Page 1289 of 2389
(f) Lift the engine out of the vehicle slowly and carefully.
NOTICE: Be careful not to hit the PS gear housing or neutral
start switch.
(g) Make sure the engine is clear of all wiring, hoses and
cables.
(h) Place the engine and transaxle assembly onto the stand.
36. SEPARATE ENGINE AND TRANSAXLE (d) Remove the through bolt, three bolts (2WD, M/T), four
bolts (Others) and LH mounting insulator.
(e) Remove the three bolts and LH mounting bracket. (b) (2WD)
Remove the bolt, four nuts and RH mounting insula-
tor.
(c) (4WD)
Remove the through bolt, two nuts and RH mounting
insulator.
± ENGINE MECHANICALCylinder Block (3S±FE)EM±112
Page 1290 of 2389
PREPARATION FOR DISASSEMBLY
1. ( M /T)
REMOVE CLUTCH COVER AND DISC
2. ( M /T)
REMOVE FLYWHEEL
3. 1A/T)
REMOVE DRIVE PLATE
4. REMOVE REAR END PLATE
5. INSTALL ENGINE TO ENGINE STAND FOR
DISASSEMBLY
6. REMOVE ALTERNATOR (See page CH±6)
7 REMOVE DISTRIBUTOR (See page IG±13)
8. REMOVE TIMING BELT AND PULLEYS
(See page EM±23)
9. REMOVE CYLINDER HEAD (See page EM±48)
10. REMOVE WATER PUMP (See page CO±6)
11. REMOVE OIL PAN AND OIL PUMP
(See page LU±9)
± ENGINE MECHANICALCylinder Block (3S±FE)EM±113
Page 1291 of 2389
2. CHECK CONNECTING ROD THRUST CLEARANCE
Using a dial indicator, measure the thrust clearance while
moving the connecting rod back and forth.
Standard thrust clearance: 0.160 ± 0.312 mm
(0.0063 ± 0.0123 in.)
Maximum thrust clearance: 0.35 mm (0.0138 in.)
If the thrust clearance is greater than maximum replace the
connecting rod assembly. If necessary, replace the crank-
shaft.
3. REMOVE CONNECTING ROD CAPS AND CHECK OIL
CLEARANCE
(a) Using a punch or numbering stamp, place the match±
marks on the connecting rod and cap to ensure correct
reassembly.
(c) Using a plastic±faced hammer, lightly tap the connect-
ing rod bolts and lift off the connecting rod cap.
HINT: Keep the lower bearing inserted with the connect-
ing cap.
DISASSEMBLY OF CYLINDER BLOCK
(See page EM±107)
1. REMOVE REAR OIL SEAL RETAINER
Remove the six bolts, retainer and gasket.
(b) Remove the connecting rod cap nuts.
± ENGINE MECHANICALCylinder Block (3S±FE)EM±114
Page 1292 of 2389
(i) Remove the connecting rod cap.
(j) Measure the Plastigage at widest point.
Standard oil clearance:
STD 0.024 ± 0.055 mm
(0.0009 ± 0.0022 in.)
U/S 0.25 0.023 ± 0.069 mm
(0.0009 ± 0.0027 in.)
Maximum oil clearance: 0.08 mm (0.0031 in.)
If the oil clearance is greater than maximum, replace
the bearings. If necessary, replace the crankshaft. (e) Clean crank pin and bearing.
(f) Check the crank pin and bearing for pitting and
scratches.
If the crank pin or bearing are damaged, replace the
bearings.
If necessary, replace the crankshaft.
(h) Install the connecting rod cap.
(See step 6 on page EM±129)
Torque: 500 kg±cm (36 ft±lb. 49 N±m)
HINT: Do not turn the crankshaft.(d) Cover the connecting rod bolts with a short piece of
hose to protect the crankshaft from damage.
(g) Lay a strip of Plastigage across the crank pin.
± ENGINE MECHANICALCylinder Block (3S±FE)EM±115
Page 1293 of 2389
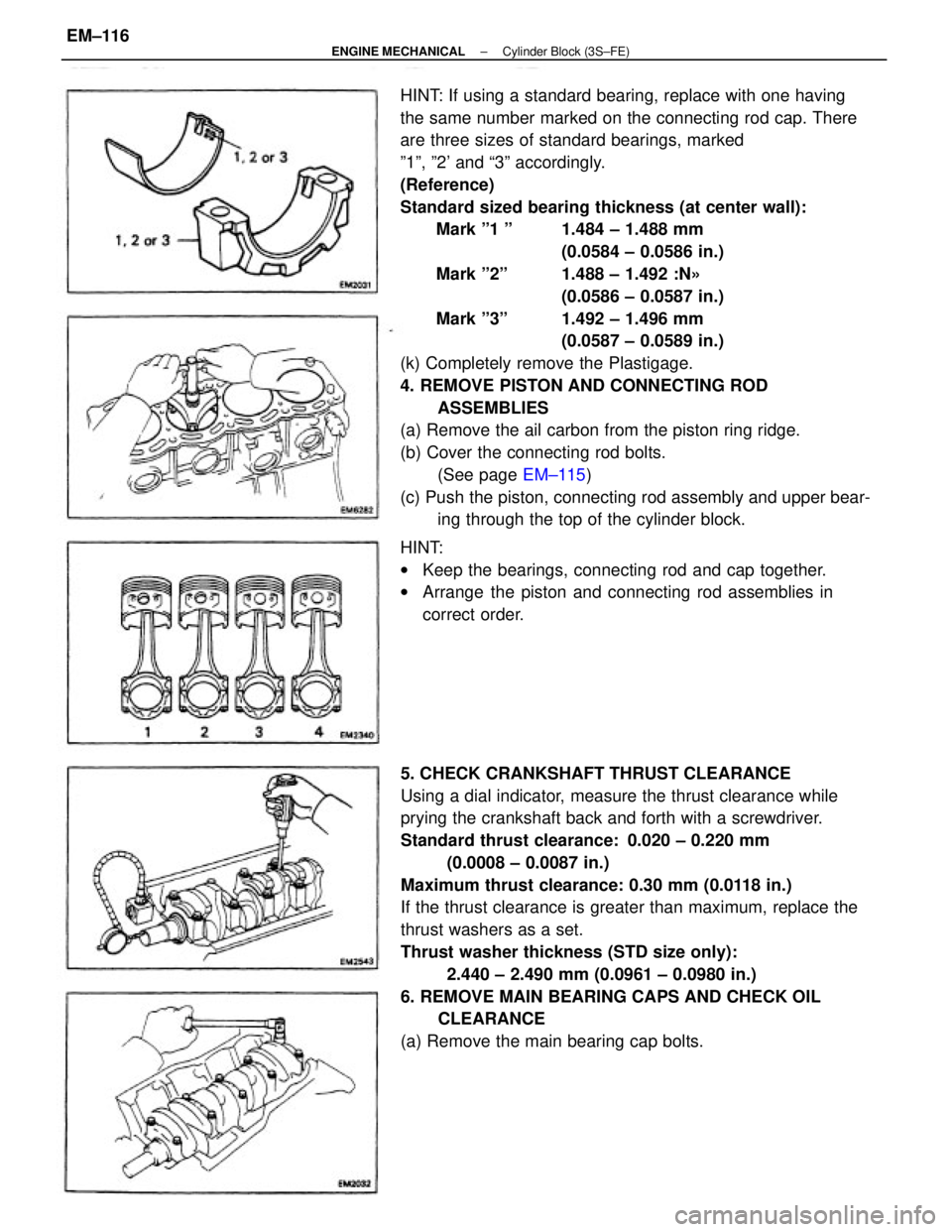
HINT: If using a standard bearing, replace with one having
the same number marked on the connecting rod cap. There
are three sizes of standard bearings, marked
º1º, º2' and ª3º accordingly.
(Reference)
Standard sized bearing thickness (at center wall):
Mark º1 º 1.484 ± 1.488 mm
(0.0584 ± 0.0586 in.)
Mark º2º 1.488 ± 1.492 :N»
(0.0586 ± 0.0587 in.)
Mark º3º 1.492 ± 1.496 mm
(0.0587 ± 0.0589 in.)
(k) Completely remove the Plastigage.
4. REMOVE PISTON AND CONNECTING ROD
ASSEMBLIES
(a) Remove the ail carbon from the piston ring ridge.
(b) Cover the connecting rod bolts.
(See page EM±115)
(c) Push the piston, connecting rod assembly and upper bear-
ing through the top of the cylinder block.
5. CHECK CRANKSHAFT THRUST CLEARANCE
Using a dial indicator, measure the thrust clearance while
prying the crankshaft back and forth with a screwdriver.
Standard thrust clearance: 0.020 ± 0.220 mm
(0.0008 ± 0.0087 in.)
Maximum thrust clearance: 0.30 mm (0.0118 in.)
If the thrust clearance is greater than maximum, replace the
thrust washers as a set.
Thrust washer thickness (STD size only):
2.440 ± 2.490 mm (0.0961 ± 0.0980 in.)
6. REMOVE MAIN BEARING CAPS AND CHECK OIL
CLEARANCE
(a) Remove the main bearing cap bolts. HINT:
wKeep the bearings, connecting rod and cap together.
wArrange the piston and connecting rod assemblies in
correct order.
± ENGINE MECHANICALCylinder Block (3S±FE)EM±116
Page 1294 of 2389
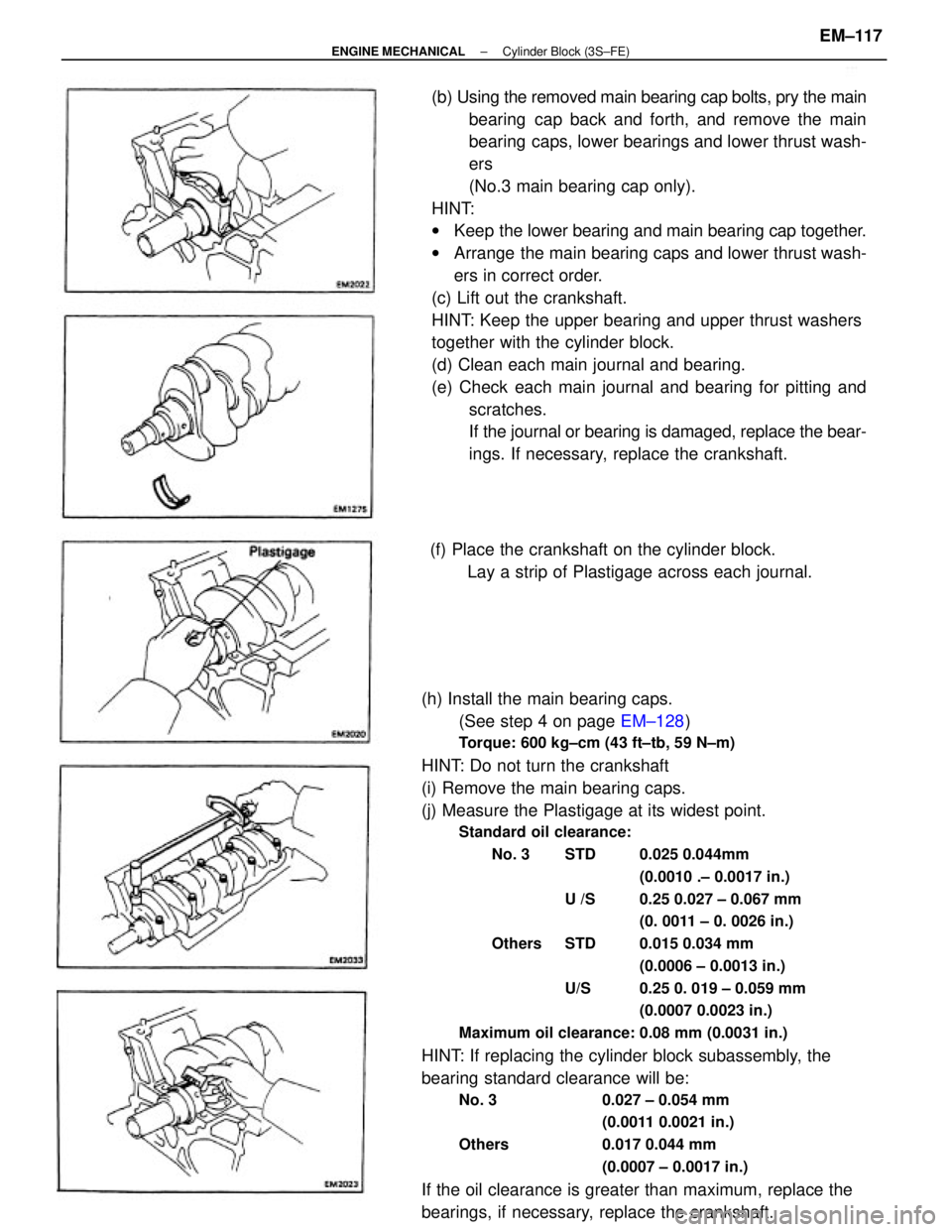
(h) Install the main bearing caps.
(See step 4 on page EM±128)
Torque: 600 kg±cm (43 ft±tb, 59 N±m)
HINT: Do not turn the crankshaft
(i) Remove the main bearing caps.
(j) Measure the Plastigage at its widest point.
Standard oil clearance:
No. 3 STD 0.025 0.044mm
(0.0010 .± 0.0017 in.)
U /S 0.25 0.027 ± 0.067 mm
(0. 0011 ± 0. 0026 in.)
Others STD 0.015 0.034 mm
(0.0006 ± 0.0013 in.)
U/S 0.25 0. 019 ± 0.059 mm
(0.0007 0.0023 in.)
Maximum oil clearance: 0.08 mm (0.0031 in.)
HINT: If replacing the cylinder block subassembly, the
bearing standard clearance will be:
No. 3 0.027 ± 0.054 mm
(0.0011 0.0021 in.)
Others 0.017 0.044 mm
(0.0007 ± 0.0017 in.)
If the oil clearance is greater than maximum, replace the
bearings, if necessary, replace the crankshaft.(b) Using the removed main bearing cap bolts, pry the main
bearing cap back and forth, and remove the main
bearing caps, lower bearings and lower thrust wash-
ers
(No.3 main bearing cap only).
HINT:
wKeep the lower bearing and main bearing cap together.
wArrange the main bearing caps and lower thrust wash-
ers in correct order.
(c) Lift out the crankshaft.
HINT: Keep the upper bearing and upper thrust washers
together with the cylinder block.
(d) Clean each main journal and bearing.
(e) Check each main journal and bearing for pitting and
scratches.
If the journal or bearing is damaged, replace the bear-
ings. If necessary, replace the crankshaft.
(f) Place the crankshaft on the cylinder block.
Lay a strip of Plastigage across each journal.
± ENGINE MECHANICALCylinder Block (3S±FE)EM±117
Page 1295 of 2389
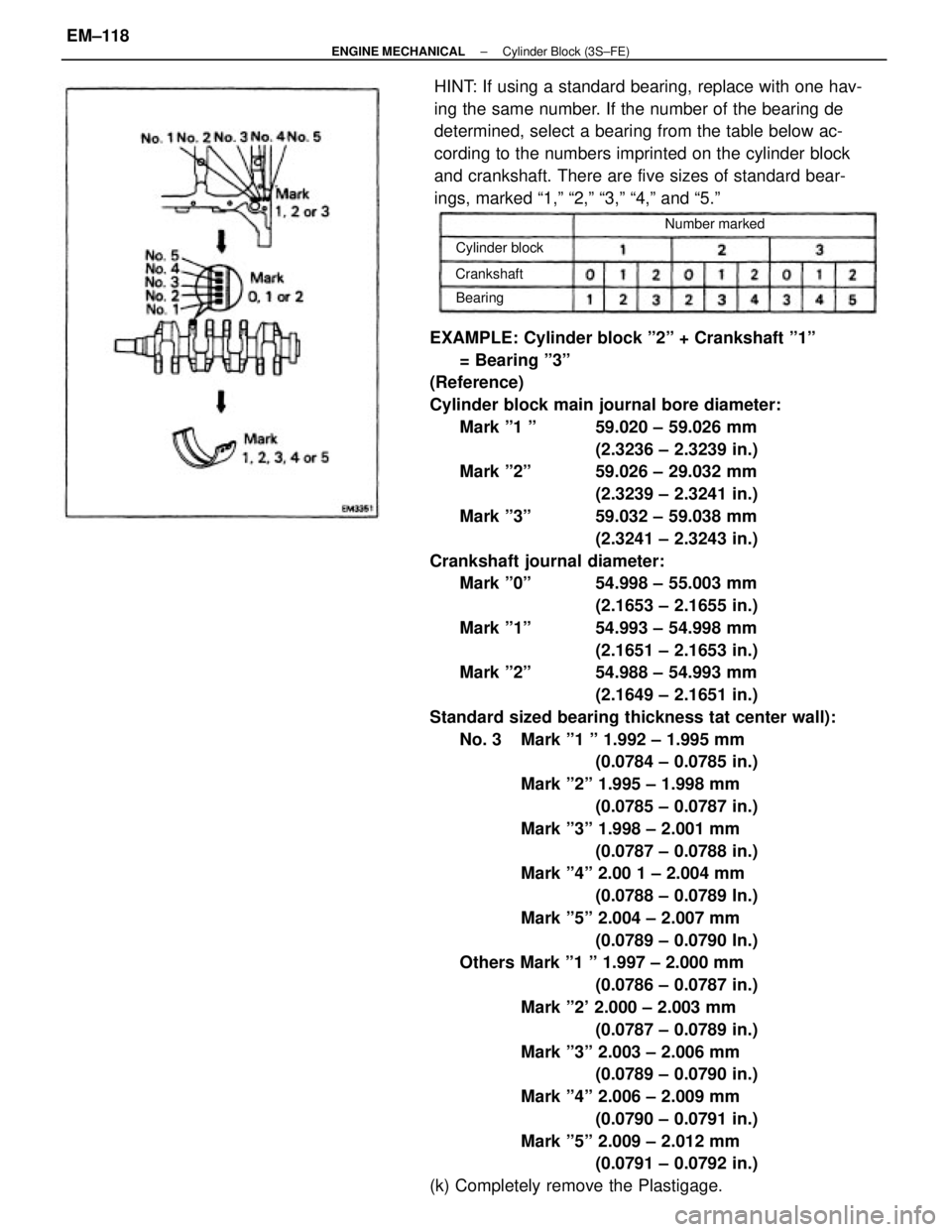
EXAMPLE: Cylinder block º2º + Crankshaft º1º
= Bearing º3º
(Reference)
Cylinder block main journal bore diameter:
Mark º1 º 59.020 ± 59.026 mm
(2.3236 ± 2.3239 in.)
Mark º2º 59.026 ± 29.032 mm
(2.3239 ± 2.3241 in.)
Mark º3º 59.032 ± 59.038 mm
(2.3241 ± 2.3243 in.)
Crankshaft journal diameter:
Mark º0º 54.998 ± 55.003 mm
(2.1653 ± 2.1655 in.)
Mark º1º 54.993 ± 54.998 mm
(2.1651 ± 2.1653 in.)
Mark º2º 54.988 ± 54.993 mm
(2.1649 ± 2.1651 in.)
Standard sized bearing thickness tat center wall):
No. 3 Mark º1 º 1.992 ± 1.995 mm
(0.0784 ± 0.0785 in.)
Mark º2º 1.995 ± 1.998 mm
(0.0785 ± 0.0787 in.)
Mark º3º 1.998 ± 2.001 mm
(0.0787 ± 0.0788 in.)
Mark º4º 2.00 1 ± 2.004 mm
(0.0788 ± 0.0789 In.)
Mark º5º 2.004 ± 2.007 mm
(0.0789 ± 0.0790 In.)
Others Mark º1 º 1.997 ± 2.000 mm
(0.0786 ± 0.0787 in.)
Mark º2' 2.000 ± 2.003 mm
(0.0787 ± 0.0789 in.)
Mark º3º 2.003 ± 2.006 mm
(0.0789 ± 0.0790 in.)
Mark º4º 2.006 ± 2.009 mm
(0.0790 ± 0.0791 in.)
Mark º5º 2.009 ± 2.012 mm
(0.0791 ± 0.0792 in.)
(k) Completely remove the Plastigage.HINT: If using a standard bearing, replace with one hav-
ing the same number. If the number of the bearing de
determined, select a bearing from the table below ac-
cording to the numbers imprinted on the cylinder block
and crankshaft. There are five sizes of standard bear-
ings, marked ª1,º ª2,º ª3,º ª4,º and ª5.º
Number marked
Cylinder block
Crankshaft
Bearing
± ENGINE MECHANICALCylinder Block (3S±FE)EM±118
Page 1296 of 2389
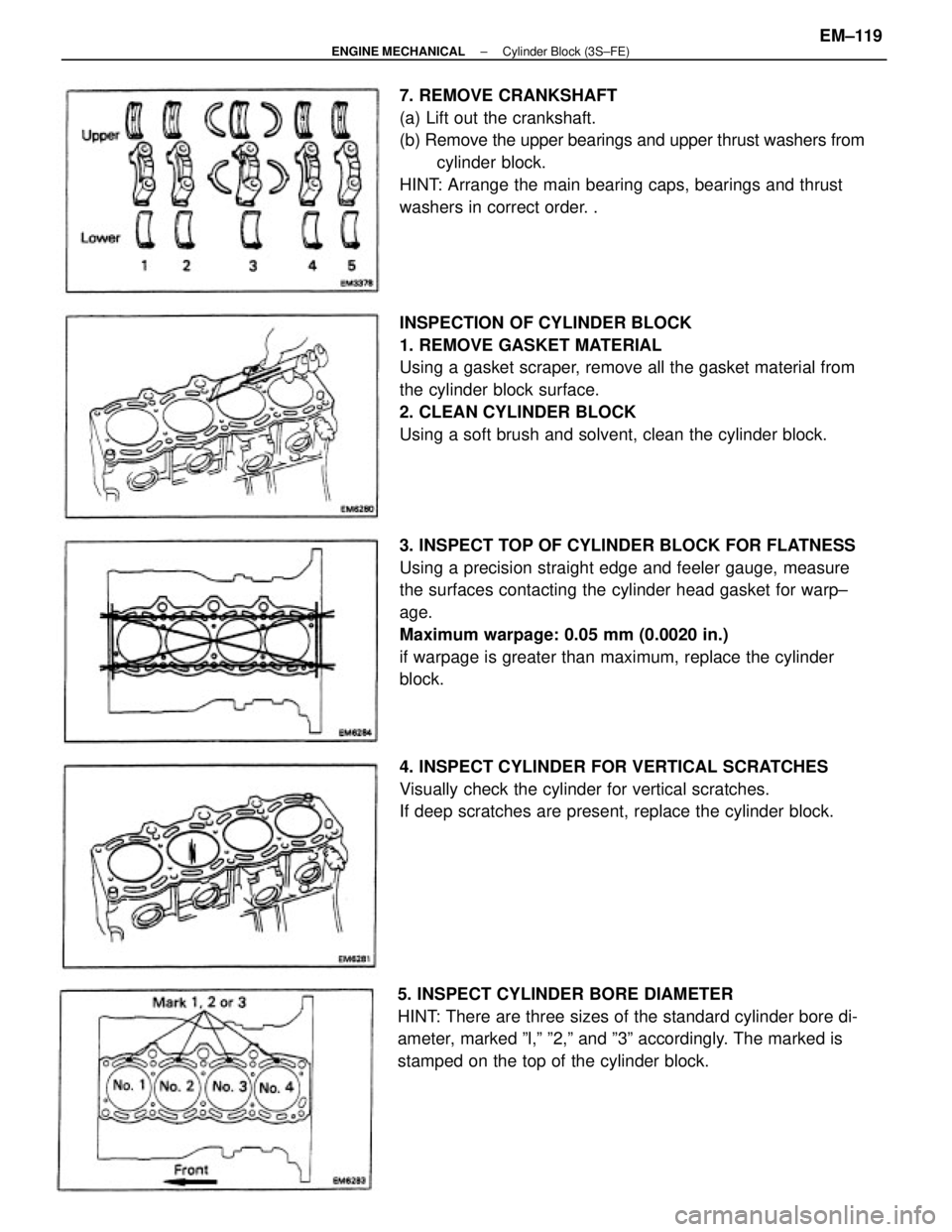
INSPECTION OF CYLINDER BLOCK
1. REMOVE GASKET MATERIAL
Using a gasket scraper, remove all the gasket material from
the cylinder block surface.
2. CLEAN CYLINDER BLOCK
Using a soft brush and solvent, clean the cylinder block.
3. INSPECT TOP OF CYLINDER BLOCK FOR FLATNESS
Using a precision straight edge and feeler gauge, measure
the surfaces contacting the cylinder head gasket for warp±
age.
Maximum warpage: 0.05 mm (0.0020 in.)
if warpage is greater than maximum, replace the cylinder
block. 7. REMOVE CRANKSHAFT
(a) Lift out the crankshaft.
(b) Remove the upper bearings and upper thrust washers from
cylinder block.
HINT: Arrange the main bearing caps, bearings and thrust
washers in correct order. .
5. INSPECT CYLINDER BORE DIAMETER
HINT: There are three sizes of the standard cylinder bore di-
ameter, marked ºl,º º2,º and º3º accordingly. The marked is
stamped on the top of the cylinder block.4. INSPECT CYLINDER FOR VERTICAL SCRATCHES
Visually check the cylinder for vertical scratches.
If deep scratches are present, replace the cylinder block.
± ENGINE MECHANICALCylinder Block (3S±FE)EM±119