Page 2233 of 4083
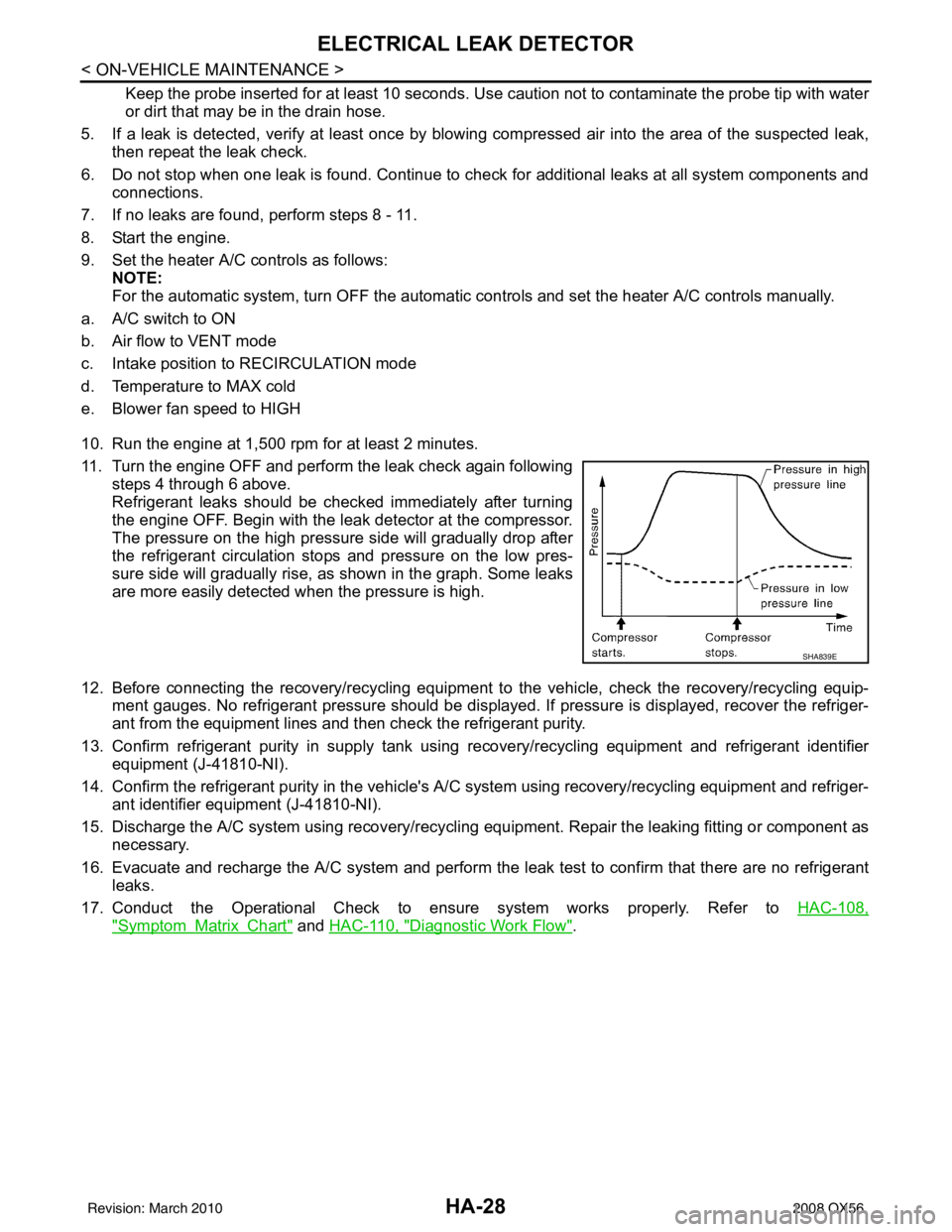
HA-28
< ON-VEHICLE MAINTENANCE >
ELECTRICAL LEAK DETECTOR
Keep the probe inserted for at least 10 seconds. Use caution not to contaminate the probe tip with water
or dirt that may be in the drain hose.
5. If a leak is detected, verify at least once by blowing compressed air into the area of the suspected leak, then repeat the leak check.
6. Do not stop when one leak is found. Continue to check for additional leaks at all system components and connections.
7. If no leaks are found, perform steps 8 - 11.
8. Start the engine.
9. Set the heater A/C controls as follows: NOTE:
For the automatic system, turn OF F the automatic controls and set the heater A/C controls manually.
a. A/C switch to ON
b. Air flow to VENT mode
c. Intake position to RECIRCULATION mode
d. Temperature to MAX cold
e. Blower fan speed to HIGH
10. Run the engine at 1,500 rpm for at least 2 minutes.
11. Turn the engine OFF and perform the leak check again following steps 4 through 6 above.
Refrigerant leaks should be checked immediately after turning
the engine OFF. Begin with the leak detector at the compressor.
The pressure on the high pressure side will gradually drop after
the refrigerant circulation stops and pressure on the low pres-
sure side will gradually rise, as shown in the graph. Some leaks
are more easily detected when the pressure is high.
12. Before connecting the recovery/recycling equipment to the vehicle, check the recovery/recycling equip-
ment gauges. No refrigerant pressure should be displayed. If pressure is displayed, recover the refriger-
ant from the equipment lines and t hen check the refrigerant purity.
13. Confirm refrigerant purity in supply tank using recovery/recycling equipment and refrigerant identifier
equipment (J-41810-NI).
14. Confirm the refrigerant purity in the vehicle's A/C system using recovery/recycling equipment and refriger-
ant identifier equipment (J-41810-NI).
15. Discharge the A/C system using recovery/recycling equipment. Repair the leaking fitting or component as
necessary.
16. Evacuate and recharge the A/C system and perform the leak test to confirm th\
at there are no refrigerant leaks.
17. Conduct the Operational Check to ensure system works properly. Refer to HAC-108,
"SymptomMatrixChart" and HAC-110, "Diagnostic Work Flow".
SHA839E
Revision: March 2010 2008 QX56
Page 2234 of 4083
REFRIGERATION SYSTEMHA-29
< ON-VEHICLE REPAIR >
C
DE
F
G H
J
K L
M A
B
HA
N
O P
ON-VEHICLE REPAIR
REFRIGERATION SYSTEM
ComponentINFOID:0000000001516651
Front A/C System
WJIA1578E
Revision: March 2010 2008 QX56
Page 2235 of 4083
HA-30
< ON-VEHICLE REPAIR >
REFRIGERATION SYSTEM
Rear A/C System
NOTE:
Refer to HA-5, "
Precaution for Refrigerant Connection".
1. High-pressure service valve 2. Grommet 3. High-pressure pipe
4. Refrigerant pressure sensor 5. Condenser 6. Compressor shaft seal
7. High-pressure flexible hose 8. Low-pressure flexible hose 9. Low-pressure service valve
10. Low-pressure pipe 11. Expansion valve (front)12. Drain hose
AWIIA0134GB
1. Rear heater and cooling unit assembly 2. Rear A/C pipes 3. Rear A/C heater core pipes
4. Rear heater core hose 5. Rear blower motor6. Underfloor rear A/C pipes
7. Underfloor rear heater core pipes A. Bolt torque specification B. Leak checking order (l - r)
C. Tightening torque D. Wrench sizeE. O-ring size
⇐ Front
NOTE: The O-ring size 8 is the high-side and the O-ring size 16 is the low-side.
Revision: March 2010 2008 QX56
Page 2236 of 4083
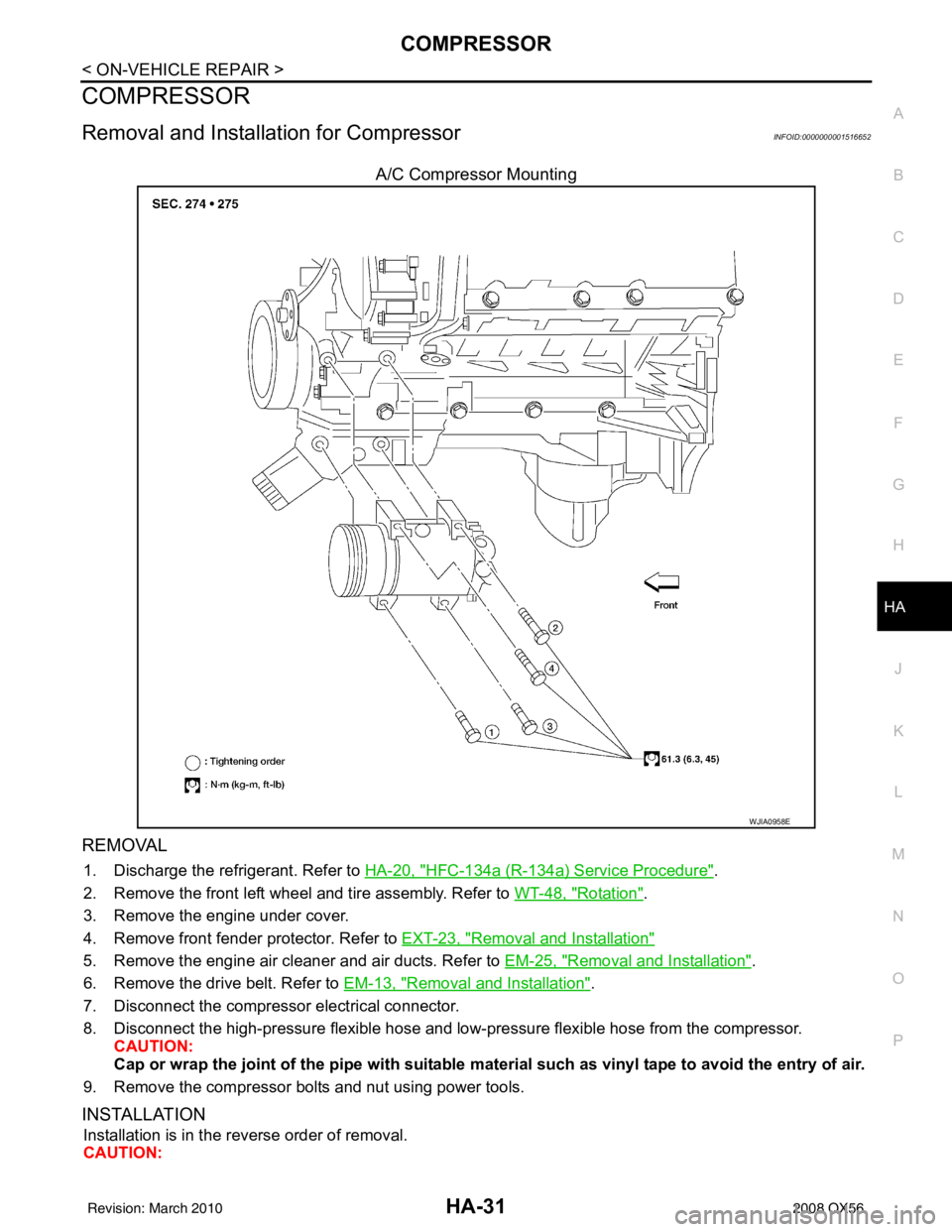
COMPRESSORHA-31
< ON-VEHICLE REPAIR >
C
DE
F
G H
J
K L
M A
B
HA
N
O P
COMPRESSOR
Removal and Installation for CompressorINFOID:0000000001516652
A/C Compressor Mounting
REMOVAL
1. Discharge the refrigerant. Refer to HA-20, "HFC-134a (R-134a) Service Procedure".
2. Remove the front left wheel and tire assembly. Refer to WT-48, "
Rotation".
3. Remove the engine under cover.
4. Remove front fender protector. Refer to EXT-23, "
Removal and Installation"
5. Remove the engine air cleaner and air ducts. Refer to EM-25, "Removal and Installation".
6. Remove the drive belt. Refer to EM-13, "
Removal and Installation".
7. Disconnect the compressor electrical connector.
8. Disconnect the high-pressure flexible hose and low-pressure flexible hose from the compressor. CAUTION:
Cap or wrap the joint of the pipe with suitable mate rial such as vinyl tape to avoid the entry of air.
9. Remove the compressor bolts and nut using power tools.
INSTALLATION
Installation is in the reverse order of removal.
CAUTION:
WJIA0958E
Revision: March 2010 2008 QX56
Page 2237 of 4083
HA-32
< ON-VEHICLE REPAIR >
COMPRESSOR
• Replace the O-rings of the low-pressure flexible hose and high-pressure flexible hose with new
ones, apply compressor oil to the O-rings when installing them.
• After recharging the A/C system with refrigerant, check for leaks.
Removal and Installation for Compressor ClutchINFOID:0000000001516653
Magnet Clutch Assembly
REMOVAL
1. Remove the compressor. Refer to HA-31, "Removal and Installation for Compressor" .
2. Remove the center bolt while holding the clutch disc stationary using Tool as shown.
3. Remove the clutch disc and shims. CAUTION:
Retain all of the shims for installation.
4. Remove the snap ring using external snap ring pliers or suitable tool.
AWIIA1286GB
1. Magnet clutch assembly 2. Magnet coil 3. Pulley
4. Clutch disc 5. Snap ring 6. Thermal protector (built in)
7. Compressor
Tool number : — ( J-44614 )
WHA228
RHA072C
Revision: March 2010 2008 QX56
Page 2238 of 4083
COMPRESSORHA-33
< ON-VEHICLE REPAIR >
C
DE
F
G H
J
K L
M A
B
HA
N
O P
5. Remove the pulley using suitable tool ( A ).
CAUTION:
To prevent deformation of the pulley groove, the puller claws should be hooked under the pulley
groove and not into the pulley groove.
6. Remove the three magnet coil screws using a suitable tool and remove the magnet coil.
INSPECTION
Clutch Disc
If the contact surface shows signs of damage due to excessive heat,
replace clutch disc and pulley.
Pulley
Check the appearance of the pulley assembly. If contact surface of pulley shows signs of excessive grooving,
replace clutch disc and pulley. The contact surfaces of the pulley assembly should be cleaned with a suitable
solvent before reinstallation.
Coil
Check magnet coil for loose connections or any cracked insulation.
INSTALLATION
WJIA1017E
WHA212
WHA183
Revision: March 2010 2008 QX56
Page 2239 of 4083
HA-34
< ON-VEHICLE REPAIR >
COMPRESSOR
1. Install the magnet coil.CAUTION:
Be sure to align the magnet coil pin with the hole in the
compressor front head.
2. Install the pulley assembly using Tool and a wrench, then install the snap ring using snap ring pliers.
3. Install the clutch disc on the compressor shaft, together with the original shim(s). Press the clutch disc down by hand.
4. Install the clutch pulley bolt using Tool, to prevent the clutch disc from turning and tighten the bolt to specification.
CAUTION:
After tightening the clutch pu lley bolt, check that the clutch
pulley rotates smoothly.
WHA213
Tool number : — (J-38873-A)
WJIA1016E
WHA184
Tool number : — ( J-44614 )
WHA229
Revision: March 2010 2008 QX56
Page 2240 of 4083
COMPRESSORHA-35
< ON-VEHICLE REPAIR >
C
DE
F
G H
J
K L
M A
B
HA
N
O P
5. Check the pulley clearance all the way around the clutch disc as shown.
6. If the specified clearance is not obtained, replace the adjusting spacer to readjust.
7. Install compressor. Refer to HA-31, "
Removal and Installation
for Compressor".
BREAK-IN OPERATION
When replacing compressor clutch assembly, always conduct the break-in operation. This is done by engag-
ing and disengaging the clutch about 30 times. Break-in operation raises the level of transmitted torque.
Clutch disc-to-pulley clearance : 0.3 - 0.6 mm
(0.012 - 0.024 in)
WHA194
Revision: March 2010 2008 QX56