Page 57 of 2389
AT3605
(e) Remove the bearing cage from drive pinion.
AT-38- AUTOMATIC TRANSAXLERemoval of Component Parts
Page 58 of 2389
AT3608r Non-reusable part
: Specified torque kg-cm (ft-lb, N-m)
r O-Ring r Oil SealDrive GearThrust WasherOil Seal Ring Driven Gear Pump BodyStator Shaft100 (7, 10)
AT3609 AT3610
Oil Pump
COMPONENTS
DISASSEMBLY OF OIL PUMP
1. REMOVE OIL SEAL RINGS
Remove the two oil seal rings from the stator shaft back
side.
2. REMOVE THRUST WASHER FROM STATOR SHAFT
BACK SIDE
- AUTOMATIC TRANSAXLEComponent Parts (Oil Pump)AT-43
Page 59 of 2389
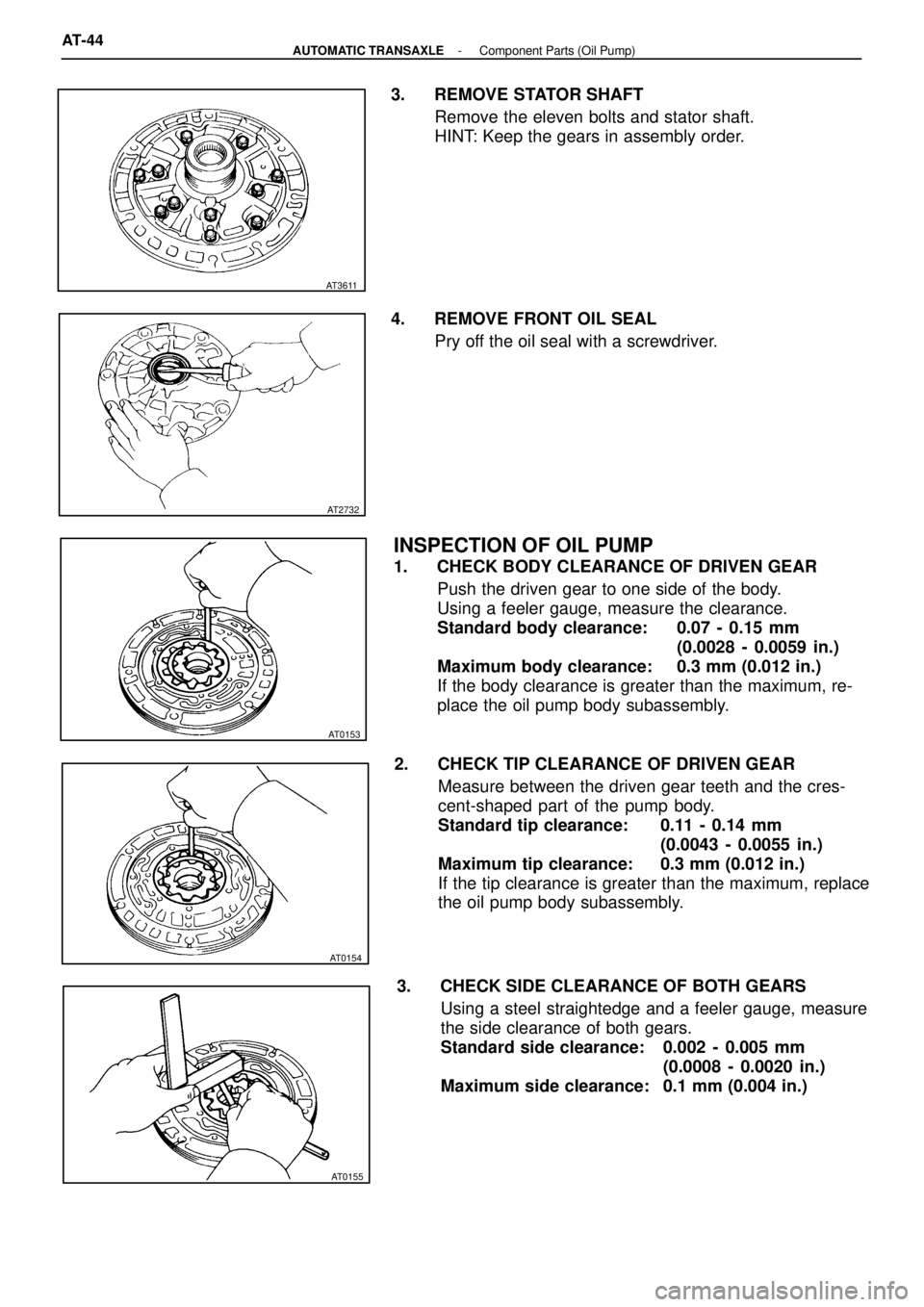
AT2732
AT0153
AT0154
AT0155 AT3611
3. REMOVE STATOR SHAFT
Remove the eleven bolts and stator shaft.
HINT: Keep the gears in assembly order.
4. REMOVE FRONT OIL SEAL
Pry off the oil seal with a screwdriver.
INSPECTION OF OIL PUMP
1. CHECK BODY CLEARANCE OF DRIVEN GEAR
Push the driven gear to one side of the body.
Using a feeler gauge, measure the clearance.
Standard body clearance: 0.07 - 0.15 mm
(0.0028 - 0.0059 in.)
Maximum body clearance: 0.3 mm (0.012 in.)
If the body clearance is greater than the maximum, re-
place the oil pump body subassembly.
2. CHECK TIP CLEARANCE OF DRIVEN GEAR
Measure between the driven gear teeth and the cres-
cent-shaped part of the pump body.
Standard tip clearance: 0.11 - 0.14 mm
(0.0043 - 0.0055 in.)
Maximum tip clearance: 0.3 mm (0.012 in.)
If the tip clearance is greater than the maximum, replace
the oil pump body subassembly.
3. CHECK SIDE CLEARANCE OF BOTH GEARS
Using a steel straightedge and a feeler gauge, measure
the side clearance of both gears.
Standard side clearance: 0.002 - 0.005 mm
(0.0008 - 0.0020 in.)
Maximum side clearance: 0.1 mm (0.004 in.)
AT-44- AUTOMATIC TRANSAXLEComponent Parts (Oil Pump)
Page 60 of 2389
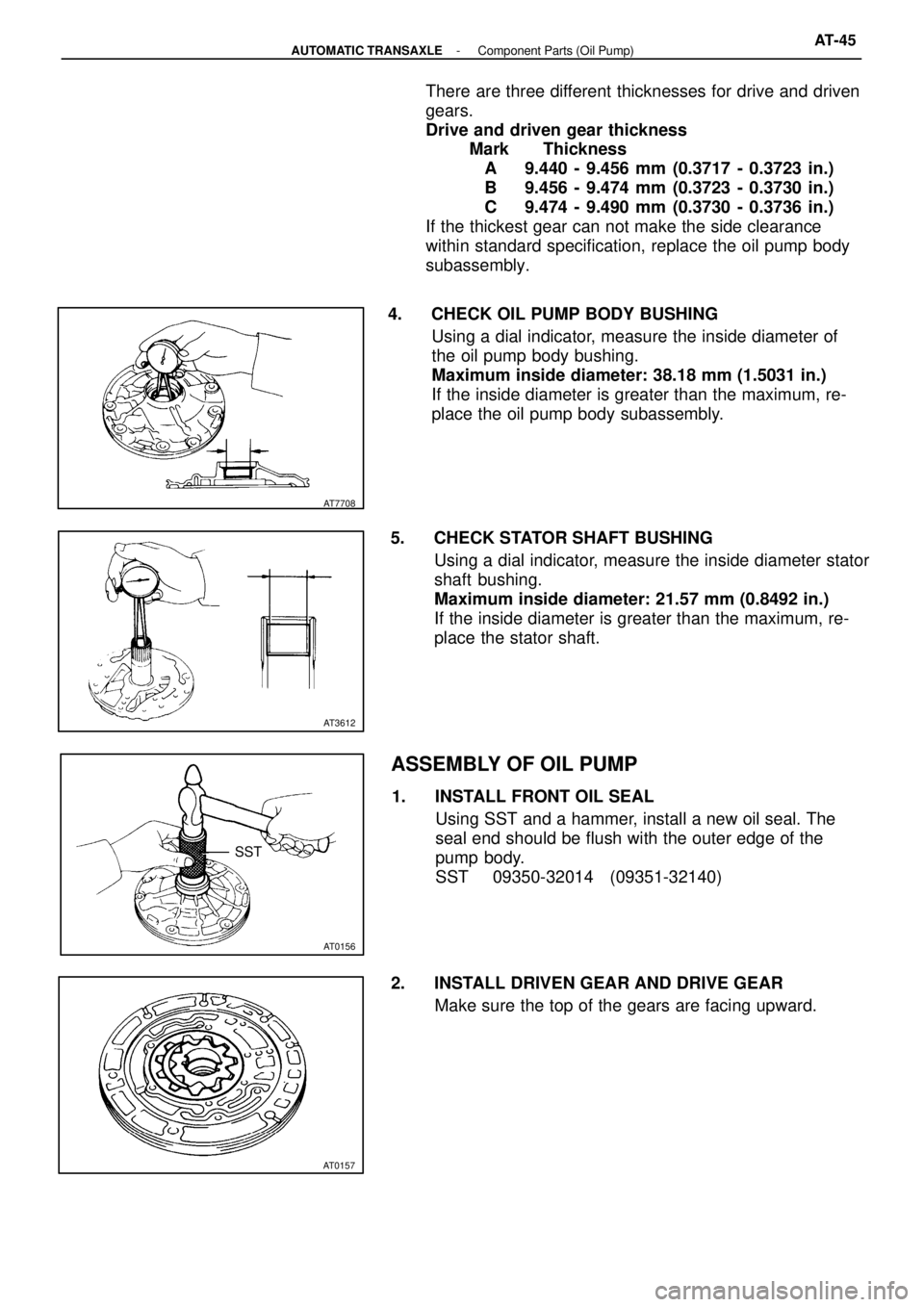
AT3612
AT0156
SST
AT0157AT7708
There are three different thicknesses for drive and driven
gears.
Drive and driven gear thickness
Mark Thickness
A 9.440 - 9.456 mm (0.3717 - 0.3723 in.)
B 9.456 - 9.474 mm (0.3723 - 0.3730 in.)
C 9.474 - 9.490 mm (0.3730 - 0.3736 in.)
If the thickest gear can not make the side clearance
within standard specification, replace the oil pump body
subassembly.
4. CHECK OIL PUMP BODY BUSHING
Using a dial indicator, measure the inside diameter of
the oil pump body bushing.
Maximum inside diameter: 38.18 mm (1.5031 in.)
If the inside diameter is greater than the maximum, re-
place the oil pump body subassembly.
5. CHECK STATOR SHAFT BUSHING
Using a dial indicator, measure the inside diameter stator
shaft bushing.
Maximum inside diameter: 21.57 mm (0.8492 in.)
If the inside diameter is greater than the maximum, re-
place the stator shaft.
ASSEMBLY OF OIL PUMP
1. INSTALL FRONT OIL SEAL
Using SST and a hammer, install a new oil seal. The
seal end should be flush with the outer edge of the
pump body.
SST 09350-32014 (09351-32140)
2. INSTALL DRIVEN GEAR AND DRIVE GEAR
Make sure the top of the gears are facing upward.
- AUTOMATIC TRANSAXLEComponent Parts (Oil Pump)AT-45
Page 61 of 2389
AT3609
AT3610
AT0161 AT3611
3. INSTALL STATOR SHAFT TO PUMP BODY
(a) Align the stator shaft with each bolt hole.
(b) Torque the eleven bolts.
Torque: 100 kg-cm (7 ft-lb, 10 N-m)
4. INSTALL THRUST WASHER
(a) Coat the thrust washer with petroleum jelly.
(b) Align the tab of the washer with the hollow of the
pump body.
5. INSTALL OIL SEAL RINGS
Install the two oil seal rings to the stator shaft back
side.
NOTICE: Do not spread the ring ends more than nec-
essary.
HINT: After installing the oil seal rings, check that they
move smoothly.
6. CHECK PUMP DRIVE GEAR ROTATION
Turn the drive gear with two screwdrivers and make
sure it rotates smoothly.
NOTICE: Be careful not to damage the oil seal lip.
AT-46- AUTOMATIC TRANSAXLEComponent Parts (Oil Pump)
Page 62 of 2389
AT7709
SST
AT7710AT3613
r Non-reusable partPlateDiscFlangeSnap Ring Thrust Washer Clutch DrumPistonr O-RingSnap Ring Piston Return
Spring
Direct Clutch
COMPONENTS
DISASSEMBLY OF DIRECT CLUTCH
1. CHECK PISTON STROKE OF DIRECT CLUTCH
(a) Install the direct clutch on the oil pump.
(b) Using a dial indicator (long type pick or SST),
measure the direct clutch piston stroke applying
and releasing the compressed air (4 - 8 kg/cm
2,
57 - 114 psi, 392 - 785 kPa) as shown.
SST 09350-32014 (09351-32190)
Piston stroke: A540E 0.91 - 1.35 mm
(0.0358 - 0.0531 in.)
A540H 1.11 - 1.47 mm
(0.0437 - 0.0579 in.)
If the piston stroke is greater than the maximum, inspect
each component.
- AUTOMATIC TRANSAXLEComponent Parts (Direct Clutch)AT-47
Page 63 of 2389
AT0163
AT2733
SST
AT3614
AT0165
AT2735
2. REMOVE SNAP RING FROM CLUTCH DRUM
3. REMOVE FLANGE, DISCS AND PLATES
4. REMOVE PISTON RETURN SPRING
(a) Place SST on the spring retainer and compress
the springs with a shop press.
SST 09350-32014 (09351-32070)
(b) Remove the snap ring with snap ring pliers.
(c) Remove the piston return spring.
5. REMOVE CLUTCH PISTON
(a) Install the direct clutch onto the oil pump.
(b) Apply compressed air to the oil pump to remove
the piston. (If the piston does not come out com-
pletely, use needle-nose pliers to remove it.)
(c) Remove the direct clutch from the oil pump.
(d) Remove the two O-rings from the piston.
AT-48- AUTOMATIC TRANSAXLEComponent Parts (Direct Clutch)
Page 64 of 2389
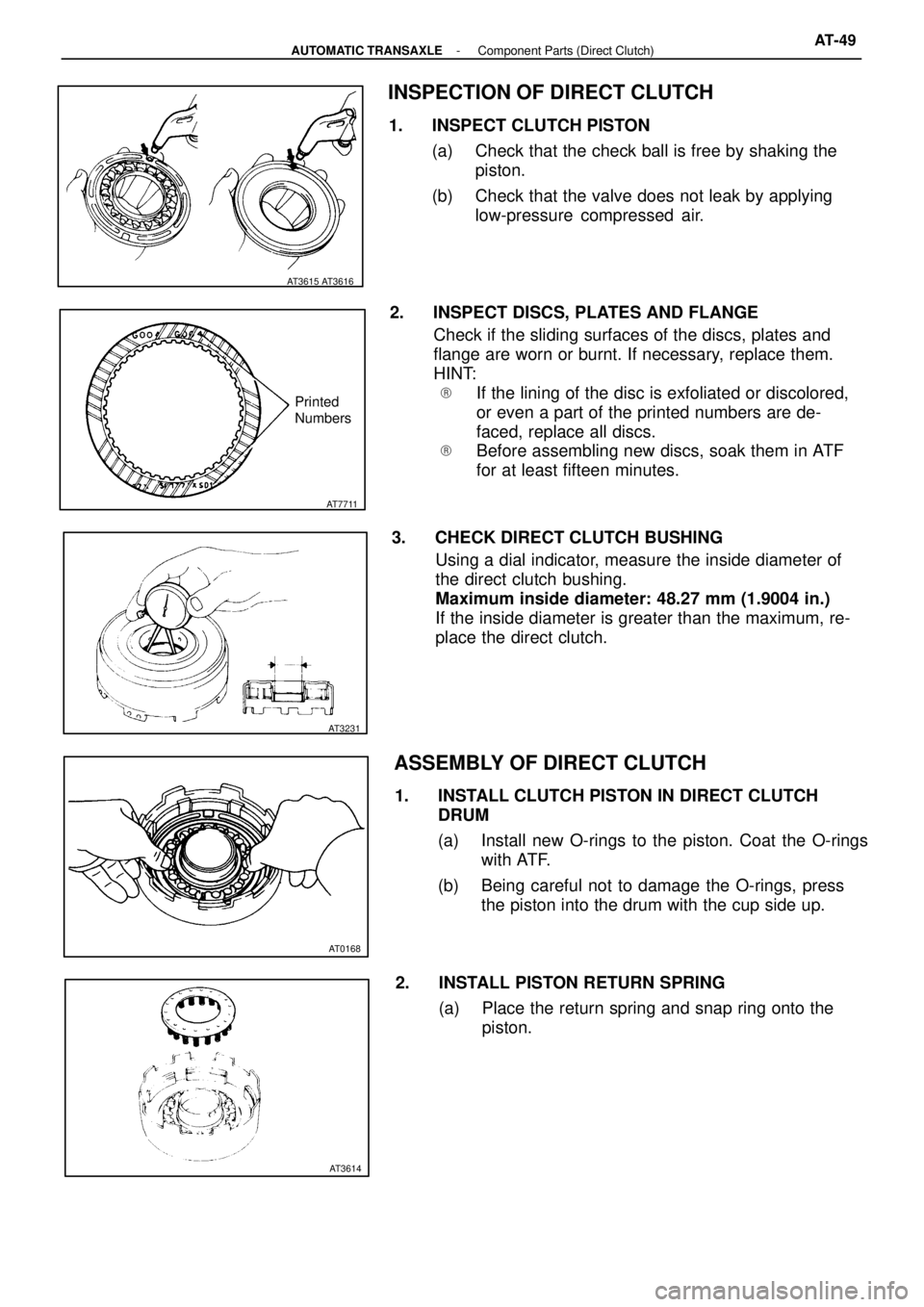
AT7711
Printed
Numbers
AT3231
AT0168
AT3614 AT3615 AT3616
INSPECTION OF DIRECT CLUTCH
1. INSPECT CLUTCH PISTON
(a) Check that the check ball is free by shaking the
piston.
(b) Check that the valve does not leak by applying
low-pressure compressed air.
2. INSPECT DISCS, PLATES AND FLANGE
Check if the sliding surfaces of the discs, plates and
flange are worn or burnt. If necessary, replace them.
HINT:
If the lining of the disc is exfoliated or discolored,
or even a part of the printed numbers are de-
faced, replace all discs.
Before assembling new discs, soak them in ATF
for at least fifteen minutes.
3. CHECK DIRECT CLUTCH BUSHING
Using a dial indicator, measure the inside diameter of
the direct clutch bushing.
Maximum inside diameter: 48.27 mm (1.9004 in.)
If the inside diameter is greater than the maximum, re-
place the direct clutch.
ASSEMBLY OF DIRECT CLUTCH
1. INSTALL CLUTCH PISTON IN DIRECT CLUTCH
DRUM
(a) Install new O-rings to the piston. Coat the O-rings
with ATF.
(b) Being careful not to damage the O-rings, press
the piston into the drum with the cup side up.
2. INSTALL PISTON RETURN SPRING
(a) Place the return spring and snap ring onto the
piston.
- AUTOMATIC TRANSAXLEComponent Parts (Direct Clutch)AT-49