Page 1977 of 2389
2. CHECK OIL CLEARANCE OF THIRD AND FOURTH
GEAR
Using dial indicator, measure the oil clearance between
the gear and shaft.
Standard clearance:
3rd gear 0.009 ± 0.053 mm
(0.0004 ± 0.0021 in.)
4th gear 0.009 ± 0.051 mm
(0.0004 ± 0.0020 in.)
Maximum clearance:
3rd and 4th gear 0.070 mm (0.0028 in.)
If clearance exceeds the limit, replace the gear, needle
roller bearing or shaft.
3. REMOVE SNAP RING
Using two screwdrivers and a hammer, tap out the snap
ring.
4. REMOVE RADIAL BALL BEARING AND FOURTH GEAR
Using SST and a press, remove the radial ball bearing.
SST 09950±00020
5.REMOVE NEEDLE ROLLER BEARINGS, SPACER AND
SYNCHRONIZER RING
7. REMOVE NO.2 CLUTCH HUB ASSEMBLY,
SYNCHRONIZER RING AND THIRD GEAR
Using a press, remove No.2 hub sleeve, 3rd gear, syn-
chronizer ring and needle roller bearings.
8. REMOVE NEEDLE ROLLER BEARING6. REMOVE SNAP RING
Using two screwdrivers and a hammer, tap out the snap ring.
± MANUAL TRANSAXLEComponent PartsMT±63
Page 1978 of 2389
9. REMOVE INPUT SHAFT FRONT BEARING INNER
RACE
Using SST and a press, remove the inner race.
SST 09950±00020
± MANUAL TRANSAXLEComponent PartsMT±64
Page 1979 of 2389
3. INSPECT INPUT SHAFT
(a) Check the input shaft for wear or damage.
(b) Using a micrometer, measure the outer diameter of
the input shaft journal surface.
Minimum outer diameter:
Part A 32.930 mm (1.2965 in.)
Part B and C 35.950 mm (1.4154 in.) 2. MEASURE CLEARANCE OF NO.2 SHIFT FORK AND
HUB SLEEVE
Using a feeler gauge, measure the clearance between
the hub sleeve and shift fork.
Maximum clearance: 1.0 mm (0.039 in.)
If the clearance exceeds the limit, replace the shift fork
or hub sleeve.
INSPECTION OF INPUT SHAFT COMPONENT
PARTS
1. INSPECT SYNCHRONIZER RINGS
(a) Check for wear or damage.
(b) Turn the ring and push it in to check the braking action.
(c) Measure the clearance between the synchronizer
ring back and the gear spline end.
Minimum clearance: 0.6 mm (0.024 in.)
If the clearance is less than the limit, replace the
synchronizer ring.
(c) Using a dial indicator, check the shaft runout.
Maximum runout: 0.05 mm (0.0020 in.)
± MANUAL TRANSAXLEComponent PartsMT±65
Page 1980 of 2389
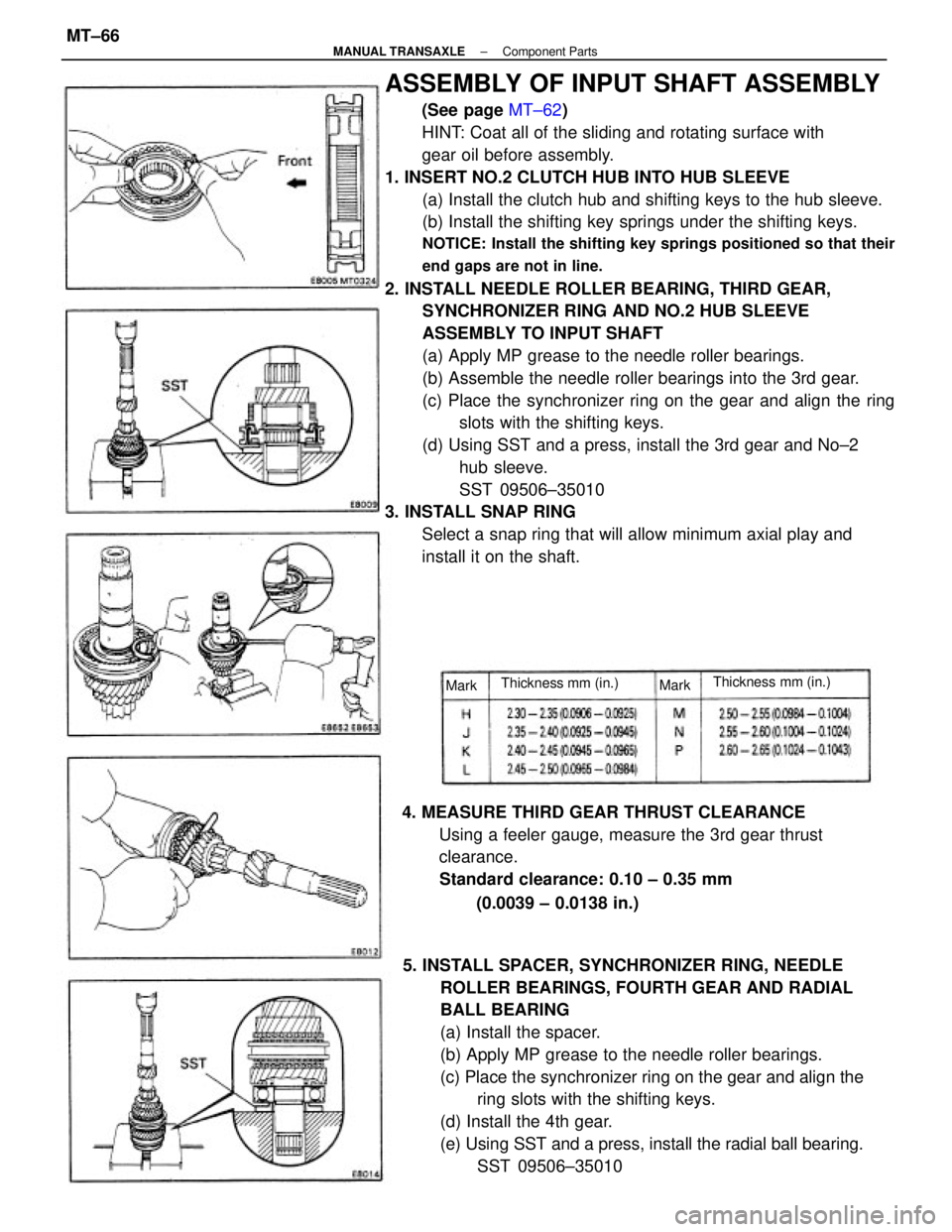
ASSEMBLY OF INPUT SHAFT ASSEMBLY
(See page MT±62)
HINT: Coat all of the sliding and rotating surface with
gear oil before assembly.
1. INSERT NO.2 CLUTCH HUB INTO HUB SLEEVE
(a) Install the clutch hub and shifting keys to the hub sleeve.
(b) Install the shifting key springs under the shifting keys.
NOTICE: Install the shifting key springs positioned so that their
end gaps are not in line.
2. INSTALL NEEDLE ROLLER BEARING, THIRD GEAR,
SYNCHRONIZER RING AND NO.2 HUB SLEEVE
ASSEMBLY TO INPUT SHAFT
(a) Apply MP grease to the needle roller bearings.
(b) Assemble the needle roller bearings into the 3rd gear.
(c) Place the synchronizer ring on the gear and align the ring
slots with the shifting keys.
(d) Using SST and a press, install the 3rd gear and No±2
hub sleeve.
SST 09506±35010
3. INSTALL SNAP RING
Select a snap ring that will allow minimum axial play and
install it on the shaft.
5. INSTALL SPACER, SYNCHRONIZER RING, NEEDLE
ROLLER BEARINGS, FOURTH GEAR AND RADIAL
BALL BEARING
(a) Install the spacer.
(b) Apply MP grease to the needle roller bearings.
(c) Place the synchronizer ring on the gear and align the
ring slots with the shifting keys.
(d) Install the 4th gear.
(e) Using SST and a press, install the radial ball bearing.
SST 09506±35010 4. MEASURE THIRD GEAR THRUST CLEARANCE
Using a feeler gauge, measure the 3rd gear thrust
clearance.
Standard clearance: 0.10 ± 0.35 mm
(0.0039 ± 0.0138 in.)
Thickness mm (in.)
Thickness mm (in.)
MarkMark
± MANUAL TRANSAXLEComponent PartsMT±66
Page 1981 of 2389
7. MEASURE FOURTH GEAR TH . RUST CLEARANCE
Using a feeler gauge, measure the 4th gear thrust clearance.
Standard clearance: 0.10 ± 0.55 mm
(0.0039 ± 0.0217 in:)
8. INSTALL INPUT SHAFT FRONT BEARING INNER RACE
Using SST and a press, install the input shaft front bearing in-
ner race.
SST 09316±60010 (09316±00020) 6. INSTALL SNAP RING
Select a snap ring that will allow minimum axial play and
install it on the shaft.
Thickness mm (in.)
Thickness mm (in.)
Mark
Mark
± MANUAL TRANSAXLEComponent PartsMT±67
Page 1982 of 2389
REMOVAL OF COMPONENT PARTS
COMPONENTS
± MANUAL TRANSAXLERemoval of Component PartsMT±47
Page 1983 of 2389
COMPONENTS (Cont'd)
± MANUAL TRANSAXLERemoval of Component PartsMT±48
Page 1984 of 2389
COMPONENTS (Cont'd)
± MANUAL TRANSAXLERemoval of Component PartsMT±49