Page 217 of 2643
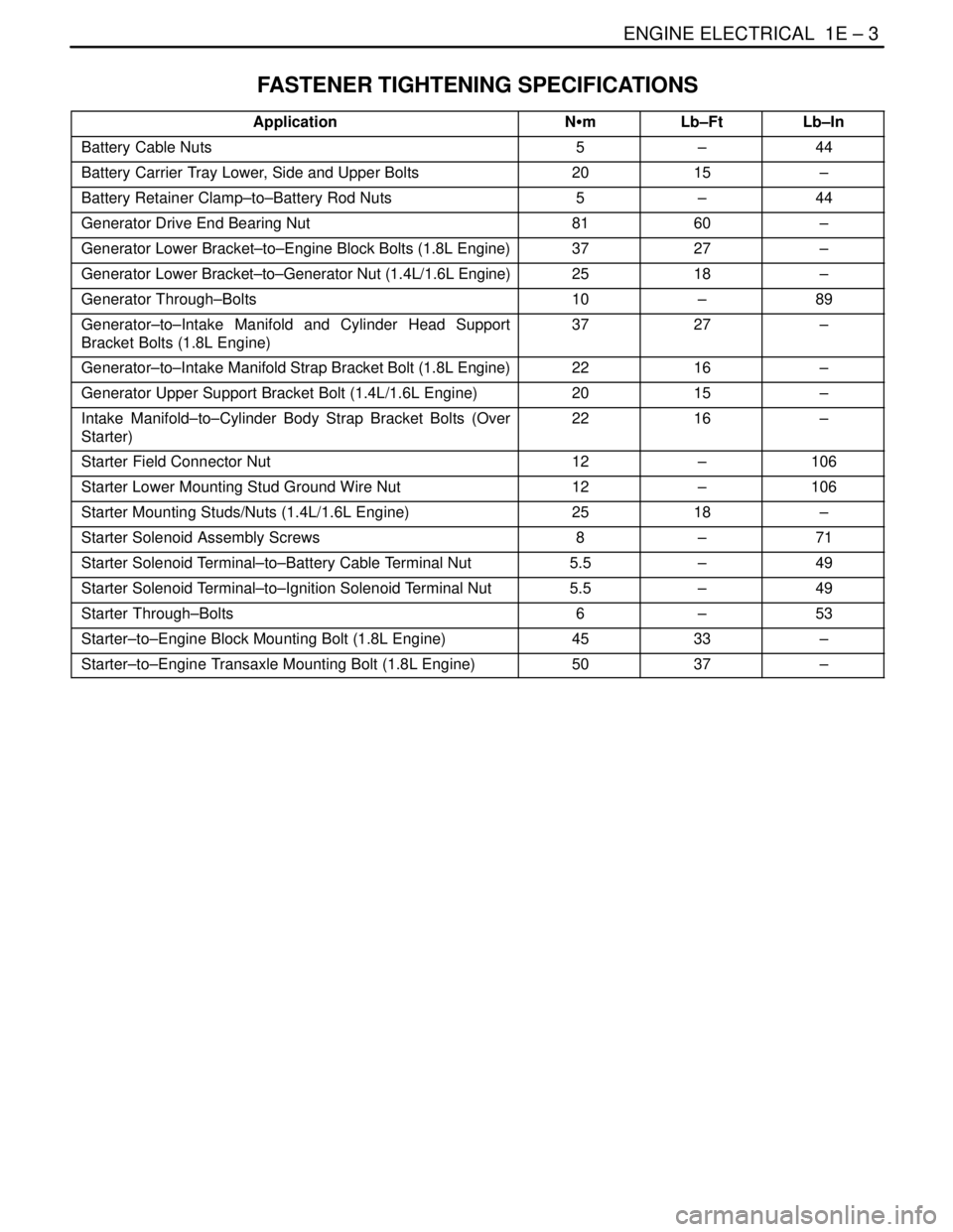
ENGINE ELECTRICAL 1E – 3
DAEWOO V–121 BL4
FASTENER TIGHTENING SPECIFICATIONS
ApplicationNSmLb–FtLb–In
Battery Cable Nuts5–44
Battery Carrier Tray Lower, Side and Upper Bolts2015–
Battery Retainer Clamp–to–Battery Rod Nuts5–44
Generator Drive End Bearing Nut8160–
Generator Lower Bracket–to–Engine Block Bolts (1.8L Engine)3727–
Generator Lower Bracket–to–Generator Nut (1.4L/1.6L Engine)2518–
Generator Through–Bolts10–89
Generator–to–Intake Manifold and Cylinder Head Support
Bracket Bolts (1.8L Engine)3727–
Generator–to–Intake Manifold Strap Bracket Bolt (1.8L Engine)2216–
Generator Upper Support Bracket Bolt (1.4L/1.6L Engine)2015–
Intake Manifold–to–Cylinder Body Strap Bracket Bolts (Over
Starter)2216–
Starter Field Connector Nut12–106
Starter Lower Mounting Stud Ground Wire Nut12–106
Starter Mounting Studs/Nuts (1.4L/1.6L Engine)2518–
Starter Solenoid Assembly Screws8–71
Starter Solenoid Terminal–to–Battery Cable Terminal Nut5.5–49
Starter Solenoid Terminal–to–Ignition Solenoid Terminal Nut5.5–49
Starter Through–Bolts6–53
Starter–to–Engine Block Mounting Bolt (1.8L Engine)4533–
Starter–to–Engine Transaxle Mounting Bolt (1.8L Engine)5037–
Page 218 of 2643
1E – 4IENGINE ELECTRICAL
DAEWOO V–121 BL4
SCHEMATIC AND ROUTING DIAGRAMS
STARTIMG SYSTEM
Page 219 of 2643
ENGINE ELECTRICAL 1E – 5
DAEWOO V–121 BL4
CHARGING SYSTEM
Page 220 of 2643
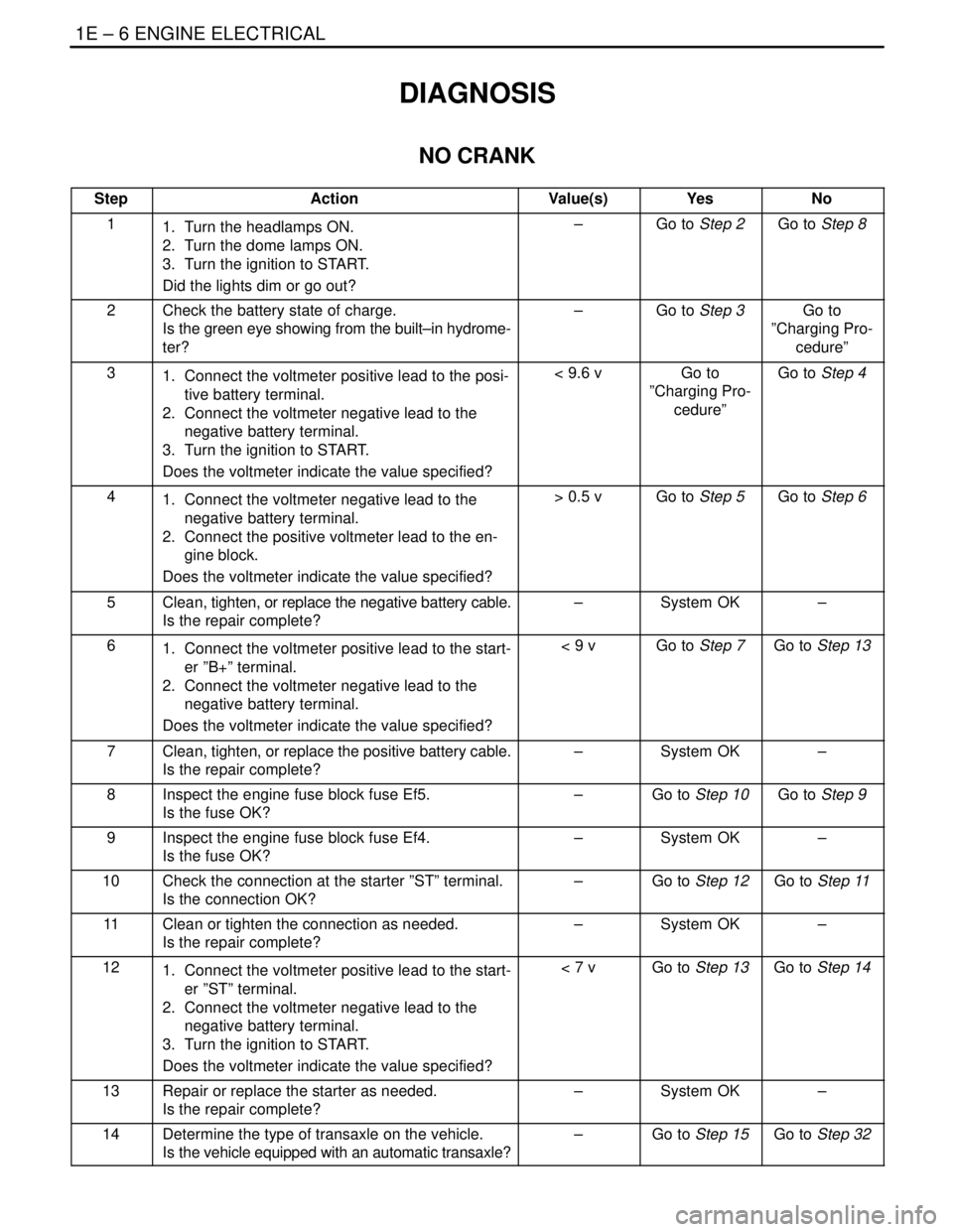
1E – 6IENGINE ELECTRICAL
DAEWOO V–121 BL4
DIAGNOSIS
NO CRANK
StepActionValue(s)YesNo
11. Turn the headlamps ON.
2. Turn the dome lamps ON.
3. Turn the ignition to START.
Did the lights dim or go out?–Go to Step 2Go to Step 8
2Check the battery state of charge.
Is the green eye showing from the built–in hydrome-
ter?–Go to Step 3Go to
”Charging Pro-
cedure”
31. Connect the voltmeter positive lead to the posi-
tive battery terminal.
2. Connect the voltmeter negative lead to the
negative battery terminal.
3. Turn the ignition to START.
Does the voltmeter indicate the value specified?< 9.6 vGo to
”Charging Pro-
cedure”Go to Step 4
41. Connect the voltmeter negative lead to the
negative battery terminal.
2. Connect the positive voltmeter lead to the en-
gine block.
Does the voltmeter indicate the value specified?> 0.5 vGo to Step 5Go to Step 6
5Clean, tighten, or replace the negative battery cable.
Is the repair complete?–System OK–
61. Connect the voltmeter positive lead to the start-
er ”B+” terminal.
2. Connect the voltmeter negative lead to the
negative battery terminal.
Does the voltmeter indicate the value specified?< 9 vGo to Step 7Go to Step 13
7Clean, tighten, or replace the positive battery cable.
Is the repair complete?–System OK–
8Inspect the engine fuse block fuse Ef5.
Is the fuse OK?–Go to Step 10Go to Step 9
9Inspect the engine fuse block fuse Ef4.
Is the fuse OK?–System OK–
10Check the connection at the starter ”ST” terminal.
Is the connection OK?–Go to Step 12Go to Step 11
11Clean or tighten the connection as needed.
Is the repair complete?–System OK–
121. Connect the voltmeter positive lead to the start-
er ”ST” terminal.
2. Connect the voltmeter negative lead to the
negative battery terminal.
3. Turn the ignition to START.
Does the voltmeter indicate the value specified?< 7 vGo to Step 13Go to Step 14
13Repair or replace the starter as needed.
Is the repair complete?–System OK–
14Determine the type of transaxle on the vehicle.
Is the vehicle equipped with an automatic transaxle?–Go to Step 15Go to Step 32
Page 221 of 2643
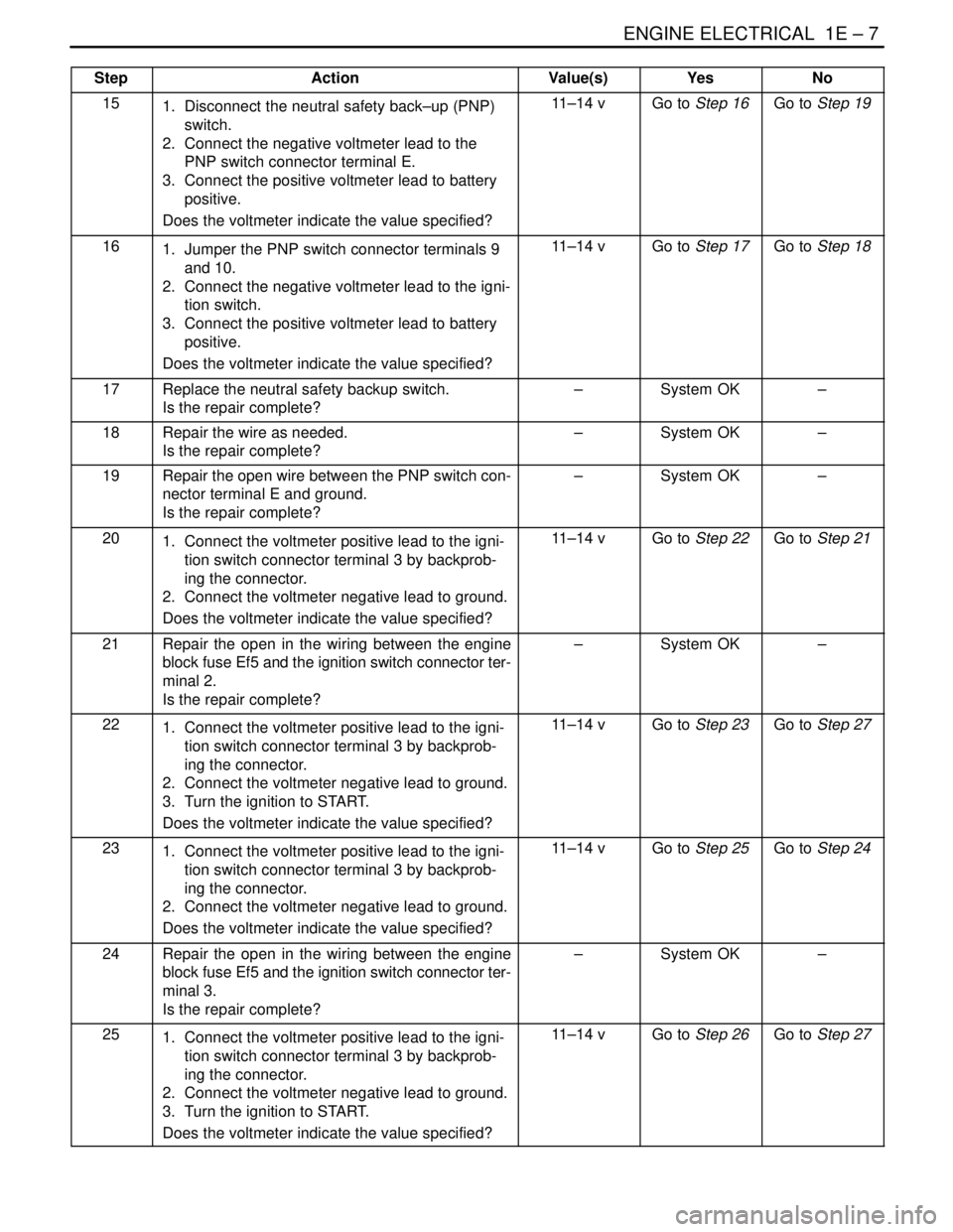
ENGINE ELECTRICAL 1E – 7
DAEWOO V–121 BL4
StepNo Yes Value(s) Action
151. Disconnect the neutral safety back–up (PNP)
switch.
2. Connect the negative voltmeter lead to the
PNP switch connector terminal E.
3. Connect the positive voltmeter lead to battery
positive.
Does the voltmeter indicate the value specified?11–14 vGo to Step 16Go to Step 19
161. Jumper the PNP switch connector terminals 9
and 10.
2. Connect the negative voltmeter lead to the igni-
tion switch.
3. Connect the positive voltmeter lead to battery
positive.
Does the voltmeter indicate the value specified?11–14 vGo to Step 17Go to Step 18
17Replace the neutral safety backup switch.
Is the repair complete?–System OK–
18Repair the wire as needed.
Is the repair complete?–System OK–
19Repair the open wire between the PNP switch con-
nector terminal E and ground.
Is the repair complete?–System OK–
201. Connect the voltmeter positive lead to the igni-
tion switch connector terminal 3 by backprob-
ing the connector.
2. Connect the voltmeter negative lead to ground.
Does the voltmeter indicate the value specified?11–14 vGo to Step 22Go to Step 21
21Repair the open in the wiring between the engine
block fuse Ef5 and the ignition switch connector ter-
minal 2.
Is the repair complete?–System OK–
221. Connect the voltmeter positive lead to the igni-
tion switch connector terminal 3 by backprob-
ing the connector.
2. Connect the voltmeter negative lead to ground.
3. Turn the ignition to START.
Does the voltmeter indicate the value specified?11–14 vGo to Step 23Go to Step 27
231. Connect the voltmeter positive lead to the igni-
tion switch connector terminal 3 by backprob-
ing the connector.
2. Connect the voltmeter negative lead to ground.
Does the voltmeter indicate the value specified?11–14 vGo to Step 25Go to Step 24
24Repair the open in the wiring between the engine
block fuse Ef5 and the ignition switch connector ter-
minal 3.
Is the repair complete?–System OK–
251. Connect the voltmeter positive lead to the igni-
tion switch connector terminal 3 by backprob-
ing the connector.
2. Connect the voltmeter negative lead to ground.
3. Turn the ignition to START.
Does the voltmeter indicate the value specified?11–14 vGo to Step 26Go to Step 27
Page 222 of 2643
1E – 8IENGINE ELECTRICAL
DAEWOO V–121 BL4
StepNo Yes Value(s) Action
26Repair the open in the wiring between the ignition
switch connector terminal 3 and the starter ”ST” ter-
minal.
Is the repair complete?–System OK–
27Replace the ignition switch.
Is the repair complete?–System OK–
Page 223 of 2643
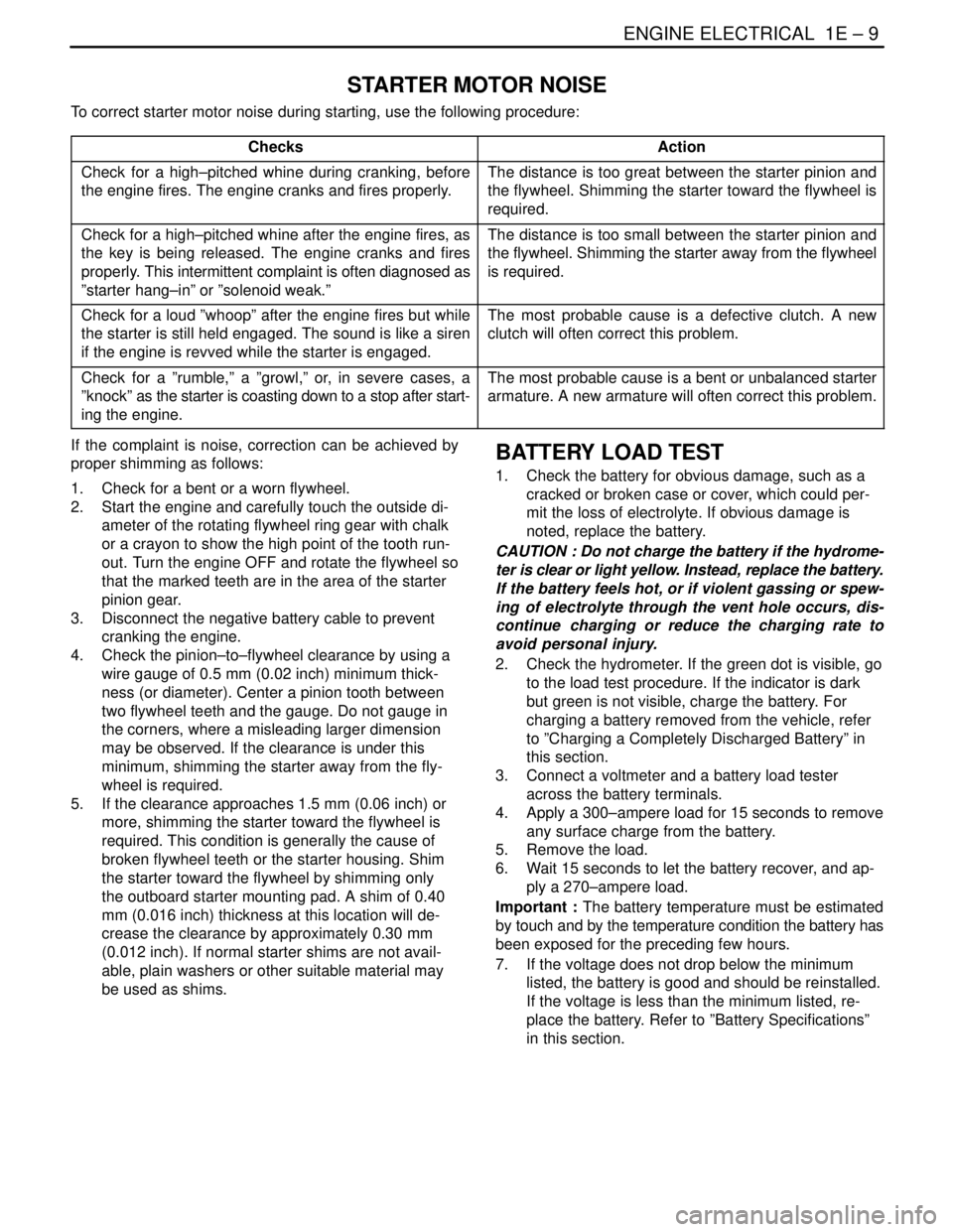
ENGINE ELECTRICAL 1E – 9
DAEWOO V–121 BL4
STARTER MOTOR NOISE
To correct starter motor noise during starting, use the following procedure:
Checks
Action
Check for a high–pitched whine during cranking, before
the engine fires. The engine cranks and fires properly.The distance is too great between the starter pinion and
the flywheel. Shimming the starter toward the flywheel is
required.
Check for a high–pitched whine after the engine fires, as
the key is being released. The engine cranks and fires
properly. This intermittent complaint is often diagnosed as
”starter hang–in” or ”solenoid weak.”The distance is too small between the starter pinion and
the flywheel. Shimming the starter away from the flywheel
is required.
Check for a loud ”whoop” after the engine fires but while
the starter is still held engaged. The sound is like a siren
if the engine is revved while the starter is engaged.The most probable cause is a defective clutch. A new
clutch will often correct this problem.
Check for a ”rumble,” a ”growl,” or, in severe cases, a
”knock” as the starter is coasting down to a stop after start-
ing the engine.The most probable cause is a bent or unbalanced starter
armature. A new armature will often correct this problem.
If the complaint is noise, correction can be achieved by
proper shimming as follows:
1. Check for a bent or a worn flywheel.
2. Start the engine and carefully touch the outside di-
ameter of the rotating flywheel ring gear with chalk
or a crayon to show the high point of the tooth run-
out. Turn the engine OFF and rotate the flywheel so
that the marked teeth are in the area of the starter
pinion gear.
3. Disconnect the negative battery cable to prevent
cranking the engine.
4. Check the pinion–to–flywheel clearance by using a
wire gauge of 0.5 mm (0.02 inch) minimum thick-
ness (or diameter). Center a pinion tooth between
two flywheel teeth and the gauge. Do not gauge in
the corners, where a misleading larger dimension
may be observed. If the clearance is under this
minimum, shimming the starter away from the fly-
wheel is required.
5. If the clearance approaches 1.5 mm (0.06 inch) or
more, shimming the starter toward the flywheel is
required. This condition is generally the cause of
broken flywheel teeth or the starter housing. Shim
the starter toward the flywheel by shimming only
the outboard starter mounting pad. A shim of 0.40
mm (0.016 inch) thickness at this location will de-
crease the clearance by approximately 0.30 mm
(0.012 inch). If normal starter shims are not avail-
able, plain washers or other suitable material may
be used as shims.BATTERY LOAD TEST
1. Check the battery for obvious damage, such as a
cracked or broken case or cover, which could per-
mit the loss of electrolyte. If obvious damage is
noted, replace the battery.
CAUTION : Do not charge the battery if the hydrome-
ter is clear or light yellow. Instead, replace the battery.
If the battery feels hot, or if violent gassing or spew-
ing of electrolyte through the vent hole occurs, dis-
continue charging or reduce the charging rate to
avoid personal injury.
2. Check the hydrometer. If the green dot is visible, go
to the load test procedure. If the indicator is dark
but green is not visible, charge the battery. For
charging a battery removed from the vehicle, refer
to ”Charging a Completely Discharged Battery” in
this section.
3. Connect a voltmeter and a battery load tester
across the battery terminals.
4. Apply a 300–ampere load for 15 seconds to remove
any surface charge from the battery.
5. Remove the load.
6. Wait 15 seconds to let the battery recover, and ap-
ply a 270–ampere load.
Important : The battery temperature must be estimated
by touch and by the temperature condition the battery has
been exposed for the preceding few hours.
7. If the voltage does not drop below the minimum
listed, the battery is good and should be reinstalled.
If the voltage is less than the minimum listed, re-
place the battery. Refer to ”Battery Specifications”
in this section.
Page 224 of 2643
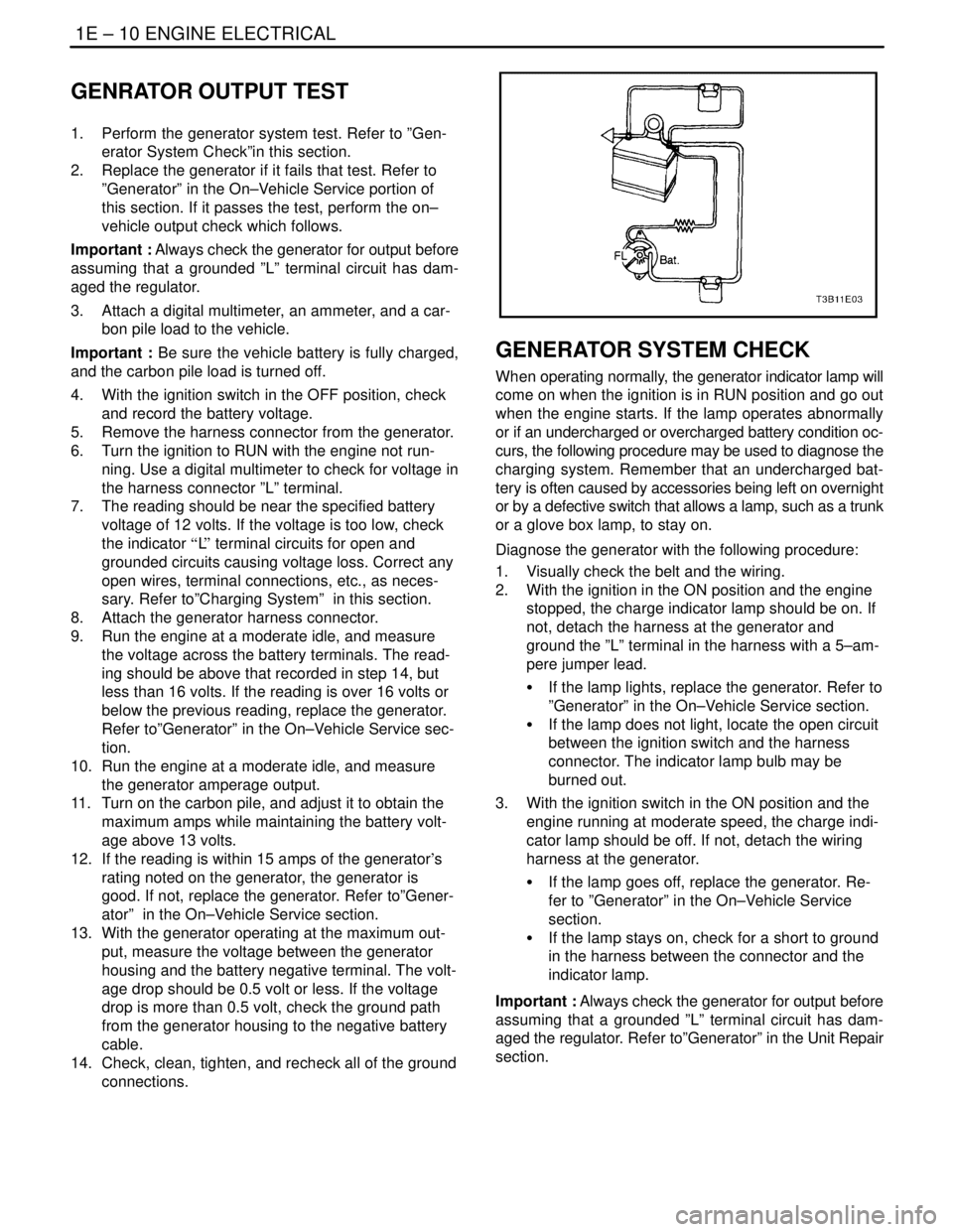
1E – 10IENGINE ELECTRICAL
DAEWOO V–121 BL4
GENRATOR OUTPUT TEST
1. Perform the generator system test. Refer to ”Gen-
erator System Check”in this section.
2. Replace the generator if it fails that test. Refer to
”Generator” in the On–Vehicle Service portion of
this section. If it passes the test, perform the on–
vehicle output check which follows.
Important : Always check the generator for output before
assuming that a grounded ”L” terminal circuit has dam-
aged the regulator.
3. Attach a digital multimeter, an ammeter, and a car-
bon pile load to the vehicle.
Important : Be sure the vehicle battery is fully charged,
and the carbon pile load is turned off.
4. With the ignition switch in the OFF position, check
and record the battery voltage.
5. Remove the harness connector from the generator.
6. Turn the ignition to RUN with the engine not run-
ning. Use a digital multimeter to check for voltage in
the harness connector ”L” terminal.
7. The reading should be near the specified battery
voltage of 12 volts. If the voltage is too low, check
the indicator L" terminal circuits for open and
grounded circuits causing voltage loss. Correct any
open wires, terminal connections, etc., as neces-
sary. Refer to”Charging System” in this section.
8. Attach the generator harness connector.
9. Run the engine at a moderate idle, and measure
the voltage across the battery terminals. The read-
ing should be above that recorded in step 14, but
less than 16 volts. If the reading is over 16 volts or
below the previous reading, replace the generator.
Refer to”Generator” in the On–Vehicle Service sec-
tion.
10. Run the engine at a moderate idle, and measure
the generator amperage output.
11. Turn on the carbon pile, and adjust it to obtain the
maximum amps while maintaining the battery volt-
age above 13 volts.
12. If the reading is within 15 amps of the generator’s
rating noted on the generator, the generator is
good. If not, replace the generator. Refer to”Gener-
ator” in the On–Vehicle Service section.
13. With the generator operating at the maximum out-
put, measure the voltage between the generator
housing and the battery negative terminal. The volt-
age drop should be 0.5 volt or less. If the voltage
drop is more than 0.5 volt, check the ground path
from the generator housing to the negative battery
cable.
14. Check, clean, tighten, and recheck all of the ground
connections.
GENERATOR SYSTEM CHECK
When operating normally, the generator indicator lamp will
come on when the ignition is in RUN position and go out
when the engine starts. If the lamp operates abnormally
or if an undercharged or overcharged battery condition oc-
curs, the following procedure may be used to diagnose the
charging system. Remember that an undercharged bat-
tery is often caused by accessories being left on overnight
or by a defective switch that allows a lamp, such as a trunk
or a glove box lamp, to stay on.
Diagnose the generator with the following procedure:
1. Visually check the belt and the wiring.
2. With the ignition in the ON position and the engine
stopped, the charge indicator lamp should be on. If
not, detach the harness at the generator and
ground the ”L” terminal in the harness with a 5–am-
pere jumper lead.
S If the lamp lights, replace the generator. Refer to
”Generator” in the On–Vehicle Service section.
S If the lamp does not light, locate the open circuit
between the ignition switch and the harness
connector. The indicator lamp bulb may be
burned out.
3. With the ignition switch in the ON position and the
engine running at moderate speed, the charge indi-
cator lamp should be off. If not, detach the wiring
harness at the generator.
S If the lamp goes off, replace the generator. Re-
fer to ”Generator” in the On–Vehicle Service
section.
S If the lamp stays on, check for a short to ground
in the harness between the connector and the
indicator lamp.
Important : Always check the generator for output before
assuming that a grounded ”L” terminal circuit has dam-
aged the regulator. Refer to”Generator” in the Unit Repair
section.