Page 1329 of 2389
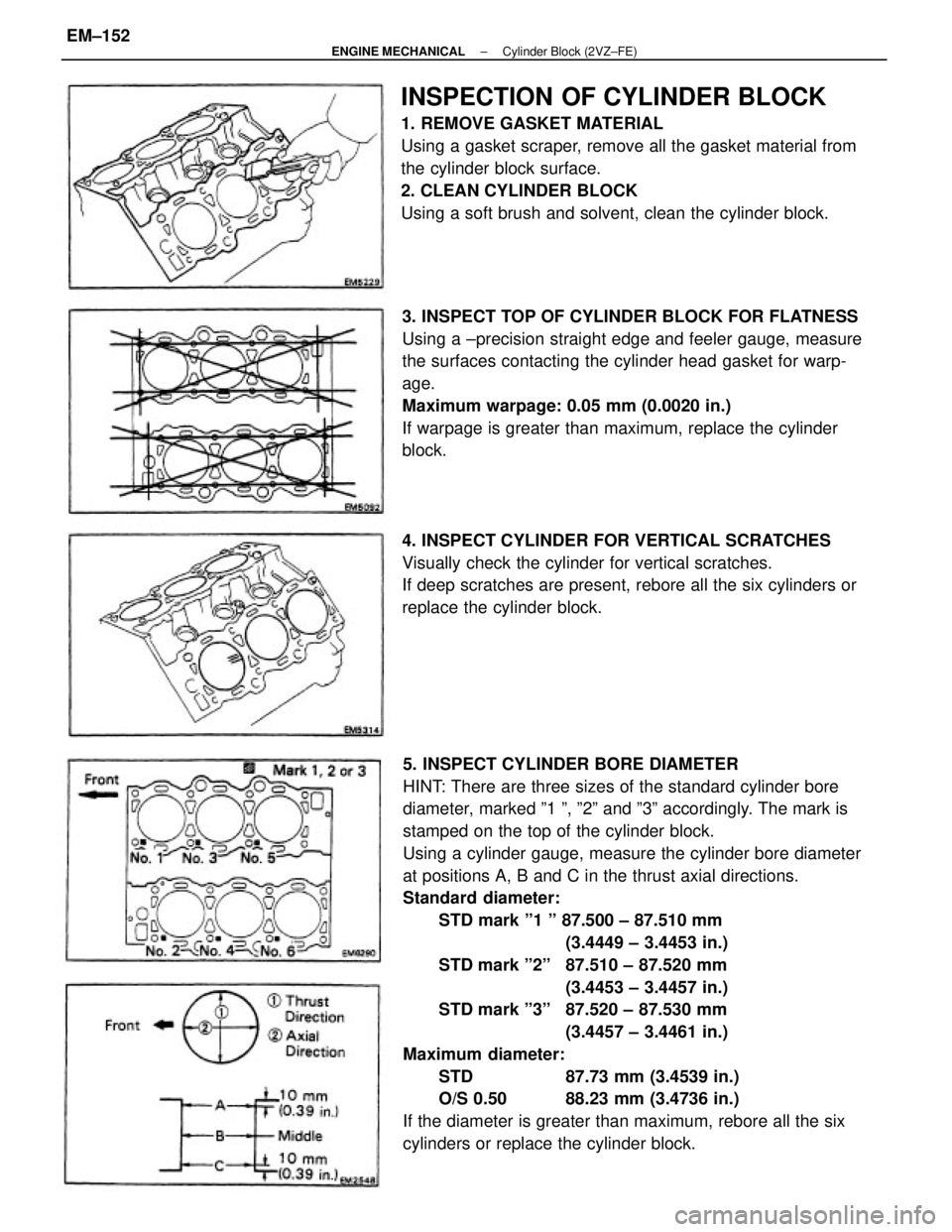
5. INSPECT CYLINDER BORE DIAMETER
HINT: There are three sizes of the standard cylinder bore
diameter, marked º1 º, º2º and º3º accordingly. The mark is
stamped on the top of the cylinder block.
Using a cylinder gauge, measure the cylinder bore diameter
at positions A, B and C in the thrust axial directions.
Standard diameter:
STD mark º1 º 87.500 ± 87.510 mm
(3.4449 ± 3.4453 in.)
STD mark º2º 87.510 ± 87.520 mm
(3.4453 ± 3.4457 in.)
STD mark º3º 87.520 ± 87.530 mm
(3.4457 ± 3.4461 in.)
Maximum diameter:
STD 87.73 mm (3.4539 in.)
O/S 0.50 88.23 mm (3.4736 in.)
If the diameter is greater than maximum, rebore all the six
cylinders or replace the cylinder block.
INSPECTION OF CYLINDER BLOCK
1. REMOVE GASKET MATERIAL
Using a gasket scraper, remove all the gasket material from
the cylinder block surface.
2. CLEAN CYLINDER BLOCK
Using a soft brush and solvent, clean the cylinder block.
3. INSPECT TOP OF CYLINDER BLOCK FOR FLATNESS
Using a ±precision straight edge and feeler gauge, measure
the surfaces contacting the cylinder head gasket for warp-
age.
Maximum warpage: 0.05 mm (0.0020 in.)
If warpage is greater than maximum, replace the cylinder
block.
4. INSPECT CYLINDER FOR VERTICAL SCRATCHES
Visually check the cylinder for vertical scratches.
If deep scratches are present, rebore all the six cylinders or
replace the cylinder block.
± ENGINE MECHANICALCylinder Block (2VZ±FE)EM±152
Page 1330 of 2389
DISASSEMBLY OF PISTON AND
CONNECTING ROD ASSEMBLIES
1. CHECK FIT BETWEEN PISTON AND PISTON PIN
Try to move the piston back and forth on the piston pin.
If any movement is felt, replace the piston and pin as a set.6. REMOVE CYLINDER RIDGE
If the wear is less than 0.2 mm (0.008 in.), use a ridge ream-
er to machine the piston ring ridge at the top of the cylinder.
2. REMOVE PISTON RINGS
(a) Using a piston ring expander, remove the two compres-
sion rings.
(b) Remove the two side rails and oil ring expander by
hand.
HINT: Arrange the rings in correct order only.
± ENGINE MECHANICALCylinder Block (2VZ±FE)EM±153
Page 1331 of 2389
INSPECTION OF PISTON AND
CONNECTING ROD ASSEMBLIES
1. CLEAN PISTON
(a) Using a gasket scraper, remove the carbon from the piston top. 3. DISCONNECT CONNECTING ROD FROM PISTON
Using SST, press out the piston pin from the piston.
SST 09221±25024 (09221±00020, 09221±00030,
09221±00181, 09221±00190, 09221±00200)
HINT:
wThe piston and pin are a matched set.
wArrange the pistons, pins, rings, connecting rods and
bearings in correct order.
(c) Using solvent and a brush, thoroughly clean the piston.
NOTICE: Do not use a wire brush.
(b) Using a groove cleaning or broken ring, clean the pis-
ton ring grooves.
± ENGINE MECHANICALCylinder Block (2112±FE)EM±154
Page 1332 of 2389
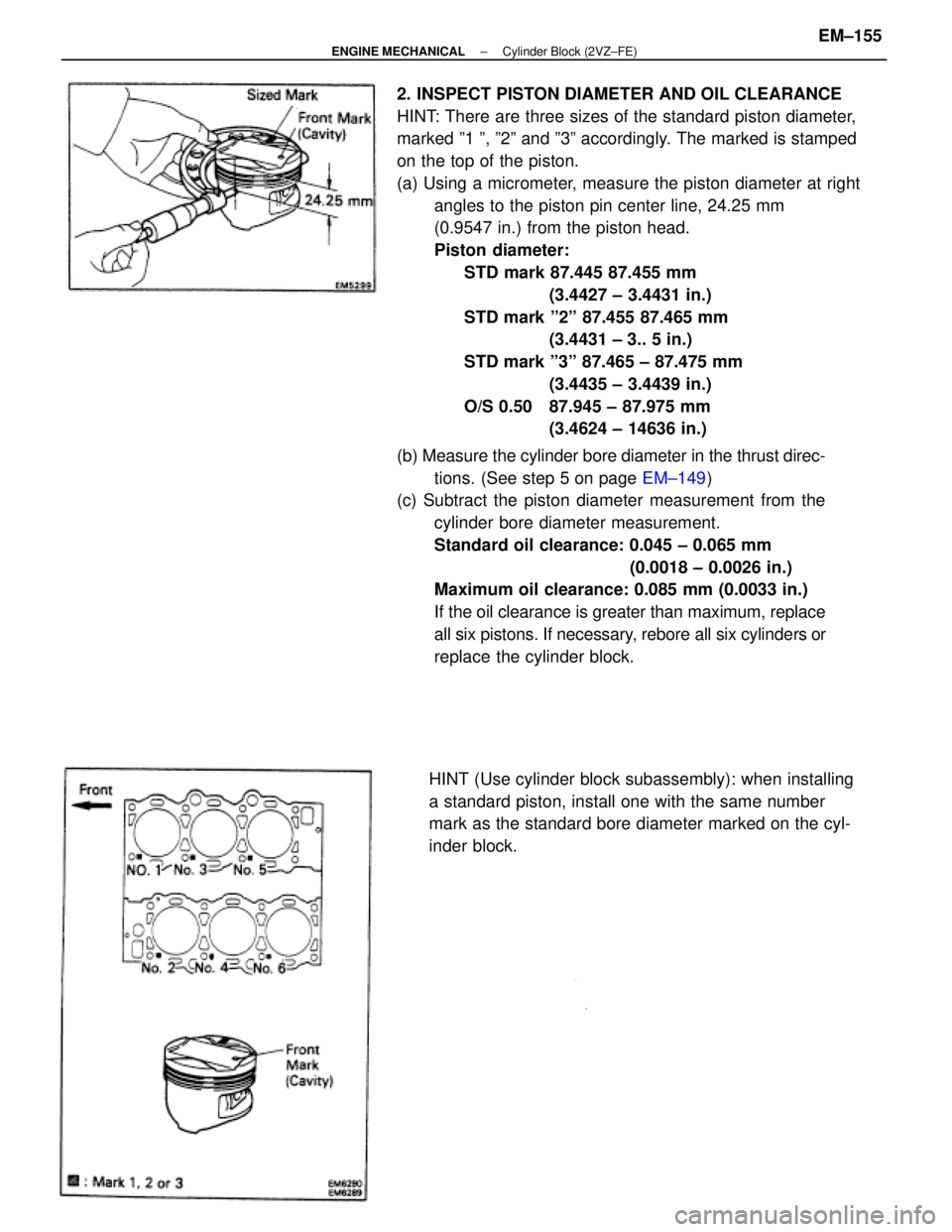
2. INSPECT PISTON DIAMETER AND OIL CLEARANCE
HINT: There are three sizes of the standard piston diameter,
marked º1 º, º2º and º3º accordingly. The marked is stamped
on the top of the piston.
(a) Using a micrometer, measure the piston diameter at right
angles to the piston pin center line, 24.25 mm
(0.9547 in.) from the piston head.
Piston diameter:
STD mark 87.445 87.455 mm
(3.4427 ± 3.4431 in.)
STD mark º2º 87.455 87.465 mm
(3.4431 ± 3.. 5 in.)
STD mark º3º 87.465 ± 87.475 mm
(3.4435 ± 3.4439 in.)
O/S 0.50 87.945 ± 87.975 mm
(3.4624 ± 14636 in.)
(b) Measure the cylinder bore diameter in the thrust direc-
tions. (See step 5 on page EM±149)
(c) Subtract the piston diameter measurement from the
cylinder bore diameter measurement.
Standard oil clearance: 0.045 ± 0.065 mm
(0.0018 ± 0.0026 in.)
Maximum oil clearance: 0.085 mm (0.0033 in.)
If the oil clearance is greater than maximum, replace
all six pistons. If necessary, rebore all six cylinders or
replace the cylinder block.
HINT (Use cylinder block subassembly): when installing
a standard piston, install one with the same number
mark as the standard bore diameter marked on the cyl-
inder block.
± ENGINE MECHANICALCylinder Block (2VZ±FE)EM±155
Page 1333 of 2389
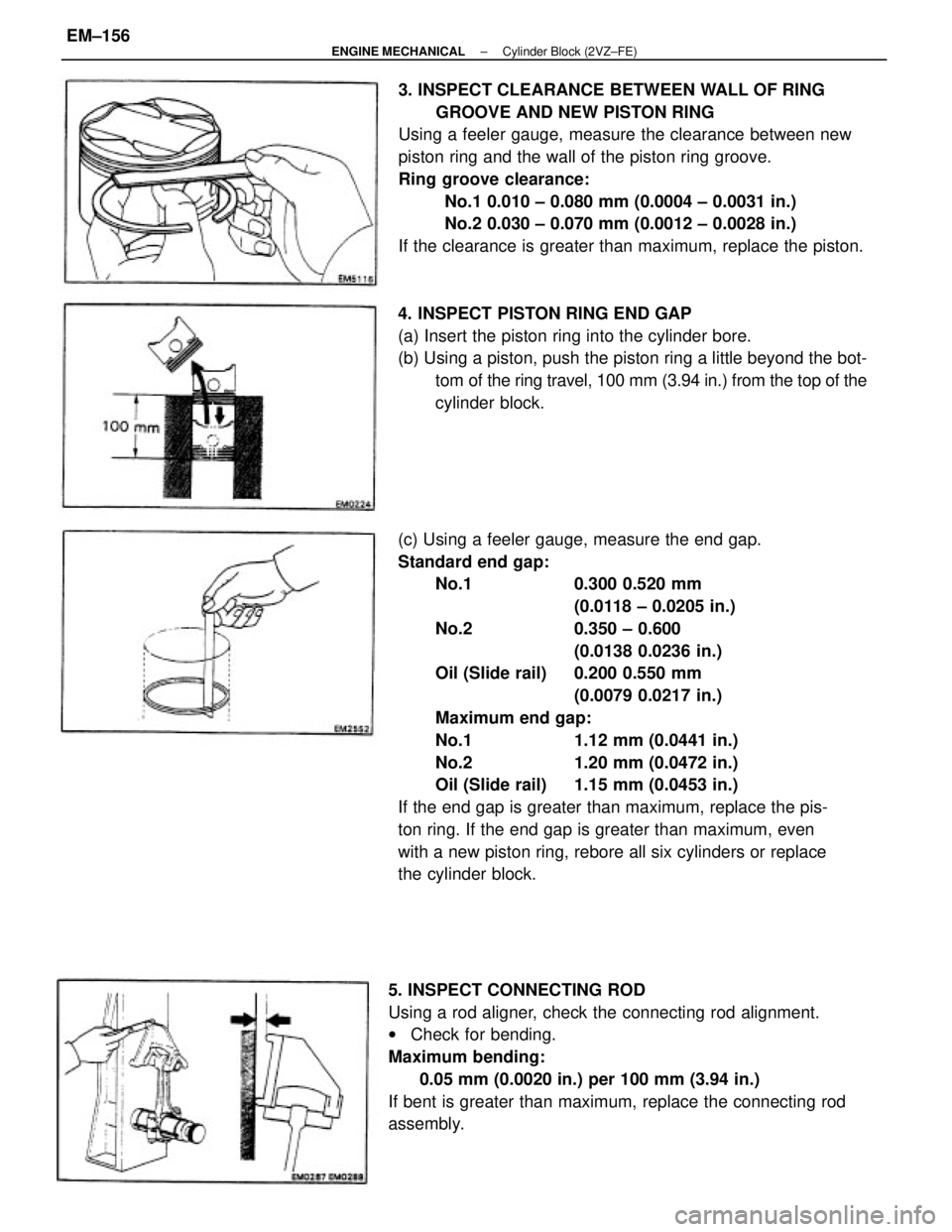
(c) Using a feeler gauge, measure the end gap.
Standard end gap:
No.1 0.300 0.520 mm
(0.0118 ± 0.0205 in.)
No.2 0.350 ± 0.600
(0.0138 0.0236 in.)
Oil (Slide rail) 0.200 0.550 mm
(0.0079 0.0217 in.)
Maximum end gap:
No.1 1.12 mm (0.0441 in.)
No.2 1.20 mm (0.0472 in.)
Oil (Slide rail) 1.15 mm (0.0453 in.)
If the end gap is greater than maximum, replace the pis-
ton ring. If the end gap is greater than maximum, even
with a new piston ring, rebore all six cylinders or replace
the cylinder block.3. INSPECT CLEARANCE BETWEEN WALL OF RING
GROOVE AND NEW PISTON RING
Using a feeler gauge, measure the clearance between new
piston ring and the wall of the piston ring groove.
Ring groove clearance:
No.1 0.010 ± 0.080 mm (0.0004 ± 0.0031 in.)
No.2 0.030 ± 0.070 mm (0.0012 ± 0.0028 in.)
If the clearance is greater than maximum, replace the piston.
5. INSPECT CONNECTING ROD
Using a rod aligner, check the connecting rod alignment.
wCheck for bending.
Maximum bending:
0.05 mm (0.0020 in.) per 100 mm (3.94 in.)
If bent is greater than maximum, replace the connecting rod
assembly.4. INSPECT PISTON RING END GAP
(a) Insert the piston ring into the cylinder bore.
(b) Using a piston, push the piston ring a little beyond the bot-
tom of the ring travel, 100 mm (3.94 in.) from the top of the
cylinder block.
± ENGINE MECHANICALCylinder Block (2VZ±FE)EM±156
Page 1334 of 2389
(b) If the cap nut cannot be turned easily, measure the outer
diameter of the compressed thread with calipers.
Standard outer diameter: 7.860 ± 8.000 mm
(0.3094 ± 0.3150 in.)
Minimum outer diameter: 7.60 mm (0.2992 in.)
HINT: If the location of this area cannot be judged by
visual inspection, measure the outer diameter at the loca-
tion shown in the illustration.
If the outer diameter is less than minimum, replace the con-
necting rod bolt and cap nut as a set.wCheck for twist.
Maximum twist:
0.15 mm (0.0059 in.) per 100 mm (3±94 in.)
If twist is greater than maximum, replace the connecting
rod assembly.
6. INSPECT CONNECTING ROD BOLTS
(a) Install the cap nut to the connecting rod bolt. Check that the
cap nut can be turned easily by hand to the end of the
thread.
± ENGINE MECHANICALCylinder Block (2VZ±FE)EM±157
Page 1335 of 2389
BORING OF CYLINDERS
HINT:
wBore all the six cylinders for the oversized piston outside di-
ameter.
wReplace the piston rings with ones to match the oversized
pistons.
1. KEEP OVERSIZED PISTONS
Oversized piston diameter:
O/S 0.50 87.945 ± 87.975 mm
(3.4624 ± 3.4636 in.)
2. CALCULATE AMOUNT TO BORE CYLINDER
(a) Using a micrometer, measure the piston diameter at right
angles to the piston pin center line, 24.25 mm
(0.9547 in.) from the piston head.
(b) Calculate the amount each cylinder is to be rebored as fol-
lows:
Size to be .rebored = P + C ± H
P= Piston diameter
C = Piston oil clearance
0.045 ± 0.065 mm (0.0018 ± 0.0026 in.)
H = Allowance for honing
0.02 mm (0.0008 in.) or less
3. BORE AND HONE CYLINDERS TO CALCULATED
DIMENSIONS
Maximum honing: 0.02 mm (0.0008 in.)
NOTICE: Excess honing will destroy the finished round-
ness.
± ENGINE MECHANICALCylinder Block (2VZ±FE)EM±158
Page 1336 of 2389
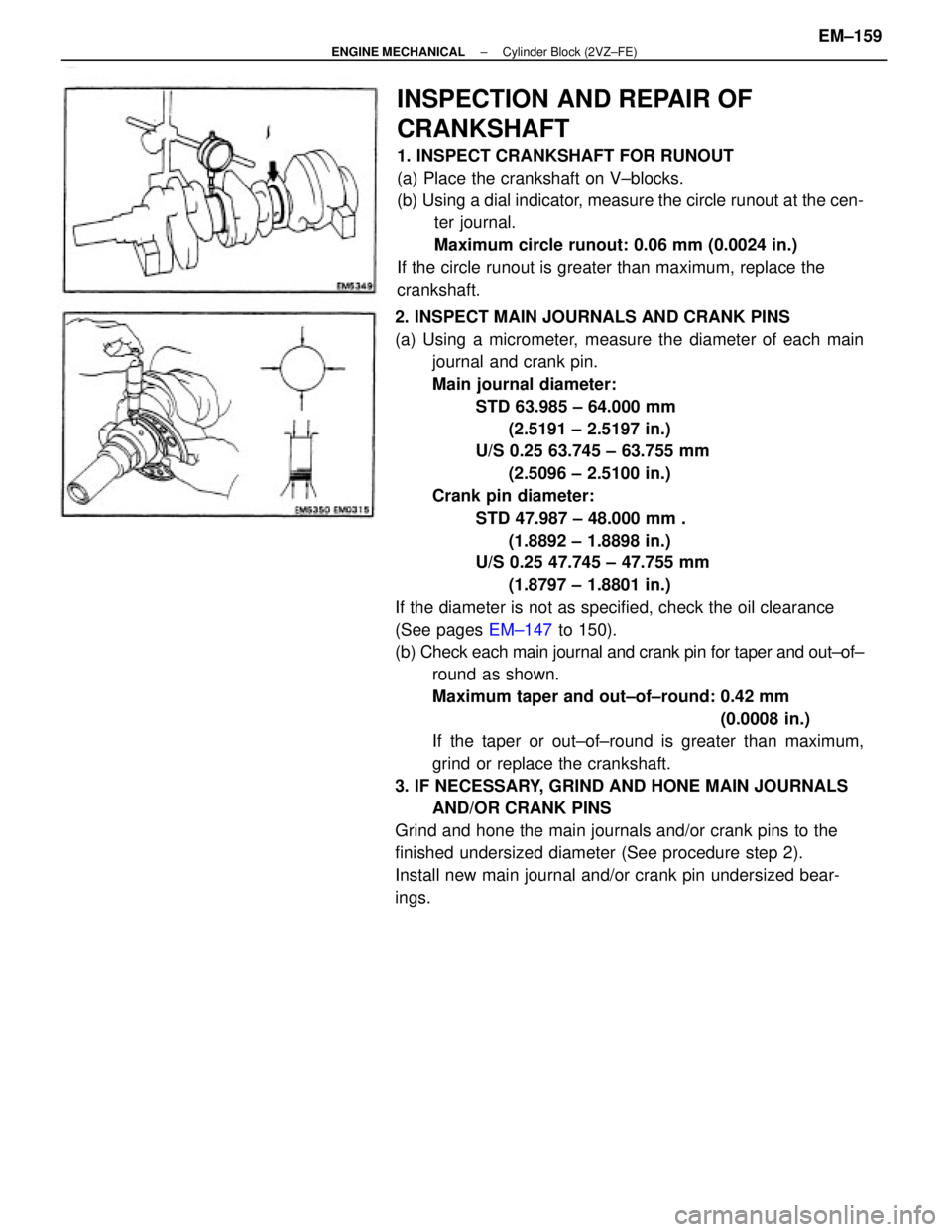
2. INSPECT MAIN JOURNALS AND CRANK PINS
(a) Using a micrometer, measure the diameter of each main
journal and crank pin.
Main journal diameter:
STD 63.985 ± 64.000 mm
(2.5191 ± 2.5197 in.)
U/S 0.25 63.745 ± 63.755 mm
(2.5096 ± 2.5100 in.)
Crank pin diameter:
STD 47.987 ± 48.000 mm .
(1.8892 ± 1.8898 in.)
U/S 0.25 47.745 ± 47.755 mm
(1.8797 ± 1.8801 in.)
If the diameter is not as specified, check the oil clearance
(See pages EM±147 to 150).
(b) Check each main journal and crank pin for taper and out±of±
round as shown.
Maximum taper and out±of±round: 0.42 mm
(0.0008 in.)
If the taper or out±of±round is greater than maximum,
grind or replace the crankshaft.
3. IF NECESSARY, GRIND AND HONE MAIN JOURNALS
AND/OR CRANK PINS
Grind and hone the main journals and/or crank pins to the
finished undersized diameter (See procedure step 2).
Install new main journal and/or crank pin undersized bear-
ings.
INSPECTION AND REPAIR OF
CRANKSHAFT
1. INSPECT CRANKSHAFT FOR RUNOUT
(a) Place the crankshaft on V±blocks.
(b) Using a dial indicator, measure the circle runout at the cen-
ter journal.
Maximum circle runout: 0.06 mm (0.0024 in.)
If the circle runout is greater than maximum, replace the
crankshaft.
± ENGINE MECHANICALCylinder Block (2VZ±FE)EM±159