Page 465 of 6000
DIFFERENTIAL (FRONT) 4A1–28
Special Tools
ILLUSTRATIONTOOL NO.
TOOL NAME
5–8840–2157–0
(J–37221)
Holder; Pinion flange
9–8522–1275–0
(J–24250)
Installer; Oil seal
5–8840–0275–0
(J–37264)
Differential holding
fixture
(Use with
5–8840–0003–0 base)
5–8840–0003–0
(J–3289–20)
Holding fixture base
5–8840–0013–0
5–8840–0014–0
(J–22888)
Puller; Side bearing
9–8521–1743–0
(J–8107–2)
Adapter; Side bearing
plug
ILLUSTRATIONTOOL NO.
TOOL NAME
5–8840–0015–0
(J–22912–01)
Separator
9–8522–1141–0
(J–24256)
Installer; Outer bearing
outer race
5–8840–0007–0
(J–8092)
Driver handle
9–8522–1274–0
(J–24252)
Installer; Inner bearing
outer race
5–8840–2085–0
(J–21777–42)
Pilot
5–8840–2089–0
(J–23597–9)
Nut and bolt
Page 466 of 6000
4A1–29 DIFFERENTIAL (FRONT)
ILLUSTRATIONTOOL NO.
TOOL NAME
5–8840–2087–0
(J–23597–7)
Gauge plate
5–8840–0126–0
(J–8001)
Dial indicator
5–8840–2088–0
(J–23597–8)
Disc
5–8840–0128–0
(J–23597–1)
Arbor
9–8522–1165–0
(J–6133–01)
Installer; Pinion bearing
5–8840–2293–0
(J–39209)
Punch; End nut lock
ILLUSTRATIONTOOL NO.
TOOL NAME
9–8522–1164–0
(J–24244)
Installer; Side bearing
5–8840–2323–0
(J–39602)
Remover; Outer bearing
Page 467 of 6000
DIFFERENTIAL (FRONT) 4A1–30
MEMO
Page 468 of 6000
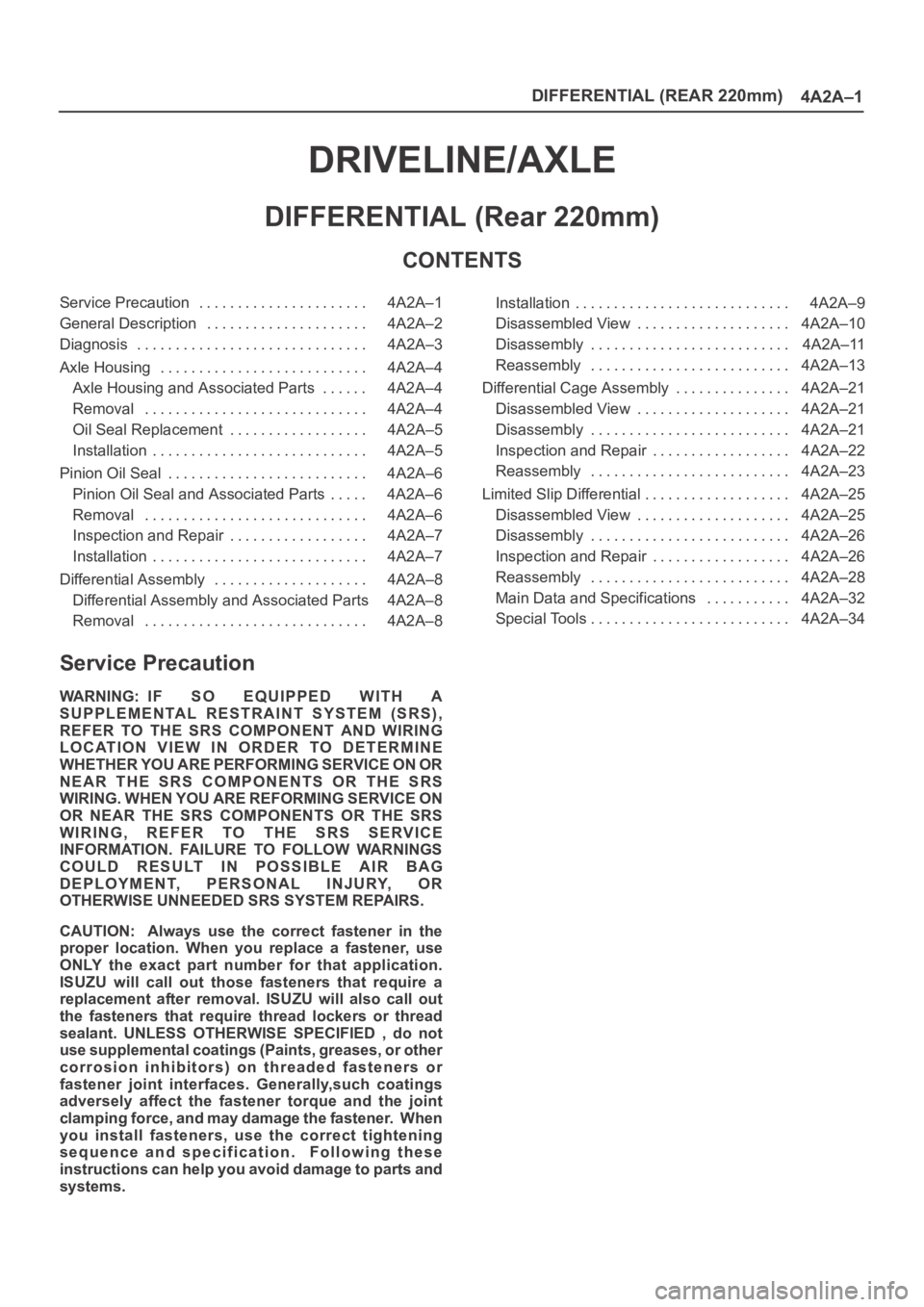
DIFFERENTIAL (REAR 220mm)
4A2A–1
DRIVELINE/AXLE
DIFFERENTIAL (Rear 220mm)
CONTENTS
Service Precaution 4A2A–1. . . . . . . . . . . . . . . . . . . . . .
General Description 4A2A–2. . . . . . . . . . . . . . . . . . . . .
Diagnosis 4A2A–3. . . . . . . . . . . . . . . . . . . . . . . . . . . . . .
Axle Housing 4A2A–4. . . . . . . . . . . . . . . . . . . . . . . . . . .
Axle Housing and Associated Parts 4A2A–4. . . . . .
Removal 4A2A–4. . . . . . . . . . . . . . . . . . . . . . . . . . . . .
Oil Seal Replacement 4A2A–5. . . . . . . . . . . . . . . . . .
Installation 4A2A–5. . . . . . . . . . . . . . . . . . . . . . . . . . . .
Pinion Oil Seal 4A2A–6. . . . . . . . . . . . . . . . . . . . . . . . . .
Pinion Oil Seal and Associated Parts 4A2A–6. . . . .
Removal 4A2A–6. . . . . . . . . . . . . . . . . . . . . . . . . . . . .
Inspection and Repair 4A2A–7. . . . . . . . . . . . . . . . . .
Installation 4A2A–7. . . . . . . . . . . . . . . . . . . . . . . . . . . .
Differential Assembly 4A2A–8. . . . . . . . . . . . . . . . . . . .
Differential Assembly and Associated Parts 4A2A–8
Removal 4A2A–8. . . . . . . . . . . . . . . . . . . . . . . . . . . . . Installation 4A2A–9. . . . . . . . . . . . . . . . . . . . . . . . . . . .
Disassembled View 4A2A–10. . . . . . . . . . . . . . . . . . . .
Disassembly 4A2A–11. . . . . . . . . . . . . . . . . . . . . . . . . .
Reassembly 4A2A–13. . . . . . . . . . . . . . . . . . . . . . . . . .
Differential Cage Assembly 4A2A–21. . . . . . . . . . . . . . .
Disassembled View 4A2A–21. . . . . . . . . . . . . . . . . . . .
Disassembly 4A2A–21. . . . . . . . . . . . . . . . . . . . . . . . . .
Inspection and Repair 4A2A–22. . . . . . . . . . . . . . . . . .
Reassembly 4A2A–23. . . . . . . . . . . . . . . . . . . . . . . . . .
Limited Slip Differential 4A2A–25. . . . . . . . . . . . . . . . . . .
Disassembled View 4A2A–25. . . . . . . . . . . . . . . . . . . .
Disassembly 4A2A–26. . . . . . . . . . . . . . . . . . . . . . . . . .
Inspection and Repair 4A2A–26. . . . . . . . . . . . . . . . . .
Reassembly 4A2A–28. . . . . . . . . . . . . . . . . . . . . . . . . .
Main Data and Specifications 4A2A–32. . . . . . . . . . .
Special Tools 4A2A–34. . . . . . . . . . . . . . . . . . . . . . . . . .
Service Precaution
WARNING: IF SO EQUIPPED WITH A
SUPPLEMENTAL RESTRAINT SYSTEM (SRS),
REFER TO THE SRS COMPONENT AND WIRING
LOCATION VIEW IN ORDER TO DETERMINE
WHETHER YOU ARE PERFORMING SERVICE ON OR
NEAR THE SRS COMPONENTS OR THE SRS
WIRING. WHEN YOU ARE REFORMING SERVICE ON
OR NEAR THE SRS COMPONENTS OR THE SRS
WIRING, REFER TO THE SRS SERVICE
INFORMATION. FAILURE TO FOLLOW WARNINGS
COULD RESULT IN POSSIBLE AIR BAG
DEPLOYMENT, PERSONAL INJURY, OR
OTHERWISE UNNEEDED SRS SYSTEM REPAIRS.
CAUTION: Always use the correct fastener in the
proper location. When you replace a fastener, use
ONLY the exact part number for that application.
ISUZU will call out those fasteners that require a
replacement after removal. ISUZU will also call out
the fasteners that require thread lockers or thread
sealant. UNLESS OTHERWISE SPECIFIED , do not
use supplemental coatings (Paints, greases, or other
corrosion inhibitors) on threaded fasteners or
fastener joint interfaces. Generally,such coatings
adversely affect the fastener torque and the joint
c l a m p i n g f o r c e , a n d m a y d a m a g e t h e f a s t e n e r. W h e n
you install fasteners, use the correct tightening
sequence and specification. Following these
instructions can help you avoid damage to parts and
systems.
Page 469 of 6000
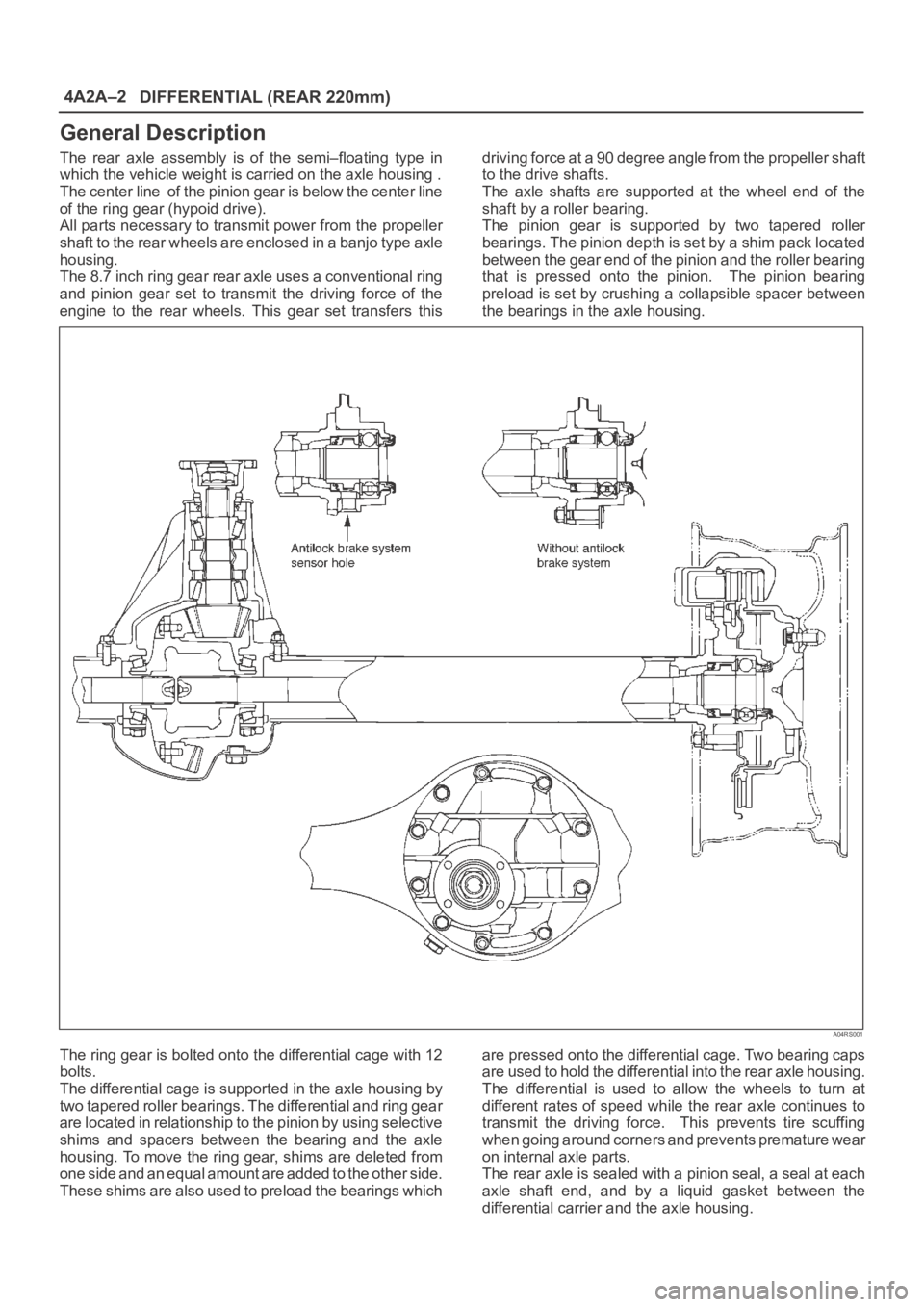
4A2A–2
DIFFERENTIAL (REAR 220mm)
General Description
The rear axle assembly is of the semi–floating type in
which the vehicle weight is carried on the axle housing .
The center line of the pinion gear is below the center line
of the ring gear (hypoid drive).
All parts necessary to transmit power from the propeller
shaft to the rear wheels are enclosed in a banjo type axle
housing.
The 8.7 inch ring gear rear axle uses a conventional ring
and pinion gear set to transmit the driving force of the
engine to the rear wheels. This gear set transfers thisdriving force at a 90 degree angle from the propeller shaft
to the drive shafts.
The axle shafts are supported at the wheel end of the
shaft by a roller bearing.
The pinion gear is supported by two tapered roller
bearings. The pinion depth is set by a shim pack located
between the gear end of the pinion and the roller bearing
that is pressed onto the pinion. The pinion bearing
preload is set by crushing a collapsible spacer between
the bearings in the axle housing.
A04RS001
The ring gear is bolted onto the differential cage with 12
bolts.
The differential cage is supported in the axle housing by
two tapered roller bearings. The differential and ring gear
are located in relationship to the pinion by using selective
shims and spacers between the bearing and the axle
housing. To move the ring gear, shims are deleted from
one side and an equal amount are added to the other side.
These shims are also used to preload the bearings whichare pressed onto the differential cage. Two bearing caps
are used to hold the differential into the rear axle housing.
The differential is used to allow the wheels to turn at
different rates of speed while the rear axle continues to
transmit the driving force. This prevents tire scuffing
when going around corners and prevents premature wear
on internal axle parts.
The rear axle is sealed with a pinion seal, a seal at each
axle shaft end, and by a liquid gasket between the
differential carrier and the axle housing.
Page 470 of 6000
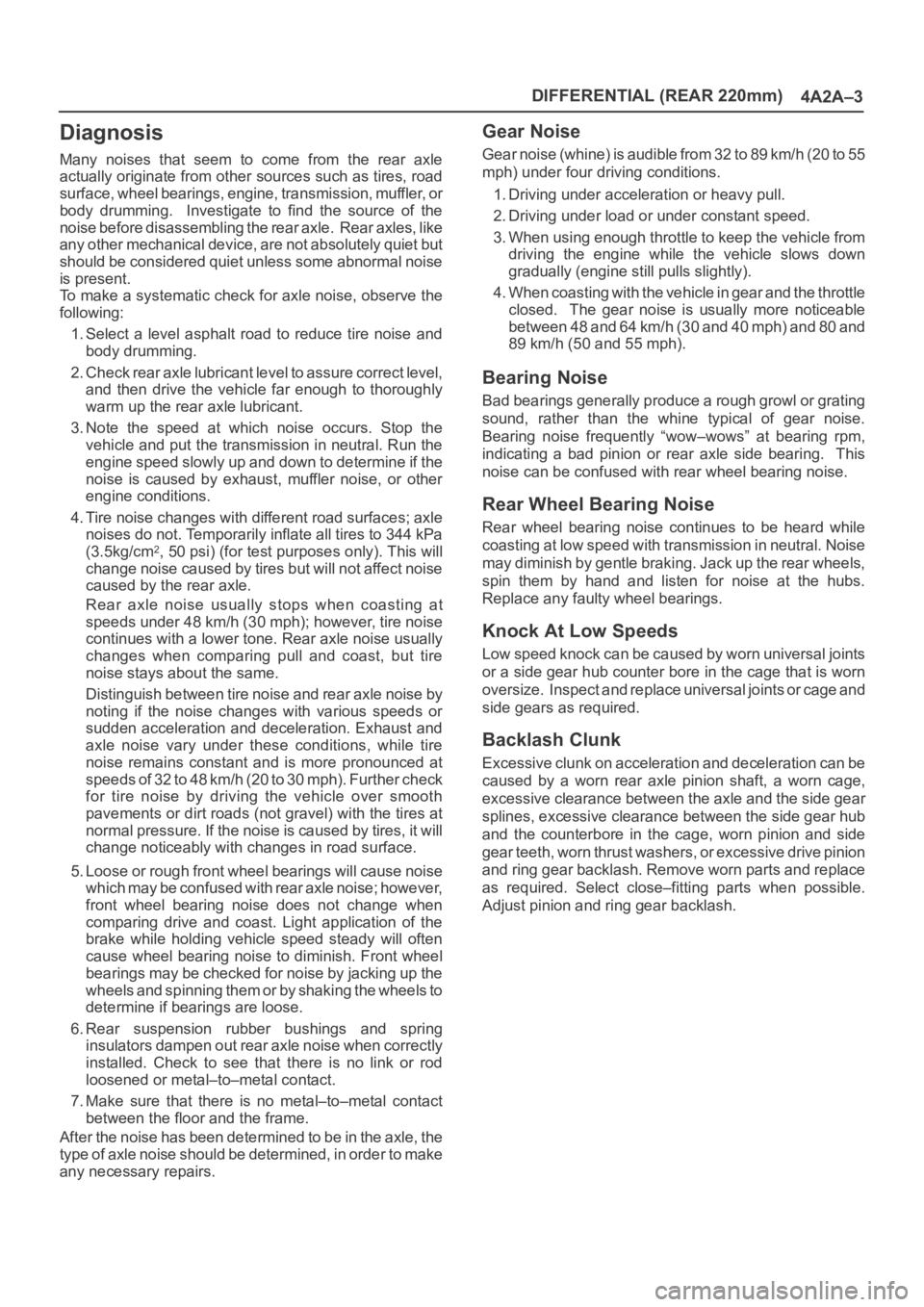
DIFFERENTIAL (REAR 220mm)
4A2A–3
Diagnosis
Many noises that seem to come from the rear axle
actually originate from other sources such as tires, road
surface, wheel bearings, engine, transmission, muffler, or
body drumming. Investigate to find the source of the
noise before disassembling the rear axle. Rear axles, like
any other mechanical device, are not absolutely quiet but
should be considered quiet unless some abnormal noise
is present.
To make a systematic check for axle noise, observe the
following:
1. Select a level asphalt road to reduce tire noise and
body drumming.
2. Check rear axle lubricant level to assure correct level,
and then drive the vehicle far enough to thoroughly
warm up the rear axle lubricant.
3. Note the speed at which noise occurs. Stop the
vehicle and put the transmission in neutral. Run the
engine speed slowly up and down to determine if the
noise is caused by exhaust, muffler noise, or other
engine conditions.
4. Tire noise changes with different road surfaces; axle
noises do not. Temporarily inflate all tires to 344 kPa
(3.5kg/cm
2, 50 psi) (for test purposes only). This will
change noise caused by tires but will not affect noise
caused by the rear axle.
Rear axle noise usually stops when coasting at
speeds under 48 km/h (30 mph); however, tire noise
continues with a lower tone. Rear axle noise usually
changes when comparing pull and coast, but tire
noise stays about the same.
Distinguish between tire noise and rear axle noise by
noting if the noise changes with various speeds or
sudden acceleration and deceleration. Exhaust and
axle noise vary under these conditions, while tire
noise remains constant and is more pronounced at
speeds of 32 to 48 km/h (20 to 30 mph). Further check
for tire noise by driving the vehicle over smooth
pavements or dirt roads (not gravel) with the tires at
normal pressure. If the noise is caused by tires, it will
change noticeably with changes in road surface.
5. Loose or rough front wheel bearings will cause noise
which may be confused with rear axle noise; however,
front wheel bearing noise does not change when
comparing drive and coast. Light application of the
brake while holding vehicle speed steady will often
cause wheel bearing noise to diminish. Front wheel
bearings may be checked for noise by jacking up the
wheels and spinning them or by shaking the wheels to
determine if bearings are loose.
6. Rear suspension rubber bushings and spring
insulators dampen out rear axle noise when correctly
installed. Check to see that there is no link or rod
loosened or metal–to–metal contact.
7. Make sure that there is no metal–to–metal contact
between the floor and the frame.
After the noise has been determined to be in the axle, the
type of axle noise should be determined, in order to make
any necessary repairs.
Gear Noise
Gear noise (whine) is audible from 32 to 89 km/h (20 to 55
mph) under four driving conditions.
1. Driving under acceleration or heavy pull.
2. Driving under load or under constant speed.
3. When using enough throttle to keep the vehicle from
driving the engine while the vehicle slows down
gradually (engine still pulls slightly).
4. When coasting with the vehicle in gear and the throttle
closed. The gear noise is usually more noticeable
between 48 and 64 km/h (30 and 40 mph) and 80 and
89 km/h (50 and 55 mph).
Bearing Noise
Bad bearings generally produce a rough growl or grating
sound, rather than the whine typical of gear noise.
Bearing noise frequently “wow–wows” at bearing rpm,
indicating a bad pinion or rear axle side bearing. This
noise can be confused with rear wheel bearing noise.
Rear Wheel Bearing Noise
Rear wheel bearing noise continues to be heard while
coasting at low speed with transmission in neutral. Noise
may diminish by gentle braking. Jack up the rear wheels,
spin them by hand and listen for noise at the hubs.
Replace any faulty wheel bearings.
Knock At Low Speeds
Low speed knock can be caused by worn universal joints
or a side gear hub counter bore in the cage that is worn
oversize. Inspect and replace universal joints or cage and
side gears as required.
Backlash Clunk
Excessive clunk on acceleration and deceleration can be
caused by a worn rear axle pinion shaft, a worn cage,
excessive clearance between the axle and the side gear
splines, excessive clearance between the side gear hub
and the counterbore in the cage, worn pinion and side
gear teeth, worn thrust washers, or excessive drive pinion
and ring gear backlash. Remove worn parts and replace
as required. Select close–fitting parts when possible.
Adjust pinion and ring gear backlash.
Page 471 of 6000
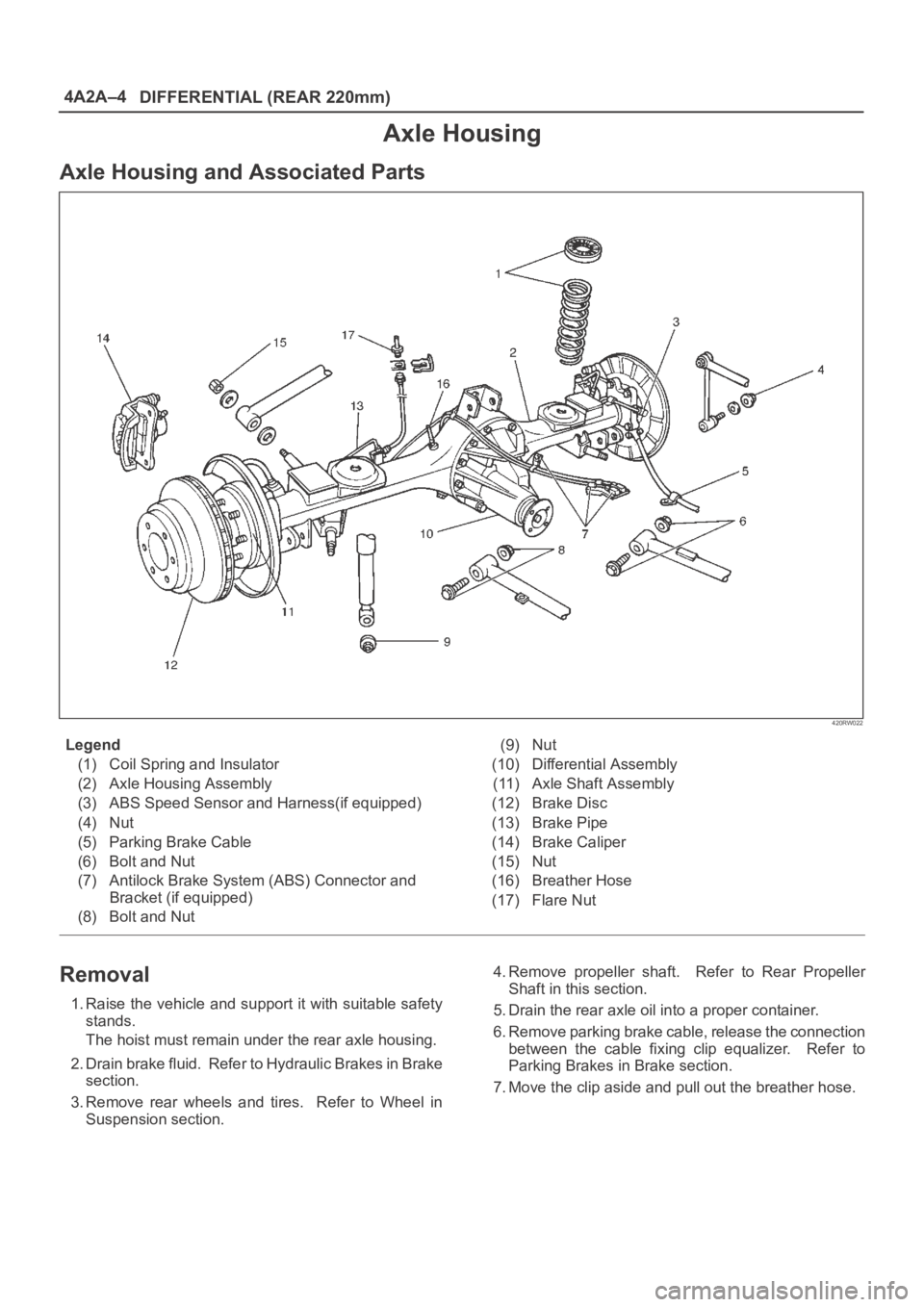
4A2A–4
DIFFERENTIAL (REAR 220mm)
Axle Housing
Axle Housing and Associated Parts
420RW022
Legend
(1) Coil Spring and Insulator
(2) Axle Housing Assembly
(3) ABS Speed Sensor and Harness(if equipped)
(4) Nut
(5) Parking Brake Cable
(6) Bolt and Nut
(7) Antilock Brake System (ABS) Connector and
Bracket (if equipped)
(8) Bolt and Nut(9) Nut
(10) Differential Assembly
(11) Axle Shaft Assembly
(12) Brake Disc
(13) Brake Pipe
(14) Brake Caliper
(15) Nut
(16) Breather Hose
(17) Flare Nut
Removal
1. Raise the vehicle and support it with suitable safety
stands.
The hoist must remain under the rear axle housing.
2. Drain brake fluid. Refer to Hydraulic Brakes in Brake
section.
3. Remove rear wheels and tires. Refer to Wheel in
Suspension section.4. Remove propeller shaft. Refer to Rear Propeller
Shaft in this section.
5. Drain the rear axle oil into a proper container.
6. Remove parking brake cable, release the connection
between the cable fixing clip equalizer. Refer to
Parking Brakes in Brake section.
7. Move the clip aside and pull out the breather hose.
Page 472 of 6000
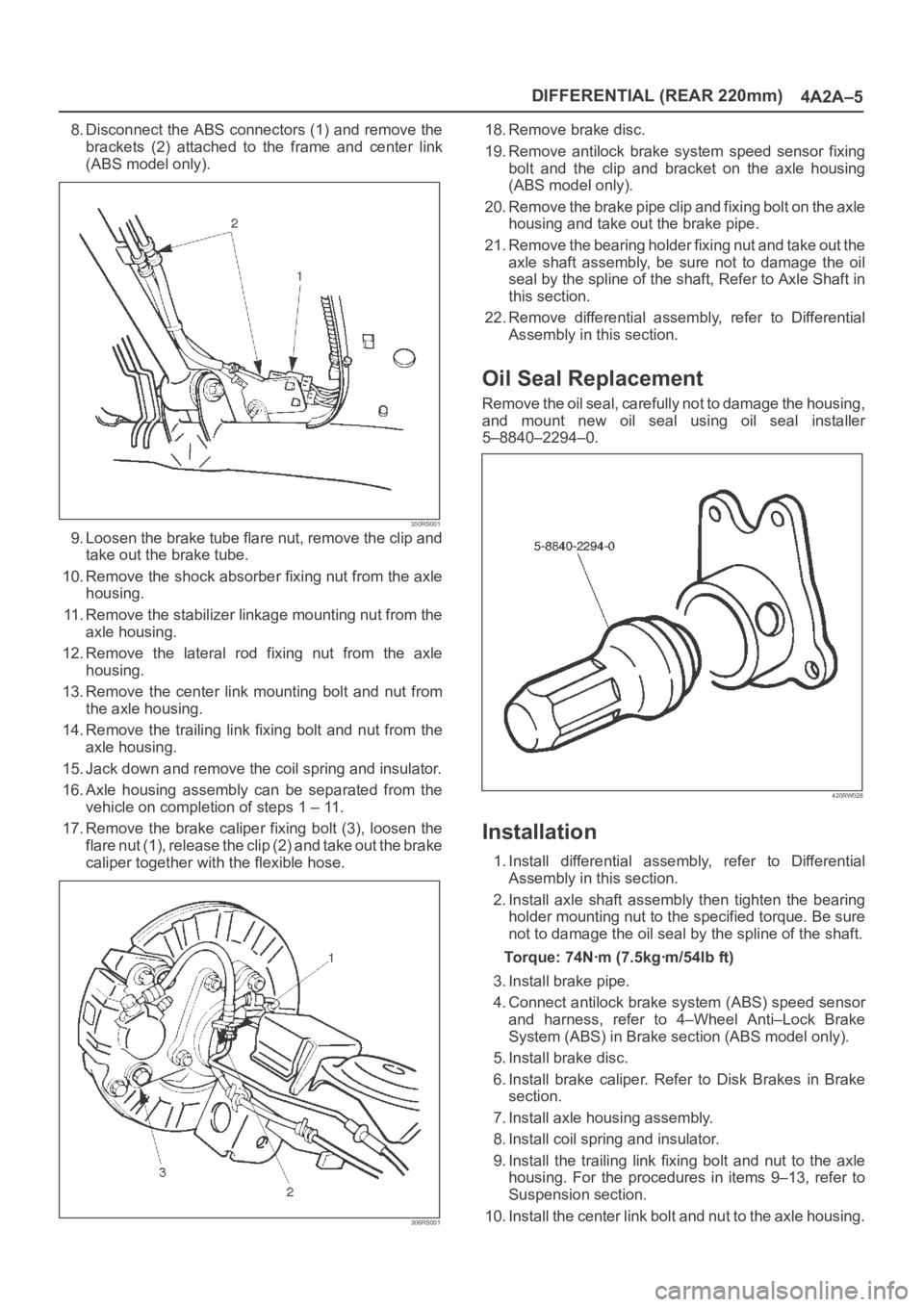
DIFFERENTIAL (REAR 220mm)
4A2A–5
8. Disconnect the ABS connectors (1) and remove the
brackets (2) attached to the frame and center link
(ABS model only).
350RS001
9. Loosen the brake tube flare nut, remove the clip and
take out the brake tube.
10. Remove the shock absorber fixing nut from the axle
housing.
11. Remove the stabilizer linkage mounting nut from the
axle housing.
12. Remove the lateral rod fixing nut from the axle
housing.
13. Remove the center link mounting bolt and nut from
the axle housing.
14. Remove the trailing link fixing bolt and nut from the
axle housing.
15. Jack down and remove the coil spring and insulator.
16. Axle housing assembly can be separated from the
vehicle on completion of steps 1 – 11.
17. Remove the brake caliper fixing bolt (3), loosen the
flare nut (1), release the clip (2) and take out the brake
caliper together with the flexible hose.
306RS001
18. Remove brake disc.
19. Remove antilock brake system speed sensor fixing
bolt and the clip and bracket on the axle housing
(ABS model only).
20. Remove the brake pipe clip and fixing bolt on the axle
housing and take out the brake pipe.
21. Remove the bearing holder fixing nut and take out the
axle shaft assembly, be sure not to damage the oil
seal by the spline of the shaft, Refer to Axle Shaft in
this section.
22. Remove differential assembly, refer to Differential
Assembly in this section.
Oil Seal Replacement
Remove the oil seal, carefully not to damage the housing,
and mount new oil seal using oil seal installer
5–8840–2294–0.
420RW028
Installation
1. Install differential assembly, refer to Differential
Assembly in this section.
2. Install axle shaft assembly then tighten the bearing
holder mounting nut to the specified torque. Be sure
not to damage the oil seal by the spline of the shaft.
Torque: 74Nꞏm (7.5kgꞏm/54lb ft)
3. Install brake pipe.
4. Connect antilock brake system (ABS) speed sensor
and harness, refer to 4–Wheel Anti–Lock Brake
System (ABS) in Brake section (ABS model only).
5. Install brake disc.
6. Install brake caliper. Refer to Disk Brakes in Brake
section.
7. Install axle housing assembly.
8. Install coil spring and insulator.
9. Install the trailing link fixing bolt and nut to the axle
housing. For the procedures in items 9–13, refer to
Suspension section.
10. Install the center link bolt and nut to the axle housing.