Page 785 of 2389
Low Oil Pressure Warning
INSPECTION OF PRESSURE WARNING
1. INSPECT WARNING LIGHT OPERATION
(a) Disconnect the connector from the pressure switch
and ground the connector on the wire harness side.
(b) Turn the ignition switch ON, check that t he warning
light lights.
If the warning light does not light, test the bulb.
2. INSPECT PRESSURE SWITCH OPERATION
(a) Disconnect the connector from the switch.
(b) Check that there is continuity between terminal and
ground with the engine stopped.
(c) Check that there is no continuity between terminal
and ground with the engine running.
HINT: Oil pressure should be over 0.3 kg/cm2 (4.3 psi, 29
kPa).
If operation is not as specified, replace the switch.If resistance value is not as specified, replace the send-
er gauge. 3. MEASURE SENDER GAUGE RESISTANCE
Measure the resistance between terminal and ground.
ater temperature oC
(OF)Resistance ()
N i ppo nde nso Yazaki
± BODY ELECTRICAL SYSTEMCombination MeterBE±39
Page 786 of 2389
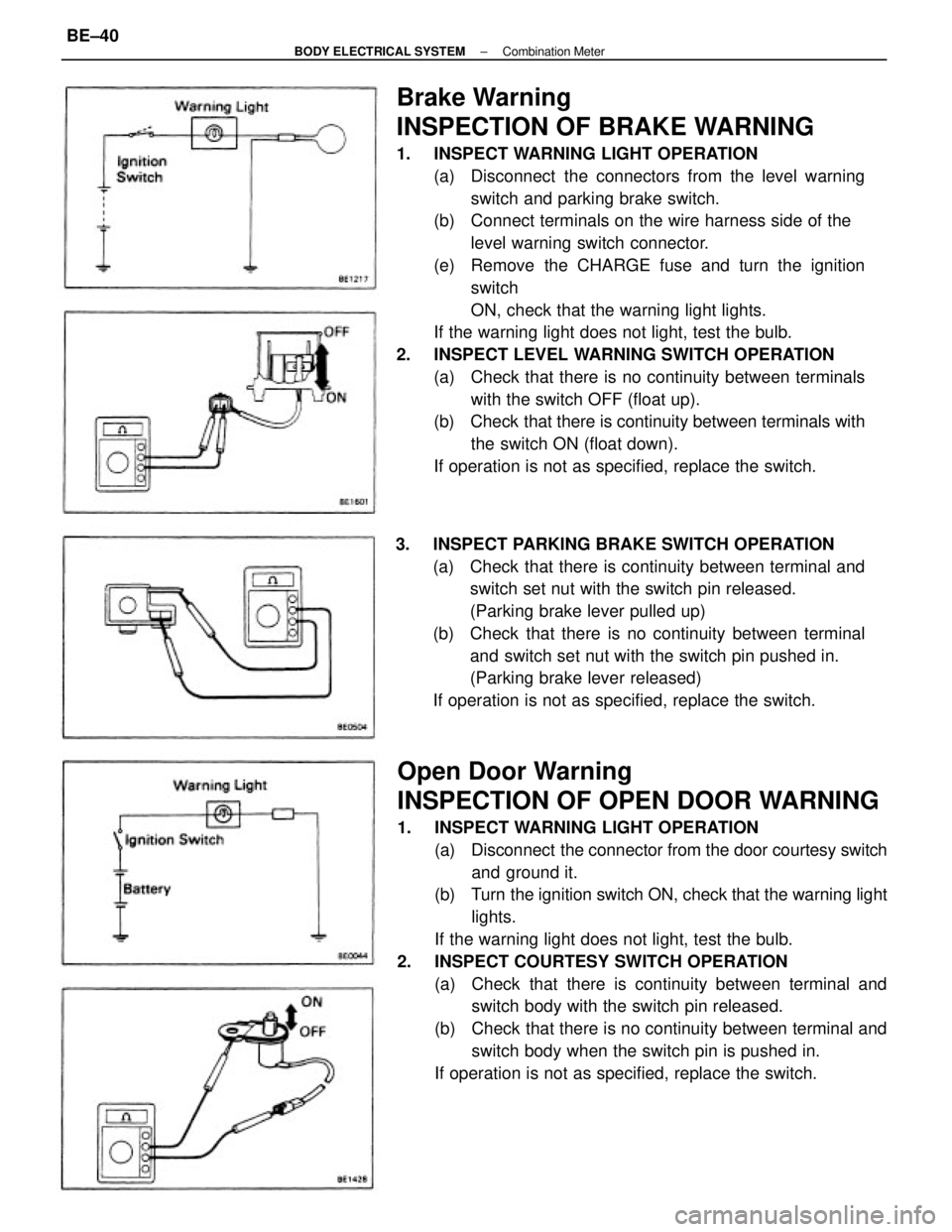
Brake Warning
INSPECTION OF BRAKE WARNING
1. INSPECT WARNING LIGHT OPERATION
(a) Disconnect the connectors from the level warning
switch and parking brake switch.
(b) Connect terminals on the wire harness side of the
level warning switch connector.
(e) Remove the CHARGE fuse and turn the ignition
switch
ON, check that the warning light lights.
If the warning light does not light, test the bulb.
2. INSPECT LEVEL WARNING SWITCH OPERATION
(a) Check that there is no continuity between terminals
with the switch OFF (float up).
(b) Check that there is continuity between terminals with
the switch ON (float down).
If operation is not as specified, replace the switch.
Open Door Warning
INSPECTION OF OPEN DOOR WARNING
1. INSPECT WARNING LIGHT OPERATION
(a) Disconnect the connector from the door courtesy switch
and ground it.
(b) Turn the ignition switch ON, check that the warning light
lights.
If the warning light does not light, test the bulb.
2. INSPECT COURTESY SWITCH OPERATION
(a) Check that there is continuity between terminal and
switch body with the switch pin released.
(b) Check that there is no continuity between terminal and
switch body when the switch pin is pushed in.
If operation is not as specified, replace the switch. 3. INSPECT PARKING BRAKE SWITCH OPERATION
(a) Check that there is continuity between terminal and
switch set nut with the switch pin released.
(Parking brake lever pulled up)
(b) Check that there is no continuity between terminal
and switch set nut with the switch pin pushed in.
(Parking brake lever released)
If operation is not as specified, replace the switch.
± BODY ELECTRICAL SYSTEMCombination MeterBE±40
Page 787 of 2389
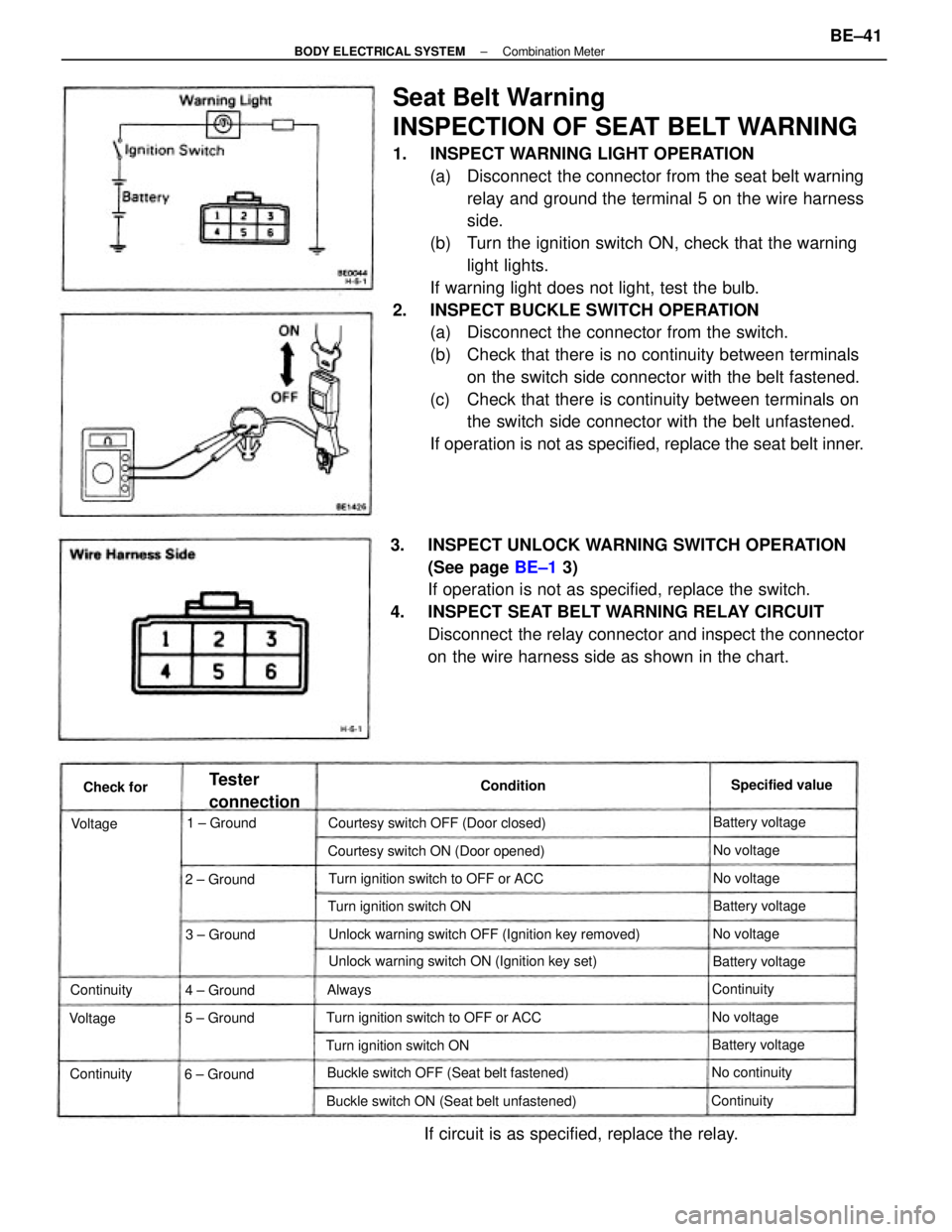
Seat Belt Warning
INSPECTION OF SEAT BELT WARNING
1. INSPECT WARNING LIGHT OPERATION
(a) Disconnect the connector from the seat belt warning
relay and ground the terminal 5 on the wire harness
side.
(b) Turn the ignition switch ON, check that the warning
light lights.
If warning light does not light, test the bulb.
2. INSPECT BUCKLE SWITCH OPERATION
(a) Disconnect the connector from the switch.
(b) Check that there is no continuity between terminals
on the switch side connector with the belt fastened.
(c) Check that there is continuity between terminals on
the switch side connector with the belt unfastened.
If operation is not as specified, replace the seat belt inner.
3. INSPECT UNLOCK WARNING SWITCH OPERATION
(See page BE±1 3)
If operation is not as specified, replace the switch.
4. INSPECT SEAT BELT WARNING RELAY CIRCUIT
Disconnect the relay connector and inspect the connector
on the wire harness side as shown in the chart.
Unlock warning switch OFF (Ignition key removed)
If circuit is as specified, replace the relay.
Unlock warning switch ON (Ignition key set)
Buckle switch ON (Seat belt unfastened)Buckle switch OFF (Seat belt fastened)Courtesy switch ON (Door opened)
Turn ignition switch to OFF or ACCTurn ignition switch to OFF or ACC Courtesy switch OFF (Door closed)
Turn ignition switch ONTurn ignition switch ON
6 ± Ground
Tester
connectionSpecified value
Battery voltage
Battery voltage
Battery voltageBattery voltage
No continuity 1 ± Ground
2 ± Ground
3 ± Ground
5 ± Ground4 ± GroundContinuity
Continuity
ContinuityNo voltageNo voltageNo voltage
No voltage
Continuity Condition
Check for
VoltageVoltage
Always
± BODY ELECTRICAL SYSTEMCombination MeterBE±41
Page 788 of 2389
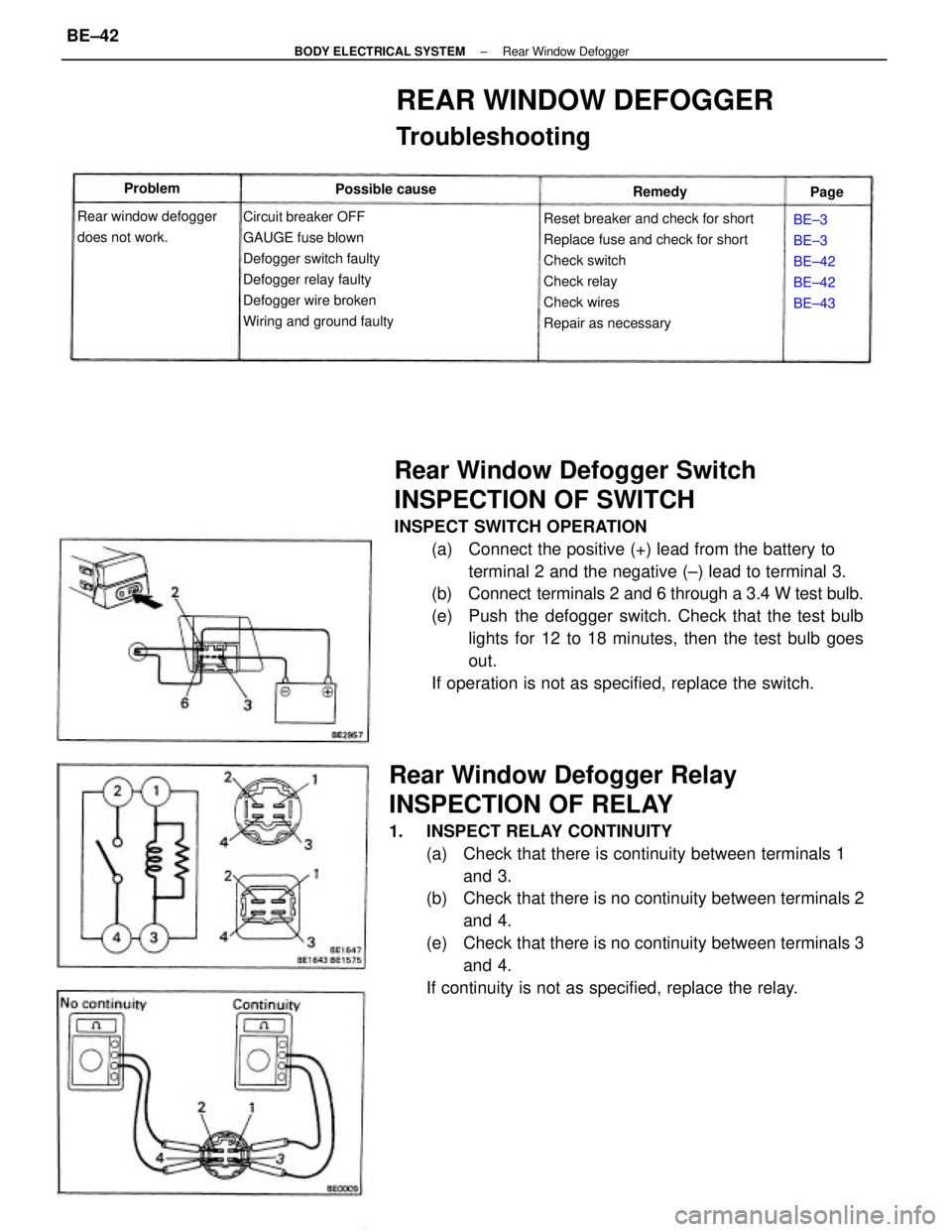
Rear Window Defogger Switch
INSPECTION OF SWITCH
INSPECT SWITCH OPERATION
(a) Connect the positive (+) lead from the battery to
terminal 2 and the negative (±) lead to terminal 3.
(b) Connect terminals 2 and 6 through a 3.4 W test bulb.
(e) Push the defogger switch. Check that the test bulb
lights for 12 to 18 minutes, then the test bulb goes
out.
If operation is not as specified, replace the switch.
Rear Window Defogger Relay
INSPECTION OF RELAY
1. INSPECT RELAY CONTINUITY
(a) Check that there is continuity between terminals 1
and 3.
(b) Check that there is no continuity between terminals 2
and 4.
(e) Check that there is no continuity between terminals 3
and 4.
If continuity is not as specified, replace the relay.
Reset breaker and check for short
Replace fuse and check for short
Check switch
Check relay
Check wires
Repair as necessary
REAR WINDOW DEFOGGER
Troubleshooting
Circuit breaker OFF
GAUGE fuse blown
Defogger switch faulty
Defogger relay faulty
Defogger wire broken
Wiring and ground faulty Rear window defogger
does not work.BE±3
BE±3
BE±42
BE±42
BE±43 Possible cause Problem
Remedy
Page
± BODY ELECTRICAL SYSTEMRear Window DefoggerBE±42
Page 789 of 2389
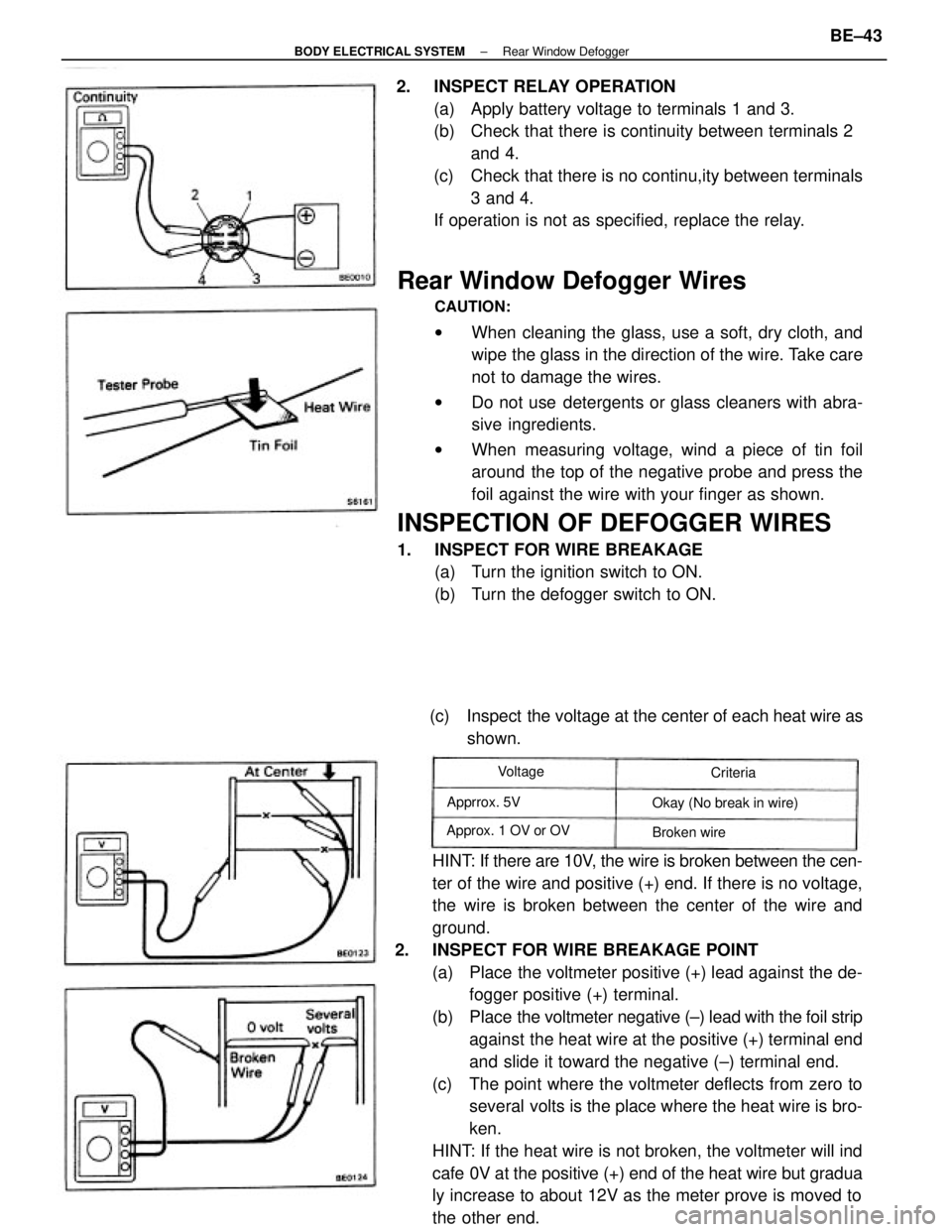
Rear Window Defogger Wires
CAUTION:
wWhen cleaning the glass, use a soft, dry cloth, and
wipe the glass in the direction of the wire. Take care
not to damage the wires.
wDo not use detergents or glass cleaners with abra-
sive ingredients.
wWhen measuring voltage, wind a piece of tin foil
around the top of the negative probe and press the
foil against the wire with your finger as shown.
INSPECTION OF DEFOGGER WIRES
1. INSPECT FOR WIRE BREAKAGE
(a) Turn the ignition switch to ON.
(b) Turn the defogger switch to ON.
HINT: If there are 10V, the wire is broken between the cen-
ter of the wire and positive (+) end. If there is no voltage,
the wire is broken between the center of the wire and
ground.
2. INSPECT FOR WIRE BREAKAGE POINT
(a) Place the voltmeter positive (+) lead against the de-
fogger positive (+) terminal.
(b) Place the voltmeter negative (±) lead with the foil strip
against the heat wire at the positive (+) terminal end
and slide it toward the negative (±) terminal end.
(c) The point where the voltmeter deflects from zero to
several volts is the place where the heat wire is bro-
ken.
HINT: If the heat wire is not broken, the voltmeter will ind
cafe 0V at the positive (+) end of the heat wire but gradua
ly increase to about 12V as the meter prove is moved to
the other end. 2. INSPECT RELAY OPERATION
(a) Apply battery voltage to terminals 1 and 3.
(b) Check that there is continuity between terminals 2
and 4.
(c) Check that there is no continu,ity between terminals
3 and 4.
If operation is not as specified, replace the relay.
(c) Inspect the voltage at the center of each heat wire as
shown.
Okay (No break in wire)
Approx. 1 OV or OVApprrox. 5V
Broken wire Voltage
Criteria
± BODY ELECTRICAL SYSTEMRear Window DefoggerBE±43
Page 790 of 2389
3. REPAIR DEFOGGER WIRES
(a) Thoroughly mix the repair agent (Dupont paste No.
4817).
(b) Using a fine tip brush, apply a small amount to the
wire.
(c) After a few minutes, remove the masking tape.
(d) Allow the repair to stand at least 24 hours.
REPAIR OF DEFOGGER WIRES
1. CLEAN BROKEN WIRE TIPS WITH WHITE GASOLINE
2. PLACE MASKING TAPE ALONG BOTH SIDES OF
WIRE TO BE REPAIRED
± BODY ELECTRICAL SYSTEMRear Window DefoggerBE±44
Page 791 of 2389
HEATER
Wiring Diagram (Push Type)
± BODY ELECTRICAL SYSTEMHeaterBE±45
Page 792 of 2389
Heater Control Assembly
Connector ºAº
Air Vent Mode Control
Servo Motor RECIRC/FRESH
Control Servo MotorAmplifier
Connector ºAº
Connectors
Air Mix Control Servo Motor
Blower Speed
Control RelayBlower Resistor Connector º6º
Connectorº6º
Blower MotorHeater Relay
± BODY ELECTRICAL SYSTEMHeaterBE±46