Page 1905 of 2389
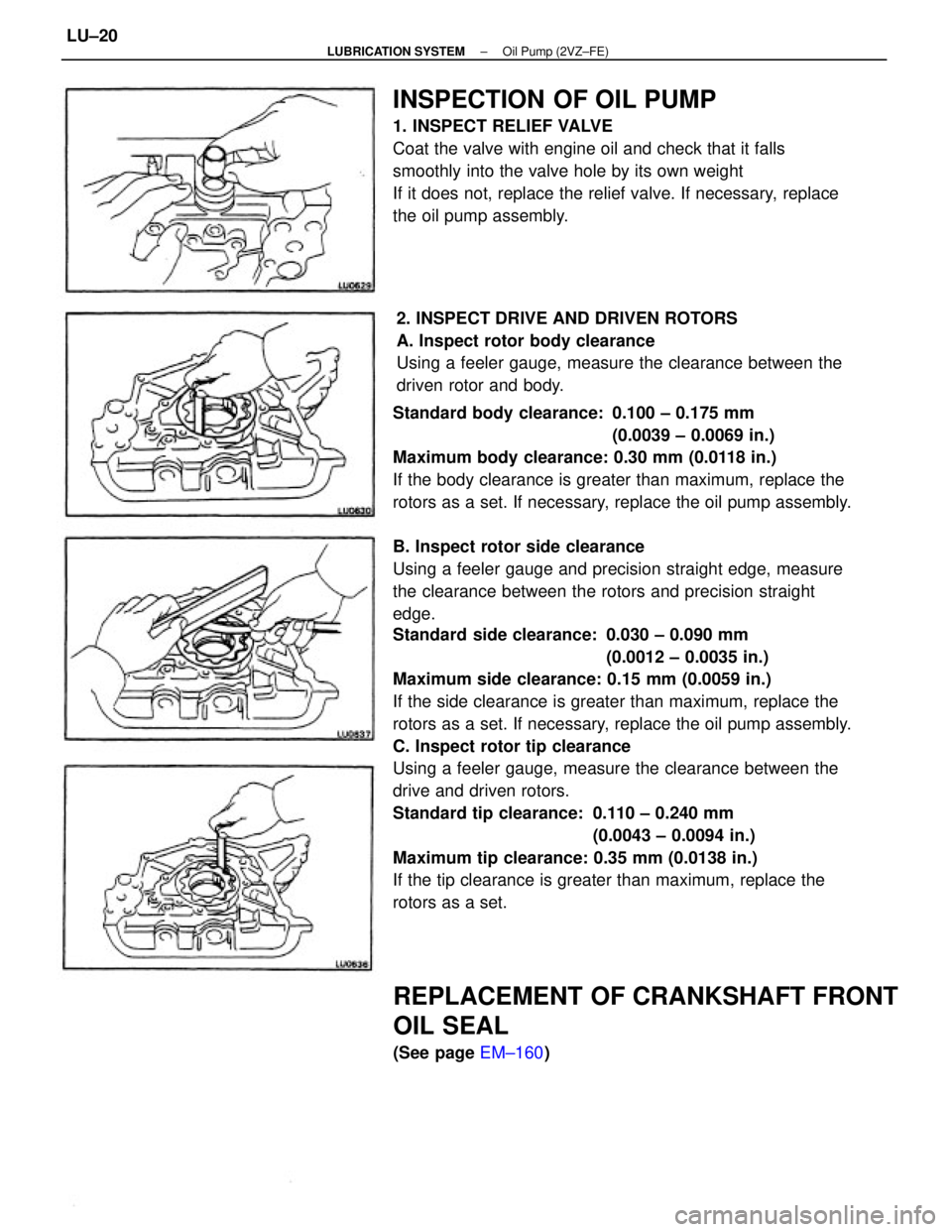
Standard side clearance: 0.030 ± 0.090 mm
(0.0012 ± 0.0035 in.)
Maximum side clearance: 0.15 mm (0.0059 in.)
If the side clearance is greater than maximum, replace the
rotors as a set. If necessary, replace the oil pump assembly.
C. Inspect rotor tip clearance
Using a feeler gauge, measure the clearance between the
drive and driven rotors.
Standard tip clearance: 0.110 ± 0.240 mm
(0.0043 ± 0.0094 in.)
Maximum tip clearance: 0.35 mm (0.0138 in.)
If the tip clearance is greater than maximum, replace the
rotors as a set. Standard body clearance: 0.100 ± 0.175 mm
(0.0039 ± 0.0069 in.)
Maximum body clearance: 0.30 mm (0.0118 in.)
If the body clearance is greater than maximum, replace the
rotors as a set. If necessary, replace the oil pump assembly.
B. Inspect rotor side clearance
Using a feeler gauge and precision straight edge, measure
the clearance between the rotors and precision straight
edge.
INSPECTION OF OIL PUMP
1. INSPECT RELIEF VALVE
Coat the valve with engine oil and check that it falls
smoothly into the valve hole by its own weight
If it does not, replace the relief valve. If necessary, replace
the oil pump assembly.
2. INSPECT DRIVE AND DRIVEN ROTORS
A. Inspect rotor body clearance
Using a feeler gauge, measure the clearance between the
driven rotor and body.
REPLACEMENT OF CRANKSHAFT FRONT
OIL SEAL
(See page EM±160)
± LUBRICATION SYSTEMOil Pump (2VZ±FE)LU±20
Page 1906 of 2389
ASSEMBLY OF OIL PUMP
(See page LU±19)
1. INSTALL DRIVE AND DRIVEN ROTORS
(a) Place the drive and driven rotors into pump body with the
marks facing the pump body cover side..
2. INSTALL RELIEF VALVE
(a) Insert the relief valve, spring and retainer into the pump body
hole.
(b) Using snap ring pliers, install the snap ring.(b) Install the pump body cover with the eight screws.
± LUBRICATION SYSTEMOil Pump (2VZ±FE)LU±21
Page 1907 of 2389
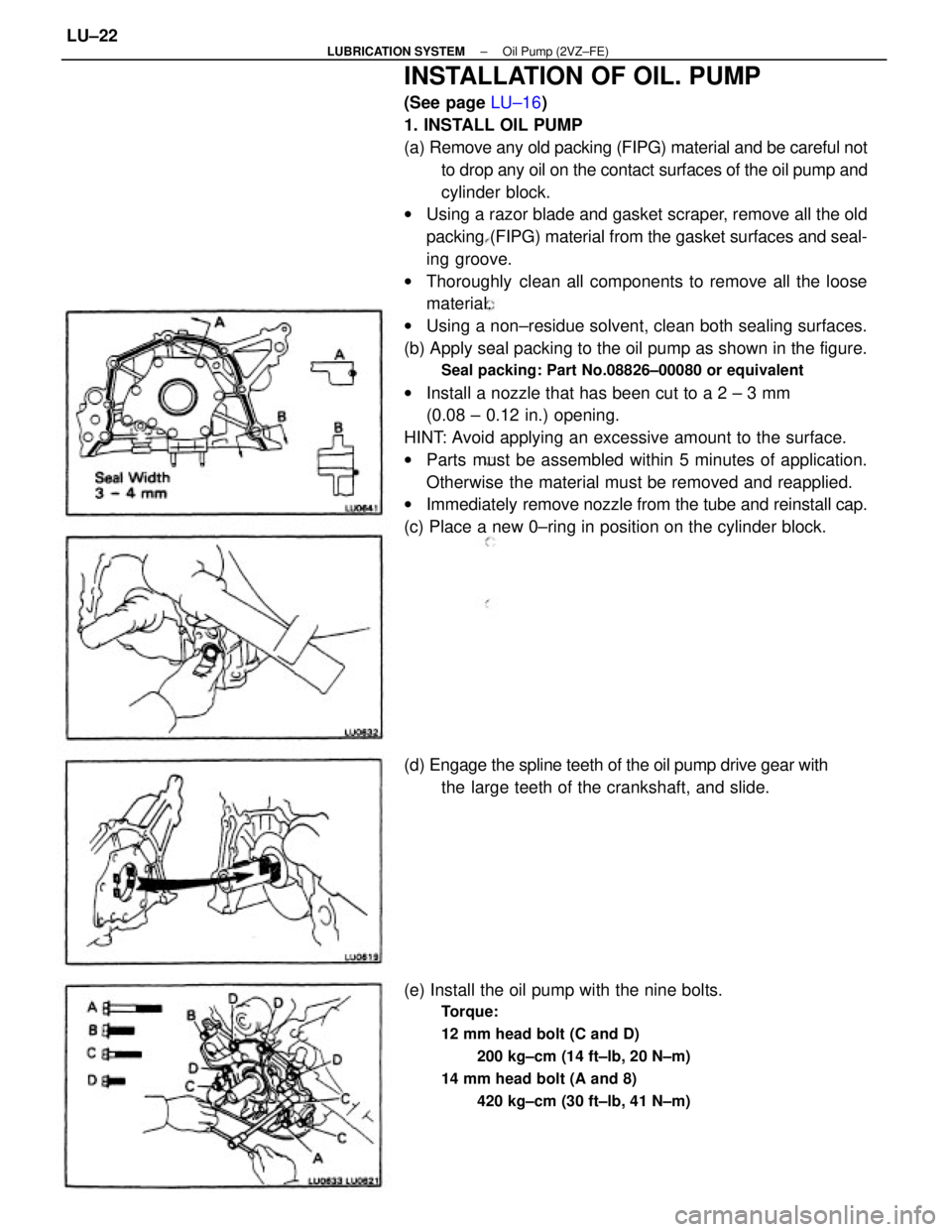
INSTALLATION OF OIL. PUMP
(See page LU±16)
1. INSTALL OIL PUMP
(a) Remove any old packing (FIPG) material and be careful not
to drop any oil on the contact surfaces of the oil pump and
cylinder block.
wUsing a razor blade and gasket scraper, remove all the old
packing (FIPG) material from the gasket surfaces and seal-
ing groove.
wThoroughly clean all components to remove all the loose
material.
wUsing a non±residue solvent, clean both sealing surfaces.
(b) Apply seal packing to the oil pump as shown in the figure.
Seal packing: Part No.08826±00080 or equivalent
wInstall a nozzle that has been cut to a 2 ± 3 mm
(0.08 ± 0.12 in.) opening.
HINT: Avoid applying an excessive amount to the surface.
wParts must be assembled within 5 minutes of application.
Otherwise the material must be removed and reapplied.
wImmediately remove nozzle from the tube and reinstall cap.
(c) Place a new 0±ring in position on the cylinder block.
(e) Install the oil pump with the nine bolts.
Torque:
12 mm head bolt (C and D)
200 kg±cm (14 ft±lb, 20 N±m)
14 mm head bolt (A and 8)
420 kg±cm (30 ft±lb, 41 N±m)
(d) Engage the spline teeth of the oil pump drive gear with
the large teeth of the crankshaft, and slide.
± LUBRICATION SYSTEMOil Pump (2VZ±FE)LU±22
Page 1908 of 2389
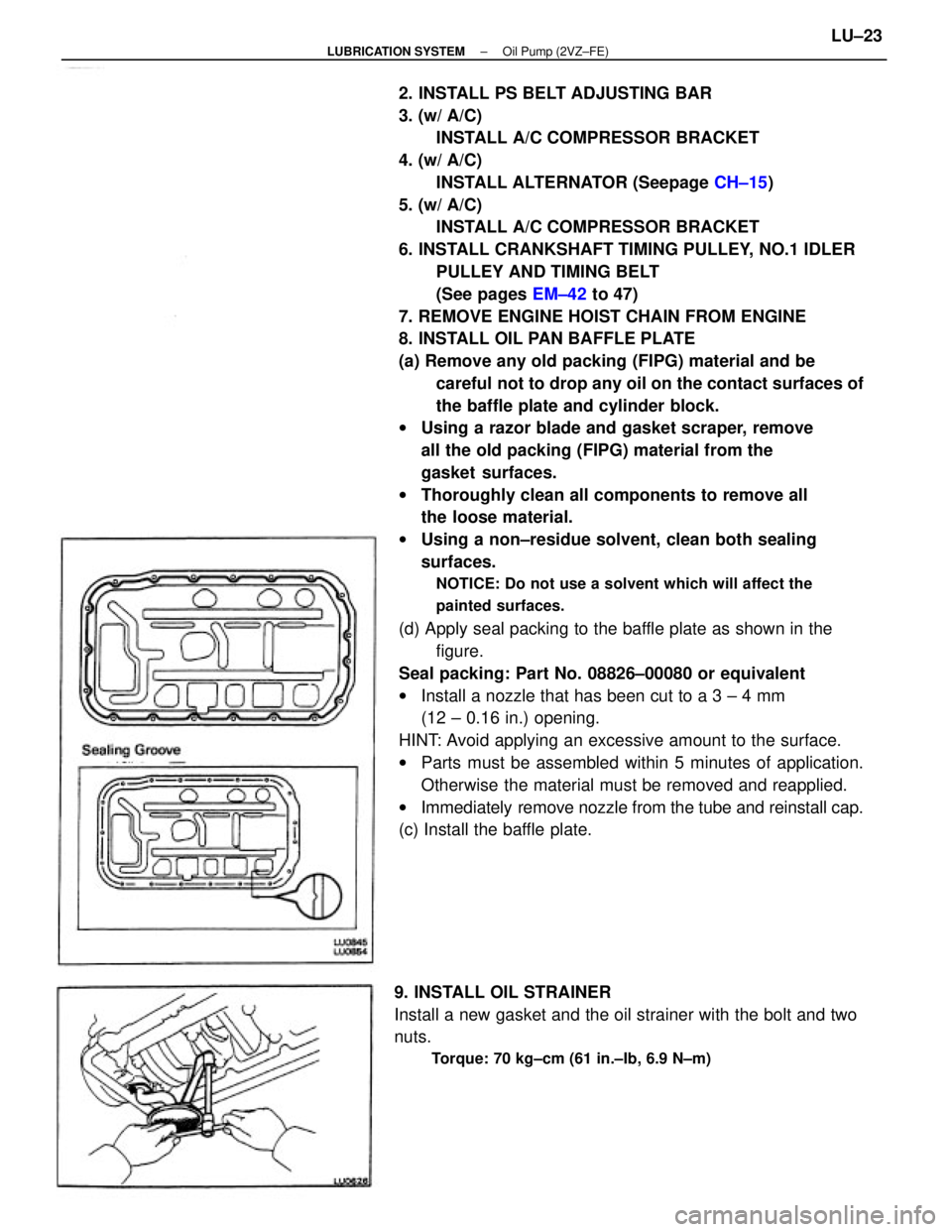
2. INSTALL PS BELT ADJUSTING BAR
3. (w/ A/C)
INSTALL A/C COMPRESSOR BRACKET
4. (w/ A/C)
INSTALL ALTERNATOR (Seepage CH±15)
5. (w/ A/C)
INSTALL A/C COMPRESSOR BRACKET
6. INSTALL CRANKSHAFT TIMING PULLEY, NO.1 IDLER
PULLEY AND TIMING BELT
(See pages EM±42 to 47)
7. REMOVE ENGINE HOIST CHAIN FROM ENGINE
8. INSTALL OIL PAN BAFFLE PLATE
(a) Remove any old packing (FIPG) material and be
careful not to drop any oil on the contact surfaces of
the baffle plate and cylinder block.
wUsing a razor blade and gasket scraper, remove
all the old packing (FIPG) material from the
gasket surfaces.
wThoroughly clean all components to remove all
the loose material.
wUsing a non±residue solvent, clean both sealing
surfaces.
NOTICE: Do not use a solvent which will affect the
painted surfaces.
(d) Apply seal packing to the baffle plate as shown in the
figure.
Seal packing: Part No. 08826±00080 or equivalent
wInstall a nozzle that has been cut to a 3 ± 4 mm
(12 ± 0.16 in.) opening.
HINT: Avoid applying an excessive amount to the surface.
wParts must be assembled within 5 minutes of application.
Otherwise the material must be removed and reapplied.
wImmediately remove nozzle from the tube and reinstall cap.
(c) Install the baffle plate.
9. INSTALL OIL STRAINER
Install a new gasket and the oil strainer with the bolt and two
nuts.
Torque: 70 kg±cm (61 in.±Ib, 6.9 N±m)
± LUBRICATION SYSTEMOil Pump (2VZ±FE)LU±23
Page 1909 of 2389
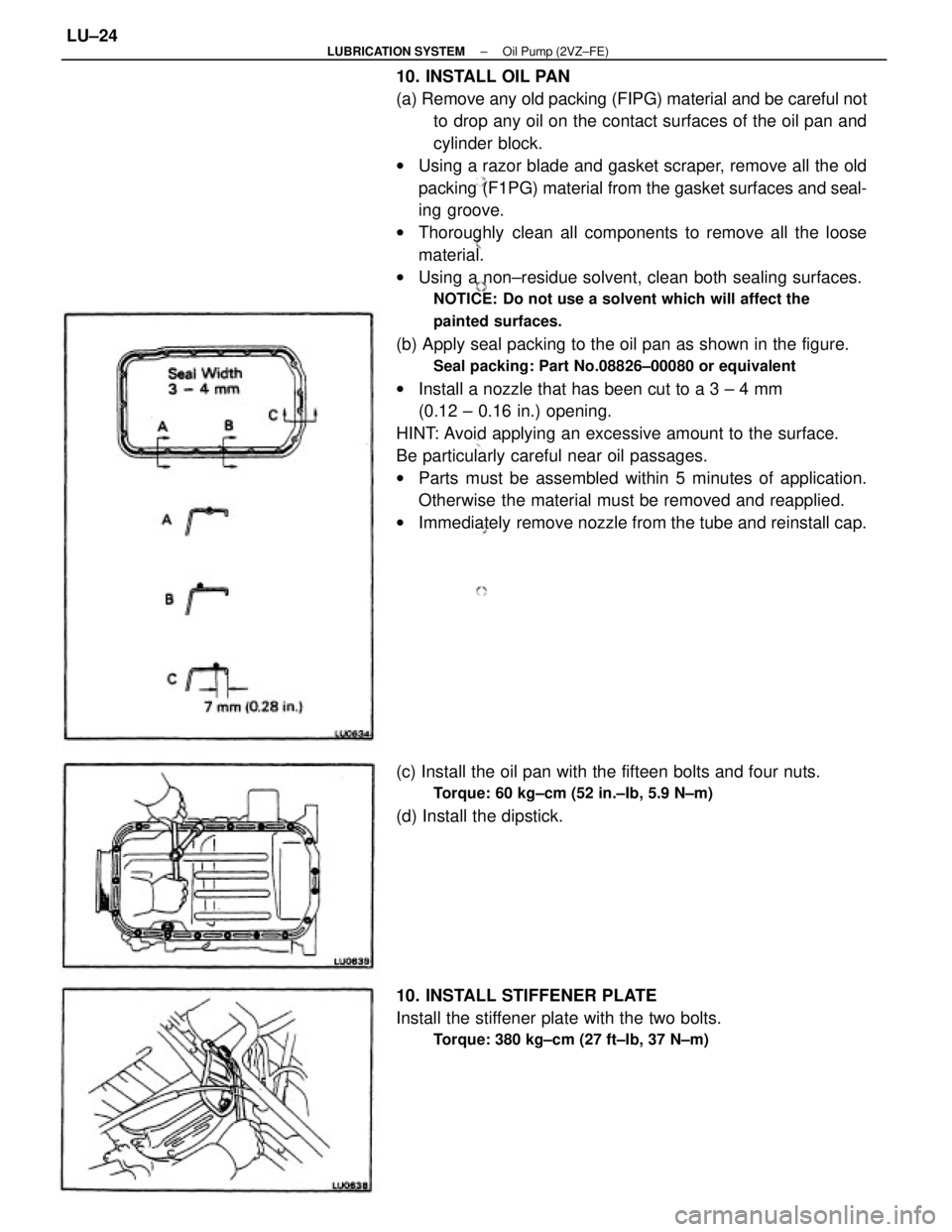
10. INSTALL OIL PAN
(a) Remove any old packing (FIPG) material and be careful not
to drop any oil on the contact surfaces of the oil pan and
cylinder block.
wUsing a razor blade and gasket scraper, remove all the old
packing (F1PG) material from the gasket surfaces and seal-
ing groove.
wThoroughly clean all components to remove all the loose
material.
wUsing a non±residue solvent, clean both sealing surfaces.
NOTICE: Do not use a solvent which will affect the
painted surfaces.
(b) Apply seal packing to the oil pan as shown in the figure.
Seal packing: Part No.08826±00080 or equivalent
wInstall a nozzle that has been cut to a 3 ± 4 mm
(0.12 ± 0.16 in.) opening.
HINT: Avoid applying an excessive amount to the surface.
Be particularly careful near oil passages.
wParts must be assembled within 5 minutes of application.
Otherwise the material must be removed and reapplied.
wImmediately remove nozzle from the tube and reinstall cap.
(c) Install the oil pan with the fifteen bolts and four nuts.
Torque: 60 kg±cm (52 in.±Ib, 5.9 N±m)
(d) Install the dipstick.
10. INSTALL STIFFENER PLATE
Install the stiffener plate with the two bolts.
Torque: 380 kg±cm (27 ft±Ib, 37 N±m)
± LUBRICATION SYSTEMOil Pump (2VZ±FE)LU±24
Page 1910 of 2389
11. INSTALL FRONT ENGINE MOUNTING BRACKET AND
INSULATOR
(See step 7 on page EM±171)
12. INSTALL ENGINE MOUNTING CENTER MEMBER
(See step 10 on page EM±171)
13. REMOVE FRONT EXHAUST PIPE
(See step 14 on page EM±172)
14. INSTALL SUSPENSION LOWER CROSSMEMBER
(See step 15 on page EM±172)
15. INSTALL ENGINE UNDER COVERS
16. LOWER VEHICLE
17. FILL WITH ENGINE OIL (See page LU±8)
18. START ENGINE AND CHECK FOR LEAKS
19. RECHECK ENGINE OIL LEVEL (See page LU±6)
20. INSTALL HOOD
± LUBRICATION SYSTEMOil Pump (2VZ±FE)LU±25
Page 1911 of 2389
MAINTENANCE
± MAINTENANCEMA±1
Page 1912 of 2389
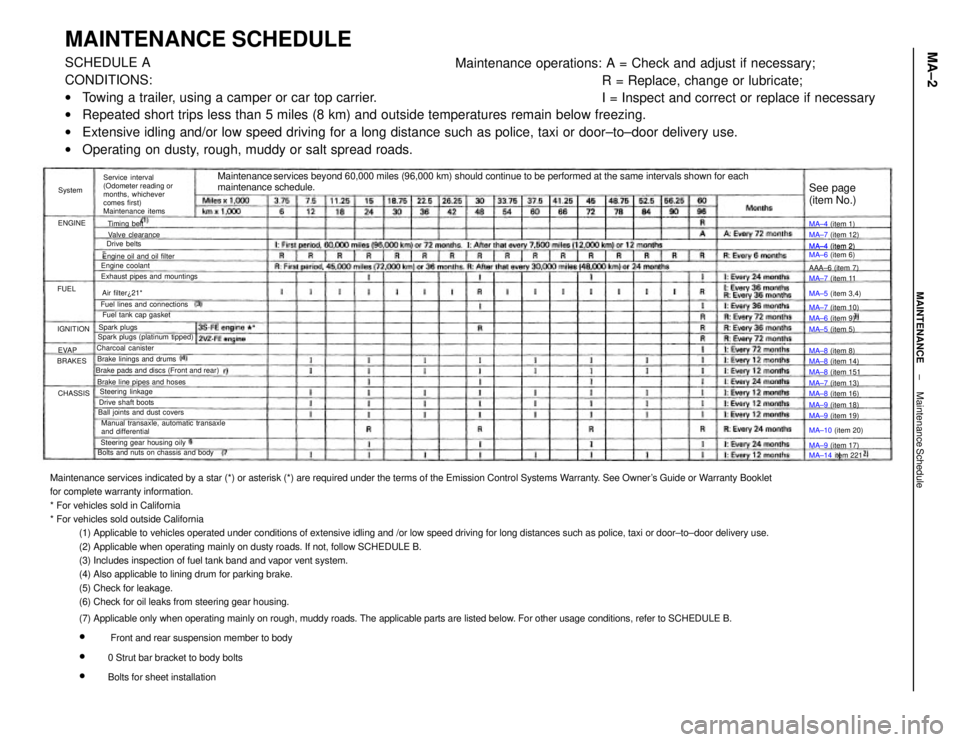
Maintenance services indicated by a star (*) or asterisk (*) are required under the terms of the Emission Control Systems Warranty. See Owner's Guide or Warranty Booklet
for complete warranty information.
* For vehicles sold in California
* For vehicles sold outside California
(1) Applicable to vehicles operated under conditions of extensive idling and /or low speed driving for long distances such as police, taxi or door±to±door delivery use.
(2) Applicable when operating mainly on dusty roads. If not, follow SCHEDULE B.
(3) Includes inspection of fuel tank band and vapor vent system.
(4) Also applicable to lining drum for parking brake.
(5) Check for leakage.
(6) Check for oil leaks from steering gear housing.
(7) Applicable only when operating mainly on rough, muddy roads. The applicable parts are listed below. For other usage conditions, refer to SCHEDULE B.
w
Front and rear suspension member to body
w
0 Strut bar bracket to body bolts
w
Bolts for sheet installation
MAINTENANCE SCHEDULESCHEDULE A
CONDITIONS:
wTowing a trailer, using a camper or car top carrier.
wRepeated short trips less than 5 miles (8 km) and outside temperatures remain below freezing.
wExtensive idling and/or low speed driving for a long distance such as police, taxi or door±to±door delivery use.
wOperating on dusty, rough, muddy or salt spread roads.Maintenance operations: A = Check and adjust if necessary;
R = Replace, change or lubricate;
I = Inspect and correct or replace if necessary
Maintenance services beyond 60,000 miles (96,000 km) should continue to be performed at the same intervals shown for each
maintenance schedule.
Service interval
(Odometer reading or
months, whichever
comes first)
Maintenance items
Manual transaxle, automatic transaxle
and differential Brake pads and discs (Front and rear)
Bolts and nuts on chassis and bodyExhaust pipes and mountings
Steering gear housing oily Brake line pipes and hosesFuel lines and connections
Ball joints and dust coversEngine oil and oil filter
Spark plugs (platinum tipped)MA±4 (item 2)
MA±6 (item 6)
Brake linings and drumsFuel tank cap gasket
Drive shaft boots
MA±14 item 221 MA±10 (item 20) MA±5 (item 3,4)
Steering linkageMA±7 (item 12)
MA±8 (item 14) Valve clearance
MA±8 (item 16)
MA±9 (item 19) MA±7 (item 13) MA±7 (item 11
MA±7 (item 10)
MA±9 (item 18) Charcoal canister
MA±9 (item 17) MA±8 (item 151
See page
(item No.)
Engine coolant
MA±6 (item 9) MA±4 (item 1)
MA±4 (item 2)
MA±5 (item 5)
MA±8 (item 8) AAA±6 (item 7)
Air filter¿21*
Spark plugsTiming belt
Drive belts
IGNITION
CHASSIS BRAKESENGINESystem
EVAP FUEL
± MAINTENANCEMaintenance ScheduleMA±2