Page 2041 of 2389
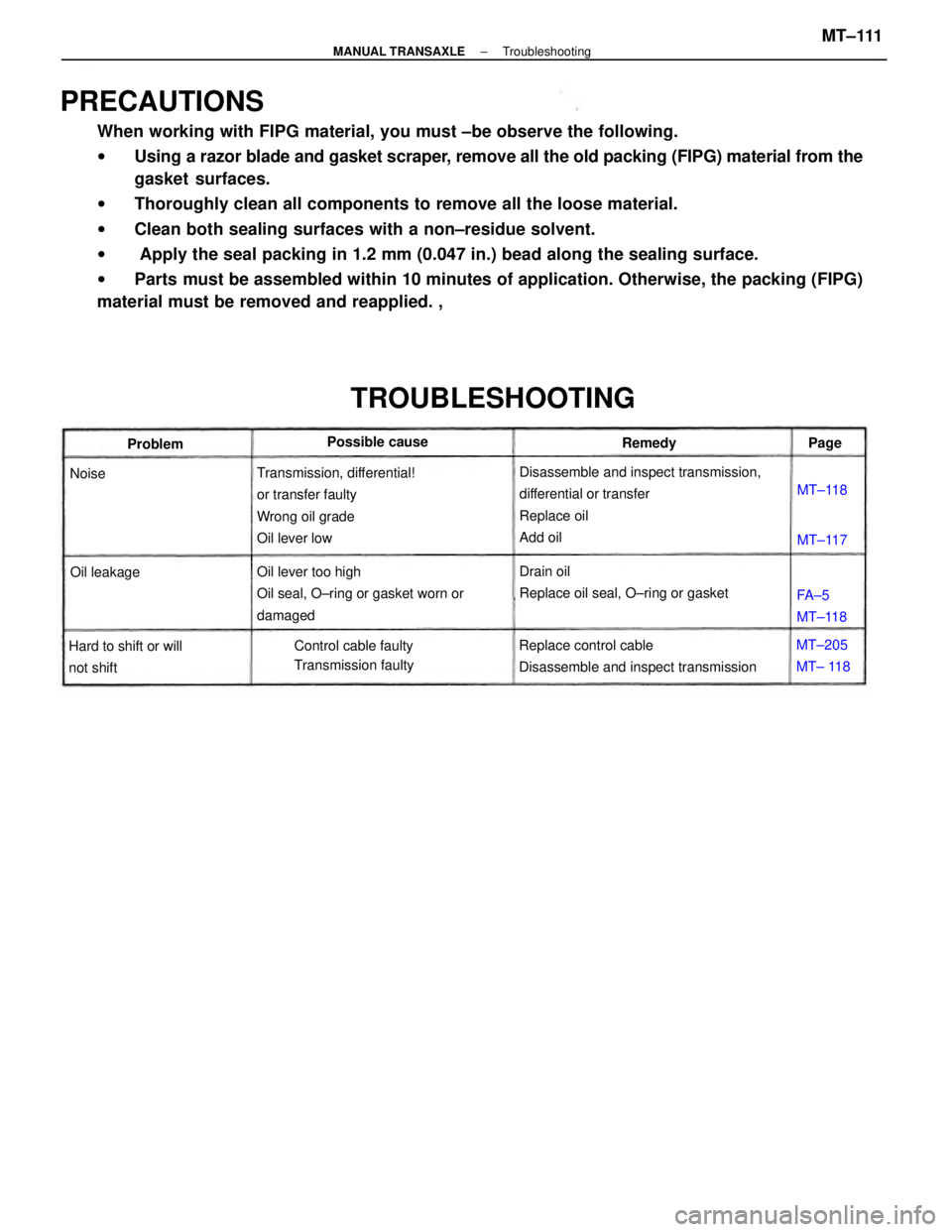
PRECAUTIONS
When working with FIPG material, you must ±be observe the following.
wUsing a razor blade and gasket scraper, remove all the old packing (FIPG) material from the
gasket surfaces.
wThoroughly clean all components to remove all the loose material.
wClean both sealing surfaces with a non±residue solvent.
w Apply the seal packing in 1.2 mm (0.047 in.) bead along the sealing surface.
wParts must be assembled within 10 minutes of application. Otherwise, the packing (FIPG)
material must be removed and reapplied. ,
Disassemble and inspect transmission,
differential or transfer
Replace oil
Add oil Transmission, differential!
or transfer faulty
Wrong oil grade
Oil lever low
Oil lever too high
Oil seal, O±ring or gasket worn or
damaged
Replace control cable
Disassemble and inspect transmissionDrain oil
Replace oil seal, O±ring or gasket
TROUBLESHOOTING
Control cable faulty
Transmission faulty Hard to shift or will
not shiftPossible cause
MT±205
MT± 118FA±5
MT±118 Oil leakageProblemRemedy
MT±118
MT±117 NoisePage
± MANUAL TRANSAXLETroubleshootingMT±111
Page 2042 of 2389
4. INSTALL OUTPUT SHAFT OIL SEAL
Using SST, drive in a new oil seal.
SST 09325±20010
Oil seal depth: 1.1 ± 1.9 mm (0.043 ± 0.075)
5. INSTALL PROPELLER SHAFT
(See page PR±13)
6. FILL TRANSAXLE WITH GEAR OIL
(See page MT±117)
ON±VEHICLE REPAIR
REPLACEMENT OF OUTPUT SHAFT
OIL SEAL
1. DRAIN TRANSAXLE OIL
2. REMOVE PROPELLER SHAFT
(See page PR±4)
3. REMOVE OUTPUT SHAFT OIL SEAL
Using SST, drive out the oil seal.
SST 09308±00010
± MANUAL TRANSAXLEOn±Vehicle RepairMT±112
Page 2043 of 2389
CENTER DIFFERENTIAL LOCK
CONTROL (E56F5)
SYSTEM DIAGRAM AND WIRING DIAGRAM
± MANUAL TRANSAXLECenter Differential Lock Control (E56F5)MT±113
Page 2044 of 2389
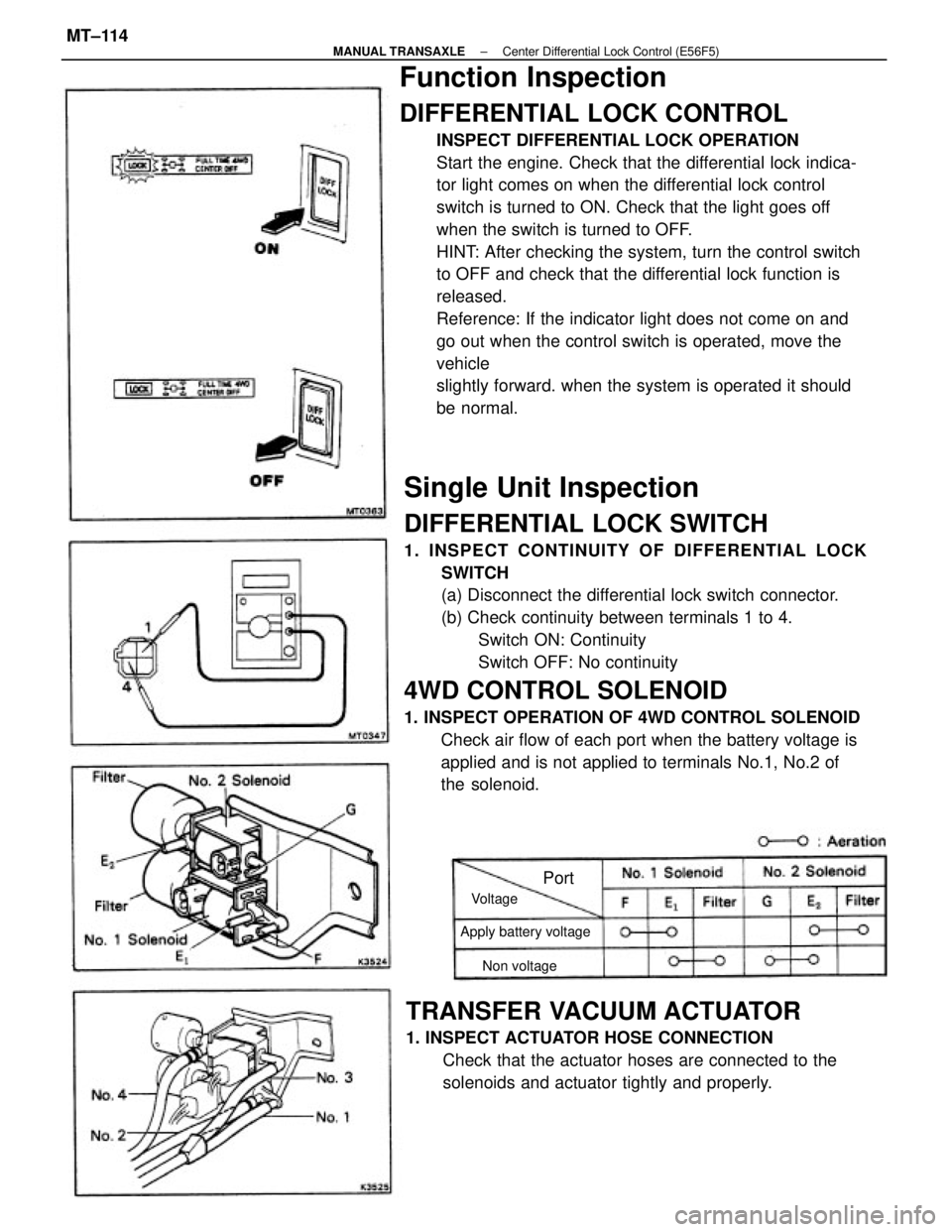
Single Unit Inspection
DIFFERENTIAL LOCK SWITCH
1. INSPECT CONTINUITY OF DIFFERENTIAL LOCK
SWITCH
(a) Disconnect the differential lock switch connector.
(b) Check continuity between terminals 1 to 4.
Switch ON: Continuity
Switch OFF: No continuity
4WD CONTROL SOLENOID
1. INSPECT OPERATION OF 4WD CONTROL SOLENOID
Check air flow of each port when the battery voltage is
applied and is not applied to terminals No.1, No.2 of
the solenoid.
Function Inspection
DIFFERENTIAL LOCK CONTROL
INSPECT DIFFERENTIAL LOCK OPERATION
Start the engine. Check that the differential lock indica-
tor light comes on when the differential lock control
switch is turned to ON. Check that the light goes off
when the switch is turned to OFF.
HINT: After checking the system, turn the control switch
to OFF and check that the differential lock function is
released.
Reference: If the indicator light does not come on and
go out when the control switch is operated, move the
vehicle
slightly forward. when the system is operated it should
be normal.
TRANSFER VACUUM ACTUATOR
1. INSPECT ACTUATOR HOSE CONNECTION
Check that the actuator hoses are connected to the
solenoids and actuator tightly and properly.
Apply battery voltage
Non voltage Voltage
Port
± MANUAL TRANSAXLECenter Differential Lock Control (E56F5)MT±114
Page 2045 of 2389
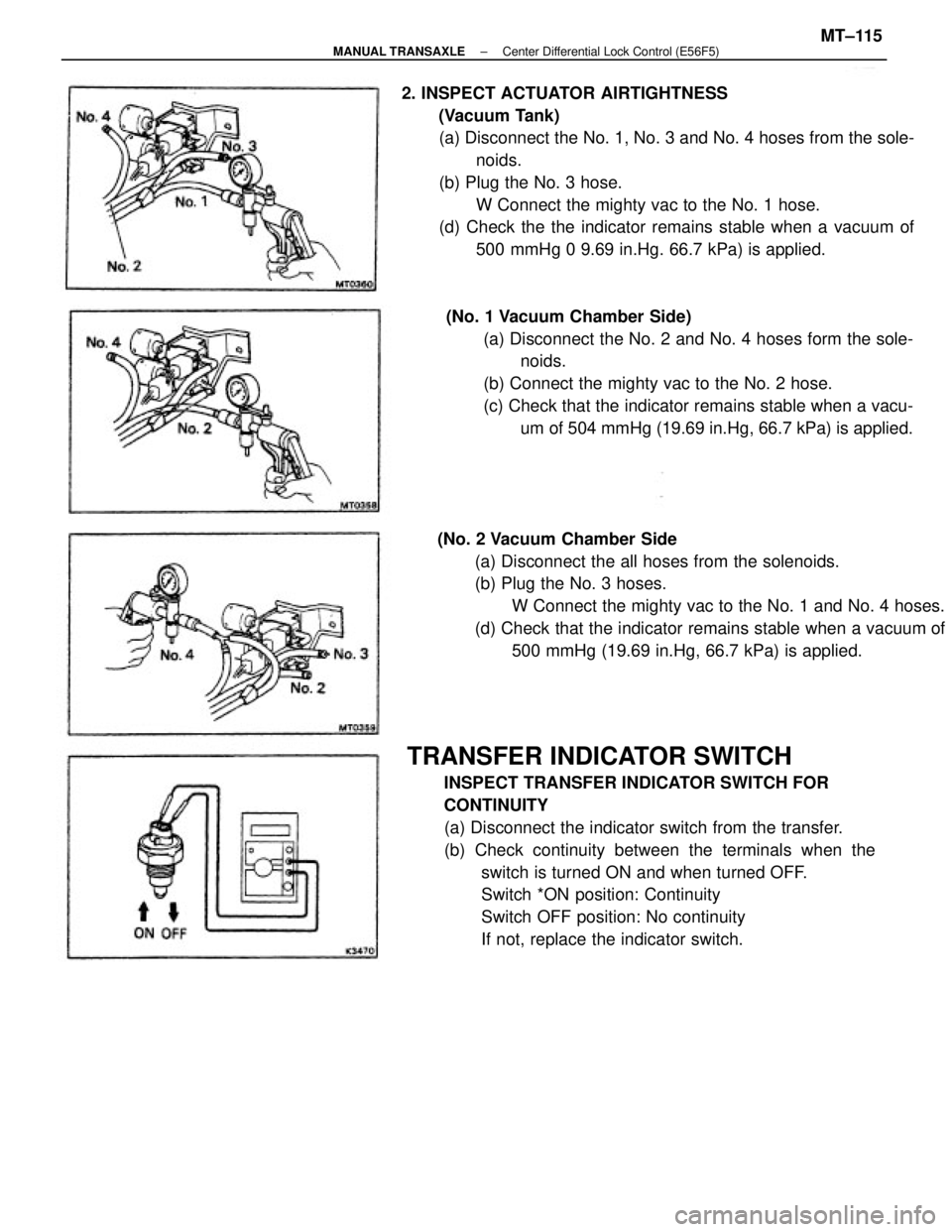
TRANSFER INDICATOR SWITCH
INSPECT TRANSFER INDICATOR SWITCH FOR
CONTINUITY
(a) Disconnect the indicator switch from the transfer.
(b) Check continuity between the terminals when the
switch is turned ON and when turned OFF.
Switch *ON position: Continuity
Switch OFF position: No continuity
If not, replace the indicator switch. 2. INSPECT ACTUATOR AIRTIGHTNESS
(Vacuum Tank)
(a) Disconnect the No. 1, No. 3 and No. 4 hoses from the sole-
noids.
(b) Plug the No. 3 hose.
W Connect the mighty vac to the No. 1 hose.
(d) Check the the indicator remains stable when a vacuum of
500 mmHg 0 9.69 in.Hg. 66.7 kPa) is applied.
(No. 2 Vacuum Chamber Side
(a) Disconnect the all hoses from the solenoids.
(b) Plug the No. 3 hoses.
W Connect the mighty vac to the No. 1 and No. 4 hoses.
(d) Check that the indicator remains stable when a vacuum of
500 mmHg (19.69 in.Hg, 66.7 kPa) is applied. (No. 1 Vacuum Chamber Side)
(a) Disconnect the No. 2 and No. 4 hoses form the sole-
noids.
(b) Connect the mighty vac to the No. 2 hose.
(c) Check that the indicator remains stable when a vacu-
um of 504 mmHg (19.69 in.Hg, 66.7 kPa) is applied.
± MANUAL TRANSAXLECenter Differential Lock Control (E56F5)MT±115
Page 2046 of 2389
REMOVAL AND INSTALLATION OF TRANSAXLE
REMOVAL AND INSTALLATION OF ENGINE
REMOVE ENGINE WITH TRANSAXLE
(See page EM±3)
INSTALL ENGINE WITH TRANSAXLE
(See page EM±7)
REMOVAL AND INSTALLATION OF
TRANSAXLE
REMOVE AND INSTALL TRANSAXLE AS SHOWN
± MANUAL TRANSAXLERemoval and Installation of TransaxleMT±116
Page 2047 of 2389
REPLACEMENT OF TRANSAXLE GEAR OIL
1. DRAIN TRANSAXLE OIL
2. FILL TRANSAXLE OIL WITH GEAR OIL
Oil: Transaxle oil E50 (08885±80206) or equivalent
Recommended oil
Oil grade: API G!±5
Viscosity: SAE 75W±90 or 80W±90
Above ±18°C (0°F) SAE 90
Below ±18°C (0°F) SAE 80W
Capacity: 5.0 liters (5.3 US qts, 4.4 Imp qts)
(MAIN POINT OF REMOVAL AND
INSTALLATION)
1. REMOVE TRANSAXLE ASSEMBLY
HINT: When removing transaxle from engine, remove as the
following procedure since cylinder block rib contacts
transfer case.
(a) Pull straight until there are space of 60 ± 80mm (2 ±3 in.)
between engine and transaxle case.
(e) While holding the transfer output slightly, pull out
whole transaxle.
2. INSTALL TRANSAXLE ASSEMBLY FOLLOWING
REMOVAL SEQUENCE IN REVERSE(b) Move the transmission case cover to the arrow in the
illustration.
± MANUAL TRANSAXLERemoval and Installation of TransaxleMT±117
Page 2048 of 2389
DISASSEMBLY OF INPUT SHAFT
ASSEMBLY
1. MEASURE THIRD AND FOURTH GEAR THRUST
CLEARANCE
Using a feeler gauge, measure the thrust clearance.
Standard clearance:
3rd gear 0.10 ± 0.35 mm
(0.0039 ± 0.0138 in.)
4th gear 0.10 ± 0.55 mm
(0.0039 ± 0.0217 in.)
Maximum clearance:
3rd gear 0.40 mm (0.0157 in.)
4th gear 0.60 mm (0.0236 in.)
COMPONENT PARTS
Input Shaft Assembly
± MANUAL TRANSAXLEComponent Parts (Input Shaft Assembly)MT±134