Page 2073 of 2395
DISASSEMBLYNBPD0036
SPD404A
CAUTION:
Do not run engine when one wheel (rear) is off the ground.
SPD275
1. Remove side bearing inner cone with Tool.
2. Loosen ring gear bolts in a criss-cross pattern.
3. Tap ring gear off gear case with a soft hammer.
Tap evenly all around to keep ring gear from binding.
SPD363A
4. Remove couple bolts on differential cases A and B with a
press.
Tool number: ST33081000 ( Ð )
5. Separate differential case A and B.
Draw out component parts (discs and plates, etc.).
Put marks on gears and pressure rings so that they can be
reinstalled in their original positions from which they were
removed.
REAR FINAL DRIVEH233B
Limited Slip Differential (Cont'd)
PD-48
Page 2074 of 2395
SPD359A
INSPECTIONNBPD0037Contact SurfacesNBPD0037S011. Clean the disassembled parts in suitable solvent and blow dry
with compressed air.
2. If following surfaces are found with burrs or scratches, smooth
with oil stone.
1Differential case B
2Differential case A
3Side gear
4Pinion mate gear
5Pinion mate shaft
6Friction plate guide
Disc and PlateNBPD0037S021. Clean the discs and plates in suitable solvent and blow dry with
compressed air.
2. Inspect discs and plates for wear, nicks and burrs.
SPD279
3. To test if friction disc or plate is not distorted, place it on a sur-
face plate and rotate it by hand with indicating finger of dial
gauge resting against disc or plate surface.
Allowable warpage:
0.08 mm (0.0031 in)
If it exceeds limits, replace with a new plate to eliminate pos-
sibility of clutch slippage or sticking.
GI
MA
EM
LC
EC
FE
AT
TF
AX
SU
BR
ST
RS
BT
HA
SC
EL
IDX
REAR FINAL DRIVEH233B
Limited Slip Differential (Cont'd)
PD-49
Page 2075 of 2395
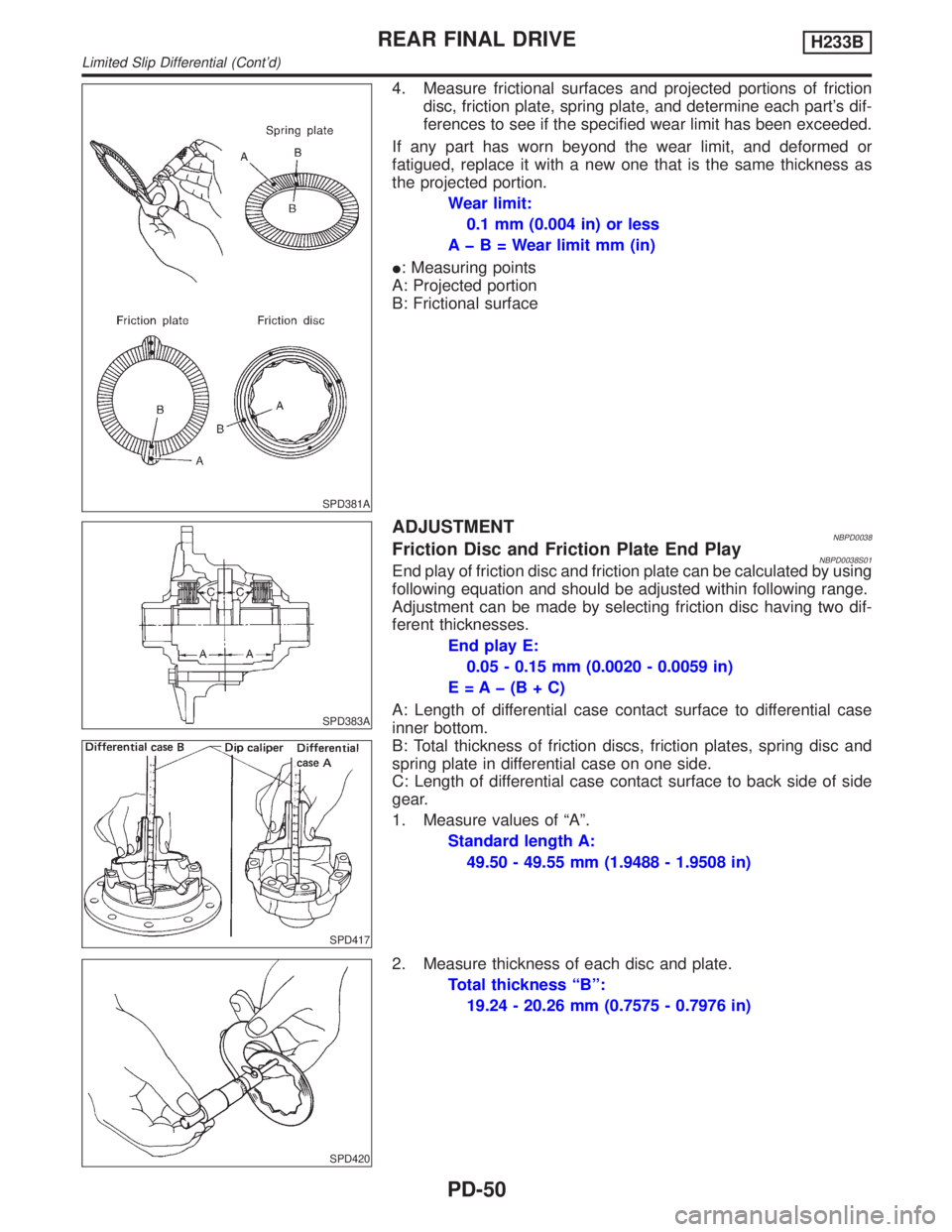
SPD381A
4. Measure frictional surfaces and projected portions of friction
disc, friction plate, spring plate, and determine each part's dif-
ferences to see if the specified wear limit has been exceeded.
If any part has worn beyond the wear limit, and deformed or
fatigued, replace it with a new one that is the same thickness as
the projected portion.
Wear limit:
0.1 mm (0.004 in) or less
AþB=Wearlimit mm (in)
I: Measuring points
A: Projected portion
B: Frictional surface
SPD383A
SPD417
ADJUSTMENTNBPD0038Friction Disc and Friction Plate End PlayNBPD0038S01End play of friction disc and friction plate can be calculated by using
following equation and should be adjusted within following range.
Adjustment can be made by selecting friction disc having two dif-
ferent thicknesses.
End play E:
0.05 - 0.15 mm (0.0020 - 0.0059 in)
E=Aþ(B+C)
A: Length of differential case contact surface to differential case
inner bottom.
B: Total thickness of friction discs, friction plates, spring disc and
spring plate in differential case on one side.
C: Length of differential case contact surface to back side of side
gear.
1. Measure values of ªAº.
Standard length A:
49.50 - 49.55 mm (1.9488 - 1.9508 in)
SPD420
2. Measure thickness of each disc and plate.
Total thickness ªBº:
19.24 - 20.26 mm (0.7575 - 0.7976 in)
REAR FINAL DRIVEH233B
Limited Slip Differential (Cont'd)
PD-50
Page 2076 of 2395
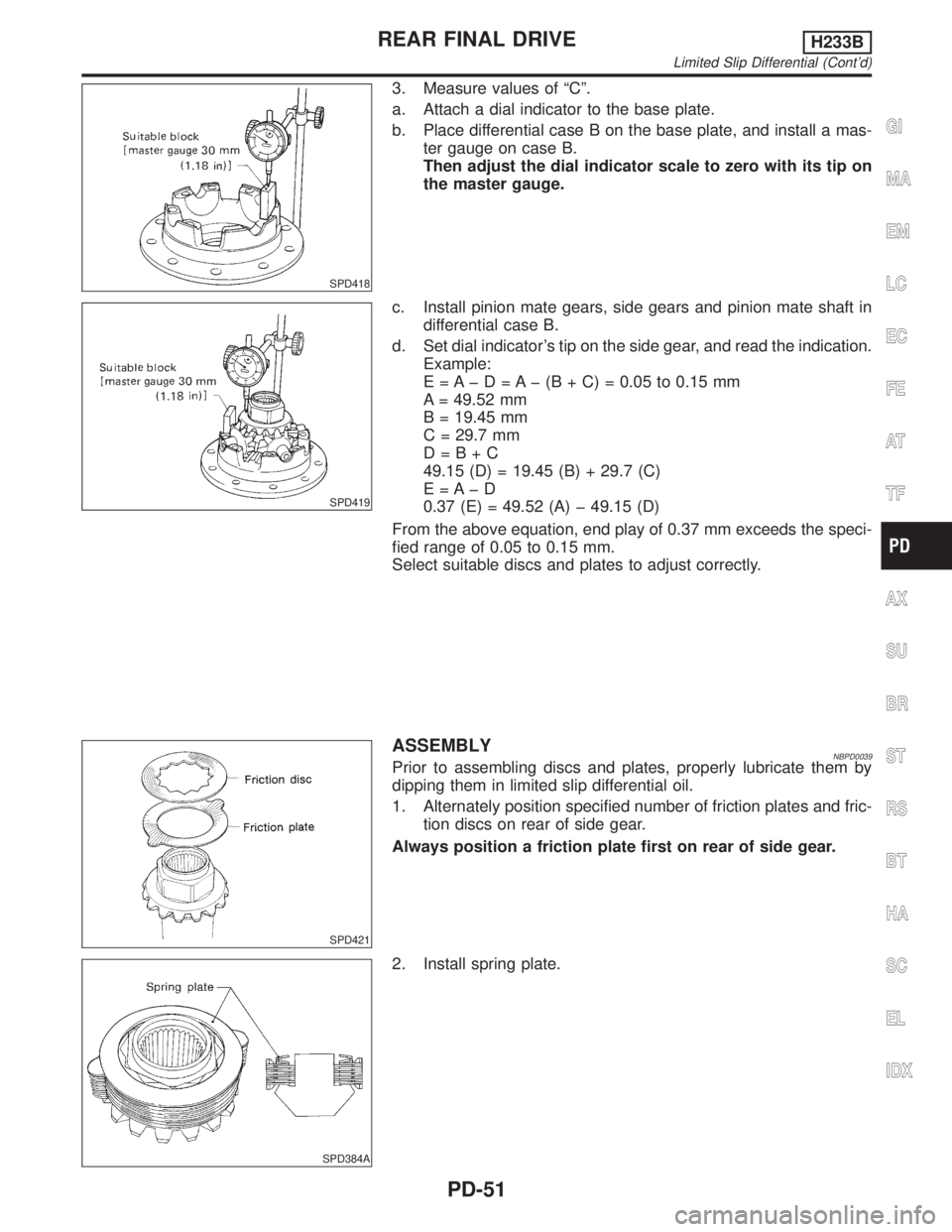
SPD418
3. Measure values of ªCº.
a. Attach a dial indicator to the base plate.
b. Place differential case B on the base plate, and install a mas-
ter gauge on case B.
Then adjust the dial indicator scale to zero with its tip on
the master gauge.
SPD419
c. Install pinion mate gears, side gears and pinion mate shaft in
differential case B.
d. Set dial indicator's tip on the side gear, and read the indication.
Example:
E = A þ D = A þ (B + C) = 0.05 to 0.15 mm
A = 49.52 mm
B = 19.45 mm
C = 29.7 mm
D=B+C
49.15 (D) = 19.45 (B) + 29.7 (C)
E =Aþ D
0.37 (E) = 49.52 (A) þ 49.15 (D)
From the above equation, end play of 0.37 mm exceeds the speci-
fied range of 0.05 to 0.15 mm.
Select suitable discs and plates to adjust correctly.
SPD421
ASSEMBLYNBPD0039Prior to assembling discs and plates, properly lubricate them by
dipping them in limited slip differential oil.
1. Alternately position specified number of friction plates and fric-
tion discs on rear of side gear.
Always position a friction plate first on rear of side gear.
SPD384A
2. Install spring plate.
GI
MA
EM
LC
EC
FE
AT
TF
AX
SU
BR
ST
RS
BT
HA
SC
EL
IDX
REAR FINAL DRIVEH233B
Limited Slip Differential (Cont'd)
PD-51
Page 2077 of 2395
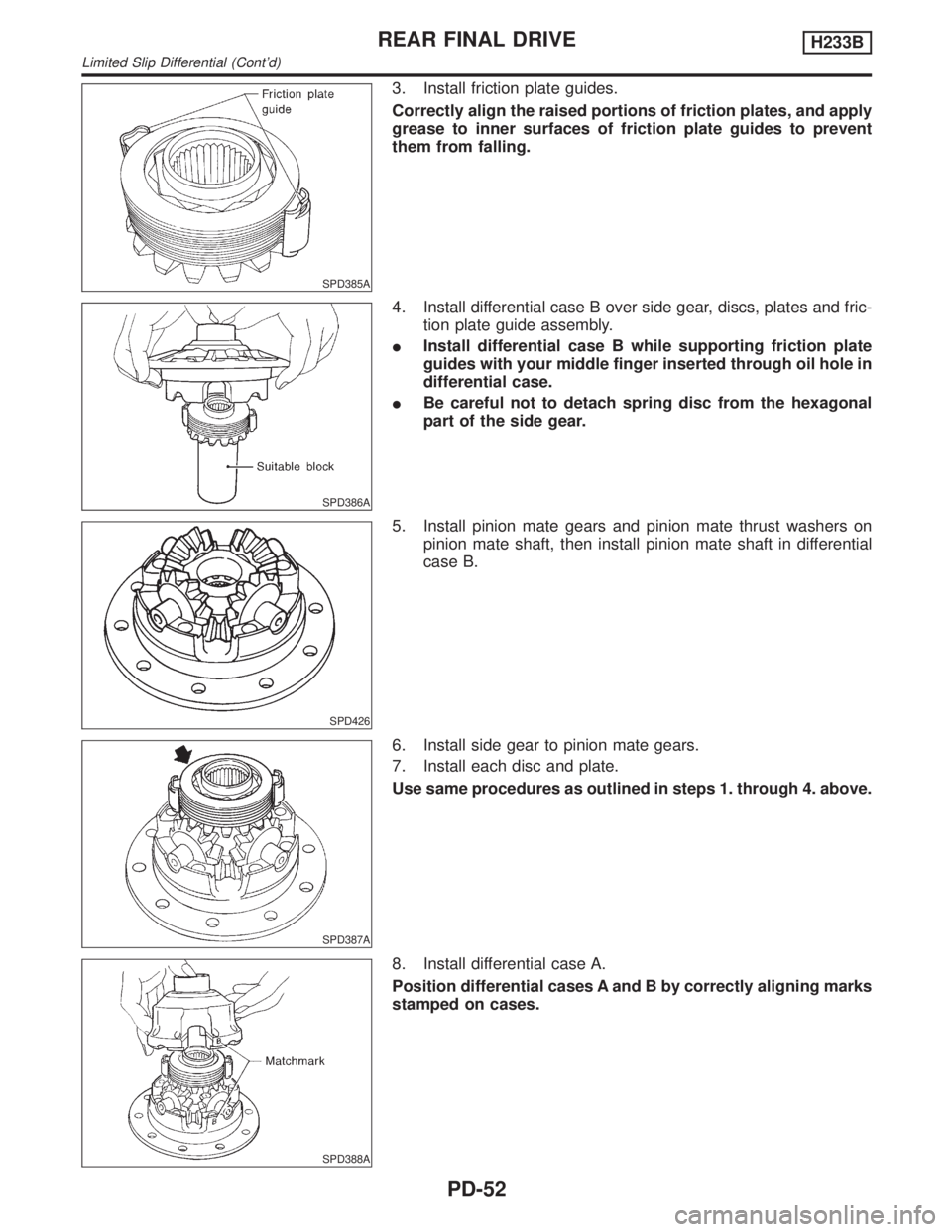
SPD385A
3. Install friction plate guides.
Correctly align the raised portions of friction plates, and apply
grease to inner surfaces of friction plate guides to prevent
them from falling.
SPD386A
4. Install differential case B over side gear, discs, plates and fric-
tion plate guide assembly.
IInstall differential case B while supporting friction plate
guides with your middle finger inserted through oil hole in
differential case.
IBe careful not to detach spring disc from the hexagonal
part of the side gear.
SPD426
5. Install pinion mate gears and pinion mate thrust washers on
pinion mate shaft, then install pinion mate shaft in differential
case B.
SPD387A
6. Install side gear to pinion mate gears.
7. Install each disc and plate.
Use same procedures as outlined in steps 1. through 4. above.
SPD388A
8. Install differential case A.
Position differential cases A and B by correctly aligning marks
stamped on cases.
REAR FINAL DRIVEH233B
Limited Slip Differential (Cont'd)
PD-52
Page 2078 of 2395
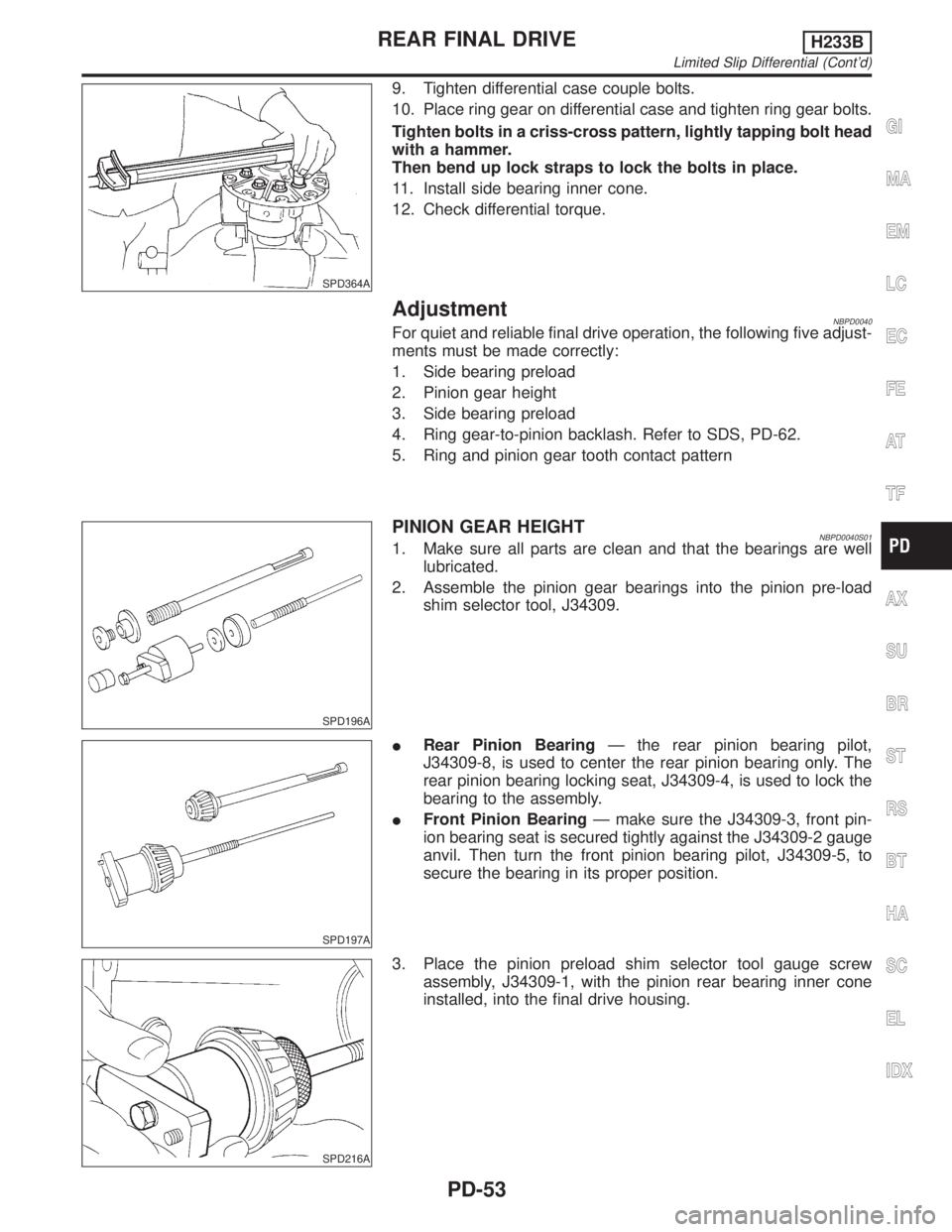
SPD364A
9. Tighten differential case couple bolts.
10. Place ring gear on differential case and tighten ring gear bolts.
Tighten bolts in a criss-cross pattern, lightly tapping bolt head
with a hammer.
Then bend up lock straps to lock the bolts in place.
11. Install side bearing inner cone.
12. Check differential torque.
AdjustmentNBPD0040For quiet and reliable final drive operation, the following five adjust-
ments must be made correctly:
1. Side bearing preload
2. Pinion gear height
3. Side bearing preload
4. Ring gear-to-pinion backlash. Refer to SDS, PD-62.
5. Ring and pinion gear tooth contact pattern
SPD196A
PINION GEAR HEIGHTNBPD0040S011. Make sure all parts are clean and that the bearings are well
lubricated.
2. Assemble the pinion gear bearings into the pinion pre-load
shim selector tool, J34309.
SPD197A
IRear Pinion BearingÐ the rear pinion bearing pilot,
J34309-8, is used to center the rear pinion bearing only. The
rear pinion bearing locking seat, J34309-4, is used to lock the
bearing to the assembly.
IFront Pinion BearingÐ make sure the J34309-3, front pin-
ion bearing seat is secured tightly against the J34309-2 gauge
anvil. Then turn the front pinion bearing pilot, J34309-5, to
secure the bearing in its proper position.
SPD216A
3. Place the pinion preload shim selector tool gauge screw
assembly, J34309-1, with the pinion rear bearing inner cone
installed, into the final drive housing.
GI
MA
EM
LC
EC
FE
AT
TF
AX
SU
BR
ST
RS
BT
HA
SC
EL
IDX
REAR FINAL DRIVEH233B
Limited Slip Differential (Cont'd)
PD-53
Page 2079 of 2395
SPD217A
4. Install the J34309-2 gauge anvil with the front pinion bearing
into the final drive housing and assemble it to the J34309-1
gauge screw. Make sure that the J34309-16 gauge plate will
turn a full 360 degrees, and tighten the two sections by hand
to set bearing pre-load.
5. Turn the assembly several times to seat the bearings.
SPD234A
6. Measure the turning torque at the end of the J34309-2 gauge
anvil using torque wrench J25765A.
Turning torque specification:
0.4 - 0.9 N´m (4 - 9 kg-cm, 3.5 - 7.8 in-lb)
SPD208A
7. Place the J34309-12 ªH233Bº pinion height adapter onto the
gauge plate and tighten it by hand.
CAUTION:
Make sure all machined surfaces are clean.
SPD286A
PINION HEIGHT ADJUSTING WASHER SELECTION
8. Position the J25269-18 side bearing discs and the arbor into
the side bearing bores.
SPD237A
9. Install the bearing caps and torque the bolts.
Specification:
93 - 103 N´m (9.5 - 10.5 kg-m, 69 - 76 ft-lb)
REAR FINAL DRIVEH233B
Adjustment (Cont'd)
PD-54
Page 2080 of 2395
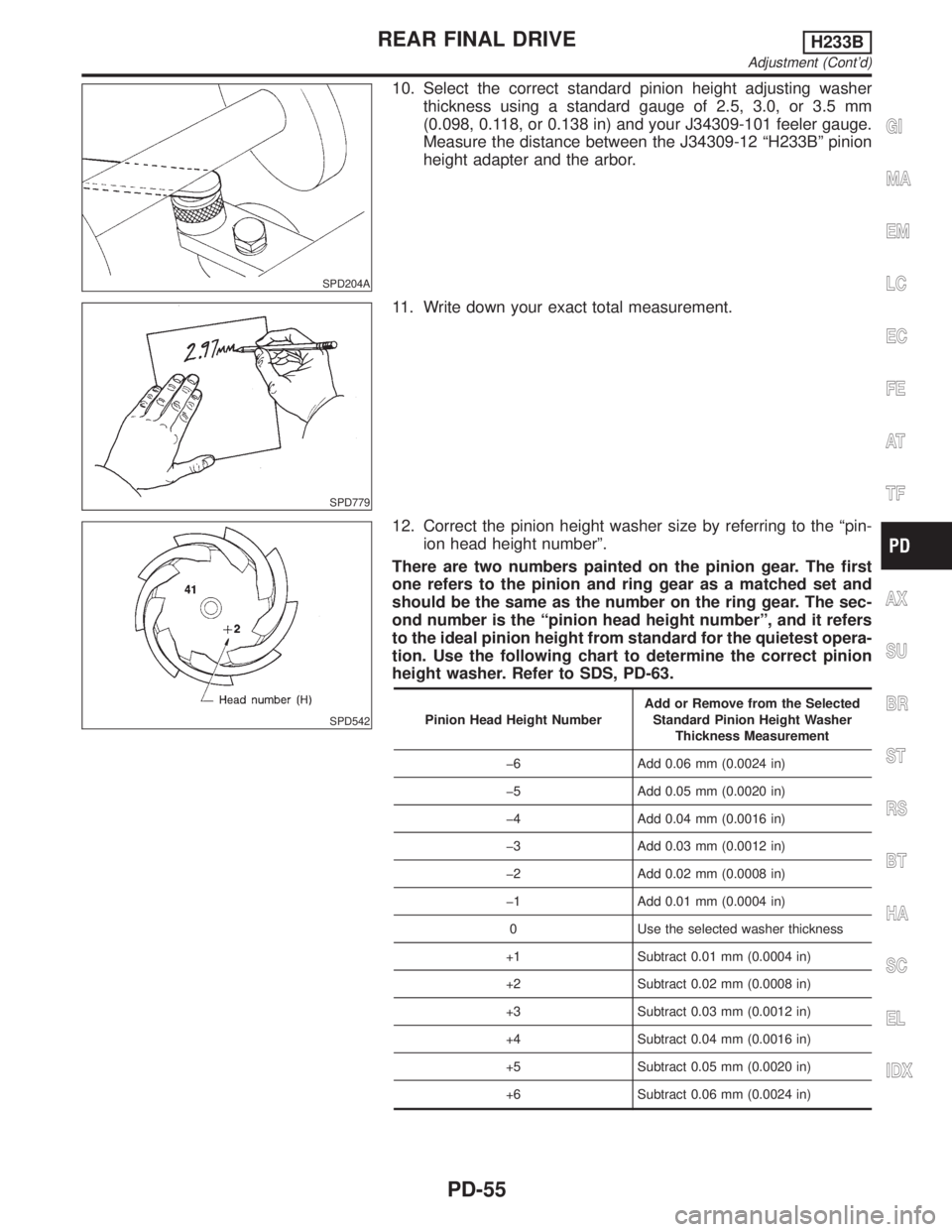
SPD204A
10. Select the correct standard pinion height adjusting washer
thickness using a standard gauge of 2.5, 3.0, or 3.5 mm
(0.098, 0.118, or 0.138 in) and your J34309-101 feeler gauge.
Measure the distance between the J34309-12 ªH233Bº pinion
height adapter and the arbor.
SPD779
11. Write down your exact total measurement.
SPD542
12. Correct the pinion height washer size by referring to the ªpin-
ion head height numberº.
There are two numbers painted on the pinion gear. The first
one refers to the pinion and ring gear as a matched set and
should be the same as the number on the ring gear. The sec-
ond number is the ªpinion head height numberº, and it refers
to the ideal pinion height from standard for the quietest opera-
tion. Use the following chart to determine the correct pinion
height washer. Refer to SDS, PD-63.
Pinion Head Height NumberAdd or Remove from the Selected
Standard Pinion Height Washer
Thickness Measurement
þ6 Add 0.06 mm (0.0024 in)
þ5 Add 0.05 mm (0.0020 in)
þ4 Add 0.04 mm (0.0016 in)
þ3 Add 0.03 mm (0.0012 in)
þ2 Add 0.02 mm (0.0008 in)
þ1 Add 0.01 mm (0.0004 in)
0 Use the selected washer thickness
+1 Subtract 0.01 mm (0.0004 in)
+2 Subtract 0.02 mm (0.0008 in)
+3 Subtract 0.03 mm (0.0012 in)
+4 Subtract 0.04 mm (0.0016 in)
+5 Subtract 0.05 mm (0.0020 in)
+6 Subtract 0.06 mm (0.0024 in)
GI
MA
EM
LC
EC
FE
AT
TF
AX
SU
BR
ST
RS
BT
HA
SC
EL
IDX
REAR FINAL DRIVEH233B
Adjustment (Cont'd)
PD-55