Page 1545 of 3061
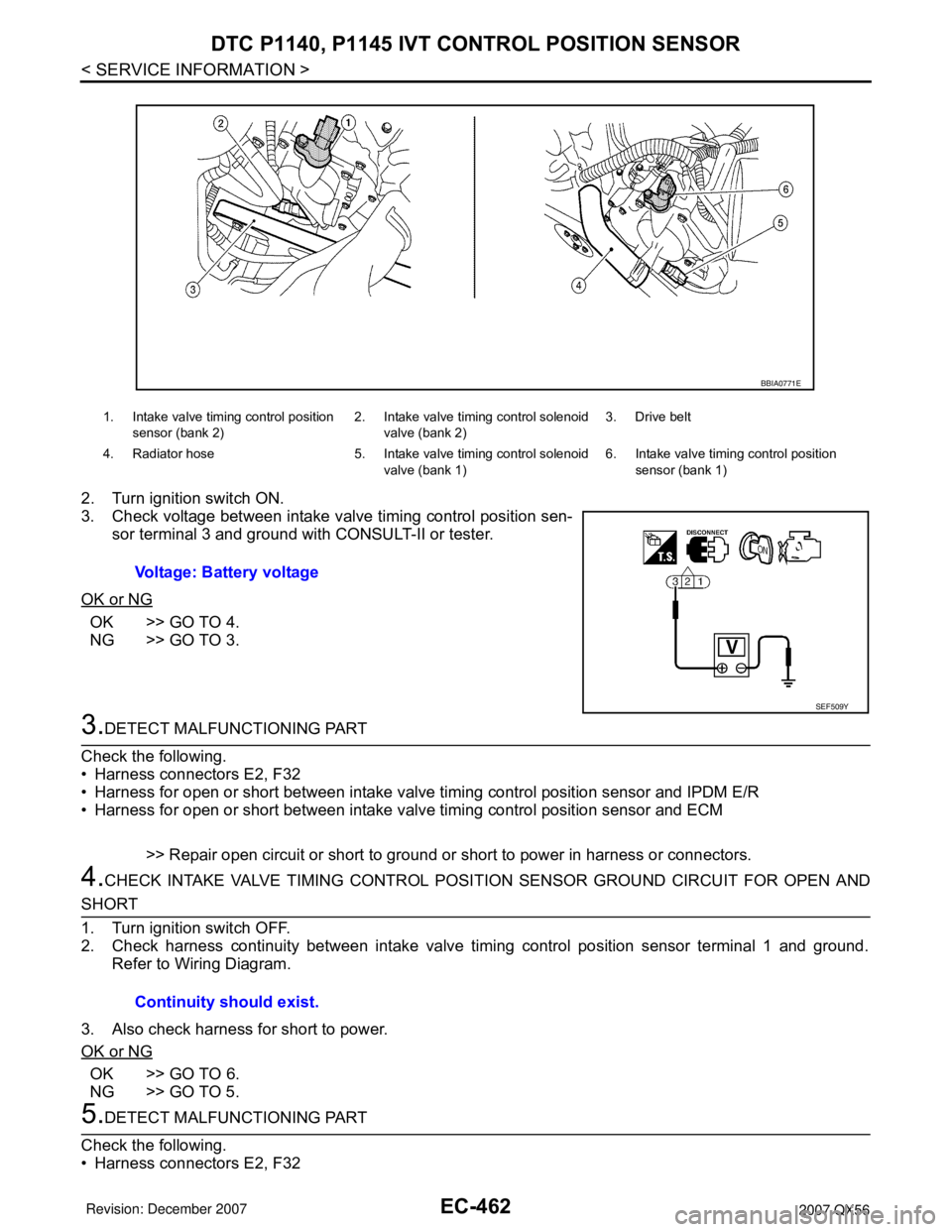
EC-462
< SERVICE INFORMATION >
DTC P1140, P1145 IVT CONTROL POSITION SENSOR
2. Turn ignition switch ON.
3. Check voltage between intake valve timing control position sen-
sor terminal 3 and ground with CONSULT-II or tester.
OK or NG
OK >> GO TO 4.
NG >> GO TO 3.
3.DETECT MALFUNCTIONING PART
Check the following.
• Harness connectors E2, F32
• Harness for open or short between intake valve timing control position sensor and IPDM E/R
• Harness for open or short between intake valve timing control position sensor and ECM
>> Repair open circuit or short to ground or short to power in harness or connectors.
4.CHECK INTAKE VALVE TIMING CONTROL POSITION SENSOR GROUND CIRCUIT FOR OPEN AND
SHORT
1. Turn ignition switch OFF.
2. Check harness continuity between intake valve timing control position sensor terminal 1 and ground.
Refer to Wiring Diagram.
3. Also check harness for short to power.
OK or NG
OK >> GO TO 6.
NG >> GO TO 5.
5.DETECT MALFUNCTIONING PART
Check the following.
• Harness connectors E2, F32
1. Intake valve timing control position
sensor (bank 2)2. Intake valve timing control solenoid
valve (bank 2)3. Drive belt
4. Radiator hose 5. Intake valve timing control solenoid
valve (bank 1)6. Intake valve timing control position
sensor (bank 1)
Voltage: Battery voltage
BBIA0771E
SEF509Y
Continuity should exist.
Page 1546 of 3061
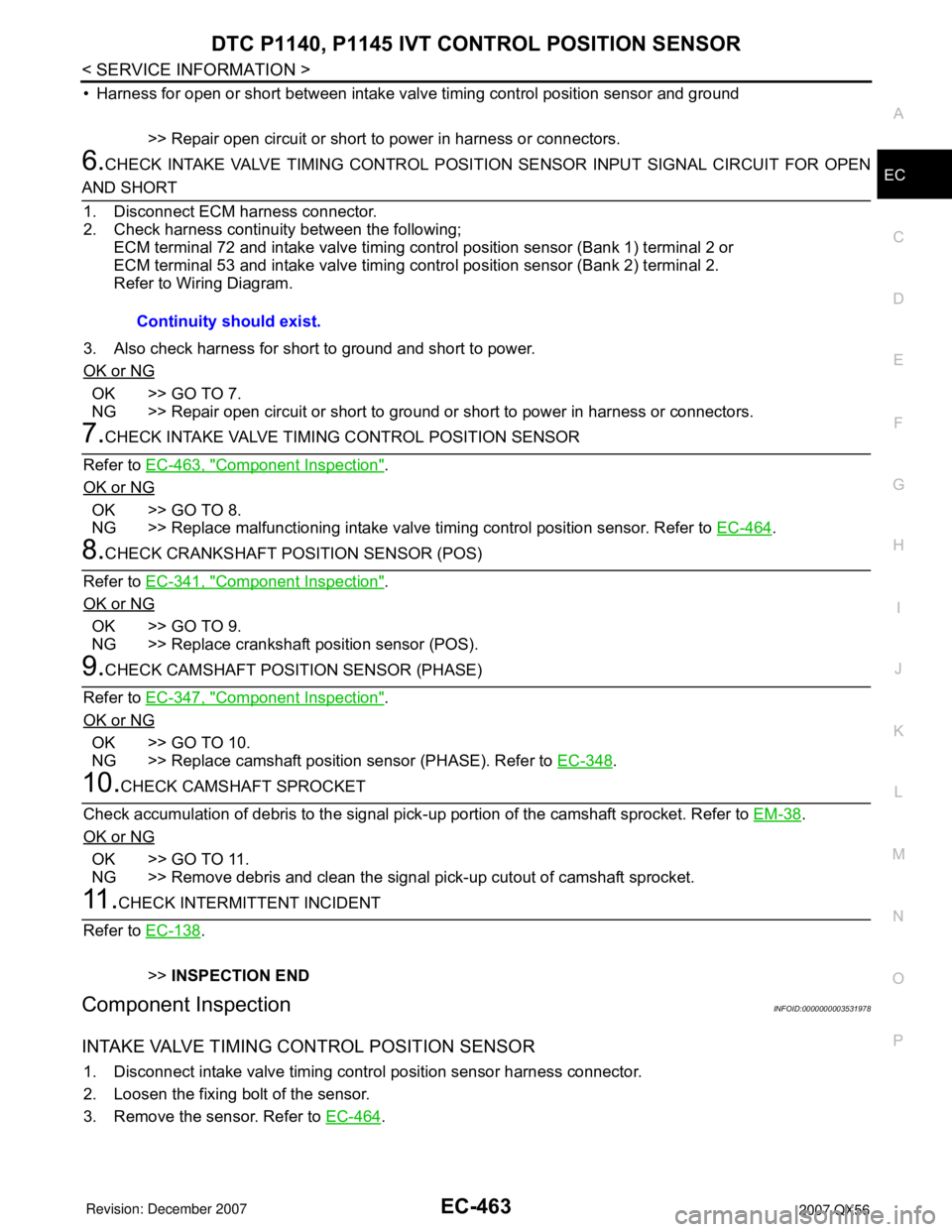
DTC P1140, P1145 IVT CONTROL POSITION SENSOR
EC-463
< SERVICE INFORMATION >
C
D
E
F
G
H
I
J
K
L
MA
EC
N
P O
• Harness for open or short between intake valve timing control position sensor and ground
>> Repair open circuit or short to power in harness or connectors.
6.CHECK INTAKE VALVE TIMING CONTROL POSITION SENSOR INPUT SIGNAL CIRCUIT FOR OPEN
AND SHORT
1. Disconnect ECM harness connector.
2. Check harness continuity between the following;
ECM terminal 72 and intake valve timing control position sensor (Bank 1) terminal 2 or
ECM terminal 53 and intake valve timing control position sensor (Bank 2) terminal 2.
Refer to Wiring Diagram.
3. Also check harness for short to ground and short to power.
OK or NG
OK >> GO TO 7.
NG >> Repair open circuit or short to ground or short to power in harness or connectors.
7.CHECK INTAKE VALVE TIMING CONTROL POSITION SENSOR
Refer to EC-463, "
Component Inspection".
OK or NG
OK >> GO TO 8.
NG >> Replace malfunctioning intake valve timing control position sensor. Refer to EC-464
.
8.CHECK CRANKSHAFT POSITION SENSOR (POS)
Refer to EC-341, "
Component Inspection".
OK or NG
OK >> GO TO 9.
NG >> Replace crankshaft position sensor (POS).
9.CHECK CAMSHAFT POSITION SENSOR (PHASE)
Refer to EC-347, "
Component Inspection".
OK or NG
OK >> GO TO 10.
NG >> Replace camshaft position sensor (PHASE). Refer to EC-348
.
10.CHECK CAMSHAFT SPROCKET
Check accumulation of debris to the signal pick-up portion of the camshaft sprocket. Refer to EM-38
.
OK or NG
OK >> GO TO 11.
NG >> Remove debris and clean the signal pick-up cutout of camshaft sprocket.
11 .CHECK INTERMITTENT INCIDENT
Refer to EC-138
.
>>INSPECTION END
Component InspectionINFOID:0000000003531978
INTAKE VALVE TIMING CONTROL POSITION SENSOR
1. Disconnect intake valve timing control position sensor harness connector.
2. Loosen the fixing bolt of the sensor.
3. Remove the sensor. Refer to EC-464
. Continuity should exist.
Page 1547 of 3061
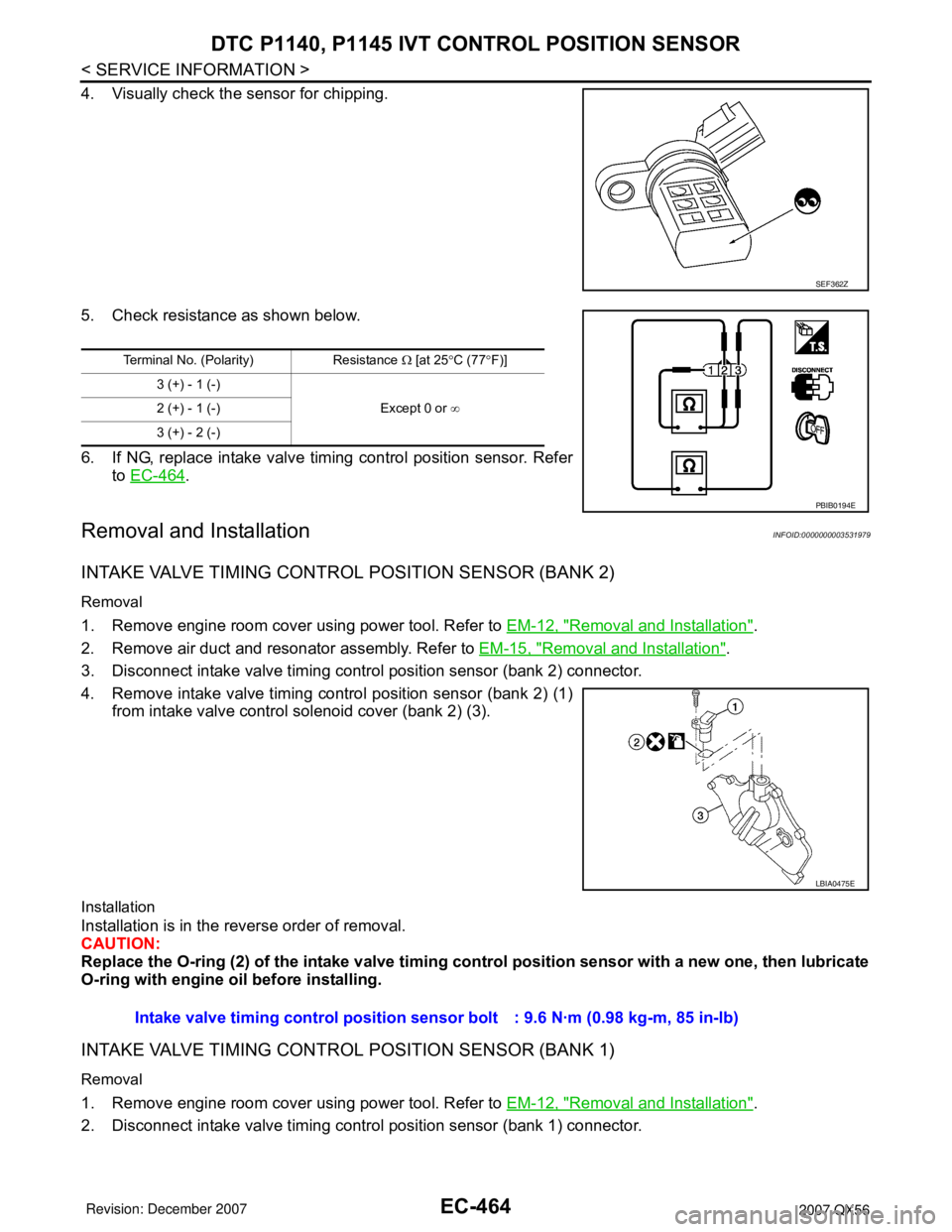
EC-464
< SERVICE INFORMATION >
DTC P1140, P1145 IVT CONTROL POSITION SENSOR
4. Visually check the sensor for chipping.
5. Check resistance as shown below.
6. If NG, replace intake valve timing control position sensor. Refer
to EC-464
.
Removal and InstallationINFOID:0000000003531979
INTAKE VALVE TIMING CONTROL POSITION SENSOR (BANK 2)
Removal
1. Remove engine room cover using power tool. Refer to EM-12, "Removal and Installation".
2. Remove air duct and resonator assembly. Refer to EM-15, "
Removal and Installation".
3. Disconnect intake valve timing control position sensor (bank 2) connector.
4. Remove intake valve timing control position sensor (bank 2) (1)
from intake valve control solenoid cover (bank 2) (3).
Installation
Installation is in the reverse order of removal.
CAUTION:
Replace the O-ring (2) of the intake valve timing control position sensor with a new one, then lubricate
O-ring with engine oil before installing.
INTAKE VALVE TIMING CONTROL POSITION SENSOR (BANK 1)
Removal
1. Remove engine room cover using power tool. Refer to EM-12, "Removal and Installation".
2. Disconnect intake valve timing control position sensor (bank 1) connector.
SEF362Z
Terminal No. (Polarity) Resistance Ω [at 25°C (77°F)]
3 (+) - 1 (-)
Except 0 or ∞ 2 (+) - 1 (-)
3 (+) - 2 (-)
PBIB0194E
LBIA0475E
Intake valve timing control position sensor bolt : 9.6 N·m (0.98 kg-m, 85 in-lb)
Page 1548 of 3061
DTC P1140, P1145 IVT CONTROL POSITION SENSOR
EC-465
< SERVICE INFORMATION >
C
D
E
F
G
H
I
J
K
L
MA
EC
N
P O
3. Remove intake valve timing control position sensor (bank 1) (1)
from intake valve control solenoid cover (bank 1) (3).
Installation
Installation is in the reverse order of removal.
CAUTION:
Replace the O-ring (2) of the intake valve timing control position sensor with a new one, then lubricate
O-ring with engine oil before installing.
LBIA0476E
Intake valve timing control position sensor bolt : 9.6 N·m (0.98 kg-m, 85 in-lb)
Page 1549 of 3061
EC-466
< SERVICE INFORMATION >
DTC P1148, P1168 CLOSED LOOP CONTROL
DTC P1148, P1168 CLOSED LOOP CONTROL
On Board Diagnosis LogicINFOID:0000000003531980
These self-diagnoses have the one trip detection logic.
DTC P1148 or P1168 is displayed with another DTC for air fuel ratio (A/F) sensor 1.
Perform the trouble diagnosis for the corresponding DTC.
DTC No. Trouble diagnosis name DTC detecting condition Possible cause
P1148
11 4 8
(Bank 1)
Closed loop control
functionThe closed loop control function for bank 1 does
not operate even when vehicle is driving in the
specified condition.• Harness or connectors
[The air fuel ratio (A/F) sensor 1 circuit is
open or shorted.]
• Air fuel ratio (A/F) sensor 1
• Air fuel ratio (A/F) sensor 1 heater P1168
11 6 8
(Bank 2)The closed loop control function for bank 2 does
not operate even when vehicle is driving in the
specified condition.
Page 1550 of 3061
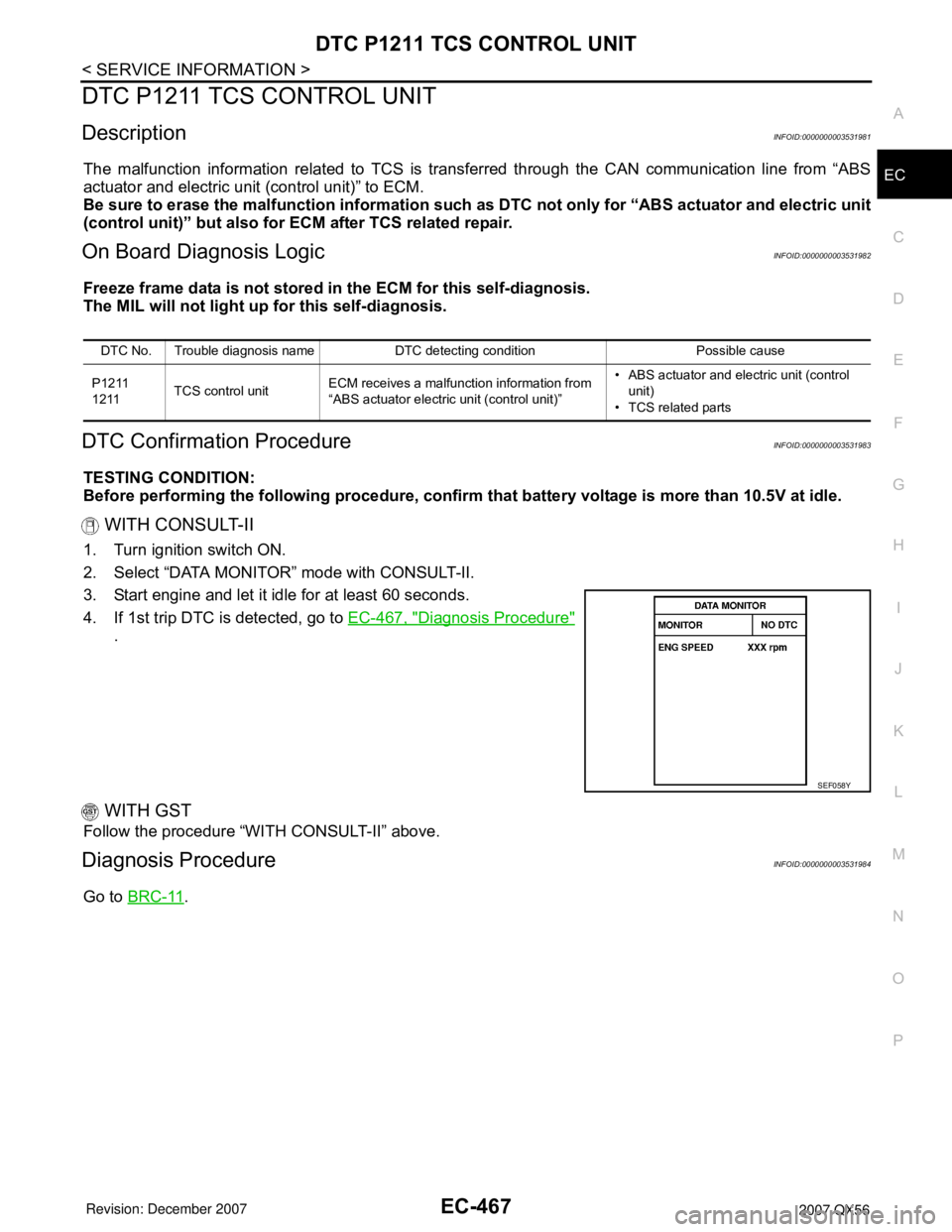
DTC P1211 TCS CONTROL UNIT
EC-467
< SERVICE INFORMATION >
C
D
E
F
G
H
I
J
K
L
MA
EC
N
P O
DTC P1211 TCS CONTROL UNIT
DescriptionINFOID:0000000003531981
The malfunction information related to TCS is transferred through the CAN communication line from “ABS
actuator and electric unit (control unit)” to ECM.
Be sure to erase the malfunction information such as DTC not only for “ABS actuator and electric unit
(control unit)” but also for ECM after TCS related repair.
On Board Diagnosis LogicINFOID:0000000003531982
Freeze frame data is not stored in the ECM for this self-diagnosis.
The MIL will not light up for this self-diagnosis.
DTC Confirmation ProcedureINFOID:0000000003531983
TESTING CONDITION:
Before performing the following procedure, confirm that battery voltage is more than 10.5V at idle.
WITH CONSULT-II
1. Turn ignition switch ON.
2. Select “DATA MONITOR” mode with CONSULT-II.
3. Start engine and let it idle for at least 60 seconds.
4. If 1st trip DTC is detected, go to EC-467, "
Diagnosis Procedure"
.
WITH GST
Follow the procedure “WITH CONSULT-II” above.
Diagnosis ProcedureINFOID:0000000003531984
Go to BRC-11.
DTC No. Trouble diagnosis name DTC detecting condition Possible cause
P1211
1211TCS control unitECM receives a malfunction information from
“ABS actuator electric unit (control unit)”• ABS actuator and electric unit (control
unit)
• TCS related parts
SEF058Y
Page 1551 of 3061
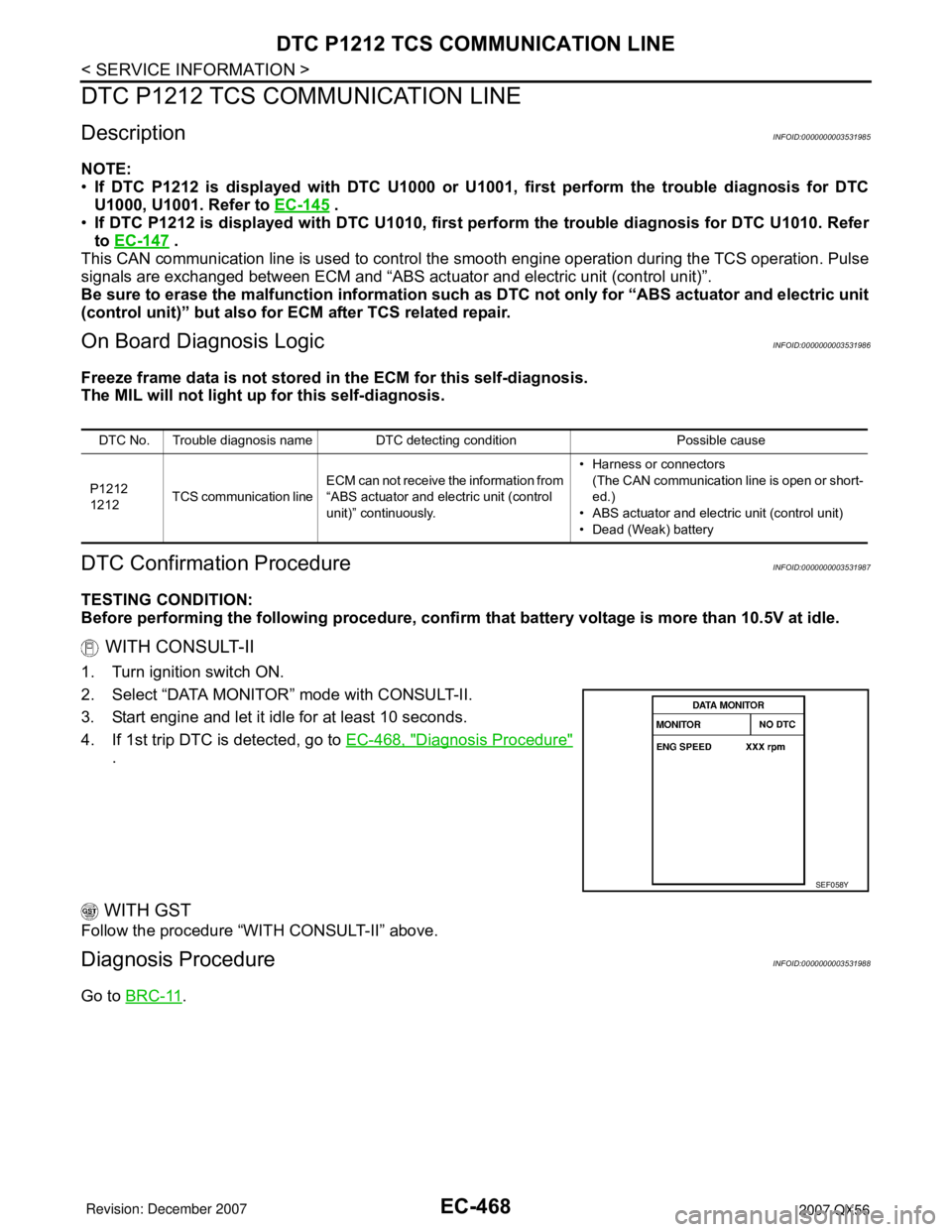
EC-468
< SERVICE INFORMATION >
DTC P1212 TCS COMMUNICATION LINE
DTC P1212 TCS COMMUNICATION LINE
DescriptionINFOID:0000000003531985
NOTE:
•If DTC P1212 is displayed with DTC U1000 or U1001, first perform the trouble diagnosis for DTC
U1000, U1001. Refer to EC-145
.
•If DTC P1212 is displayed with DTC U1010, first perform the trouble diagnosis for DTC U1010. Refer
to EC-147
.
This CAN communication line is used to control the smooth engine operation during the TCS operation. Pulse
signals are exchanged between ECM and “ABS actuator and electric unit (control unit)”.
Be sure to erase the malfunction information such as DTC not only for “ABS actuator and electric unit
(control unit)” but also for ECM after TCS related repair.
On Board Diagnosis LogicINFOID:0000000003531986
Freeze frame data is not stored in the ECM for this self-diagnosis.
The MIL will not light up for this self-diagnosis.
DTC Confirmation ProcedureINFOID:0000000003531987
TESTING CONDITION:
Before performing the following procedure, confirm that battery voltage is more than 10.5V at idle.
WITH CONSULT-II
1. Turn ignition switch ON.
2. Select “DATA MONITOR” mode with CONSULT-II.
3. Start engine and let it idle for at least 10 seconds.
4. If 1st trip DTC is detected, go to EC-468, "
Diagnosis Procedure"
.
WITH GST
Follow the procedure “WITH CONSULT-II” above.
Diagnosis ProcedureINFOID:0000000003531988
Go to BRC-11.
DTC No. Trouble diagnosis name DTC detecting condition Possible cause
P1212
1212TCS communication lineECM can not receive the information from
“ABS actuator and electric unit (control
unit)” continuously.• Harness or connectors
(The CAN communication line is open or short-
ed.)
• ABS actuator and electric unit (control unit)
• Dead (Weak) battery
SEF058Y
Page 1552 of 3061
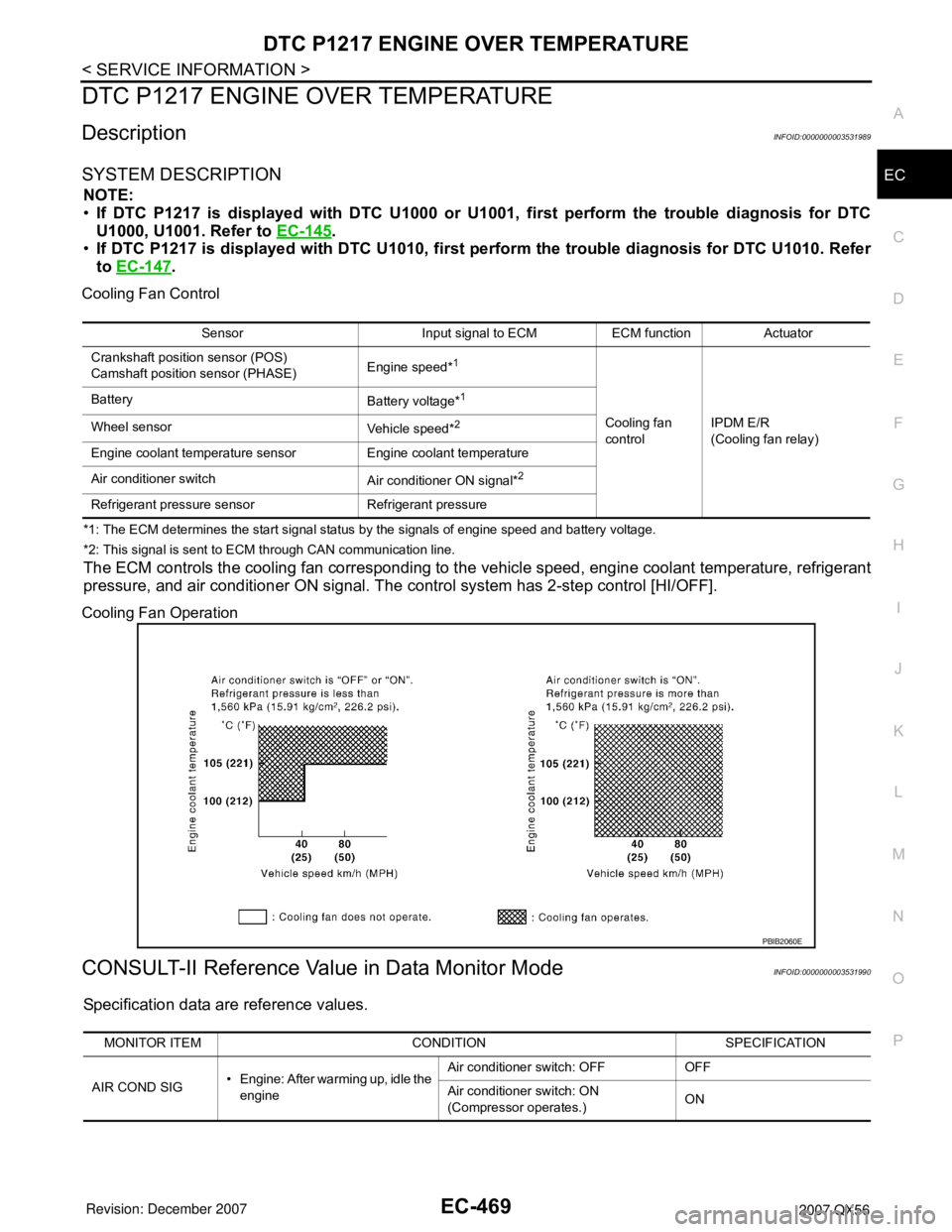
DTC P1217 ENGINE OVER TEMPERATURE
EC-469
< SERVICE INFORMATION >
C
D
E
F
G
H
I
J
K
L
MA
EC
N
P O
DTC P1217 ENGINE OVER TEMPERATURE
DescriptionINFOID:0000000003531989
SYSTEM DESCRIPTION
NOTE:
•If DTC P1217 is displayed with DTC U1000 or U1001, first perform the trouble diagnosis for DTC
U1000, U1001. Refer to EC-145
.
•If DTC P1217 is displayed with DTC U1010, first perform the trouble diagnosis for DTC U1010. Refer
to EC-147
.
Cooling Fan Control
*1: The ECM determines the start signal status by the signals of engine speed and battery voltage.
*2: This signal is sent to ECM through CAN communication line.
The ECM controls the cooling fan corresponding to the vehicle speed, engine coolant temperature, refrigerant
pressure, and air conditioner ON signal. The control system has 2-step control [HI/OFF].
Cooling Fan Operation
CONSULT-II Reference Value in Data Monitor ModeINFOID:0000000003531990
Specification data are reference values.
Sensor Input signal to ECM ECM function Actuator
Crankshaft position sensor (POS)
Camshaft position sensor (PHASE)Engine speed*
1
Cooling fan
controlIPDM E/R
(Cooling fan relay) Battery
Battery voltage*
1
Wheel sensor
Vehicle speed*2
Engine coolant temperature sensor Engine coolant temperature
Air conditioner switch
Air conditioner ON signal*
2
Refrigerant pressure sensor Refrigerant pressure
PBIB2060E
MONITOR ITEM CONDITION SPECIFICATION
AIR COND SIG• Engine: After warming up, idle the
engineAir conditioner switch: OFF OFF
Air conditioner switch: ON
(Compressor operates.)ON