Page 1321 of 2389
35. REMOVE PS OIL RESERVOIR TANK WITHOUT
DISCONNECTING HOSES
Remove the two bolts and reservoir tank. Disconnect the
ground strap.
36. REMOVE ENGINE RH MOUNTING STAYS
(a) Remove the three bolts and No. 1 mounting stay.
(b) Remove the bolt, nut and No. 2 mounting stay.
38. REMOVE ENGINE AND TRANSAXLE ASSEMBLY
FROM VEHICLE
(a) Attach the engine hoist chain to the engine hangers.37. REMOVE ENGINE LH MOUNTING STAY
(M/T)
Remove the bolt, two nuts and mounting stay.
(A/T)
Remove the three nuts and mounting
stay.
± ENGINE MECHANICALCylinder Block (2VZ±FE)EM±144
Page 1322 of 2389
(f) Lift the engine out of the vehicle slowly and carefully.
NOTICE: Be careful not to hit the PS gear housing or
neutral start switch.
(g) Make sure the engine is clear of all wiring, hoses and
cables.
(h) Place the engine. and transaxle assembly onto the
stand. (d) Remove the through bolt, nut, four bolts and LH
mounting insulator.
(e) Remove the three bolts and LH mounting bracket. (b) (w/ A.B.S.)
Remove the clamp bolts of the PS oil cooler pipes.
(c) Remove the bolt, four nuts and RH mounting insulator.
39. (A/T)
REMOVE STARTER
40. SEPARATE ENGINE AND TRANSAXLE
± ENGINE MECHANICALCylinder Block (2VZ±FE)EM±145
Page 1323 of 2389
PREPARATION FOR DISASSEMBLY
1. (M/T)
REMOVE CLUTCH COVER AND DISC
2. (M/T)
REMOVE FLYWHEEL
3. (A/T)
REMOVE DRIVE PLATE
4 REMOVE REAR END PLATE
Remove the bolt and end plate.
5. INSTALL ENGINE TO ENGINE STAND FOR
DISASSEMBLY
6. REMOVE DISTRIBUTOR (See page IG±18)
7. REMOVE TIMING BELT AND PULLEYS
(See page EM±34)
8. REMOVE CYLINDER HEADS (See page EM±76)
9. REMOVE WATER PUMP (See page CO±9)
10. REMOVE OIL PAN AND OIL PUMP
(See page LU±17)
11. REMOVE OIL FILTER (See page LU±7)
12. REMOVE KNOCK SENSOR
Using SST, remove the knock sensor.
SST 09816±30010
13. REMOVE WATER BY±PASS PIPE
Remove the two bolts, two nuts and by±pass pipe.
14. REMOVE NO.2 IDLER PULLEY BRACKET
Remove the three bolts and mounting bracket.
± ENGINE MECHANICALCylinder Block (2VZ±FE)EM±146
Page 1324 of 2389
2. CHECK CONNECTING ROD THRUST CLEARANCE
Using a dial indicator, measure the thrust clearance while
moving the connecting rod back and forth.
Standard thrust clearance: 0.150 ± 0.330 mm
(0.0059 ± 0.0130 in.)
Maximum thrust clearance: 0.38 mm (0.0150 in.)
If the thrust clearance is greater than maximum, replace the
connecting rod assembly. If necessary, replace the crank-
shaft.
3. REMOVE CONNECTING ROD CAPS AND CHECK OIL
CLEARANCE
(a) Using a punch or numbering stamp, place the rnatchmarks
on the connecting rod and cap to ensure correct reas-
sembly.
(c) Using a plastic±faced hammer, lightly tap the connect-
ing rod bolts and lift off the connecting rod cap.
HINT: Keep the lower bearing inserted with the connect-
ing cap.
DISASSEMBLY OF CYLINDER BLOCK
(See page EM±139)
1. REMOVE REAR OIL SEAL RETAINER
Remove the six bolts and retainer.
(b) Using SST, remove the connecting rod cap nuts.
SST 09011±38121
± ENGINE MECHANICALCylinder Block (2VZ±FE)EM±147
Page 1325 of 2389
(i) Remove the connecting rod cap.
(j) Measure the Plastigage at widest point.
Standard oil clearance:
STD 0.028 ± 0.065 mm
(0.0011 ± 0.0026 in.)
U/S 0.25 0.027 ± 0.080 mm
(0.0011 ± 0.0031 in.)
Maximum oil clearance: 0.08 mm (0.0031 in.)
If the oil clearance is greater than maximum, replace
the bearings. If necessary, grind or replace the crank-
shaft. (e) Clean the crank pin and bearing.
(f) Check the crank pin and bearing for pitting and scratches.
If the crank pin or bearing is damaged, replace the bearing.
If necessary, grind or replace the crankshaft.
(h) Install the connecting rod cap.
(See step 6 on page EM±165)
Torque: 1st 250 kg±cm (18 ft±ib, 25 N±m)
2nd turns 90°
NOTICE: Do not turn the crankshaft
(d) Cover the connecting rod bolts with a short piece of
hose to protect the crankshaft from damage.
(g) Lay a strip of Plastigage across the crank pin.
± ENGINE MECHANICALCylinder Block (2VZ±FE)EM±148
Page 1326 of 2389
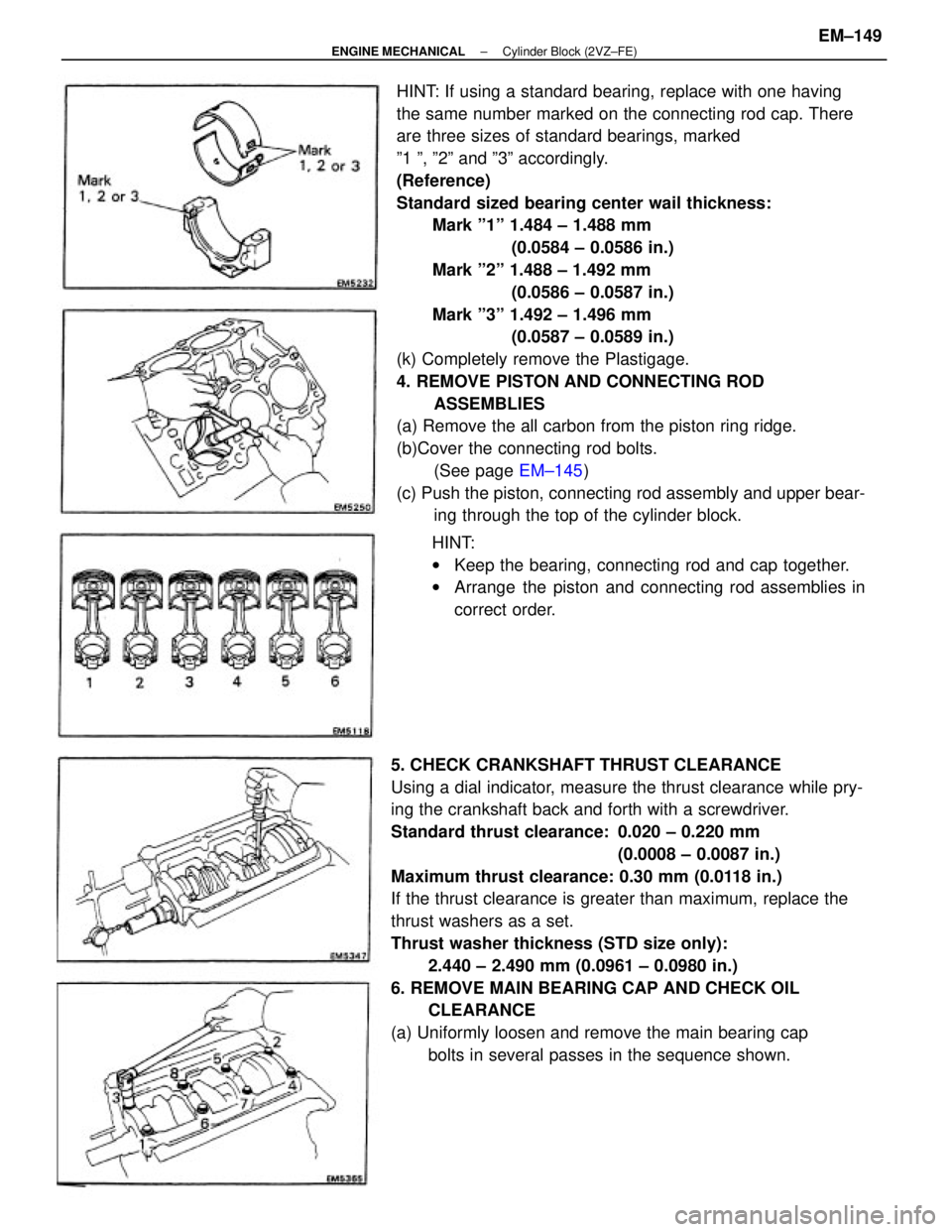
HINT: If using a standard bearing, replace with one having
the same number marked on the connecting rod cap. There
are three sizes of standard bearings, marked
º1 º, º2º and º3º accordingly.
(Reference)
Standard sized bearing center wail thickness:
Mark º1º 1.484 ± 1.488 mm
(0.0584 ± 0.0586 in.)
Mark º2º 1.488 ± 1.492 mm
(0.0586 ± 0.0587 in.)
Mark º3º 1.492 ± 1.496 mm
(0.0587 ± 0.0589 in.)
(k) Completely remove the Plastigage.
4. REMOVE PISTON AND CONNECTING ROD
ASSEMBLIES
(a) Remove the all carbon from the piston ring ridge.
(b)Cover the connecting rod bolts.
(See page EM±145)
(c) Push the piston, connecting rod assembly and upper bear-
ing through the top of the cylinder block.
5. CHECK CRANKSHAFT THRUST CLEARANCE
Using a dial indicator, measure the thrust clearance while pry-
ing the crankshaft back and forth with a screwdriver.
Standard thrust clearance: 0.020 ± 0.220 mm
(0.0008 ± 0.0087 in.)
Maximum thrust clearance: 0.30 mm (0.0118 in.)
If the thrust clearance is greater than maximum, replace the
thrust washers as a set.
Thrust washer thickness (STD size only):
2.440 ± 2.490 mm (0.0961 ± 0.0980 in.)
6. REMOVE MAIN BEARING CAP AND CHECK OIL
CLEARANCE
(a) Uniformly loosen and remove the main bearing cap
bolts in several passes in the sequence shown.HINT:
wKeep the bearing, connecting rod and cap together.
wArrange the piston and connecting rod assemblies in
correct order.
± ENGINE MECHANICALCylinder Block (2VZ±FE)EM±149
Page 1327 of 2389
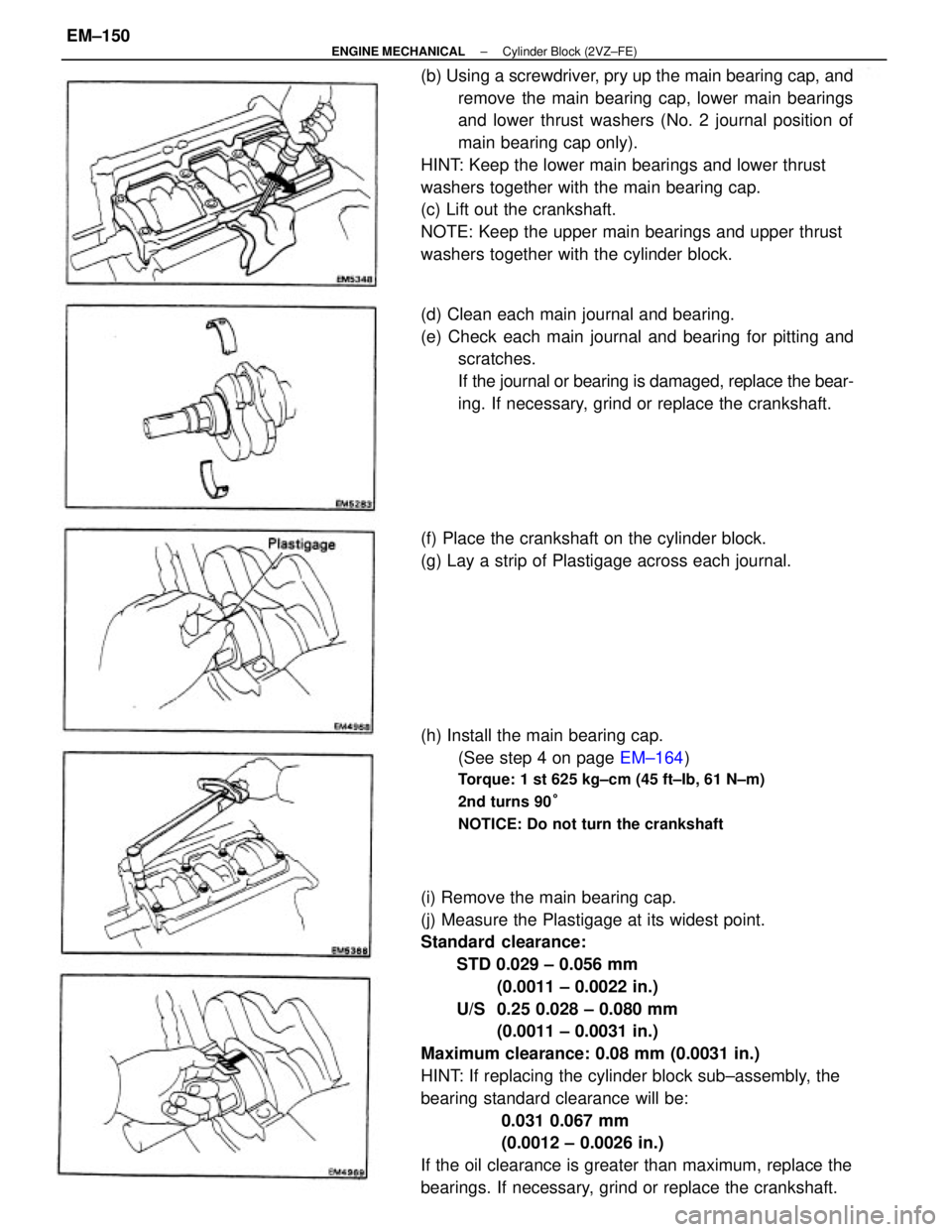
(i) Remove the main bearing cap.
(j) Measure the Plastigage at its widest point.
Standard clearance:
STD 0.029 ± 0.056 mm
(0.0011 ± 0.0022 in.)
U/S 0.25 0.028 ± 0.080 mm
(0.0011 ± 0.0031 in.)
Maximum clearance: 0.08 mm (0.0031 in.)
HINT: If replacing the cylinder block sub±assembly, the
bearing standard clearance will be:
0.031 0.067 mm
(0.0012 ± 0.0026 in.)
If the oil clearance is greater than maximum, replace the
bearings. If necessary, grind or replace the crankshaft. (b) Using a screwdriver, pry up the main bearing cap, and
remove the main bearing cap, lower main bearings
and lower thrust washers (No. 2 journal position of
main bearing cap only).
HINT: Keep the lower main bearings and lower thrust
washers together with the main bearing cap.
(c) Lift out the crankshaft.
NOTE: Keep the upper main bearings and upper thrust
washers together with the cylinder block.
(d) Clean each main journal and bearing.
(e) Check each main journal and bearing for pitting and
scratches.
If the journal or bearing is damaged, replace the bear-
ing. If necessary, grind or replace the crankshaft.
(h) Install the main bearing cap.
(See step 4 on page EM±164)
Torque: 1 st 625 kg±cm (45 ft±Ib, 61 N±m)
2nd turns 90°
NOTICE: Do not turn the crankshaft
(f) Place the crankshaft on the cylinder block.
(g) Lay a strip of Plastigage across each journal.
± ENGINE MECHANICALCylinder Block (2VZ±FE)EM±150
Page 1328 of 2389
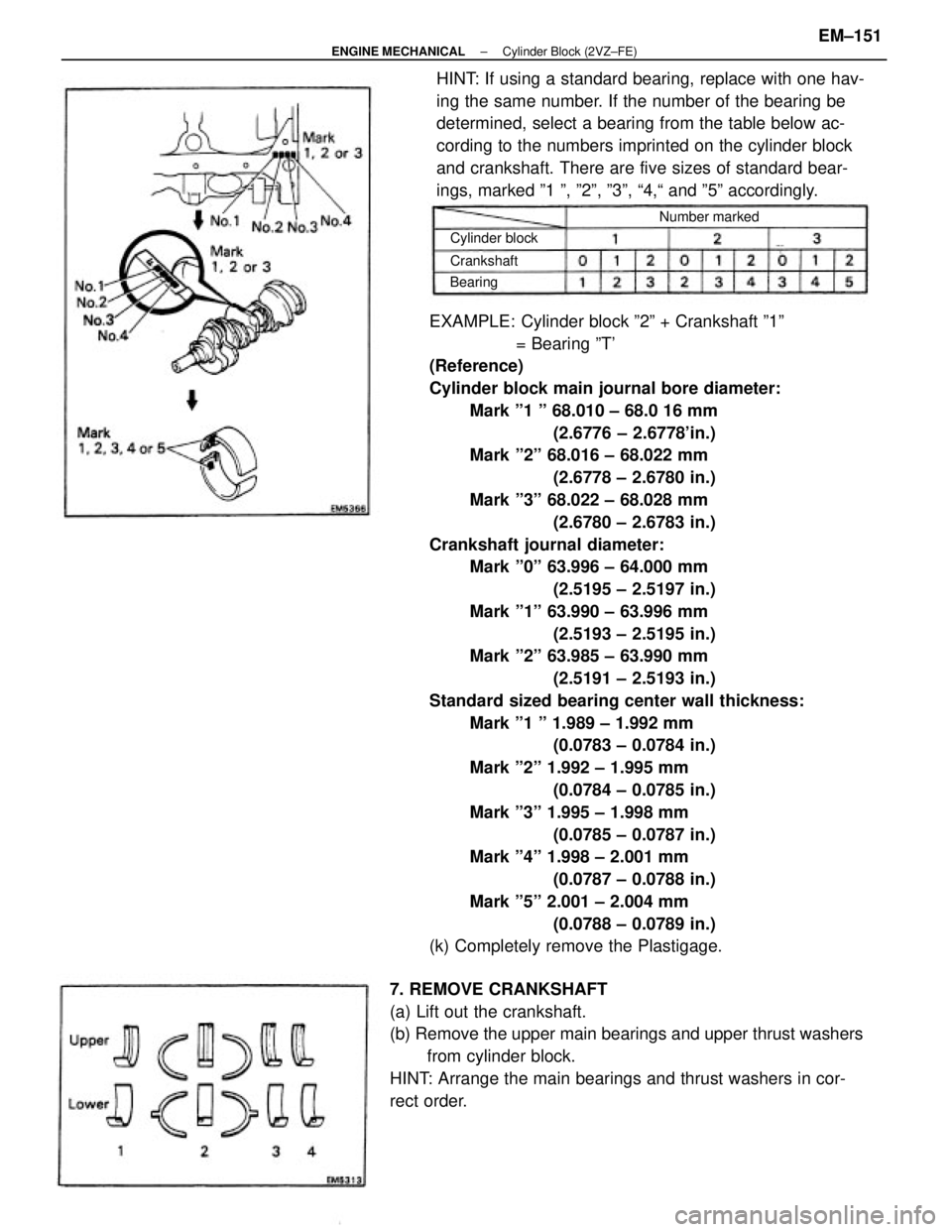
EXAMPLE: Cylinder block º2º + Crankshaft º1º
= Bearing ºT'
(Reference)
Cylinder block main journal bore diameter:
Mark º1 º 68.010 ± 68.0 16 mm
(2.6776 ± 2.6778'in.)
Mark º2º 68.016 ± 68.022 mm
(2.6778 ± 2.6780 in.)
Mark º3º 68.022 ± 68.028 mm
(2.6780 ± 2.6783 in.)
Crankshaft journal diameter:
Mark º0º 63.996 ± 64.000 mm
(2.5195 ± 2.5197 in.)
Mark º1º 63.990 ± 63.996 mm
(2.5193 ± 2.5195 in.)
Mark º2º 63.985 ± 63.990 mm
(2.5191 ± 2.5193 in.)
Standard sized bearing center wall thickness:
Mark º1 º 1.989 ± 1.992 mm
(0.0783 ± 0.0784 in.)
Mark º2º 1.992 ± 1.995 mm
(0.0784 ± 0.0785 in.)
Mark º3º 1.995 ± 1.998 mm
(0.0785 ± 0.0787 in.)
Mark º4º 1.998 ± 2.001 mm
(0.0787 ± 0.0788 in.)
Mark º5º 2.001 ± 2.004 mm
(0.0788 ± 0.0789 in.)
(k) Completely remove the Plastigage.
7. REMOVE CRANKSHAFT
(a) Lift out the crankshaft.
(b) Remove the upper main bearings and upper thrust washers
from cylinder block.
HINT: Arrange the main bearings and thrust washers in cor-
rect order.HINT: If using a standard bearing, replace with one hav-
ing the same number. If the number of the bearing be
determined, select a bearing from the table below ac-
cording to the numbers imprinted on the cylinder block
and crankshaft. There are five sizes of standard bear-
ings, marked º1 º, º2º, º3º, ª4,ª and º5º accordingly.
Number marked
Cylinder block
Crankshaft
Bearing
± ENGINE MECHANICALCylinder Block (2VZ±FE)EM±151