Page 585 of 2389
4. REMOVE EXTENSION HOUSING
(a) Remove the dust deflector from the extension housing.
(b) Remove the four bolts and extension housing.
(c) Remove the O±ring from the extension housing. 3. REMOVE DYNAMIC DAMPER
Remove the four bolts and dynamic damper.
REMOVAL OF COMPONENT PARTS
7. REMOVE TRANSFER MODE SELECT LEVER AND ROD
2: REMOVE REAR WHEEL SPEED SENSOR
(a) Remove the bolt and pull out the speed sensor.
(b) Remove the O±ring from speed sensor.
(d) Using SST, remove the oil seal.
SST 09308±00010
± AUTOMATIC TRANSAXLEComponent Parts (Transfer A540M)AT±344
Page 586 of 2389
7. CHECK PRELOAD
(a) Using SST and a spring tension gauge, measure the driven
pinion preload of the backlash between the driven pinion
and ring gear.
SST 09326±20011
Driven pinion preload (at starting) :
0.9± 1.4 kg (2.0±3.1 Ib,8.8± 13.7 N)
(b) Using SST and a spring tension gauge, measure the total
preload.
SST 09326±20011
Total pre load (at starting):
Add driven pinion preload
0.5±0.9kg(1.1 ±2.0 Ib,4.9±8.8N)
8. CHECK RING GEAR BACKLASH
Using a dial indicator, measure the ±ring gear backlash.
Backlash: 0.13 ± 0.18 mm (0.0051 ± 0.0071 in.)
CHECK TOOTH CONTACT
(See page AT±374) 5. REMOVE TRANSFER RIGHT CASE RETAINER
(a) Remove the five bolts.
(b) Using a plastic hammer, remove the right case
retainer.
6. REMOVE TRANSFER INSPECTION HOLE COVER
Remove the three bolts and inspection hole cover.(e) Remove the O±ring and apply gasket from the
right case retainer.
± AUTOMATIC TRANSAXLEComponent Parts (Transfer A540H)AT±345
Page 587 of 2389
13. REMOVE OIL PUMP DRIVEN GEAR AND OIL PUMP
STRAINER
(a) Remove oil pump driven gear.
(b) Remove the bolt and oil pump strainer.
(c) Remove the O±ring from the oil pump strainer. 9. REMOVE DRIVEN PINION BEARING CAGE
(a) the six bolts and bearing cage.
(b) Remove the O±ring and the shims from the bearing
cage.
10. REMOVE TRANSFER RIGHT CASE
Remove the ten bolts and right case.
12. REMOVE APPLY GASKET
Remove the apply gasket from the left case. 11. REMOVE CENTER DIFFERENTIAL ASSEMBLY
± AUTOMATIC TRANSAXLEComponent Parts (Transfer A540H)AT±346
Page 588 of 2389
15. REMOVE DIFFERENTIAL RIGHT SIDE BEARING
OUTER RACE
(a) Using SST, remove the adjusting nut and oil reservoir
from the right case.
SST 09318±12010 14. REMOVE ADJUSTING NUT LOCK PLATE
(a) Remove the bolt and nut lock plate from the right case.
(b) Remove the O±ring from the bolt.
16. REMOVE DIFFERENTIAL LEFT SIDE BEARING OUTER
RACE
Using SST, remove the outer race and plate washer.
SST 09308±00010
17. REMOVE LEFT CASE OIL SEAL
Using SST, remove the oil seal.
SST 09308±00010(b) Using a brass bar, remove the outer race.
± AUTOMATIC TRANSAXLEComponent Parts (Transfer A540H)AT±347
Page 589 of 2389
DISASSEMBLY OF DRIVEN PINION BEARING
CAGE
1. REMOVE LOCK NUT
(a) Using a chisel and hammer, unstake the lock nut.
(b) Using SST, remove the lock nut.
SST 09326±20011
NOTICE: Using soft jaws, hold the driven pinion in a
vise.
(Driven Pinion Bearing Cage)
± AUTOMATIC TRANSAXLEComponent Parts (Transfer Driven Pinion Bearing Cage
A540H)AT±348
Page 590 of 2389
ASSEMBLY OF DRIVEN PINION BEARING
CAGE
1. INSTALL BEARING OUTER RACES
Using a press and SST, install the two bearing outer races to
the bearing cage.
SST
Front side:
09608±35014 (09608±06020, 09608±06120)
Rear side:
09608±30022 (09608±05010. 09608±00050)
2. INSTALL DRIVEN PINION FRONT SIDE BEARING
Using a press and SST, install the front side bearing.
SST 09506±35010 3. REMOVE FRONT SIDE BEARING
Using a press and SST, remove the front side bearing.
SST 09950±00020 2. REMOVE DRIVEN PINION
Using a press, remove the driven pinion, rear side
bearing and spacer.
4. REMOVE BEARING OUTER RACES
Using a brass bar and hammer, remove the two bear-
ing outer races.
± AUTOMATIC TRANSAXLEComponent Parts (Transfer Driven Pinion Bearing Cage
A540H)AT±349
Page 591 of 2389
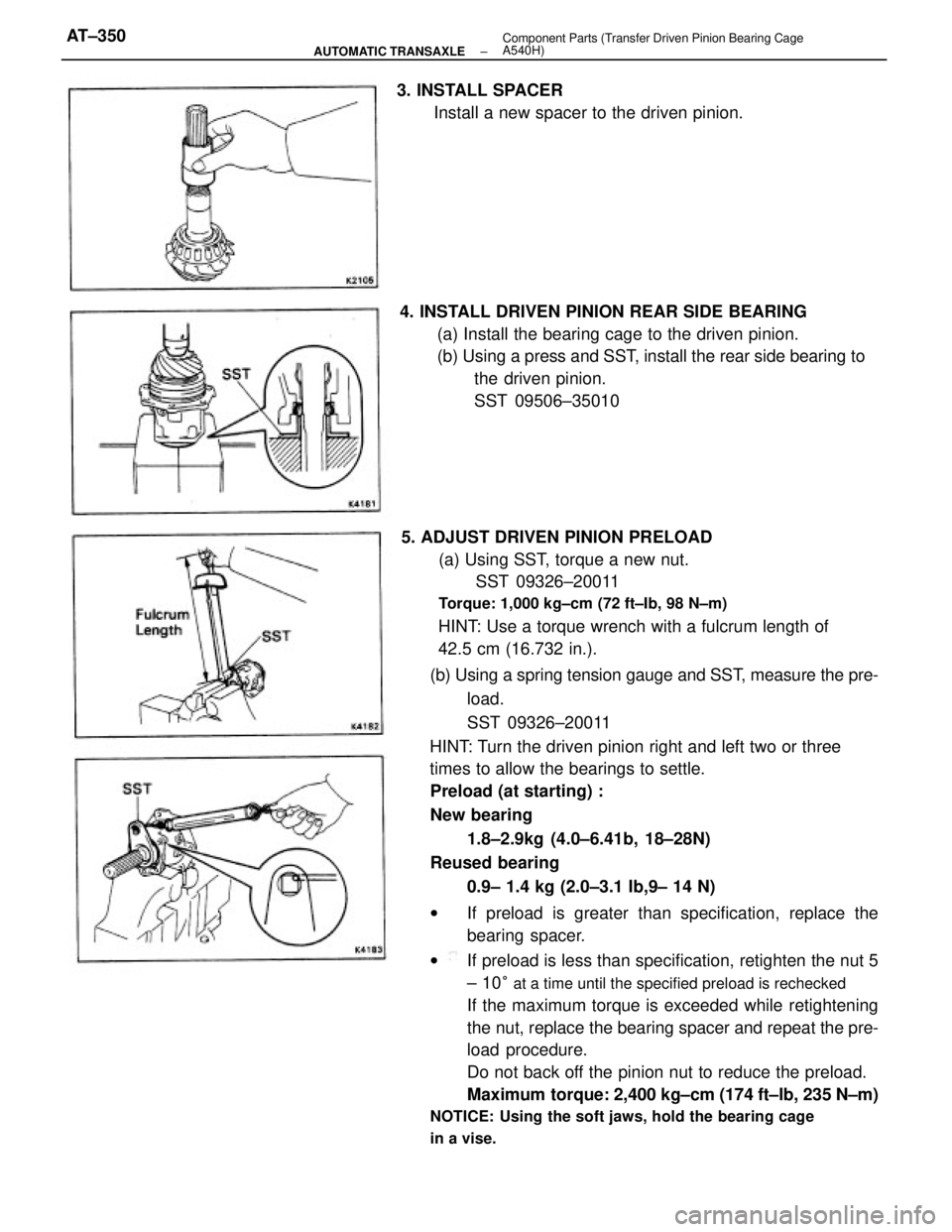
(b) Using a spring tension gauge and SST, measure the pre-
load.
SST 09326±20011
HINT: Turn the driven pinion right and left two or three
times to allow the bearings to settle.
Preload (at starting) :
New bearing
1.8±2.9kg (4.0±6.41b, 18±28N)
Reused bearing
0.9± 1.4 kg (2.0±3.1 Ib,9± 14 N)
wIf preload is greater than specification, replace the
bearing spacer.
wIf preload is less than specification, retighten the nut 5
± 10
° at a time until the specified preload is rechecked
If the maximum torque is exceeded while retightening
the nut, replace the bearing spacer and repeat the pre-
load procedure.
Do not back off the pinion nut to reduce the preload.
Maximum torque: 2,400 kg±cm (174 ft±Ib, 235 N±m)
NOTICE: Using the soft jaws, hold the bearing cage
in a vise.
5. ADJUST DRIVEN PINION PRELOAD
(a) Using SST, torque a new nut.
SST 09326±20011
Torque: 1,000 kg±cm (72 ft±Ib, 98 N±m)
HINT: Use a torque wrench with a fulcrum length of
42.5 cm (16.732 in.). 4. INSTALL DRIVEN PINION REAR SIDE BEARING
(a) Install the bearing cage to the driven pinion.
(b) Using a press and SST, install the rear side bearing to
the driven pinion.
SST 09506±35010 3. INSTALL SPACER
Install a new spacer to the driven pinion.
± AUTOMATIC TRANSAXLEComponent Parts (Transfer Driven Pinion Bearing Cage
A540H)AT±350
Page 592 of 2389
6. STAKE LOCK NUT
Using a punch and hammer, stake the nut.
± AUTOMATIC TRANSAXLEComponent Parts (Transfer Driven Pinion Bearing Cage
A540H)AT±351