Page 49 of 2255
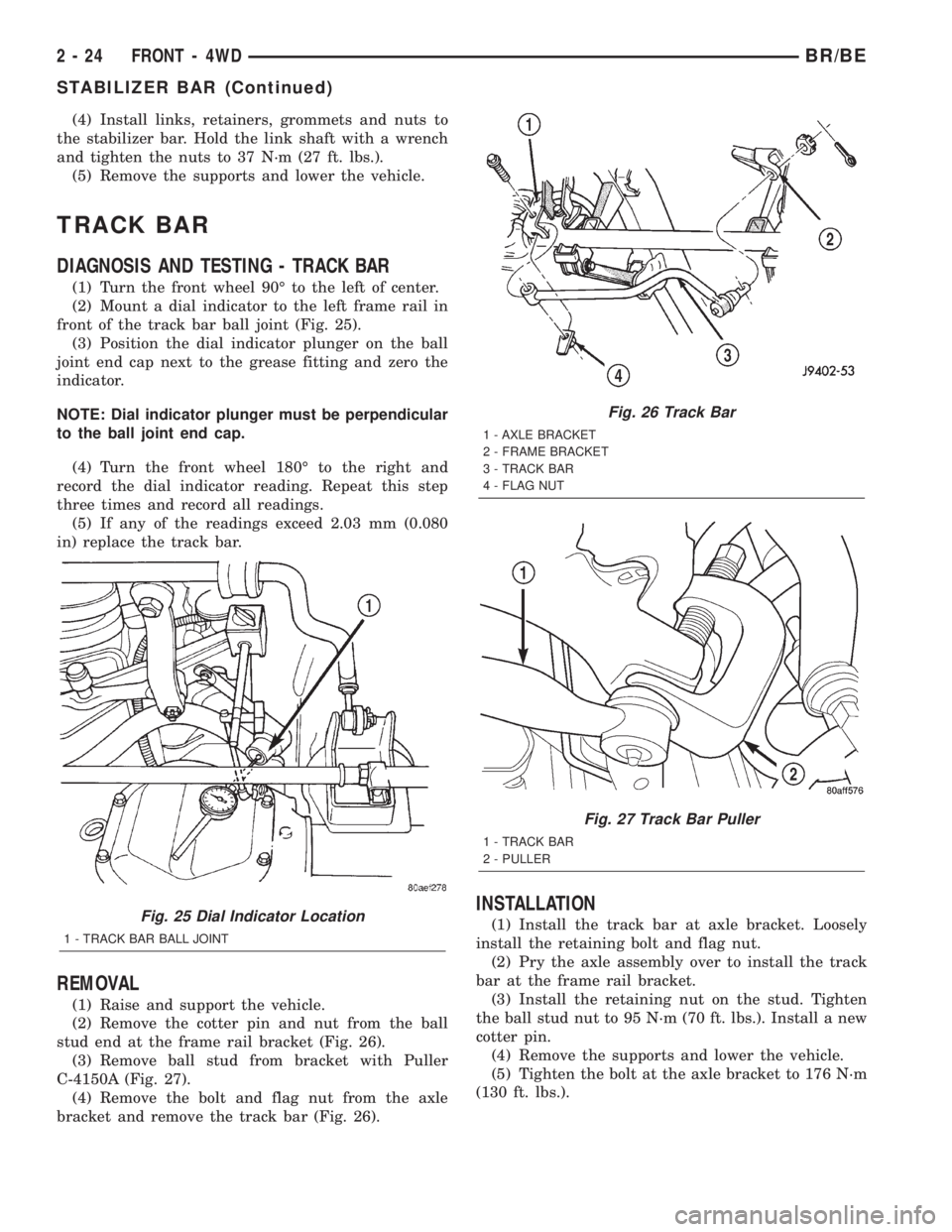
(4) Install links, retainers, grommets and nuts to
the stabilizer bar. Hold the link shaft with a wrench
and tighten the nuts to 37 N´m (27 ft. lbs.).
(5) Remove the supports and lower the vehicle.
TRACK BAR
DIAGNOSIS AND TESTING - TRACK BAR
(1) Turn the front wheel 90É to the left of center.
(2) Mount a dial indicator to the left frame rail in
front of the track bar ball joint (Fig. 25).
(3) Position the dial indicator plunger on the ball
joint end cap next to the grease fitting and zero the
indicator.
NOTE: Dial indicator plunger must be perpendicular
to the ball joint end cap.
(4) Turn the front wheel 180É to the right and
record the dial indicator reading. Repeat this step
three times and record all readings.
(5) If any of the readings exceed 2.03 mm (0.080
in) replace the track bar.
REMOVAL
(1) Raise and support the vehicle.
(2) Remove the cotter pin and nut from the ball
stud end at the frame rail bracket (Fig. 26).
(3) Remove ball stud from bracket with Puller
C-4150A (Fig. 27).
(4) Remove the bolt and flag nut from the axle
bracket and remove the track bar (Fig. 26).
INSTALLATION
(1) Install the track bar at axle bracket. Loosely
install the retaining bolt and flag nut.
(2) Pry the axle assembly over to install the track
bar at the frame rail bracket.
(3) Install the retaining nut on the stud. Tighten
the ball stud nut to 95 N´m (70 ft. lbs.). Install a new
cotter pin.
(4) Remove the supports and lower the vehicle.
(5) Tighten the bolt at the axle bracket to 176 N´m
(130 ft. lbs.).Fig. 25 Dial Indicator Location
1 - TRACK BAR BALL JOINT
Fig. 26 Track Bar
1 - AXLE BRACKET
2 - FRAME BRACKET
3 - TRACK BAR
4 - FLAG NUT
Fig. 27 Track Bar Puller
1 - TRACK BAR
2 - PULLER
2 - 24 FRONT - 4WDBR/BE
STABILIZER BAR (Continued)
Page 50 of 2255
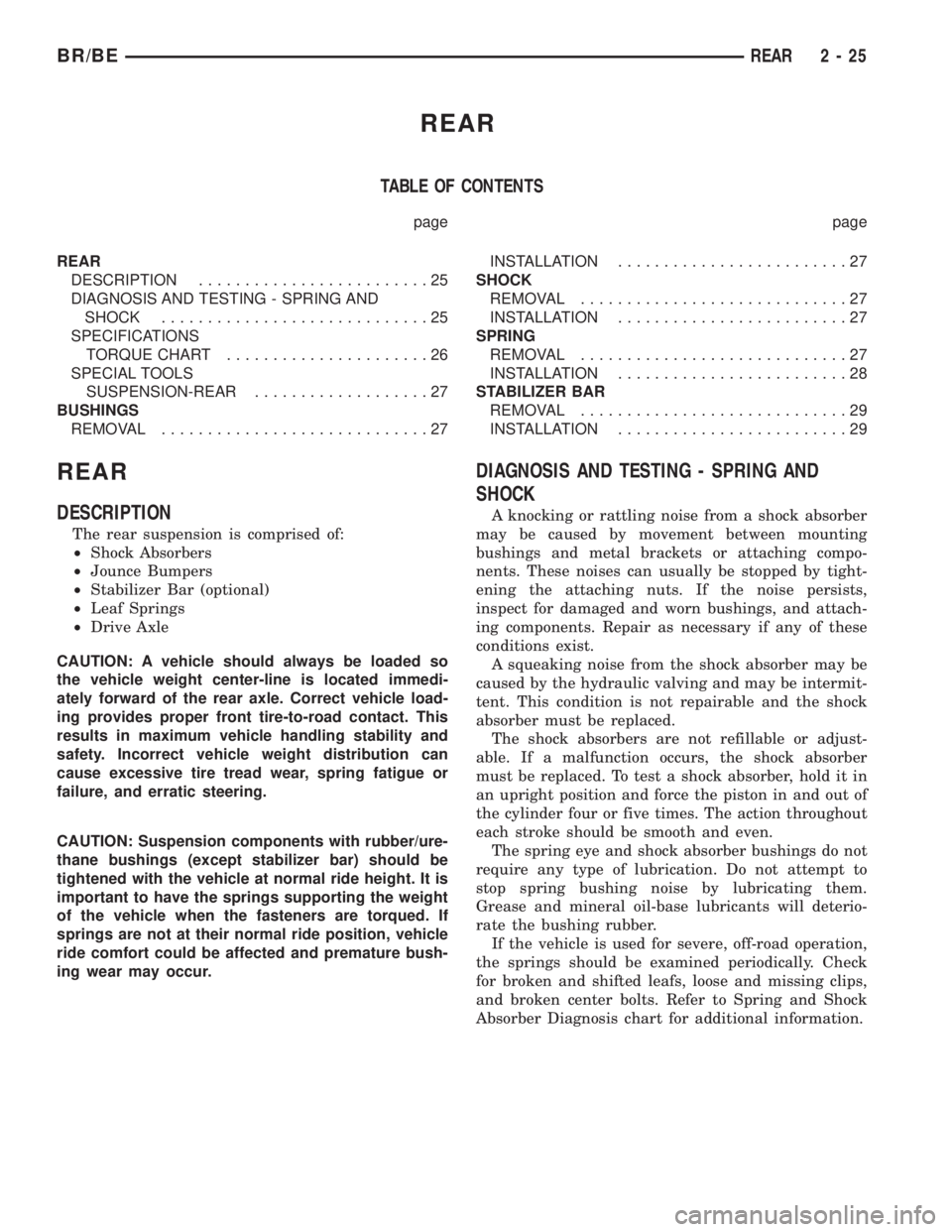
REAR
TABLE OF CONTENTS
page page
REAR
DESCRIPTION.........................25
DIAGNOSIS AND TESTING - SPRING AND
SHOCK.............................25
SPECIFICATIONS
TORQUE CHART......................26
SPECIAL TOOLS
SUSPENSION-REAR...................27
BUSHINGS
REMOVAL.............................27INSTALLATION.........................27
SHOCK
REMOVAL.............................27
INSTALLATION.........................27
SPRING
REMOVAL.............................27
INSTALLATION.........................28
STABILIZER BAR
REMOVAL.............................29
INSTALLATION.........................29
REAR
DESCRIPTION
The rear suspension is comprised of:
²Shock Absorbers
²Jounce Bumpers
²Stabilizer Bar (optional)
²Leaf Springs
²Drive Axle
CAUTION: A vehicle should always be loaded so
the vehicle weight center-line is located immedi-
ately forward of the rear axle. Correct vehicle load-
ing provides proper front tire-to-road contact. This
results in maximum vehicle handling stability and
safety. Incorrect vehicle weight distribution can
cause excessive tire tread wear, spring fatigue or
failure, and erratic steering.
CAUTION: Suspension components with rubber/ure-
thane bushings (except stabilizer bar) should be
tightened with the vehicle at normal ride height. It is
important to have the springs supporting the weight
of the vehicle when the fasteners are torqued. If
springs are not at their normal ride position, vehicle
ride comfort could be affected and premature bush-
ing wear may occur.
DIAGNOSIS AND TESTING - SPRING AND
SHOCK
A knocking or rattling noise from a shock absorber
may be caused by movement between mounting
bushings and metal brackets or attaching compo-
nents. These noises can usually be stopped by tight-
ening the attaching nuts. If the noise persists,
inspect for damaged and worn bushings, and attach-
ing components. Repair as necessary if any of these
conditions exist.
A squeaking noise from the shock absorber may be
caused by the hydraulic valving and may be intermit-
tent. This condition is not repairable and the shock
absorber must be replaced.
The shock absorbers are not refillable or adjust-
able. If a malfunction occurs, the shock absorber
must be replaced. To test a shock absorber, hold it in
an upright position and force the piston in and out of
the cylinder four or five times. The action throughout
each stroke should be smooth and even.
The spring eye and shock absorber bushings do not
require any type of lubrication. Do not attempt to
stop spring bushing noise by lubricating them.
Grease and mineral oil-base lubricants will deterio-
rate the bushing rubber.
If the vehicle is used for severe, off-road operation,
the springs should be examined periodically. Check
for broken and shifted leafs, loose and missing clips,
and broken center bolts. Refer to Spring and Shock
Absorber Diagnosis chart for additional information.
BR/BEREAR 2 - 25
Page 51 of 2255
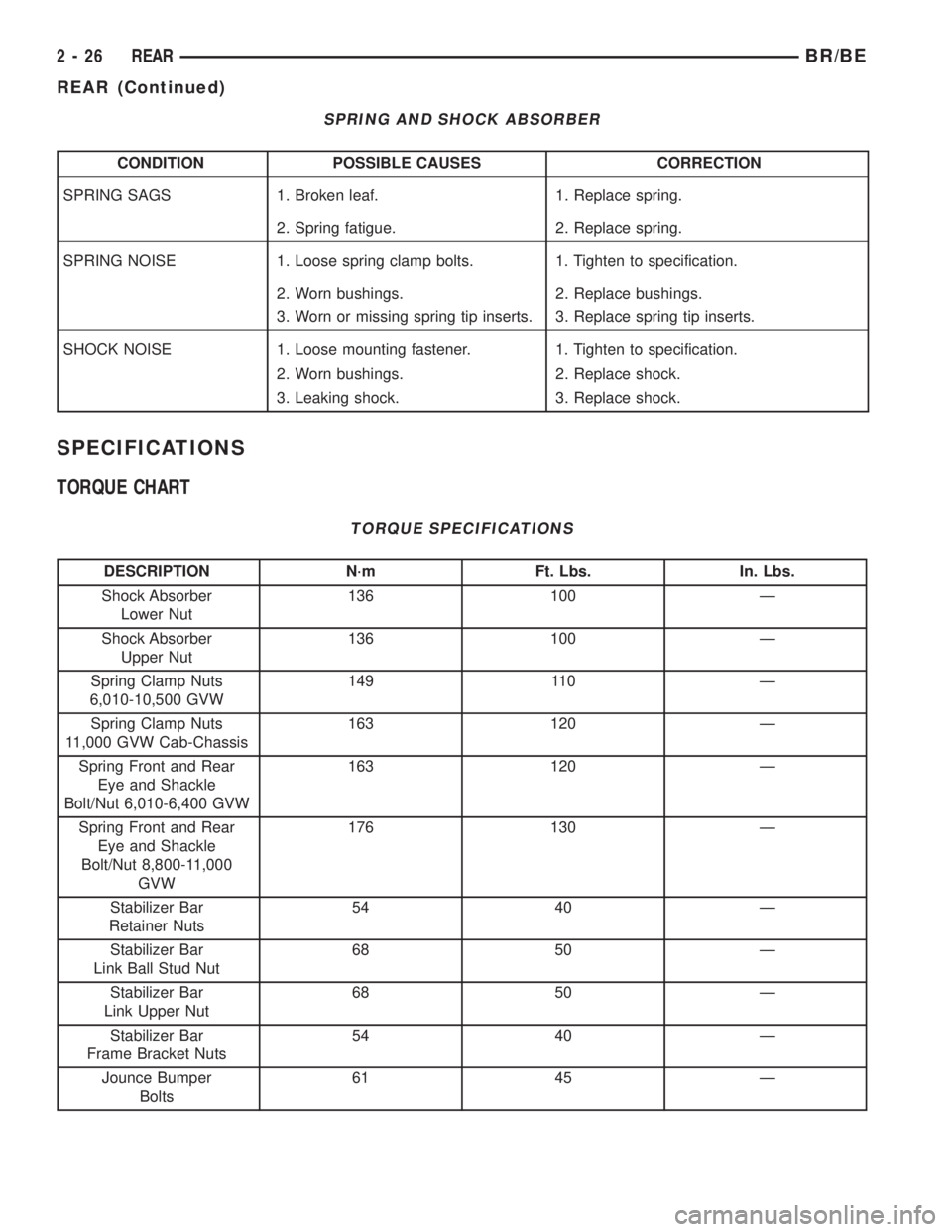
SPRING AND SHOCK ABSORBER
CONDITION POSSIBLE CAUSES CORRECTION
SPRING SAGS 1. Broken leaf. 1. Replace spring.
2. Spring fatigue. 2. Replace spring.
SPRING NOISE 1. Loose spring clamp bolts. 1. Tighten to specification.
2. Worn bushings. 2. Replace bushings.
3. Worn or missing spring tip inserts. 3. Replace spring tip inserts.
SHOCK NOISE 1. Loose mounting fastener. 1. Tighten to specification.
2. Worn bushings. 2. Replace shock.
3. Leaking shock. 3. Replace shock.
SPECIFICATIONS
TORQUE CHART
TORQUE SPECIFICATIONS
DESCRIPTION N´m Ft. Lbs. In. Lbs.
Shock Absorber
Lower Nut136 100 Ð
Shock Absorber
Upper Nut136 100 Ð
Spring Clamp Nuts
6,010-10,500 GVW149 110 Ð
Spring Clamp Nuts
11,000 GVW Cab-Chassis163 120 Ð
Spring Front and Rear
Eye and Shackle
Bolt/Nut 6,010-6,400 GVW163 120 Ð
Spring Front and Rear
Eye and Shackle
Bolt/Nut 8,800-11,000
GVW176 130 Ð
Stabilizer Bar
Retainer Nuts54 40 Ð
Stabilizer Bar
Link Ball Stud Nut68 50 Ð
Stabilizer Bar
Link Upper Nut68 50 Ð
Stabilizer Bar
Frame Bracket Nuts54 40 Ð
Jounce Bumper
Bolts61 45 Ð
2 - 26 REARBR/BE
REAR (Continued)
Page 52 of 2255
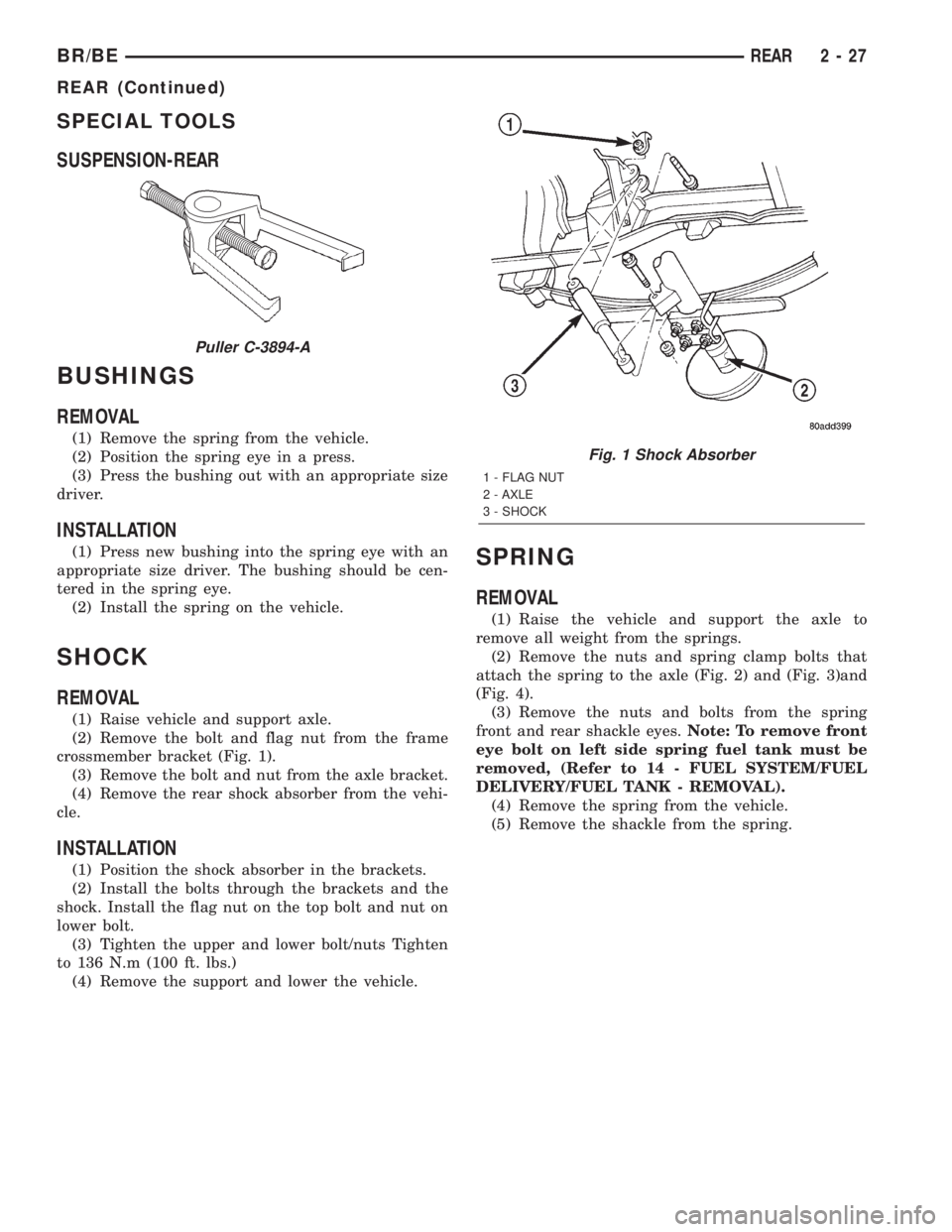
SPECIAL TOOLS
SUSPENSION-REAR
BUSHINGS
REMOVAL
(1) Remove the spring from the vehicle.
(2) Position the spring eye in a press.
(3) Press the bushing out with an appropriate size
driver.
INSTALLATION
(1) Press new bushing into the spring eye with an
appropriate size driver. The bushing should be cen-
tered in the spring eye.
(2) Install the spring on the vehicle.
SHOCK
REMOVAL
(1) Raise vehicle and support axle.
(2) Remove the bolt and flag nut from the frame
crossmember bracket (Fig. 1).
(3) Remove the bolt and nut from the axle bracket.
(4) Remove the rear shock absorber from the vehi-
cle.
INSTALLATION
(1) Position the shock absorber in the brackets.
(2) Install the bolts through the brackets and the
shock. Install the flag nut on the top bolt and nut on
lower bolt.
(3) Tighten the upper and lower bolt/nuts Tighten
to 136 N.m (100 ft. lbs.)
(4) Remove the support and lower the vehicle.
SPRING
REMOVAL
(1) Raise the vehicle and support the axle to
remove all weight from the springs.
(2) Remove the nuts and spring clamp bolts that
attach the spring to the axle (Fig. 2) and (Fig. 3)and
(Fig. 4).
(3) Remove the nuts and bolts from the spring
front and rear shackle eyes.Note: To remove front
eye bolt on left side spring fuel tank must be
removed, (Refer to 14 - FUEL SYSTEM/FUEL
DELIVERY/FUEL TANK - REMOVAL).
(4) Remove the spring from the vehicle.
(5) Remove the shackle from the spring.
Puller C-3894-A
Fig. 1 Shock Absorber
1 - FLAG NUT
2 - AXLE
3 - SHOCK
BR/BEREAR 2 - 27
REAR (Continued)
Page 53 of 2255
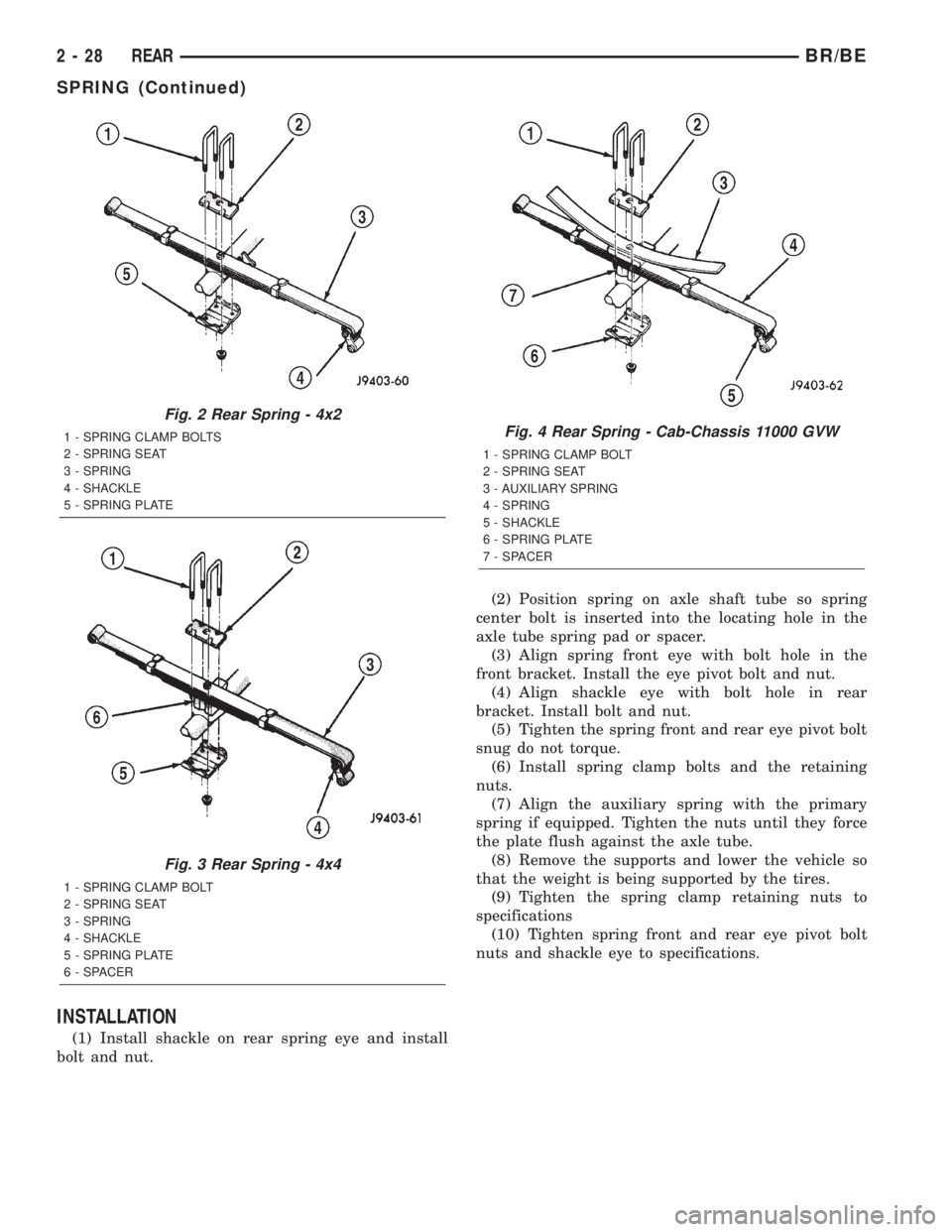
INSTALLATION
(1) Install shackle on rear spring eye and install
bolt and nut.(2) Position spring on axle shaft tube so spring
center bolt is inserted into the locating hole in the
axle tube spring pad or spacer.
(3) Align spring front eye with bolt hole in the
front bracket. Install the eye pivot bolt and nut.
(4) Align shackle eye with bolt hole in rear
bracket. Install bolt and nut.
(5) Tighten the spring front and rear eye pivot bolt
snug do not torque.
(6) Install spring clamp bolts and the retaining
nuts.
(7) Align the auxiliary spring with the primary
spring if equipped. Tighten the nuts until they force
the plate flush against the axle tube.
(8) Remove the supports and lower the vehicle so
that the weight is being supported by the tires.
(9) Tighten the spring clamp retaining nuts to
specifications
(10) Tighten spring front and rear eye pivot bolt
nuts and shackle eye to specifications.
Fig. 2 Rear Spring - 4x2
1 - SPRING CLAMP BOLTS
2 - SPRING SEAT
3 - SPRING
4 - SHACKLE
5 - SPRING PLATE
Fig. 3 Rear Spring - 4x4
1 - SPRING CLAMP BOLT
2 - SPRING SEAT
3 - SPRING
4 - SHACKLE
5 - SPRING PLATE
6 - SPACER
Fig. 4 Rear Spring - Cab-Chassis 11000 GVW
1 - SPRING CLAMP BOLT
2 - SPRING SEAT
3 - AUXILIARY SPRING
4 - SPRING
5 - SHACKLE
6 - SPRING PLATE
7 - SPACER
2 - 28 REARBR/BE
SPRING (Continued)
Page 54 of 2255
STABILIZER BAR
REMOVAL
(1) Raise and support vehicle.
(2) Remove nuts from the links at the stabilizer
bar and separate the links with Puller C-3894-A (Fig.
5).
(3) Remove stabilizer bar retainer nuts and retain-
ers (Fig. 6).
(4) Remove stabilizer bar and replace worn,
cracked or distorted bushings.
(5) Remove links upper mounting nuts and bolts
and remove links.
INSTALLATION
(1) Install link into frame brackets and install
mounting nuts and bolts.
(2) Install the stabilizer bar and center it with
equal spacing on both sides. Install stabilizer bar
retainers and tighten nuts to 54 N´m (40 ft. lbs.).
(3) Install stabilizer link ball studs into the bar
and tighten nuts to 68 N´m (50 ft. lbs.).
(4) Remove support and lower vehicle.
(5) Tighten upper link mounting nuts to 68 N´m
(50 ft. lbs.).
Fig. 5 Stabilizer Link
1 - LINK
2 - PULLER
Fig. 6 Stabilizer Bar Mounting Bolts And
1 - STABILIZER BAR
2 - RETAINERS
BR/BEREAR 2 - 29
Page 55 of 2255
Page 56 of 2255
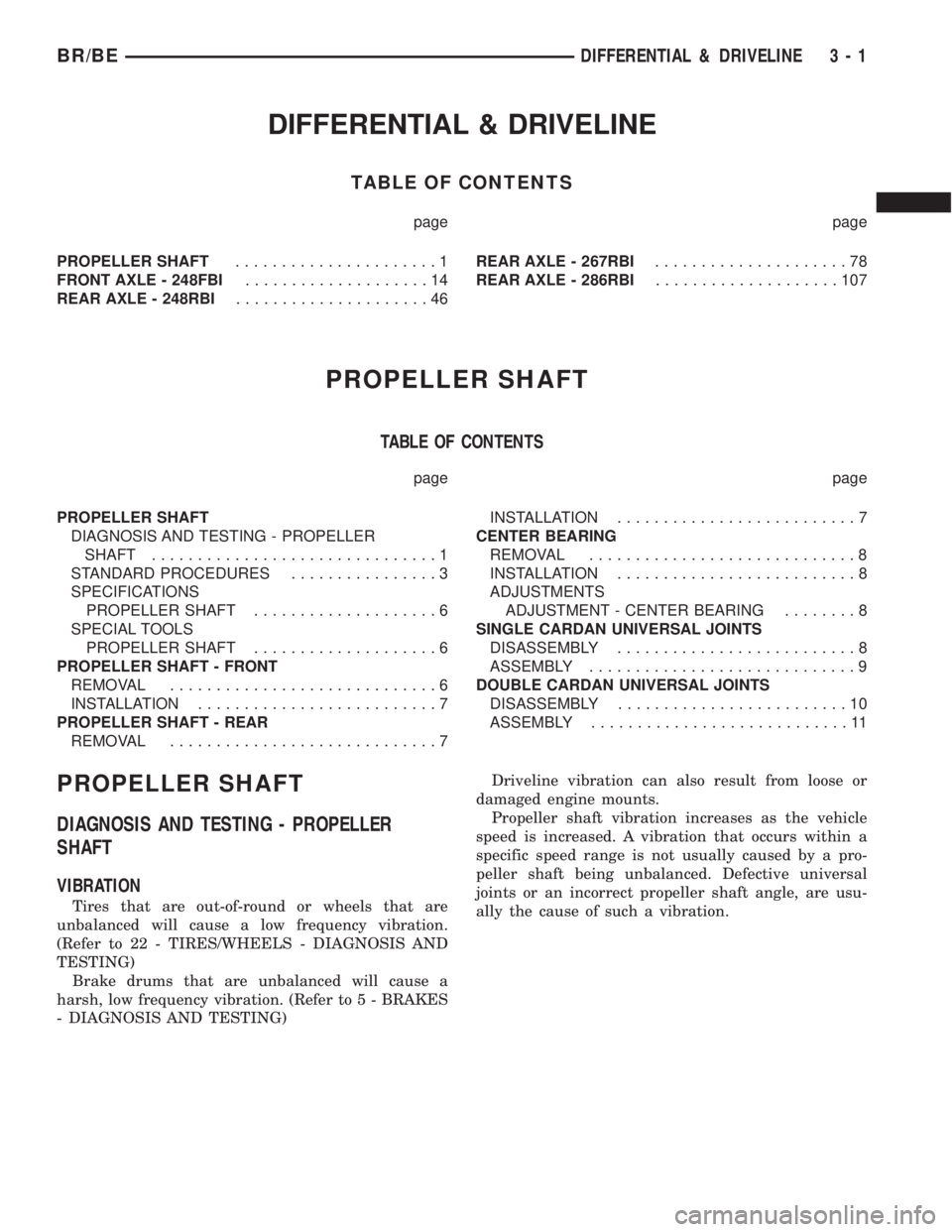
DIFFERENTIAL & DRIVELINE
TABLE OF CONTENTS
page page
PROPELLER SHAFT......................1
FRONT AXLE - 248FBI....................14
REAR AXLE - 248RBI.....................46REAR AXLE - 267RBI.....................78
REAR AXLE - 286RBI....................107
PROPELLER SHAFT
TABLE OF CONTENTS
page page
PROPELLER SHAFT
DIAGNOSIS AND TESTING - PROPELLER
SHAFT...............................1
STANDARD PROCEDURES................3
SPECIFICATIONS
PROPELLER SHAFT....................6
SPECIAL TOOLS
PROPELLER SHAFT....................6
PROPELLER SHAFT - FRONT
REMOVAL.............................6
INSTALLATION..........................7
PROPELLER SHAFT - REAR
REMOVAL.............................7INSTALLATION..........................7
CENTER BEARING
REMOVAL.............................8
INSTALLATION..........................8
ADJUSTMENTS
ADJUSTMENT - CENTER BEARING........8
SINGLE CARDAN UNIVERSAL JOINTS
DISASSEMBLY..........................8
ASSEMBLY.............................9
DOUBLE CARDAN UNIVERSAL JOINTS
DISASSEMBLY.........................10
ASSEMBLY............................11
PROPELLER SHAFT
DIAGNOSIS AND TESTING - PROPELLER
SHAFT
VIBRATION
Tires that are out-of-round or wheels that are
unbalanced will cause a low frequency vibration.
(Refer to 22 - TIRES/WHEELS - DIAGNOSIS AND
TESTING)
Brake drums that are unbalanced will cause a
harsh, low frequency vibration. (Refer to 5 - BRAKES
- DIAGNOSIS AND TESTING)Driveline vibration can also result from loose or
damaged engine mounts.
Propeller shaft vibration increases as the vehicle
speed is increased. A vibration that occurs within a
specific speed range is not usually caused by a pro-
peller shaft being unbalanced. Defective universal
joints or an incorrect propeller shaft angle, are usu-
ally the cause of such a vibration.
BR/BEDIFFERENTIAL & DRIVELINE 3 - 1