Page 1393 of 2255
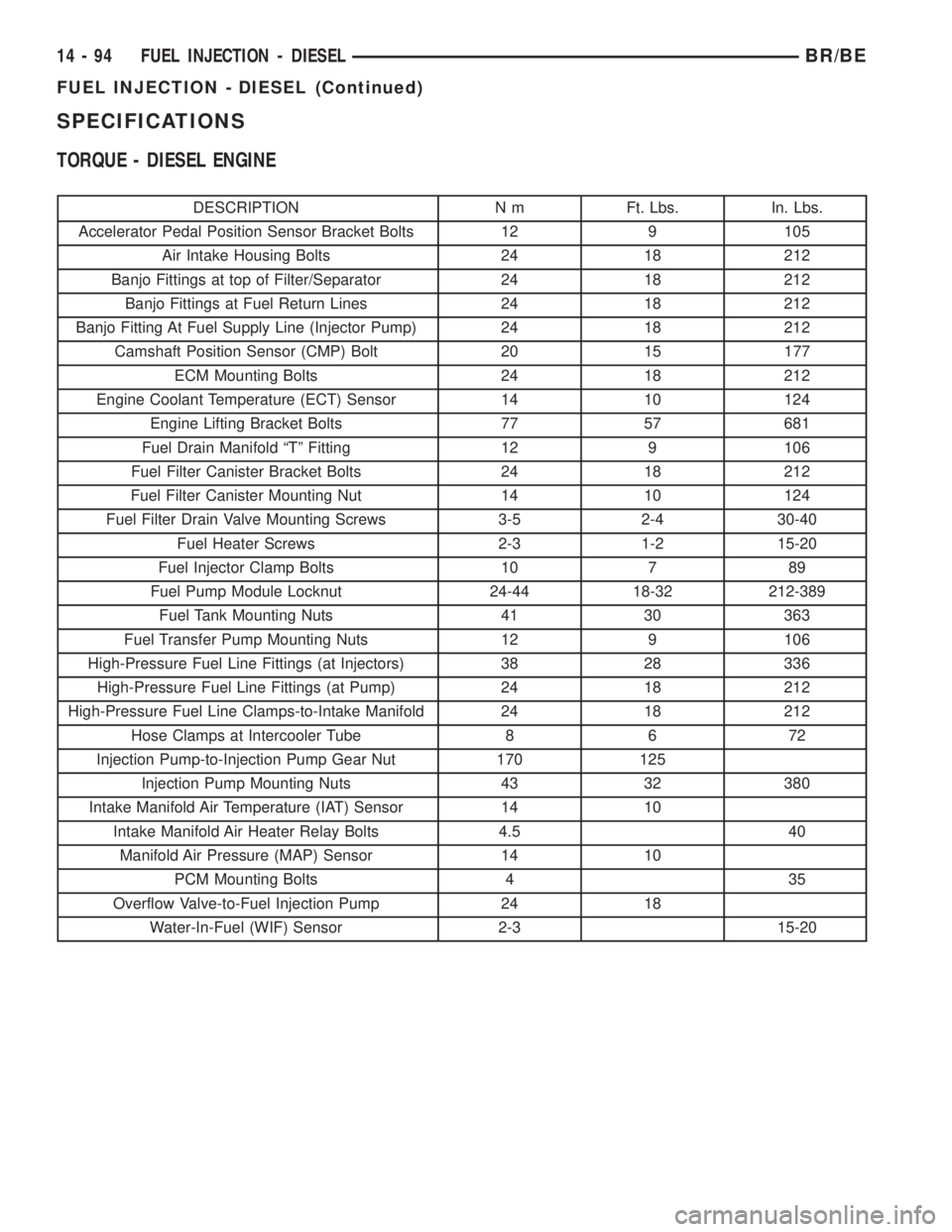
SPECIFICATIONS
TORQUE - DIESEL ENGINE
DESCRIPTION N m Ft. Lbs. In. Lbs.
Accelerator Pedal Position Sensor Bracket Bolts 12 9 105
Air Intake Housing Bolts 24 18 212
Banjo Fittings at top of Filter/Separator 24 18 212
Banjo Fittings at Fuel Return Lines 24 18 212
Banjo Fitting At Fuel Supply Line (Injector Pump) 24 18 212
Camshaft Position Sensor (CMP) Bolt 20 15 177
ECM Mounting Bolts 24 18 212
Engine Coolant Temperature (ECT) Sensor 14 10 124
Engine Lifting Bracket Bolts 77 57 681
Fuel Drain Manifold ªTº Fitting 12 9 106
Fuel Filter Canister Bracket Bolts 24 18 212
Fuel Filter Canister Mounting Nut 14 10 124
Fuel Filter Drain Valve Mounting Screws 3-5 2-4 30-40
Fuel Heater Screws 2-3 1-2 15-20
Fuel Injector Clamp Bolts 10 7 89
Fuel Pump Module Locknut 24-44 18-32 212-389
Fuel Tank Mounting Nuts 41 30 363
Fuel Transfer Pump Mounting Nuts 12 9 106
High-Pressure Fuel Line Fittings (at Injectors) 38 28 336
High-Pressure Fuel Line Fittings (at Pump) 24 18 212
High-Pressure Fuel Line Clamps-to-Intake Manifold 24 18 212
Hose Clamps at Intercooler Tube 8 6 72
Injection Pump-to-Injection Pump Gear Nut 170 125
Injection Pump Mounting Nuts 43 32 380
Intake Manifold Air Temperature (IAT) Sensor 14 10
Intake Manifold Air Heater Relay Bolts 4.5 40
Manifold Air Pressure (MAP) Sensor 14 10
PCM Mounting Bolts 4 35
Overflow Valve-to-Fuel Injection Pump 24 18
Water-In-Fuel (WIF) Sensor 2-3 15-20
14 - 94 FUEL INJECTION - DIESELBR/BE
FUEL INJECTION - DIESEL (Continued)
Page 1394 of 2255

ACCELERATOR PEDAL
POSITION SENSOR
DESCRIPTION
The APPS assembly is located at the top-left-front
of the engine (Fig. 4). A plastic cover is used to cover
the assembly. The actual sensor is located behind its
mounting bracket (Fig. 5).
OPERATION
The Accelerator Pedal Position Sensor (APPS) is a
linear potentiometer. It provides the Engine Control
Module (ECM) with a DC voltage signal proportional
to the angle, or position of the accelerator pedal. In
previous model years, this part was known as the
Throttle Position Sensor (TPS).
Diesel engines used in previous model years used a
mechanical cable between the accelerator pedal and
the TPS lever. Linkage and bellcranks between the
TPS cable lever and the fuel injection pump were
also used. Although the cable has been retained with
the APPS, the linkage and bellcranks between the
cable lever and the fuel injection pump are no longer
used.
The APPS is serviced (replaced) as one assembly
including the lever, brackets and sensor. The APPS is
calibrated and permanently positioned to its mount-
ing bracket.CAUTION: Do not attempt to remove sensor from
its mounting bracket as electronic calibration will
be destroyed (sensor-to-bracket mounting screws
are permanently attached). Two accelerator lever
set screws (Fig. 4) are used to position lever. Do
not attempt to alter positions of these set screws as
electronic calibration will be destroyed.
REMOVAL
The APPS is serviced (replaced) as one assembly
including the lever, brackets and sensor. The APPS is
calibrated to its mounting bracket. The APPS assem-
bly is located at left-front of engine below plastic
cable/lever/linkage cover (Fig. 6).
CAUTION: Do not attempt to remove sensor from
its mounting bracket as electronic calibration will
be destroyed (sensor-to-bracket mounting screws
are permanently attached). Two accelerator lever
set screws (Fig. 8) are used to position lever. Do
not attempt to alter positions of these set screws as
electronic calibration will be destroyed.
Fig. 4 APPS Assembly Location
1 - LEVER
2 - MOUNTING BOLTS (6)
3 - WIRE HARNESS CLIP
4 - CALIBRATION SCREWS (NO ADJUSTMENT)
5 - APPS ASSEMBLY
Fig. 5 APPS Sensor Location (Rear View)
1 - APPS
2-TAB
3 - PUSH FOR REMOVAL
4 - APPS CONNECTOR
BR/BEFUEL INJECTION - DIESEL 14 - 95
Page 1395 of 2255
Fig. 6 Cable/Lever/Linkage/Cover
1 - CABLE/LEVER/LINKAGE COVER
2 - PUSH UP LOWER TAB
3 - SCREWS/CLIPS (2)
4 - TAB PUSH HERE
Fig. 7 Cables at Throttle Lever
1 - PINCH (2) TABS
2 - CABLE MOUNTING BRACKET
3 - PINCH TABS (2)
4 - OFF
5 - THROTTLE CABLE
6 - THROTTLE LEVER
7 - THROTTLE LEVER PIN
8 - OFF
9 - CONNECTOR
10 - SPEED CONTROL CABLE
Fig. 8 APPS Assembly
1 - LEVER
2 - MOUNTING BOLTS (6)
3 - WIRE HARNESS CLIP
4 - CALIBRATION SCREWS (NO ADJUSTMENT)
5 - APPS ASSEMBLY
Fig. 9 Electrical Connector at Bottom of APPS
1 - APPS
2-TAB
3 - PUSH FOR REMOVAL
4 - APPS CONNECTOR
14 - 96 FUEL INJECTION - DIESELBR/BE
ACCELERATOR PEDAL POSITION SENSOR (Continued)
Page 1396 of 2255
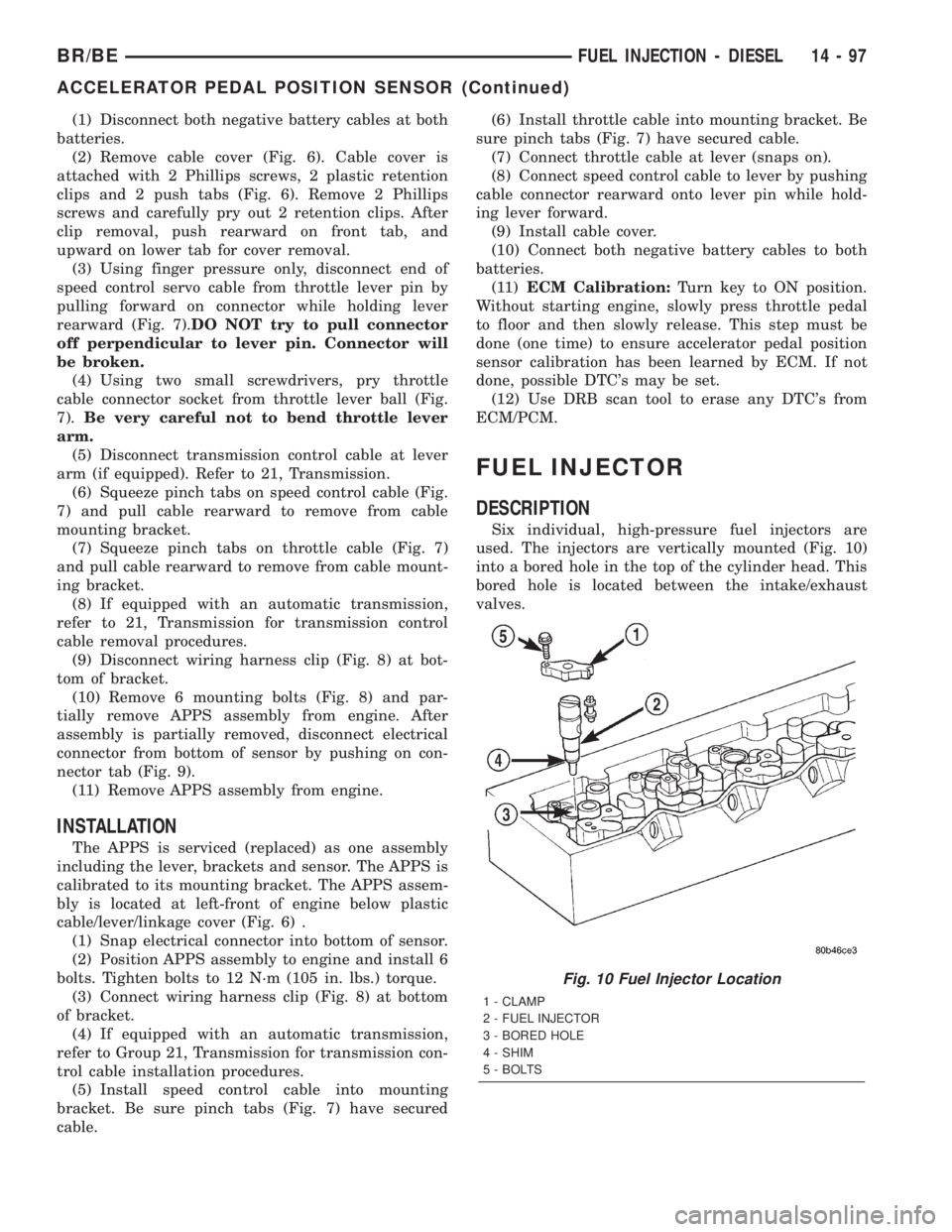
(1) Disconnect both negative battery cables at both
batteries.
(2) Remove cable cover (Fig. 6). Cable cover is
attached with 2 Phillips screws, 2 plastic retention
clips and 2 push tabs (Fig. 6). Remove 2 Phillips
screws and carefully pry out 2 retention clips. After
clip removal, push rearward on front tab, and
upward on lower tab for cover removal.
(3) Using finger pressure only, disconnect end of
speed control servo cable from throttle lever pin by
pulling forward on connector while holding lever
rearward (Fig. 7).DO NOT try to pull connector
off perpendicular to lever pin. Connector will
be broken.
(4) Using two small screwdrivers, pry throttle
cable connector socket from throttle lever ball (Fig.
7).Be very careful not to bend throttle lever
arm.
(5) Disconnect transmission control cable at lever
arm (if equipped). Refer to 21, Transmission.
(6) Squeeze pinch tabs on speed control cable (Fig.
7) and pull cable rearward to remove from cable
mounting bracket.
(7) Squeeze pinch tabs on throttle cable (Fig. 7)
and pull cable rearward to remove from cable mount-
ing bracket.
(8) If equipped with an automatic transmission,
refer to 21, Transmission for transmission control
cable removal procedures.
(9) Disconnect wiring harness clip (Fig. 8) at bot-
tom of bracket.
(10) Remove 6 mounting bolts (Fig. 8) and par-
tially remove APPS assembly from engine. After
assembly is partially removed, disconnect electrical
connector from bottom of sensor by pushing on con-
nector tab (Fig. 9).
(11) Remove APPS assembly from engine.
INSTALLATION
The APPS is serviced (replaced) as one assembly
including the lever, brackets and sensor. The APPS is
calibrated to its mounting bracket. The APPS assem-
bly is located at left-front of engine below plastic
cable/lever/linkage cover (Fig. 6) .
(1) Snap electrical connector into bottom of sensor.
(2) Position APPS assembly to engine and install 6
bolts. Tighten bolts to 12 N´m (105 in. lbs.) torque.
(3) Connect wiring harness clip (Fig. 8) at bottom
of bracket.
(4) If equipped with an automatic transmission,
refer to Group 21, Transmission for transmission con-
trol cable installation procedures.
(5) Install speed control cable into mounting
bracket. Be sure pinch tabs (Fig. 7) have secured
cable.(6) Install throttle cable into mounting bracket. Be
sure pinch tabs (Fig. 7) have secured cable.
(7) Connect throttle cable at lever (snaps on).
(8) Connect speed control cable to lever by pushing
cable connector rearward onto lever pin while hold-
ing lever forward.
(9) Install cable cover.
(10) Connect both negative battery cables to both
batteries.
(11)ECM Calibration:Turn key to ON position.
Without starting engine, slowly press throttle pedal
to floor and then slowly release. This step must be
done (one time) to ensure accelerator pedal position
sensor calibration has been learned by ECM. If not
done, possible DTC's may be set.
(12) Use DRB scan tool to erase any DTC's from
ECM/PCM.
FUEL INJECTOR
DESCRIPTION
Six individual, high-pressure fuel injectors are
used. The injectors are vertically mounted (Fig. 10)
into a bored hole in the top of the cylinder head. This
bored hole is located between the intake/exhaust
valves.
Fig. 10 Fuel Injector Location
1 - CLAMP
2 - FUEL INJECTOR
3 - BORED HOLE
4 - SHIM
5 - BOLTS
BR/BEFUEL INJECTION - DIESEL 14 - 97
ACCELERATOR PEDAL POSITION SENSOR (Continued)
Page 1397 of 2255
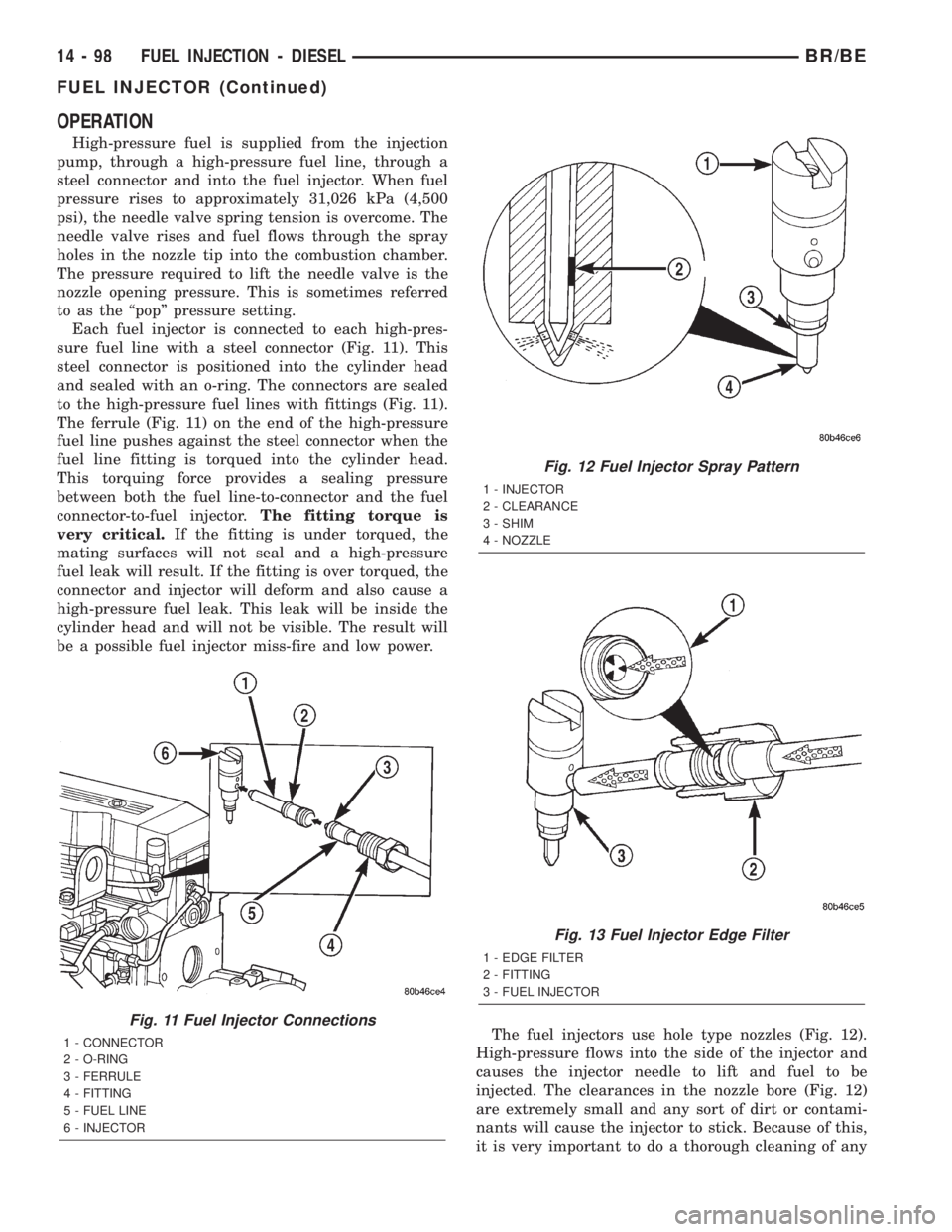
OPERATION
High-pressure fuel is supplied from the injection
pump, through a high-pressure fuel line, through a
steel connector and into the fuel injector. When fuel
pressure rises to approximately 31,026 kPa (4,500
psi), the needle valve spring tension is overcome. The
needle valve rises and fuel flows through the spray
holes in the nozzle tip into the combustion chamber.
The pressure required to lift the needle valve is the
nozzle opening pressure. This is sometimes referred
to as the ªpopº pressure setting.
Each fuel injector is connected to each high-pres-
sure fuel line with a steel connector (Fig. 11). This
steel connector is positioned into the cylinder head
and sealed with an o-ring. The connectors are sealed
to the high-pressure fuel lines with fittings (Fig. 11).
The ferrule (Fig. 11) on the end of the high-pressure
fuel line pushes against the steel connector when the
fuel line fitting is torqued into the cylinder head.
This torquing force provides a sealing pressure
between both the fuel line-to-connector and the fuel
connector-to-fuel injector.The fitting torque is
very critical.If the fitting is under torqued, the
mating surfaces will not seal and a high-pressure
fuel leak will result. If the fitting is over torqued, the
connector and injector will deform and also cause a
high-pressure fuel leak. This leak will be inside the
cylinder head and will not be visible. The result will
be a possible fuel injector miss-fire and low power.
The fuel injectors use hole type nozzles (Fig. 12).
High-pressure flows into the side of the injector and
causes the injector needle to lift and fuel to be
injected. The clearances in the nozzle bore (Fig. 12)
are extremely small and any sort of dirt or contami-
nants will cause the injector to stick. Because of this,
it is very important to do a thorough cleaning of any
Fig. 11 Fuel Injector Connections
1 - CONNECTOR
2 - O-RING
3 - FERRULE
4 - FITTING
5 - FUEL LINE
6 - INJECTOR
Fig. 12 Fuel Injector Spray Pattern
1 - INJECTOR
2 - CLEARANCE
3 - SHIM
4 - NOZZLE
Fig. 13 Fuel Injector Edge Filter
1 - EDGE FILTER
2 - FITTING
3 - FUEL INJECTOR
14 - 98 FUEL INJECTION - DIESELBR/BE
FUEL INJECTOR (Continued)
Page 1398 of 2255
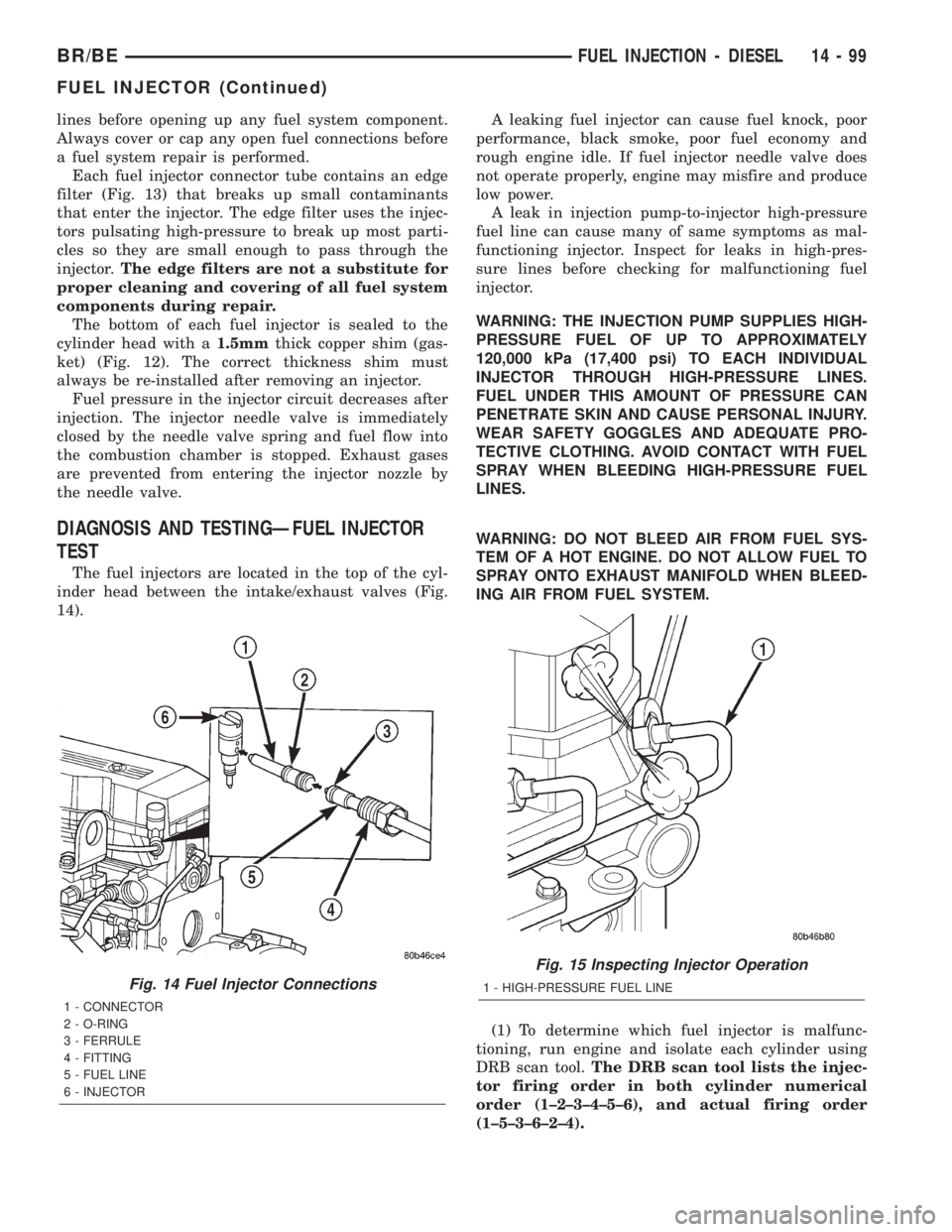
lines before opening up any fuel system component.
Always cover or cap any open fuel connections before
a fuel system repair is performed.
Each fuel injector connector tube contains an edge
filter (Fig. 13) that breaks up small contaminants
that enter the injector. The edge filter uses the injec-
tors pulsating high-pressure to break up most parti-
cles so they are small enough to pass through the
injector.The edge filters are not a substitute for
proper cleaning and covering of all fuel system
components during repair.
The bottom of each fuel injector is sealed to the
cylinder head with a1.5mmthick copper shim (gas-
ket) (Fig. 12). The correct thickness shim must
always be re-installed after removing an injector.
Fuel pressure in the injector circuit decreases after
injection. The injector needle valve is immediately
closed by the needle valve spring and fuel flow into
the combustion chamber is stopped. Exhaust gases
are prevented from entering the injector nozzle by
the needle valve.
DIAGNOSIS AND TESTINGÐFUEL INJECTOR
TEST
The fuel injectors are located in the top of the cyl-
inder head between the intake/exhaust valves (Fig.
14).A leaking fuel injector can cause fuel knock, poor
performance, black smoke, poor fuel economy and
rough engine idle. If fuel injector needle valve does
not operate properly, engine may misfire and produce
low power.
A leak in injection pump-to-injector high-pressure
fuel line can cause many of same symptoms as mal-
functioning injector. Inspect for leaks in high-pres-
sure lines before checking for malfunctioning fuel
injector.
WARNING: THE INJECTION PUMP SUPPLIES HIGH-
PRESSURE FUEL OF UP TO APPROXIMATELY
120,000 kPa (17,400 psi) TO EACH INDIVIDUAL
INJECTOR THROUGH HIGH-PRESSURE LINES.
FUEL UNDER THIS AMOUNT OF PRESSURE CAN
PENETRATE SKIN AND CAUSE PERSONAL INJURY.
WEAR SAFETY GOGGLES AND ADEQUATE PRO-
TECTIVE CLOTHING. AVOID CONTACT WITH FUEL
SPRAY WHEN BLEEDING HIGH-PRESSURE FUEL
LINES.
WARNING: DO NOT BLEED AIR FROM FUEL SYS-
TEM OF A HOT ENGINE. DO NOT ALLOW FUEL TO
SPRAY ONTO EXHAUST MANIFOLD WHEN BLEED-
ING AIR FROM FUEL SYSTEM.
(1) To determine which fuel injector is malfunc-
tioning, run engine and isolate each cylinder using
DRB scan tool.The DRB scan tool lists the injec-
tor firing order in both cylinder numerical
order (1±2±3±4±5±6), and actual firing order
(1±5±3±6±2±4).
Fig. 14 Fuel Injector Connections
1 - CONNECTOR
2 - O-RING
3 - FERRULE
4 - FITTING
5 - FUEL LINE
6 - INJECTOR
Fig. 15 Inspecting Injector Operation
1 - HIGH-PRESSURE FUEL LINE
BR/BEFUEL INJECTION - DIESEL 14 - 99
FUEL INJECTOR (Continued)
Page 1399 of 2255
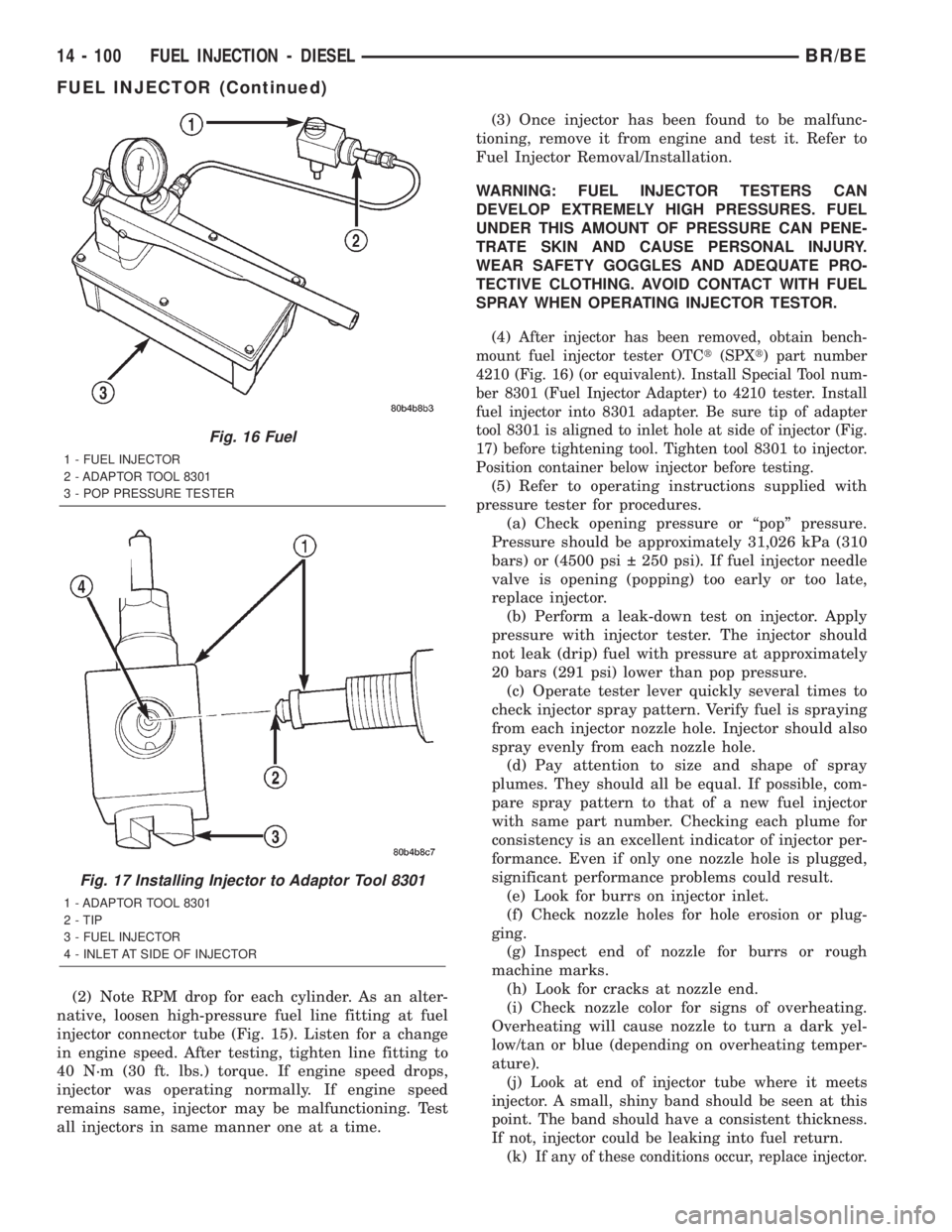
(2) Note RPM drop for each cylinder. As an alter-
native, loosen high-pressure fuel line fitting at fuel
injector connector tube (Fig. 15). Listen for a change
in engine speed. After testing, tighten line fitting to
40 N´m (30 ft. lbs.) torque. If engine speed drops,
injector was operating normally. If engine speed
remains same, injector may be malfunctioning. Test
all injectors in same manner one at a time.(3) Once injector has been found to be malfunc-
tioning, remove it from engine and test it. Refer to
Fuel Injector Removal/Installation.
WARNING: FUEL INJECTOR TESTERS CAN
DEVELOP EXTREMELY HIGH PRESSURES. FUEL
UNDER THIS AMOUNT OF PRESSURE CAN PENE-
TRATE SKIN AND CAUSE PERSONAL INJURY.
WEAR SAFETY GOGGLES AND ADEQUATE PRO-
TECTIVE CLOTHING. AVOID CONTACT WITH FUEL
SPRAY WHEN OPERATING INJECTOR TESTOR.
(4)
After injector has been removed, obtain bench-
mount fuel injector tester OTCt(SPXt) part number
4210 (Fig. 16) (or equivalent). Install Special Tool num-
ber 8301 (Fuel Injector Adapter) to 4210 tester. Install
fuel injector into 8301 adapter. Be sure tip of adapter
tool 8301 is aligned to inlet hole at side of injector (Fig.
17) before tightening tool. Tighten tool 8301 to injector.
Position container below injector before testing.
(5) Refer to operating instructions supplied with
pressure tester for procedures.
(a) Check opening pressure or ªpopº pressure.
Pressure should be approximately 31,026 kPa (310
bars) or (4500 psi 250 psi). If fuel injector needle
valve is opening (popping) too early or too late,
replace injector.
(b) Perform a leak-down test on injector. Apply
pressure with injector tester. The injector should
not leak (drip) fuel with pressure at approximately
20 bars (291 psi) lower than pop pressure.
(c) Operate tester lever quickly several times to
check injector spray pattern. Verify fuel is spraying
from each injector nozzle hole. Injector should also
spray evenly from each nozzle hole.
(d) Pay attention to size and shape of spray
plumes. They should all be equal. If possible, com-
pare spray pattern to that of a new fuel injector
with same part number. Checking each plume for
consistency is an excellent indicator of injector per-
formance. Even if only one nozzle hole is plugged,
significant performance problems could result.
(e) Look for burrs on injector inlet.
(f) Check nozzle holes for hole erosion or plug-
ging.
(g) Inspect end of nozzle for burrs or rough
machine marks.
(h) Look for cracks at nozzle end.
(i) Check nozzle color for signs of overheating.
Overheating will cause nozzle to turn a dark yel-
low/tan or blue (depending on overheating temper-
ature).
(j)
Look at end of injector tube where it meets
injector. A small, shiny band should be seen at this
point. The band should have a consistent thickness.
If not, injector could be leaking into fuel return.
(k)If any of these conditions occur, replace injector.
Fig. 16 Fuel
1 - FUEL INJECTOR
2 - ADAPTOR TOOL 8301
3 - POP PRESSURE TESTER
Fig. 17 Installing Injector to Adaptor Tool 8301
1 - ADAPTOR TOOL 8301
2 - TIP
3 - FUEL INJECTOR
4 - INLET AT SIDE OF INJECTOR
14 - 100 FUEL INJECTION - DIESELBR/BE
FUEL INJECTOR (Continued)
Page 1400 of 2255
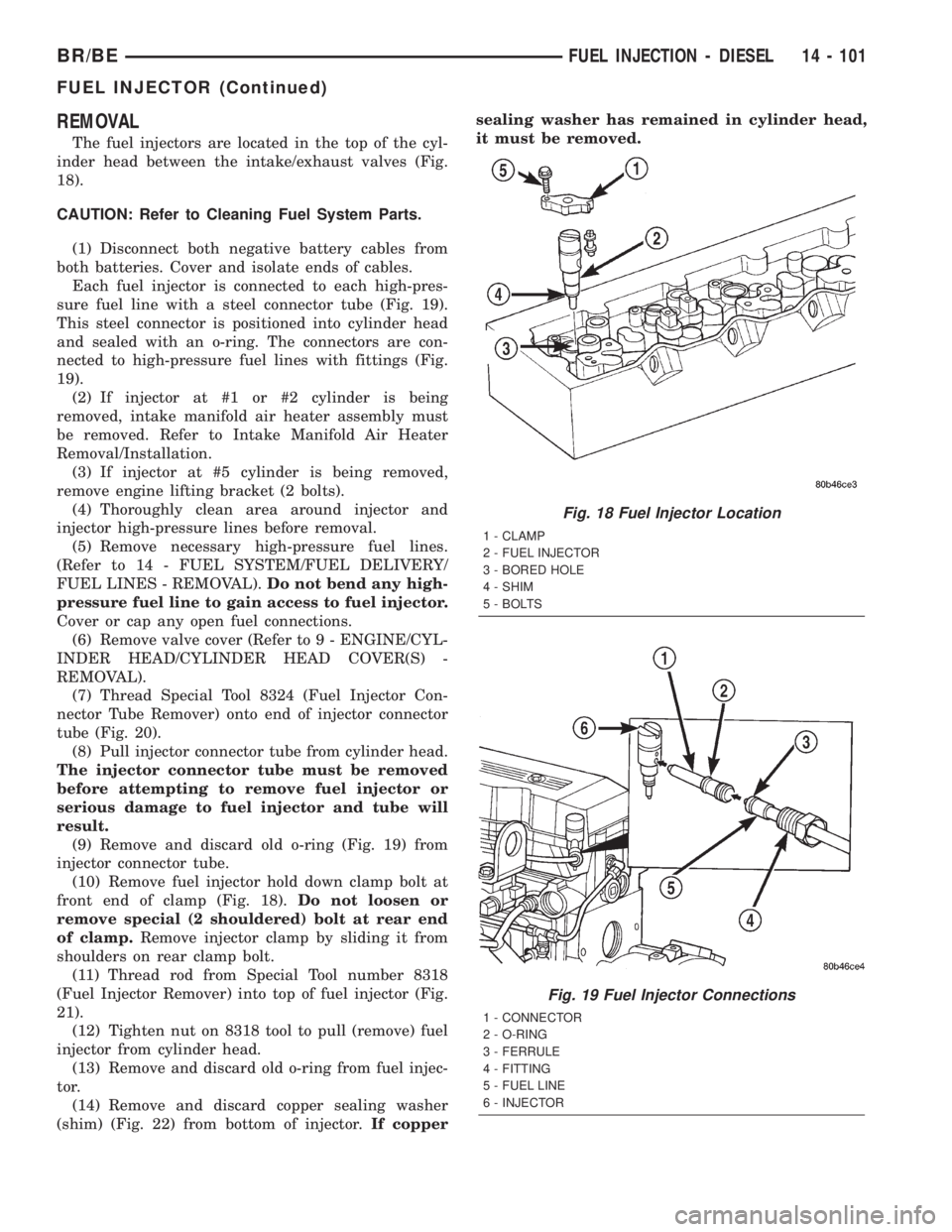
REMOVAL
The fuel injectors are located in the top of the cyl-
inder head between the intake/exhaust valves (Fig.
18).
CAUTION: Refer to Cleaning Fuel System Parts.
(1) Disconnect both negative battery cables from
both batteries. Cover and isolate ends of cables.
Each fuel injector is connected to each high-pres-
sure fuel line with a steel connector tube (Fig. 19).
This steel connector is positioned into cylinder head
and sealed with an o-ring. The connectors are con-
nected to high-pressure fuel lines with fittings (Fig.
19).
(2) If injector at #1 or #2 cylinder is being
removed, intake manifold air heater assembly must
be removed. Refer to Intake Manifold Air Heater
Removal/Installation.
(3) If injector at #5 cylinder is being removed,
remove engine lifting bracket (2 bolts).
(4) Thoroughly clean area around injector and
injector high-pressure lines before removal.
(5) Remove necessary high-pressure fuel lines.
(Refer to 14 - FUEL SYSTEM/FUEL DELIVERY/
FUEL LINES - REMOVAL).Do not bend any high-
pressure fuel line to gain access to fuel injector.
Cover or cap any open fuel connections.
(6) Remove valve cover (Refer to 9 - ENGINE/CYL-
INDER HEAD/CYLINDER HEAD COVER(S) -
REMOVAL).
(7) Thread Special Tool 8324 (Fuel Injector Con-
nector Tube Remover) onto end of injector connector
tube (Fig. 20).
(8) Pull injector connector tube from cylinder head.
The injector connector tube must be removed
before attempting to remove fuel injector or
serious damage to fuel injector and tube will
result.
(9) Remove and discard old o-ring (Fig. 19) from
injector connector tube.
(10) Remove fuel injector hold down clamp bolt at
front end of clamp (Fig. 18).Do not loosen or
remove special (2 shouldered) bolt at rear end
of clamp.Remove injector clamp by sliding it from
shoulders on rear clamp bolt.
(11) Thread rod from Special Tool number 8318
(Fuel Injector Remover) into top of fuel injector (Fig.
21).
(12) Tighten nut on 8318 tool to pull (remove) fuel
injector from cylinder head.
(13) Remove and discard old o-ring from fuel injec-
tor.
(14) Remove and discard copper sealing washer
(shim) (Fig. 22) from bottom of injector.If coppersealing washer has remained in cylinder head,
it must be removed.
Fig. 18 Fuel Injector Location
1 - CLAMP
2 - FUEL INJECTOR
3 - BORED HOLE
4 - SHIM
5 - BOLTS
Fig. 19 Fuel Injector Connections
1 - CONNECTOR
2 - O-RING
3 - FERRULE
4 - FITTING
5 - FUEL LINE
6 - INJECTOR
BR/BEFUEL INJECTION - DIESEL 14 - 101
FUEL INJECTOR (Continued)