Page 281 of 2255
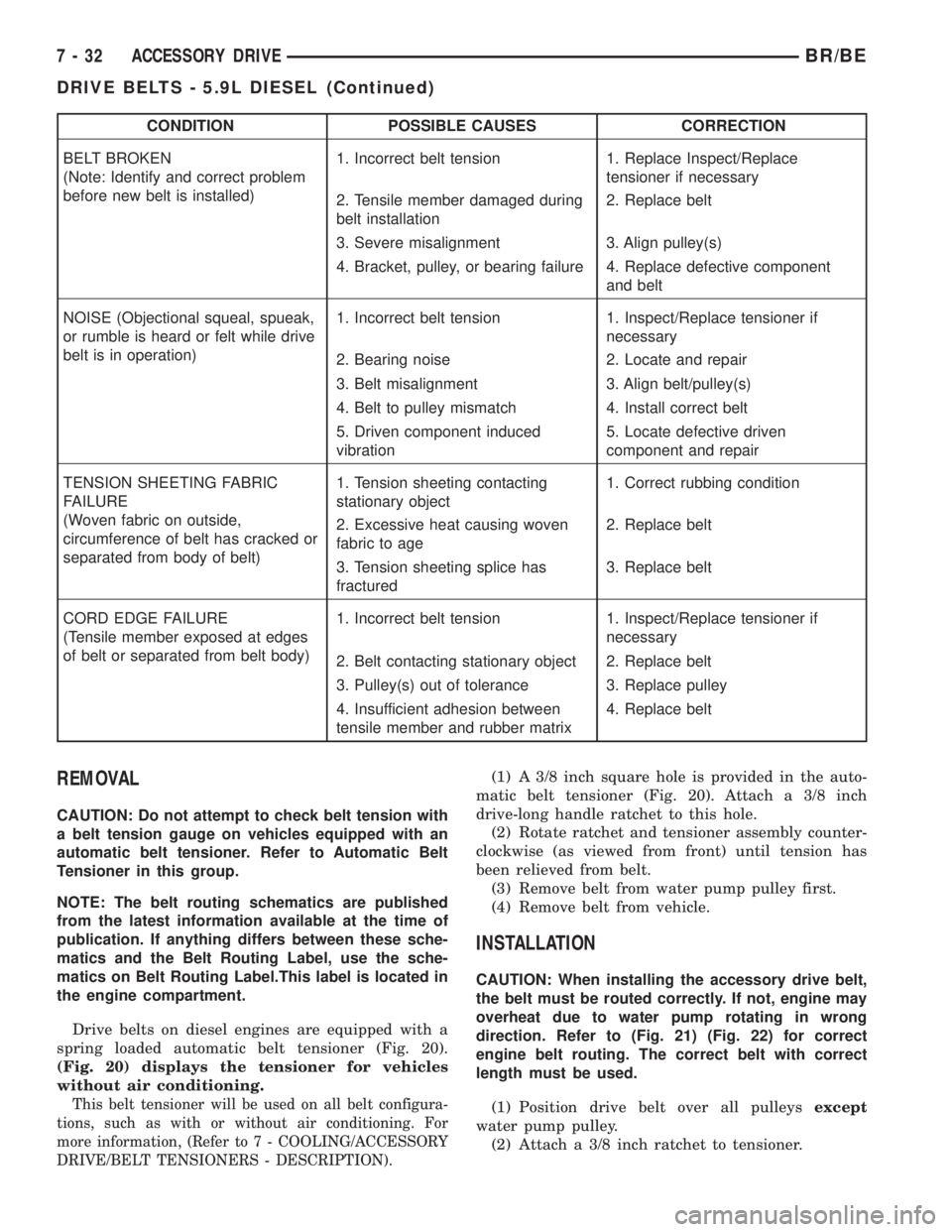
CONDITION POSSIBLE CAUSES CORRECTION
BELT BROKEN
(Note: Identify and correct problem
before new belt is installed)1. Incorrect belt tension 1. Replace Inspect/Replace
tensioner if necessary
2. Tensile member damaged during
belt installation2. Replace belt
3. Severe misalignment 3. Align pulley(s)
4. Bracket, pulley, or bearing failure 4. Replace defective component
and belt
NOISE (Objectional squeal, spueak,
or rumble is heard or felt while drive
belt is in operation)1. Incorrect belt tension 1. Inspect/Replace tensioner if
necessary
2. Bearing noise 2. Locate and repair
3. Belt misalignment 3. Align belt/pulley(s)
4. Belt to pulley mismatch 4. Install correct belt
5. Driven component induced
vibration5. Locate defective driven
component and repair
TENSION SHEETING FABRIC
FAILURE
(Woven fabric on outside,
circumference of belt has cracked or
separated from body of belt)1. Tension sheeting contacting
stationary object1. Correct rubbing condition
2. Excessive heat causing woven
fabric to age2. Replace belt
3. Tension sheeting splice has
fractured3. Replace belt
CORD EDGE FAILURE
(Tensile member exposed at edges
of belt or separated from belt body)1. Incorrect belt tension 1. Inspect/Replace tensioner if
necessary
2. Belt contacting stationary object 2. Replace belt
3. Pulley(s) out of tolerance 3. Replace pulley
4. Insufficient adhesion between
tensile member and rubber matrix4. Replace belt
REMOVAL
CAUTION: Do not attempt to check belt tension with
a belt tension gauge on vehicles equipped with an
automatic belt tensioner. Refer to Automatic Belt
Tensioner in this group.
NOTE: The belt routing schematics are published
from the latest information available at the time of
publication. If anything differs between these sche-
matics and the Belt Routing Label, use the sche-
matics on Belt Routing Label.This label is located in
the engine compartment.
Drive belts on diesel engines are equipped with a
spring loaded automatic belt tensioner (Fig. 20).
(Fig. 20) displays the tensioner for vehicles
without air conditioning.
This belt tensioner will be used on all belt configura-
tions, such as with or without air conditioning. For
more information, (Refer to 7 - COOLING/ACCESSORY
DRIVE/BELT TENSIONERS - DESCRIPTION).
(1) A 3/8 inch square hole is provided in the auto-
matic belt tensioner (Fig. 20). Attach a 3/8 inch
drive-long handle ratchet to this hole.
(2) Rotate ratchet and tensioner assembly counter-
clockwise (as viewed from front) until tension has
been relieved from belt.
(3) Remove belt from water pump pulley first.
(4) Remove belt from vehicle.
INSTALLATION
CAUTION: When installing the accessory drive belt,
the belt must be routed correctly. If not, engine may
overheat due to water pump rotating in wrong
direction. Refer to (Fig. 21) (Fig. 22) for correct
engine belt routing. The correct belt with correct
length must be used.
(1) Position drive belt over all pulleysexcept
water pump pulley.
(2) Attach a 3/8 inch ratchet to tensioner.
7 - 32 ACCESSORY DRIVEBR/BE
DRIVE BELTS - 5.9L DIESEL (Continued)
Page 282 of 2255
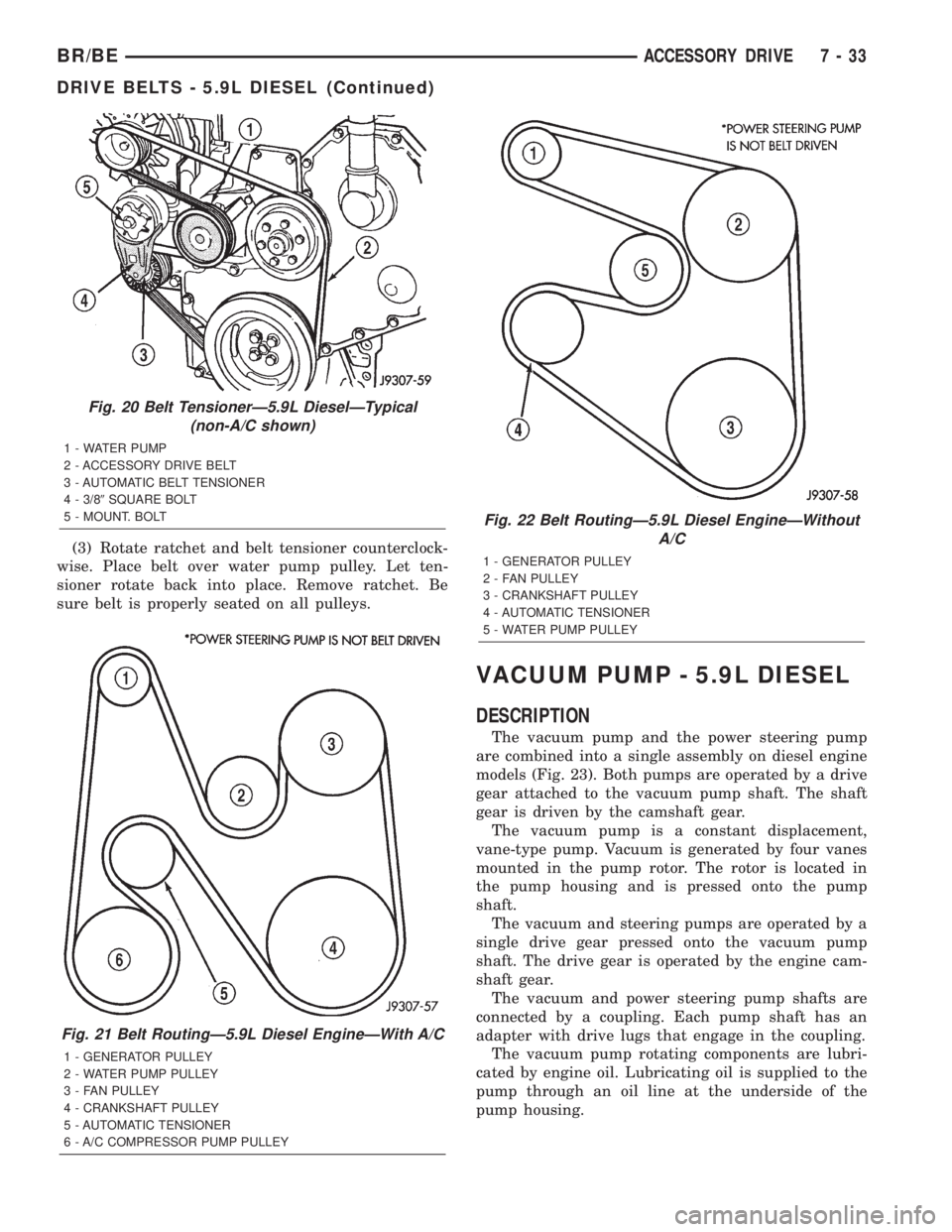
(3) Rotate ratchet and belt tensioner counterclock-
wise. Place belt over water pump pulley. Let ten-
sioner rotate back into place. Remove ratchet. Be
sure belt is properly seated on all pulleys.
VACUUM PUMP - 5.9L DIESEL
DESCRIPTION
The vacuum pump and the power steering pump
are combined into a single assembly on diesel engine
models (Fig. 23). Both pumps are operated by a drive
gear attached to the vacuum pump shaft. The shaft
gear is driven by the camshaft gear.
The vacuum pump is a constant displacement,
vane-type pump. Vacuum is generated by four vanes
mounted in the pump rotor. The rotor is located in
the pump housing and is pressed onto the pump
shaft.
The vacuum and steering pumps are operated by a
single drive gear pressed onto the vacuum pump
shaft. The drive gear is operated by the engine cam-
shaft gear.
The vacuum and power steering pump shafts are
connected by a coupling. Each pump shaft has an
adapter with drive lugs that engage in the coupling.
The vacuum pump rotating components are lubri-
cated by engine oil. Lubricating oil is supplied to the
pump through an oil line at the underside of the
pump housing.
Fig. 20 Belt TensionerÐ5.9L DieselÐTypical
(non-A/C shown)
1 - WATER PUMP
2 - ACCESSORY DRIVE BELT
3 - AUTOMATIC BELT TENSIONER
4 - 3/89SQUARE BOLT
5 - MOUNT. BOLT
Fig. 21 Belt RoutingÐ5.9L Diesel EngineÐWith A/C
1 - GENERATOR PULLEY
2 - WATER PUMP PULLEY
3 - FAN PULLEY
4 - CRANKSHAFT PULLEY
5 - AUTOMATIC TENSIONER
6 - A/C COMPRESSOR PUMP PULLEY
Fig. 22 Belt RoutingÐ5.9L Diesel EngineÐWithout
A/C
1 - GENERATOR PULLEY
2 - FAN PULLEY
3 - CRANKSHAFT PULLEY
4 - AUTOMATIC TENSIONER
5 - WATER PUMP PULLEY
BR/BEACCESSORY DRIVE 7 - 33
DRIVE BELTS - 5.9L DIESEL (Continued)
Page 283 of 2255
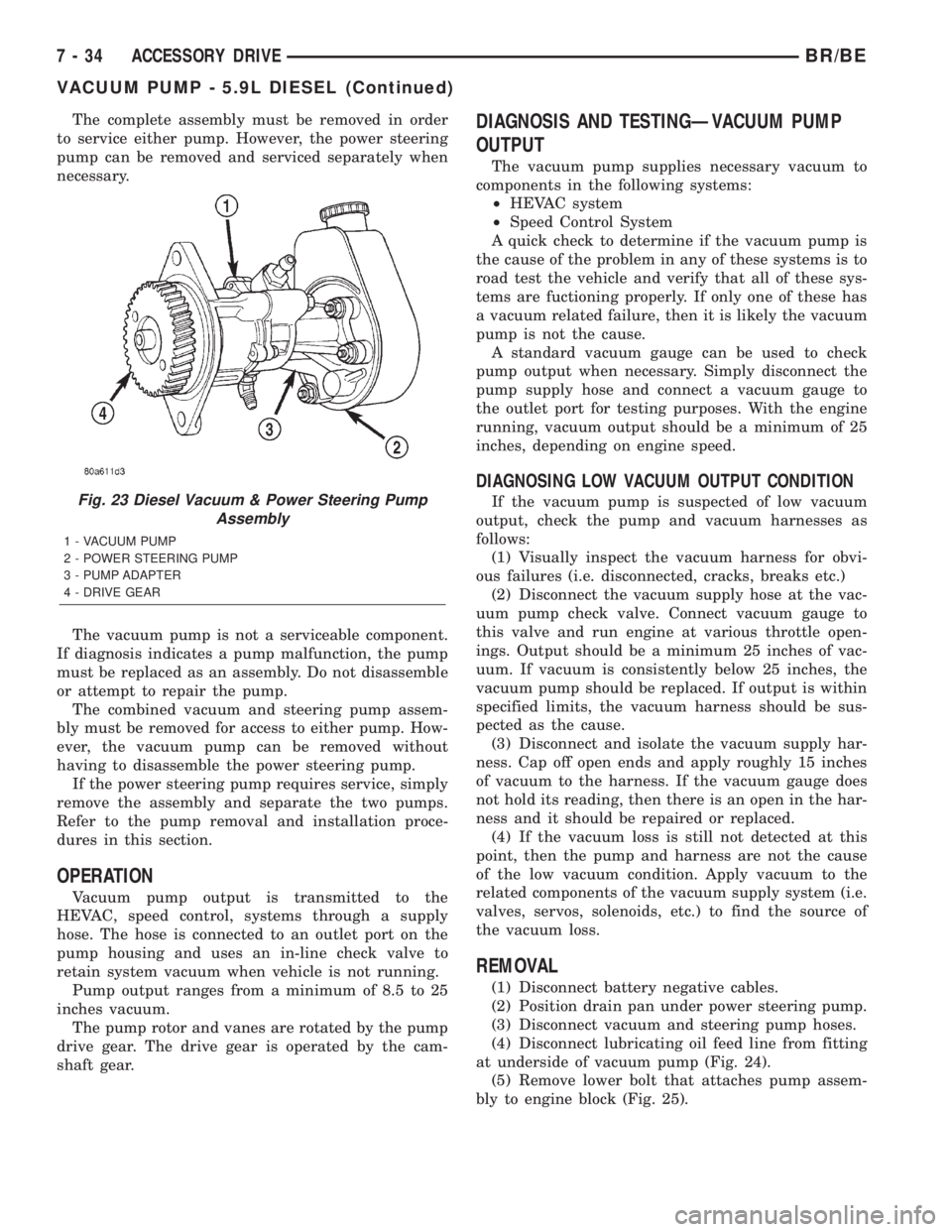
The complete assembly must be removed in order
to service either pump. However, the power steering
pump can be removed and serviced separately when
necessary.
The vacuum pump is not a serviceable component.
If diagnosis indicates a pump malfunction, the pump
must be replaced as an assembly. Do not disassemble
or attempt to repair the pump.
The combined vacuum and steering pump assem-
bly must be removed for access to either pump. How-
ever, the vacuum pump can be removed without
having to disassemble the power steering pump.
If the power steering pump requires service, simply
remove the assembly and separate the two pumps.
Refer to the pump removal and installation proce-
dures in this section.
OPERATION
Vacuum pump output is transmitted to the
HEVAC, speed control, systems through a supply
hose. The hose is connected to an outlet port on the
pump housing and uses an in-line check valve to
retain system vacuum when vehicle is not running.
Pump output ranges from a minimum of 8.5 to 25
inches vacuum.
The pump rotor and vanes are rotated by the pump
drive gear. The drive gear is operated by the cam-
shaft gear.
DIAGNOSIS AND TESTINGÐVACUUM PUMP
OUTPUT
The vacuum pump supplies necessary vacuum to
components in the following systems:
²HEVAC system
²Speed Control System
A quick check to determine if the vacuum pump is
the cause of the problem in any of these systems is to
road test the vehicle and verify that all of these sys-
tems are fuctioning properly. If only one of these has
a vacuum related failure, then it is likely the vacuum
pump is not the cause.
A standard vacuum gauge can be used to check
pump output when necessary. Simply disconnect the
pump supply hose and connect a vacuum gauge to
the outlet port for testing purposes. With the engine
running, vacuum output should be a minimum of 25
inches, depending on engine speed.
DIAGNOSING LOW VACUUM OUTPUT CONDITION
If the vacuum pump is suspected of low vacuum
output, check the pump and vacuum harnesses as
follows:
(1) Visually inspect the vacuum harness for obvi-
ous failures (i.e. disconnected, cracks, breaks etc.)
(2) Disconnect the vacuum supply hose at the vac-
uum pump check valve. Connect vacuum gauge to
this valve and run engine at various throttle open-
ings. Output should be a minimum 25 inches of vac-
uum. If vacuum is consistently below 25 inches, the
vacuum pump should be replaced. If output is within
specified limits, the vacuum harness should be sus-
pected as the cause.
(3) Disconnect and isolate the vacuum supply har-
ness. Cap off open ends and apply roughly 15 inches
of vacuum to the harness. If the vacuum gauge does
not hold its reading, then there is an open in the har-
ness and it should be repaired or replaced.
(4) If the vacuum loss is still not detected at this
point, then the pump and harness are not the cause
of the low vacuum condition. Apply vacuum to the
related components of the vacuum supply system (i.e.
valves, servos, solenoids, etc.) to find the source of
the vacuum loss.
REMOVAL
(1) Disconnect battery negative cables.
(2) Position drain pan under power steering pump.
(3) Disconnect vacuum and steering pump hoses.
(4) Disconnect lubricating oil feed line from fitting
at underside of vacuum pump (Fig. 24).
(5) Remove lower bolt that attaches pump assem-
bly to engine block (Fig. 25).
Fig. 23 Diesel Vacuum & Power Steering Pump
Assembly
1 - VACUUM PUMP
2 - POWER STEERING PUMP
3 - PUMP ADAPTER
4 - DRIVE GEAR
7 - 34 ACCESSORY DRIVEBR/BE
VACUUM PUMP - 5.9L DIESEL (Continued)
Page 284 of 2255
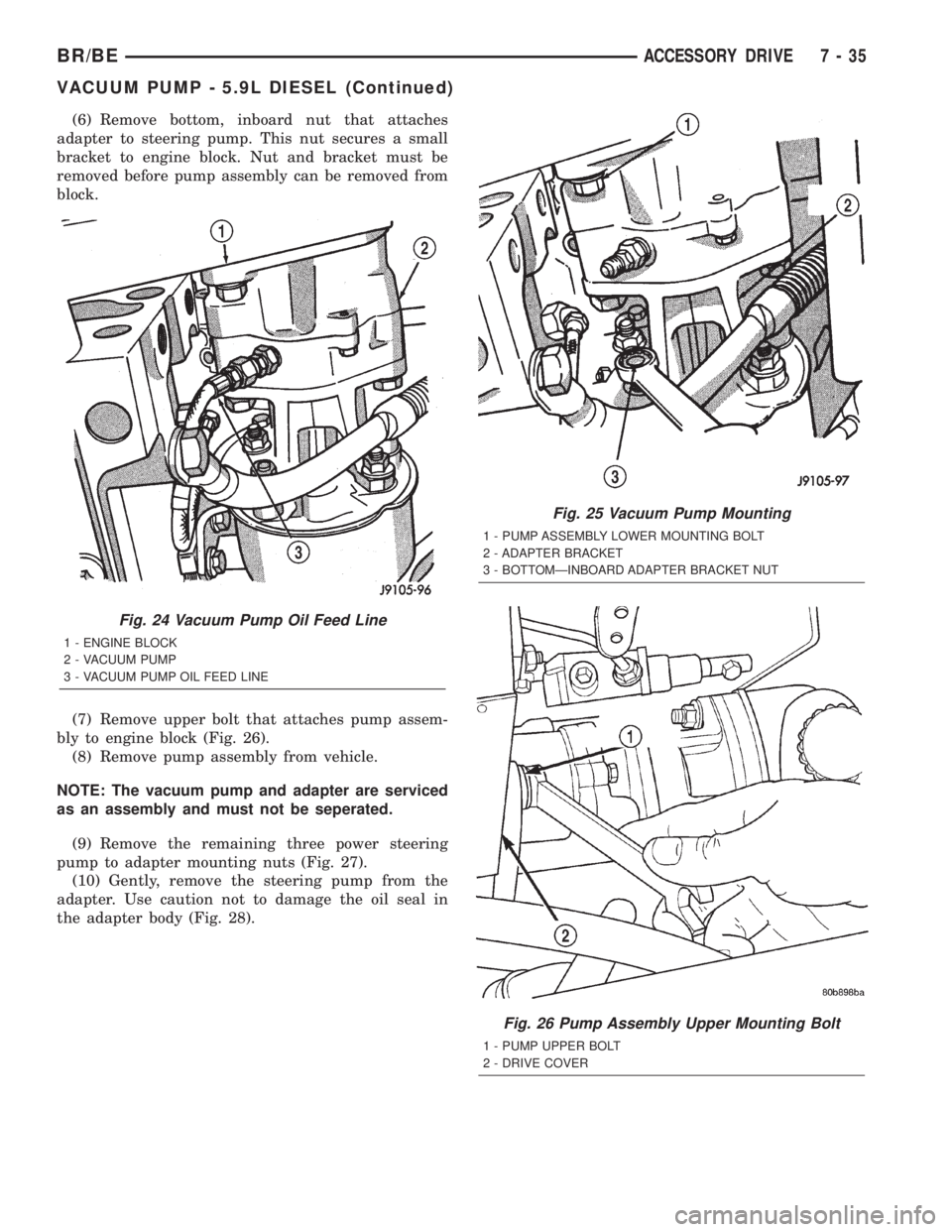
(6) Remove bottom, inboard nut that attaches
adapter to steering pump. This nut secures a small
bracket to engine block. Nut and bracket must be
removed before pump assembly can be removed from
block.
(7) Remove upper bolt that attaches pump assem-
bly to engine block (Fig. 26).
(8) Remove pump assembly from vehicle.
NOTE: The vacuum pump and adapter are serviced
as an assembly and must not be seperated.
(9) Remove the remaining three power steering
pump to adapter mounting nuts (Fig. 27).
(10) Gently, remove the steering pump from the
adapter. Use caution not to damage the oil seal in
the adapter body (Fig. 28).
Fig. 24 Vacuum Pump Oil Feed Line
1 - ENGINE BLOCK
2 - VACUUM PUMP
3 - VACUUM PUMP OIL FEED LINE
Fig. 25 Vacuum Pump Mounting
1 - PUMP ASSEMBLY LOWER MOUNTING BOLT
2 - ADAPTER BRACKET
3 - BOTTOMÐINBOARD ADAPTER BRACKET NUT
Fig. 26 Pump Assembly Upper Mounting Bolt
1 - PUMP UPPER BOLT
2 - DRIVE COVER
BR/BEACCESSORY DRIVE 7 - 35
VACUUM PUMP - 5.9L DIESEL (Continued)
Page 285 of 2255

INSTALLATION
NOTE: Make sure the two pump spacers are
present before assembling power steering pump to
adapter.
(1) Aline the steering pump drive dog with the slot
in the vacuum pump drive assembly, slide the steer-
ing pump into place on the adapter.Use care not to
damage the oil seal in the adapter body.
(2) Install the three steering pump to adapter
nuts, do not install the lower inboard mounting nut
at this time. Tighten nuts to 24 N´m (18 ft. lbs.).
(3) Position new gasket on vacuum pump mount-
ing flange (Fig. 29). Use MopartPerfect Seal, or sil-
icone adhesive/sealer to hold gasket in place.
(4) Insert pump assembly upper attaching bolt in
mounting flange and gasket. Use sealer or grease to
hold bolt in place if necessary.
(5) Position pump assembly on engine and install
upper bolt (Fig. 30). Tighten upper bolt only enough
to hold assembly in place at this time.
Fig. 27 Adapter to Power Steering Pump Nuts
1 - VACUUM PUMP
2 - ATTACHING NUTS
3 - STEERING PUMP
4 - PUMP SPACERS
5 - OIL FEED FITTING
Fig. 28 Steering Pump, Vacuum Pump and Adapter
1 - PUMP SHAFT
2 - VACUUM FITTING
3 - VACUUM PUMP DRIVE
4 - OIL SEAL
5 - MOUNTING BRACKET
6 - DRIVE DOG
7 - PUMP SPACERS
Fig. 29 Pump Mounting Flange Gasket
1 - PUMP MOUNTING FLANGE
2 - PUMP GASKET (APPLY SEALER TO BOTH SIDES)
7 - 36 ACCESSORY DRIVEBR/BE
VACUUM PUMP - 5.9L DIESEL (Continued)
Page 286 of 2255
(6) Working from under vehicle, install pump
assembly lower attaching bolt. Then tighten upper
and lower bolt to 77 N´m (57 ft. lbs.).
(7) Position bracket on steering pump inboard
stud. Then install remaining adapter attaching nut
on stud. Tighten nut to 24 N´m (18 ft. lbs.).
(8) Connect oil feed line to vacuum pump connec-
tor and tighten line fitting.
(9) Connect steering pump pressure and return
lines to pump. Tighten pressure line fitting to 30
N´m (22 ft. lbs.).
(10) Connect vacuum hose to vacuum pump.
(11) Connect battery cables, if removed.
(12) Fill power steering pump reservoir and Purge
air from steering pump lines (Refer to 19 - STEER-
ING/PUMP - STANDARD PROCEDURE).
Fig. 30 Installing Pump Assembly On Engine
1 - PUMP ASSEMBLY
2 - PUMP GASKET
3 - DRIVE GEAR
BR/BEACCESSORY DRIVE 7 - 37
VACUUM PUMP - 5.9L DIESEL (Continued)
Page 287 of 2255
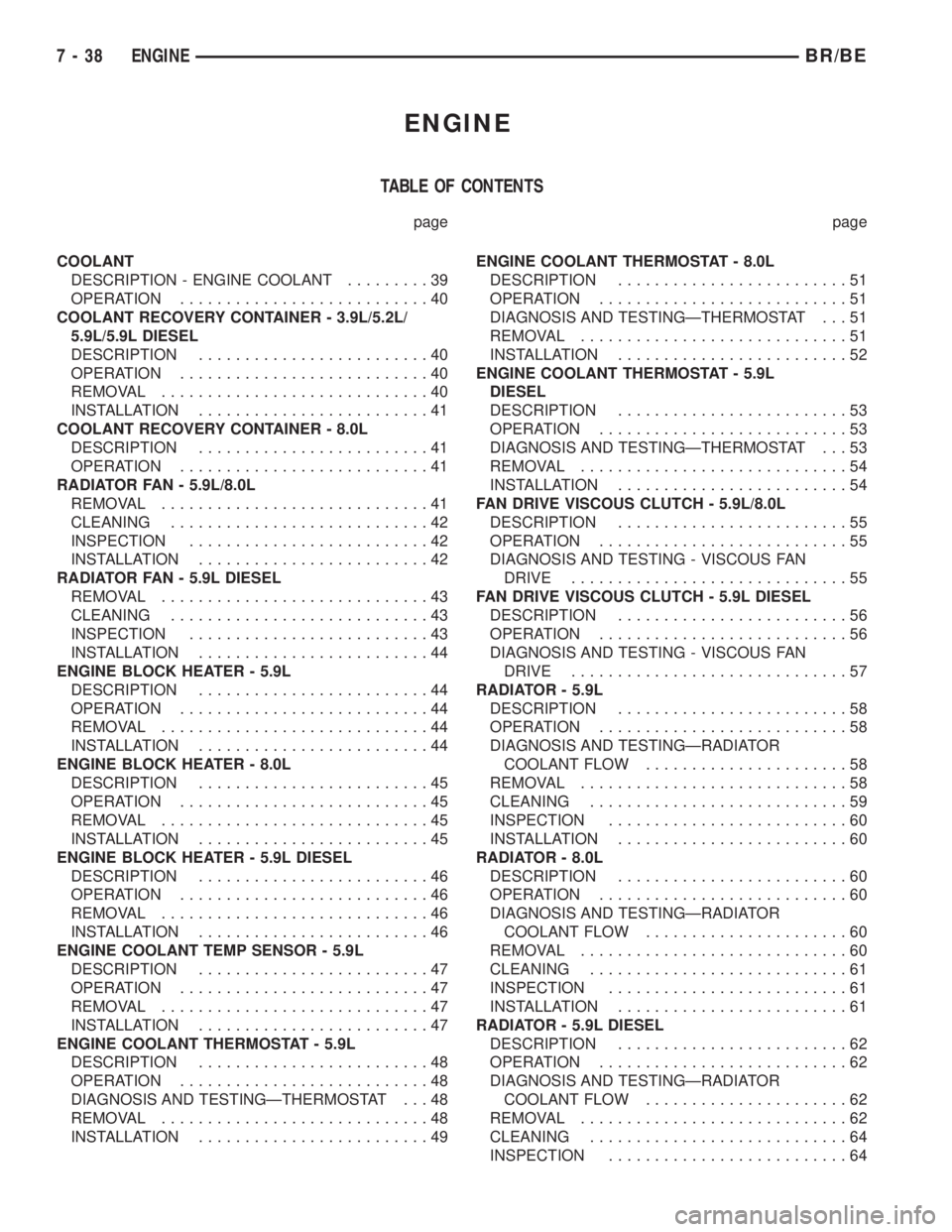
ENGINE
TABLE OF CONTENTS
page page
COOLANT
DESCRIPTION - ENGINE COOLANT.........39
OPERATION...........................40
COOLANT RECOVERY CONTAINER - 3.9L/5.2L/
5.9L/5.9L DIESEL
DESCRIPTION.........................40
OPERATION...........................40
REMOVAL.............................40
INSTALLATION.........................41
COOLANT RECOVERY CONTAINER - 8.0L
DESCRIPTION.........................41
OPERATION...........................41
RADIATOR FAN - 5.9L/8.0L
REMOVAL.............................41
CLEANING............................42
INSPECTION..........................42
INSTALLATION.........................42
RADIATOR FAN - 5.9L DIESEL
REMOVAL.............................43
CLEANING............................43
INSPECTION..........................43
INSTALLATION.........................44
ENGINE BLOCK HEATER - 5.9L
DESCRIPTION.........................44
OPERATION...........................44
REMOVAL.............................44
INSTALLATION.........................44
ENGINE BLOCK HEATER - 8.0L
DESCRIPTION.........................45
OPERATION...........................45
REMOVAL.............................45
INSTALLATION.........................45
ENGINE BLOCK HEATER - 5.9L DIESEL
DESCRIPTION.........................46
OPERATION...........................46
REMOVAL.............................46
INSTALLATION.........................46
ENGINE COOLANT TEMP SENSOR - 5.9L
DESCRIPTION.........................47
OPERATION...........................47
REMOVAL.............................47
INSTALLATION.........................47
ENGINE COOLANT THERMOSTAT - 5.9L
DESCRIPTION.........................48
OPERATION...........................48
DIAGNOSIS AND TESTINGÐTHERMOSTAT . . . 48
REMOVAL.............................48
INSTALLATION.........................49ENGINE COOLANT THERMOSTAT - 8.0L
DESCRIPTION.........................51
OPERATION...........................51
DIAGNOSIS AND TESTINGÐTHERMOSTAT . . . 51
REMOVAL.............................51
INSTALLATION.........................52
ENGINE COOLANT THERMOSTAT - 5.9L
DIESEL
DESCRIPTION.........................53
OPERATION...........................53
DIAGNOSIS AND TESTINGÐTHERMOSTAT . . . 53
REMOVAL.............................54
INSTALLATION.........................54
FAN DRIVE VISCOUS CLUTCH - 5.9L/8.0L
DESCRIPTION.........................55
OPERATION...........................55
DIAGNOSIS AND TESTING - VISCOUS FAN
DRIVE..............................55
FAN DRIVE VISCOUS CLUTCH - 5.9L DIESEL
DESCRIPTION.........................56
OPERATION...........................56
DIAGNOSIS AND TESTING - VISCOUS FAN
DRIVE..............................57
RADIATOR - 5.9L
DESCRIPTION.........................58
OPERATION...........................58
DIAGNOSIS AND TESTINGÐRADIATOR
COOLANT FLOW......................58
REMOVAL.............................58
CLEANING............................59
INSPECTION..........................60
INSTALLATION.........................60
RADIATOR - 8.0L
DESCRIPTION.........................60
OPERATION...........................60
DIAGNOSIS AND TESTINGÐRADIATOR
COOLANT FLOW......................60
REMOVAL.............................60
CLEANING............................61
INSPECTION..........................61
INSTALLATION.........................61
RADIATOR - 5.9L DIESEL
DESCRIPTION.........................62
OPERATION...........................62
DIAGNOSIS AND TESTINGÐRADIATOR
COOLANT FLOW......................62
REMOVAL.............................62
CLEANING............................64
INSPECTION..........................64
7 - 38 ENGINEBR/BE
Page 288 of 2255
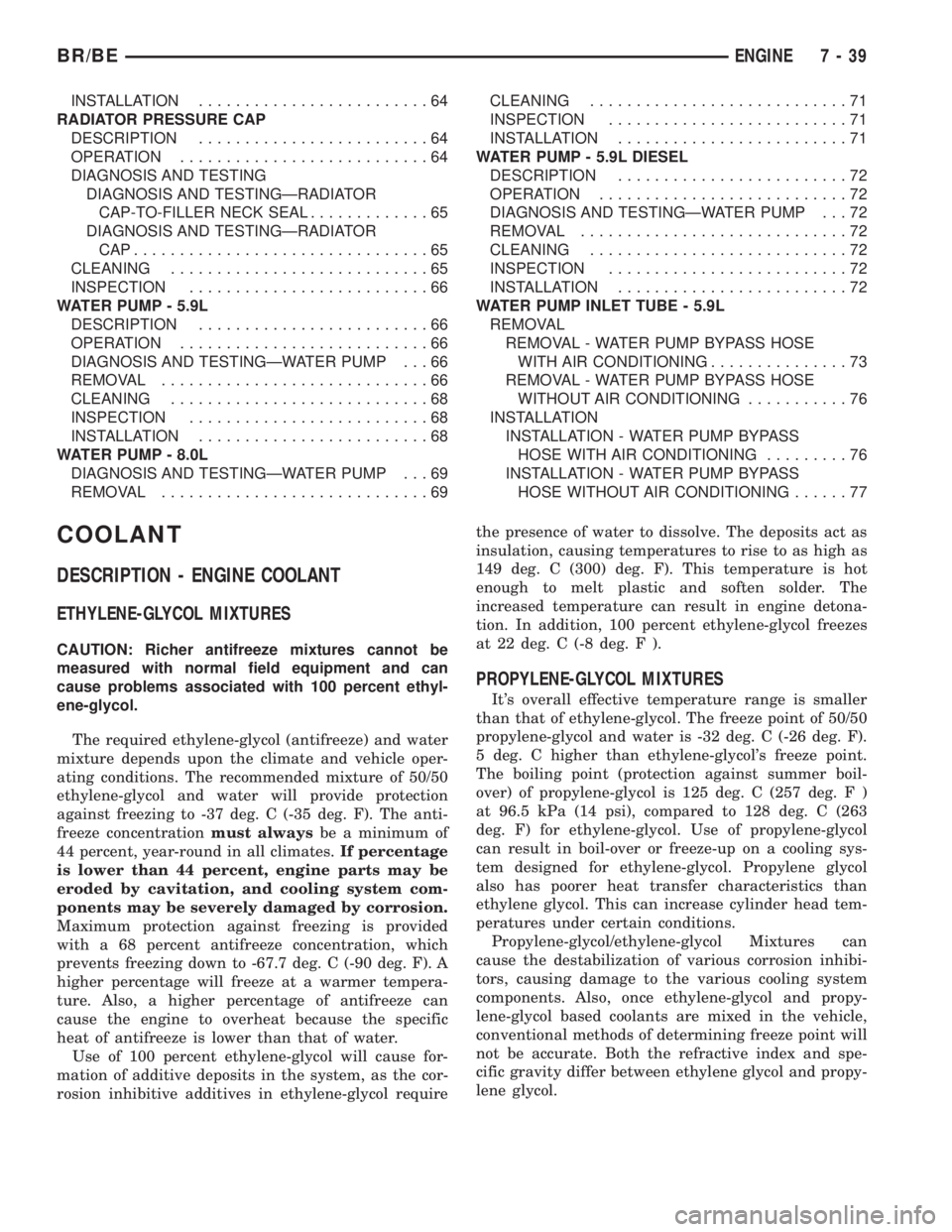
INSTALLATION.........................64
RADIATOR PRESSURE CAP
DESCRIPTION.........................64
OPERATION...........................64
DIAGNOSIS AND TESTING
DIAGNOSIS AND TESTINGÐRADIATOR
CAP-TO-FILLER NECK SEAL.............65
DIAGNOSIS AND TESTINGÐRADIATOR
CAP................................65
CLEANING............................65
INSPECTION..........................66
WATER PUMP - 5.9L
DESCRIPTION.........................66
OPERATION...........................66
DIAGNOSIS AND TESTINGÐWATER PUMP . . . 66
REMOVAL.............................66
CLEANING............................68
INSPECTION..........................68
INSTALLATION.........................68
WATER PUMP - 8.0L
DIAGNOSIS AND TESTINGÐWATER PUMP . . . 69
REMOVAL.............................69CLEANING............................71
INSPECTION..........................71
INSTALLATION.........................71
WATER PUMP - 5.9L DIESEL
DESCRIPTION.........................72
OPERATION...........................72
DIAGNOSIS AND TESTINGÐWATER PUMP . . . 72
REMOVAL.............................72
CLEANING............................72
INSPECTION..........................72
INSTALLATION.........................72
WATER PUMP INLET TUBE - 5.9L
REMOVAL
REMOVAL - WATER PUMP BYPASS HOSE
WITH AIR CONDITIONING...............73
REMOVAL - WATER PUMP BYPASS HOSE
WITHOUT AIR CONDITIONING...........76
INSTALLATION
INSTALLATION - WATER PUMP BYPASS
HOSE WITH AIR CONDITIONING.........76
INSTALLATION - WATER PUMP BYPASS
HOSE WITHOUT AIR CONDITIONING......77
COOLANT
DESCRIPTION - ENGINE COOLANT
ETHYLENE-GLYCOL MIXTURES
CAUTION: Richer antifreeze mixtures cannot be
measured with normal field equipment and can
cause problems associated with 100 percent ethyl-
ene-glycol.
The required ethylene-glycol (antifreeze) and water
mixture depends upon the climate and vehicle oper-
ating conditions. The recommended mixture of 50/50
ethylene-glycol and water will provide protection
against freezing to -37 deg. C (-35 deg. F). The anti-
freeze concentrationmust alwaysbe a minimum of
44 percent, year-round in all climates.If percentage
is lower than 44 percent, engine parts may be
eroded by cavitation, and cooling system com-
ponents may be severely damaged by corrosion.
Maximum protection against freezing is provided
with a 68 percent antifreeze concentration, which
prevents freezing down to -67.7 deg. C (-90 deg. F). A
higher percentage will freeze at a warmer tempera-
ture. Also, a higher percentage of antifreeze can
cause the engine to overheat because the specific
heat of antifreeze is lower than that of water.
Use of 100 percent ethylene-glycol will cause for-
mation of additive deposits in the system, as the cor-
rosion inhibitive additives in ethylene-glycol requirethe presence of water to dissolve. The deposits act as
insulation, causing temperatures to rise to as high as
149 deg. C (300) deg. F). This temperature is hot
enough to melt plastic and soften solder. The
increased temperature can result in engine detona-
tion. In addition, 100 percent ethylene-glycol freezes
at 22 deg. C (-8 deg. F ).
PROPYLENE-GLYCOL MIXTURES
It's overall effective temperature range is smaller
than that of ethylene-glycol. The freeze point of 50/50
propylene-glycol and water is -32 deg. C (-26 deg. F).
5 deg. C higher than ethylene-glycol's freeze point.
The boiling point (protection against summer boil-
over) of propylene-glycol is 125 deg. C (257 deg. F )
at 96.5 kPa (14 psi), compared to 128 deg. C (263
deg. F) for ethylene-glycol. Use of propylene-glycol
can result in boil-over or freeze-up on a cooling sys-
tem designed for ethylene-glycol. Propylene glycol
also has poorer heat transfer characteristics than
ethylene glycol. This can increase cylinder head tem-
peratures under certain conditions.
Propylene-glycol/ethylene-glycol Mixtures can
cause the destabilization of various corrosion inhibi-
tors, causing damage to the various cooling system
components. Also, once ethylene-glycol and propy-
lene-glycol based coolants are mixed in the vehicle,
conventional methods of determining freeze point will
not be accurate. Both the refractive index and spe-
cific gravity differ between ethylene glycol and propy-
lene glycol.
BR/BEENGINE 7 - 39