Page 4409 of 6000
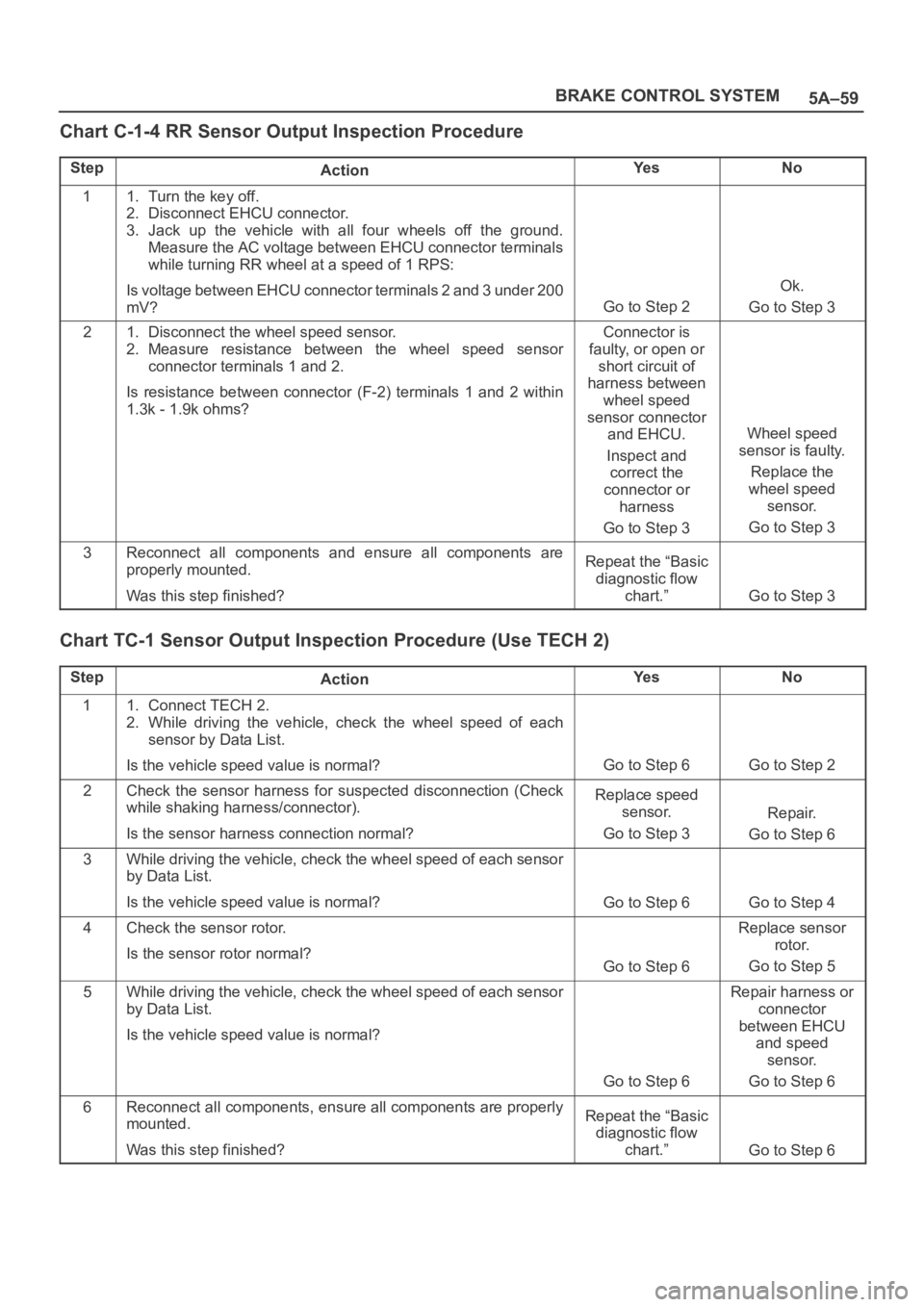
5A–59 BRAKE CONTROL SYSTEM
Chart C-1-4 RR Sensor Output Inspection Procedure
StepActionYe sNo
11. Turn the key off.
2. Disconnect EHCU connector.
3. Jack up the vehicle with all four wheels off the ground.
Measure the AC voltage between EHCU connector terminals
while turning RR wheel at a speed of 1 RPS:
Is voltage between EHCU connector terminals 2 and 3 under 200
mV?
Go to Step 2
Ok.
Go to Step 3
21. Disconnect the wheel speed sensor.
2. Measure resistance between the wheel speed sensor
connector terminals 1 and 2.
Is resistance between connector (F-2) terminals 1 and 2 within
1.3k - 1.9k ohms?Connector is
faulty, or open or
short circuit of
harness between
wheel speed
sensor connector
and EHCU.
Inspect and
correct the
connector or
harness
Go to Step 3
Wheel speed
sensor is faulty.
Replace the
wheel speed
sensor.
Go to Step 3
3Reconnect all components and ensure all components are
properly mounted.
Was this step finished?Repeat the “Basic
diagnostic flow
chart.”
Go to Step 3
Chart TC-1 Sensor Output Inspection Procedure (Use TECH 2)
StepActionYe sNo
11. Connect TECH 2.
2. While driving the vehicle, check the wheel speed of each
sensor by Data List.
Is the vehicle speed value is normal?
Go to Step 6Go to Step 2
2Check the sensor harness for suspected disconnection (Check
while shaking harness/connector).
Is the sensor harness connection normal?Replace speed
sensor.
Go to Step 3
Repair.
Go to Step 6
3While driving the vehicle, check the wheel speed of each sensor
by Data List.
Is the vehicle speed value is normal?
Go to Step 6Go to Step 4
4Check the sensor rotor.
Is the sensor rotor normal?
Go to Step 6
Replace sensor
rotor.
Go to Step 5
5While driving the vehicle, check the wheel speed of each sensor
by Data List.
Is the vehicle speed value is normal?
Go to Step 6
Repair harness or
connector
between EHCU
and speed
sensor.
Go to Step 6
6Reconnect all components, ensure all components are properly
mounted.
Was this step finished?Repeat the “Basic
diagnostic flow
chart.”
Go to Step 6
Page 4410 of 6000
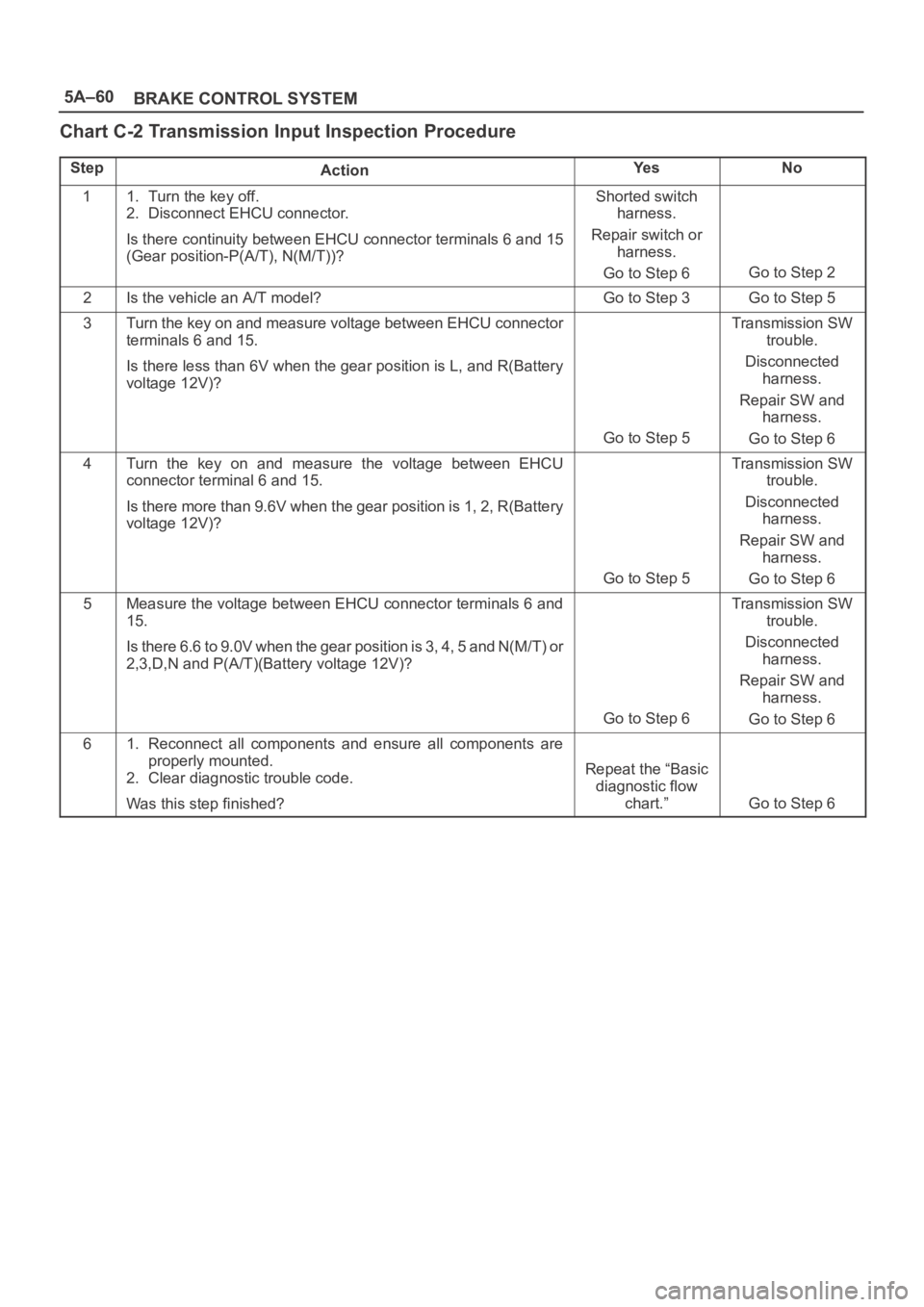
5A–60
BRAKE CONTROL SYSTEM
Chart C-2 Transmission Input Inspection Procedure
StepActionYe sNo
11. Turn the key off.
2. Disconnect EHCU connector.
Is there continuity between EHCU connector terminals 6 and 15
(Gear position-P(A/T), N(M/T))?Shorted switch
harness.
Repair switch or
harness.
Go to Step 6
Go to Step 2
2Is the vehicle an A/T model?Go to Step 3Go to Step 5
3Turn the key on and measure voltage between EHCU connector
terminals 6 and 15.
Is there less than 6V when the gear position is L, and R(Battery
voltage 12V)?
Go to Step 5
Transmission SW
trouble.
Disconnected
harness.
Repair SW and
harness.
Go to Step 6
4Turn the key on and measure the voltage between EHCU
connector terminal 6 and 15.
Is there more than 9.6V when the gear position is 1, 2, R(Battery
voltage 12V)?
Go to Step 5
Transmission SW
trouble.
Disconnected
harness.
Repair SW and
harness.
Go to Step 6
5Measure the voltage between EHCU connector terminals 6 and
15.
Is there 6.6 to 9.0V when the gear position is 3, 4, 5 and N(M/T) or
2,3,D,N and P(A/T)(Battery voltage 12V)?
Go to Step 6
Transmission SW
trouble.
Disconnected
harness.
Repair SW and
harness.
Go to Step 6
61. Reconnect all components and ensure all components are
properly mounted.
2. Clear diagnostic trouble code.
Was this step finished?
Repeat the “Basic
diagnostic flow
chart.”
Go to Step 6
Page 4411 of 6000
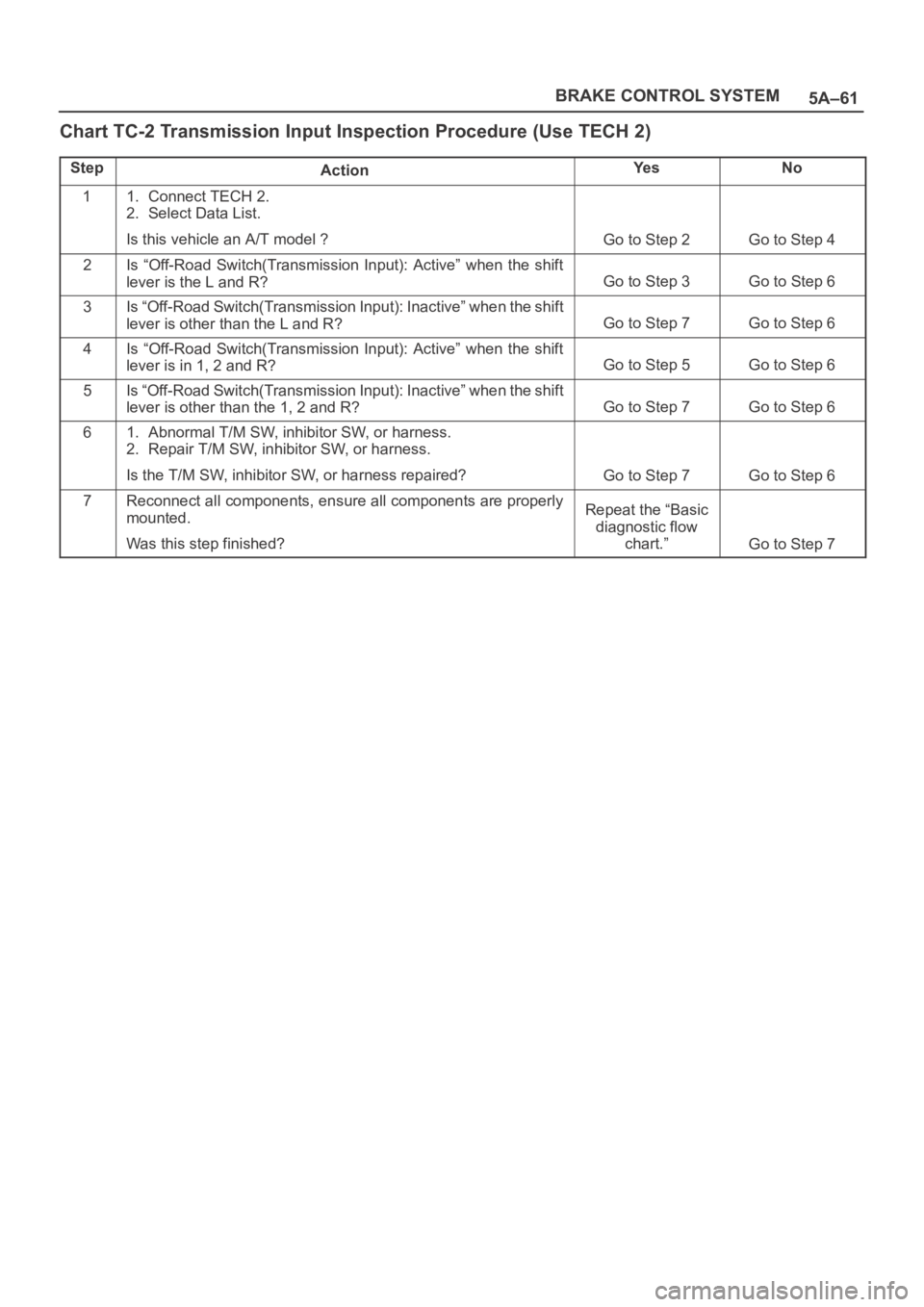
5A–61 BRAKE CONTROL SYSTEM
Chart TC-2 Transmission Input Inspection Procedure (Use TECH 2)
StepActionYe sNo
11. Connect TECH 2.
2. Select Data List.
Is this vehicle an A/T model ?
Go to Step 2Go to Step 4
2Is “Off-Road Switch(Transmission Input): Active” when the shift
lever is the L and R?
Go to Step 3Go to Step 6
3Is “Off-Road Switch(Transmission Input): Inactive” when the shift
lever is other than the L and R?
Go to Step 7Go to Step 6
4Is “Off-Road Switch(Transmission Input): Active” when the shift
lever is in 1, 2 and R?
Go to Step 5Go to Step 6
5Is “Off-Road Switch(Transmission Input): Inactive” when the shift
lever is other than the 1, 2 and R?
Go to Step 7Go to Step 6
61. Abnormal T/M SW, inhibitor SW, or harness.
2. Repair T/M SW, inhibitor SW, or harness.
Is the T/M SW, inhibitor SW, or harness repaired?
Go to Step 7Go to Step 6
7Reconnect all components, ensure all components are properly
mounted.
Was this step finished?Repeat the “Basic
diagnostic flow
chart.”
Go to Step 7
Page 4412 of 6000
5A–62
BRAKE CONTROL SYSTEM
Special Tools
ILLUSTRATIONTOOL NO.
TOOL NAME
5–8840–0385–0
(J–35616)
Connector test adapter
kit
5–8840–0366–0
(J–39200)
High impedance
multimeter
(1) PCMCIA Card
(2) SAE 16/19 Adapter
(3) DLC Cable
(4) Tech–2
Page 4413 of 6000
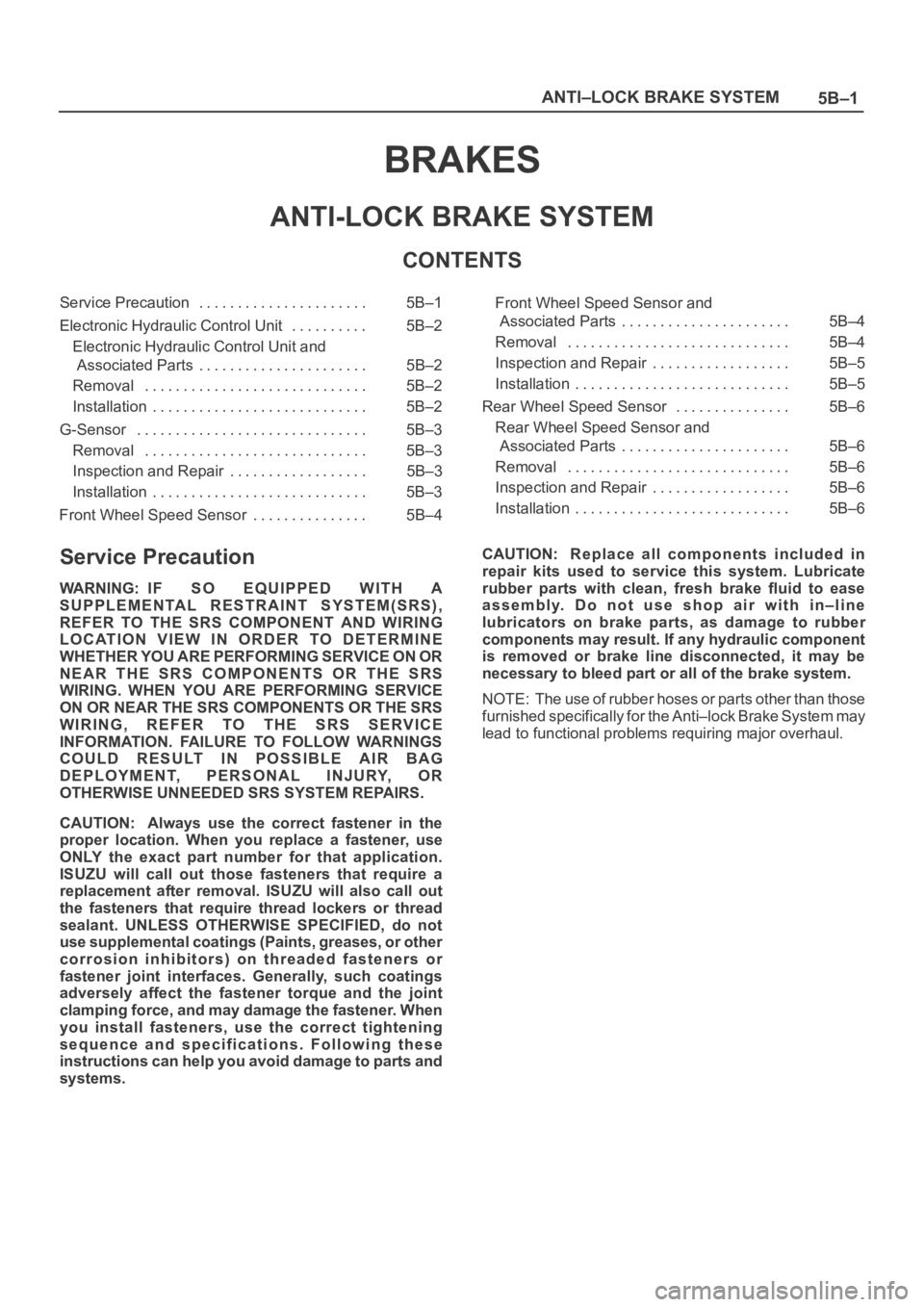
5B–1 ANTI–LOCK BRAKE SYSTEM
BRAKES
ANTI-LOCK BRAKE SYSTEM
CONTENTS
Service Precaution 5B–1. . . . . . . . . . . . . . . . . . . . . .
Electronic Hydraulic Control Unit 5B–2. . . . . . . . . .
Electronic Hydraulic Control Unit and
Associated Parts 5B–2. . . . . . . . . . . . . . . . . . . . . .
Removal 5B–2. . . . . . . . . . . . . . . . . . . . . . . . . . . . .
Installation 5B–2. . . . . . . . . . . . . . . . . . . . . . . . . . . .
G-Sensor 5B–3. . . . . . . . . . . . . . . . . . . . . . . . . . . . . .
Removal 5B–3. . . . . . . . . . . . . . . . . . . . . . . . . . . . .
Inspection and Repair 5B–3. . . . . . . . . . . . . . . . . .
Installation 5B–3. . . . . . . . . . . . . . . . . . . . . . . . . . . .
Front Wheel Speed Sensor 5B–4. . . . . . . . . . . . . . . Front Wheel Speed Sensor and
Associated Parts 5B–4. . . . . . . . . . . . . . . . . . . . . .
Removal 5B–4. . . . . . . . . . . . . . . . . . . . . . . . . . . . .
Inspection and Repair 5B–5. . . . . . . . . . . . . . . . . .
Installation 5B–5. . . . . . . . . . . . . . . . . . . . . . . . . . . .
Rear Wheel Speed Sensor 5B–6. . . . . . . . . . . . . . .
Rear Wheel Speed Sensor and
Associated Parts 5B–6. . . . . . . . . . . . . . . . . . . . . .
Removal 5B–6. . . . . . . . . . . . . . . . . . . . . . . . . . . . .
Inspection and Repair 5B–6. . . . . . . . . . . . . . . . . .
Installation 5B–6. . . . . . . . . . . . . . . . . . . . . . . . . . . .
Service Precaution
WARNING: IF SO EQUIPPED WITH A
SUPPLEMENTAL RESTRAINT SYSTEM(SRS),
REFER TO THE SRS COMPONENT AND WIRING
LOCATION VIEW IN ORDER TO DETERMINE
WHETHER YOU ARE PERFORMING SERVICE ON OR
NEAR THE SRS COMPONENTS OR THE SRS
WIRING. WHEN YOU ARE PERFORMING SERVICE
ON OR NEAR THE SRS COMPONENTS OR THE SRS
WIRING, REFER TO THE SRS SERVICE
INFORMATION. FAILURE TO FOLLOW WARNINGS
COULD RESULT IN POSSIBLE AIR BAG
DEPLOYMENT, PERSONAL INJURY, OR
OTHERWISE UNNEEDED SRS SYSTEM REPAIRS.
CAUTION: Always use the correct fastener in the
proper location. When you replace a fastener, use
ONLY the exact part number for that application.
ISUZU will call out those fasteners that require a
replacement after removal. ISUZU will also call out
the fasteners that require thread lockers or thread
sealant. UNLESS OTHERWISE SPECIFIED, do not
use supplemental coatings (Paints, greases, or other
corrosion inhibitors) on threaded fasteners or
fastener joint interfaces. Generally, such coatings
adversely affect the fastener torque and the joint
clamping force, and may damage the fastener. When
you install fasteners, use the correct tightening
sequence and specifications. Following these
instructions can help you avoid damage to parts and
systems.CAUTION: Replace all components included in
repair kits used to service this system. Lubricate
rubber parts with clean, fresh brake fluid to ease
assembly. Do not use shop air with in–line
lubricators on brake parts, as damage to rubber
components may result. If any hydraulic component
is removed or brake line disconnected, it may be
necessary to bleed part or all of the brake system.
NOTE: The use of rubber hoses or parts other than those
furnished specifically for the Anti–lock Brake System may
lead to functional problems requiring major overhaul.
Page 4414 of 6000
5B–2ANTI–LOCK BRAKE SYSTEM
Electronic Hydraulic Control Unit
Electronic Hydraulic Control Unit and Associated Parts
350RW013
Legend
(1) Connector
(2) Hydraulic Unit ASM(3) Bolts
(4) Nut
(5) Bolt
Removal
1. Remove battery ASM.
2. Remove harness connector.
3. Remove EHCU fixing nuts.
4. Remove brake pipes.
After disconnecting brake pipe, cap or tape the
openings of the brake pipe to prevent the entry of
foreign matter.
5. Remove hydraulic unit fixing nuts.
Installation
To install, follow the removal steps in the reverse order,
noting the following points:
To r q u e
Hydraulic unit fixing nuts : 22 Nꞏm (2.2kgꞏm/16
lb ft)
Ground cable : 14 Nꞏm (1.4kgꞏm/10 lb ft)
Brake pipe (joint bolts) : 16 Nꞏm (1.6kgꞏm/12
lb ft)
After installing the hydraulic unit, bleed brakes
completely. Refer to Servicing in Power Assisted
Brake System section.
Page 4415 of 6000
5B–3 ANTI–LOCK BRAKE SYSTEM
G-Sensor
Removal
350RX001
1. Remove center console.
Refer to Consoles in Body and Accessories
section.
2. Remove clip from G-sensor connector (1), then
disconnect connector.
3. Remove G-sensor assembly fixing bolt (2).
4. Remove G-sensor assembly (3).
Inspection and Repair
Refer to Chart B-5 in Brake Control System section.
Installation
1. Install G-sensor assembly (3).
Care should be taken so that the G-sensor is not
installed in the wrong direction.
2. Install G-sensor assembly fixing bolt (2).
Tighten the fixing bolt to the specified torque.
Torque : 10 Nꞏm (1.0kgꞏm/87 lb in)
3. Install G-sensor wiring connector (1).
4. Install center console.
Refer to Consoles in Body and Accessories
section.
Page 4416 of 6000
5B–4ANTI–LOCK BRAKE SYSTEM
Front Wheel Speed Sensor
Front Wheel Speed Sensor and Associated Parts
350RW012
Legend
(1) Speed Sensor Connector
(2) Sensor Cable Fixing Bolt (Upper side)(3) Sensor Cable Fixing Bolt (Lower side)
(4) Sensor Cable Fixing Bolt (Sensor side)
(5) Speed Sensor
Removal
1. Remove speed sensor connector.
2. Remove sensor cable fixing bolt (Upper side).
3. Remove sensor cable fixing bolt (Lower side).
4. Remove the speed sensor cable fixing bolts (1) and
caliper fixing bolt (2) from caliper side speed sensor
cable bracket (3).
350RW010
5. Remove speed sensor.