Page 1009 of 3061
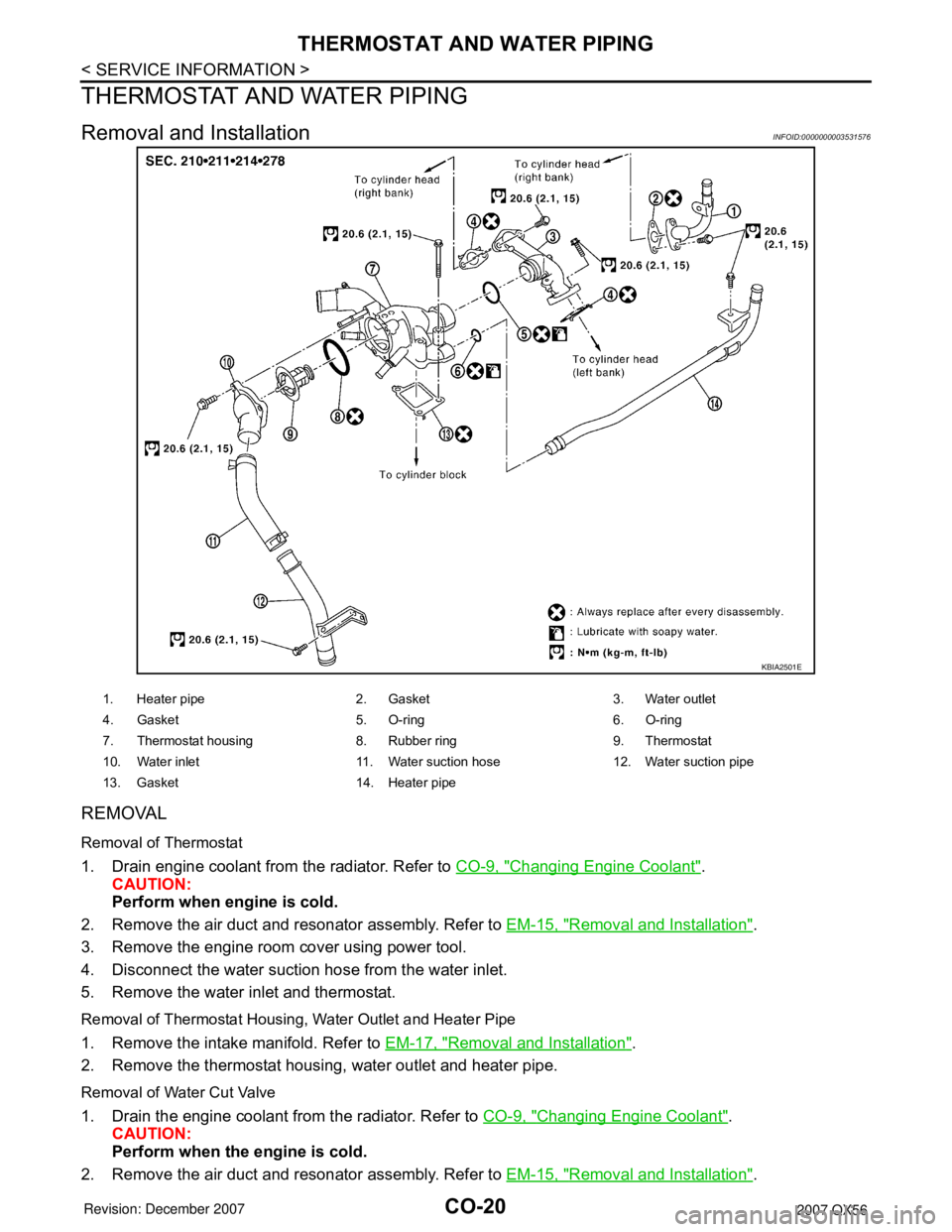
CO-20
< SERVICE INFORMATION >
THERMOSTAT AND WATER PIPING
THERMOSTAT AND WATER PIPING
Removal and InstallationINFOID:0000000003531576
REMOVAL
Removal of Thermostat
1. Drain engine coolant from the radiator. Refer to CO-9, "Changing Engine Coolant".
CAUTION:
Perform when engine is cold.
2. Remove the air duct and resonator assembly. Refer to EM-15, "
Removal and Installation".
3. Remove the engine room cover using power tool.
4. Disconnect the water suction hose from the water inlet.
5. Remove the water inlet and thermostat.
Removal of Thermostat Housing, Water Outlet and Heater Pipe
1. Remove the intake manifold. Refer to EM-17, "Removal and Installation".
2. Remove the thermostat housing, water outlet and heater pipe.
Removal of Water Cut Valve
1. Drain the engine coolant from the radiator. Refer to CO-9, "Changing Engine Coolant".
CAUTION:
Perform when the engine is cold.
2. Remove the air duct and resonator assembly. Refer to EM-15, "
Removal and Installation".
KBIA2501E
1. Heater pipe 2. Gasket 3. Water outlet
4. Gasket 5. O-ring 6. O-ring
7. Thermostat housing 8. Rubber ring 9. Thermostat
10. Water inlet 11. Water suction hose 12. Water suction pipe
13. Gasket 14. Heater pipe
Page 1010 of 3061
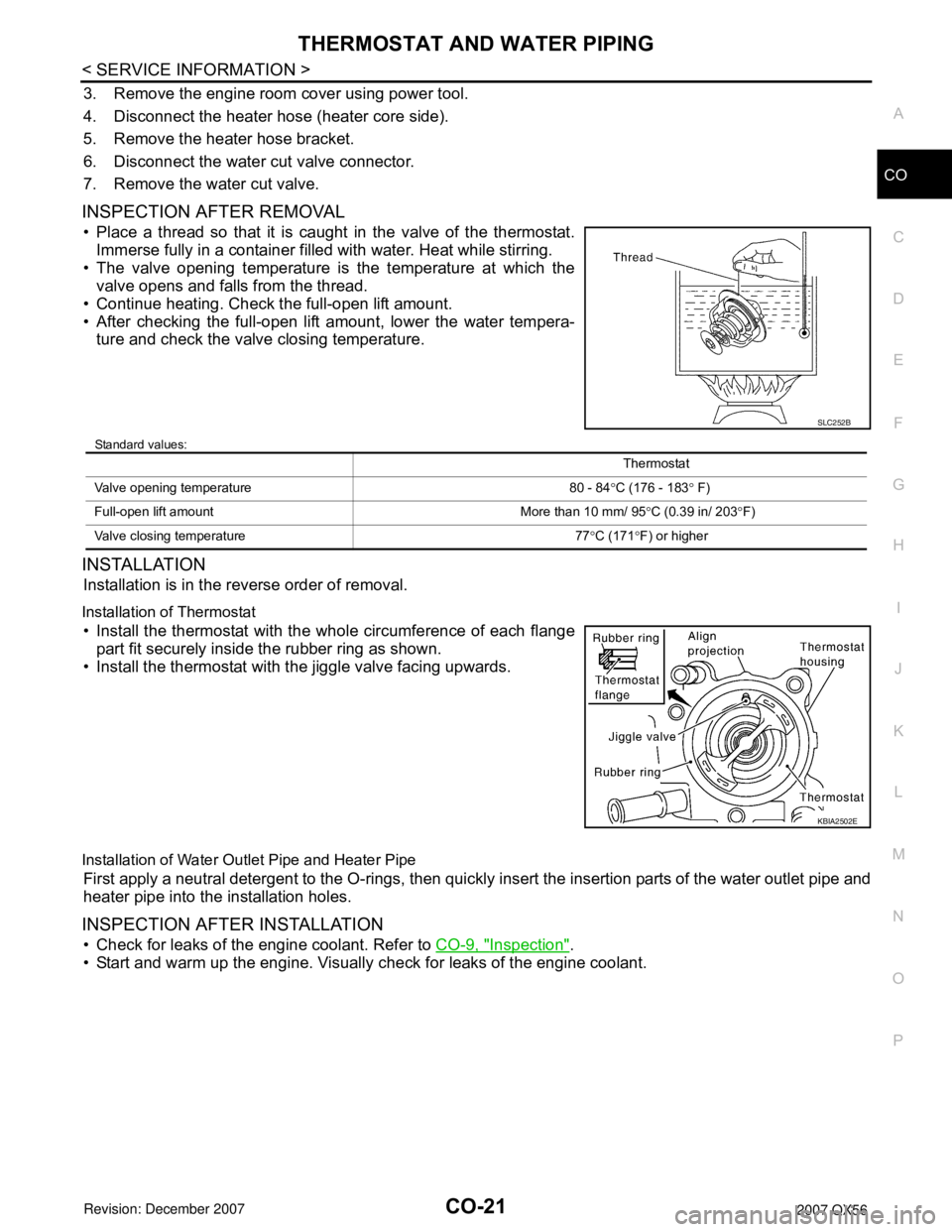
THERMOSTAT AND WATER PIPING
CO-21
< SERVICE INFORMATION >
C
D
E
F
G
H
I
J
K
L
MA
CO
N
P O
3. Remove the engine room cover using power tool.
4. Disconnect the heater hose (heater core side).
5. Remove the heater hose bracket.
6. Disconnect the water cut valve connector.
7. Remove the water cut valve.
INSPECTION AFTER REMOVAL
• Place a thread so that it is caught in the valve of the thermostat.
Immerse fully in a container filled with water. Heat while stirring.
• The valve opening temperature is the temperature at which the
valve opens and falls from the thread.
• Continue heating. Check the full-open lift amount.
• After checking the full-open lift amount, lower the water tempera-
ture and check the valve closing temperature.
Standard values:
INSTALLATION
Installation is in the reverse order of removal.
Installation of Thermostat
• Install the thermostat with the whole circumference of each flange
part fit securely inside the rubber ring as shown.
• Install the thermostat with the jiggle valve facing upwards.
Installation of Water Outlet Pipe and Heater Pipe
First apply a neutral detergent to the O-rings, then quickly insert the insertion parts of the water outlet pipe and
heater pipe into the installation holes.
INSPECTION AFTER INSTALLATION
• Check for leaks of the engine coolant. Refer to CO-9, "Inspection".
• Start and warm up the engine. Visually check for leaks of the engine coolant.
SLC252B
Thermostat
Valve opening temperature 80 - 84°C (176 - 183° F)
Full-open lift amount More than 10 mm/ 95°C (0.39 in/ 203°F)
Valve closing temperature 77°C (171°F) or higher
KBIA2502E
Page 1011 of 3061
CO-22
< SERVICE INFORMATION >
SERVICE DATA AND SPECIFICATIONS (SDS)
SERVICE DATA AND SPECIFICATIONS (SDS)
Standard and LimitINFOID:0000000003531577
ENGINE COOLANT CAPACITY (APPROXIMATE)
Unit: (US gal, Imp gal)
THERMOSTAT
RADIATOR
Unit: kPa (kg/cm2, psi)
Engine coolant capacity with reservoir tank ("MAX" level) 14.4 (3 3/4, 3 1/8)
Valve opening temperature 80 - 84°C (176 - 183°F)
Maximum valve lift More than 10 mm/95°C (0.39 in/203°F)
Valve closing temperature 77°C (171°F) or higher
Reservoir cap relief pressure Standard 95 - 125 (0.97- 1.28, 14 - 18)
Leakage test pressure 137 (1.4, 20)
Page 1012 of 3061
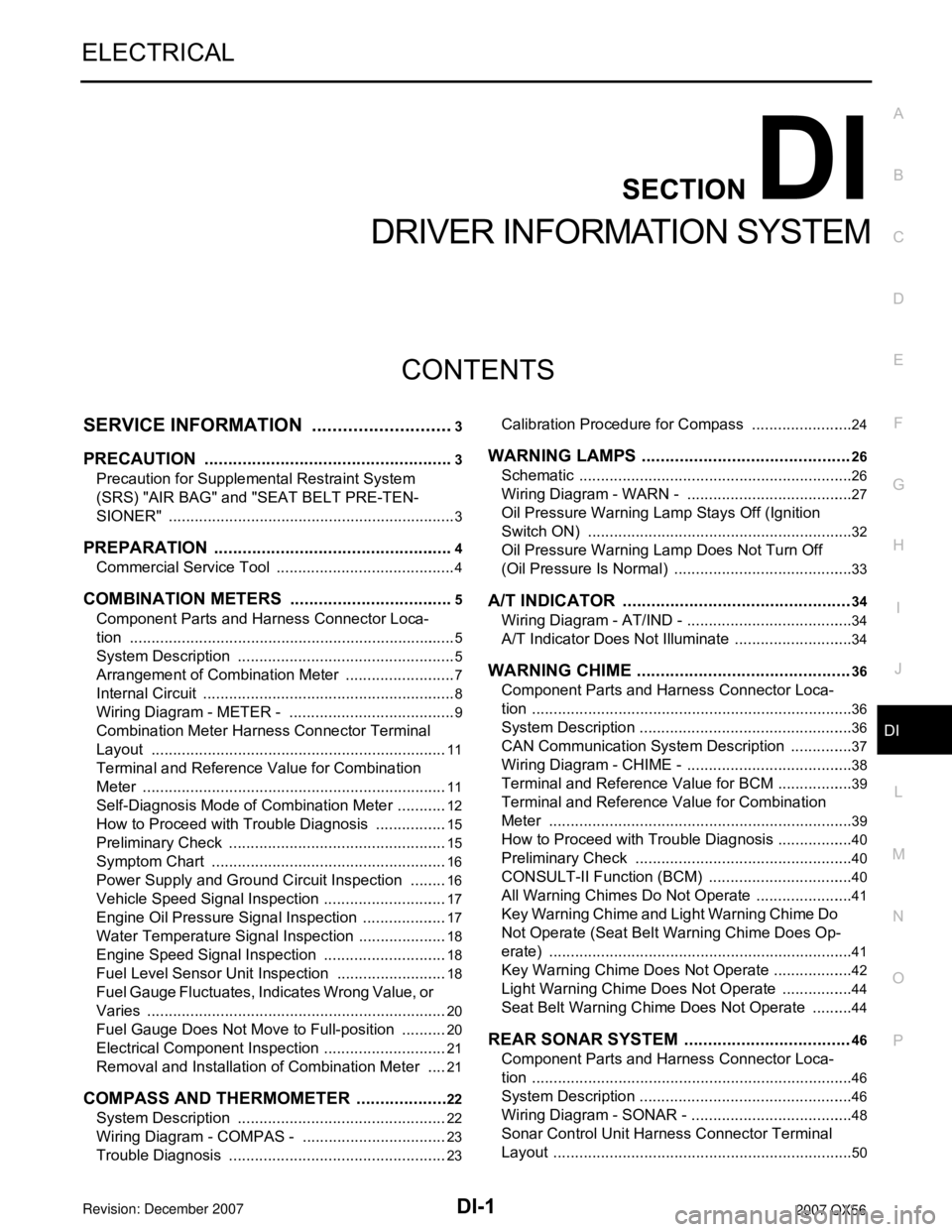
DI-1
ELECTRICAL
C
DE
F
G H
I
J
L
M
SECTION DI
A
B
DI
N
O P
CONTENTS
DRIVER INFORMATION SYSTEM
SERVICE INFORMATION .. ..........................3
PRECAUTION ................................................ .....3
Precaution for Supplemental Restraint System
(SRS) "AIR BAG" and "SEAT BELT PRE-TEN-
SIONER" ............................................................. ......
3
PREPARATION ...................................................4
Commercial Service Tool .................................... ......4
COMBINATION METERS ...................................5
Component Parts and Harness Connector Loca-
tion ...................................................................... ......
5
System Description ...................................................5
Arrangement of Combination Meter ..........................7
Internal Circuit ...........................................................8
Wiring Diagram - METER - .......................................9
Combination Meter Harness Connector Terminal
Layout .....................................................................
11
Terminal and Reference Value for Combination
Meter .......................................................................
11
Self-Diagnosis Mode of Combination Meter ........ ....12
How to Proceed with Trouble Diagnosis ............. ....15
Preliminary Check ...................................................15
Symptom Chart .......................................................16
Power Supply and Ground Circuit Inspection .........16
Vehicle Speed Signal Inspection .............................17
Engine Oil Pressure Signal Inspection ....................17
Water Temperature Signal Inspection .....................18
Engine Speed Signal Inspection ......................... ....18
Fuel Level Sensor Unit Inspection ...................... ....18
Fuel Gauge Fluctuates, Indicates Wrong Value, or
Varies .................................................................. ....
20
Fuel Gauge Does Not Move to Full-position ...........20
Electrical Component Inspection ......................... ....21
Removal and Installation of Combination Meter .....21
COMPASS AND THERMOMETER ................ ....22
System Description ............................................. ....22
Wiring Diagram - COMPAS - ..................................23
Trouble Diagnosis ............................................... ....23
Calibration Procedure for Compass .................... ....24
WARNING LAMPS ............................................26
Schematic ............................................................ ....26
Wiring Diagram - WARN - .......................................27
Oil Pressure Warning Lamp Stays Off (Ignition
Switch ON) .......................................................... ....
32
Oil Pressure Warning Lamp Does Not Turn Off
(Oil Pressure Is Normal) ...................................... ....
33
A/T INDICATOR ................................................34
Wiring Diagram - AT/IND - .......................................34
A/T Indicator Does Not Illuminate ............................34
WARNING CHIME .............................................36
Component Parts and Harness Connector Loca-
tion ....................................................................... ....
36
System Description ..................................................36
CAN Communication System Description ...............37
Wiring Diagram - CHIME - .......................................38
Terminal and Reference Value for BCM ..................39
Terminal and Reference Value for Combination
Meter ................................................................... ....
39
How to Proceed with Trouble Diagnosis ..................40
Preliminary Check ............................................... ....40
CONSULT-II Function (BCM) ..................................40
All Warning Chimes Do Not Operate .......................41
Key Warning Chime and Light Warning Chime Do
Not Operate (Seat Belt Warning Chime Does Op-
erate) .......................................................................
41
Key Warning Chime Does Not Operate ...................42
Light Warning Chime Does Not Operate .................44
Seat Belt Warning Chime Does Not Operate ..........44
REAR SONAR SYSTEM ...................................46
Component Parts and Harness Connector Loca-
tion ....................................................................... ....
46
System Description ..................................................46
Wiring Diagram - SONAR - ......................................48
Sonar Control Unit Harness Connector Terminal
Layout ......................................................................
50
Page 1013 of 3061
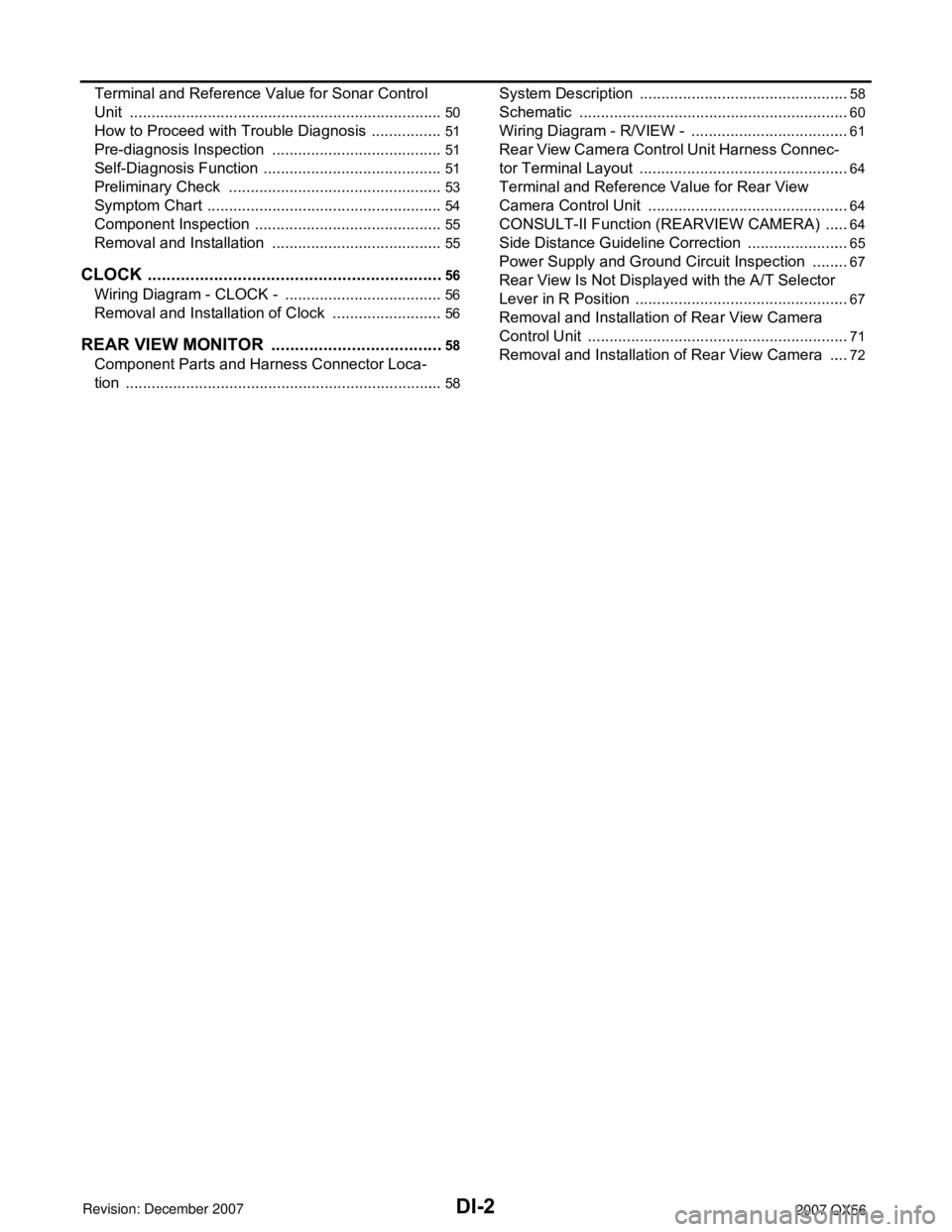
DI-2
Terminal and Reference Value for Sonar Control
Unit .........................................................................
50
How to Proceed with Trouble Diagnosis .................51
Pre-diagnosis Inspection ........................................51
Self-Diagnosis Function ..........................................51
Preliminary Check ..................................................53
Symptom Chart .......................................................54
Component Inspection ............................................55
Removal and Installation ........................................55
CLOCK ...............................................................56
Wiring Diagram - CLOCK - .................................. ...56
Removal and Installation of Clock ..........................56
REAR VIEW MONITOR .....................................58
Component Parts and Harness Connector Loca-
tion ....................................................................... ...
58
System Description .............................................. ...58
Schematic ...............................................................60
Wiring Diagram - R/VIEW - .....................................61
Rear View Camera Control Unit Harness Connec-
tor Terminal Layout .............................................. ...
64
Terminal and Reference Value for Rear View
Camera Control Unit ...............................................
64
CONSULT-II Function (REARVIEW CAMERA) ......64
Side Distance Guideline Correction ........................65
Power Supply and Ground Circuit Inspection .........67
Rear View Is Not Displayed with the A/T Selector
Lever in R Position ..................................................
67
Removal and Installation of Rear View Camera
Control Unit .......................................................... ...
71
Removal and Installation of Rear View Camera .....72
Page 1014 of 3061
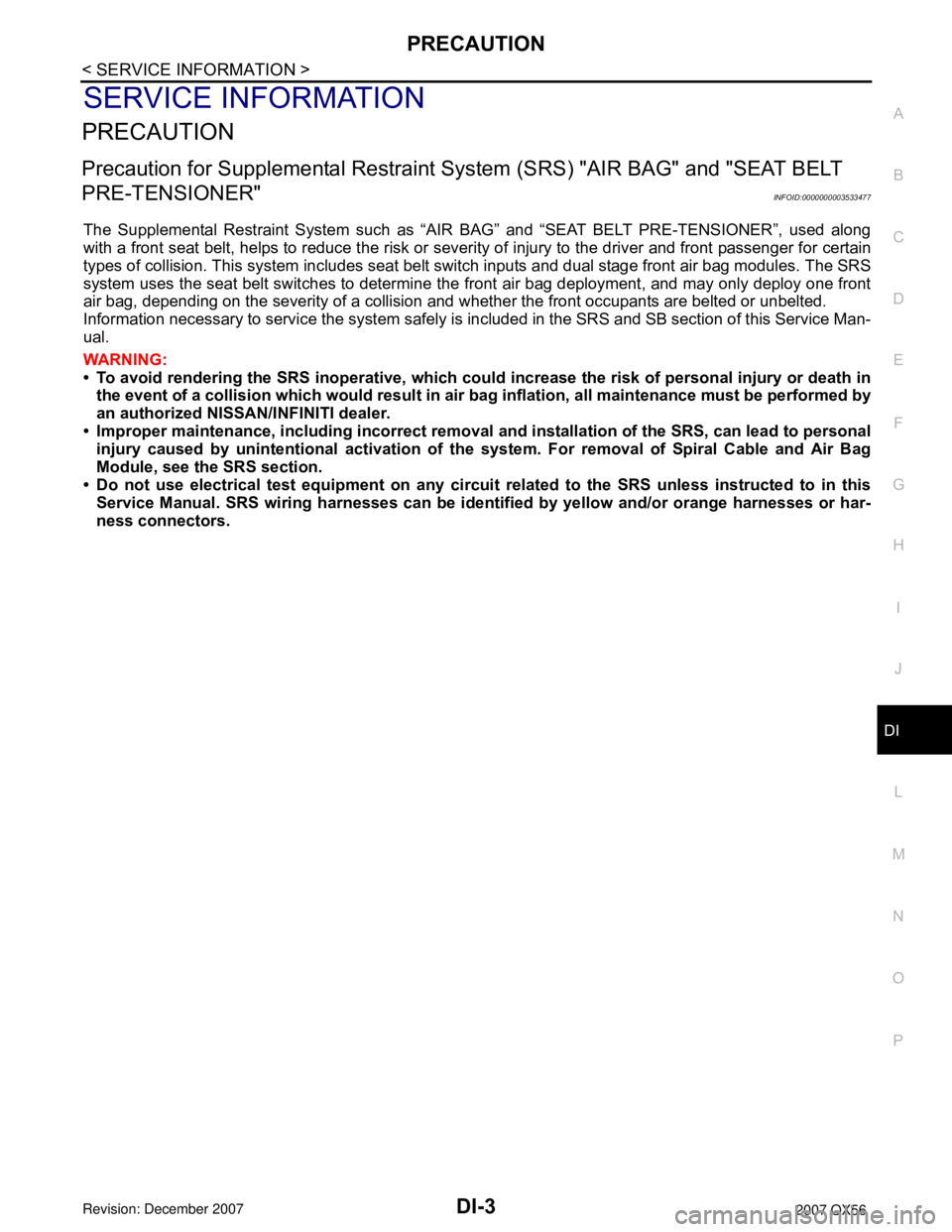
PRECAUTIONDI-3
< SERVICE INFORMATION >
C
DE
F
G H
I
J
L
M A
B
DI
N
O P
SERVICE INFORMATION
PRECAUTION
Precaution for Supplemental Restraint System (SRS) "AIR BAG" and "SEAT BELT
PRE-TENSIONER"
INFOID:0000000003533477
The Supplemental Restraint System such as “A IR BAG” and “SEAT BELT PRE-TENSIONER”, used along
with a front seat belt, helps to reduce the risk or severi ty of injury to the driver and front passenger for certain
types of collision. This system includes seat belt switch inputs and dual stage front air bag modules. The SRS
system uses the seat belt switches to determine the front air bag deployment, and may only deploy one front
air bag, depending on the severity of a collision and w hether the front occupants are belted or unbelted.
Information necessary to service the system safely is included in the SRS and SB section of this Service Man-
ual.
WARNING:
• To avoid rendering the SRS inoper ative, which could increase the risk of personal injury or death in
the event of a collision which would result in air bag inflation, all maintenance must be performed by
an authorized NISSAN/INFINITI dealer.
• Improper maintenance, including in correct removal and installation of the SRS, can lead to personal
injury caused by unintentional act ivation of the system. For removal of Spiral Cable and Air Bag
Module, see the SRS section.
• Do not use electrical test equipm ent on any circuit related to the SRS unless instructed to in this
Service Manual. SRS wiring harnesses can be identi fied by yellow and/or orange harnesses or har-
ness connectors.
Page 1015 of 3061
DI-4
< SERVICE INFORMATION >
PREPARATION
PREPARATION
Commercial Service ToolINFOID:0000000003533478
Tool nameDescription
Power tool Loosening bolts and nuts.
PBIC0191E
Page 1016 of 3061
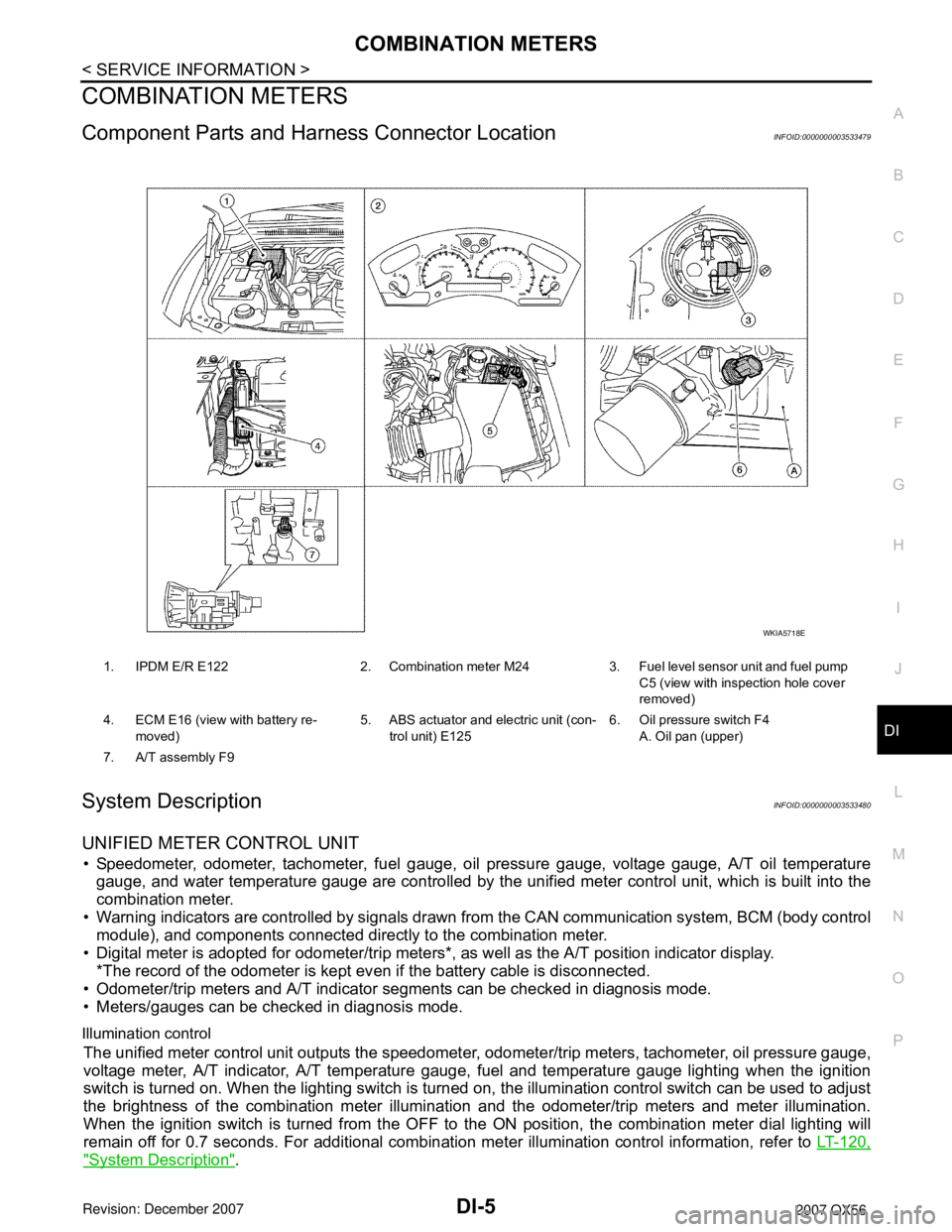
COMBINATION METERSDI-5
< SERVICE INFORMATION >
C
DE
F
G H
I
J
L
M A
B
DI
N
O P
COMBINATION METERS
Component Parts and Har ness Connector LocationINFOID:0000000003533479
System DescriptionINFOID:0000000003533480
UNIFIED METER CONTROL UNIT
• Speedometer, odometer, tachometer, fuel gauge, oil pressure gauge, voltage gauge, A/T oil temperature
gauge, and water temperature gauge are controlled by the unified meter control unit, which is built into the
combination meter.
• Warning indicators are controlled by signals drawn fr om the CAN communication system, BCM (body control
module), and components connected directly to the combination meter.
• Digital meter is adopted for odometer/trip meters*, as well as the A/T position indicator display. *The record of the odometer is kept ev en if the battery cable is disconnected.
• Odometer/trip meters and A/T indicator segments can be checked in diagnosis mode.
• Meters/gauges can be checked in diagnosis mode.
Illumination control
The unified meter control unit outputs the speedometer, odometer/trip meters, tachometer, oil pressure gauge,
voltage meter, A/T indicator, A/T temperature gauge, fuel and temperature gauge lighting when the ignition
switch is turned on. When the lighting switch is turned on, the illumination control switch can be used to adjust
the brightness of the combination meter illuminati on and the odometer/trip meters and meter illumination.
When the ignition switch is turned from the OFF to the ON position, the combination meter dial lighting will
remain off for 0.7 seconds. For additional combination meter illumination control information, refer to LT-120,
"System Description".
1. IPDM E/R E122 2. Combination meter M24 3. Fuel level sensor unit and fuel pump
C5 (view with inspection hole cover
removed)
4. ECM E16 (view with battery re- moved) 5. ABS actuator and electric unit (con-
trol unit) E125 6. Oil pressure switch F4
A. Oil pan (upper)
7. A/T assembly F9
WKIA5718E