Page 977 of 2395
Wiring DiagramNBEC0269
MEC968C
DTC P0600 A/T COMMUNICATION LINE
Wiring Diagram
EC-442
Page 978 of 2395

Diagnostic ProcedureNBEC0270
1 CHECK A/T CONTROL INPUT SIGNAL CIRCUIT FOR OPEN
1. Turn ignition switch ªOFFº.
2. Disconnect ECM harness connector and TCM (Transmission Control Module) harness connector.
SEF955Y
SEF001Z
3. Check harness continuity between ECM terminal 114 and TCM terminal 33.
Refer to Wiring Diagram.
Continuity should exist.
OK or NG
OK©GO TO 3.
NG©GO TO 2.
2 DETECT MALFUNCTION PART
Check the following.
IHarness connectors M94, F27
IHarness for open or short between ECM and TCM (Transmission control module)
©Repair harness or connectors.
3 CHECK A/T CONTROL INPUT SIGNAL CIRCUIT FOR SHORT
1. Check harness continuity between ECM terminal 114 and ground.
Refer to Wiring Diagram.
Continuity should not exist.
2. Also check harness for short to power.
OK or NG
OK©GO TO 4.
NG©Repair short to ground or short to power in harness or connectos.
4 CHECK INTERMITTENT INCIDENT
Refer to ªTROUBLE DIAGNOSIS FOR INTERMITTENT INCIDENTº, EC-140.
©INSPECTION END
GI
MA
EM
LC
FE
AT
TF
PD
AX
SU
BR
ST
RS
BT
HA
SC
EL
IDX
DTC P0600 A/T COMMUNICATION LINE
Diagnostic Procedure
EC-443
Page 979 of 2395
SEC220B
Component DescriptionNBEC0271The ECM consists of a microcomputer and connectors for signal
input and output and for power supply. The unit controls the engine.
On Board Diagnosis LogicNBEC0272Malfunction is detected when ECM calculation function is
malfunctioning.
Possible CauseNBEC0518IECM
DTC Confirmation ProcedureNBEC0273NOTE:
If ªDTC Confirmation Procedureº has been previously conducted,
always turn ignition switch ªOFFº and wait at least 10 seconds
before conducting the next test.
SEF058Y
WITH CONSULT-IINBEC0273S011) Turn ignition switch ªONº.
2) Select ªDATA MONITORº mode with CONSULT-II.
3) Start engine.
4) Run engine for at least 30 seconds at idle speed.
5) If 1st trip DTC is detected, go to ªDiagnostic Procedureº,
EC-445.
WITH GSTNBEC0273S02Follow the procedure ªWITH CONSULT-IIº above.
DTC P0605 ECM
Component Description
EC-444
Page 980 of 2395
Diagnostic ProcedureNBEC0274
1 INSPECTION START
With CONSULT-II
1. Turn ignition switch ªONº.
2. Select ªSELF DIAG RESULTSº mode with CONSULT-II.
3. Touch ªERASEº.
4.Perform ªDTC Confirmation Procedureº.
See EC-444.
5. Is the 1st trip DTC P0605 displayed again?
With GST
1. Turn ignition switch ªONº.
2. Select MODE 4 with GST.
3. Touch ªERASEº.
4.Perform ªDTC Confirmation Procedureº.
See EC-444.
5. Is the 1st trip DTC P0605 displayed again?
YesorNo
Ye s©GO TO 2.
No©INSPECTION END
2 REPLACE ECM
1. Replace ECM.
2. Perform initialization of NVIS (NATS) system and registration of all NVIS (NATS) ignition key IDs. Refer to ªNVIS (NIS-
SAN VEHICLE IMMOBILIZER SYSTEM Ð NATS)º, EC-74.
3. Perform ªIdle Air Volume Learningº, EC-57,
Is the result CMPLT or INCMP?
CMPLT or INCMP
CMPLT©INSPECTION END
INCMP©Follow the construction of ªIdle Air Volume Learningº.
GI
MA
EM
LC
FE
AT
TF
PD
AX
SU
BR
ST
RS
BT
HA
SC
EL
IDX
DTC P0605 ECM
Diagnostic Procedure
EC-445
Page 981 of 2395
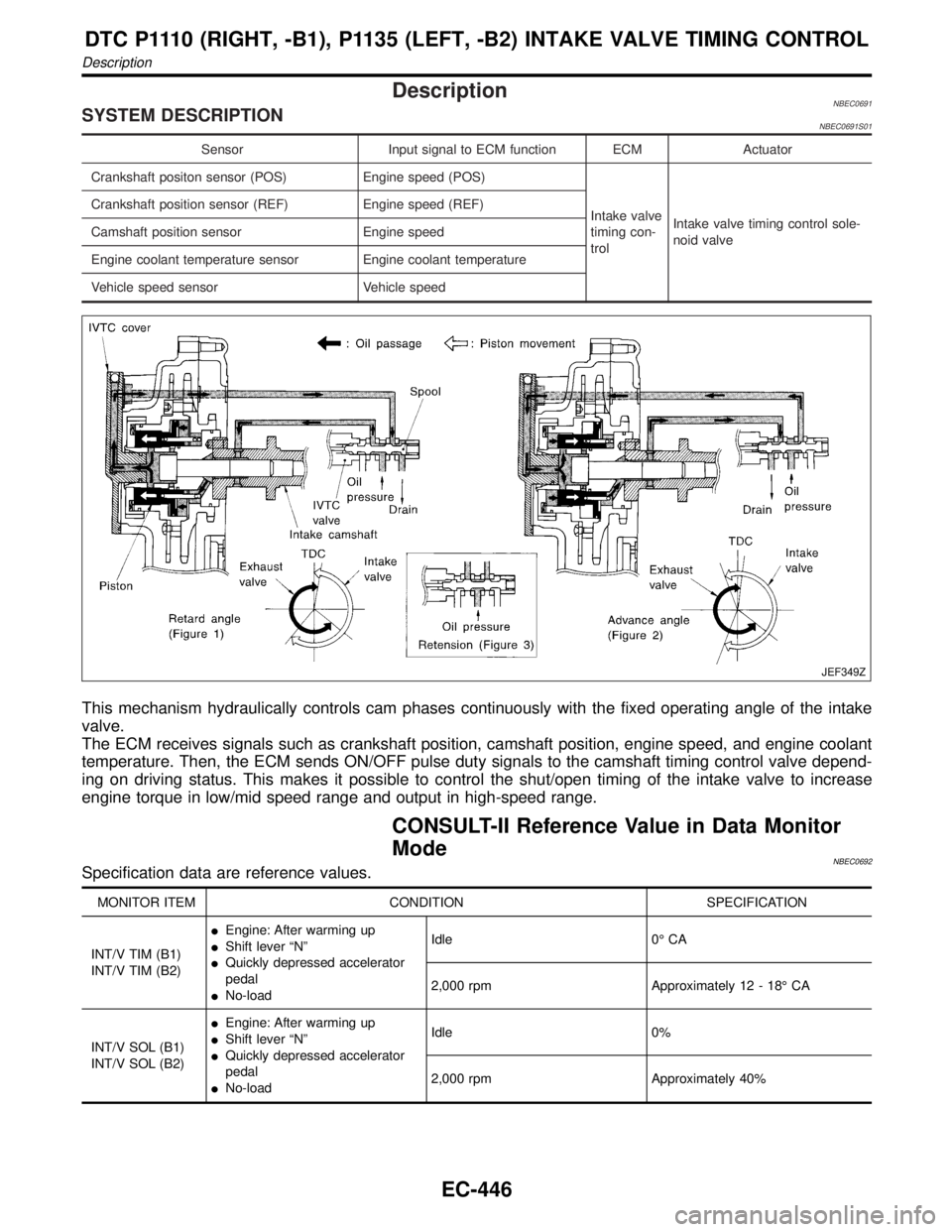
DescriptionNBEC0691SYSTEM DESCRIPTIONNBEC0691S01
Sensor Input signal to ECM function ECM Actuator
Crankshaft positon sensor (POS) Engine speed (POS)
Intake valve
timing con-
trolIntake valve timing control sole-
noid valve Crankshaft position sensor (REF) Engine speed (REF)
Camshaft position sensor Engine speed
Engine coolant temperature sensor Engine coolant temperature
Vehicle speed sensor Vehicle speed
JEF349Z
This mechanism hydraulically controls cam phases continuously with the fixed operating angle of the intake
valve.
The ECM receives signals such as crankshaft position, camshaft position, engine speed, and engine coolant
temperature. Then, the ECM sends ON/OFF pulse duty signals to the camshaft timing control valve depend-
ing on driving status. This makes it possible to control the shut/open timing of the intake valve to increase
engine torque in low/mid speed range and output in high-speed range.
CONSULT-II Reference Value in Data Monitor
Mode
NBEC0692Specification data are reference values.
MONITOR ITEM CONDITION SPECIFICATION
INT/V TIM (B1)
INT/V TIM (B2)IEngine: After warming up
IShift lever ªNº
IQuickly depressed accelerator
pedal
INo-loadIdle 0É CA
2,000 rpm Approximately 12 - 18É CA
INT/V SOL (B1)
INT/V SOL (B2)IEngine: After warming up
IShift lever ªNº
IQuickly depressed accelerator
pedal
INo-loadIdle 0%
2,000 rpm Approximately 40%
DTC P1110 (RIGHT, -B1), P1135 (LEFT, -B2) INTAKE VALVE TIMING CONTROL
Description
EC-446
Page 982 of 2395
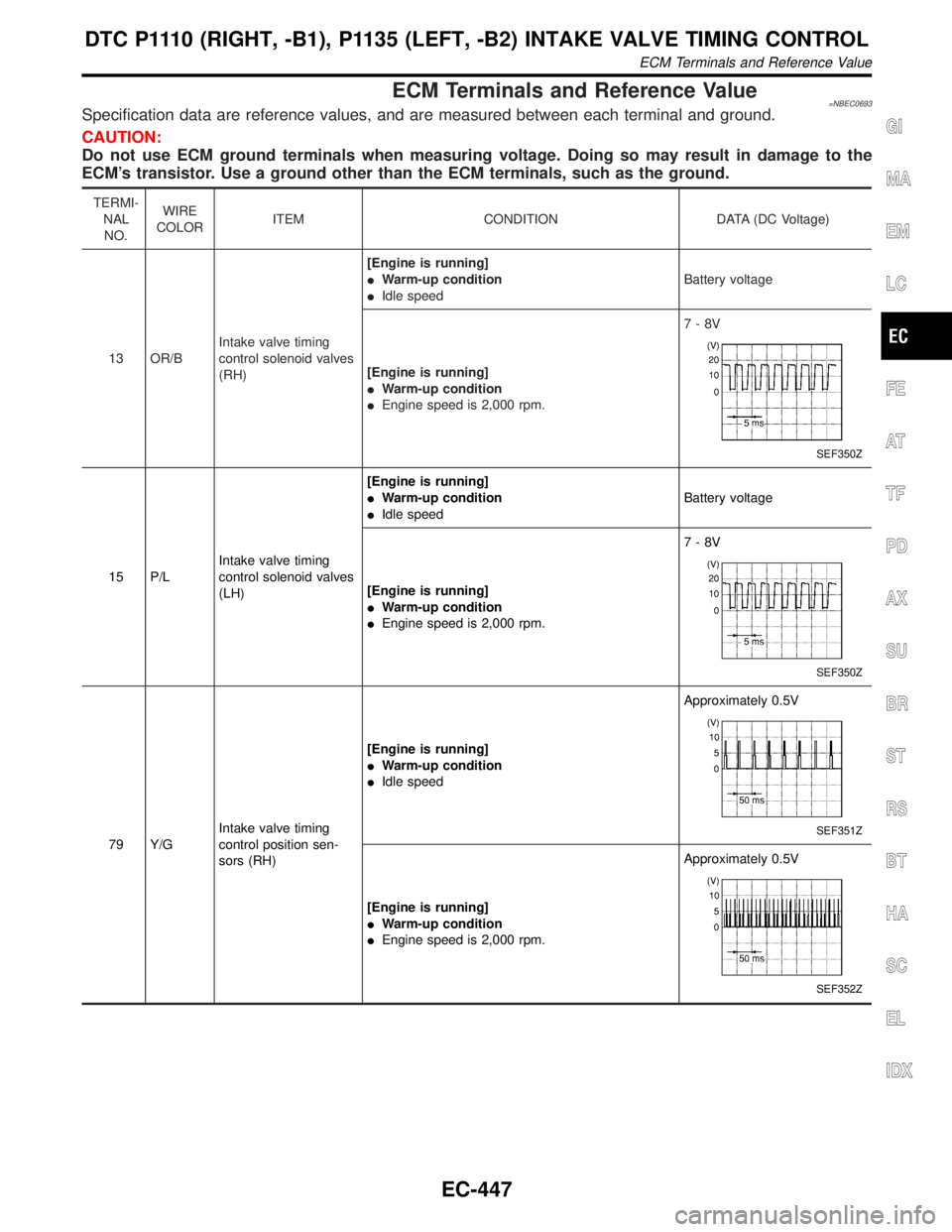
ECM Terminals and Reference Value=NBEC0693Specification data are reference values, and are measured between each terminal and ground.
CAUTION:
Do not use ECM ground terminals when measuring voltage. Doing so may result in damage to the
ECM's transistor. Use a ground other than the ECM terminals, such as the ground.
TERMI-
NAL
NO.WIRE
COLORITEM CONDITION DATA (DC Voltage)
13 OR/BIntake valve timing
control solenoid valves
(RH)[Engine is running]
IWarm-up condition
IIdle speedBattery voltage
[Engine is running]
IWarm-up condition
IEngine speed is 2,000 rpm.7-8V
SEF350Z
15 P/LIntake valve timing
control solenoid valves
(LH)[Engine is running]
IWarm-up condition
IIdle speedBattery voltage
[Engine is running]
IWarm-up condition
IEngine speed is 2,000 rpm.7-8V
SEF350Z
79 Y/GIntake valve timing
control position sen-
sors (RH)[Engine is running]
IWarm-up condition
IIdle speedApproximately 0.5VSEF351Z
[Engine is running]
IWarm-up condition
IEngine speed is 2,000 rpm.Approximately 0.5V
SEF352Z
GI
MA
EM
LC
FE
AT
TF
PD
AX
SU
BR
ST
RS
BT
HA
SC
EL
IDX
DTC P1110 (RIGHT, -B1), P1135 (LEFT, -B2) INTAKE VALVE TIMING CONTROL
ECM Terminals and Reference Value
EC-447
Page 983 of 2395
![INFINITI QX4 2001 Factory Service Manual TERMI-
NAL
NO.WIRE
COLORITEM CONDITION DATA (DC Voltage)
89 ORIntake valve timing
control position sen-
sors (LH)[Engine is running]
IWarm-up condition
IIdle speedApproximately 0.5V
SEF351Z
[Engine is INFINITI QX4 2001 Factory Service Manual TERMI-
NAL
NO.WIRE
COLORITEM CONDITION DATA (DC Voltage)
89 ORIntake valve timing
control position sen-
sors (LH)[Engine is running]
IWarm-up condition
IIdle speedApproximately 0.5V
SEF351Z
[Engine is](/manual-img/42/57027/w960_57027-982.png)
TERMI-
NAL
NO.WIRE
COLORITEM CONDITION DATA (DC Voltage)
89 ORIntake valve timing
control position sen-
sors (LH)[Engine is running]
IWarm-up condition
IIdle speedApproximately 0.5V
SEF351Z
[Engine is running]
IWarm-up condition
IEngine speed is 2,000 rpm.Approximately 0.5V
SEF352Z
On Board Diagnosis LogicNBEC0694Malfunction is detected when:
(Malfunction A)
The alignment of the intake valve timing control has been misreg-
istered.
(Malfunction B)
There is a gap between angle of target and phase-control angle
degree.
FAIL-SAFE MODENBEC0694S01When malfunction A or B is detected, the ECM enters fail-safe
mode and the MIL lights up.
Detected items Engine operating condition in fail-safe mode
Intake valve timing control The signal is not energized to the solenoid valve and the valve control does not function.
Possible CauseNBEC0695MALFUNCTION A OR BNBEC0695S01IHarness or connectors
(Intake valve timing control position sensor circuit is open or
shorted.) Refer to EC-482.
ICrankshaft position sensor (REF)
ICrankshaft position sensor (POS)
ICamshaft position sensor (PHASE)
DTC P1110 (RIGHT, -B1), P1135 (LEFT, -B2) INTAKE VALVE TIMING CONTROL
ECM Terminals and Reference Value (Cont'd)
EC-448
Page 984 of 2395
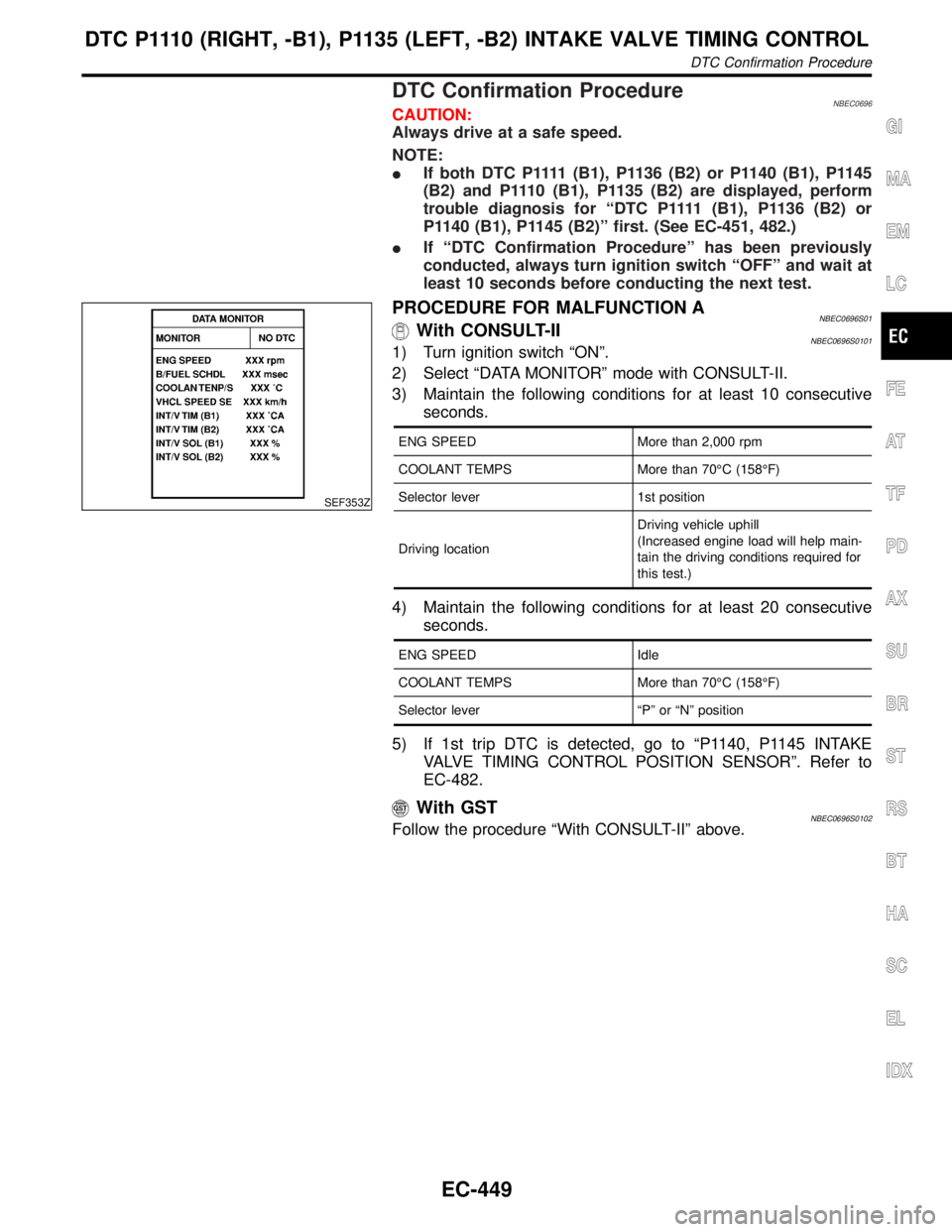
DTC Confirmation ProcedureNBEC0696CAUTION:
Always drive at a safe speed.
NOTE:
IIf both DTC P1111(B1), P1136 (B2) or P1140 (B1), P1145
(B2) and P1110 (B1), P1135 (B2) are displayed, perform
trouble diagnosis for ªDTC P1111(B1), P1136 (B2) or
P1140 (B1), P1145 (B2)º first. (See EC-451, 482.)
IIf ªDTC Confirmation Procedureº has been previously
conducted, always turn ignition switch ªOFFº and wait at
least 10 seconds before conducting the next test.
SEF353Z
PROCEDURE FOR MALFUNCTION ANBEC0696S01With CONSULT-IINBEC0696S01011) Turn ignition switch ªONº.
2) Select ªDATA MONITORº mode with CONSULT-II.
3) Maintain the following conditions for at least 10 consecutive
seconds.
ENG SPEED More than 2,000 rpm
COOLANT TEMPS More than 70ÉC (158ÉF)
Selector lever 1st position
Driving locationDriving vehicle uphill
(Increased engine load will help main-
tain the driving conditions required for
this test.)
4) Maintain the following conditions for at least 20 consecutive
seconds.
ENG SPEED Idle
COOLANT TEMPS More than 70ÉC (158ÉF)
Selector lever ªPº or ªNº position
5) If 1st trip DTC is detected, go to ªP1140, P1145 INTAKE
VALVE TIMING CONTROL POSITION SENSORº. Refer to
EC-482.
With GSTNBEC0696S0102Follow the procedure ªWith CONSULT-IIº above.
GI
MA
EM
LC
FE
AT
TF
PD
AX
SU
BR
ST
RS
BT
HA
SC
EL
IDX
DTC P1110 (RIGHT, -B1), P1135 (LEFT, -B2) INTAKE VALVE TIMING CONTROL
DTC Confirmation Procedure
EC-449