Page 2049 of 2643
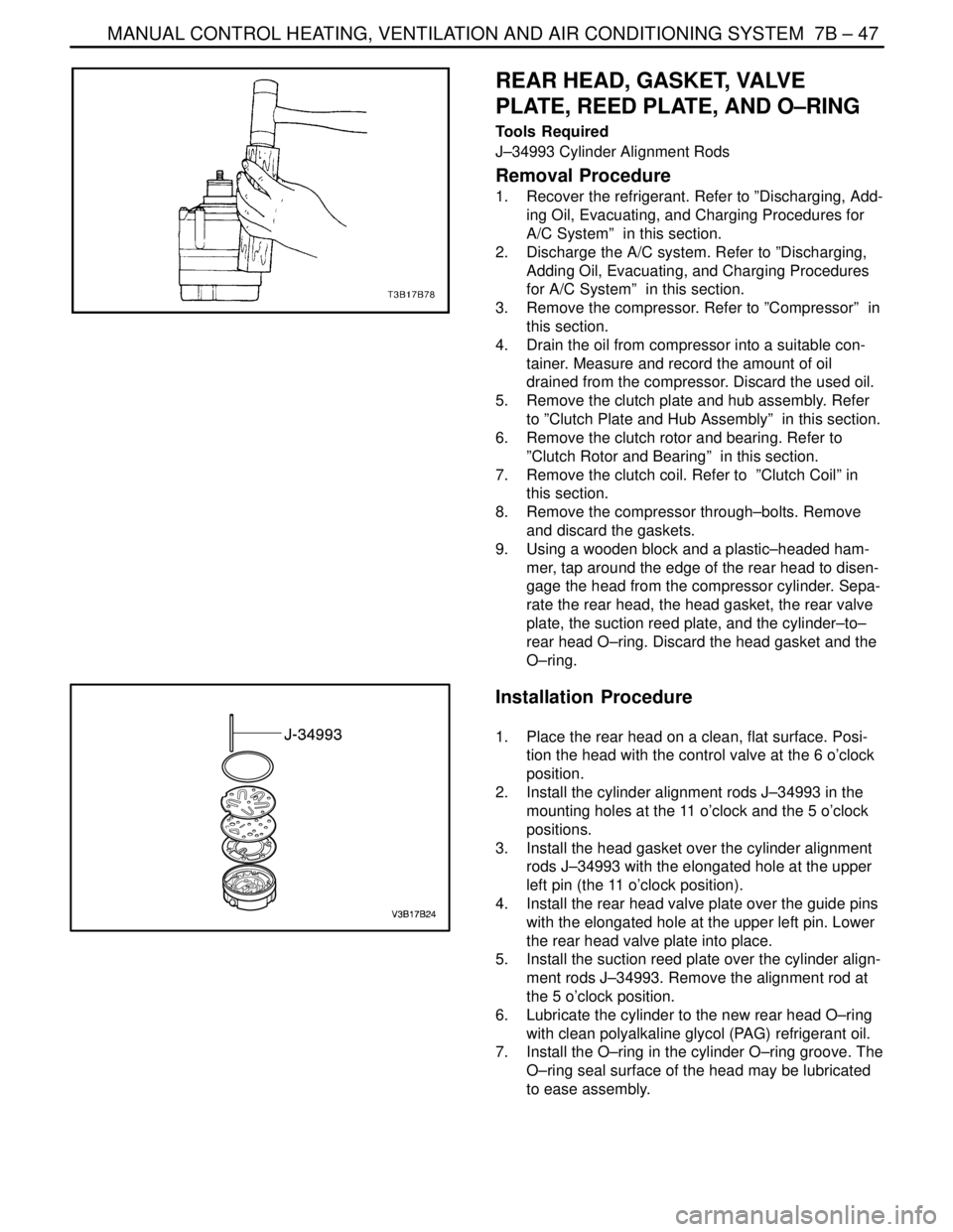
MANUAL CONTROL HEATING, VENTILATION AND AIR CONDITIONING SYSTEM 7B – 47
DAEWOO V–121 BL4
REAR HEAD, GASKET, VALVE
PLATE, REED PLATE, AND O–RING
Tools Required
J–34993 Cylinder Alignment Rods
Removal Procedure
1. Recover the refrigerant. Refer to ”Discharging, Add-
ing Oil, Evacuating, and Charging Procedures for
A/C System” in this section.
2. Discharge the A/C system. Refer to ”Discharging,
Adding Oil, Evacuating, and Charging Procedures
for A/C System” in this section.
3. Remove the compressor. Refer to ”Compressor” in
this section.
4. Drain the oil from compressor into a suitable con-
tainer. Measure and record the amount of oil
drained from the compressor. Discard the used oil.
5. Remove the clutch plate and hub assembly. Refer
to ”Clutch Plate and Hub Assembly” in this section.
6. Remove the clutch rotor and bearing. Refer to
”Clutch Rotor and Bearing” in this section.
7. Remove the clutch coil. Refer to ”Clutch Coil” in
this section.
8. Remove the compressor through–bolts. Remove
and discard the gaskets.
9. Using a wooden block and a plastic–headed ham-
mer, tap around the edge of the rear head to disen-
gage the head from the compressor cylinder. Sepa-
rate the rear head, the head gasket, the rear valve
plate, the suction reed plate, and the cylinder–to–
rear head O–ring. Discard the head gasket and the
O–ring.
Installation Procedure
1. Place the rear head on a clean, flat surface. Posi-
tion the head with the control valve at the 6 o’clock
position.
2. Install the cylinder alignment rods J–34993 in the
mounting holes at the 11 o’clock and the 5 o’clock
positions.
3. Install the head gasket over the cylinder alignment
rods J–34993 with the elongated hole at the upper
left pin (the 11 o’clock position).
4. Install the rear head valve plate over the guide pins
with the elongated hole at the upper left pin. Lower
the rear head valve plate into place.
5. Install the suction reed plate over the cylinder align-
ment rods J–34993. Remove the alignment rod at
the 5 o’clock position.
6. Lubricate the cylinder to the new rear head O–ring
with clean polyalkaline glycol (PAG) refrigerant oil.
7. Install the O–ring in the cylinder O–ring groove. The
O–ring seal surface of the head may be lubricated
to ease assembly.
Page 2050 of 2643

7B – 48IMANUAL CONTROL HEATING, VENTILATION AND AIR CONDITIONING SYSTEM
DAEWOO V–121 BL4
8. With the O–ring in place on the rear of the cylinder
assembly, locate the relief boss for the compressor
guide pin at the 6 o’clock position, directly above
the hole in the side of the rear head. Carefully lower
the cylinder and the front head assembly over the
guide pin to the rear head.
9. Press the cylinder and the compressor housing as-
sembly down onto the rear head using both hands.
10. Add the new through–bolt gasket to the through–
bolts and install it into the compressor assembly.
Four of the through–bolts must thread into the rear
head before removing the alignment rod.
Tighten
Alternately tighten the through–bolts in progressive
torque sequence to 10 NSm (89 lb–in).
11. Add new PAG refrigerant oil as determined in Step
1 of Removal Procedure.
12. Place the shaft nut on the shaft and rotate the com-
pressor shaft several times.
13. Perform a leak test on the compressor. Refer to
”Leak Testing (External)” in this section.
14. Install the clutch coil. Refer to ”Clutch Coil” in this
section.
15. Install the clutch rotor and bearing. Refer to ”Clutch
Rotor and Bearing” in this section.
16. Install the clutch plate and hub assembly. Refer to
”Clutch Plate and Hub Assembly” in this section.
17. Install the compressor. Refer to ”Compressor” in
this section.
18. Evacuate and recharge the A/C system. Refer to
”Discharging, Adding Oil, Evacuating, and Charging
Procedures for A/C System” in this section.
CYLINDER–TO–FRONT HEAD
O–RING
Tools Required
J–34993 Cylinder Alignment Rods
J–35372 Support Block
Removal Procedure
1. Recover the refrigerant. Refer to ”Discharging, Add-
ing Oil, Evacuating, and Charging Procedures for
A/C System” in this section.
2. Remove the compressor. Refer to ”Compressor” in
this section.
3. Drain the oil from compressor into a suitable con-
tainer. Measure and record the amount of oil
drained from the compressor. Discard all used oil.
4. Remove the clutch plate and hub assembly. Refer
to ”Clutch Plate and Hub Assembly” in this section.
5. Remove the clutch rotor and bearing. Refer to
”Clutch Rotor and Bearing” in this section.
6. Remove the clutch coil. Refer to ”Clutch Coil” in
this section.
Page 2051 of 2643
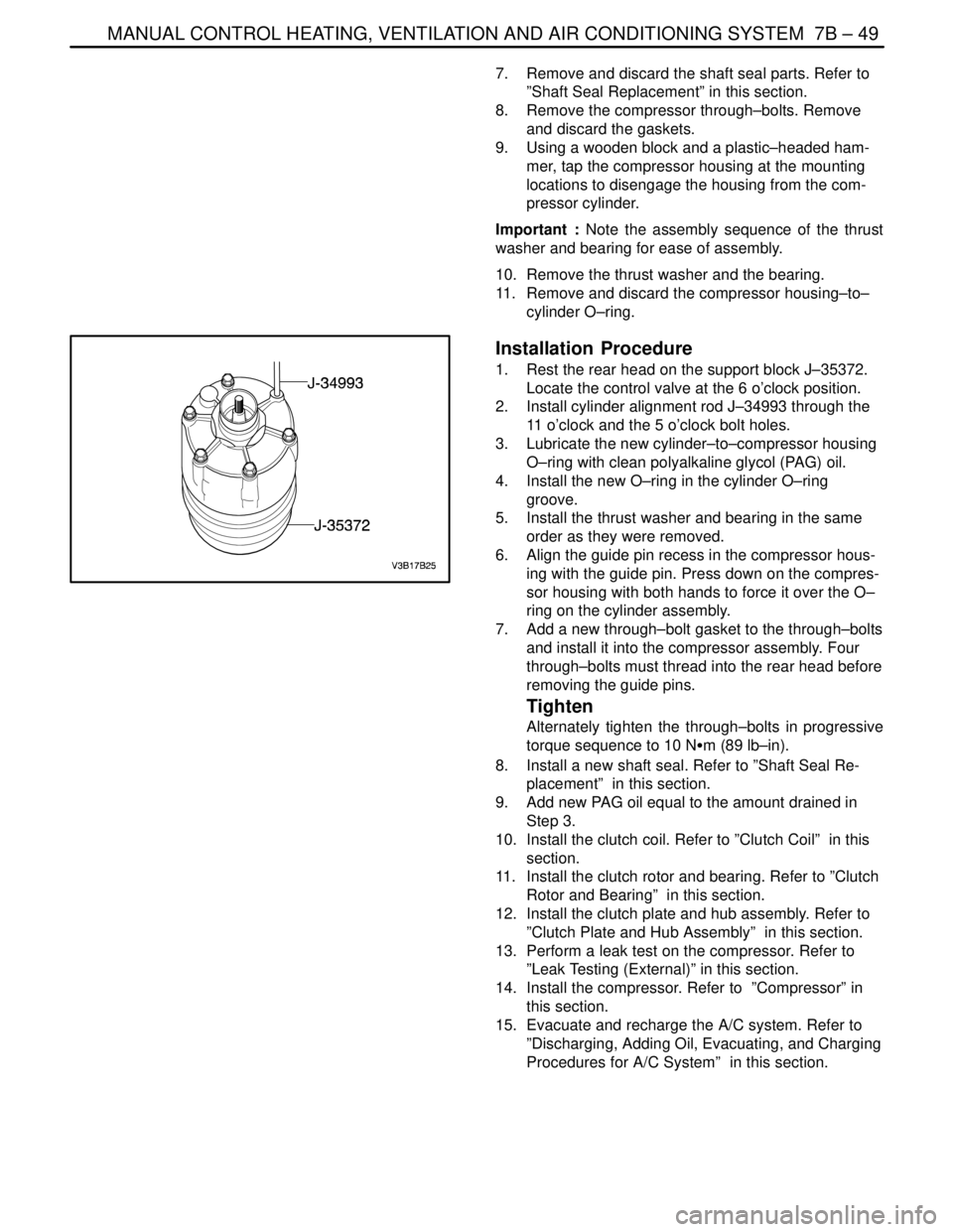
MANUAL CONTROL HEATING, VENTILATION AND AIR CONDITIONING SYSTEM 7B – 49
DAEWOO V–121 BL4
7. Remove and discard the shaft seal parts. Refer to
”Shaft Seal Replacement” in this section.
8. Remove the compressor through–bolts. Remove
and discard the gaskets.
9. Using a wooden block and a plastic–headed ham-
mer, tap the compressor housing at the mounting
locations to disengage the housing from the com-
pressor cylinder.
Important : Note the assembly sequence of the thrust
washer and bearing for ease of assembly.
10. Remove the thrust washer and the bearing.
11. Remove and discard the compressor housing–to–
cylinder O–ring.
Installation Procedure
1. Rest the rear head on the support block J–35372.
Locate the control valve at the 6 o’clock position.
2. Install cylinder alignment rod J–34993 through the
11 o’clock and the 5 o’clock bolt holes.
3. Lubricate the new cylinder–to–compressor housing
O–ring with clean polyalkaline glycol (PAG) oil.
4. Install the new O–ring in the cylinder O–ring
groove.
5. Install the thrust washer and bearing in the same
order as they were removed.
6. Align the guide pin recess in the compressor hous-
ing with the guide pin. Press down on the compres-
sor housing with both hands to force it over the O–
ring on the cylinder assembly.
7. Add a new through–bolt gasket to the through–bolts
and install it into the compressor assembly. Four
through–bolts must thread into the rear head before
removing the guide pins.
Tighten
Alternately tighten the through–bolts in progressive
torque sequence to 10 NSm (89 lb–in).
8. Install a new shaft seal. Refer to ”Shaft Seal Re-
placement” in this section.
9. Add new PAG oil equal to the amount drained in
Step 3.
10. Install the clutch coil. Refer to ”Clutch Coil” in this
section.
11. Install the clutch rotor and bearing. Refer to ”Clutch
Rotor and Bearing” in this section.
12. Install the clutch plate and hub assembly. Refer to
”Clutch Plate and Hub Assembly” in this section.
13. Perform a leak test on the compressor. Refer to
”Leak Testing (External)” in this section.
14. Install the compressor. Refer to ”Compressor” in
this section.
15. Evacuate and recharge the A/C system. Refer to
”Discharging, Adding Oil, Evacuating, and Charging
Procedures for A/C System” in this section.
Page 2052 of 2643
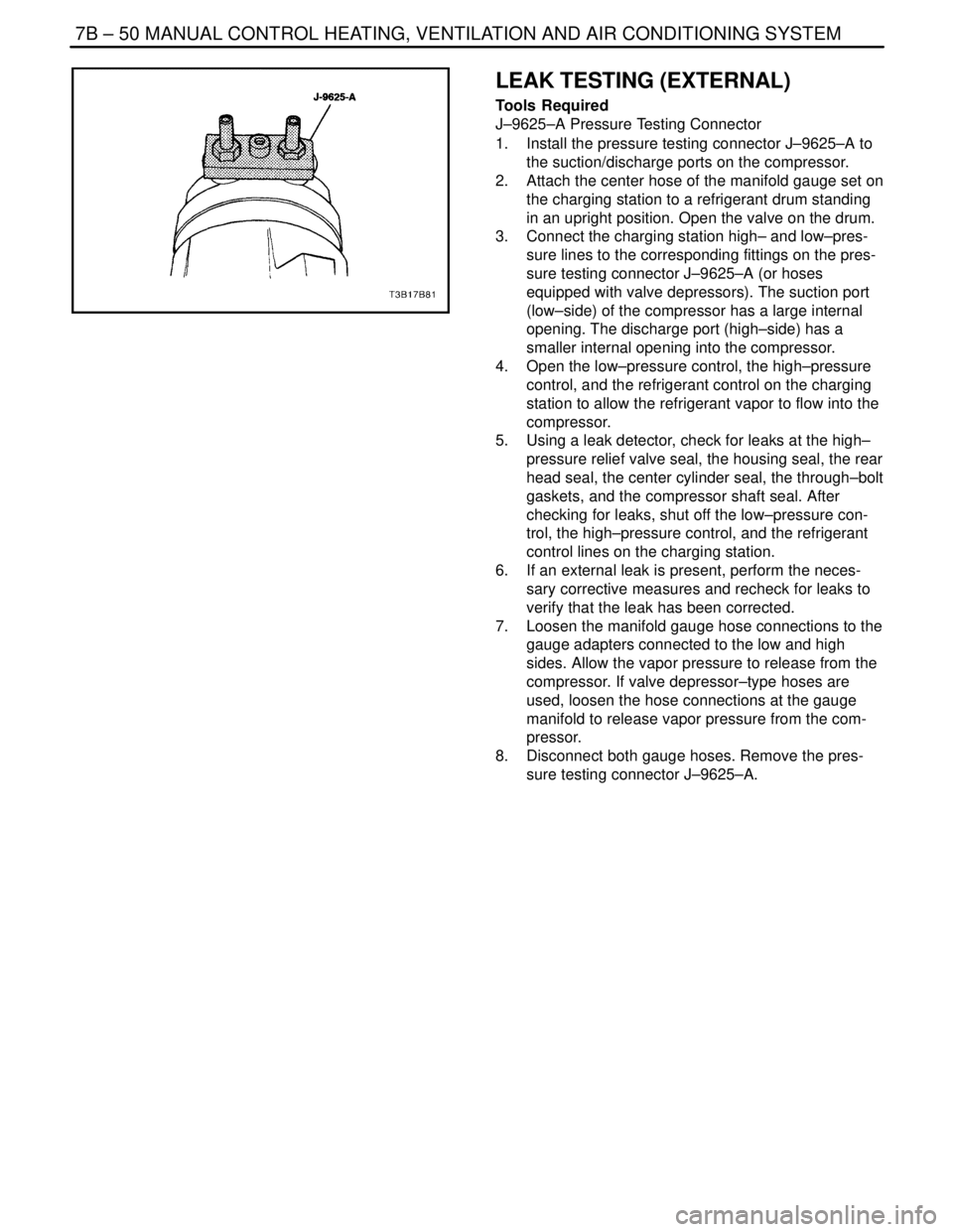
7B – 50IMANUAL CONTROL HEATING, VENTILATION AND AIR CONDITIONING SYSTEM
DAEWOO V–121 BL4
LEAK TESTING (EXTERNAL)
Tools Required
J–9625–A Pressure Testing Connector
1. Install the pressure testing connector J–9625–A to
the suction/discharge ports on the compressor.
2. Attach the center hose of the manifold gauge set on
the charging station to a refrigerant drum standing
in an upright position. Open the valve on the drum.
3. Connect the charging station high– and low–pres-
sure lines to the corresponding fittings on the pres-
sure testing connector J–9625–A (or hoses
equipped with valve depressors). The suction port
(low–side) of the compressor has a large internal
opening. The discharge port (high–side) has a
smaller internal opening into the compressor.
4. Open the low–pressure control, the high–pressure
control, and the refrigerant control on the charging
station to allow the refrigerant vapor to flow into the
compressor.
5. Using a leak detector, check for leaks at the high–
pressure relief valve seal, the housing seal, the rear
head seal, the center cylinder seal, the through–bolt
gaskets, and the compressor shaft seal. After
checking for leaks, shut off the low–pressure con-
trol, the high–pressure control, and the refrigerant
control lines on the charging station.
6. If an external leak is present, perform the neces-
sary corrective measures and recheck for leaks to
verify that the leak has been corrected.
7. Loosen the manifold gauge hose connections to the
gauge adapters connected to the low and high
sides. Allow the vapor pressure to release from the
compressor. If valve depressor–type hoses are
used, loosen the hose connections at the gauge
manifold to release vapor pressure from the com-
pressor.
8. Disconnect both gauge hoses. Remove the pres-
sure testing connector J–9625–A.
Page 2053 of 2643
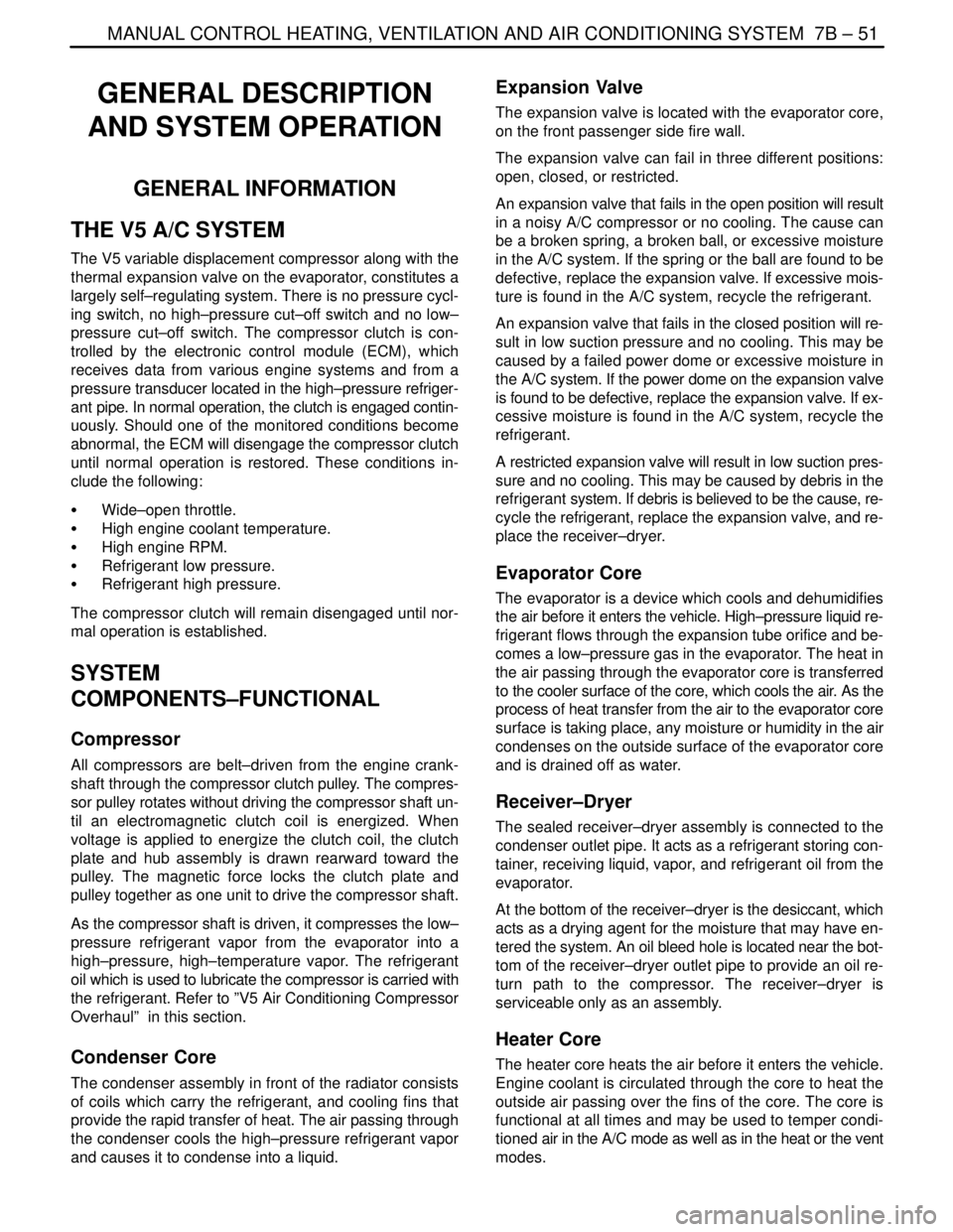
MANUAL CONTROL HEATING, VENTILATION AND AIR CONDITIONING SYSTEM 7B – 51
DAEWOO V–121 BL4
GENERAL DESCRIPTION
AND SYSTEM OPERATION
GENERAL INFORMATION
THE V5 A/C SYSTEM
The V5 variable displacement compressor along with the
thermal expansion valve on the evaporator, constitutes a
largely self–regulating system. There is no pressure cycl-
ing switch, no high–pressure cut–off switch and no low–
pressure cut–off switch. The compressor clutch is con-
trolled by the electronic control module (ECM), which
receives data from various engine systems and from a
pressure transducer located in the high–pressure refriger-
ant pipe. In normal operation, the clutch is engaged contin-
uously. Should one of the monitored conditions become
abnormal, the ECM will disengage the compressor clutch
until normal operation is restored. These conditions in-
clude the following:
S Wide–open throttle.
S High engine coolant temperature.
S High engine RPM.
S Refrigerant low pressure.
S Refrigerant high pressure.
The compressor clutch will remain disengaged until nor-
mal operation is established.
SYSTEM
COMPONENTS–FUNCTIONAL
Compressor
All compressors are belt–driven from the engine crank-
shaft through the compressor clutch pulley. The compres-
sor pulley rotates without driving the compressor shaft un-
til an electromagnetic clutch coil is energized. When
voltage is applied to energize the clutch coil, the clutch
plate and hub assembly is drawn rearward toward the
pulley. The magnetic force locks the clutch plate and
pulley together as one unit to drive the compressor shaft.
As the compressor shaft is driven, it compresses the low–
pressure refrigerant vapor from the evaporator into a
high–pressure, high–temperature vapor. The refrigerant
oil which is used to lubricate the compressor is carried with
the refrigerant. Refer to ”V5 Air Conditioning Compressor
Overhaul” in this section.
Condenser Core
The condenser assembly in front of the radiator consists
of coils which carry the refrigerant, and cooling fins that
provide the rapid transfer of heat. The air passing through
the condenser cools the high–pressure refrigerant vapor
and causes it to condense into a liquid.
Expansion Valve
The expansion valve is located with the evaporator core,
on the front passenger side fire wall.
The expansion valve can fail in three different positions:
open, closed, or restricted.
An expansion valve that fails in the open position will result
in a noisy A/C compressor or no cooling. The cause can
be a broken spring, a broken ball, or excessive moisture
in the A/C system. If the spring or the ball are found to be
defective, replace the expansion valve. If excessive mois-
ture is found in the A/C system, recycle the refrigerant.
An expansion valve that fails in the closed position will re-
sult in low suction pressure and no cooling. This may be
caused by a failed power dome or excessive moisture in
the A/C system. If the power dome on the expansion valve
is found to be defective, replace the expansion valve. If ex-
cessive moisture is found in the A/C system, recycle the
refrigerant.
A restricted expansion valve will result in low suction pres-
sure and no cooling. This may be caused by debris in the
refrigerant system. If debris is believed to be the cause, re-
cycle the refrigerant, replace the expansion valve, and re-
place the receiver–dryer.
Evaporator Core
The evaporator is a device which cools and dehumidifies
the air before it enters the vehicle. High–pressure liquid re-
frigerant flows through the expansion tube orifice and be-
comes a low–pressure gas in the evaporator. The heat in
the air passing through the evaporator core is transferred
to the cooler surface of the core, which cools the air. As the
process of heat transfer from the air to the evaporator core
surface is taking place, any moisture or humidity in the air
condenses on the outside surface of the evaporator core
and is drained off as water.
Receiver–Dryer
The sealed receiver–dryer assembly is connected to the
condenser outlet pipe. It acts as a refrigerant storing con-
tainer, receiving liquid, vapor, and refrigerant oil from the
evaporator.
At the bottom of the receiver–dryer is the desiccant, which
acts as a drying agent for the moisture that may have en-
tered the system. An oil bleed hole is located near the bot-
tom of the receiver–dryer outlet pipe to provide an oil re-
turn path to the compressor. The receiver–dryer is
serviceable only as an assembly.
Heater Core
The heater core heats the air before it enters the vehicle.
Engine coolant is circulated through the core to heat the
outside air passing over the fins of the core. The core is
functional at all times and may be used to temper condi-
tioned air in the A/C mode as well as in the heat or the vent
modes.
Page 2054 of 2643
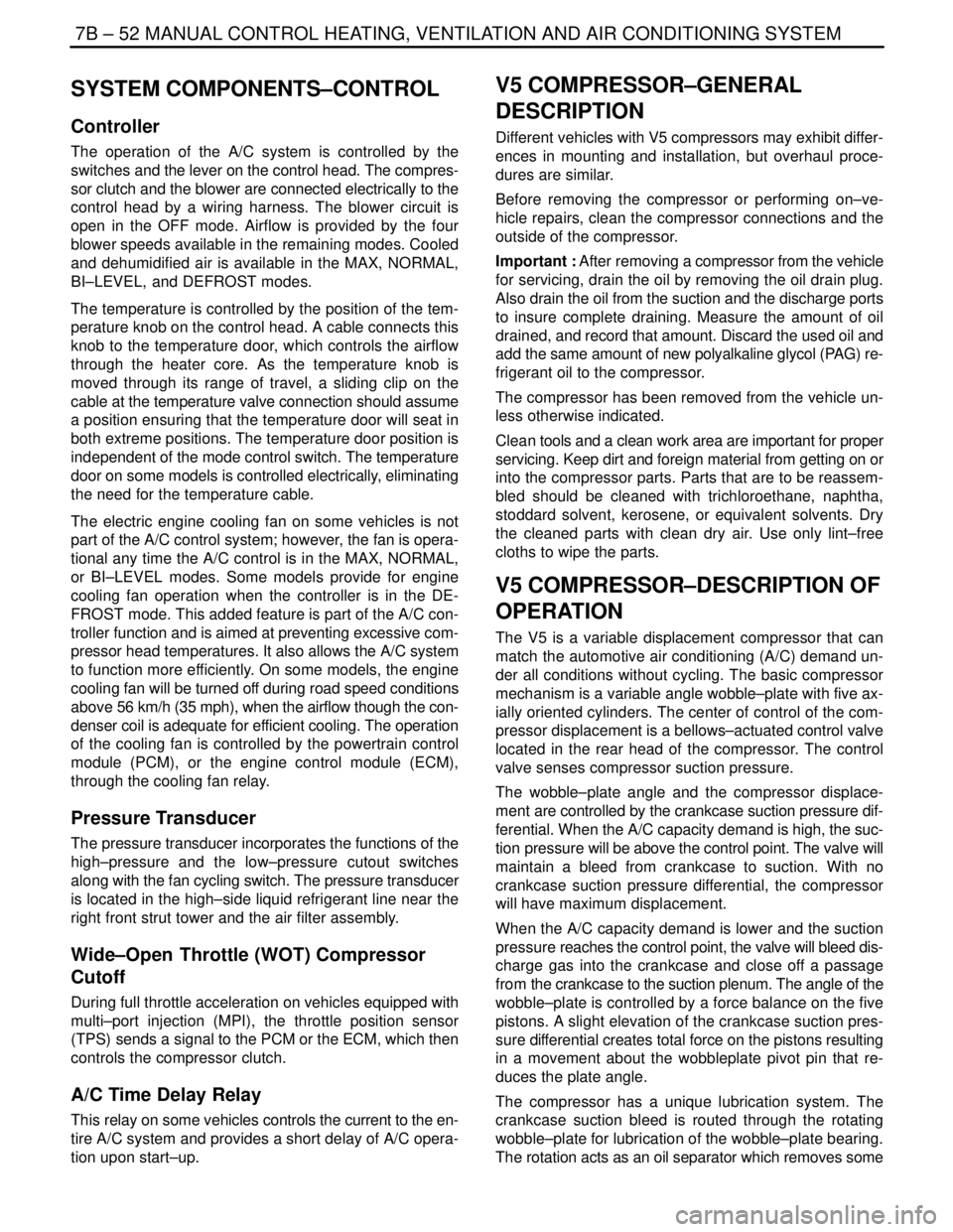
7B – 52IMANUAL CONTROL HEATING, VENTILATION AND AIR CONDITIONING SYSTEM
DAEWOO V–121 BL4
SYSTEM COMPONENTS–CONTROL
Controller
The operation of the A/C system is controlled by the
switches and the lever on the control head. The compres-
sor clutch and the blower are connected electrically to the
control head by a wiring harness. The blower circuit is
open in the OFF mode. Airflow is provided by the four
blower speeds available in the remaining modes. Cooled
and dehumidified air is available in the MAX, NORMAL,
BI–LEVEL, and DEFROST modes.
The temperature is controlled by the position of the tem-
perature knob on the control head. A cable connects this
knob to the temperature door, which controls the airflow
through the heater core. As the temperature knob is
moved through its range of travel, a sliding clip on the
cable at the temperature valve connection should assume
a position ensuring that the temperature door will seat in
both extreme positions. The temperature door position is
independent of the mode control switch. The temperature
door on some models is controlled electrically, eliminating
the need for the temperature cable.
The electric engine cooling fan on some vehicles is not
part of the A/C control system; however, the fan is opera-
tional any time the A/C control is in the MAX, NORMAL,
or BI–LEVEL modes. Some models provide for engine
cooling fan operation when the controller is in the DE-
FROST mode. This added feature is part of the A/C con-
troller function and is aimed at preventing excessive com-
pressor head temperatures. It also allows the A/C system
to function more efficiently. On some models, the engine
cooling fan will be turned off during road speed conditions
above 56 km/h (35 mph), when the airflow though the con-
denser coil is adequate for efficient cooling. The operation
of the cooling fan is controlled by the powertrain control
module (PCM), or the engine control module (ECM),
through the cooling fan relay.
Pressure Transducer
The pressure transducer incorporates the functions of the
high–pressure and the low–pressure cutout switches
along with the fan cycling switch. The pressure transducer
is located in the high–side liquid refrigerant line near the
right front strut tower and the air filter assembly.
Wide–Open Throttle (WOT) Compressor
Cutoff
During full throttle acceleration on vehicles equipped with
multi–port injection (MPI), the throttle position sensor
(TPS) sends a signal to the PCM or the ECM, which then
controls the compressor clutch.
A/C Time Delay Relay
This relay on some vehicles controls the current to the en-
tire A/C system and provides a short delay of A/C opera-
tion upon start–up.
V5 COMPRESSOR–GENERAL
DESCRIPTION
Different vehicles with V5 compressors may exhibit differ-
ences in mounting and installation, but overhaul proce-
dures are similar.
Before removing the compressor or performing on–ve-
hicle repairs, clean the compressor connections and the
outside of the compressor.
Important : After removing a compressor from the vehicle
for servicing, drain the oil by removing the oil drain plug.
Also drain the oil from the suction and the discharge ports
to insure complete draining. Measure the amount of oil
drained, and record that amount. Discard the used oil and
add the same amount of new polyalkaline glycol (PAG) re-
frigerant oil to the compressor.
The compressor has been removed from the vehicle un-
less otherwise indicated.
Clean tools and a clean work area are important for proper
servicing. Keep dirt and foreign material from getting on or
into the compressor parts. Parts that are to be reassem-
bled should be cleaned with trichloroethane, naphtha,
stoddard solvent, kerosene, or equivalent solvents. Dry
the cleaned parts with clean dry air. Use only lint–free
cloths to wipe the parts.
V5 COMPRESSOR–DESCRIPTION OF
OPERATION
The V5 is a variable displacement compressor that can
match the automotive air conditioning (A/C) demand un-
der all conditions without cycling. The basic compressor
mechanism is a variable angle wobble–plate with five ax-
ially oriented cylinders. The center of control of the com-
pressor displacement is a bellows–actuated control valve
located in the rear head of the compressor. The control
valve senses compressor suction pressure.
The wobble–plate angle and the compressor displace-
ment are controlled by the crankcase suction pressure dif-
ferential. When the A/C capacity demand is high, the suc-
tion pressure will be above the control point. The valve will
maintain a bleed from crankcase to suction. With no
crankcase suction pressure differential, the compressor
will have maximum displacement.
When the A/C capacity demand is lower and the suction
pressure reaches the control point, the valve will bleed dis-
charge gas into the crankcase and close off a passage
from the crankcase to the suction plenum. The angle of the
wobble–plate is controlled by a force balance on the five
pistons. A slight elevation of the crankcase suction pres-
sure differential creates total force on the pistons resulting
in a movement about the wobbleplate pivot pin that re-
duces the plate angle.
The compressor has a unique lubrication system. The
crankcase suction bleed is routed through the rotating
wobble–plate for lubrication of the wobble–plate bearing.
The rotation acts as an oil separator which removes some
Page 2055 of 2643
MANUAL CONTROL HEATING, VENTILATION AND AIR CONDITIONING SYSTEM 7B – 53
DAEWOO V–121 BL4
of the oil from the crankcase suction bleed, re–routing it to
the crankcase where it can lubricate the compressor
mechanism.
Page 2056 of 2643
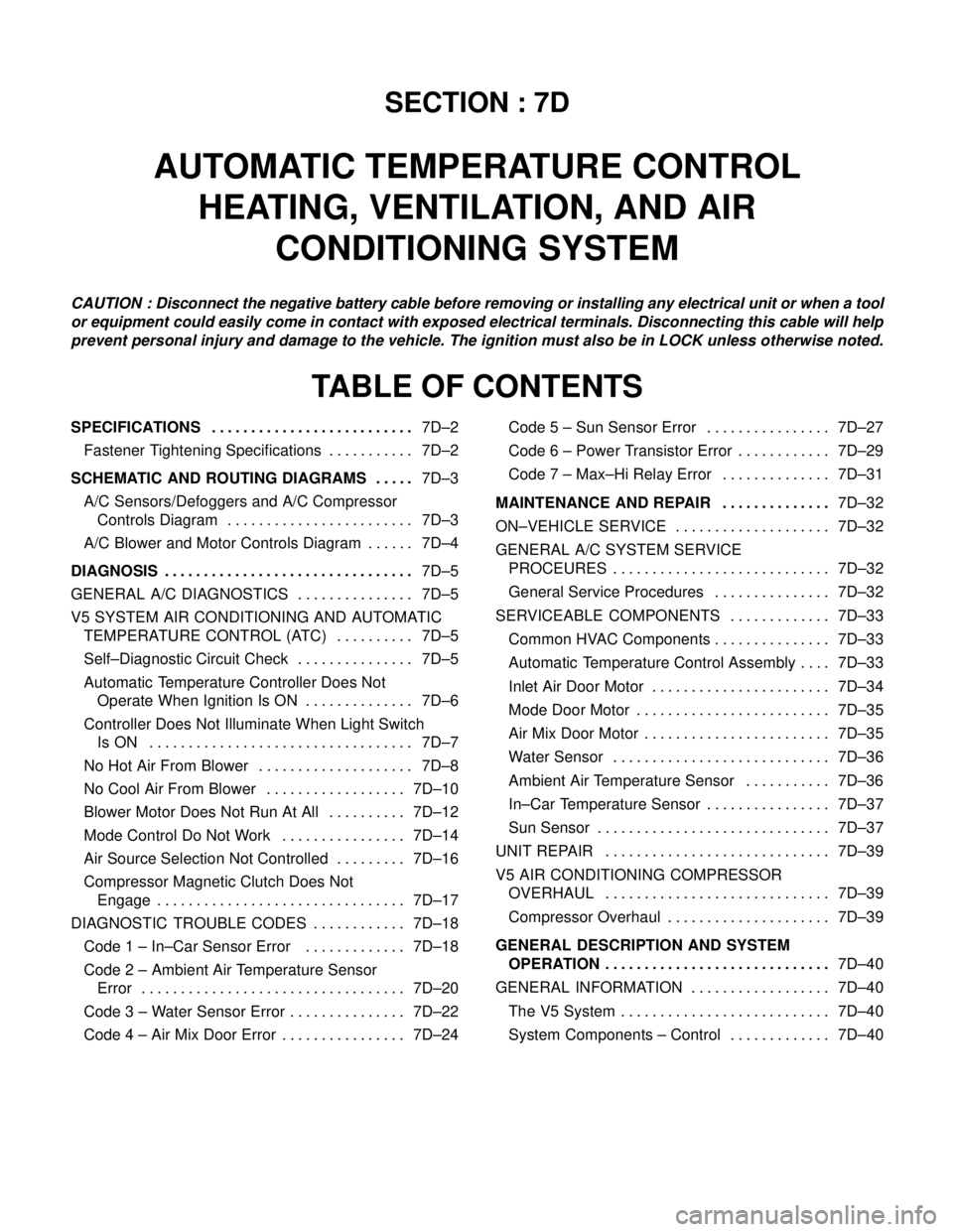
SECTION : 7D
AUTOMATIC TEMPERATURE CONTROL
HEATING, VENTILATION, AND AIR
CONDITIONING SYSTEM
CAUTION : Disconnect the negative battery cable before removing or installing any electrical unit or when a tool
or equipment could easily come in contact with exposed electrical terminals. Disconnecting this cable will help
prevent personal injury and damage to the vehicle. The ignition must also be in LOCK unless otherwise noted.
TABLE OF CONTENTS
SPECIFICATIONS7D–2 . . . . . . . . . . . . . . . . . . . . . . . . . .
Fastener Tightening Specifications 7D–2. . . . . . . . . . .
SCHEMATIC AND ROUTING DIAGRAMS7D–3 . . . . .
A/C Sensors/Defoggers and A/C Compressor
Controls Diagram 7D–3. . . . . . . . . . . . . . . . . . . . . . . .
A/C Blower and Motor Controls Diagram 7D–4. . . . . .
DIAGNOSIS7D–5 . . . . . . . . . . . . . . . . . . . . . . . . . . . . . . . .
GENERAL A/C DIAGNOSTICS 7D–5. . . . . . . . . . . . . . .
V5 SYSTEM AIR CONDITIONING AND AUTOMATIC
TEMPERATURE CONTROL (ATC) 7D–5. . . . . . . . . .
Self–Diagnostic Circuit Check 7D–5. . . . . . . . . . . . . . .
Automatic Temperature Controller Does Not
Operate When Ignition Is ON 7D–6. . . . . . . . . . . . . .
Controller Does Not Illuminate When Light Switch
Is ON 7D–7. . . . . . . . . . . . . . . . . . . . . . . . . . . . . . . . . .
No Hot Air From Blower 7D–8. . . . . . . . . . . . . . . . . . . .
No Cool Air From Blower 7D–10. . . . . . . . . . . . . . . . . .
Blower Motor Does Not Run At All 7D–12. . . . . . . . . .
Mode Control Do Not Work 7D–14. . . . . . . . . . . . . . . .
Air Source Selection Not Controlled 7D–16. . . . . . . . .
Compressor Magnetic Clutch Does Not
Engage 7D–17. . . . . . . . . . . . . . . . . . . . . . . . . . . . . . . .
DIAGNOSTIC TROUBLE CODES 7D–18. . . . . . . . . . . .
Code 1 – In–Car Sensor Error 7D–18. . . . . . . . . . . . .
Code 2 – Ambient Air Temperature Sensor
Error 7D–20. . . . . . . . . . . . . . . . . . . . . . . . . . . . . . . . . .
Code 3 – Water Sensor Error 7D–22. . . . . . . . . . . . . . .
Code 4 – Air Mix Door Error 7D–24. . . . . . . . . . . . . . . . Code 5 – Sun Sensor Error 7D–27. . . . . . . . . . . . . . . .
Code 6 – Power Transistor Error 7D–29. . . . . . . . . . . .
Code 7 – Max–Hi Relay Error 7D–31. . . . . . . . . . . . . .
MAINTENANCE AND REPAIR7D–32 . . . . . . . . . . . . . .
ON–VEHICLE SERVICE 7D–32. . . . . . . . . . . . . . . . . . . .
GENERAL A/C SYSTEM SERVICE
PROCEURES 7D–32. . . . . . . . . . . . . . . . . . . . . . . . . . . .
General Service Procedures 7D–32. . . . . . . . . . . . . . .
SERVICEABLE COMPONENTS 7D–33. . . . . . . . . . . . .
Common HVAC Components 7D–33. . . . . . . . . . . . . . .
Automatic Temperature Control Assembly 7D–33. . . .
Inlet Air Door Motor 7D–34. . . . . . . . . . . . . . . . . . . . . . .
Mode Door Motor 7D–35. . . . . . . . . . . . . . . . . . . . . . . . .
Air Mix Door Motor 7D–35. . . . . . . . . . . . . . . . . . . . . . . .
Water Sensor 7D–36. . . . . . . . . . . . . . . . . . . . . . . . . . . .
Ambient Air Temperature Sensor 7D–36. . . . . . . . . . .
In–Car Temperature Sensor 7D–37. . . . . . . . . . . . . . . .
Sun Sensor 7D–37. . . . . . . . . . . . . . . . . . . . . . . . . . . . . .
UNIT REPAIR 7D–39. . . . . . . . . . . . . . . . . . . . . . . . . . . . .
V5 AIR CONDITIONING COMPRESSOR
OVERHAUL 7D–39. . . . . . . . . . . . . . . . . . . . . . . . . . . . .
Compressor Overhaul 7D–39. . . . . . . . . . . . . . . . . . . . .
GENERAL DESCRIPTION AND SYSTEM
OPERATION7D–40 . . . . . . . . . . . . . . . . . . . . . . . . . . . . .
GENERAL INFORMATION 7D–40. . . . . . . . . . . . . . . . . .
The V5 System 7D–40. . . . . . . . . . . . . . . . . . . . . . . . . . .
System Components – Control 7D–40. . . . . . . . . . . . .