Page 1265 of 3061
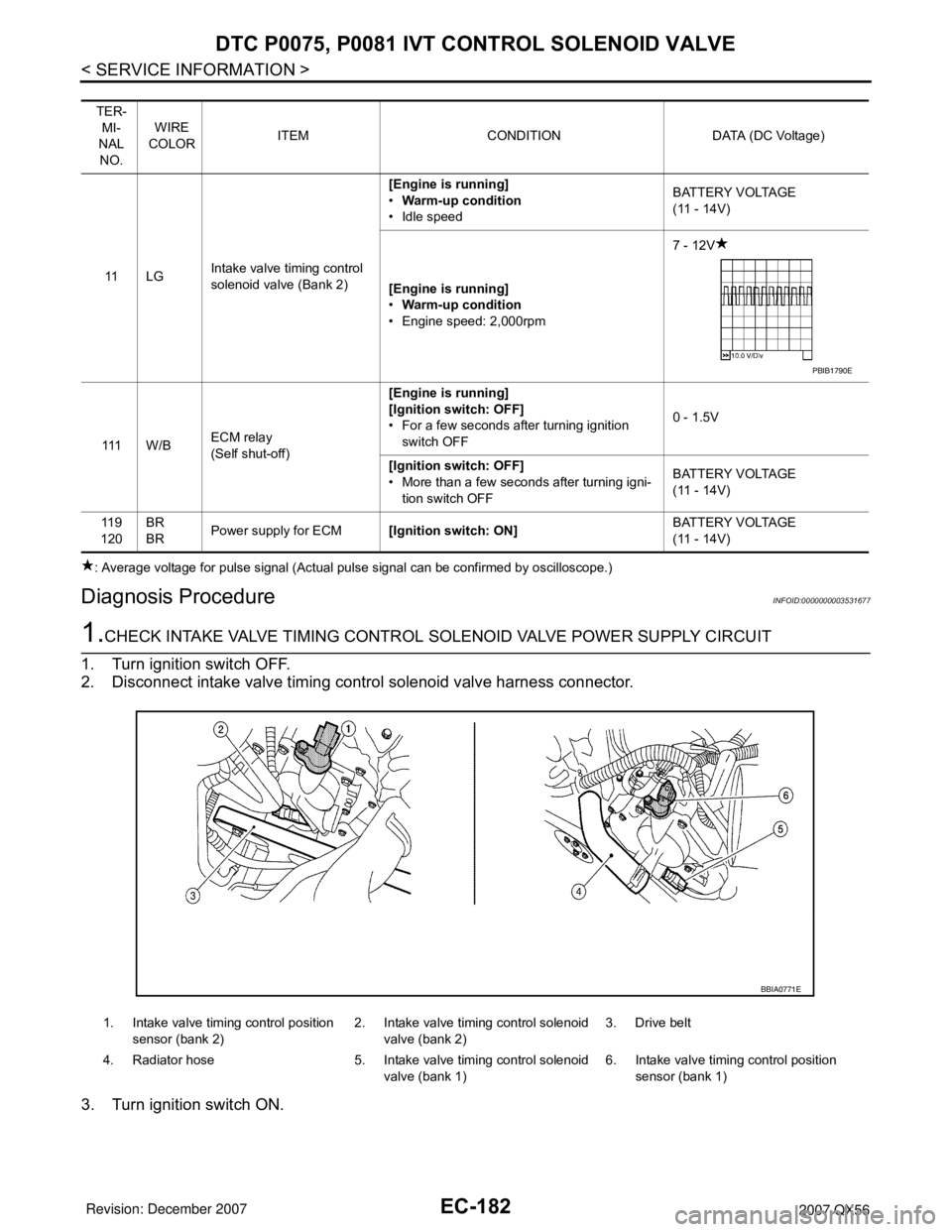
EC-182
< SERVICE INFORMATION >
DTC P0075, P0081 IVT CONTROL SOLENOID VALVE
: Average voltage for pulse signal (Actual pulse signal can be confirmed by oscilloscope.)
Diagnosis ProcedureINFOID:0000000003531677
1.CHECK INTAKE VALVE TIMING CONTROL SOLENOID VALVE POWER SUPPLY CIRCUIT
1. Turn ignition switch OFF.
2. Disconnect intake valve timing control solenoid valve harness connector.
3. Turn ignition switch ON.
TER-
MI-
NAL
NO.WIRE
COLORITEM CONDITION DATA (DC Voltage)
11 L GIntake valve timing control
solenoid valve (Bank 2)[Engine is running]
•Warm-up condition
• Idle speedBATTERY VOLTAGE
(11 - 14V)
[Engine is running]
•Warm-up condition
• Engine speed: 2,000rpm7 - 12V
111 W / BECM relay
(Self shut-off)[Engine is running]
[Ignition switch: OFF]
• For a few seconds after turning ignition
switch OFF0 - 1.5V
[Ignition switch: OFF]
• More than a few seconds after turning igni-
tion switch OFFBATTERY VOLTAGE
(11 - 14V)
11 9
120BR
BRPower supply for ECM[Ignition switch: ON]BATTERY VOLTAGE
(11 - 14V)
PBIB1790E
1. Intake valve timing control position
sensor (bank 2)2. Intake valve timing control solenoid
valve (bank 2)3. Drive belt
4. Radiator hose 5. Intake valve timing control solenoid
valve (bank 1)6. Intake valve timing control position
sensor (bank 1)
BBIA0771E
Page 1266 of 3061
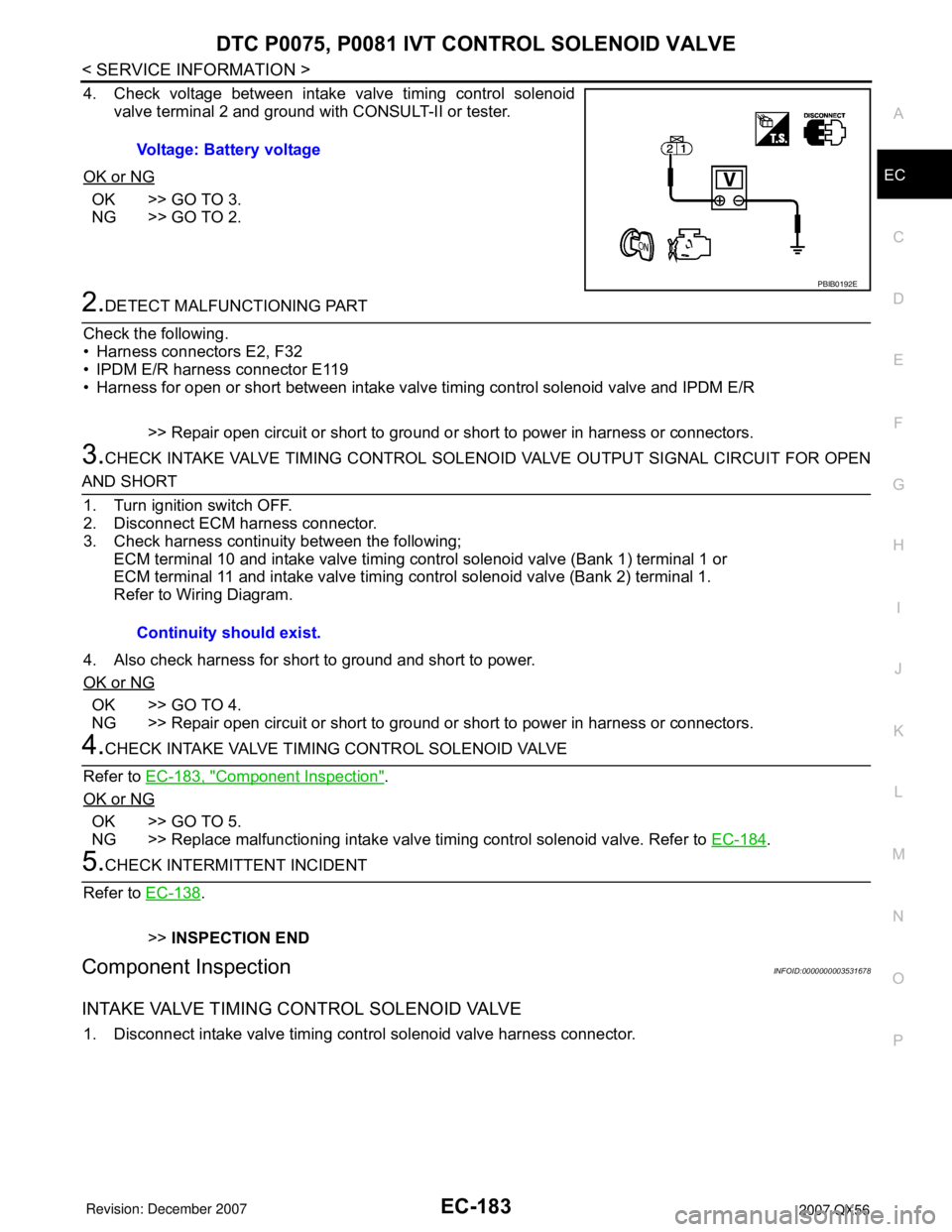
DTC P0075, P0081 IVT CONTROL SOLENOID VALVE
EC-183
< SERVICE INFORMATION >
C
D
E
F
G
H
I
J
K
L
MA
EC
N
P O
4. Check voltage between intake valve timing control solenoid
valve terminal 2 and ground with CONSULT-II or tester.
OK or NG
OK >> GO TO 3.
NG >> GO TO 2.
2.DETECT MALFUNCTIONING PART
Check the following.
• Harness connectors E2, F32
• IPDM E/R harness connector E119
• Harness for open or short between intake valve timing control solenoid valve and IPDM E/R
>> Repair open circuit or short to ground or short to power in harness or connectors.
3.CHECK INTAKE VALVE TIMING CONTROL SOLENOID VALVE OUTPUT SIGNAL CIRCUIT FOR OPEN
AND SHORT
1. Turn ignition switch OFF.
2. Disconnect ECM harness connector.
3. Check harness continuity between the following;
ECM terminal 10 and intake valve timing control solenoid valve (Bank 1) terminal 1 or
ECM terminal 11 and intake valve timing control solenoid valve (Bank 2) terminal 1.
Refer to Wiring Diagram.
4. Also check harness for short to ground and short to power.
OK or NG
OK >> GO TO 4.
NG >> Repair open circuit or short to ground or short to power in harness or connectors.
4.CHECK INTAKE VALVE TIMING CONTROL SOLENOID VALVE
Refer to EC-183, "
Component Inspection".
OK or NG
OK >> GO TO 5.
NG >> Replace malfunctioning intake valve timing control solenoid valve. Refer to EC-184
.
5.CHECK INTERMITTENT INCIDENT
Refer to EC-138
.
>>INSPECTION END
Component InspectionINFOID:0000000003531678
INTAKE VALVE TIMING CONTROL SOLENOID VALVE
1. Disconnect intake valve timing control solenoid valve harness connector.Voltage: Battery voltage
PBIB0192E
Continuity should exist.
Page 1267 of 3061
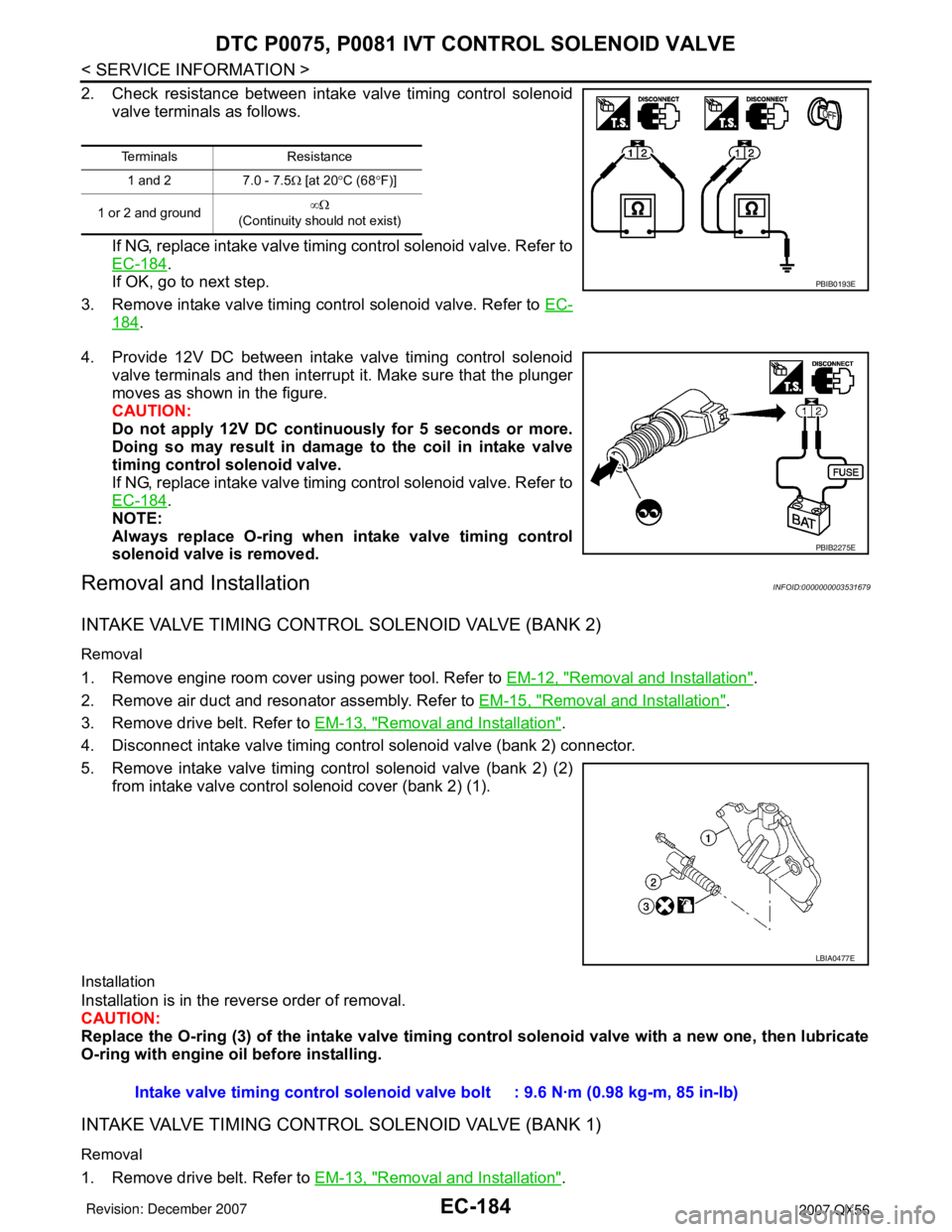
EC-184
< SERVICE INFORMATION >
DTC P0075, P0081 IVT CONTROL SOLENOID VALVE
2. Check resistance between intake valve timing control solenoid
valve terminals as follows.
If NG, replace intake valve timing control solenoid valve. Refer to
EC-184
.
If OK, go to next step.
3. Remove intake valve timing control solenoid valve. Refer to EC-
184.
4. Provide 12V DC between intake valve timing control solenoid
valve terminals and then interrupt it. Make sure that the plunger
moves as shown in the figure.
CAUTION:
Do not apply 12V DC continuously for 5 seconds or more.
Doing so may result in damage to the coil in intake valve
timing control solenoid valve.
If NG, replace intake valve timing control solenoid valve. Refer to
EC-184
.
NOTE:
Always replace O-ring when intake valve timing control
solenoid valve is removed.
Removal and InstallationINFOID:0000000003531679
INTAKE VALVE TIMING CONTROL SOLENOID VALVE (BANK 2)
Removal
1. Remove engine room cover using power tool. Refer to EM-12, "Removal and Installation".
2. Remove air duct and resonator assembly. Refer to EM-15, "
Removal and Installation".
3. Remove drive belt. Refer to EM-13, "
Removal and Installation".
4. Disconnect intake valve timing control solenoid valve (bank 2) connector.
5. Remove intake valve timing control solenoid valve (bank 2) (2)
from intake valve control solenoid cover (bank 2) (1).
Installation
Installation is in the reverse order of removal.
CAUTION:
Replace the O-ring (3) of the intake valve timing control solenoid valve with a new one, then lubricate
O-ring with engine oil before installing.
INTAKE VALVE TIMING CONTROL SOLENOID VALVE (BANK 1)
Removal
1. Remove drive belt. Refer to EM-13, "Removal and Installation".
Terminals Resistance
1 and 2 7.0 - 7.5Ω [at 20°C (68°F)]
1 or 2 and ground∞Ω
(Continuity should not exist)
PBIB0193E
PBIB2275E
LBIA0477E
Intake valve timing control solenoid valve bolt : 9.6 N·m (0.98 kg-m, 85 in-lb)
Page 1268 of 3061
DTC P0075, P0081 IVT CONTROL SOLENOID VALVE
EC-185
< SERVICE INFORMATION >
C
D
E
F
G
H
I
J
K
L
MA
EC
N
P O
2. Disconnect intake valve timing control solenoid valve (bank 1) connector.
3. Remove intake valve timing control solenoid valve (bank 1) (3)
from intake valve control solenoid cover (bank 1) (1).
Installation
Installation is in the reverse order of removal.
CAUTION:
Replace the O-ring (2) of the intake valve timing control solenoid valve with a new one, then lubricate
O-ring with engine oil before installing.
LBIA0478E
Intake valve timing control solenoid valve bolt : 9.6 N·m (0.98 kg-m, 85 in-lb)
Page 1269 of 3061
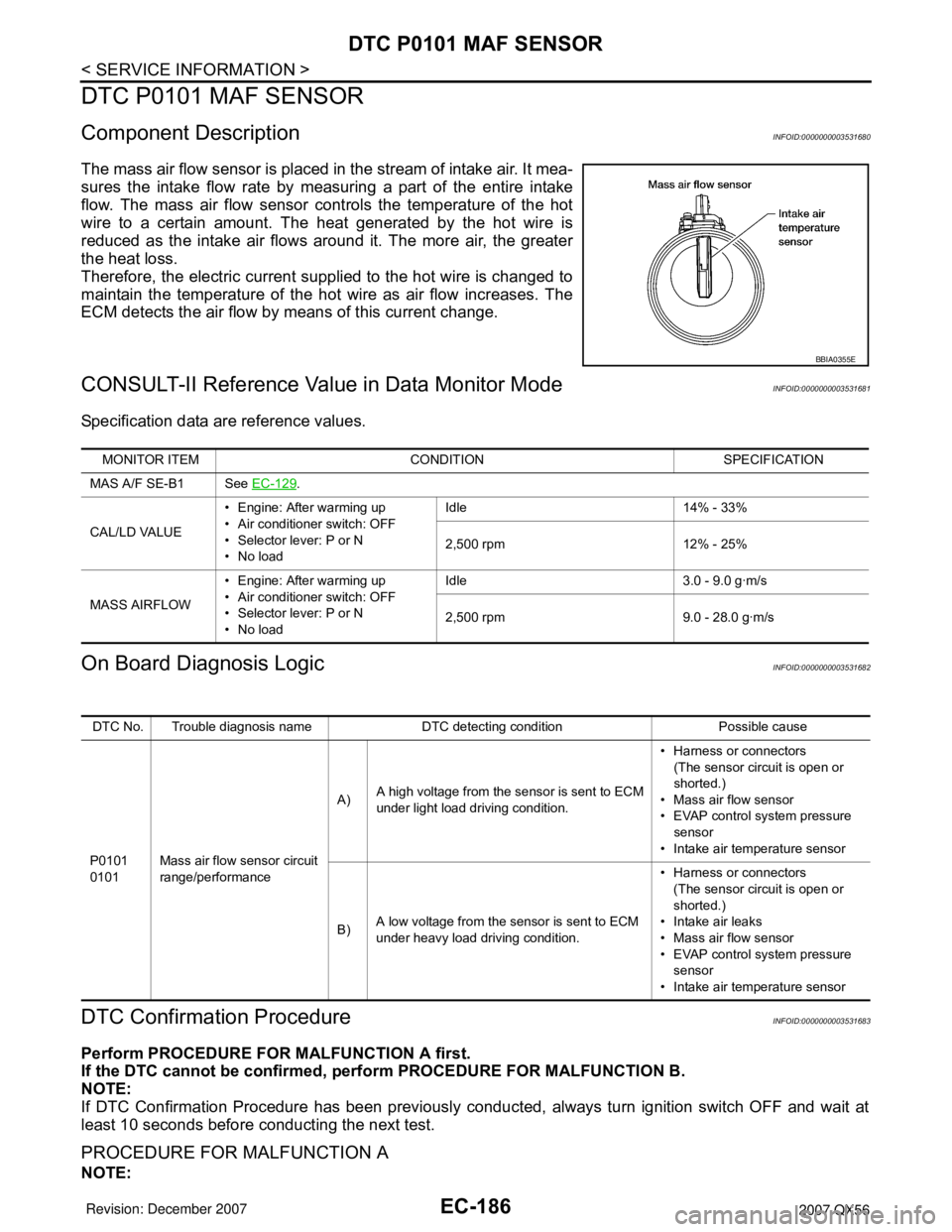
EC-186
< SERVICE INFORMATION >
DTC P0101 MAF SENSOR
DTC P0101 MAF SENSOR
Component DescriptionINFOID:0000000003531680
The mass air flow sensor is placed in the stream of intake air. It mea-
sures the intake flow rate by measuring a part of the entire intake
flow. The mass air flow sensor controls the temperature of the hot
wire to a certain amount. The heat generated by the hot wire is
reduced as the intake air flows around it. The more air, the greater
the heat loss.
Therefore, the electric current supplied to the hot wire is changed to
maintain the temperature of the hot wire as air flow increases. The
ECM detects the air flow by means of this current change.
CONSULT-II Reference Value in Data Monitor ModeINFOID:0000000003531681
Specification data are reference values.
On Board Diagnosis LogicINFOID:0000000003531682
DTC Confirmation ProcedureINFOID:0000000003531683
Perform PROCEDURE FOR MALFUNCTION A first.
If the DTC cannot be confirmed, perform PROCEDURE FOR MALFUNCTION B.
NOTE:
If DTC Confirmation Procedure has been previously conducted, always turn ignition switch OFF and wait at
least 10 seconds before conducting the next test.
PROCEDURE FOR MALFUNCTION A
NOTE:
BBIA0355E
MONITOR ITEM CONDITION SPECIFICATION
MAS A/F SE-B1 See EC-129
.
CAL/LD VALUE• Engine: After warming up
• Air conditioner switch: OFF
• Selector lever: P or N
•No loadIdle 14% - 33%
2,500 rpm 12% - 25%
MASS AIRFLOW• Engine: After warming up
• Air conditioner switch: OFF
• Selector lever: P or N
•No loadIdle 3.0 - 9.0 g·m/s
2,500 rpm 9.0 - 28.0 g·m/s
DTC No. Trouble diagnosis name DTC detecting condition Possible cause
P0101
0101Mass air flow sensor circuit
range/performanceA)A high voltage from the sensor is sent to ECM
under light load driving condition.• Harness or connectors
(The sensor circuit is open or
shorted.)
• Mass air flow sensor
• EVAP control system pressure
sensor
• Intake air temperature sensor
B)A low voltage from the sensor is sent to ECM
under heavy load driving condition.• Harness or connectors
(The sensor circuit is open or
shorted.)
• Intake air leaks
• Mass air flow sensor
• EVAP control system pressure
sensor
• Intake air temperature sensor
Page 1270 of 3061
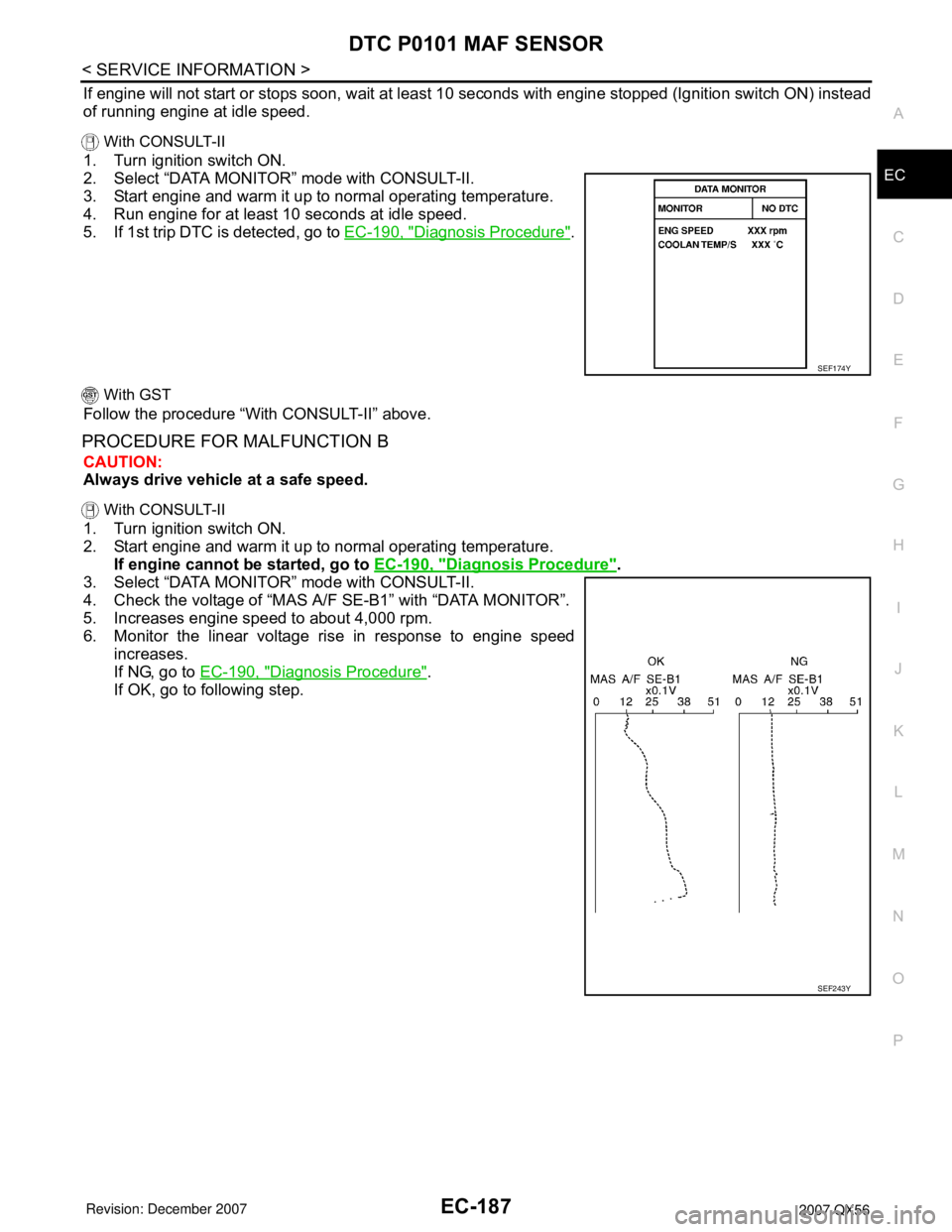
DTC P0101 MAF SENSOR
EC-187
< SERVICE INFORMATION >
C
D
E
F
G
H
I
J
K
L
MA
EC
N
P O
If engine will not start or stops soon, wait at least 10 seconds with engine stopped (Ignition switch ON) instead
of running engine at idle speed.
With CONSULT-II
1. Turn ignition switch ON.
2. Select “DATA MONITOR” mode with CONSULT-II.
3. Start engine and warm it up to normal operating temperature.
4. Run engine for at least 10 seconds at idle speed.
5. If 1st trip DTC is detected, go to EC-190, "
Diagnosis Procedure".
With GST
Follow the procedure “With CONSULT-II” above.
PROCEDURE FOR MALFUNCTION B
CAUTION:
Always drive vehicle at a safe speed.
With CONSULT-II
1. Turn ignition switch ON.
2. Start engine and warm it up to normal operating temperature.
If engine cannot be started, go to EC-190, "
Diagnosis Procedure".
3. Select “DATA MONITOR” mode with CONSULT-II.
4. Check the voltage of “MAS A/F SE-B1” with “DATA MONITOR”.
5. Increases engine speed to about 4,000 rpm.
6. Monitor the linear voltage rise in response to engine speed
increases.
If NG, go to EC-190, "
Diagnosis Procedure".
If OK, go to following step.
SEF174Y
SEF243Y
Page 1271 of 3061
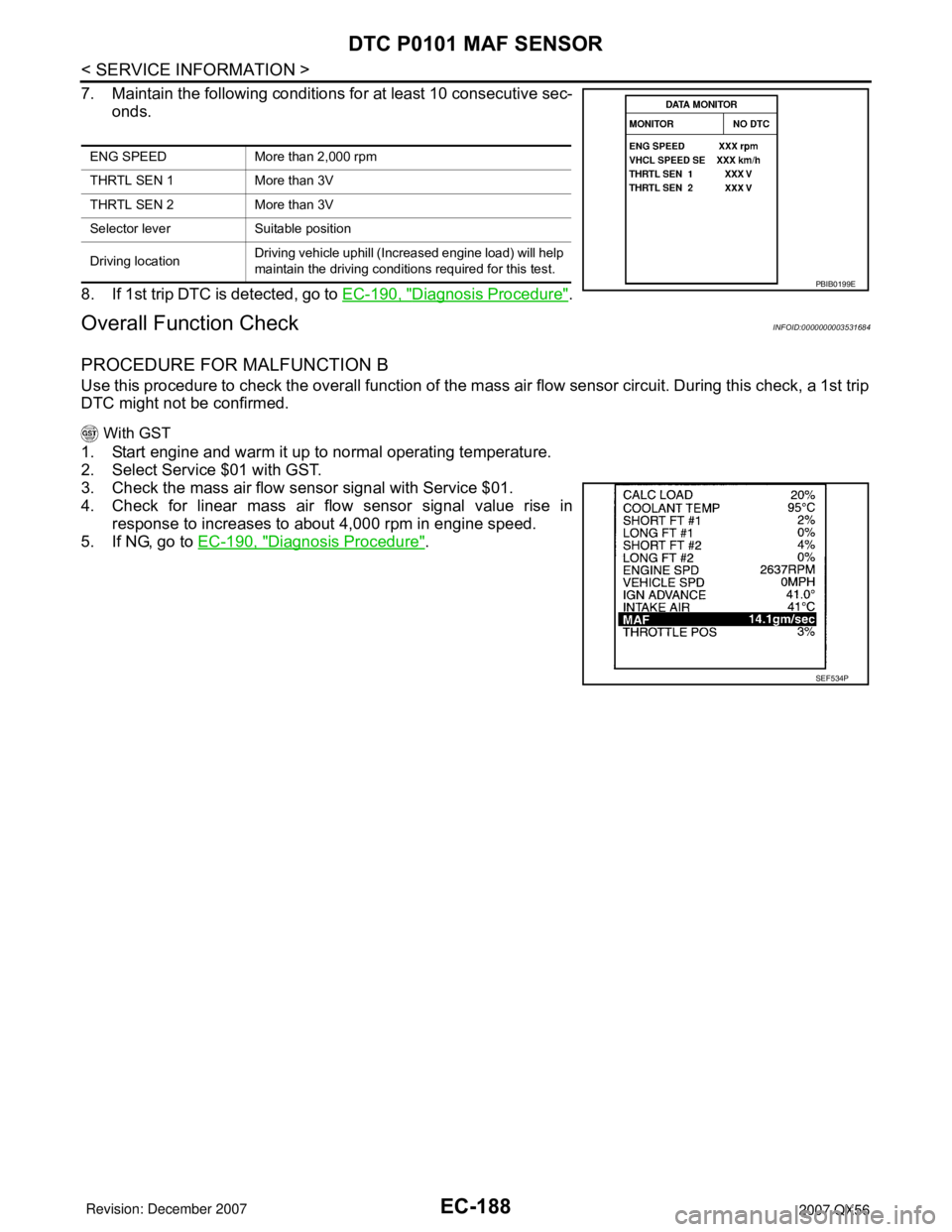
EC-188
< SERVICE INFORMATION >
DTC P0101 MAF SENSOR
7. Maintain the following conditions for at least 10 consecutive sec-
onds.
8. If 1st trip DTC is detected, go to EC-190, "
Diagnosis Procedure".
Overall Function CheckINFOID:0000000003531684
PROCEDURE FOR MALFUNCTION B
Use this procedure to check the overall function of the mass air flow sensor circuit. During this check, a 1st trip
DTC might not be confirmed.
With GST
1. Start engine and warm it up to normal operating temperature.
2. Select Service $01 with GST.
3. Check the mass air flow sensor signal with Service $01.
4. Check for linear mass air flow sensor signal value rise in
response to increases to about 4,000 rpm in engine speed.
5. If NG, go to EC-190, "
Diagnosis Procedure".
ENG SPEED More than 2,000 rpm
THRTL SEN 1 More than 3V
THRTL SEN 2 More than 3V
Selector lever Suitable position
Driving locationDriving vehicle uphill (Increased engine load) will help
maintain the driving conditions required for this test.
PBIB0199E
SEF534P
Page 1272 of 3061
DTC P0101 MAF SENSOR
EC-189
< SERVICE INFORMATION >
C
D
E
F
G
H
I
J
K
L
MA
EC
N
P O
Wiring DiagramINFOID:0000000003531685
Specification data are reference values and are measured between each terminal and ground.
CAUTION:
Do not use ECM ground terminals when measuring input/output voltage. Doing so may result in dam-
age to the ECM's transistor. Use a ground other than ECM terminals, such as the ground.
BBWA1674E