Page 969 of 2643
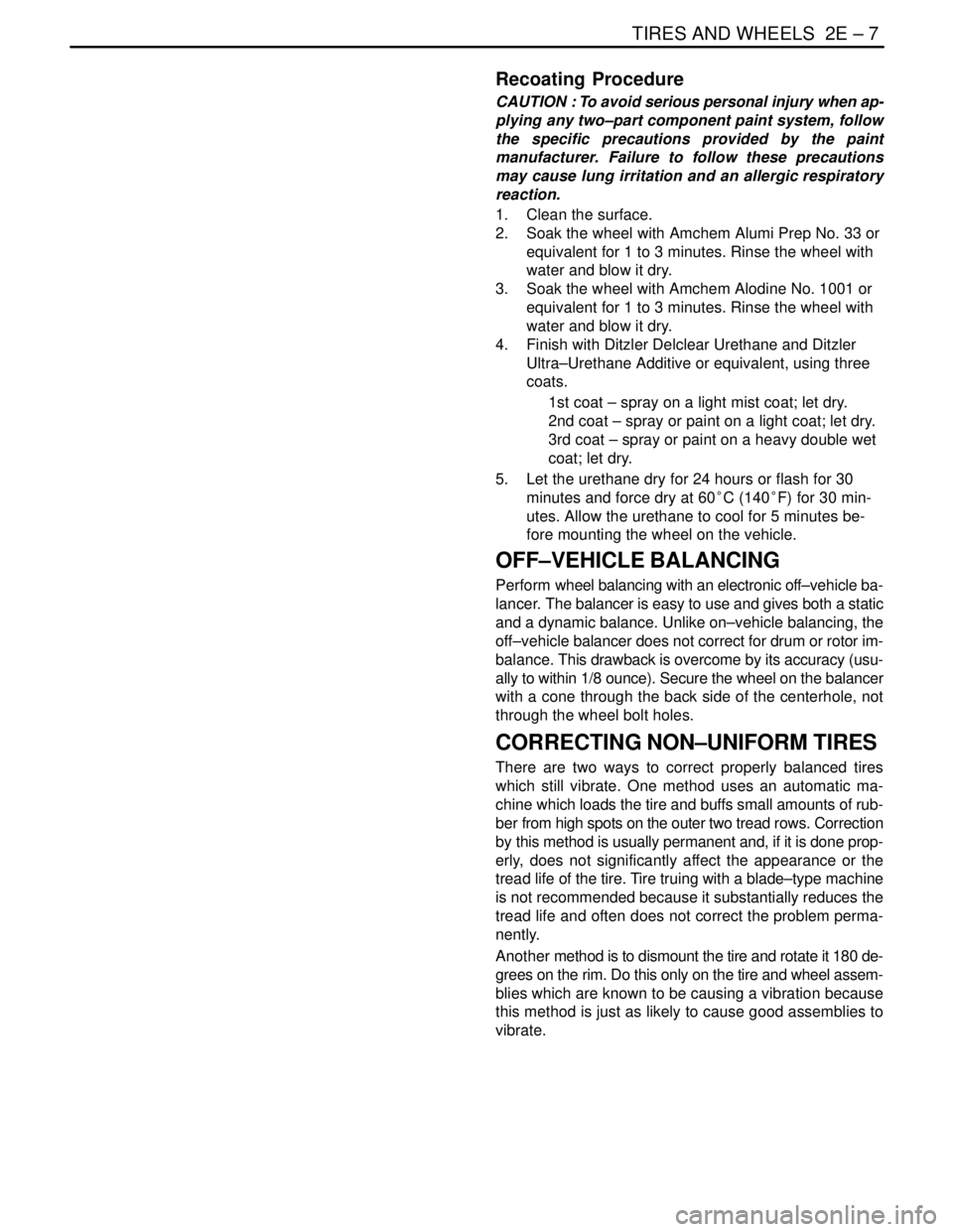
TIRES AND WHEELS 2E – 7
DAEWOO V–121 BL4
Recoating Procedure
CAUTION : To avoid serious personal injury when ap-
plying any two–part component paint system, follow
the specific precautions provided by the paint
manufacturer. Failure to follow these precautions
may cause lung irritation and an allergic respiratory
reaction.
1. Clean the surface.
2. Soak the wheel with Amchem Alumi Prep No. 33 or
equivalent for 1 to 3 minutes. Rinse the wheel with
water and blow it dry.
3. Soak the wheel with Amchem Alodine No. 1001 or
equivalent for 1 to 3 minutes. Rinse the wheel with
water and blow it dry.
4. Finish with Ditzler Delclear Urethane and Ditzler
Ultra–Urethane Additive or equivalent, using three
coats.
1st coat – spray on a light mist coat; let dry.
2nd coat – spray or paint on a light coat; let dry.
3rd coat – spray or paint on a heavy double wet
coat; let dry.
5. Let the urethane dry for 24 hours or flash for 30
minutes and force dry at 60°C (140°F) for 30 min-
utes. Allow the urethane to cool for 5 minutes be-
fore mounting the wheel on the vehicle.
OFF–VEHICLE BALANCING
Perform wheel balancing with an electronic off–vehicle ba-
lancer. The balancer is easy to use and gives both a static
and a dynamic balance. Unlike on–vehicle balancing, the
off–vehicle balancer does not correct for drum or rotor im-
balance. This drawback is overcome by its accuracy (usu-
ally to within 1/8 ounce). Secure the wheel on the balancer
with a cone through the back side of the centerhole, not
through the wheel bolt holes.
CORRECTING NON–UNIFORM TIRES
There are two ways to correct properly balanced tires
which still vibrate. One method uses an automatic ma-
chine which loads the tire and buffs small amounts of rub-
ber from high spots on the outer two tread rows. Correction
by this method is usually permanent and, if it is done prop-
erly, does not significantly affect the appearance or the
tread life of the tire. Tire truing with a blade–type machine
is not recommended because it substantially reduces the
tread life and often does not correct the problem perma-
nently.
Another method is to dismount the tire and rotate it 180 de-
grees on the rim. Do this only on the tire and wheel assem-
blies which are known to be causing a vibration because
this method is just as likely to cause good assemblies to
vibrate.
Page 970 of 2643
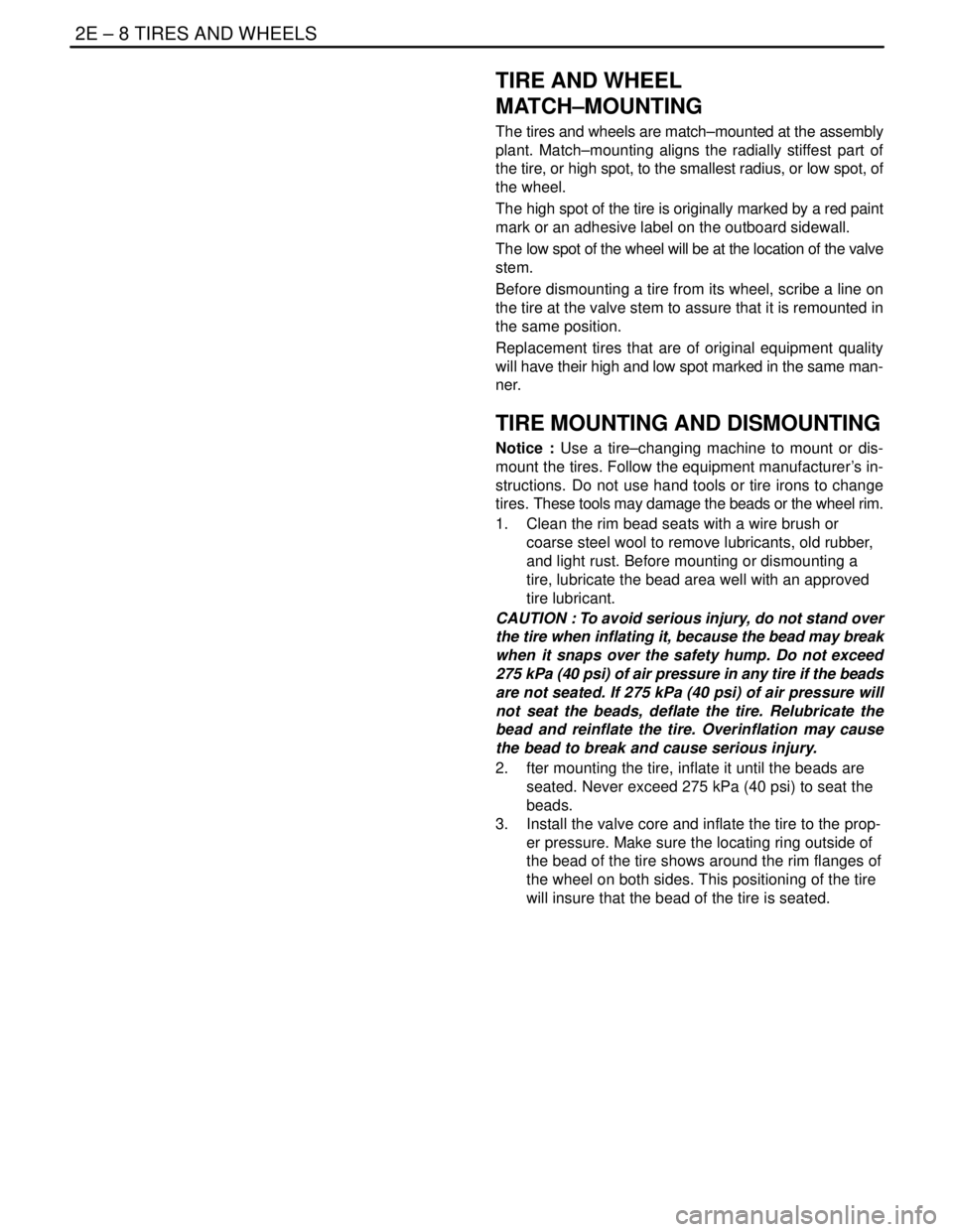
2E – 8ITIRES AND WHEELS
DAEWOO V–121 BL4
TIRE AND WHEEL
MATCH–MOUNTING
The tires and wheels are match–mounted at the assembly
plant. Match–mounting aligns the radially stiffest part of
the tire, or high spot, to the smallest radius, or low spot, of
the wheel.
The high spot of the tire is originally marked by a red paint
mark or an adhesive label on the outboard sidewall.
The low spot of the wheel will be at the location of the valve
stem.
Before dismounting a tire from its wheel, scribe a line on
the tire at the valve stem to assure that it is remounted in
the same position.
Replacement tires that are of original equipment quality
will have their high and low spot marked in the same man-
ner.
TIRE MOUNTING AND DISMOUNTING
Notice : Use a tire–changing machine to mount or dis-
mount the tires. Follow the equipment manufacturer’s in-
structions. Do not use hand tools or tire irons to change
tires. These tools may damage the beads or the wheel rim.
1. Clean the rim bead seats with a wire brush or
coarse steel wool to remove lubricants, old rubber,
and light rust. Before mounting or dismounting a
tire, lubricate the bead area well with an approved
tire lubricant.
CAUTION : To avoid serious injury, do not stand over
the tire when inflating it, because the bead may break
when it snaps over the safety hump. Do not exceed
275 kPa (40 psi) of air pressure in any tire if the beads
are not seated. If 275 kPa (40 psi) of air pressure will
not seat the beads, deflate the tire. Relubricate the
bead and reinflate the tire. Overinflation may cause
the bead to break and cause serious injury.
2. fter mounting the tire, inflate it until the beads are
seated. Never exceed 275 kPa (40 psi) to seat the
beads.
3. Install the valve core and inflate the tire to the prop-
er pressure. Make sure the locating ring outside of
the bead of the tire shows around the rim flanges of
the wheel on both sides. This positioning of the tire
will insure that the bead of the tire is seated.
Page 971 of 2643
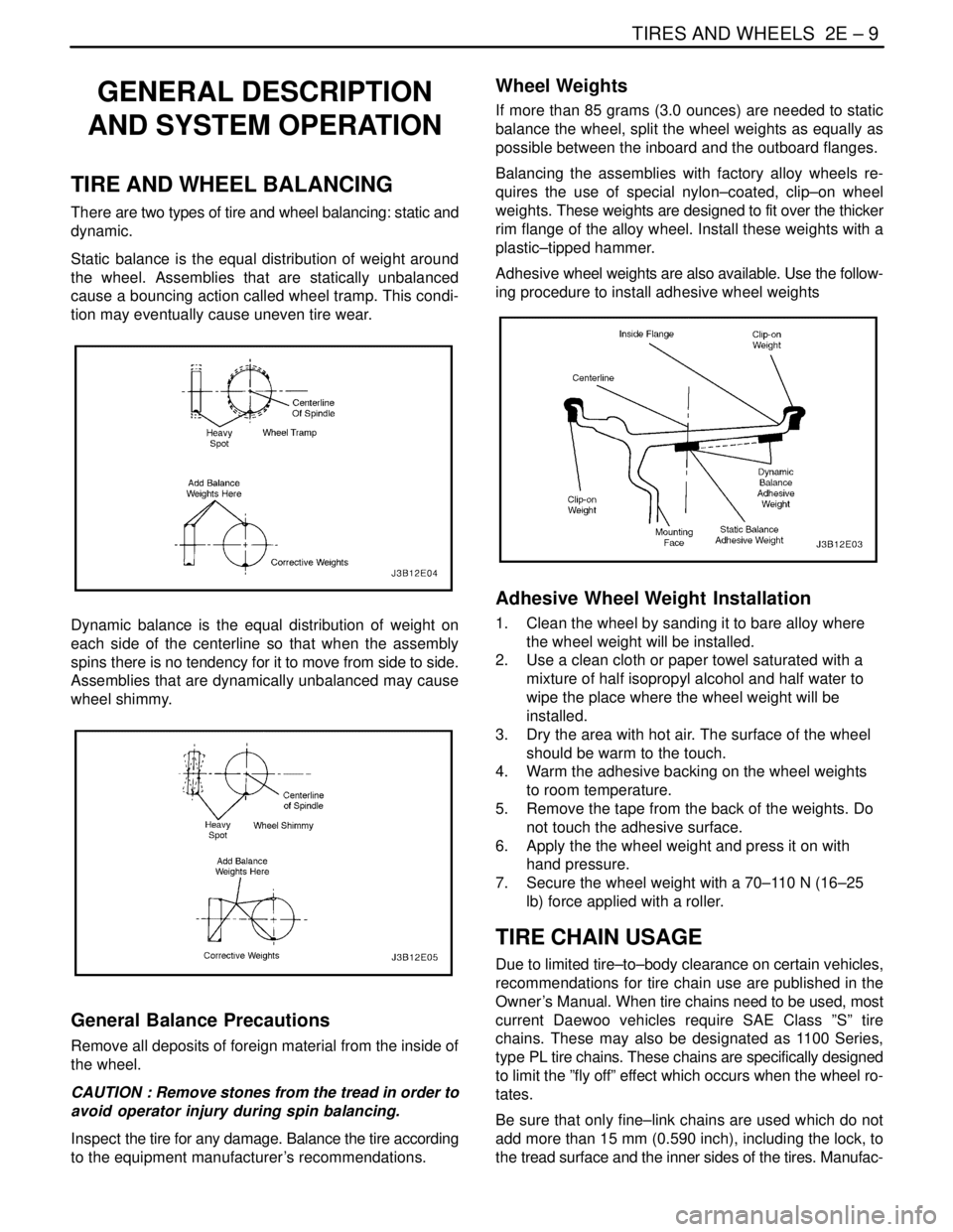
TIRES AND WHEELS 2E – 9
DAEWOO V–121 BL4
GENERAL DESCRIPTION
AND SYSTEM OPERATION
TIRE AND WHEEL BALANCING
There are two types of tire and wheel balancing: static and
dynamic.
Static balance is the equal distribution of weight around
the wheel. Assemblies that are statically unbalanced
cause a bouncing action called wheel tramp. This condi-
tion may eventually cause uneven tire wear.
Dynamic balance is the equal distribution of weight on
each side of the centerline so that when the assembly
spins there is no tendency for it to move from side to side.
Assemblies that are dynamically unbalanced may cause
wheel shimmy.
General Balance Precautions
Remove all deposits of foreign material from the inside of
the wheel.
CAUTION : Remove stones from the tread in order to
avoid operator injury during spin balancing.
Inspect the tire for any damage. Balance the tire according
to the equipment manufacturer’s recommendations.
Wheel Weights
If more than 85 grams (3.0 ounces) are needed to static
balance the wheel, split the wheel weights as equally as
possible between the inboard and the outboard flanges.
Balancing the assemblies with factory alloy wheels re-
quires the use of special nylon–coated, clip–on wheel
weights. These weights are designed to fit over the thicker
rim flange of the alloy wheel. Install these weights with a
plastic–tipped hammer.
Adhesive wheel weights are also available. Use the follow-
ing procedure to install adhesive wheel weights
Adhesive Wheel Weight Installation
1. Clean the wheel by sanding it to bare alloy where
the wheel weight will be installed.
2. Use a clean cloth or paper towel saturated with a
mixture of half isopropyl alcohol and half water to
wipe the place where the wheel weight will be
installed.
3. Dry the area with hot air. The surface of the wheel
should be warm to the touch.
4. Warm the adhesive backing on the wheel weights
to room temperature.
5. Remove the tape from the back of the weights. Do
not touch the adhesive surface.
6. Apply the the wheel weight and press it on with
hand pressure.
7. Secure the wheel weight with a 70–110 N (16–25
lb) force applied with a roller.
TIRE CHAIN USAGE
Due to limited tire–to–body clearance on certain vehicles,
recommendations for tire chain use are published in the
Owner ’s Manual. When tire chains need to be used, most
current Daewoo vehicles require SAE Class ”S” tire
chains. These may also be designated as 1100 Series,
type PL tire chains. These chains are specifically designed
to limit the ”fly off” effect which occurs when the wheel ro-
tates.
Be sure that only fine–link chains are used which do not
add more than 15 mm (0.590 inch), including the lock, to
the tread surface and the inner sides of the tires. Manufac-
Page 972 of 2643
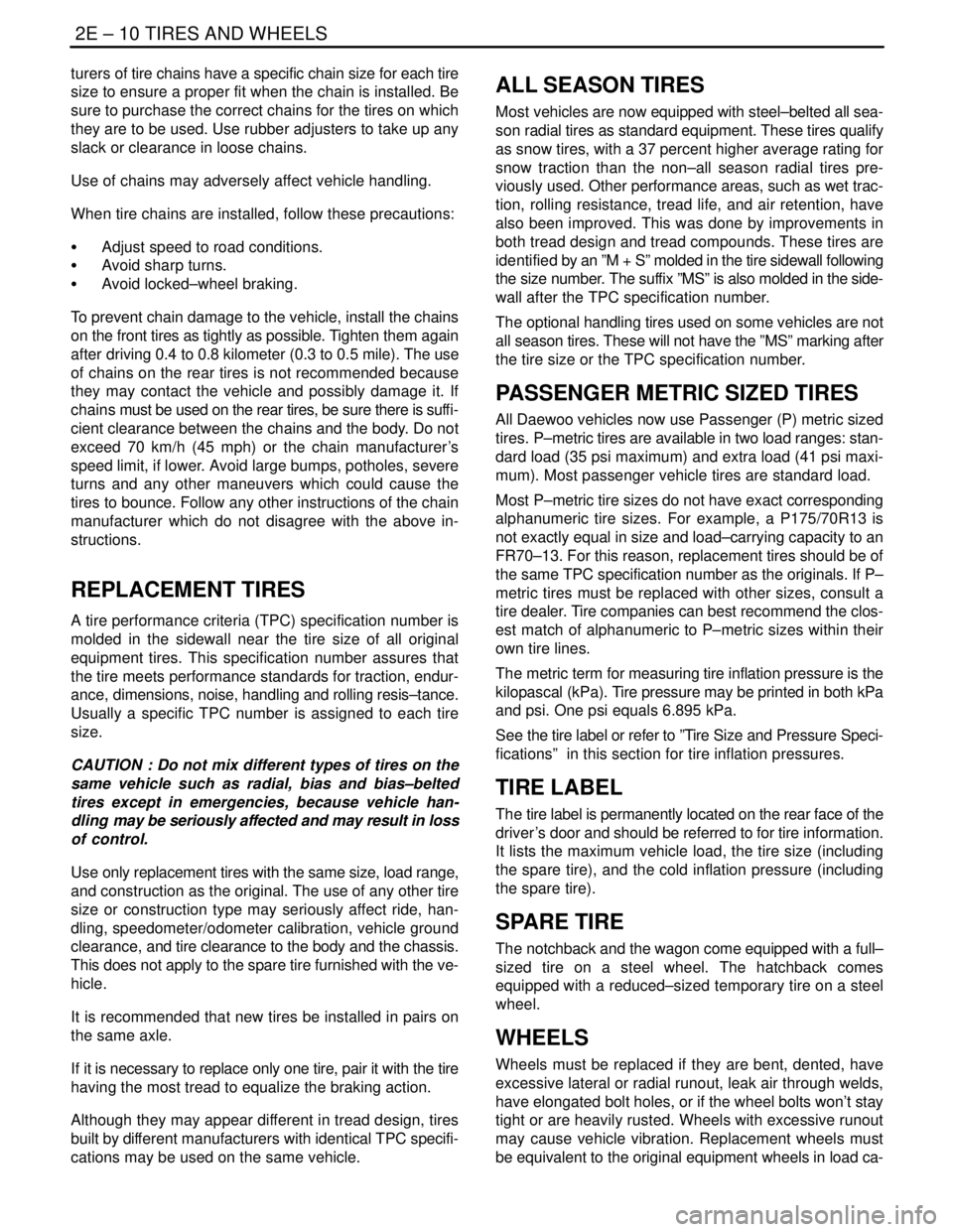
2E – 10ITIRES AND WHEELS
DAEWOO V–121 BL4
turers of tire chains have a specific chain size for each tire
size to ensure a proper fit when the chain is installed. Be
sure to purchase the correct chains for the tires on which
they are to be used. Use rubber adjusters to take up any
slack or clearance in loose chains.
Use of chains may adversely affect vehicle handling.
When tire chains are installed, follow these precautions:
S Adjust speed to road conditions.
S Avoid sharp turns.
S Avoid locked–wheel braking.
To prevent chain damage to the vehicle, install the chains
on the front tires as tightly as possible. Tighten them again
after driving 0.4 to 0.8 kilometer (0.3 to 0.5 mile). The use
of chains on the rear tires is not recommended because
they may contact the vehicle and possibly damage it. If
chains must be used on the rear tires, be sure there is suffi-
cient clearance between the chains and the body. Do not
exceed 70 km/h (45 mph) or the chain manufacturer’s
speed limit, if lower. Avoid large bumps, potholes, severe
turns and any other maneuvers which could cause the
tires to bounce. Follow any other instructions of the chain
manufacturer which do not disagree with the above in-
structions.
REPLACEMENT TIRES
A tire performance criteria (TPC) specification number is
molded in the sidewall near the tire size of all original
equipment tires. This specification number assures that
the tire meets performance standards for traction, endur-
ance, dimensions, noise, handling and rolling resis–tance.
Usually a specific TPC number is assigned to each tire
size.
CAUTION : Do not mix different types of tires on the
same vehicle such as radial, bias and bias–belted
tires except in emergencies, because vehicle han-
dling may be seriously affected and may result in loss
of control.
Use only replacement tires with the same size, load range,
and construction as the original. The use of any other tire
size or construction type may seriously affect ride, han-
dling, speedometer/odometer calibration, vehicle ground
clearance, and tire clearance to the body and the chassis.
This does not apply to the spare tire furnished with the ve-
hicle.
It is recommended that new tires be installed in pairs on
the same axle.
If it is necessary to replace only one tire, pair it with the tire
having the most tread to equalize the braking action.
Although they may appear different in tread design, tires
built by different manufacturers with identical TPC specifi-
cations may be used on the same vehicle.
ALL SEASON TIRES
Most vehicles are now equipped with steel–belted all sea-
son radial tires as standard equipment. These tires qualify
as snow tires, with a 37 percent higher average rating for
snow traction than the non–all season radial tires pre-
viously used. Other performance areas, such as wet trac-
tion, rolling resistance, tread life, and air retention, have
also been improved. This was done by improvements in
both tread design and tread compounds. These tires are
identified by an ”M + S” molded in the tire sidewall following
the size number. The suffix ”MS” is also molded in the side-
wall after the TPC specification number.
The optional handling tires used on some vehicles are not
all season tires. These will not have the ”MS” marking after
the tire size or the TPC specification number.
PASSENGER METRIC SIZED TIRES
All Daewoo vehicles now use Passenger (P) metric sized
tires. P–metric tires are available in two load ranges: stan-
dard load (35 psi maximum) and extra load (41 psi maxi-
mum). Most passenger vehicle tires are standard load.
Most P–metric tire sizes do not have exact corresponding
alphanumeric tire sizes. For example, a P175/70R13 is
not exactly equal in size and load–carrying capacity to an
FR70–13. For this reason, replacement tires should be of
the same TPC specification number as the originals. If P–
metric tires must be replaced with other sizes, consult a
tire dealer. Tire companies can best recommend the clos-
est match of alphanumeric to P–metric sizes within their
own tire lines.
The metric term for measuring tire inflation pressure is the
kilopascal (kPa). Tire pressure may be printed in both kPa
and psi. One psi equals 6.895 kPa.
See the tire label or refer to ”Tire Size and Pressure Speci-
fications” in this section for tire inflation pressures.
TIRE LABEL
The tire label is permanently located on the rear face of the
driver’s door and should be referred to for tire information.
It lists the maximum vehicle load, the tire size (including
the spare tire), and the cold inflation pressure (including
the spare tire).
SPARE TIRE
The notchback and the wagon come equipped with a full–
sized tire on a steel wheel. The hatchback comes
equipped with a reduced–sized temporary tire on a steel
wheel.
WHEELS
Wheels must be replaced if they are bent, dented, have
excessive lateral or radial runout, leak air through welds,
have elongated bolt holes, or if the wheel bolts won’t stay
tight or are heavily rusted. Wheels with excessive runout
may cause vehicle vibration. Replacement wheels must
be equivalent to the original equipment wheels in load ca-
Page 973 of 2643
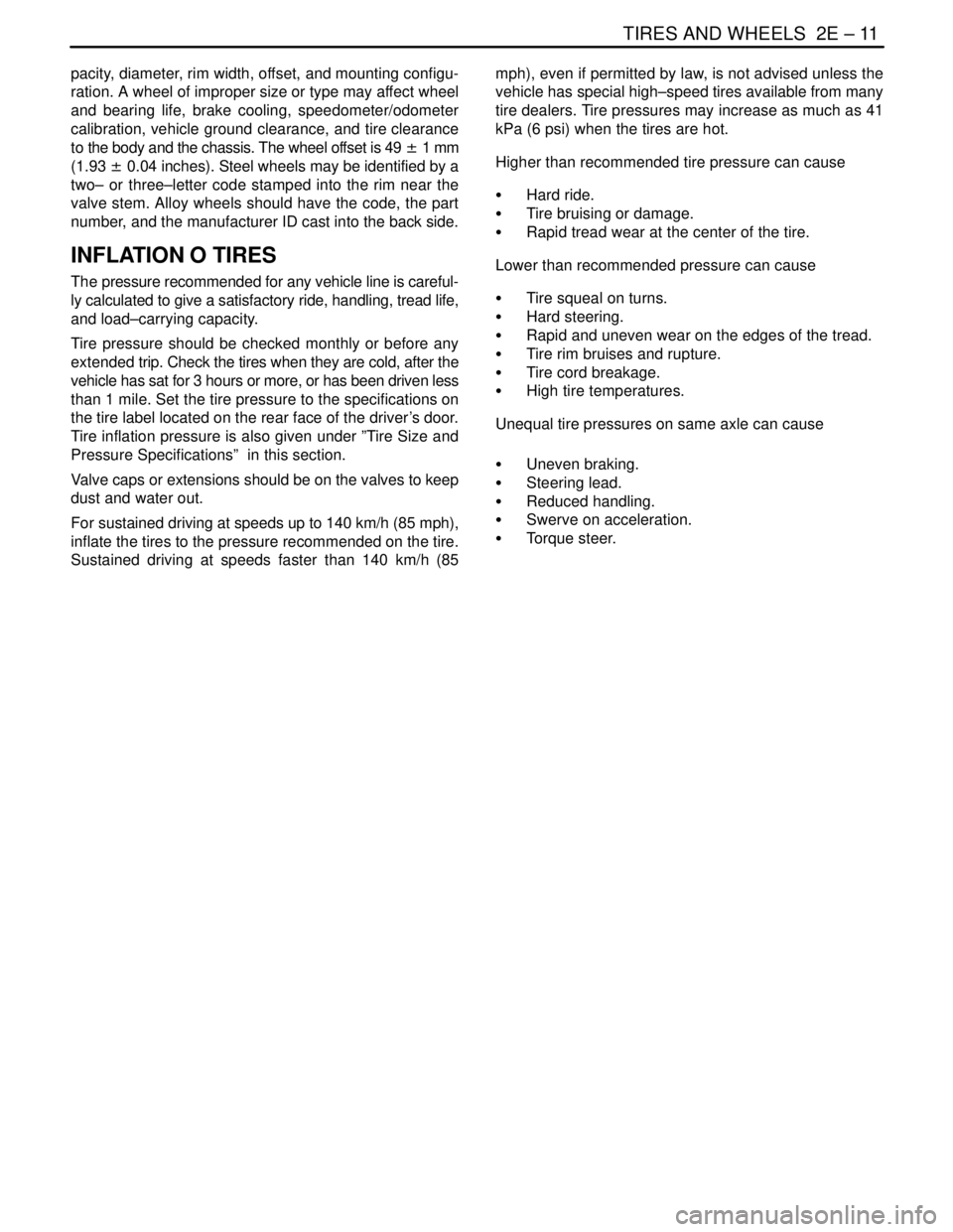
TIRES AND WHEELS 2E – 11
DAEWOO V–121 BL4
pacity, diameter, rim width, offset, and mounting configu-
ration. A wheel of improper size or type may affect wheel
and bearing life, brake cooling, speedometer/odometer
calibration, vehicle ground clearance, and tire clearance
to the body and the chassis. The wheel offset is 49 ± 1 mm
(1.93 ± 0.04 inches). Steel wheels may be identified by a
two– or three–letter code stamped into the rim near the
valve stem. Alloy wheels should have the code, the part
number, and the manufacturer ID cast into the back side.
INFLATION O TIRES
The pressure recommended for any vehicle line is careful-
ly calculated to give a satisfactory ride, handling, tread life,
and load–carrying capacity.
Tire pressure should be checked monthly or before any
extended trip. Check the tires when they are cold, after the
vehicle has sat for 3 hours or more, or has been driven less
than 1 mile. Set the tire pressure to the specifications on
the tire label located on the rear face of the driver’s door.
Tire inflation pressure is also given under ”Tire Size and
Pressure Specifications” in this section.
Valve caps or extensions should be on the valves to keep
dust and water out.
For sustained driving at speeds up to 140 km/h (85 mph),
inflate the tires to the pressure recommended on the tire.
Sustained driving at speeds faster than 140 km/h (85mph), even if permitted by law, is not advised unless the
vehicle has special high–speed tires available from many
tire dealers. Tire pressures may increase as much as 41
kPa (6 psi) when the tires are hot.
Higher than recommended tire pressure can cause
S Hard ride.
S Tire bruising or damage.
S Rapid tread wear at the center of the tire.
Lower than recommended pressure can cause
S Tire squeal on turns.
S Hard steering.
S Rapid and uneven wear on the edges of the tread.
S Tire rim bruises and rupture.
S Tire cord breakage.
S High tire temperatures.
Unequal tire pressures on same axle can cause
S Uneven braking.
S Steering lead.
S Reduced handling.
S Swerve on acceleration.
S Torque steer.
Page 974 of 2643
SECTION 3
WIRING DIAGRAM FOR POWER SUPPLIES
CONTENTS
1. IGNITION SWITCH CIRCUIT3–2 . . . . . . . . . . . . . . . . . . . . . . . . . . . . . . . . . . . . . . . . . . . . . . . . . . . . . . . . . . . . . . . . . . . . . .
2. 30 TER ”BAT+” POWER SUPPLY CIRCUIT(I.P FUSE BLOCK) 3–2. . . . . . . . . . . . . . . . . . . . . . . . . . . . . . . . . . . . . . .
3. 15 TER ”IGN 1” POWER SUPPLY CIRCUIT(I.P FUSE BLOCK) 3–3. . . . . . . . . . . . . . . . . . . . . . . . . . . . . . . . . . . . . . .
4. 15A TER ”IGN2”, 15C TER ”ACC” POWER SUPPLY CIRCUIT(I.P FUSE BLOCK) 3–4. . . . . . . . . . . . . . . . . . . . . .
5. ENGINE FUSE BLOCK & RELAY CIRCUIT 3–5. . . . . . . . . . . . . . . . . . . . . . . . . . . . . . . . . . . . . . . . . . . . . . . . . . . . . . . . .
Page 975 of 2643
3–2WWIRING DIAGRAM FOR POWER SUPPLIES
1. IGNITION SWITCH CIRCUIT2. 30 TER ”BAT+” POWER SUPPLY CIRCUIT (I.P FUSE BLOCK)
Page 976 of 2643
WIRING DIAGRAM FOR POWER SUPPLIESW3–3
3. 15 TER ”IGN1” POWER SUPPLY CIRCUIT (I.P FUSE BLOCK)