Page 2209 of 2255
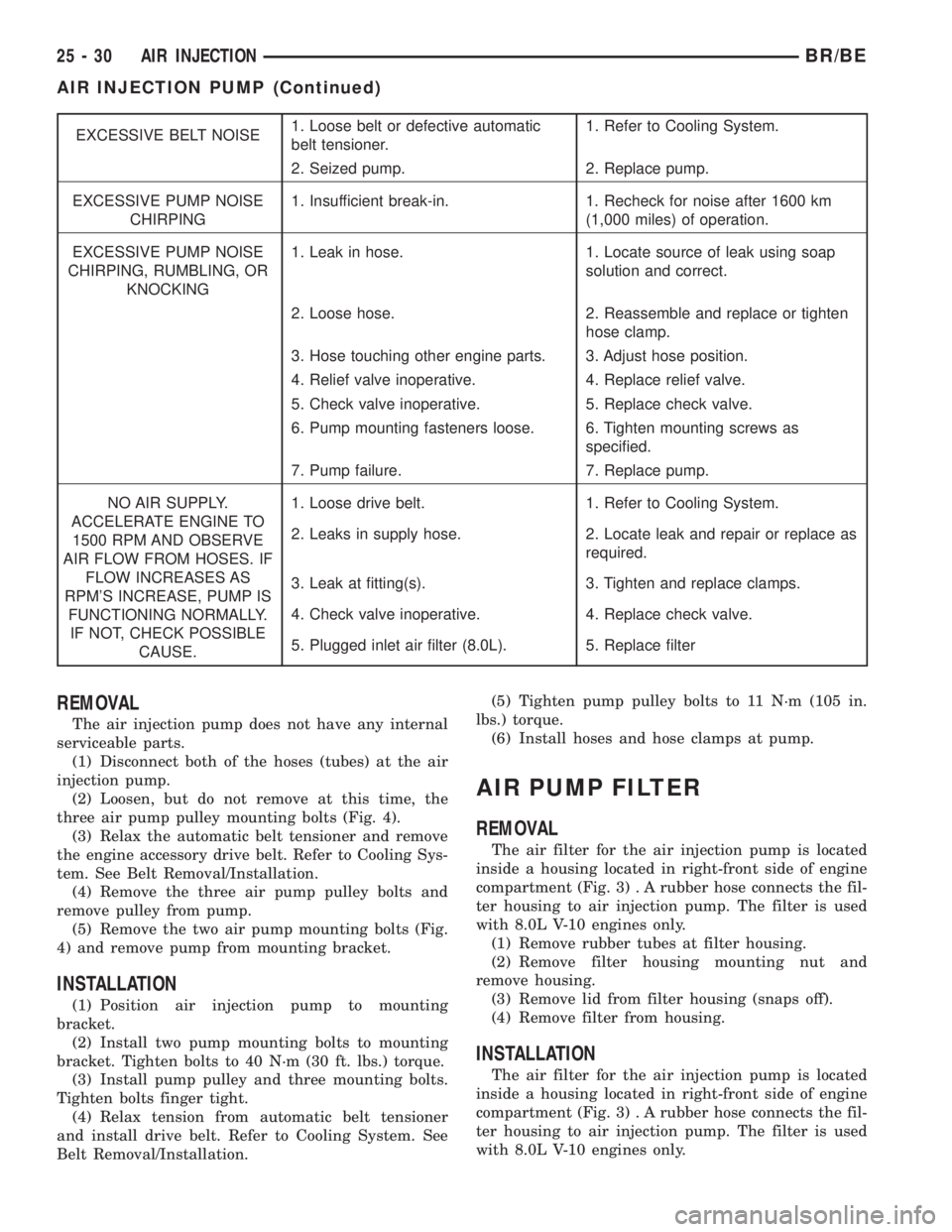
EXCESSIVE BELT NOISE1. Loose belt or defective automatic
belt tensioner.1. Refer to Cooling System.
2. Seized pump. 2. Replace pump.
EXCESSIVE PUMP NOISE
CHIRPING1. Insufficient break-in. 1. Recheck for noise after 1600 km
(1,000 miles) of operation.
EXCESSIVE PUMP NOISE
CHIRPING, RUMBLING, OR
KNOCKING1. Leak in hose. 1. Locate source of leak using soap
solution and correct.
2. Loose hose. 2. Reassemble and replace or tighten
hose clamp.
3. Hose touching other engine parts. 3. Adjust hose position.
4. Relief valve inoperative. 4. Replace relief valve.
5. Check valve inoperative. 5. Replace check valve.
6. Pump mounting fasteners loose. 6. Tighten mounting screws as
specified.
7. Pump failure. 7. Replace pump.
NO AIR SUPPLY.
ACCELERATE ENGINE TO
1500 RPM AND OBSERVE
AIR FLOW FROM HOSES. IF
FLOW INCREASES AS
RPM'S INCREASE, PUMP IS
FUNCTIONING NORMALLY.
IF NOT, CHECK POSSIBLE
CAUSE.1. Loose drive belt. 1. Refer to Cooling System.
2. Leaks in supply hose. 2. Locate leak and repair or replace as
required.
3. Leak at fitting(s). 3. Tighten and replace clamps.
4. Check valve inoperative. 4. Replace check valve.
5. Plugged inlet air filter (8.0L). 5. Replace filter
REMOVAL
The air injection pump does not have any internal
serviceable parts.
(1) Disconnect both of the hoses (tubes) at the air
injection pump.
(2) Loosen, but do not remove at this time, the
three air pump pulley mounting bolts (Fig. 4).
(3) Relax the automatic belt tensioner and remove
the engine accessory drive belt. Refer to Cooling Sys-
tem. See Belt Removal/Installation.
(4) Remove the three air pump pulley bolts and
remove pulley from pump.
(5) Remove the two air pump mounting bolts (Fig.
4) and remove pump from mounting bracket.
INSTALLATION
(1) Position air injection pump to mounting
bracket.
(2) Install two pump mounting bolts to mounting
bracket. Tighten bolts to 40 N´m (30 ft. lbs.) torque.
(3) Install pump pulley and three mounting bolts.
Tighten bolts finger tight.
(4) Relax tension from automatic belt tensioner
and install drive belt. Refer to Cooling System. See
Belt Removal/Installation.(5) Tighten pump pulley bolts to 11 N´m (105 in.
lbs.) torque.
(6) Install hoses and hose clamps at pump.
AIR PUMP FILTER
REMOVAL
The air filter for the air injection pump is located
inside a housing located in right-front side of engine
compartment (Fig. 3) . A rubber hose connects the fil-
ter housing to air injection pump. The filter is used
with 8.0L V-10 engines only.
(1) Remove rubber tubes at filter housing.
(2) Remove filter housing mounting nut and
remove housing.
(3) Remove lid from filter housing (snaps off).
(4) Remove filter from housing.
INSTALLATION
The air filter for the air injection pump is located
inside a housing located in right-front side of engine
compartment (Fig. 3) . A rubber hose connects the fil-
ter housing to air injection pump. The filter is used
with 8.0L V-10 engines only.
25 - 30 AIR INJECTIONBR/BE
AIR INJECTION PUMP (Continued)
Page 2210 of 2255
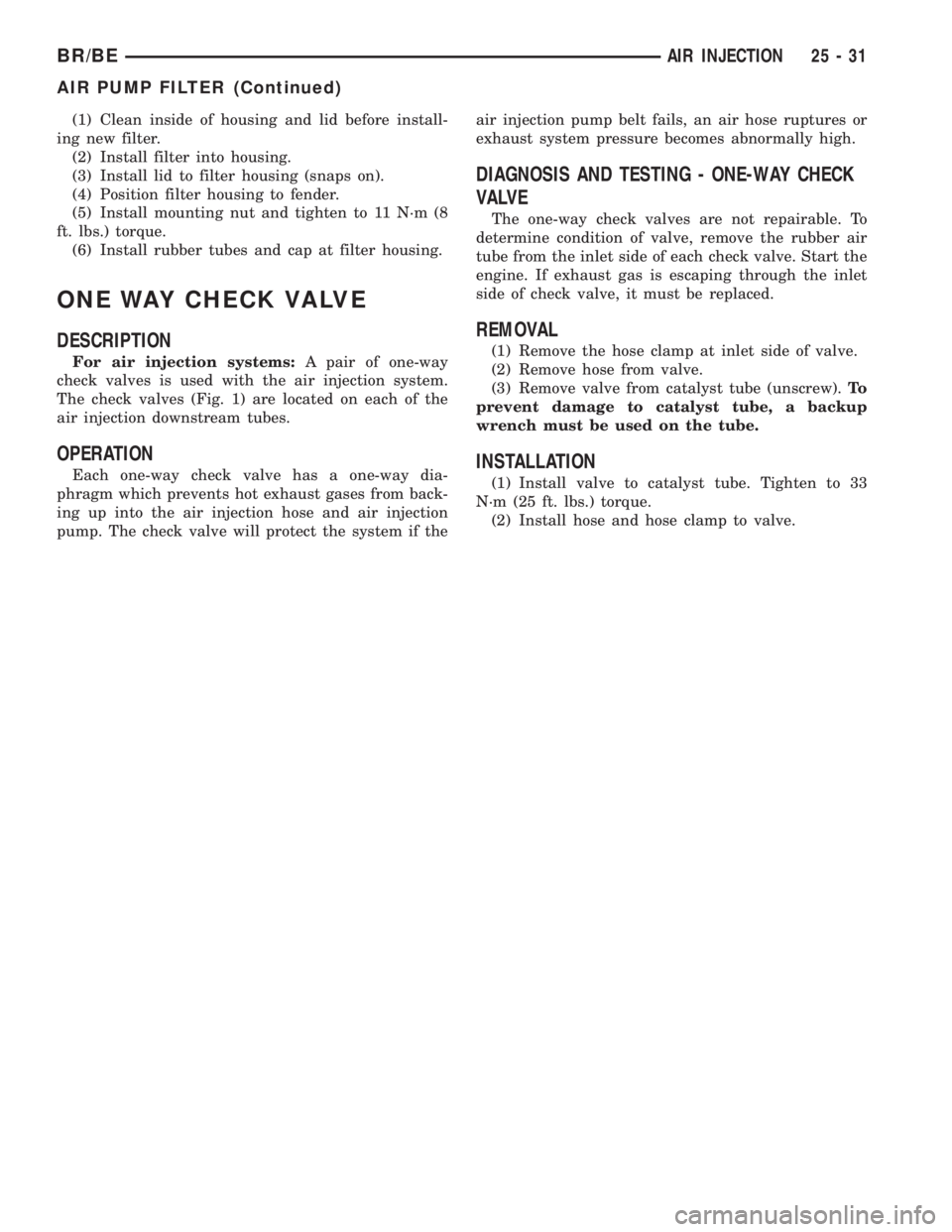
(1) Clean inside of housing and lid before install-
ing new filter.
(2) Install filter into housing.
(3) Install lid to filter housing (snaps on).
(4) Position filter housing to fender.
(5) Install mounting nut and tighten to 11 N´m (8
ft. lbs.) torque.
(6) Install rubber tubes and cap at filter housing.
ONE WAY CHECK VALVE
DESCRIPTION
For air injection systems:A pair of one-way
check valves is used with the air injection system.
The check valves (Fig. 1) are located on each of the
air injection downstream tubes.
OPERATION
Each one-way check valve has a one-way dia-
phragm which prevents hot exhaust gases from back-
ing up into the air injection hose and air injection
pump. The check valve will protect the system if theair injection pump belt fails, an air hose ruptures or
exhaust system pressure becomes abnormally high.
DIAGNOSIS AND TESTING - ONE-WAY CHECK
VALVE
The one-way check valves are not repairable. To
determine condition of valve, remove the rubber air
tube from the inlet side of each check valve. Start the
engine. If exhaust gas is escaping through the inlet
side of check valve, it must be replaced.
REMOVAL
(1) Remove the hose clamp at inlet side of valve.
(2) Remove hose from valve.
(3) Remove valve from catalyst tube (unscrew).To
prevent damage to catalyst tube, a backup
wrench must be used on the tube.
INSTALLATION
(1) Install valve to catalyst tube. Tighten to 33
N´m (25 ft. lbs.) torque.
(2) Install hose and hose clamp to valve.
BR/BEAIR INJECTION 25 - 31
AIR PUMP FILTER (Continued)
Page 2211 of 2255
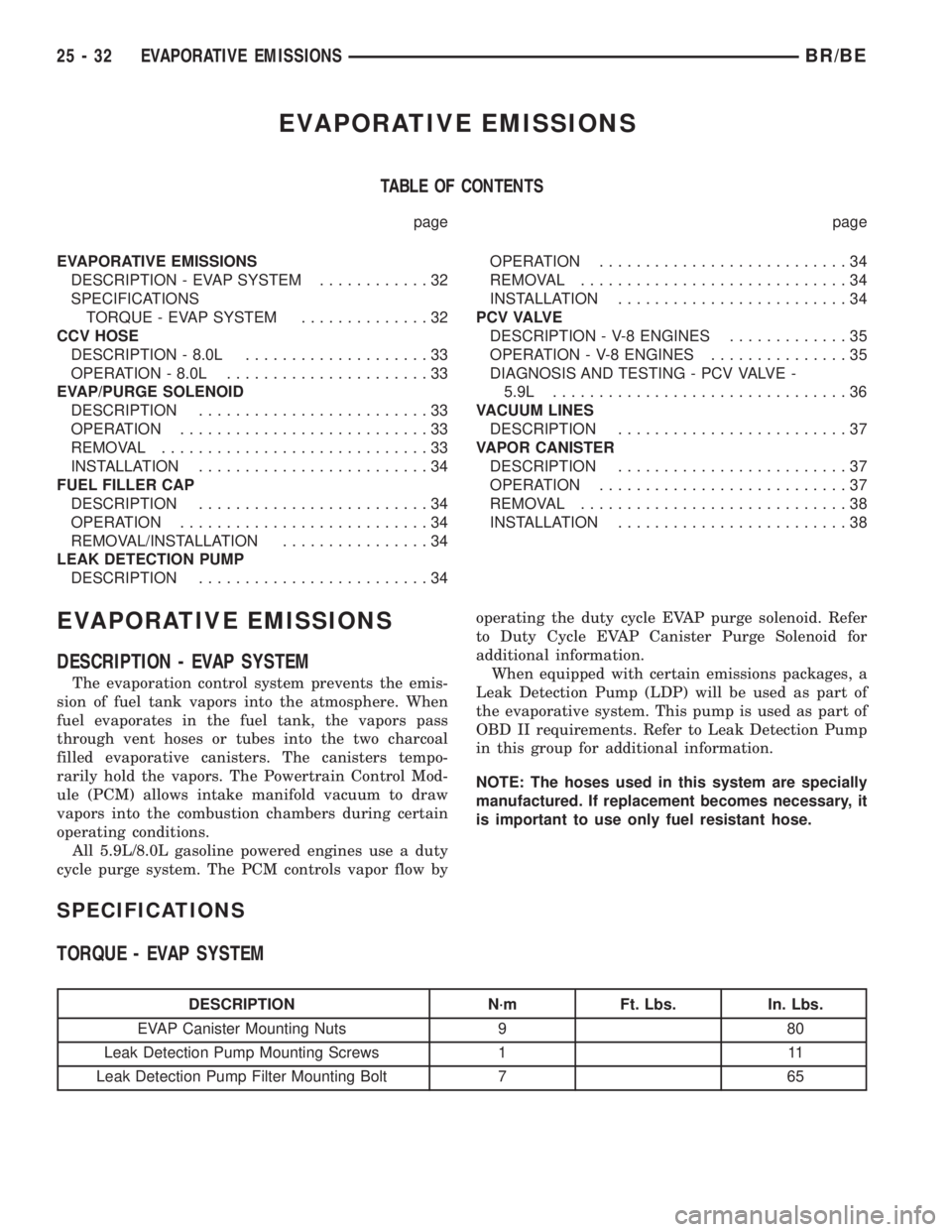
EVAPORATIVE EMISSIONS
TABLE OF CONTENTS
page page
EVAPORATIVE EMISSIONS
DESCRIPTION - EVAP SYSTEM............32
SPECIFICATIONS
TORQUE - EVAP SYSTEM..............32
CCV HOSE
DESCRIPTION - 8.0L....................33
OPERATION - 8.0L......................33
EVAP/PURGE SOLENOID
DESCRIPTION.........................33
OPERATION...........................33
REMOVAL.............................33
INSTALLATION.........................34
FUEL FILLER CAP
DESCRIPTION.........................34
OPERATION...........................34
REMOVAL/INSTALLATION................34
LEAK DETECTION PUMP
DESCRIPTION.........................34OPERATION...........................34
REMOVAL.............................34
INSTALLATION.........................34
P C V VA LV E
DESCRIPTION - V-8 ENGINES.............35
OPERATION - V-8 ENGINES...............35
DIAGNOSIS AND TESTING - PCV VALVE -
5.9L................................36
VACUUM LINES
DESCRIPTION.........................37
VAPOR CANISTER
DESCRIPTION.........................37
OPERATION...........................37
REMOVAL.............................38
INSTALLATION.........................38
EVAPORATIVE EMISSIONS
DESCRIPTION - EVAP SYSTEM
The evaporation control system prevents the emis-
sion of fuel tank vapors into the atmosphere. When
fuel evaporates in the fuel tank, the vapors pass
through vent hoses or tubes into the two charcoal
filled evaporative canisters. The canisters tempo-
rarily hold the vapors. The Powertrain Control Mod-
ule (PCM) allows intake manifold vacuum to draw
vapors into the combustion chambers during certain
operating conditions.
All 5.9L/8.0L gasoline powered engines use a duty
cycle purge system. The PCM controls vapor flow byoperating the duty cycle EVAP purge solenoid. Refer
to Duty Cycle EVAP Canister Purge Solenoid for
additional information.
When equipped with certain emissions packages, a
Leak Detection Pump (LDP) will be used as part of
the evaporative system. This pump is used as part of
OBD II requirements. Refer to Leak Detection Pump
in this group for additional information.
NOTE: The hoses used in this system are specially
manufactured. If replacement becomes necessary, it
is important to use only fuel resistant hose.
SPECIFICATIONS
TORQUE - EVAP SYSTEM
DESCRIPTION N´m Ft. Lbs. In. Lbs.
EVAP Canister Mounting Nuts 9 80
Leak Detection Pump Mounting Screws 1 11
Leak Detection Pump Filter Mounting Bolt 7 65
25 - 32 EVAPORATIVE EMISSIONSBR/BE
Page 2212 of 2255
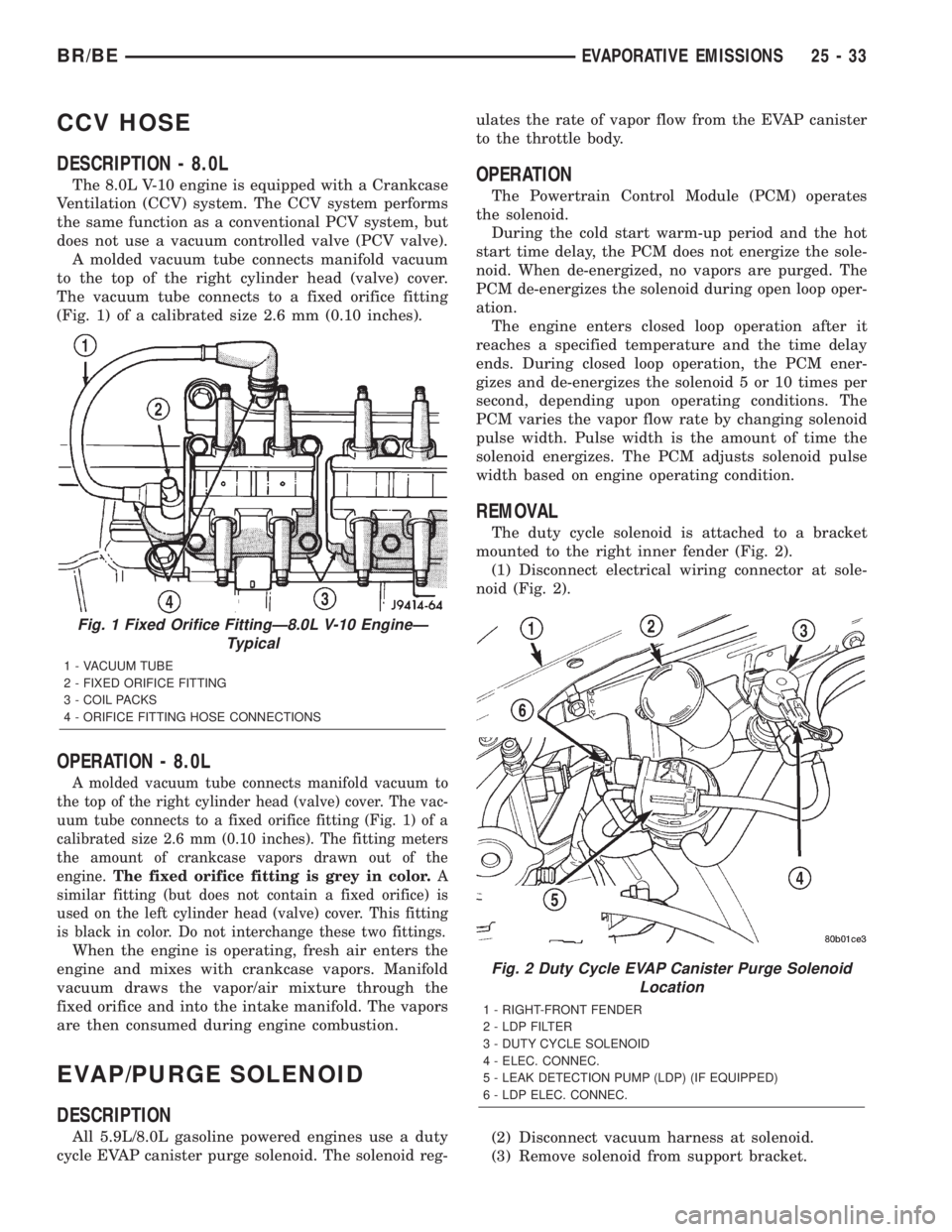
CCV HOSE
DESCRIPTION - 8.0L
The 8.0L V-10 engine is equipped with a Crankcase
Ventilation (CCV) system. The CCV system performs
the same function as a conventional PCV system, but
does not use a vacuum controlled valve (PCV valve).
A molded vacuum tube connects manifold vacuum
to the top of the right cylinder head (valve) cover.
The vacuum tube connects to a fixed orifice fitting
(Fig. 1) of a calibrated size 2.6 mm (0.10 inches).
OPERATION - 8.0L
A molded vacuum tube connects manifold vacuum to
the top of the right cylinder head (valve) cover. The vac-
uum tube connects to a fixed orifice fitting (Fig. 1) of a
calibrated size 2.6 mm (0.10 inches). The fitting meters
the amount of crankcase vapors drawn out of the
engine.The fixed orifice fitting is grey in color.A
similar fitting (but does not contain a fixed orifice) is
used on the left cylinder head (valve) cover. This fitting
is black in color. Do not interchange these two fittings.
When the engine is operating, fresh air enters the
engine and mixes with crankcase vapors. Manifold
vacuum draws the vapor/air mixture through the
fixed orifice and into the intake manifold. The vapors
are then consumed during engine combustion.
EVAP/PURGE SOLENOID
DESCRIPTION
All 5.9L/8.0L gasoline powered engines use a duty
cycle EVAP canister purge solenoid. The solenoid reg-ulates the rate of vapor flow from the EVAP canister
to the throttle body.
OPERATION
The Powertrain Control Module (PCM) operates
the solenoid.
During the cold start warm-up period and the hot
start time delay, the PCM does not energize the sole-
noid. When de-energized, no vapors are purged. The
PCM de-energizes the solenoid during open loop oper-
ation.
The engine enters closed loop operation after it
reaches a specified temperature and the time delay
ends. During closed loop operation, the PCM ener-
gizes and de-energizes the solenoid 5 or 10 times per
second, depending upon operating conditions. The
PCM varies the vapor flow rate by changing solenoid
pulse width. Pulse width is the amount of time the
solenoid energizes. The PCM adjusts solenoid pulse
width based on engine operating condition.
REMOVAL
The duty cycle solenoid is attached to a bracket
mounted to the right inner fender (Fig. 2).
(1) Disconnect electrical wiring connector at sole-
noid (Fig. 2).
(2) Disconnect vacuum harness at solenoid.
(3) Remove solenoid from support bracket.
Fig. 1 Fixed Orifice FittingÐ8.0L V-10 EngineÐ
Typical
1 - VACUUM TUBE
2 - FIXED ORIFICE FITTING
3 - COIL PACKS
4 - ORIFICE FITTING HOSE CONNECTIONS
Fig. 2 Duty Cycle EVAP Canister Purge Solenoid
Location
1 - RIGHT-FRONT FENDER
2 - LDP FILTER
3 - DUTY CYCLE SOLENOID
4 - ELEC. CONNEC.
5 - LEAK DETECTION PUMP (LDP) (IF EQUIPPED)
6 - LDP ELEC. CONNEC.
BR/BEEVAPORATIVE EMISSIONS 25 - 33
Page 2213 of 2255
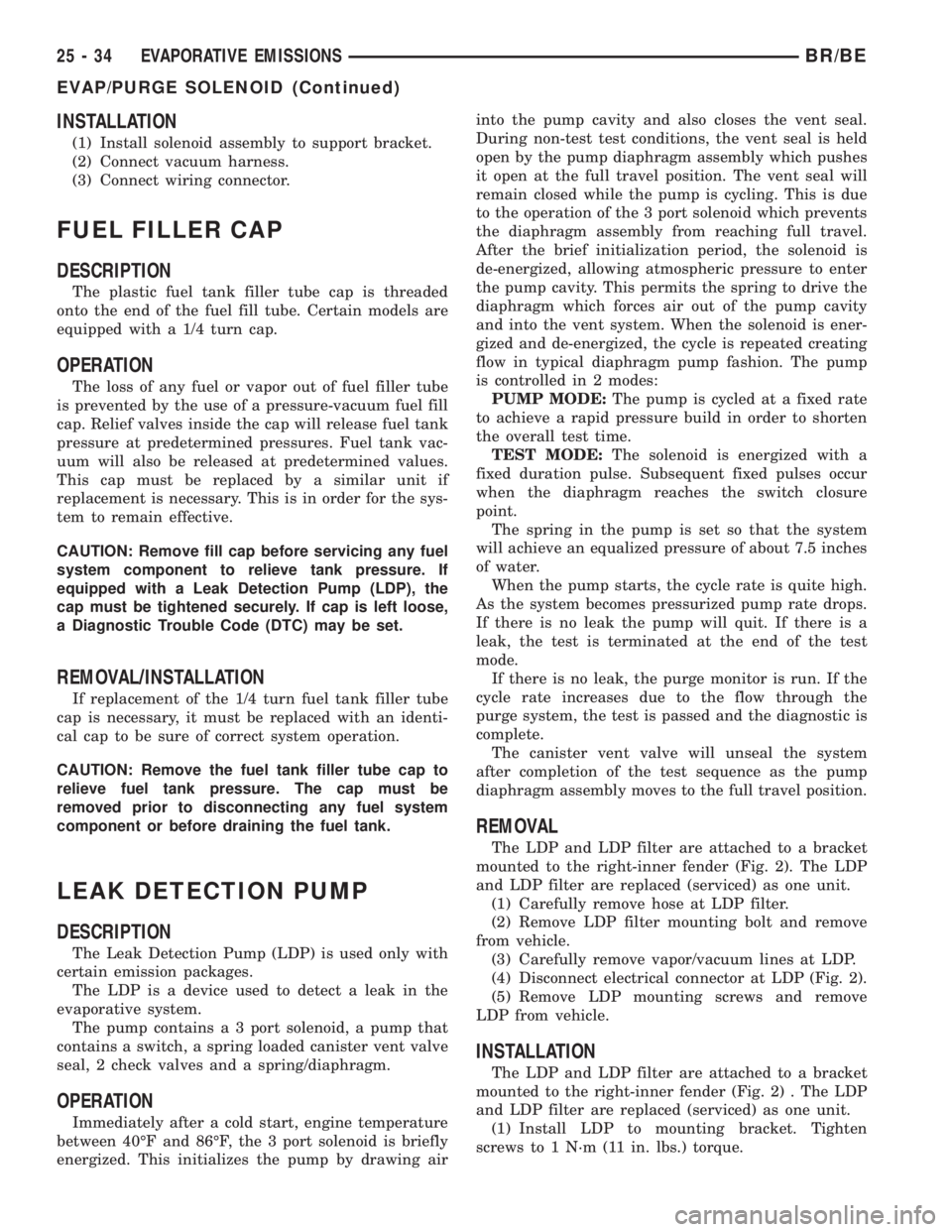
INSTALLATION
(1) Install solenoid assembly to support bracket.
(2) Connect vacuum harness.
(3) Connect wiring connector.
FUEL FILLER CAP
DESCRIPTION
The plastic fuel tank filler tube cap is threaded
onto the end of the fuel fill tube. Certain models are
equipped with a 1/4 turn cap.
OPERATION
The loss of any fuel or vapor out of fuel filler tube
is prevented by the use of a pressure-vacuum fuel fill
cap. Relief valves inside the cap will release fuel tank
pressure at predetermined pressures. Fuel tank vac-
uum will also be released at predetermined values.
This cap must be replaced by a similar unit if
replacement is necessary. This is in order for the sys-
tem to remain effective.
CAUTION: Remove fill cap before servicing any fuel
system component to relieve tank pressure. If
equipped with a Leak Detection Pump (LDP), the
cap must be tightened securely. If cap is left loose,
a Diagnostic Trouble Code (DTC) may be set.
REMOVAL/INSTALLATION
If replacement of the 1/4 turn fuel tank filler tube
cap is necessary, it must be replaced with an identi-
cal cap to be sure of correct system operation.
CAUTION: Remove the fuel tank filler tube cap to
relieve fuel tank pressure. The cap must be
removed prior to disconnecting any fuel system
component or before draining the fuel tank.
LEAK DETECTION PUMP
DESCRIPTION
The Leak Detection Pump (LDP) is used only with
certain emission packages.
The LDP is a device used to detect a leak in the
evaporative system.
The pump contains a 3 port solenoid, a pump that
contains a switch, a spring loaded canister vent valve
seal, 2 check valves and a spring/diaphragm.
OPERATION
Immediately after a cold start, engine temperature
between 40ÉF and 86ÉF, the 3 port solenoid is briefly
energized. This initializes the pump by drawing airinto the pump cavity and also closes the vent seal.
During non-test test conditions, the vent seal is held
open by the pump diaphragm assembly which pushes
it open at the full travel position. The vent seal will
remain closed while the pump is cycling. This is due
to the operation of the 3 port solenoid which prevents
the diaphragm assembly from reaching full travel.
After the brief initialization period, the solenoid is
de-energized, allowing atmospheric pressure to enter
the pump cavity. This permits the spring to drive the
diaphragm which forces air out of the pump cavity
and into the vent system. When the solenoid is ener-
gized and de-energized, the cycle is repeated creating
flow in typical diaphragm pump fashion. The pump
is controlled in 2 modes:
PUMP MODE:The pump is cycled at a fixed rate
to achieve a rapid pressure build in order to shorten
the overall test time.
TEST MODE:The solenoid is energized with a
fixed duration pulse. Subsequent fixed pulses occur
when the diaphragm reaches the switch closure
point.
The spring in the pump is set so that the system
will achieve an equalized pressure of about 7.5 inches
of water.
When the pump starts, the cycle rate is quite high.
As the system becomes pressurized pump rate drops.
If there is no leak the pump will quit. If there is a
leak, the test is terminated at the end of the test
mode.
If there is no leak, the purge monitor is run. If the
cycle rate increases due to the flow through the
purge system, the test is passed and the diagnostic is
complete.
The canister vent valve will unseal the system
after completion of the test sequence as the pump
diaphragm assembly moves to the full travel position.
REMOVAL
The LDP and LDP filter are attached to a bracket
mounted to the right-inner fender (Fig. 2). The LDP
and LDP filter are replaced (serviced) as one unit.
(1) Carefully remove hose at LDP filter.
(2) Remove LDP filter mounting bolt and remove
from vehicle.
(3) Carefully remove vapor/vacuum lines at LDP.
(4) Disconnect electrical connector at LDP (Fig. 2).
(5) Remove LDP mounting screws and remove
LDP from vehicle.
INSTALLATION
The LDP and LDP filter are attached to a bracket
mounted to the right-inner fender (Fig. 2) . The LDP
and LDP filter are replaced (serviced) as one unit.
(1) Install LDP to mounting bracket. Tighten
screws to 1 N´m (11 in. lbs.) torque.
25 - 34 EVAPORATIVE EMISSIONSBR/BE
EVAP/PURGE SOLENOID (Continued)
Page 2214 of 2255
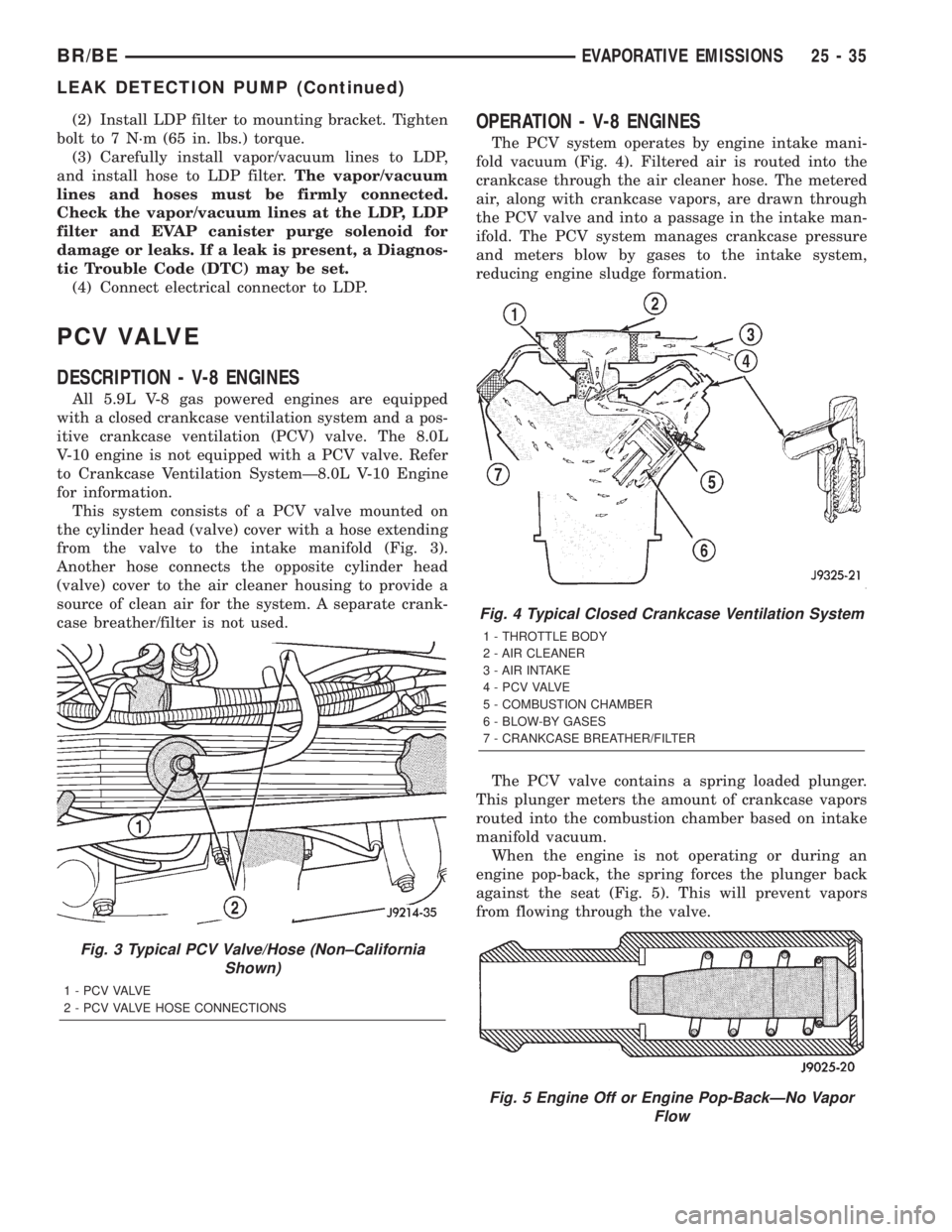
(2) Install LDP filter to mounting bracket. Tighten
bolt to 7 N´m (65 in. lbs.) torque.
(3) Carefully install vapor/vacuum lines to LDP,
and install hose to LDP filter.The vapor/vacuum
lines and hoses must be firmly connected.
Check the vapor/vacuum lines at the LDP, LDP
filter and EVAP canister purge solenoid for
damage or leaks. If a leak is present, a Diagnos-
tic Trouble Code (DTC) may be set.
(4) Connect electrical connector to LDP.
PCV VALVE
DESCRIPTION - V-8 ENGINES
All 5.9L V-8 gas powered engines are equipped
with a closed crankcase ventilation system and a pos-
itive crankcase ventilation (PCV) valve. The 8.0L
V-10 engine is not equipped with a PCV valve. Refer
to Crankcase Ventilation SystemÐ8.0L V-10 Engine
for information.
This system consists of a PCV valve mounted on
the cylinder head (valve) cover with a hose extending
from the valve to the intake manifold (Fig. 3).
Another hose connects the opposite cylinder head
(valve) cover to the air cleaner housing to provide a
source of clean air for the system. A separate crank-
case breather/filter is not used.
OPERATION - V-8 ENGINES
The PCV system operates by engine intake mani-
fold vacuum (Fig. 4). Filtered air is routed into the
crankcase through the air cleaner hose. The metered
air, along with crankcase vapors, are drawn through
the PCV valve and into a passage in the intake man-
ifold. The PCV system manages crankcase pressure
and meters blow by gases to the intake system,
reducing engine sludge formation.
The PCV valve contains a spring loaded plunger.
This plunger meters the amount of crankcase vapors
routed into the combustion chamber based on intake
manifold vacuum.
When the engine is not operating or during an
engine pop-back, the spring forces the plunger back
against the seat (Fig. 5). This will prevent vapors
from flowing through the valve.
Fig. 3 Typical PCV Valve/Hose (Non±California
Shown)
1 - P C V VA LV E
2 - PCV VALVE HOSE CONNECTIONS
Fig. 4 Typical Closed Crankcase Ventilation System
1 - THROTTLE BODY
2 - AIR CLEANER
3 - AIR INTAKE
4 - P C V VA LV E
5 - COMBUSTION CHAMBER
6 - BLOW-BY GASES
7 - CRANKCASE BREATHER/FILTER
Fig. 5 Engine Off or Engine Pop-BackÐNo Vapor
Flow
BR/BEEVAPORATIVE EMISSIONS 25 - 35
LEAK DETECTION PUMP (Continued)
Page 2215 of 2255
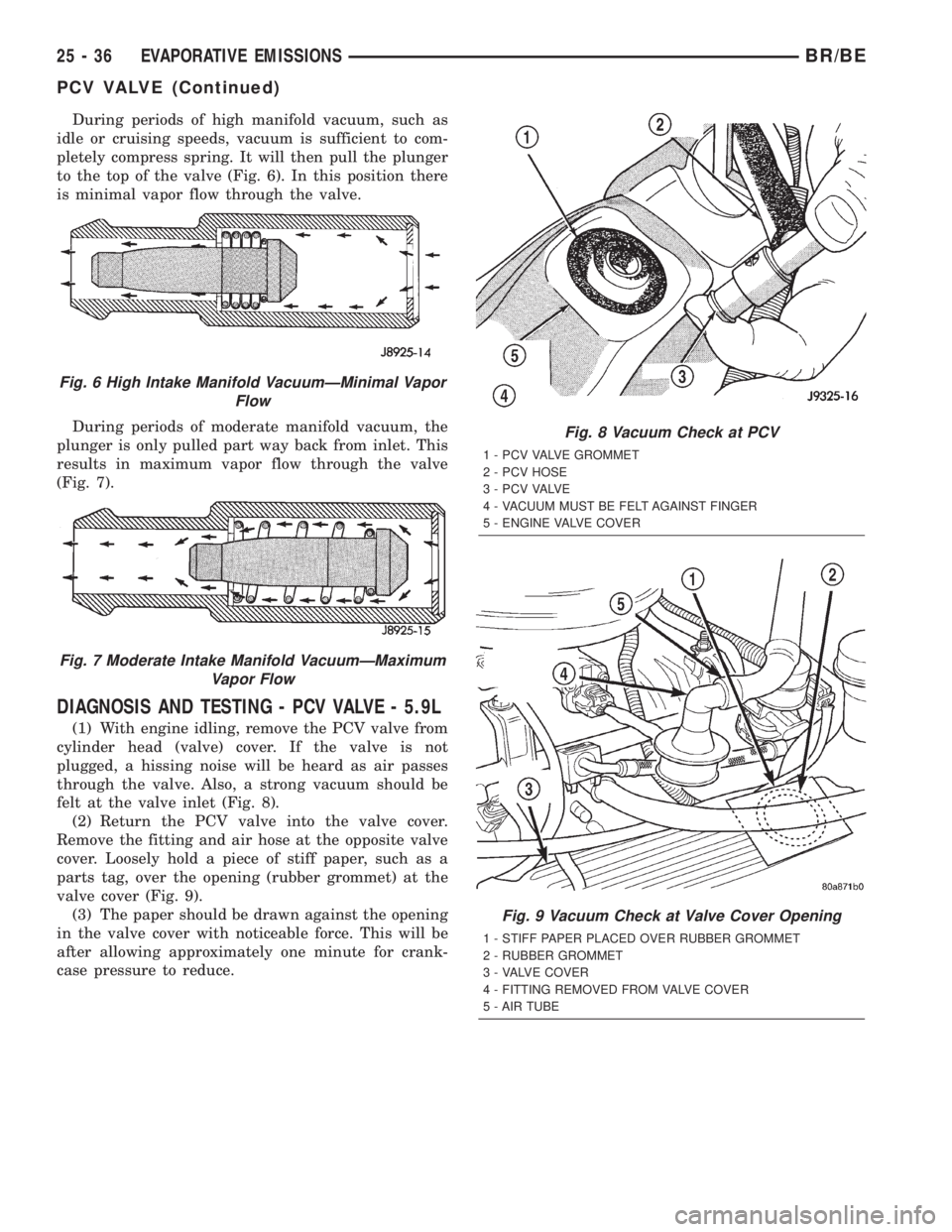
During periods of high manifold vacuum, such as
idle or cruising speeds, vacuum is sufficient to com-
pletely compress spring. It will then pull the plunger
to the top of the valve (Fig. 6). In this position there
is minimal vapor flow through the valve.
During periods of moderate manifold vacuum, the
plunger is only pulled part way back from inlet. This
results in maximum vapor flow through the valve
(Fig. 7).
DIAGNOSIS AND TESTING - PCV VALVE - 5.9L
(1) With engine idling, remove the PCV valve from
cylinder head (valve) cover. If the valve is not
plugged, a hissing noise will be heard as air passes
through the valve. Also, a strong vacuum should be
felt at the valve inlet (Fig. 8).
(2) Return the PCV valve into the valve cover.
Remove the fitting and air hose at the opposite valve
cover. Loosely hold a piece of stiff paper, such as a
parts tag, over the opening (rubber grommet) at the
valve cover (Fig. 9).
(3) The paper should be drawn against the opening
in the valve cover with noticeable force. This will be
after allowing approximately one minute for crank-
case pressure to reduce.
Fig. 6 High Intake Manifold VacuumÐMinimal Vapor
Flow
Fig. 7 Moderate Intake Manifold VacuumÐMaximum
Vapor Flow
Fig. 8 Vacuum Check at PCV
1 - PCV VALVE GROMMET
2 - PCV HOSE
3 - P C V VA LV E
4 - VACUUM MUST BE FELT AGAINST FINGER
5 - ENGINE VALVE COVER
Fig. 9 Vacuum Check at Valve Cover Opening
1 - STIFF PAPER PLACED OVER RUBBER GROMMET
2 - RUBBER GROMMET
3 - VALVE COVER
4 - FITTING REMOVED FROM VALVE COVER
5 - AIR TUBE
25 - 36 EVAPORATIVE EMISSIONSBR/BE
PCV VALVE (Continued)
Page 2216 of 2255
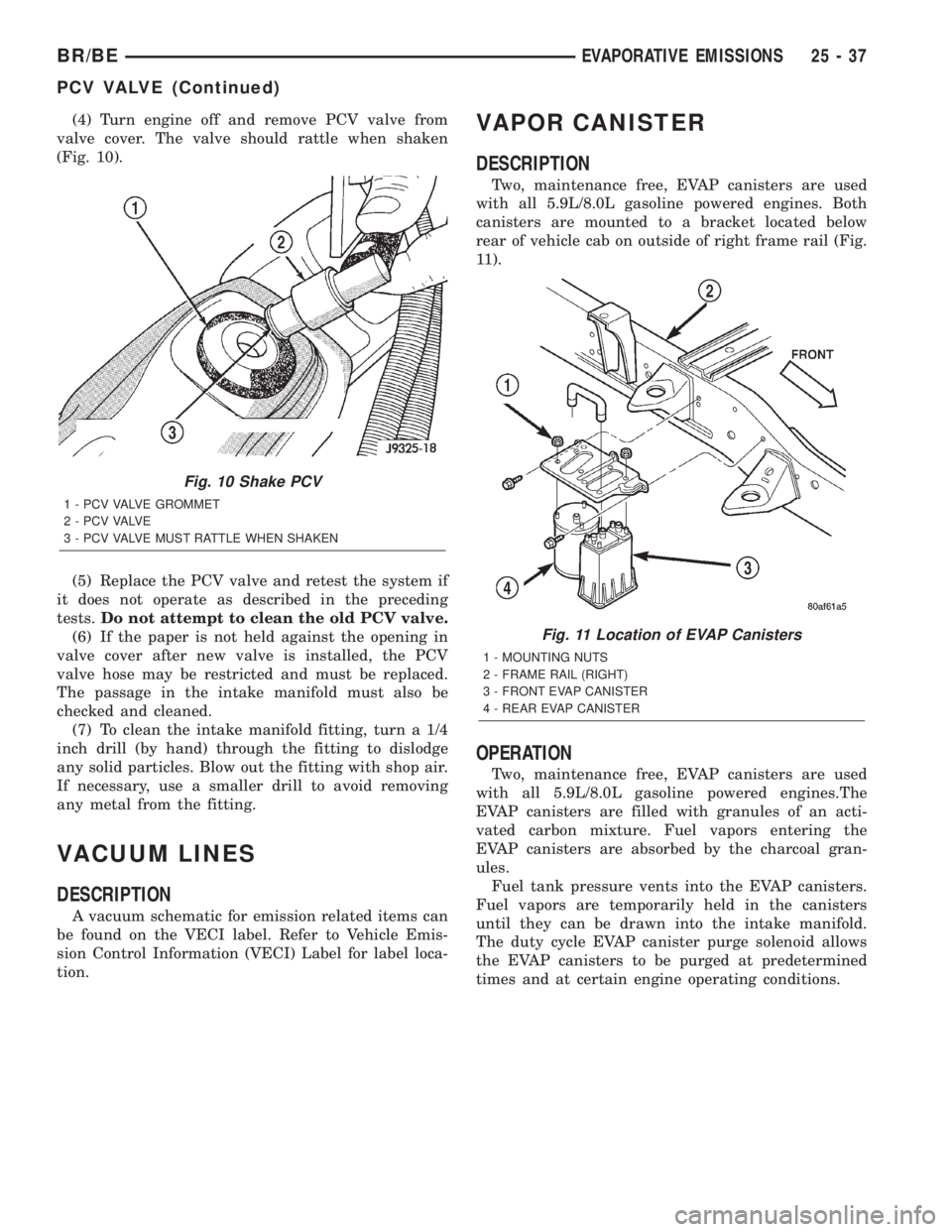
(4) Turn engine off and remove PCV valve from
valve cover. The valve should rattle when shaken
(Fig. 10).
(5) Replace the PCV valve and retest the system if
it does not operate as described in the preceding
tests.Do not attempt to clean the old PCV valve.
(6) If the paper is not held against the opening in
valve cover after new valve is installed, the PCV
valve hose may be restricted and must be replaced.
The passage in the intake manifold must also be
checked and cleaned.
(7) To clean the intake manifold fitting, turn a 1/4
inch drill (by hand) through the fitting to dislodge
any solid particles. Blow out the fitting with shop air.
If necessary, use a smaller drill to avoid removing
any metal from the fitting.
VACUUM LINES
DESCRIPTION
A vacuum schematic for emission related items can
be found on the VECI label. Refer to Vehicle Emis-
sion Control Information (VECI) Label for label loca-
tion.
VAPOR CANISTER
DESCRIPTION
Two, maintenance free, EVAP canisters are used
with all 5.9L/8.0L gasoline powered engines. Both
canisters are mounted to a bracket located below
rear of vehicle cab on outside of right frame rail (Fig.
11).
OPERATION
Two, maintenance free, EVAP canisters are used
with all 5.9L/8.0L gasoline powered engines.The
EVAP canisters are filled with granules of an acti-
vated carbon mixture. Fuel vapors entering the
EVAP canisters are absorbed by the charcoal gran-
ules.
Fuel tank pressure vents into the EVAP canisters.
Fuel vapors are temporarily held in the canisters
until they can be drawn into the intake manifold.
The duty cycle EVAP canister purge solenoid allows
the EVAP canisters to be purged at predetermined
times and at certain engine operating conditions.
Fig. 10 Shake PCV
1 - PCV VALVE GROMMET
2 - P C V VA LV E
3 - PCV VALVE MUST RATTLE WHEN SHAKEN
Fig. 11 Location of EVAP Canisters
1 - MOUNTING NUTS
2 - FRAME RAIL (RIGHT)
3 - FRONT EVAP CANISTER
4 - REAR EVAP CANISTER
BR/BEEVAPORATIVE EMISSIONS 25 - 37
PCV VALVE (Continued)