Page 5673 of 6000
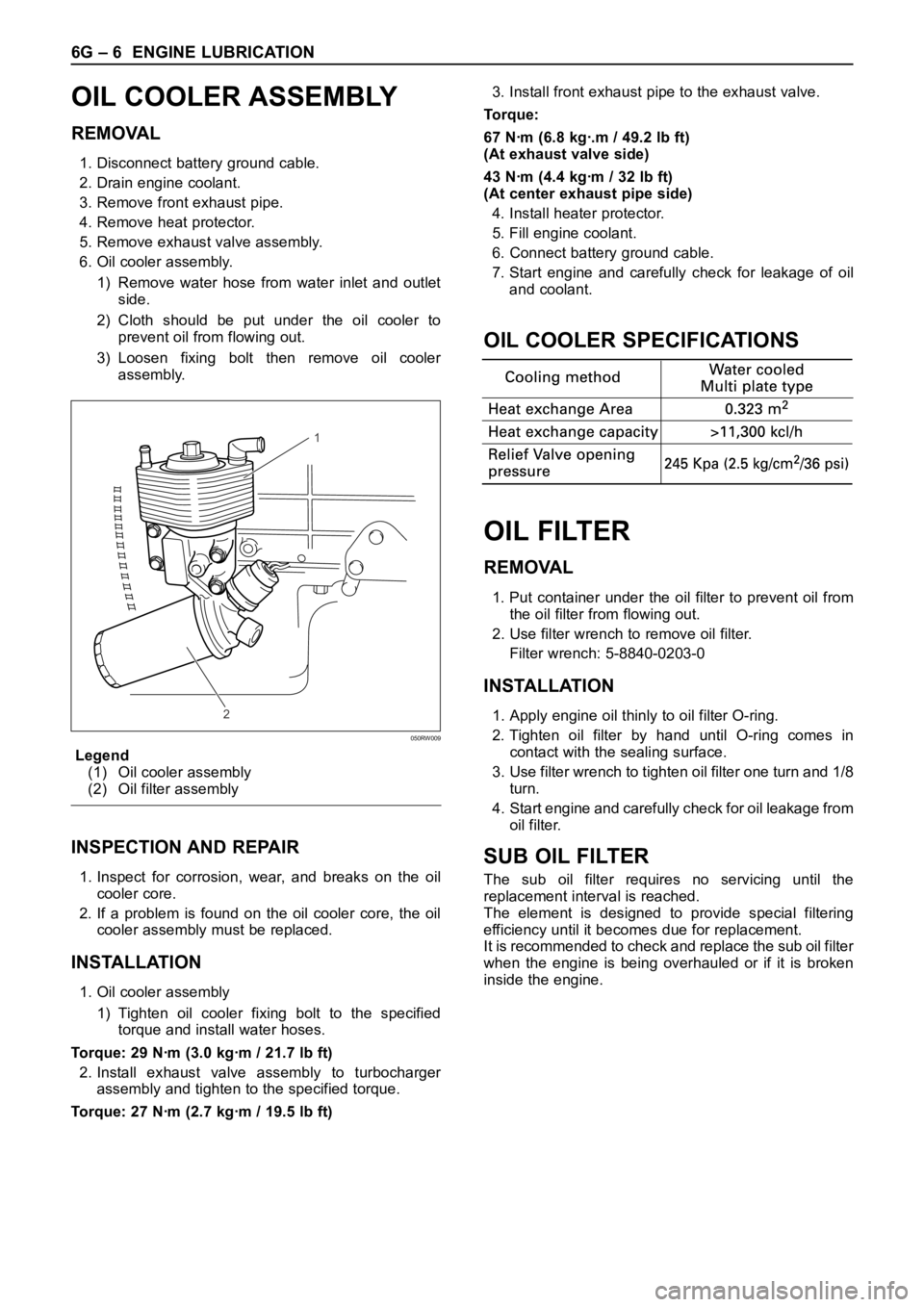
6G – 6 ENGINE LUBRICATION
OIL COOLER ASSEMBLY
REMOVAL
1. Disconnect battery ground cable.
2. Drain engine coolant.
3. Remove front exhaust pipe.
4. Remove heat protector.
5. Remove exhaust valve assembly.
6. Oil cooler assembly.
1) Remove water hose from water inlet and outlet
side.
2) Cloth should be put under the oil cooler to
prevent oil from flowing out.
3) Loosen fixing bolt then remove oil cooler
assembly.
Legend
(1) Oil cooler assembly
(2) Oil filter assembly
INSPECTION AND REPAIR
1. Inspect for corrosion, wear, and breaks on the oil
cooler core.
2. If a problem is found on the oil cooler core, the oil
cooler assembly must be replaced.
INSTALLATION
1. Oil cooler assembly
1) Tighten oil cooler fixing bolt to the specified
torque and install water hoses.
Torque: 29 Nꞏm (3.0 kgꞏm / 21.7 lb ft)
2. Install exhaust valve assembly to turbocharger
assembly and tighten to the specified torque.
Torque: 27 Nꞏm (2.7 kgꞏm / 19.5 lb ft)3. Install front exhaust pipe to the exhaust valve.
To r q u e :
67 Nꞏm (6.8 kgꞏ.m / 49.2 lb ft)
(At exhaust valve side)
43 Nꞏm (4.4 kgꞏm / 32 lb ft)
(At center exhaust pipe side)
4. Install heater protector.
5. Fill engine coolant.
6. Connect battery ground cable.
7. Start engine and carefully check for leakage of oil
and coolant.
OIL COOLER SPECIFICATIONS
OIL FILTER
REMOVAL
1. Put container under the oil filter to prevent oil from
the oil filter from flowing out.
2. Use filter wrench to remove oil filter.
Filter wrench: 5-8840-0203-0
INSTALLATION
1. Apply engine oil thinly to oil filter O-ring.
2. Tighten oil filter by hand until O-ring comes in
contact with the sealing surface.
3. Use filter wrench to tighten oil filter one turn and 1/8
turn.
4. Start engine and carefully check for oil leakage from
oil filter.
SUB OIL FILTER
The sub oil filter requires no servicing until the
replacement interval is reached.
The element is designed to provide special filtering
efficiency until it becomes due for replacement.
It is recommended to check and replace the sub oil filter
when the engine is being overhauled or if it is broken
inside the engine.
1
2
050RW009
Page 5674 of 6000
ENGINE SPEED CONTROL 6H – 1
ENGINE SPEED CONTROL
CONTENTS
General Description . . . . . . . . . . . . . . . . . . 6H–2 Engine Speed Control . . . . . . . . . . . . . . . . . 6H–3
Page 5675 of 6000
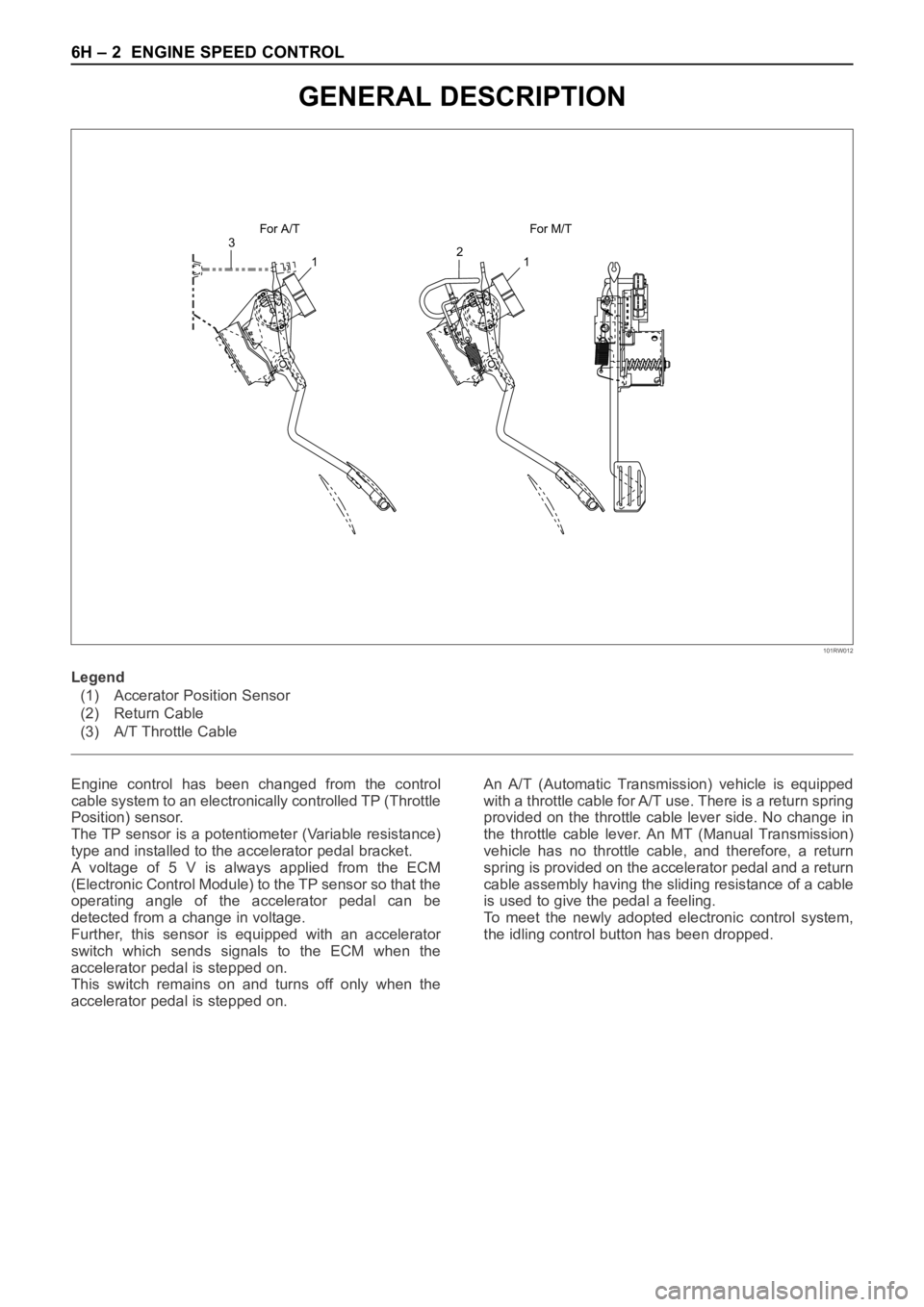
6H – 2 ENGINE SPEED CONTROL
GENERAL DESCRIPTION
3For A/T
1For M/T
2
1
101RW012
Engine control has been changed from the control
cable system to an electronically controlled TP (Throttle
Position) sensor.
The TP sensor is a potentiometer (Variable resistance)
type and installed to the accelerator pedal bracket.
A voltage of 5 V is always applied from the ECM
(Electronic Control Module) to the TP sensor so that the
operating angle of the accelerator pedal can be
detected from a change in voltage.
Further, this sensor is equipped with an accelerator
switch which sends signals to the ECM when the
accelerator pedal is stepped on.
This switch remains on and turns off only when the
accelerator pedal is stepped on.An A/T (Automatic Transmission) vehicle is equipped
with a throttle cable for A/T use. There is a return spring
provided on the throttle cable lever side. No change in
the throttle cable lever. An MT (Manual Transmission)
vehicle has no throttle cable, and therefore, a return
spring is provided on the accelerator pedal and a return
cable assembly having the sliding resistance of a cable
is used to give the pedal a feeling.
To meet the newly adopted electronic control system,
the idling control button has been dropped. Legend
(1) Accerator Position Sensor
(2) Return Cable
(3) A/T Throttle Cable
Page 5676 of 6000
ENGINE SPEED CONTROL 6H – 3
REMOVAL
1. For vehicle with MT
1) Remove harness connector from accelerator
pedal sensor.
2) Remove accelerator pedal assembly from
chassis.
2. For vehicle with A/T
1) Remove A/T control cable from accelerator
pedal assembly.
2) Remove harness connector from accelerator
pedal sensor.
3) Remove accelerator pedal assembly from
chassis.
INSPECTION AND REPAIR
1. Check moving condition of accelerator pedal, if not
smooth working, apply oil to the pivot etc.
2. Check tightening condition of accelerator sensor, if
not completely tightened, it should be tightened
additionally.
INSTALLATION
The installation for both MT and A/T vehicles follows the
reverse manner of removal.
ENGINE SPEED CONTROL
Page 5677 of 6000
Page 5678 of 6000
INDUCTION 6J – 1
INDUCTION
CONTENTS
General Description . . . . . . . . . . . . . . . . . . 6J–2
Air Cleaner . . . . . . . . . . . . . . . . . . . . . . . . . 6J–3
Turbocharger . . . . . . . . . . . . . . . . . . . . . . . 6J–4
Intercooler . . . . . . . . . . . . . . . . . . . . . . . . . 6J–8Intake Throttle Valve . . . . . . . . . . . . . . . . . . 6J–9
Intake Manifold . . . . . . . . . . . . . . . . . . . . . . 6J–10
Main Data and Specifications . . . . . . . . . . . 6J–11
Page 5679 of 6000
6J – 2 INDUCTION
There is a large intake silencer provided at the entrance
of the air cleaner. Air cleaner element is a viscous type
which features high filtration efficiency.
A resonator is used also in the air duct between the air
cleaner and turbocharger to reduce air intake noise.
The air taken in flows through the turbocharger to the
intercooler where the air is cooled and then taken in the
cylinder through the intake manifold.
71
23
4 8
5 6
Legend
(1) Air Cleaner
(2) Connector for Fuel Tank Breather Hose
(3) Resonator
(4) Air Duct(5) Connector for PCV Hose
(6) Connector for EGR VSV Hose
(7) Air Duct
(8) Air Duct
130RW015
GENERAL DESCRIPTION
Page 5680 of 6000
INDUCTION 6J – 3
REMOVAL
1. Remove air cleaner cover with air duct.
2. Remove air cleaner element.
INSPECTION
Check air cleaner element for clogs, chokes and
breaks, and if any problem is found during inspection,
the element must be replaced.
INSTALLATION
1. Air cleaner element
2. Air cleaner cover with air duct.
1) Put air cleaner cover in original position and
tighten it with the clip.
130RW010
AIR CLEANER