Page 1401 of 2643
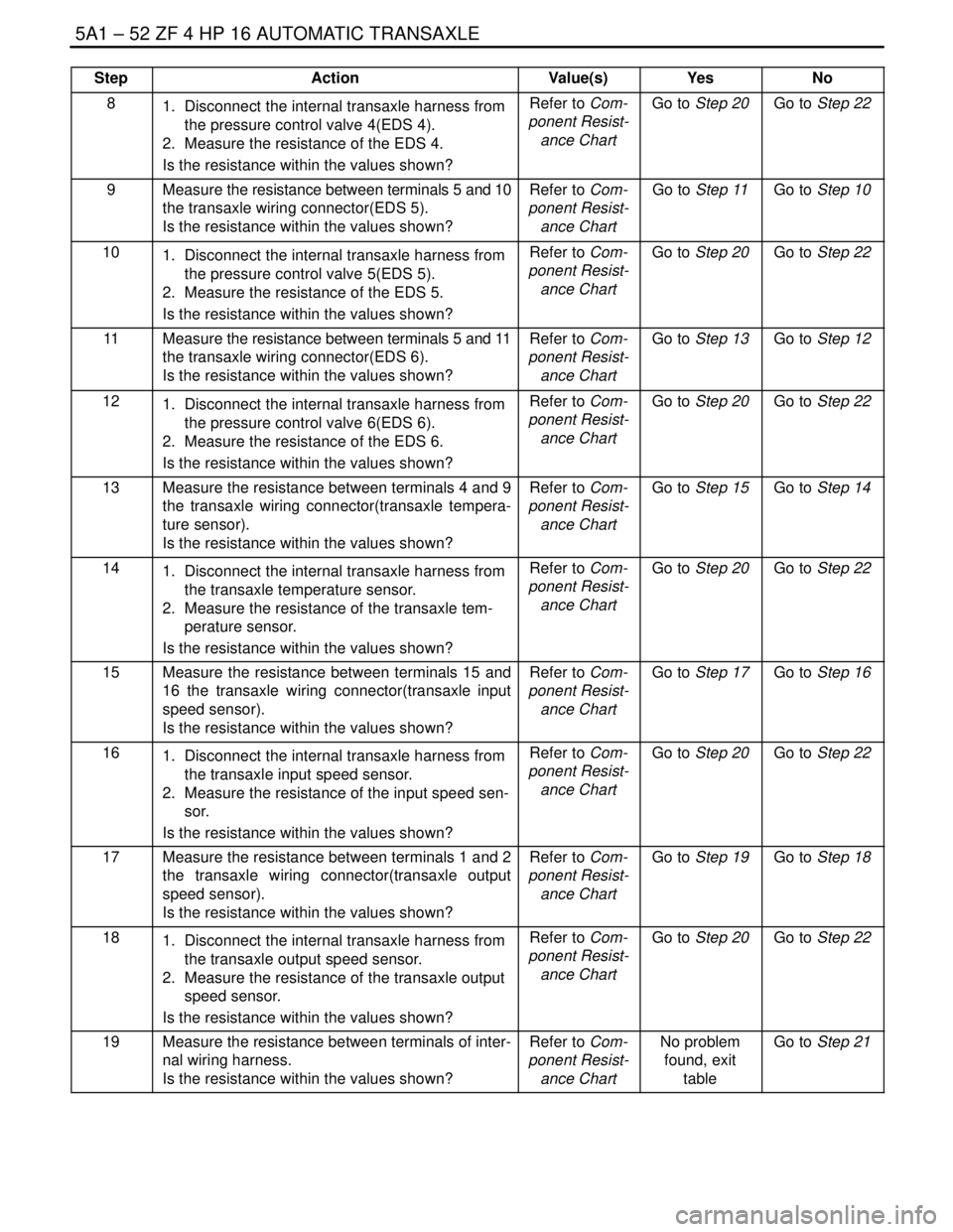
5A1 – 52IZF 4 HP 16 AUTOMATIC TRANSAXLE
DAEWOO V–121 BL4
StepNo Yes Value(s) Action
81. Disconnect the internal transaxle harness from
the pressure control valve 4(EDS 4).
2. Measure the resistance of the EDS 4.
Is the resistance within the values shown?Refer to Com-
ponent Resist-
ance ChartGo to Step 20Go to Step 22
9Measure the resistance between terminals 5 and 10
the transaxle wiring connector(EDS 5).
Is the resistance within the values shown?Refer to Com-
ponent Resist-
ance ChartGo to Step 11Go to Step 10
101. Disconnect the internal transaxle harness from
the pressure control valve 5(EDS 5).
2. Measure the resistance of the EDS 5.
Is the resistance within the values shown?Refer to Com-
ponent Resist-
ance ChartGo to Step 20Go to Step 22
11Measure the resistance between terminals 5 and 11
the transaxle wiring connector(EDS 6).
Is the resistance within the values shown?Refer to Com-
ponent Resist-
ance ChartGo to Step 13Go to Step 12
121. Disconnect the internal transaxle harness from
the pressure control valve 6(EDS 6).
2. Measure the resistance of the EDS 6.
Is the resistance within the values shown?Refer to Com-
ponent Resist-
ance ChartGo to Step 20Go to Step 22
13Measure the resistance between terminals 4 and 9
the transaxle wiring connector(transaxle tempera-
ture sensor).
Is the resistance within the values shown?Refer to Com-
ponent Resist-
ance ChartGo to Step 15Go to Step 14
141. Disconnect the internal transaxle harness from
the transaxle temperature sensor.
2. Measure the resistance of the transaxle tem-
perature sensor.
Is the resistance within the values shown?Refer to Com-
ponent Resist-
ance ChartGo to Step 20Go to Step 22
15Measure the resistance between terminals 15 and
16 the transaxle wiring connector(transaxle input
speed sensor).
Is the resistance within the values shown?Refer to Com-
ponent Resist-
ance ChartGo to Step 17Go to Step 16
161. Disconnect the internal transaxle harness from
the transaxle input speed sensor.
2. Measure the resistance of the input speed sen-
sor.
Is the resistance within the values shown?Refer to Com-
ponent Resist-
ance ChartGo to Step 20Go to Step 22
17Measure the resistance between terminals 1 and 2
the transaxle wiring connector(transaxle output
speed sensor).
Is the resistance within the values shown?Refer to Com-
ponent Resist-
ance ChartGo to Step 19Go to Step 18
181. Disconnect the internal transaxle harness from
the transaxle output speed sensor.
2. Measure the resistance of the transaxle output
speed sensor.
Is the resistance within the values shown?Refer to Com-
ponent Resist-
ance ChartGo to Step 20Go to Step 22
19Measure the resistance between terminals of inter-
nal wiring harness.
Is the resistance within the values shown?Refer to Com-
ponent Resist-
ance ChartNo problem
found, exit
tableGo to Step 21
Page 1402 of 2643
ZF 4 HP 16 AUTOMATIC TRANSAXLE 5A1 – 53
DAEWOO V–121 BL4
StepNo Yes Value(s) Action
20Inspect for resistance:
S Ispect the transaxle wiring for poor electrical
connections at the transaxle.
S Look for possible bent, backed out, deformed
of damaged terminals.
Check for weak terminal tension.–Verify repair
and Go to Step
12No problem
found, exit
table
21Replace the internal wiring harness.
Is the replacement complete.–No problem
found, exit
table–
22Replace the component.
Is the replacement complete.–No problem
found, exit
table–
Page 1403 of 2643
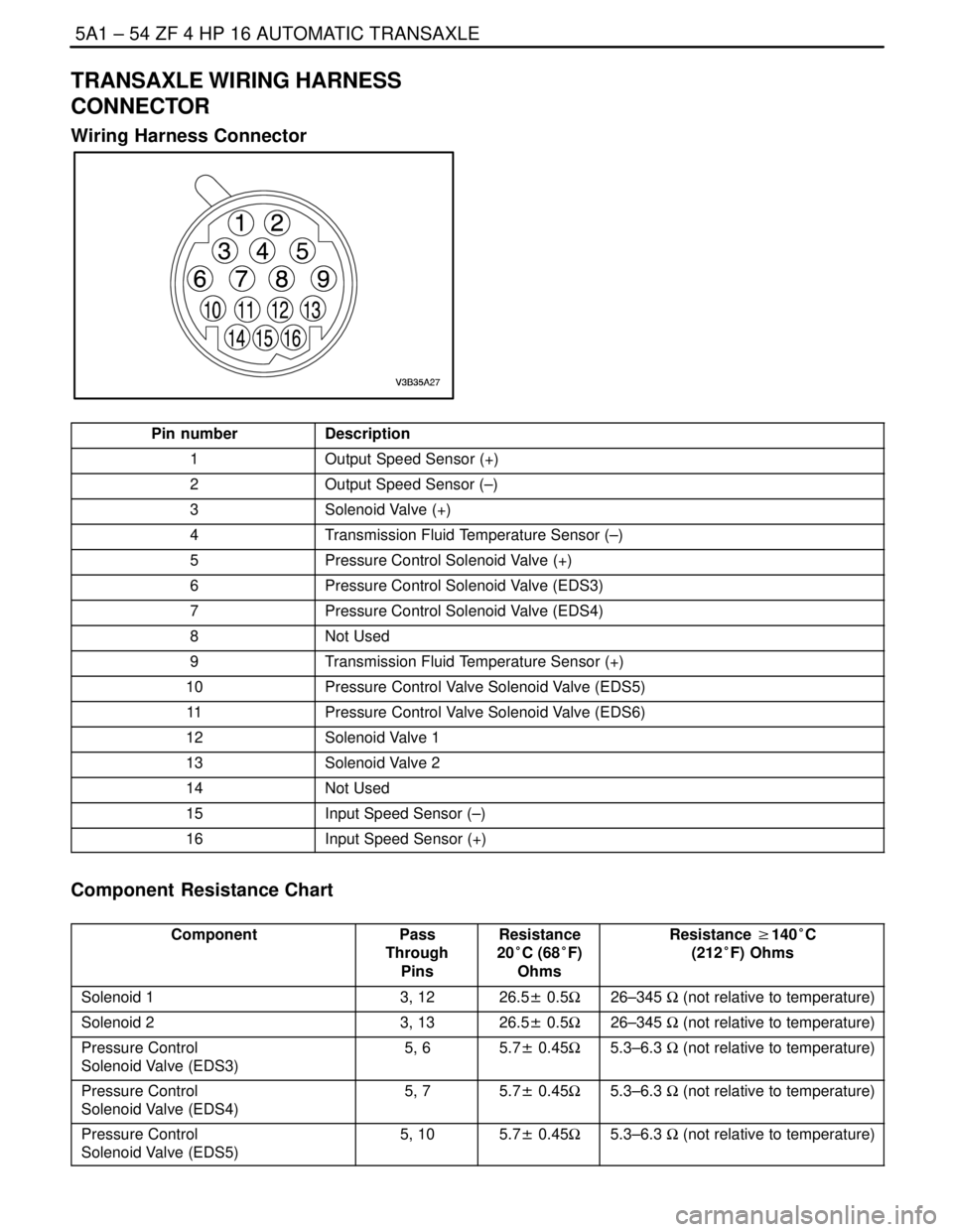
5A1 – 54IZF 4 HP 16 AUTOMATIC TRANSAXLE
DAEWOO V–121 BL4
TRANSAXLE WIRING HARNESS
CONNECTOR
Wiring Harness Connector
Pin numberDescription
1Output Speed Sensor (+)
2Output Speed Sensor (–)
3Solenoid Valve (+)
4Transmission Fluid Temperature Sensor (–)
5Pressure Control Solenoid Valve (+)
6Pressure Control Solenoid Valve (EDS3)
7Pressure Control Solenoid Valve (EDS4)
8Not Used
9Transmission Fluid Temperature Sensor (+)
10Pressure Control Valve Solenoid Valve (EDS5)
11Pressure Control Valve Solenoid Valve (EDS6)
12Solenoid Valve 1
13Solenoid Valve 2
14Not Used
15Input Speed Sensor (–)
16Input Speed Sensor (+)
Component Resistance Chart
ComponentPass
Through
PinsResistance
20°C (68°F)
OhmsResistance w140°C
(212°F) Ohms
Solenoid 13, 1226.5± 0.5Ω26–345 Ω (not relative to temperature)
Solenoid 23, 1326.5± 0.5Ω26–345 Ω (not relative to temperature)
Pressure Control
Solenoid Valve (EDS3)5, 65.7± 0.45Ω5.3–6.3 Ω (not relative to temperature)
Pressure Control
Solenoid Valve (EDS4)5, 75.7± 0.45Ω5.3–6.3 Ω (not relative to temperature)
Pressure Control
Solenoid Valve (EDS5)5, 105.7± 0.45Ω5.3–6.3 Ω (not relative to temperature)
Page 1404 of 2643
ZF 4 HP 16 AUTOMATIC TRANSAXLE 5A1 – 55
DAEWOO V–121 BL4
Component Resistance w140°C
(212°F) Ohms Resistance
20°C (68°F)
Ohms Pass
Through
Pins
Pressure Control
Solenoid Valve (EDS6)5, 115.7± 0.45Ω5.3–6.3 Ω (not relative to temperature)
Transaxle Temperature Sensor*4, 9980–1,000 Ω
Input Speed Sensor15, 16830 ± 5 Ω788–871 Ω (not relative to tempera-
ture)
Output Speed Sensor*1, 2
* The resistance of the transaxle is necessarily dependent on the temperature.
Page 1405 of 2643
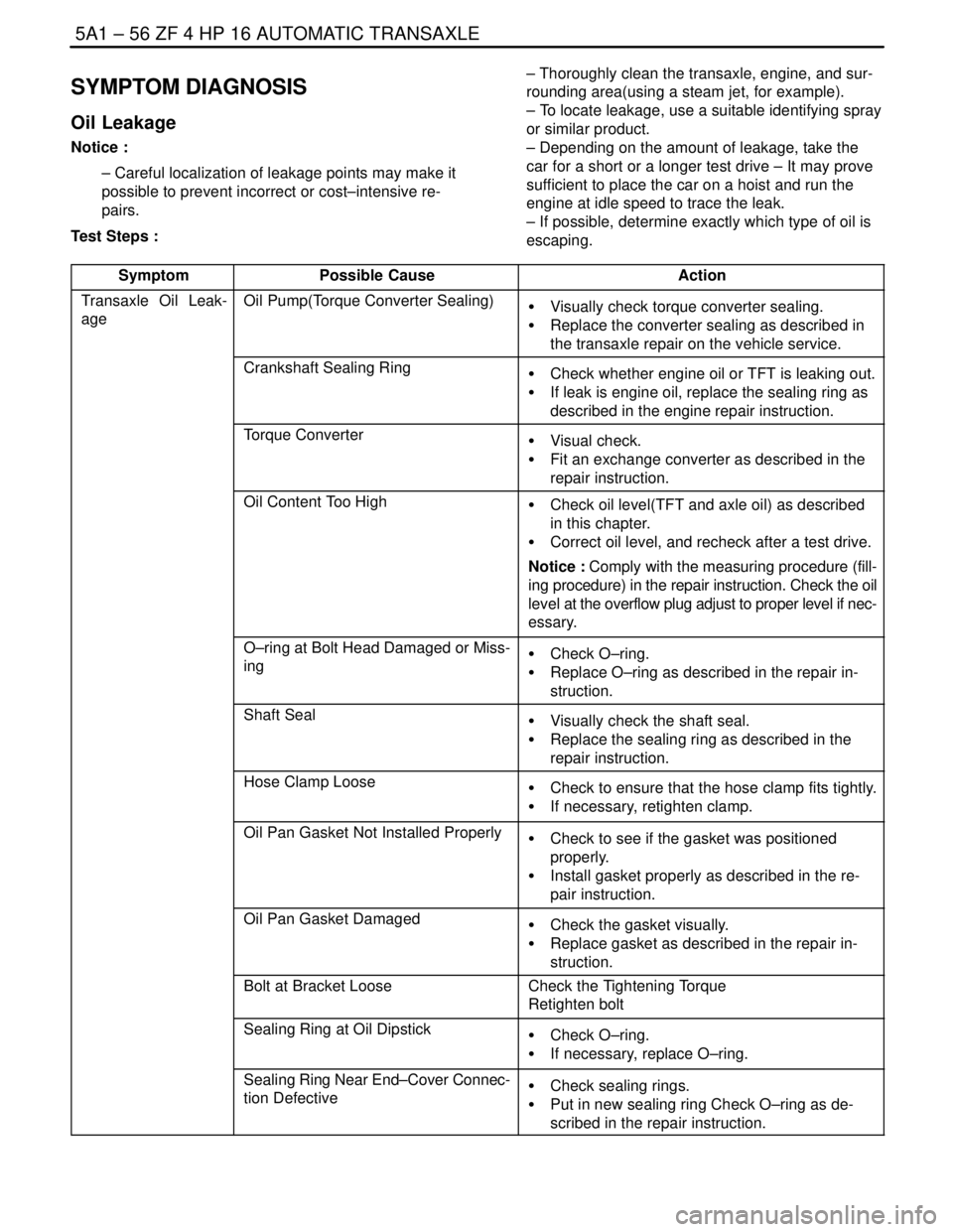
5A1 – 56IZF 4 HP 16 AUTOMATIC TRANSAXLE
DAEWOO V–121 BL4
SYMPTOM DIAGNOSIS
Oil Leakage
Notice :
– Careful localization of leakage points may make it
possible to prevent incorrect or cost–intensive re-
pairs.
Test Steps :– Thoroughly clean the transaxle, engine, and sur-
rounding area(using a steam jet, for example).
– To locate leakage, use a suitable identifying spray
or similar product.
– Depending on the amount of leakage, take the
car for a short or a longer test drive – It may prove
sufficient to place the car on a hoist and run the
engine at idle speed to trace the leak.
– If possible, determine exactly which type of oil is
escaping.
Symptom
Possible CauseAction
Transaxle Oil Leak-
ageOil Pump(Torque Converter Sealing)S Visually check torque converter sealing.
S Replace the converter sealing as described in
the transaxle repair on the vehicle service.
Crankshaft Sealing RingS Check whether engine oil or TFT is leaking out.
S If leak is engine oil, replace the sealing ring as
described in the engine repair instruction.
Torque ConverterS Visual check.
S Fit an exchange converter as described in the
repair instruction.
Oil Content Too HighS Check oil level(TFT and axle oil) as described
in this chapter.
S Correct oil level, and recheck after a test drive.
Notice : Comply with the measuring procedure (fill-
ing procedure) in the repair instruction. Check the oil
level at the overflow plug adjust to proper level if nec-
essary.
O–ring at Bolt Head Damaged or Miss-
ingS Check O–ring.
S Replace O–ring as described in the repair in-
struction.
Shaft SealS Visually check the shaft seal.
S Replace the sealing ring as described in the
repair instruction.
Hose Clamp LooseS Check to ensure that the hose clamp fits tightly.
S If necessary, retighten clamp.
Oil Pan Gasket Not Installed ProperlyS Check to see if the gasket was positioned
properly.
S Install gasket properly as described in the re-
pair instruction.
Oil Pan Gasket DamagedS Check the gasket visually.
S Replace gasket as described in the repair in-
struction.
Bolt at Bracket LooseCheck the Tightening Torque
Retighten bolt
Sealing Ring at Oil DipstickS Check O–ring.
S If necessary, replace O–ring.
Sealing Ring Near End–Cover Connec-
tion DefectiveS Check sealing rings.
S Put in new sealing ring Check O–ring as de-
scribed in the repair instruction.
Page 1406 of 2643
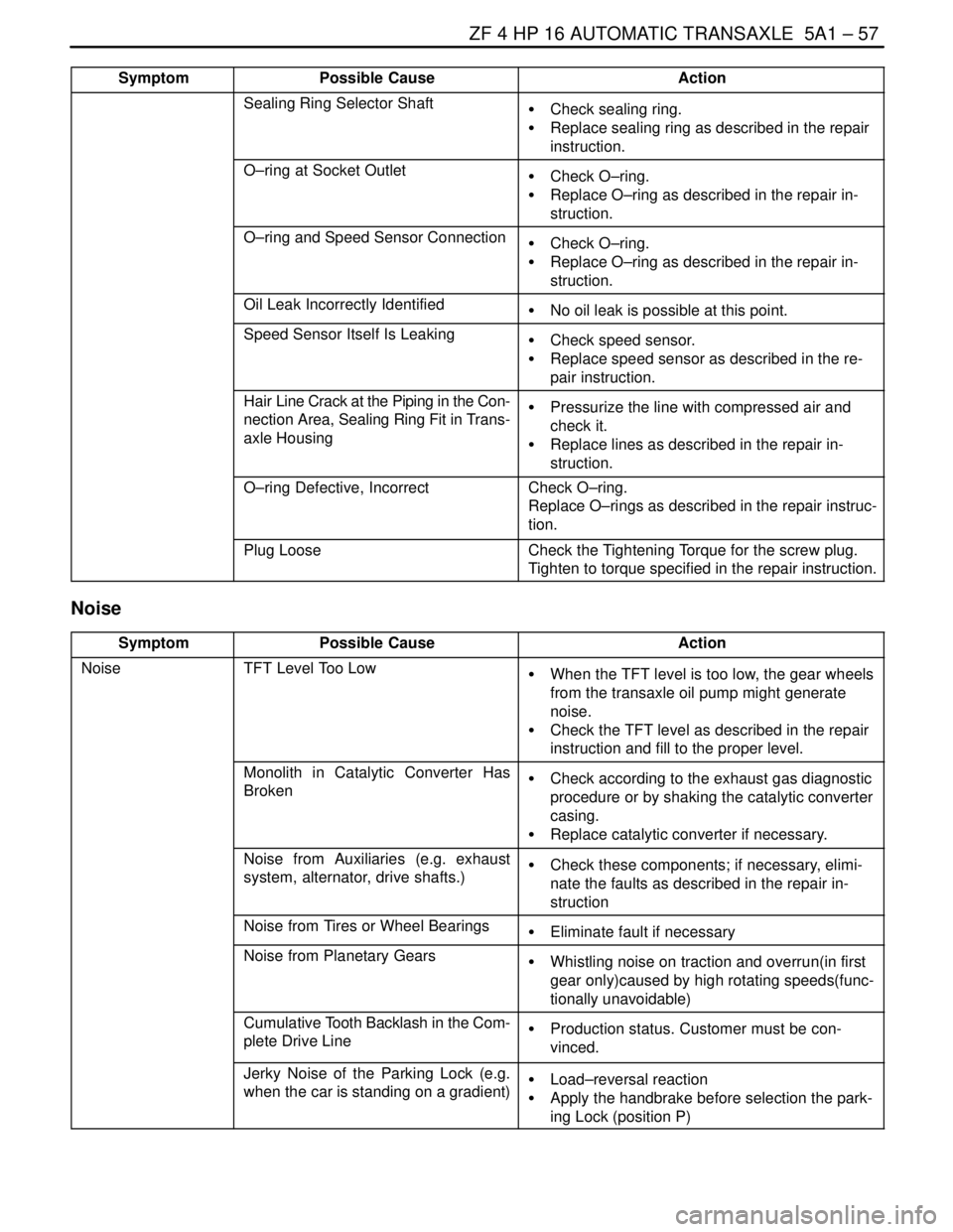
ZF 4 HP 16 AUTOMATIC TRANSAXLE 5A1 – 57
DAEWOO V–121 BL4
Symptom ActionPossible Cause
Sealing Ring Selector ShaftS Check sealing ring.
S Replace sealing ring as described in the repair
instruction.
O–ring at Socket OutletS Check O–ring.
S Replace O–ring as described in the repair in-
struction.
O–ring and Speed Sensor ConnectionS Check O–ring.
S Replace O–ring as described in the repair in-
struction.
Oil Leak Incorrectly IdentifiedS No oil leak is possible at this point.
Speed Sensor Itself Is LeakingS Check speed sensor.
S Replace speed sensor as described in the re-
pair instruction.
Hair Line Crack at the Piping in the Con-
nection Area, Sealing Ring Fit in Trans-
axle HousingS Pressurize the line with compressed air and
check it.
S Replace lines as described in the repair in-
struction.
O–ring Defective, IncorrectCheck O–ring.
Replace O–rings as described in the repair instruc-
tion.
Plug LooseCheck the Tightening Torque for the screw plug.
Tighten to torque specified in the repair instruction.
Noise
SymptomPossible CauseAction
NoiseTFT Level Too LowS When the TFT level is too low, the gear wheels
from the transaxle oil pump might generate
noise.
S Check the TFT level as described in the repair
instruction and fill to the proper level.
Monolith in Catalytic Converter Has
BrokenS Check according to the exhaust gas diagnostic
procedure or by shaking the catalytic converter
casing.
S Replace catalytic converter if necessary.
Noise from Auxiliaries (e.g. exhaust
system, alternator, drive shafts.)S Check these components; if necessary, elimi-
nate the faults as described in the repair in-
struction
Noise from Tires or Wheel BearingsS Eliminate fault if necessary
Noise from Planetary GearsS Whistling noise on traction and overrun(in first
gear only)caused by high rotating speeds(func-
tionally unavoidable)
Cumulative Tooth Backlash in the Com-
plete Drive LineS Production status. Customer must be con-
vinced.
Jerky Noise of the Parking Lock (e.g.
when the car is standing on a gradient)S Load–reversal reaction
S Apply the handbrake before selection the park-
ing Lock (position P)
Page 1407 of 2643
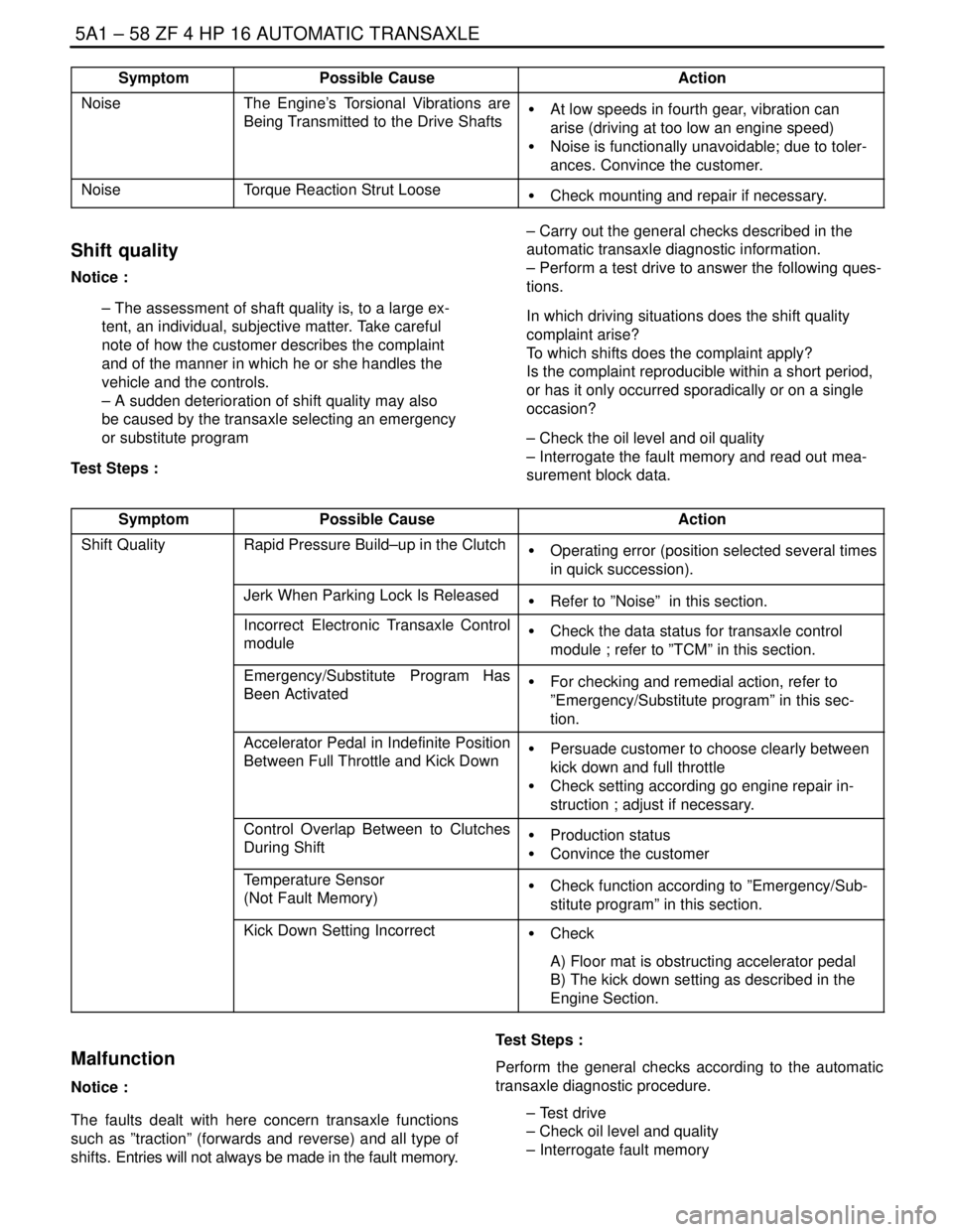
5A1 – 58IZF 4 HP 16 AUTOMATIC TRANSAXLE
DAEWOO V–121 BL4
Symptom ActionPossible Cause
NoiseThe Engine’s Torsional Vibrations are
Being Transmitted to the Drive ShaftsS At low speeds in fourth gear, vibration can
arise (driving at too low an engine speed)
S Noise is functionally unavoidable; due to toler-
ances. Convince the customer.
NoiseTorque Reaction Strut LooseS Check mounting and repair if necessary.
Shift quality
Notice :
– The assessment of shaft quality is, to a large ex-
tent, an individual, subjective matter. Take careful
note of how the customer describes the complaint
and of the manner in which he or she handles the
vehicle and the controls.
– A sudden deterioration of shift quality may also
be caused by the transaxle selecting an emergency
or substitute program
Test Steps :– Carry out the general checks described in the
automatic transaxle diagnostic information.
– Perform a test drive to answer the following ques-
tions.
In which driving situations does the shift quality
complaint arise?
To which shifts does the complaint apply?
Is the complaint reproducible within a short period,
or has it only occurred sporadically or on a single
occasion?
– Check the oil level and oil quality
– Interrogate the fault memory and read out mea-
surement block data.
Symptom
Possible CauseAction
Shift QualityRapid Pressure Build–up in the ClutchS Operating error (position selected several times
in quick succession).
Jerk When Parking Lock Is ReleasedS Refer to ”Noise” in this section.
Incorrect Electronic Transaxle Control
moduleS Check the data status for transaxle control
module ; refer to ”TCM” in this section.
Emergency/Substitute Program Has
Been ActivatedS For checking and remedial action, refer to
”Emergency/Substitute program” in this sec-
tion.
Accelerator Pedal in Indefinite Position
Between Full Throttle and Kick DownS Persuade customer to choose clearly between
kick down and full throttle
S Check setting according go engine repair in-
struction ; adjust if necessary.
Control Overlap Between to Clutches
During ShiftS Production status
S Convince the customer
Temperature Sensor
(Not Fault Memory)S Check function according to ”Emergency/Sub-
stitute program” in this section.
Kick Down Setting IncorrectS Check
A) Floor mat is obstructing accelerator pedal
B) The kick down setting as described in the
Engine Section.
Malfunction
Notice :
The faults dealt with here concern transaxle functions
such as ”traction” (forwards and reverse) and all type of
shifts. Entries will not always be made in the fault memory.Test Steps :
Perform the general checks according to the automatic
transaxle diagnostic procedure.
– Test drive
– Check oil level and quality
– Interrogate fault memory
Page 1408 of 2643
ZF 4 HP 16 AUTOMATIC TRANSAXLE 5A1 – 59
DAEWOO V–121 BL4
SymptomPossible CauseAction
MalfunctionDefective Clutch in Transaxle It There Is
Still No Drive With the TCM Discon-
nectedS This is usually due to too little oil being added
or to internal leakage.
S Repair is not possible ; if necessary, exchange
transaxle.
Kick Down Switch Not Functioning
ProperlyS For checking and remedial action, refer to
”Emergency/Substitute Program” in this sec-
tion.
Kick Down Switch Not Operating Prop-
erlyS For checking and remedial action, refer to En-
gine Instruction.
Vehicle Is in Emergency ModeS For checking and remedial action, refer to
”Emergency/Substitute Program” in this sec-
tion.