Page 569 of 2395
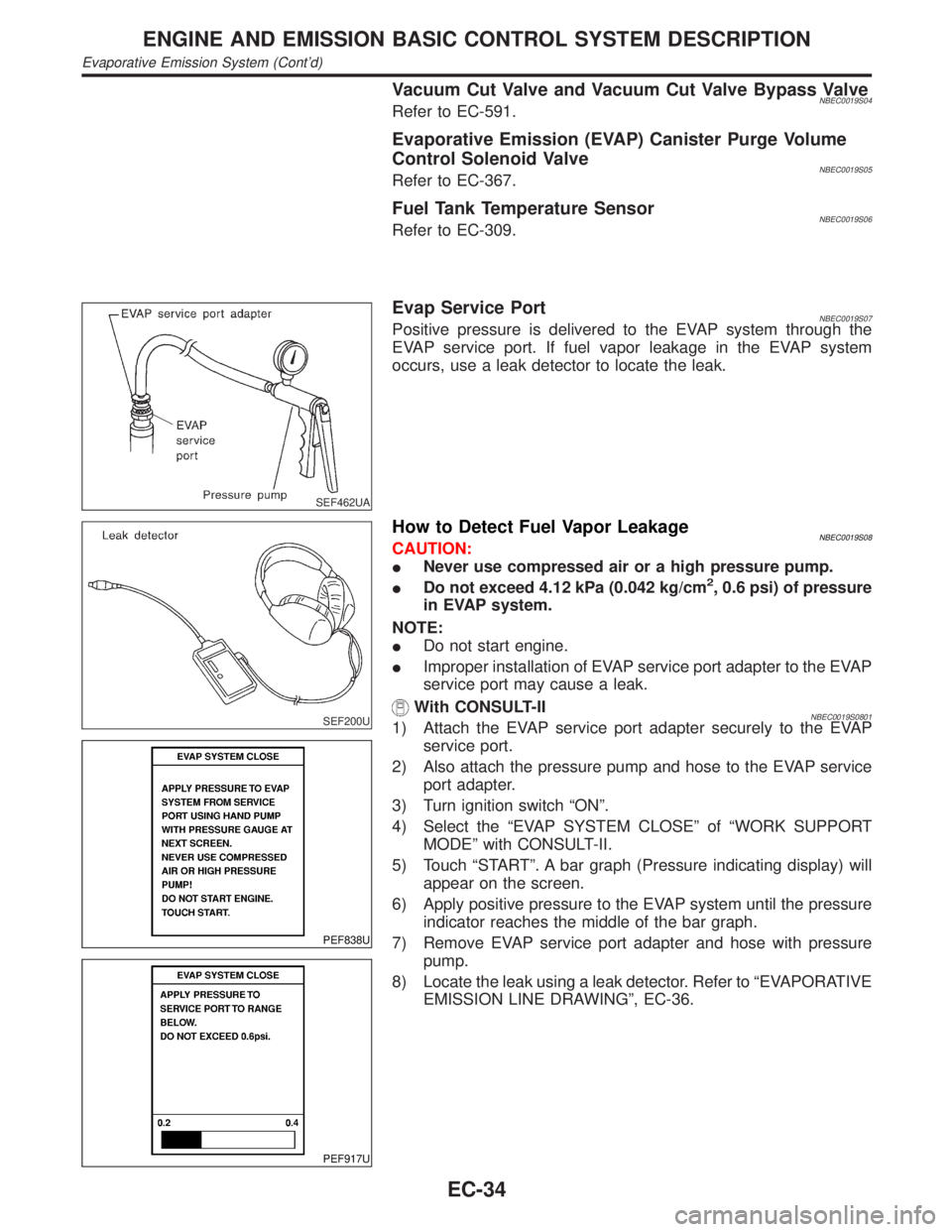
Vacuum Cut Valve and Vacuum Cut Valve Bypass ValveNBEC0019S04Refer to EC-591.
Evaporative Emission (EVAP) Canister Purge Volume
Control Solenoid Valve
NBEC0019S05Refer to EC-367.
Fuel Tank Temperature SensorNBEC0019S06Refer to EC-309.
SEF462UA
Evap Service PortNBEC0019S07Positive pressure is delivered to the EVAP system through the
EVAP service port. If fuel vapor leakage in the EVAP system
occurs, use a leak detector to locate the leak.
SEF200U
PEF838U
PEF917U
How to Detect Fuel Vapor LeakageNBEC0019S08CAUTION:
INever use compressed air or a high pressure pump.
IDo not exceed 4.12 kPa (0.042 kg/cm
2, 0.6 psi) of pressure
in EVAP system.
NOTE:
IDo not start engine.
IImproper installation of EVAP service port adapter to the EVAP
service port may cause a leak.
With CONSULT-IINBEC0019S08011) Attach the EVAP service port adapter securely to the EVAP
service port.
2) Also attach the pressure pump and hose to the EVAP service
port adapter.
3) Turn ignition switch ªONº.
4) Select the ªEVAP SYSTEM CLOSEº of ªWORK SUPPORT
MODEº with CONSULT-II.
5) Touch ªSTARTº. A bar graph (Pressure indicating display) will
appear on the screen.
6) Apply positive pressure to the EVAP system until the pressure
indicator reaches the middle of the bar graph.
7) Remove EVAP service port adapter and hose with pressure
pump.
8) Locate the leak using a leak detector. Refer to ªEVAPORATIVE
EMISSION LINE DRAWINGº, EC-36.
ENGINE AND EMISSION BASIC CONTROL SYSTEM DESCRIPTION
Evaporative Emission System (Cont'd)
EC-34
Page 570 of 2395
SEF462UA
SEF598U
Without CONSULT-IINBEC0019S08021) Attach the EVAP service port adapter securely to the EVAP
service port.
2) Also attach the pressure pump with pressure gauge to the
EVAP service port adapter.
3) Apply battery voltage to between the terminals of both EVAP
canister vent control valve and vacuum cut valve bypass valve
to make a closed EVAP system.
4) To locate the leak, deliver positive pressure to the EVAP sys-
tem until pressure gauge points reach 1.38 to 2.76 kPa (0.014
to 0.028 kg/cm
2, 0.2 to 0.4 psi).
5) Remove EVAP service port adapter and hose with pressure
pump.
6) Locate the leak using a leak detector. Refer to ªEVAPORATIVE
EMISSION LINE DRAWINGº, EC-36.
GI
MA
EM
LC
FE
AT
TF
PD
AX
SU
BR
ST
RS
BT
HA
SC
EL
IDX
ENGINE AND EMISSION BASIC CONTROL SYSTEM DESCRIPTION
Evaporative Emission System (Cont'd)
EC-35
Page 571 of 2395
EVAPORATIVE EMISSION LINE DRAWINGNBEC0020
SEF932Y
ENGINE AND EMISSION BASIC CONTROL SYSTEM DESCRIPTION
Evaporative Emission System (Cont'd)
EC-36
Page 572 of 2395
SEF870T
GI
MA
EM
LC
FE
AT
TF
PD
AX
SU
BR
ST
RS
BT
HA
SC
EL
IDX
ENGINE AND EMISSION BASIC CONTROL SYSTEM DESCRIPTION
Evaporative Emission System (Cont'd)
EC-37
Page 573 of 2395
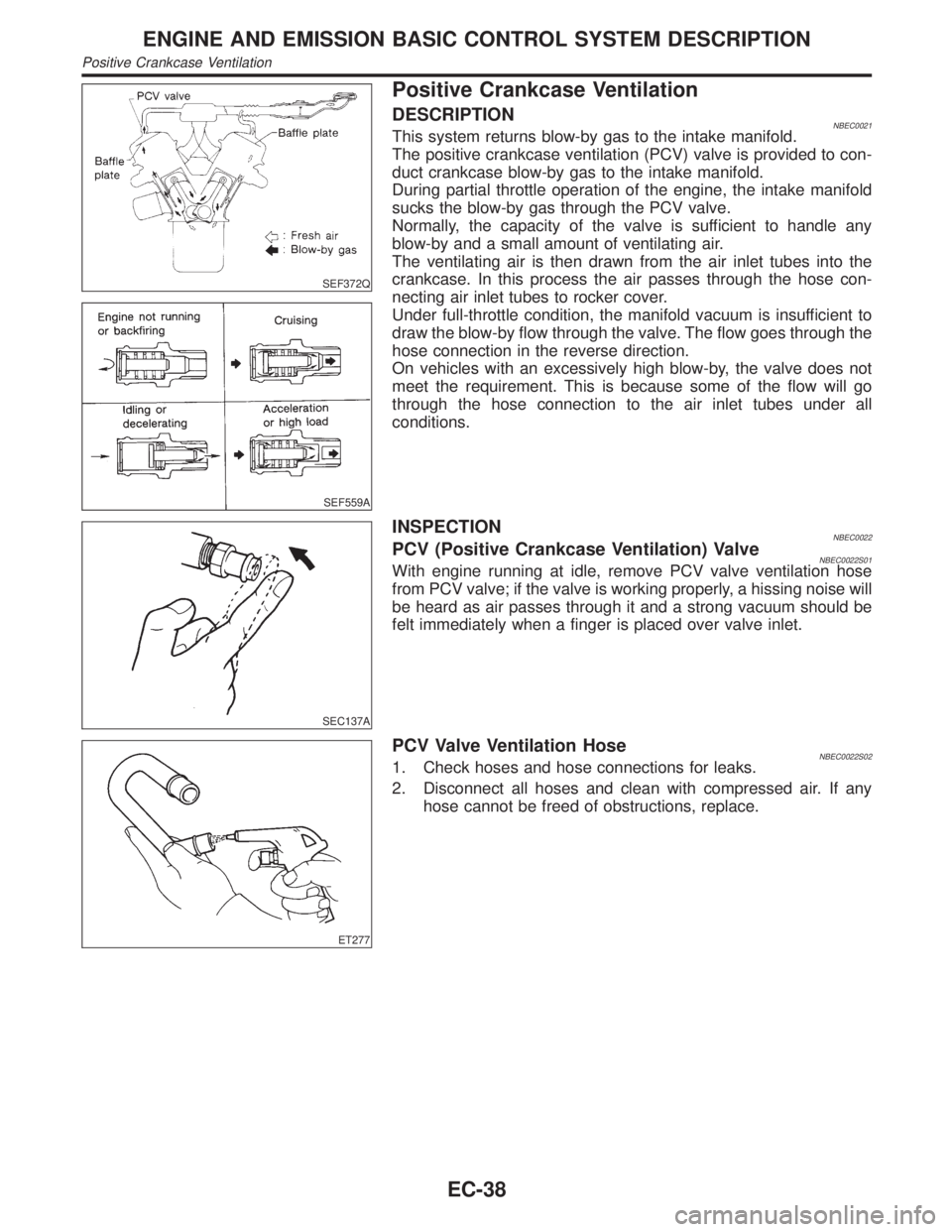
SEF372Q
SEF559A
Positive Crankcase Ventilation
DESCRIPTIONNBEC0021This system returns blow-by gas to the intake manifold.
The positive crankcase ventilation (PCV) valve is provided to con-
duct crankcase blow-by gas to the intake manifold.
During partial throttle operation of the engine, the intake manifold
sucks the blow-by gas through the PCV valve.
Normally, the capacity of the valve is sufficient to handle any
blow-by and a small amount of ventilating air.
The ventilating air is then drawn from the air inlet tubes into the
crankcase. In this process the air passes through the hose con-
necting air inlet tubes to rocker cover.
Under full-throttle condition, the manifold vacuum is insufficient to
draw the blow-by flow through the valve. The flow goes through the
hose connection in the reverse direction.
On vehicles with an excessively high blow-by, the valve does not
meet the requirement. This is because some of the flow will go
through the hose connection to the air inlet tubes under all
conditions.
SEC137A
INSPECTIONNBEC0022PCV (Positive Crankcase Ventilation) ValveNBEC0022S01With engine running at idle, remove PCV valve ventilation hose
from PCV valve; if the valve is working properly, a hissing noise will
be heard as air passes through it and a strong vacuum should be
felt immediately when a finger is placed over valve inlet.
ET277
PCV Valve Ventilation HoseNBEC0022S021. Check hoses and hose connections for leaks.
2. Disconnect all hoses and clean with compressed air. If any
hose cannot be freed of obstructions, replace.
ENGINE AND EMISSION BASIC CONTROL SYSTEM DESCRIPTION
Positive Crankcase Ventilation
EC-38
Page 574 of 2395
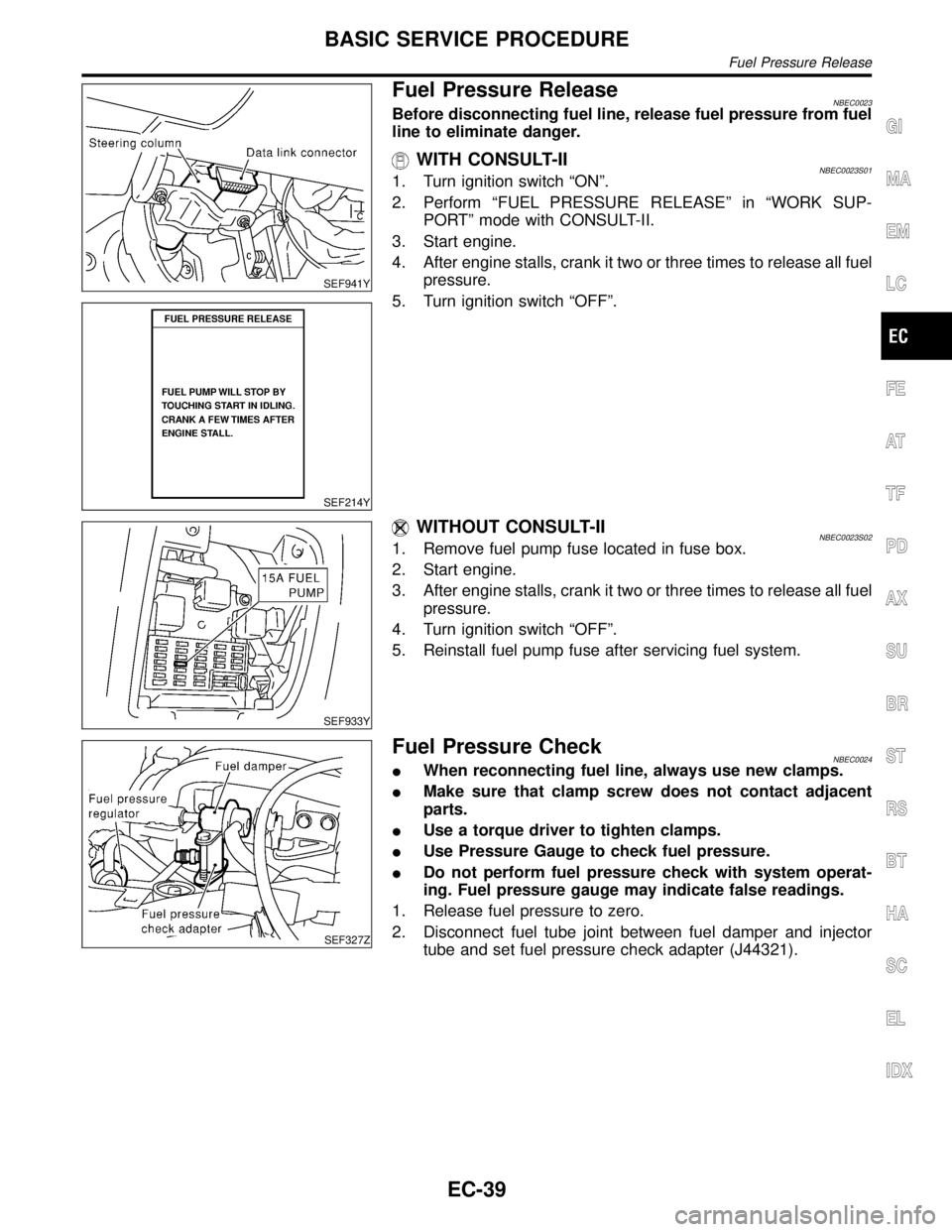
SEF941Y
SEF214Y
Fuel Pressure ReleaseNBEC0023Before disconnecting fuel line, release fuel pressure from fuel
line to eliminate danger.
WITH CONSULT-IINBEC0023S011. Turn ignition switch ªONº.
2. Perform ªFUEL PRESSURE RELEASEº in ªWORK SUP-
PORTº mode with CONSULT-II.
3. Start engine.
4. After engine stalls, crank it two or three times to release all fuel
pressure.
5. Turn ignition switch ªOFFº.
SEF933Y
WITHOUT CONSULT-IINBEC0023S021. Remove fuel pump fuse located in fuse box.
2. Start engine.
3. After engine stalls, crank it two or three times to release all fuel
pressure.
4. Turn ignition switch ªOFFº.
5. Reinstall fuel pump fuse after servicing fuel system.
SEF327Z
Fuel Pressure CheckNBEC0024IWhen reconnecting fuel line, always use new clamps.
IMake sure that clamp screw does not contact adjacent
parts.
IUse a torque driver to tighten clamps.
IUse Pressure Gauge to check fuel pressure.
IDo not perform fuel pressure check with system operat-
ing. Fuel pressure gauge may indicate false readings.
1. Release fuel pressure to zero.
2. Disconnect fuel tube joint between fuel damper and injector
tube and set fuel pressure check adapter (J44321).
GI
MA
EM
LC
FE
AT
TF
PD
AX
SU
BR
ST
RS
BT
HA
SC
EL
IDX
BASIC SERVICE PROCEDURE
Fuel Pressure Release
EC-39
Page 575 of 2395
SEF328Z
3. Install pressure gauge to the fuel pressure check adapter as
shown in the figure.
4. Start engine and check for fuel leakage.
5. Read the indication of fuel pressure gauge.
At idling:
With vacuum hose connected
Approximately 235 kPa (2.4 kg/cm
2, 34 psi)
With vacuum hose disconnected
Approximately 294 kPa (3.0 kg/cm
2, 43 psi)
If results are unsatisfactory, perform Fuel Pressure Regulator
Check.
SEF329Z
Fuel Pressure Regulator CheckNBEC00251. Stop engine and disconnect fuel pressure regulator vacuum
hose from vacuum gallery.
2. Plug vacuum gallery with a blind cap.
3. Connect variable vacuum source to fuel pressure regulator.
SEF718BA
4. Start engine and read indication of fuel pressure gauge as
vacuum is changed.
Fuel pressure should decrease as vacuum increases. If results
are unsatisfactory, replace fuel pressure regulator.
BASIC SERVICE PROCEDURE
Fuel Pressure Check (Cont'd)
EC-40
Page 576 of 2395
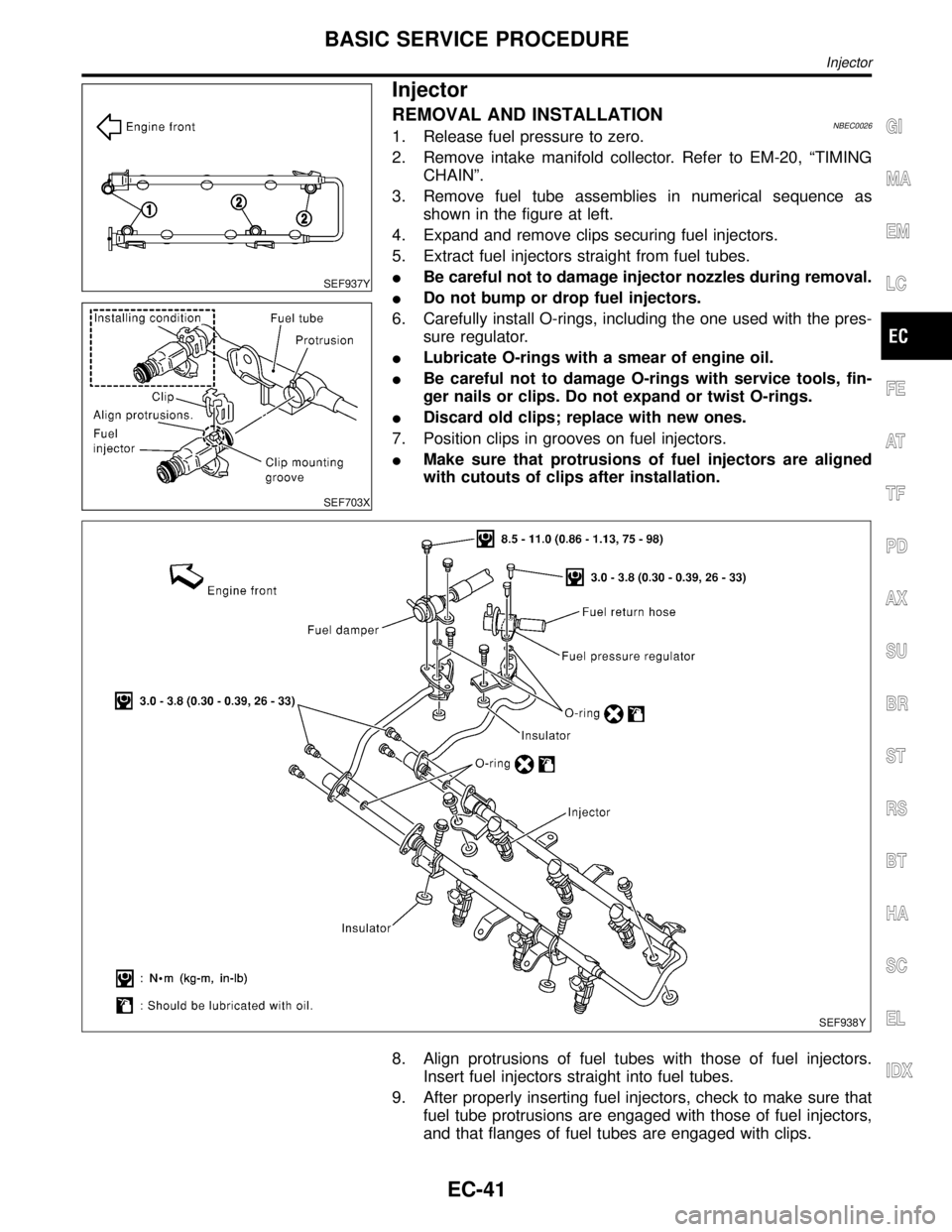
SEF937Y
SEF703X
Injector
REMOVAL AND INSTALLATIONNBEC00261. Release fuel pressure to zero.
2. Remove intake manifold collector. Refer to EM-20, ªTIMING
CHAINº.
3. Remove fuel tube assemblies in numerical sequence as
shown in the figure at left.
4. Expand and remove clips securing fuel injectors.
5. Extract fuel injectors straight from fuel tubes.
IBe careful not to damage injector nozzles during removal.
IDo not bump or drop fuel injectors.
6. Carefully install O-rings, including the one used with the pres-
sure regulator.
ILubricate O-rings with a smear of engine oil.
IBe careful not to damage O-rings with service tools, fin-
ger nails or clips. Do not expand or twist O-rings.
IDiscard old clips; replace with new ones.
7. Position clips in grooves on fuel injectors.
IMake sure that protrusions of fuel injectors are aligned
with cutouts of clips after installation.
SEF938Y
8. Align protrusions of fuel tubes with those of fuel injectors.
Insert fuel injectors straight into fuel tubes.
9. After properly inserting fuel injectors, check to make sure that
fuel tube protrusions are engaged with those of fuel injectors,
and that flanges of fuel tubes are engaged with clips.
GI
MA
EM
LC
FE
AT
TF
PD
AX
SU
BR
ST
RS
BT
HA
SC
EL
IDX
BASIC SERVICE PROCEDURE
Injector
EC-41