Page 2665 of 3061
CHARGING SYSTEM
SC-17
< SERVICE INFORMATION >
C
D
E
F
G
H
I
J
L
MA
B
SC
N
O
P
Wiring Diagram - CHARGE -INFOID:0000000003533324
Trouble Diagnosis with Battery/Starting/Charging System TesterINFOID:0000000003533325
NOTE:
To ensure a complete and thorough diagnosis, the battery, starter and generator test segments must be done
as a set from start to finish.
WKWA5141E
Page 2666 of 3061
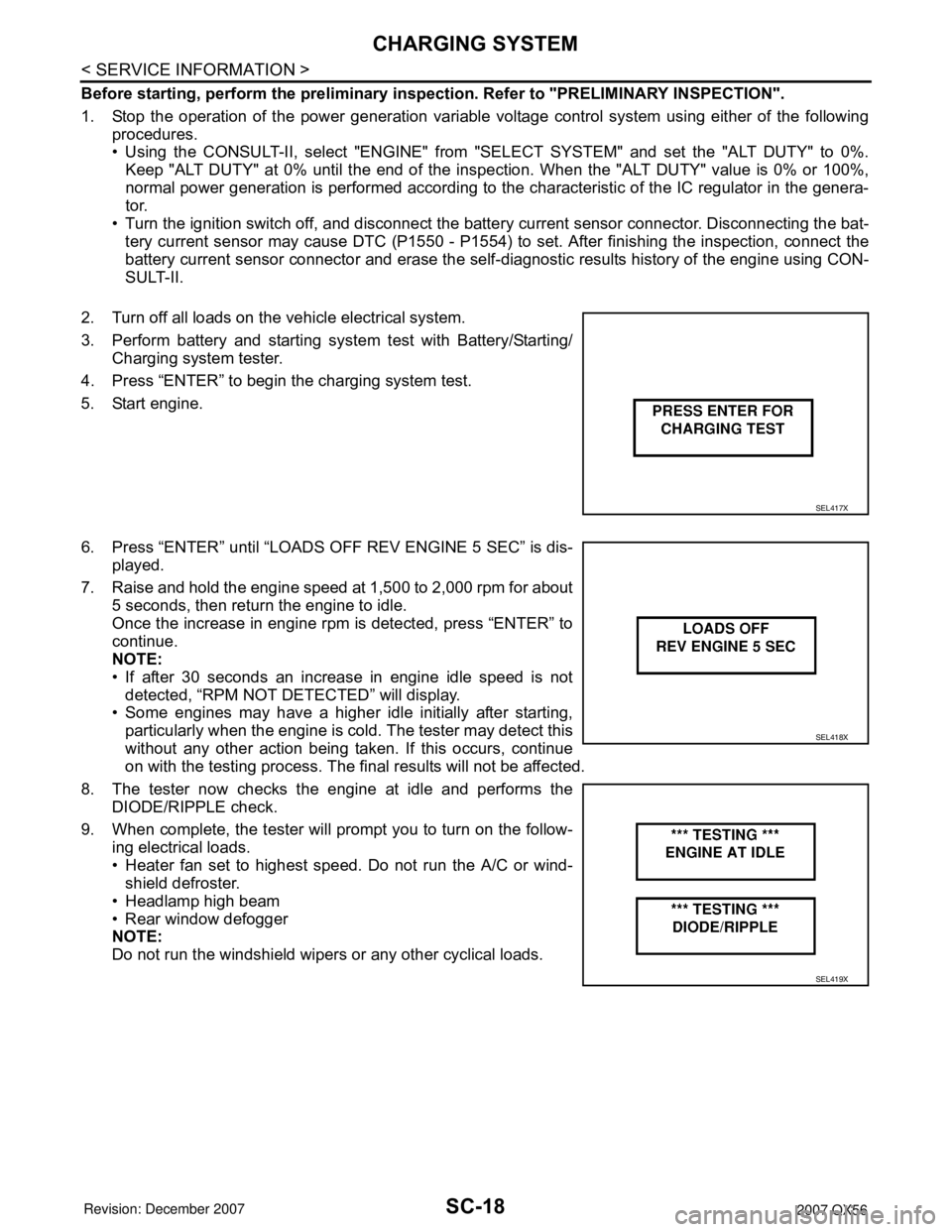
SC-18
< SERVICE INFORMATION >
CHARGING SYSTEM
Before starting, perform the preliminary inspection. Refer to "PRELIMINARY INSPECTION".
1. Stop the operation of the power generation variable voltage control system using either of the following
procedures.
• Using the CONSULT-II, select "ENGINE" from "SELECT SYSTEM" and set the "ALT DUTY" to 0%.
Keep "ALT DUTY" at 0% until the end of the inspection. When the "ALT DUTY" value is 0% or 100%,
normal power generation is performed according to the characteristic of the IC regulator in the genera-
tor.
• Turn the ignition switch off, and disconnect the battery current sensor connector. Disconnecting the bat-
tery current sensor may cause DTC (P1550 - P1554) to set. After finishing the inspection, connect the
battery current sensor connector and erase the self-diagnostic results history of the engine using CON-
SULT-II.
2. Turn off all loads on the vehicle electrical system.
3. Perform battery and starting system test with Battery/Starting/
Charging system tester.
4. Press “ENTER” to begin the charging system test.
5. Start engine.
6. Press “ENTER” until “LOADS OFF REV ENGINE 5 SEC” is dis-
played.
7. Raise and hold the engine speed at 1,500 to 2,000 rpm for about
5 seconds, then return the engine to idle.
Once the increase in engine rpm is detected, press “ENTER” to
continue.
NOTE:
• If after 30 seconds an increase in engine idle speed is not
detected, “RPM NOT DETECTED” will display.
• Some engines may have a higher idle initially after starting,
particularly when the engine is cold. The tester may detect this
without any other action being taken. If this occurs, continue
on with the testing process. The final results will not be affected.
8. The tester now checks the engine at idle and performs the
DIODE/RIPPLE check.
9. When complete, the tester will prompt you to turn on the follow-
ing electrical loads.
• Heater fan set to highest speed. Do not run the A/C or wind-
shield defroster.
• Headlamp high beam
• Rear window defogger
NOTE:
Do not run the windshield wipers or any other cyclical loads.
SEL417X
SEL418X
SEL419X
Page 2667 of 3061
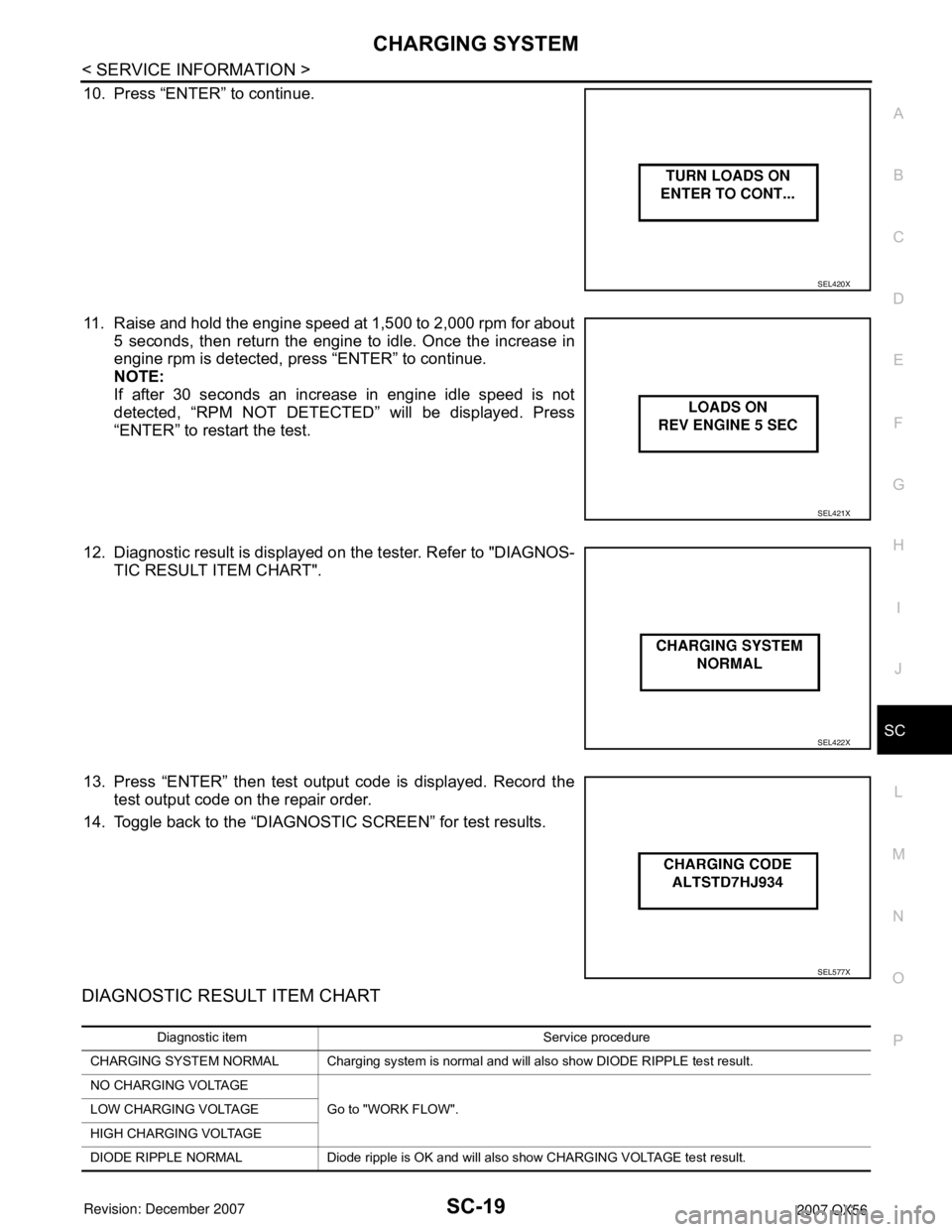
CHARGING SYSTEM
SC-19
< SERVICE INFORMATION >
C
D
E
F
G
H
I
J
L
MA
B
SC
N
O
P
10. Press “ENTER” to continue.
11. Raise and hold the engine speed at 1,500 to 2,000 rpm for about
5 seconds, then return the engine to idle. Once the increase in
engine rpm is detected, press “ENTER” to continue.
NOTE:
If after 30 seconds an increase in engine idle speed is not
detected, “RPM NOT DETECTED” will be displayed. Press
“ENTER” to restart the test.
12. Diagnostic result is displayed on the tester. Refer to "DIAGNOS-
TIC RESULT ITEM CHART".
13. Press “ENTER” then test output code is displayed. Record the
test output code on the repair order.
14. Toggle back to the “DIAGNOSTIC SCREEN” for test results.
DIAGNOSTIC RESULT ITEM CHART
SEL420X
SEL421X
SEL422X
SEL577X
Diagnostic item Service procedure
CHARGING SYSTEM NORMAL Charging system is normal and will also show DIODE RIPPLE test result.
NO CHARGING VOLTAGE
Go to "WORK FLOW". LOW CHARGING VOLTAGE
HIGH CHARGING VOLTAGE
DIODE RIPPLE NORMAL Diode ripple is OK and will also show CHARGING VOLTAGE test result.
Page 2668 of 3061
SC-20
< SERVICE INFORMATION >
CHARGING SYSTEM
WORK FLOW
PRELIMINARY INSPECTION
1.CHECK BATTERY TERMINALS CONNECTION
Check if battery terminals are clean and tight.
OK or NG
OK >> GO TO 2.
EXCESS RIPPLE DETECTEDReplace the generator. Refer to SC-22, "Removal and Installation". Perform “DIODE RIPPLE”
test again using Battery/Starting/Charging system tester to confirm repair.
DIODE RIPPLE NOT DETECTED Go to "WORK FLOW". Diagnostic item Service procedure
WKIA4022E
Page 2669 of 3061
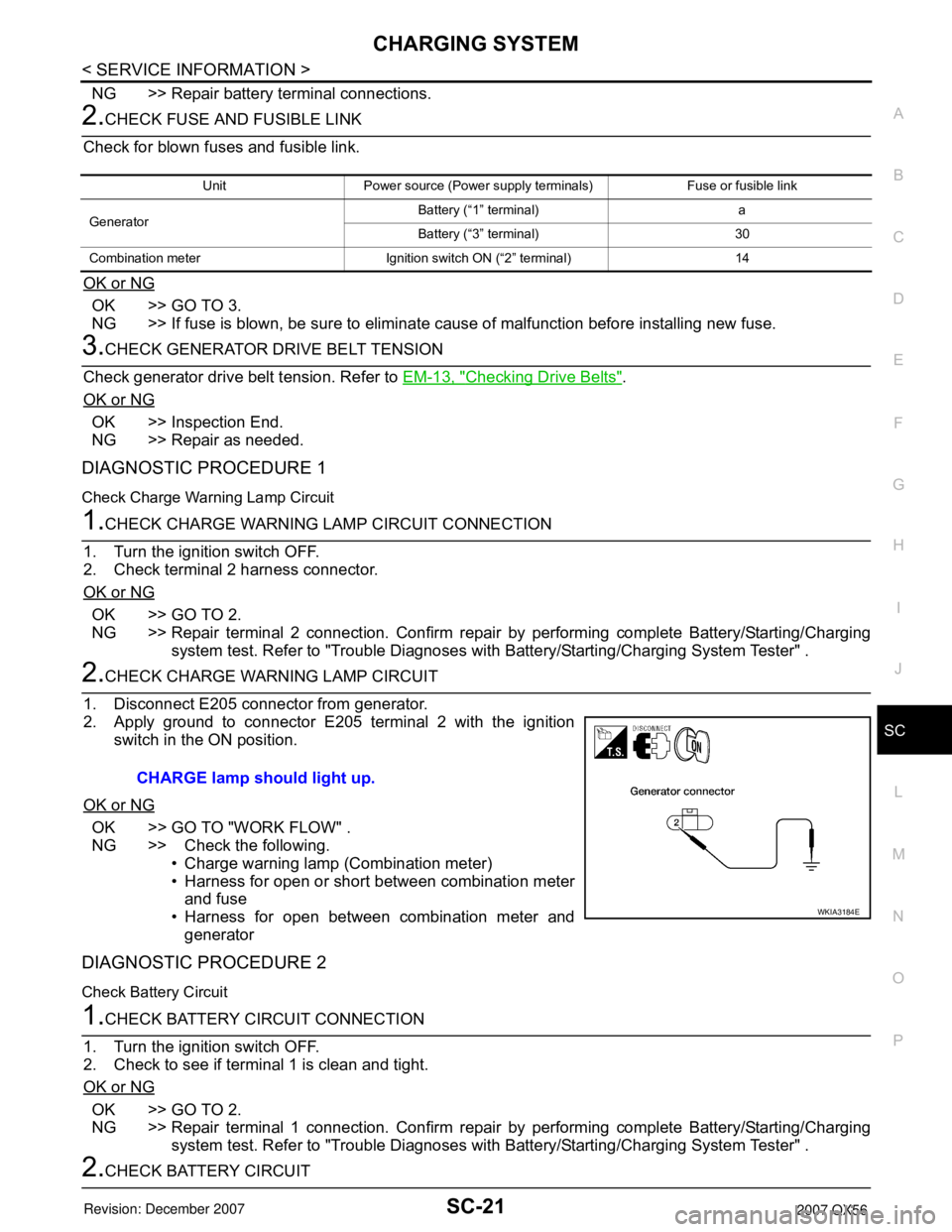
CHARGING SYSTEM
SC-21
< SERVICE INFORMATION >
C
D
E
F
G
H
I
J
L
MA
B
SC
N
O
P
NG >> Repair battery terminal connections.
2.CHECK FUSE AND FUSIBLE LINK
Check for blown fuses and fusible link.
OK or NG
OK >> GO TO 3.
NG >> If fuse is blown, be sure to eliminate cause of malfunction before installing new fuse.
3.CHECK GENERATOR DRIVE BELT TENSION
Check generator drive belt tension. Refer to EM-13, "
Checking Drive Belts".
OK or NG
OK >> Inspection End.
NG >> Repair as needed.
DIAGNOSTIC PROCEDURE 1
Check Charge Warning Lamp Circuit
1.CHECK CHARGE WARNING LAMP CIRCUIT CONNECTION
1. Turn the ignition switch OFF.
2. Check terminal 2 harness connector.
OK or NG
OK >> GO TO 2.
NG >> Repair terminal 2 connection. Confirm repair by performing complete Battery/Starting/Charging
system test. Refer to "Trouble Diagnoses with Battery/Starting/Charging System Tester" .
2.CHECK CHARGE WARNING LAMP CIRCUIT
1. Disconnect E205 connector from generator.
2. Apply ground to connector E205 terminal 2 with the ignition
switch in the ON position.
OK or NG
OK >> GO TO "WORK FLOW" .
NG >> Check the following.
• Charge warning lamp (Combination meter)
• Harness for open or short between combination meter
and fuse
• Harness for open between combination meter and
generator
DIAGNOSTIC PROCEDURE 2
Check Battery Circuit
1.CHECK BATTERY CIRCUIT CONNECTION
1. Turn the ignition switch OFF.
2. Check to see if terminal 1 is clean and tight.
OK or NG
OK >> GO TO 2.
NG >> Repair terminal 1 connection. Confirm repair by performing complete Battery/Starting/Charging
system test. Refer to "Trouble Diagnoses with Battery/Starting/Charging System Tester" .
2.CHECK BATTERY CIRCUIT
Unit Power source (Power supply terminals) Fuse or fusible link
GeneratorBattery (“1” terminal) a
Battery (“3” terminal) 30
Combination meter Ignition switch ON (“2” terminal) 14
CHARGE lamp should light up.
WKIA3184E
Page 2670 of 3061
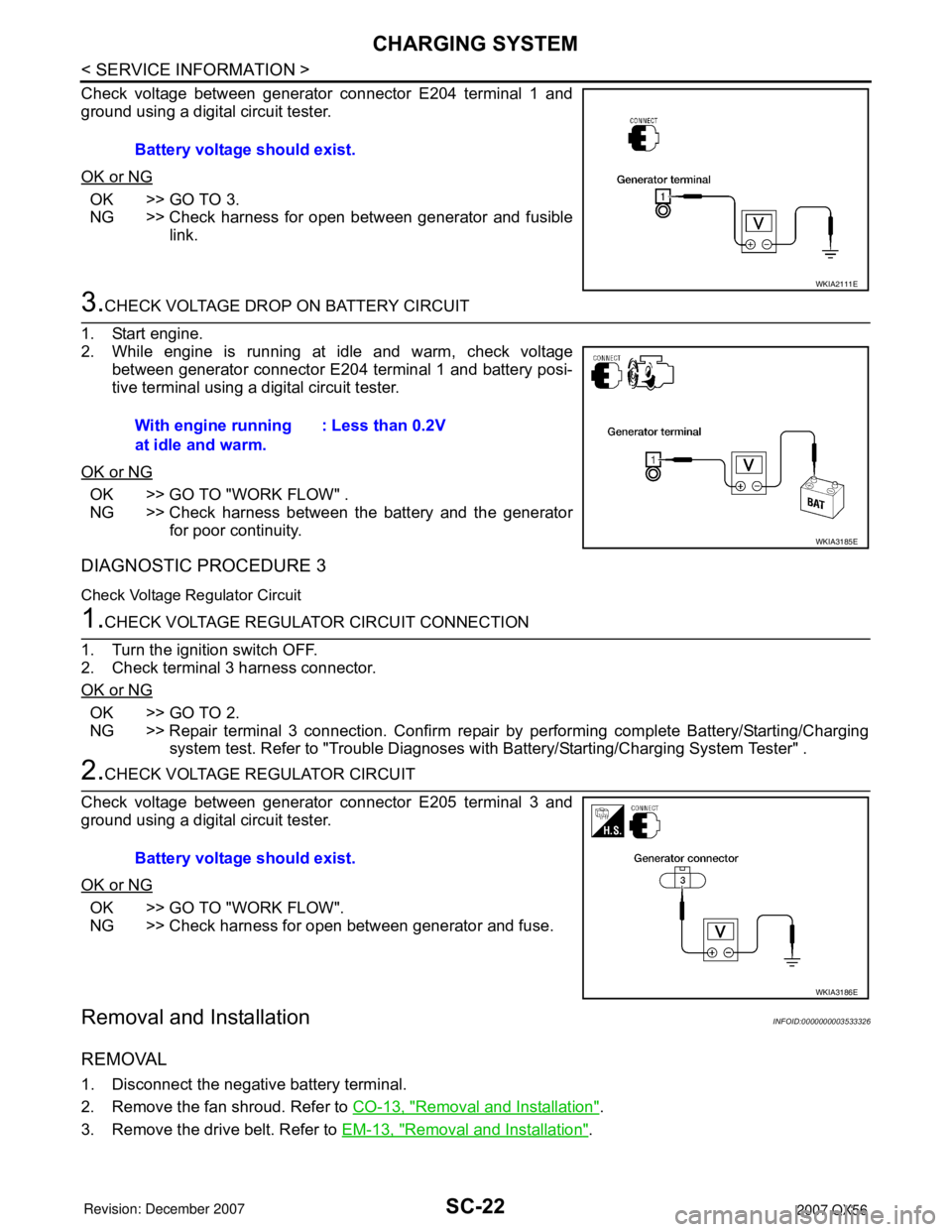
SC-22
< SERVICE INFORMATION >
CHARGING SYSTEM
Check voltage between generator connector E204 terminal 1 and
ground using a digital circuit tester.
OK or NG
OK >> GO TO 3.
NG >> Check harness for open between generator and fusible
link.
3.CHECK VOLTAGE DROP ON BATTERY CIRCUIT
1. Start engine.
2. While engine is running at idle and warm, check voltage
between generator connector E204 terminal 1 and battery posi-
tive terminal using a digital circuit tester.
OK or NG
OK >> GO TO "WORK FLOW" .
NG >> Check harness between the battery and the generator
for poor continuity.
DIAGNOSTIC PROCEDURE 3
Check Voltage Regulator Circuit
1.CHECK VOLTAGE REGULATOR CIRCUIT CONNECTION
1. Turn the ignition switch OFF.
2. Check terminal 3 harness connector.
OK or NG
OK >> GO TO 2.
NG >> Repair terminal 3 connection. Confirm repair by performing complete Battery/Starting/Charging
system test. Refer to "Trouble Diagnoses with Battery/Starting/Charging System Tester" .
2.CHECK VOLTAGE REGULATOR CIRCUIT
Check voltage between generator connector E205 terminal 3 and
ground using a digital circuit tester.
OK or NG
OK >> GO TO "WORK FLOW".
NG >> Check harness for open between generator and fuse.
Removal and InstallationINFOID:0000000003533326
REMOVAL
1. Disconnect the negative battery terminal.
2. Remove the fan shroud. Refer to CO-13, "
Removal and Installation".
3. Remove the drive belt. Refer to EM-13, "
Removal and Installation". Battery voltage should exist.
WKIA2111E
With engine running
at idle and warm.: Less than 0.2V
WKIA3185E
Battery voltage should exist.
WKIA3186E
Page 2671 of 3061
CHARGING SYSTEM
SC-23
< SERVICE INFORMATION >
C
D
E
F
G
H
I
J
L
MA
B
SC
N
O
P
4. Remove the lower bracket, using power tools.
5. Remove the generator upper bolt, using power tools.
6. Remove/disconnect the generator harness connectors.
7. Remove the generator.
INSTALLATION
Installation is in the reverse order of removal.
• Install the generator and check the tension of the drive belt. Refer to EM-13, "
Checking Drive Belts".
CAUTION:
Tighten terminal nut carefully.
WKIA1390E
Terminal nut : 10.8 N·m (1.1 kg-m, 8 ft-lb)
Page 2672 of 3061
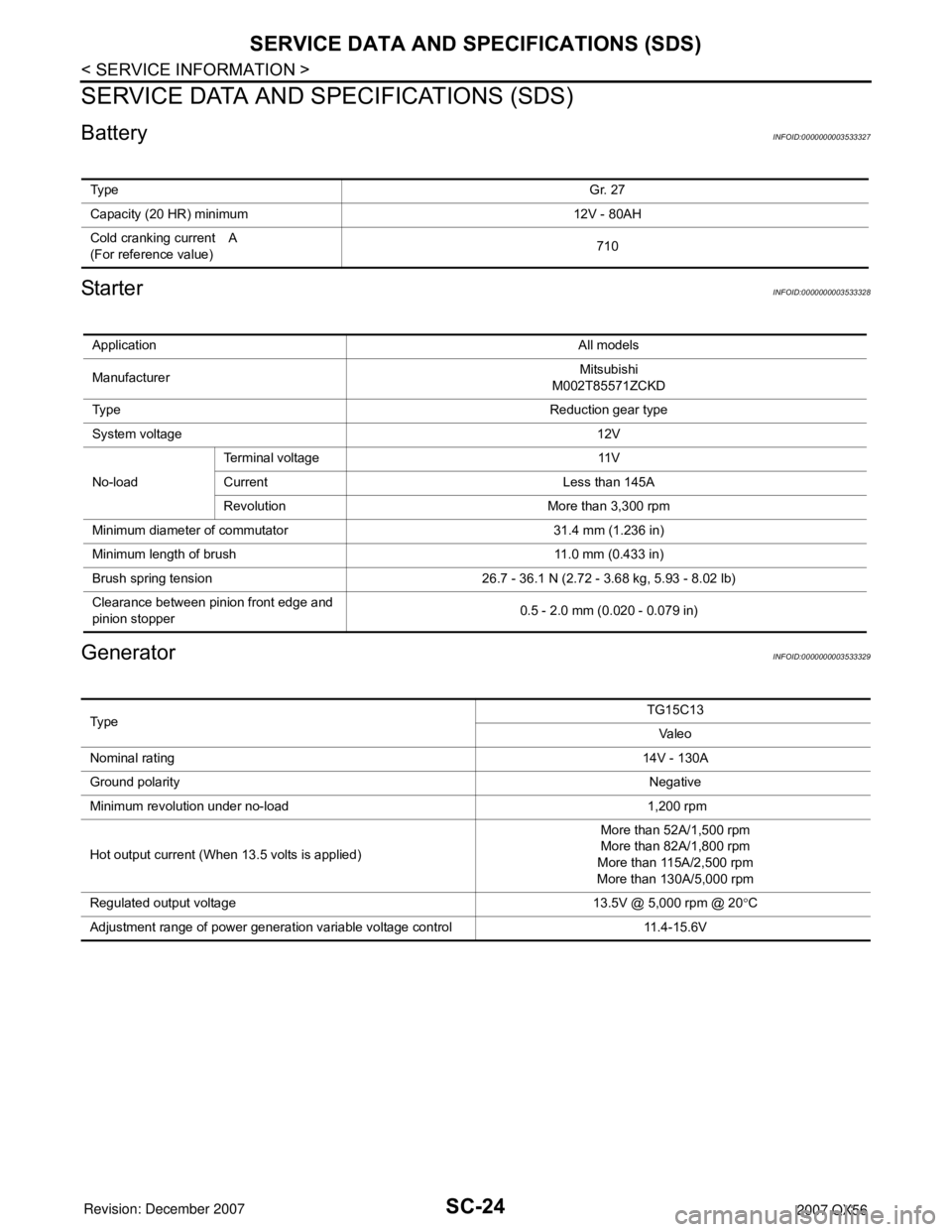
SC-24
< SERVICE INFORMATION >
SERVICE DATA AND SPECIFICATIONS (SDS)
SERVICE DATA AND SPECIFICATIONS (SDS)
BatteryINFOID:0000000003533327
StarterINFOID:0000000003533328
GeneratorINFOID:0000000003533329
Ty p eGr. 27
Capacity (20 HR) minimum 12V - 80AH
Cold cranking current A
(For reference value)710
ApplicationAll models
ManufacturerMitsubishi
M002T85571ZCKD
Ty p eReduction gear type
System voltage 12V
No-loadTerminal voltage 11V
Current Less than 145A
Revolution More than 3,300 rpm
Minimum diameter of commutator 31.4 mm (1.236 in)
Minimum length of brush 11.0 mm (0.433 in)
Brush spring tension 26.7 - 36.1 N (2.72 - 3.68 kg, 5.93 - 8.02 lb)
Clearance between pinion front edge and
pinion stopper0.5 - 2.0 mm (0.020 - 0.079 in)
Ty p eTG15C13
Va l e o
Nominal rating14V - 130A
Ground polarityNegative
Minimum revolution under no-load 1,200 rpm
Hot output current (When 13.5 volts is applied)More than 52A/1,500 rpm
More than 82A/1,800 rpm
More than 115A/2,500 rpm
More than 130A/5,000 rpm
Regulated output voltage 13.5V @ 5,000 rpm @ 20°C
Adjustment range of power generation variable voltage control 11.4-15.6V