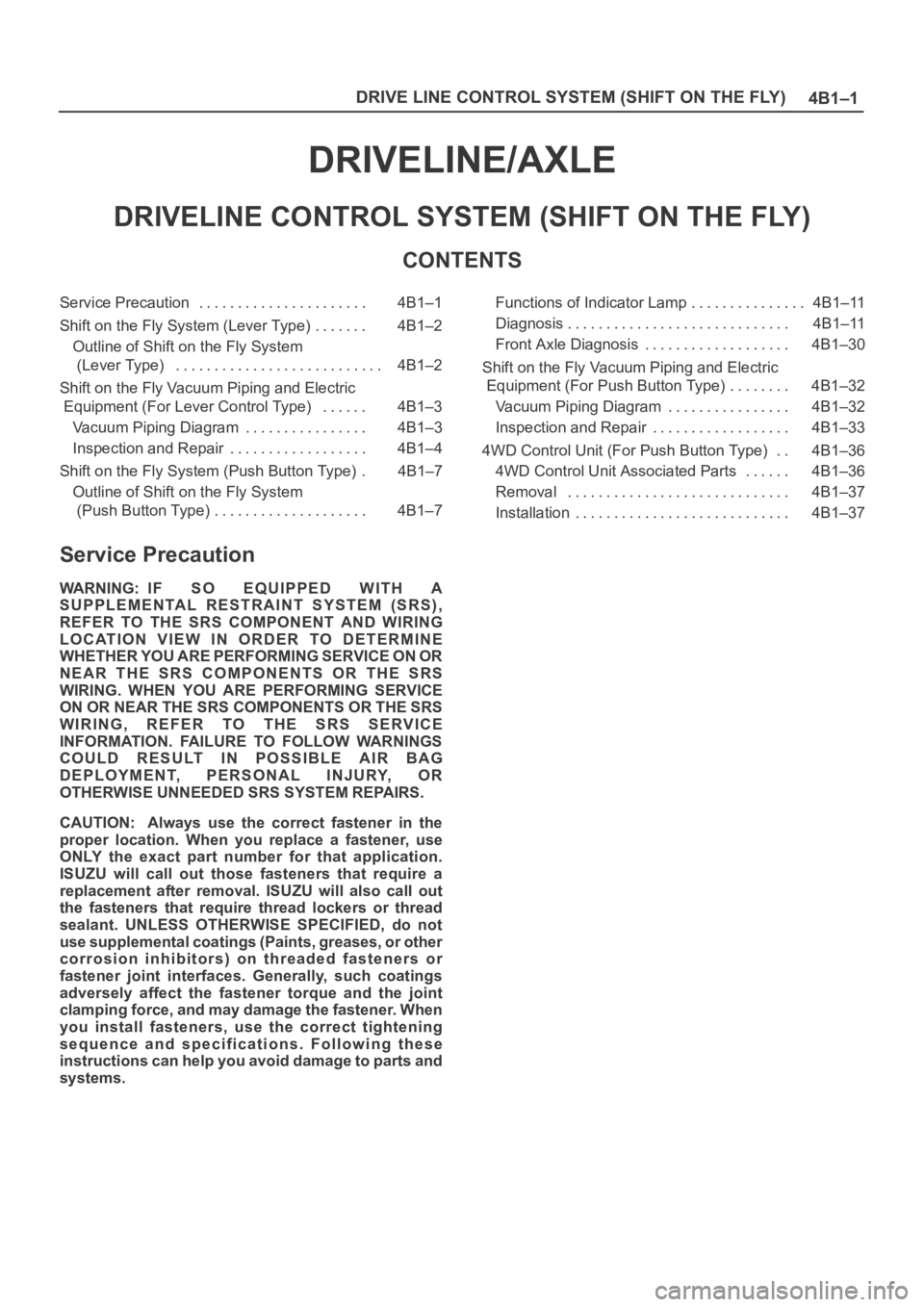
4B1–1 DRIVE LINE CONTROL SYSTEM (SHIFT ON THE FLY)
DRIVELINE/AXLE
DRIVELINE CONTROL SYSTEM (SHIFT ON THE FLY)
CONTENTS
Service Precaution 4B1–1. . . . . . . . . . . . . . . . . . . . . .
Shift on the Fly System (Lever Type) 4B1–2. . . . . . .
Outline of Shift on the Fly System
(Lever Type) 4B1–2. . . . . . . . . . . . . . . . . . . . . . . . . . .
Shift on the Fly Vacuum Piping and Electric
Equipment (For Lever Control Type) 4B1–3. . . . . .
Vacuum Piping Diagram 4B1–3. . . . . . . . . . . . . . . .
Inspection and Repair 4B1–4. . . . . . . . . . . . . . . . . .
Shift on the Fly System (Push Button Type) 4B1–7.
Outline of Shift on the Fly System
(Push Button Type) 4B1–7. . . . . . . . . . . . . . . . . . . . Functions of Indicator Lamp 4B1–11. . . . . . . . . . . . . . .
Diagnosis 4B1–11. . . . . . . . . . . . . . . . . . . . . . . . . . . . .
Front Axle Diagnosis 4B1–30. . . . . . . . . . . . . . . . . . .
Shift on the Fly Vacuum Piping and Electric
Equipment (For Push Button Type) 4B1–32. . . . . . . .
Vacuum Piping Diagram 4B1–32. . . . . . . . . . . . . . . .
Inspection and Repair 4B1–33. . . . . . . . . . . . . . . . . .
4WD Control Unit (For Push Button Type) 4B1–36. .
4WD Control Unit Associated Parts 4B1–36. . . . . .
Removal 4B1–37. . . . . . . . . . . . . . . . . . . . . . . . . . . . .
Installation 4B1–37. . . . . . . . . . . . . . . . . . . . . . . . . . . .
Service Precaution
WARNING: IF SO EQUIPPED WITH A
SUPPLEMENTAL RESTRAINT SYSTEM (SRS),
REFER TO THE SRS COMPONENT AND WIRING
LOCATION VIEW IN ORDER TO DETERMINE
WHETHER YOU ARE PERFORMING SERVICE ON OR
NEAR THE SRS COMPONENTS OR THE SRS
WIRING. WHEN YOU ARE PERFORMING SERVICE
ON OR NEAR THE SRS COMPONENTS OR THE SRS
WIRING, REFER TO THE SRS SERVICE
INFORMATION. FAILURE TO FOLLOW WARNINGS
COULD RESULT IN POSSIBLE AIR BAG
DEPLOYMENT, PERSONAL INJURY, OR
OTHERWISE UNNEEDED SRS SYSTEM REPAIRS.
CAUTION: Always use the correct fastener in the
proper location. When you replace a fastener, use
ONLY the exact part number for that application.
ISUZU will call out those fasteners that require a
replacement after removal. ISUZU will also call out
the fasteners that require thread lockers or thread
sealant. UNLESS OTHERWISE SPECIFIED, do not
use supplemental coatings (Paints, greases, or other
corrosion inhibitors) on threaded fasteners or
fastener joint interfaces. Generally, such coatings
adversely affect the fastener torque and the joint
clamping force, and may damage the fastener. When
you install fasteners, use the correct tightening
sequence and specifications. Following these
instructions can help you avoid damage to parts and
systems.
Page 535 of 6000
4B1–2
DRIVE LINE CONTROL SYSTEM (SHIFT ON THE FLY)
Shift on the Fly System (Lever Type)
Outline of Shift on the Fly System
(Lever Type)
The shift on the fly system (Lever type) switches between
2 wheel drive (2WD) and 4 wheel drive (4WD) by driver’s
shifting the transfer control lever on the floor.
This system controls below operations.
1. Connecting front wheels to, and disconnecting them
from, the front axles by vacuum actuator.
2. Indicator on instrument panel.
3. 4WD signal to Electronic Hydraulic Control Unit for
brake system (If anti–lock brake system is equipped).
Page 536 of 6000
4B1–3 DRIVE LINE CONTROL SYSTEM (SHIFT ON THE FLY)
Shift on the Fly Vacuum Piping and Electric Equipment
(For Lever Control Type)
Vacuum Piping Diagram
C04RW015
VSV Assembly, Actuator Assembly
412RS032
Vacuum Tank
412RS033