Page 2121 of 2389
19. IF NECESSARY, REPLACE RING GEAR MOUNTING
CASE SIDE BEARING OUTER RACE
(Transfer Right Case)
(a) Using SST, turn the bearing adjusting nut, remove the
outer race and bearing adjusting nut.
SST 09318±20010
(Transfer Left Case)
(a) Using a brass bar and hammer, drive out the bear-
ing outer race lightly and evenly.
Remove the plate washer. (b) Install the bearing adjusting nut until it touches the
lip of the case.
HINT: If the nut is difficult to turn, use SST (09318±
20010).
(c) Using SST and a press, install the press until it is
almost touching the bearing adjusting nut.
SST 09608±35014 (09608±06020,
09608±06160)
(c) Install the plate washer.
HINT: First install a washer of the same thickness
as before.
± MANUAL TRANSAXLEComponent Parts (Transfer Assembly E5.6F5)MT±176
Page 2122 of 2389
21. INSPECT TRANSFER VACUUM ACTUATOR
(a) the push rod.
(b) Apply a vacuum of 500 mmHg to port Y1 and Y2.
Move in the push rod and measure the push rod strake.
Push rod strake: 16.5 mm (0.650 in.) or more
(c) Apply a vacuum of 500 mmHg to port Y3. Check that no remain
the vacuum in actuator.
If not, replace the actuator.
(d) After the check, apply a vacuum of 500 mmHg to port Y of the ac-
tuator (Put the differential lock on the free side). 20. MEASURE CLEARANCE OF DIFFERENTIAL LOCK
SHIFT FORK AND SLEEVE
Measure the clearance between the shift fork and
sleeve.
Maximum clearance: 1.0 mm (0.039 in.)(d) Using. SST and a press, install the outer race.
SST 09316±60010 (09316±00010, 09316±00060)
± MANUAL TRANSAXLEComponent Parts (Transfer Assembly E56F5)MT±177
Page 2123 of 2389
DISASSEMBLY OF DRIVEN PINION BEARING
CAGE
1. REMOVE LOCK NUT
(a) Unstake the lock nut.
(b) Using SST, remove the luck nut.
SST 09326±20011
2. REMOVE DRIVEN PINION
Using a press, remove the driven pinion, rear bearing
and spacer.
DRIVEN PINION. BEARING CAGE ASSEMBLY
± MANUAL TRANSAXLEComponent Parts (Transfer Assembly E56F5)MT±178
Page 2124 of 2389
ASSEMBLY OF DRIVEN PINION BEARING
CAGE
(See page MT± 178)
HINT: Coat all of the sliding and rotating surface with gear oil be-
fore assembly.
1. INSTALL DRIVEN PINION BEARING CAGE
(a) Install a new bearing spacer.
HINT: Insert the spacer with the smaller facing upwards. (b) Using SST and a press, install the front bearing outer race.
SST 09608±35014 (09608±06020, 09608±06210)
(c) Using SST and a press, install the rear bearing outer race.
SST 09550±10012 (09252±10010, 09555±10010) 4. IF NECESSARY, REPLACE FRONT AND REAR
BEARING OUTER RACE
(a) Using a brass bar and hammer, drive out the bearing
outer race race lightly and evenly.
HINT: Be careful not to damage the drive pinion bearing
cage and earing outer race. 3. IF NECESSARY, REPLACE DRIVEN PINION FRONT
BEARING
(a) Using SST and a press, remove the front bearing.
SST 09950±00020
(b) Using SST and a press, install the front bearing.
SST 09506±35010
± MANUAL TRANSAXLEComponent Parts (Transfer Assembly E56F5)MT±179
Page 2125 of 2389
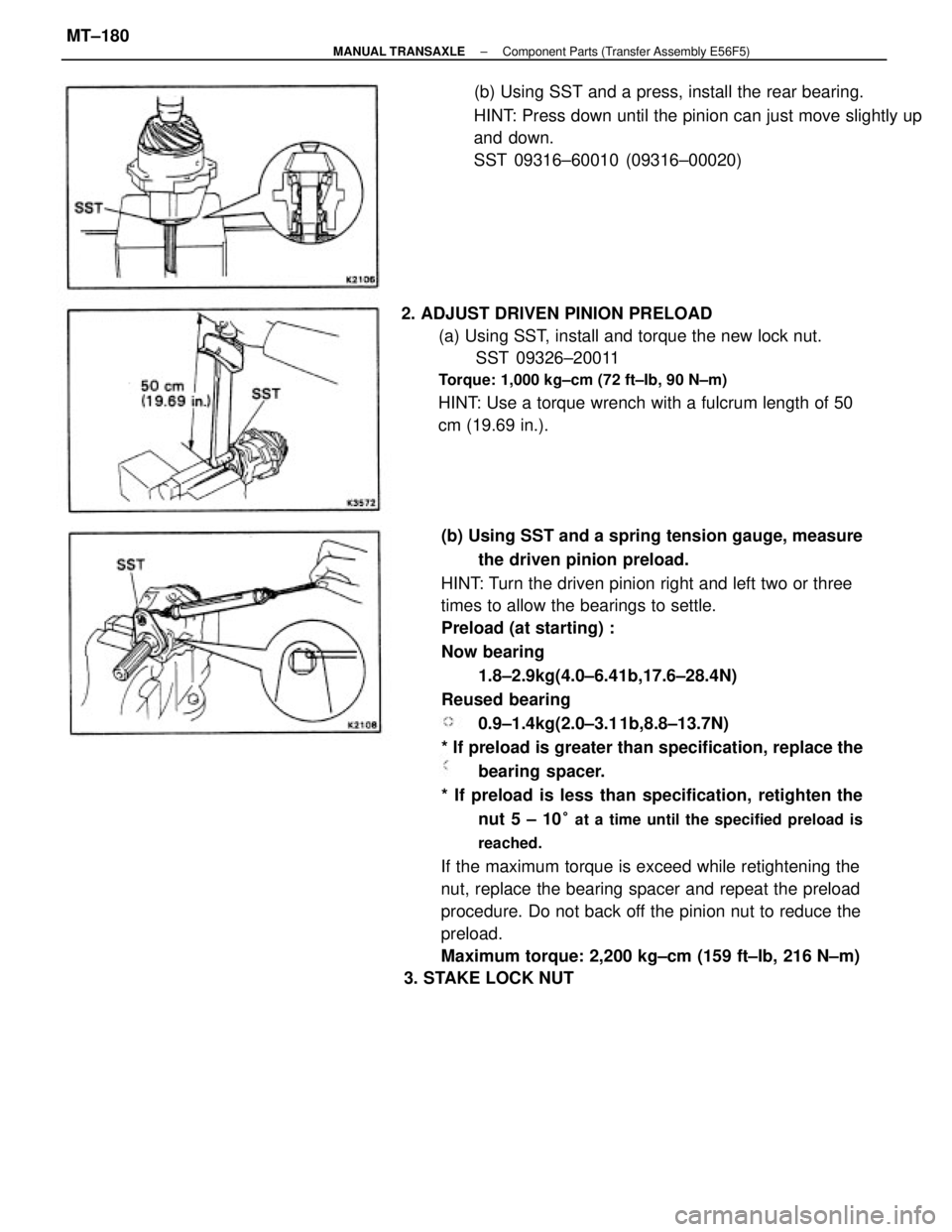
(b) Using SST and a spring tension gauge, measure
the driven pinion preload.
HINT: Turn the driven pinion right and left two or three
times to allow the bearings to settle.
Preload (at starting) :
Now bearing
1.8±2.9kg(4.0±6.41b,17.6±28.4N)
Reused bearing
0.9±1.4kg(2.0±3.1 1b,8.8±13.7N)
* If preload is greater than specification, replace the
bearing spacer.
* If preload is less than specification, retighten the
nut 5 ± 10
° at a time until the specified preload is
reached.
If the maximum torque is exceed while retightening the
nut, replace the bearing spacer and repeat the preload
procedure. Do not back off the pinion nut to reduce the
preload.
Maximum torque: 2,200 kg±cm (159 ft±Ib, 216 N±m)
3. STAKE LOCK NUT 2. ADJUST DRIVEN PINION PRELOAD
(a) Using SST, install and torque the new lock nut.
SST 09326±20011
Torque: 1,000 kg±cm (72 ft±Ib, 90 N±m)
HINT: Use a torque wrench with a fulcrum length of 50
cm (19.69 in.).(b) Using SST and a press, install the rear bearing.
HINT: Press down until the pinion can just move slightly up
and down.
SST 09316±60010 (09316±00020)
± MANUAL TRANSAXLEComponent Parts (Transfer Assembly E56F5)MT±180
Page 2126 of 2389
DISASSEMBLY OF RING GEAR MOUNTING
CASE
1. REMOVE MOUNTING CASE SIDE BEARING
Using SST, remove the side bearing.
SST 09950±20017
2. CHECK RING GEAR RUNOUT
Using a dial indicator, check the ring gear runout.
Maximum runout: 0.1 mm (0.004 in.)
RING GEAR MOUNTING CASE
ASSEMBLY
± MANUAL TRANSAXLEComponent Parts (Transfer Assembly E56F5)MT±181
Page 2127 of 2389
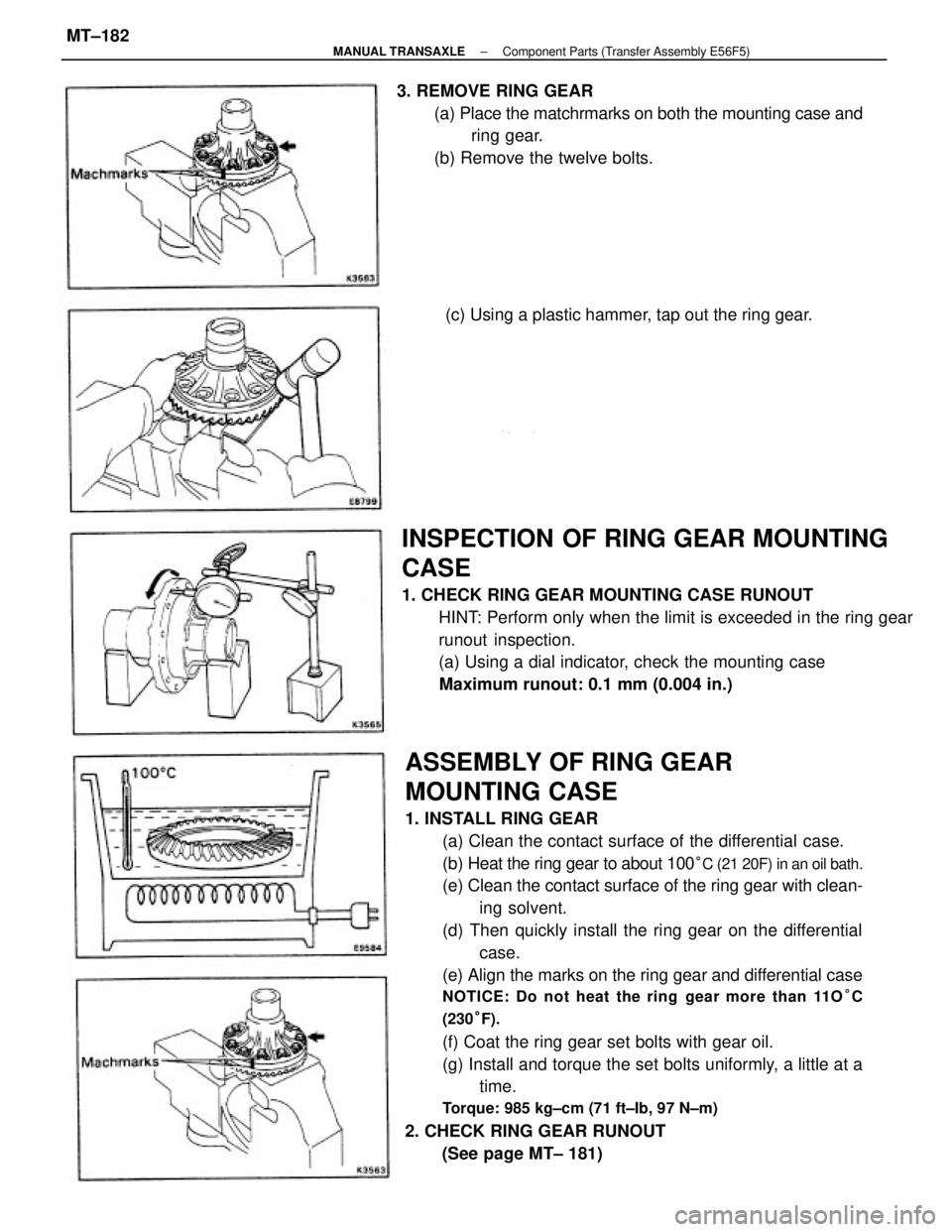
ASSEMBLY OF RING GEAR
MOUNTING CASE
1. INSTALL RING GEAR
(a) Clean the contact surface of the differential case.
(b) Heat the ring gear to about 100
°C (21 20F) in an oil bath.
(e) Clean the contact surface of the ring gear with clean-
ing solvent.
(d) Then quickly install the ring gear on the differential
case.
(e) Align the marks on the ring gear and differential case
NOTICE: Do not heat the ring gear more than 11O°C
(230°F).
(f) Coat the ring gear set bolts with gear oil.
(g) Install and torque the set bolts uniformly, a little at a
time.
Torque: 985 kg±cm (71 ft±Ib, 97 N±m)
2. CHECK RING GEAR RUNOUT
(See page MT± 181)
INSPECTION OF RING GEAR MOUNTING
CASE
1. CHECK RING GEAR MOUNTING CASE RUNOUT
HINT: Perform only when the limit is exceeded in the ring gear
runout inspection.
(a) Using a dial indicator, check the mounting case
Maximum runout: 0.1 mm (0.004 in.) 3. REMOVE RING GEAR
(a) Place the matchrmarks on both the mounting case and
ring gear.
(b) Remove the twelve bolts.
(c) Using a plastic hammer, tap out the ring gear.
± MANUAL TRANSAXLEComponent Parts (Transfer Assembly E56F5)MT±182
Page 2128 of 2389
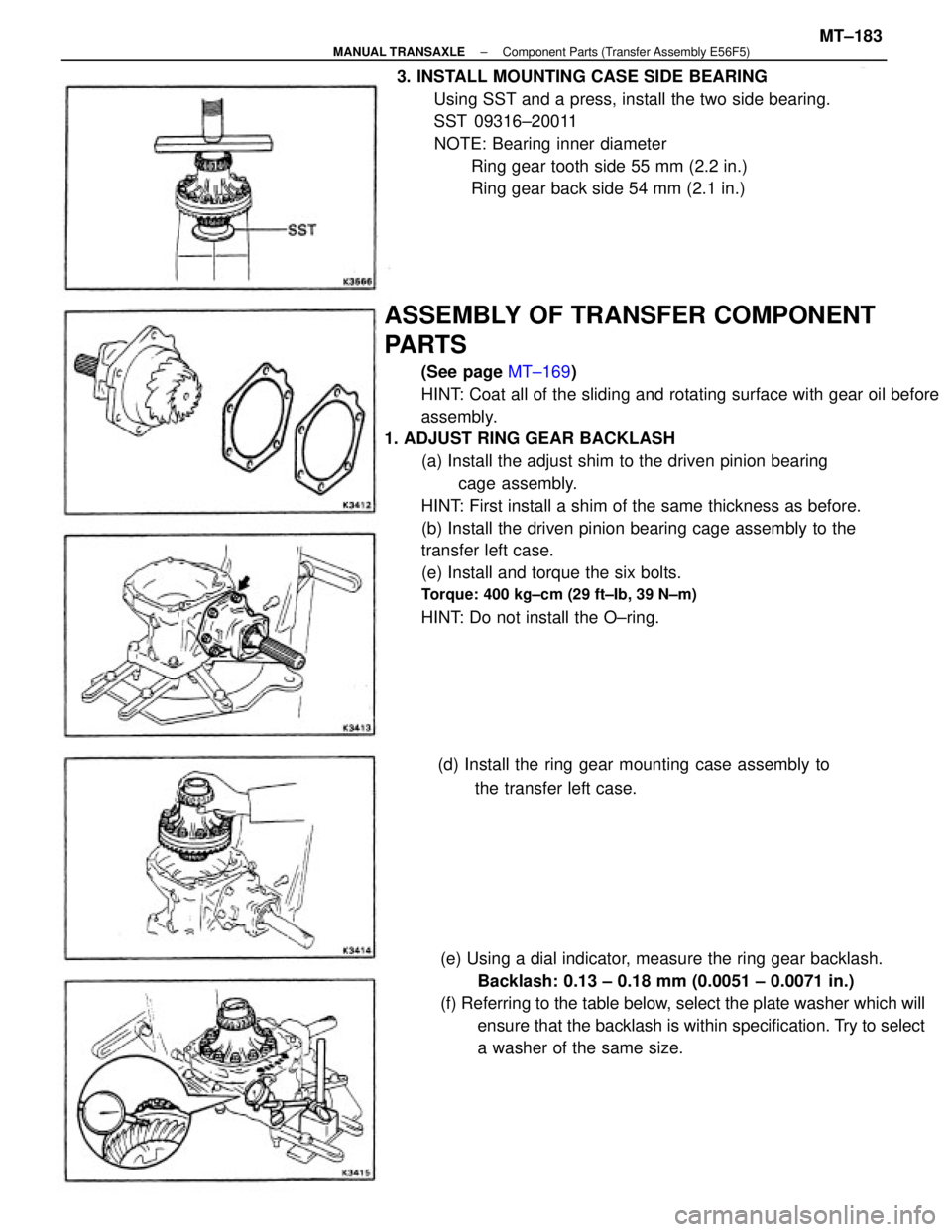
ASSEMBLY OF TRANSFER COMPONENT
PARTS
(See page MT±169)
HINT: Coat all of the sliding and rotating surface with gear oil before
assembly.
1. ADJUST RING GEAR BACKLASH
(a) Install the adjust shim to the driven pinion bearing
cage assembly.
HINT: First install a shim of the same thickness as before.
(b) Install the driven pinion bearing cage assembly to the
transfer left case.
(e) Install and torque the six bolts.
Torque: 400 kg±cm (29 ft±Ib, 39 N±m)
HINT: Do not install the O±ring.
(e) Using a dial indicator, measure the ring gear backlash.
Backlash: 0.13 ± 0.18 mm (0.0051 ± 0.0071 in.)
(f) Referring to the table below, select the plate washer which will
ensure that the backlash is within specification. Try to select
a washer of the same size. 3. INSTALL MOUNTING CASE SIDE BEARING
Using SST and a press, install the two side bearing.
SST 09316±20011
NOTE: Bearing inner diameter
Ring gear tooth side 55 mm (2.2 in.)
Ring gear back side 54 mm (2.1 in.)
(d) Install the ring gear mounting case assembly to
the transfer left case.
± MANUAL TRANSAXLEComponent Parts (Transfer Assembly E56F5)MT±183