Page 1369 of 2255
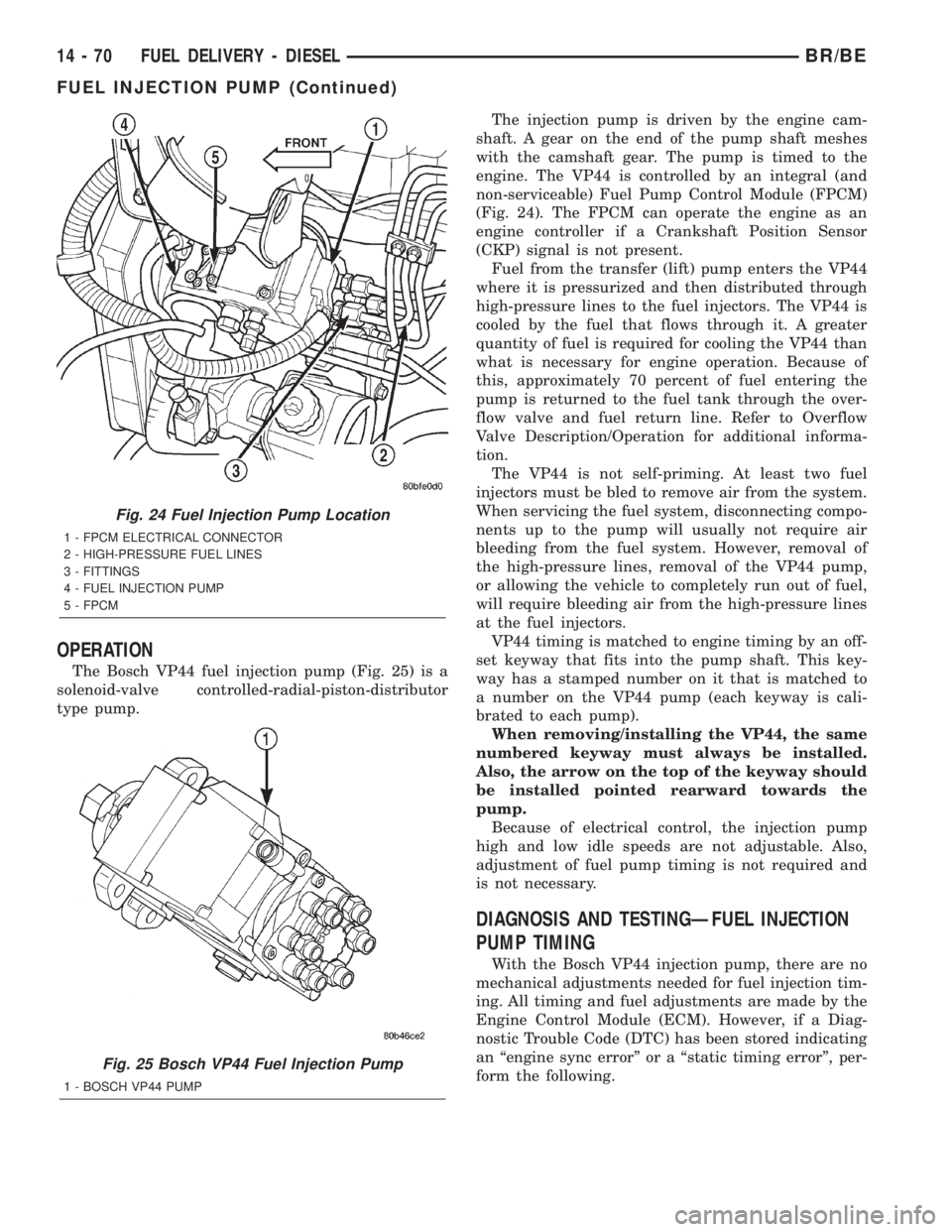
OPERATION
The Bosch VP44 fuel injection pump (Fig. 25) is a
solenoid-valve controlled-radial-piston-distributor
type pump.The injection pump is driven by the engine cam-
shaft. A gear on the end of the pump shaft meshes
with the camshaft gear. The pump is timed to the
engine. The VP44 is controlled by an integral (and
non-serviceable) Fuel Pump Control Module (FPCM)
(Fig. 24). The FPCM can operate the engine as an
engine controller if a Crankshaft Position Sensor
(CKP) signal is not present.
Fuel from the transfer (lift) pump enters the VP44
where it is pressurized and then distributed through
high-pressure lines to the fuel injectors. The VP44 is
cooled by the fuel that flows through it. A greater
quantity of fuel is required for cooling the VP44 than
what is necessary for engine operation. Because of
this, approximately 70 percent of fuel entering the
pump is returned to the fuel tank through the over-
flow valve and fuel return line. Refer to Overflow
Valve Description/Operation for additional informa-
tion.
The VP44 is not self-priming. At least two fuel
injectors must be bled to remove air from the system.
When servicing the fuel system, disconnecting compo-
nents up to the pump will usually not require air
bleeding from the fuel system. However, removal of
the high-pressure lines, removal of the VP44 pump,
or allowing the vehicle to completely run out of fuel,
will require bleeding air from the high-pressure lines
at the fuel injectors.
VP44 timing is matched to engine timing by an off-
set keyway that fits into the pump shaft. This key-
way has a stamped number on it that is matched to
a number on the VP44 pump (each keyway is cali-
brated to each pump).
When removing/installing the VP44, the same
numbered keyway must always be installed.
Also, the arrow on the top of the keyway should
be installed pointed rearward towards the
pump.
Because of electrical control, the injection pump
high and low idle speeds are not adjustable. Also,
adjustment of fuel pump timing is not required and
is not necessary.
DIAGNOSIS AND TESTINGÐFUEL INJECTION
PUMP TIMING
With the Bosch VP44 injection pump, there are no
mechanical adjustments needed for fuel injection tim-
ing. All timing and fuel adjustments are made by the
Engine Control Module (ECM). However, if a Diag-
nostic Trouble Code (DTC) has been stored indicating
an ªengine sync errorº or a ªstatic timing errorº, per-
form the following.
Fig. 24 Fuel Injection Pump Location
1 - FPCM ELECTRICAL CONNECTOR
2 - HIGH-PRESSURE FUEL LINES
3 - FITTINGS
4 - FUEL INJECTION PUMP
5 - FPCM
Fig. 25 Bosch VP44 Fuel Injection Pump
1 - BOSCH VP44 PUMP
14 - 70 FUEL DELIVERY - DIESELBR/BE
FUEL INJECTION PUMP (Continued)
Page 1370 of 2255
Note: If this DTC appears after installation of
a new or rebuilt injection pump, the pump key-
way has probably been installed backwards.
Refer to Fuel Injection Pump Removal/Installa-
tion for keyway information.
Fig. 26 Crankcase Vent Hose
1 - HOSE CLAMP
2 - CRANKCASE VENT HOSE
3 - CRANKCASE BREATHER
Fig. 27 Injection Pump Gear Nut/Washer
1 - WASHER
2 - PUMP NUT
3 - ACCESS CAP
Fig. 28 Pump Keyway, Keyway Arrow and Keyway
Number
1 - INJECTION PUMP
2 - DIRECTIONAL ARROW
3 - 3±DIGIT KEYWAY NUMBER
4 - O-RING
Fig. 29 Pump Data Plate Location
1 - PUMP DATA PLATE
BR/BEFUEL DELIVERY - DIESEL 14 - 71
FUEL INJECTION PUMP (Continued)
Page 1371 of 2255
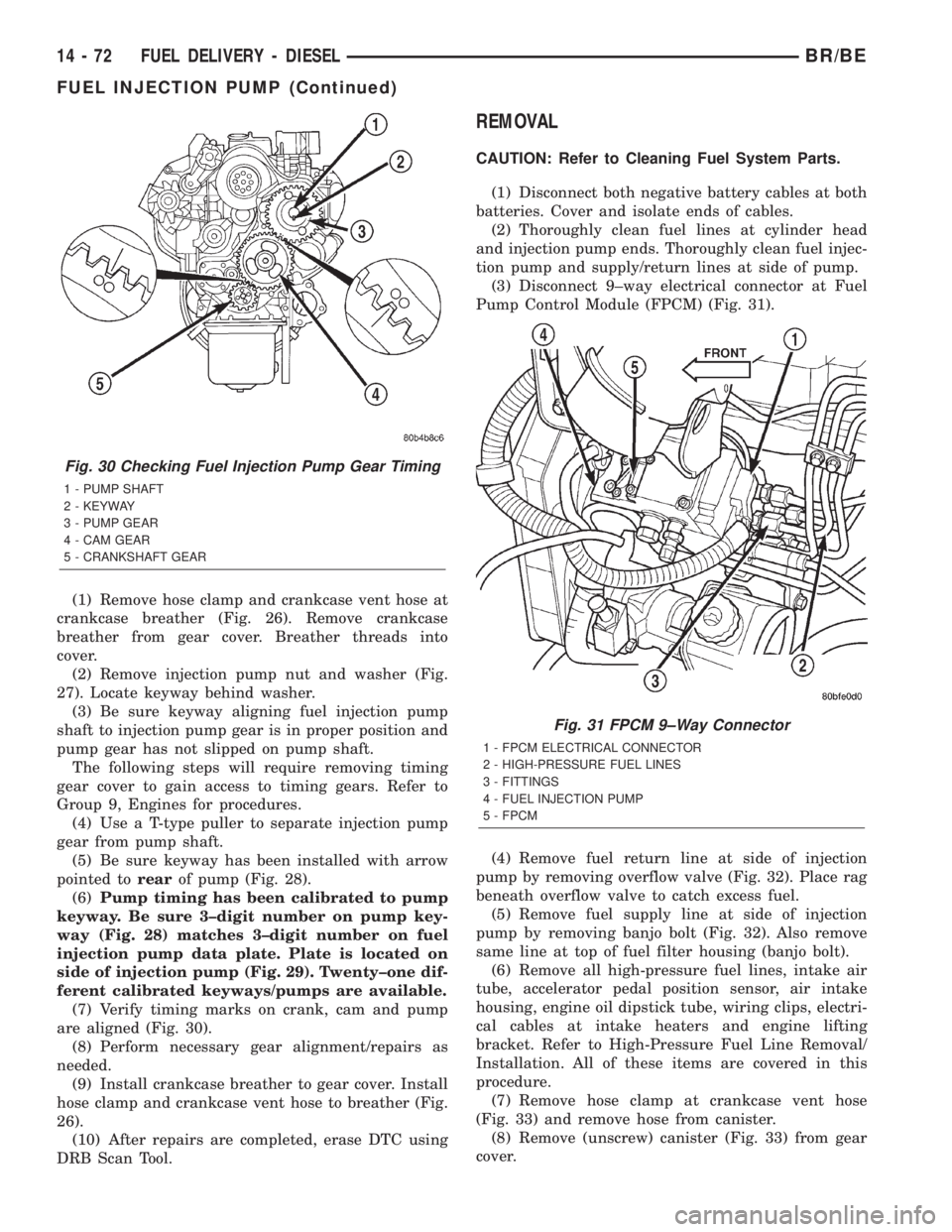
(1) Remove hose clamp and crankcase vent hose at
crankcase breather (Fig. 26). Remove crankcase
breather from gear cover. Breather threads into
cover.
(2) Remove injection pump nut and washer (Fig.
27). Locate keyway behind washer.
(3) Be sure keyway aligning fuel injection pump
shaft to injection pump gear is in proper position and
pump gear has not slipped on pump shaft.
The following steps will require removing timing
gear cover to gain access to timing gears. Refer to
Group 9, Engines for procedures.
(4) Use a T-type puller to separate injection pump
gear from pump shaft.
(5) Be sure keyway has been installed with arrow
pointed torearof pump (Fig. 28).
(6)Pump timing has been calibrated to pump
keyway. Be sure 3±digit number on pump key-
way (Fig. 28) matches 3±digit number on fuel
injection pump data plate. Plate is located on
side of injection pump (Fig. 29). Twenty±one dif-
ferent calibrated keyways/pumps are available.
(7) Verify timing marks on crank, cam and pump
are aligned (Fig. 30).
(8) Perform necessary gear alignment/repairs as
needed.
(9) Install crankcase breather to gear cover. Install
hose clamp and crankcase vent hose to breather (Fig.
26).
(10) After repairs are completed, erase DTC using
DRB Scan Tool.
REMOVAL
CAUTION: Refer to Cleaning Fuel System Parts.
(1) Disconnect both negative battery cables at both
batteries. Cover and isolate ends of cables.
(2) Thoroughly clean fuel lines at cylinder head
and injection pump ends. Thoroughly clean fuel injec-
tion pump and supply/return lines at side of pump.
(3) Disconnect 9±way electrical connector at Fuel
Pump Control Module (FPCM) (Fig. 31).
(4) Remove fuel return line at side of injection
pump by removing overflow valve (Fig. 32). Place rag
beneath overflow valve to catch excess fuel.
(5) Remove fuel supply line at side of injection
pump by removing banjo bolt (Fig. 32). Also remove
same line at top of fuel filter housing (banjo bolt).
(6) Remove all high-pressure fuel lines, intake air
tube, accelerator pedal position sensor, air intake
housing, engine oil dipstick tube, wiring clips, electri-
cal cables at intake heaters and engine lifting
bracket. Refer to High-Pressure Fuel Line Removal/
Installation. All of these items are covered in this
procedure.
(7) Remove hose clamp at crankcase vent hose
(Fig. 33) and remove hose from canister.
(8) Remove (unscrew) canister (Fig. 33) from gear
cover.
Fig. 30 Checking Fuel Injection Pump Gear Timing
1 - PUMP SHAFT
2 - KEYWAY
3 - PUMP GEAR
4 - CAM GEAR
5 - CRANKSHAFT GEAR
Fig. 31 FPCM 9±Way Connector
1 - FPCM ELECTRICAL CONNECTOR
2 - HIGH-PRESSURE FUEL LINES
3 - FITTINGS
4 - FUEL INJECTION PUMP
5 - FPCM
14 - 72 FUEL DELIVERY - DIESELBR/BE
FUEL INJECTION PUMP (Continued)
Page 1372 of 2255
CAUTION: To prevent pump/gear keyway from fall-
ing into gear housing, engine must be rotated until
keyway is at 12 o'clock position (Fig. 36). If gear
retainer nut, washer or key drops into gear housing,
cover may have to be removed to retrieve them
before engine is started.
(9) Remove nut and washer retaining injection
pump gear to injection pump shaft (Fig. 34).
Fig. 32 Fuel Supply and Return Lines at Pump
1 - FUEL SUPPLY LINE
2 - FUEL RETURN LINE
3 - BANJO BOLT (TEST PORT FITTING)
4 - OVERFLOW VALVE
5 - BANJO FITTING
Fig. 33 Crankcase Vent Hose
1 - HOSE CLAMP
2 - CRANKCASE VENT HOSE
3 - CRANKCASE BREATHER
Fig. 34 Pump Shaft Nut/Washer
1 - WASHER
2 - PUMP NUT
3 - GEAR COVER
Fig. 35 Rotating Engine with Barring Tool
1 - REAR FLANGE
2 - BARRING TOOL
BR/BEFUEL DELIVERY - DIESEL 14 - 73
FUEL INJECTION PUMP (Continued)
Page 1373 of 2255
(10) The engine can be rotated with a barring tool
such as Snap-On No. SP371, MTE No. 3377371
(Cummins Tool Division), or an equivalent. The open-
ing for barring tool is located in rear flange of engine
on exhaust manifold side (Fig. 35). Remove rubber
access plug covering this opening.
(11) Insert barring tool into flywheel housing open-
ing (Fig. 35).(12) Rotate engine until keyway is at 12 o'clock
position (Fig. 36).
Fig. 36 Placing Keyway at 12 O'clock Position
1 - KEYWAY AT 12 O'CLOCK POSITION
2 - PUMP GEAR
Fig. 37 Separating Injection Pump Gear from Pump
Shaft
1 - T-BAR PULLER
Fig. 38 Rear/Lower Pump Bracket and Mounting
Bolts
1 - FUEL INJECTION PUMP
2 - BOLTS (2)
3 - REAR/LOWER BRACKET
Fig. 39 Injection Pump Mounting Nuts
1 - PUMP MOUNTING NUTS (4)
14 - 74 FUEL DELIVERY - DIESELBR/BE
FUEL INJECTION PUMP (Continued)
Page 1374 of 2255
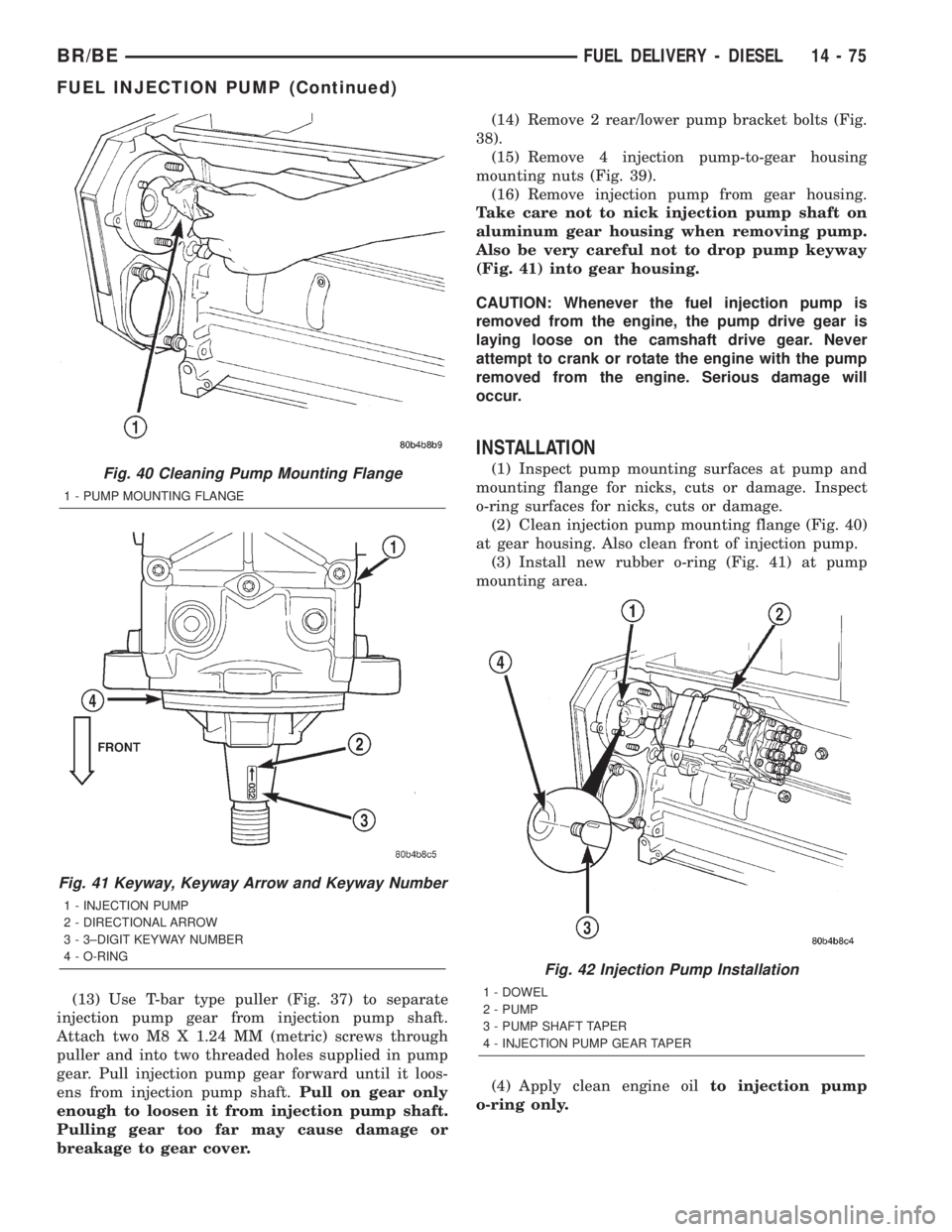
(13) Use T-bar type puller (Fig. 37) to separate
injection pump gear from injection pump shaft.
Attach two M8 X 1.24 MM (metric) screws through
puller and into two threaded holes supplied in pump
gear. Pull injection pump gear forward until it loos-
ens from injection pump shaft.Pull on gear only
enough to loosen it from injection pump shaft.
Pulling gear too far may cause damage or
breakage to gear cover.(14) Remove 2 rear/lower pump bracket bolts (Fig.
38).
(15) Remove 4 injection pump-to-gear housing
mounting nuts (Fig. 39).
(16) Remove injection pump from gear housing.
Take care not to nick injection pump shaft on
aluminum gear housing when removing pump.
Also be very careful not to drop pump keyway
(Fig. 41) into gear housing.
CAUTION: Whenever the fuel injection pump is
removed from the engine, the pump drive gear is
laying loose on the camshaft drive gear. Never
attempt to crank or rotate the engine with the pump
removed from the engine. Serious damage will
occur.
INSTALLATION
(1) Inspect pump mounting surfaces at pump and
mounting flange for nicks, cuts or damage. Inspect
o-ring surfaces for nicks, cuts or damage.
(2) Clean injection pump mounting flange (Fig. 40)
at gear housing. Also clean front of injection pump.
(3) Install new rubber o-ring (Fig. 41) at pump
mounting area.
(4) Apply clean engine oilto injection pump
o-ring only.Fig. 40 Cleaning Pump Mounting Flange
1 - PUMP MOUNTING FLANGE
Fig. 41 Keyway, Keyway Arrow and Keyway Number
1 - INJECTION PUMP
2 - DIRECTIONAL ARROW
3 - 3±DIGIT KEYWAY NUMBER
4 - O-RING
Fig. 42 Injection Pump Installation
1 - DOWEL
2 - PUMP
3 - PUMP SHAFT TAPER
4 - INJECTION PUMP GEAR TAPER
BR/BEFUEL DELIVERY - DIESEL 14 - 75
FUEL INJECTION PUMP (Continued)
Page 1375 of 2255
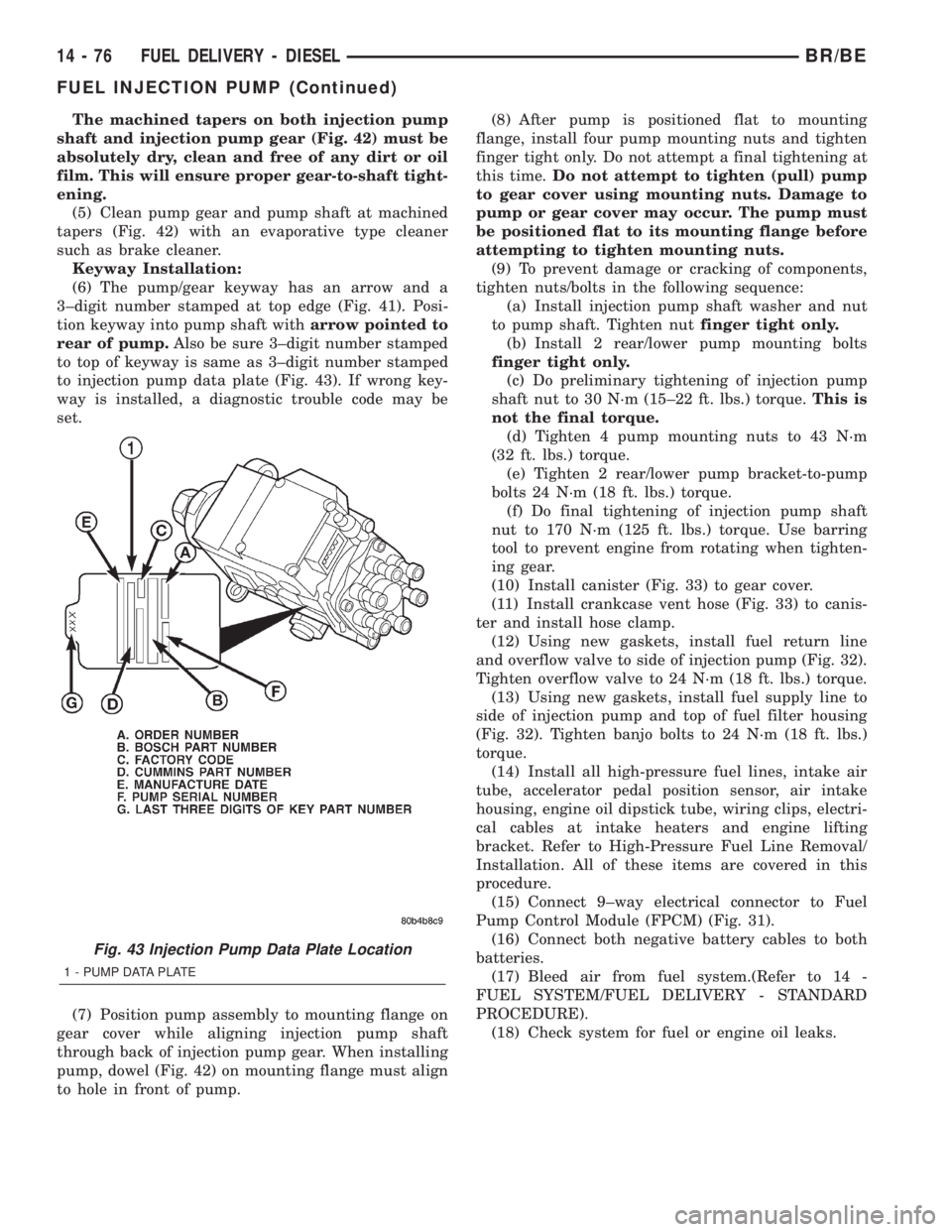
The machined tapers on both injection pump
shaft and injection pump gear (Fig. 42) must be
absolutely dry, clean and free of any dirt or oil
film. This will ensure proper gear-to-shaft tight-
ening.
(5) Clean pump gear and pump shaft at machined
tapers (Fig. 42) with an evaporative type cleaner
such as brake cleaner.
Keyway Installation:
(6) The pump/gear keyway has an arrow and a
3±digit number stamped at top edge (Fig. 41). Posi-
tion keyway into pump shaft witharrow pointed to
rear of pump.Also be sure 3±digit number stamped
to top of keyway is same as 3±digit number stamped
to injection pump data plate (Fig. 43). If wrong key-
way is installed, a diagnostic trouble code may be
set.
(7) Position pump assembly to mounting flange on
gear cover while aligning injection pump shaft
through back of injection pump gear. When installing
pump, dowel (Fig. 42) on mounting flange must align
to hole in front of pump.(8) After pump is positioned flat to mounting
flange, install four pump mounting nuts and tighten
finger tight only. Do not attempt a final tightening at
this time.Do not attempt to tighten (pull) pump
to gear cover using mounting nuts. Damage to
pump or gear cover may occur. The pump must
be positioned flat to its mounting flange before
attempting to tighten mounting nuts.
(9) To prevent damage or cracking of components,
tighten nuts/bolts in the following sequence:
(a) Install injection pump shaft washer and nut
to pump shaft. Tighten nutfinger tight only.
(b) Install 2 rear/lower pump mounting bolts
finger tight only.
(c) Do preliminary tightening of injection pump
shaft nut to 30 N´m (15±22 ft. lbs.) torque.This is
not the final torque.
(d) Tighten 4 pump mounting nuts to 43 N´m
(32 ft. lbs.) torque.
(e) Tighten 2 rear/lower pump bracket-to-pump
bolts 24 N´m (18 ft. lbs.) torque.
(f) Do final tightening of injection pump shaft
nut to 170 N´m (125 ft. lbs.) torque. Use barring
tool to prevent engine from rotating when tighten-
ing gear.
(10) Install canister (Fig. 33) to gear cover.
(11) Install crankcase vent hose (Fig. 33) to canis-
ter and install hose clamp.
(12) Using new gaskets, install fuel return line
and overflow valve to side of injection pump (Fig. 32).
Tighten overflow valve to 24 N´m (18 ft. lbs.) torque.
(13) Using new gaskets, install fuel supply line to
side of injection pump and top of fuel filter housing
(Fig. 32). Tighten banjo bolts to 24 N´m (18 ft. lbs.)
torque.
(14) Install all high-pressure fuel lines, intake air
tube, accelerator pedal position sensor, air intake
housing, engine oil dipstick tube, wiring clips, electri-
cal cables at intake heaters and engine lifting
bracket. Refer to High-Pressure Fuel Line Removal/
Installation. All of these items are covered in this
procedure.
(15) Connect 9±way electrical connector to Fuel
Pump Control Module (FPCM) (Fig. 31).
(16) Connect both negative battery cables to both
batteries.
(17) Bleed air from fuel system.(Refer to 14 -
FUEL SYSTEM/FUEL DELIVERY - STANDARD
PROCEDURE).
(18) Check system for fuel or engine oil leaks.
Fig. 43 Injection Pump Data Plate Location
1 - PUMP DATA PLATE
14 - 76 FUEL DELIVERY - DIESELBR/BE
FUEL INJECTION PUMP (Continued)
Page 1376 of 2255
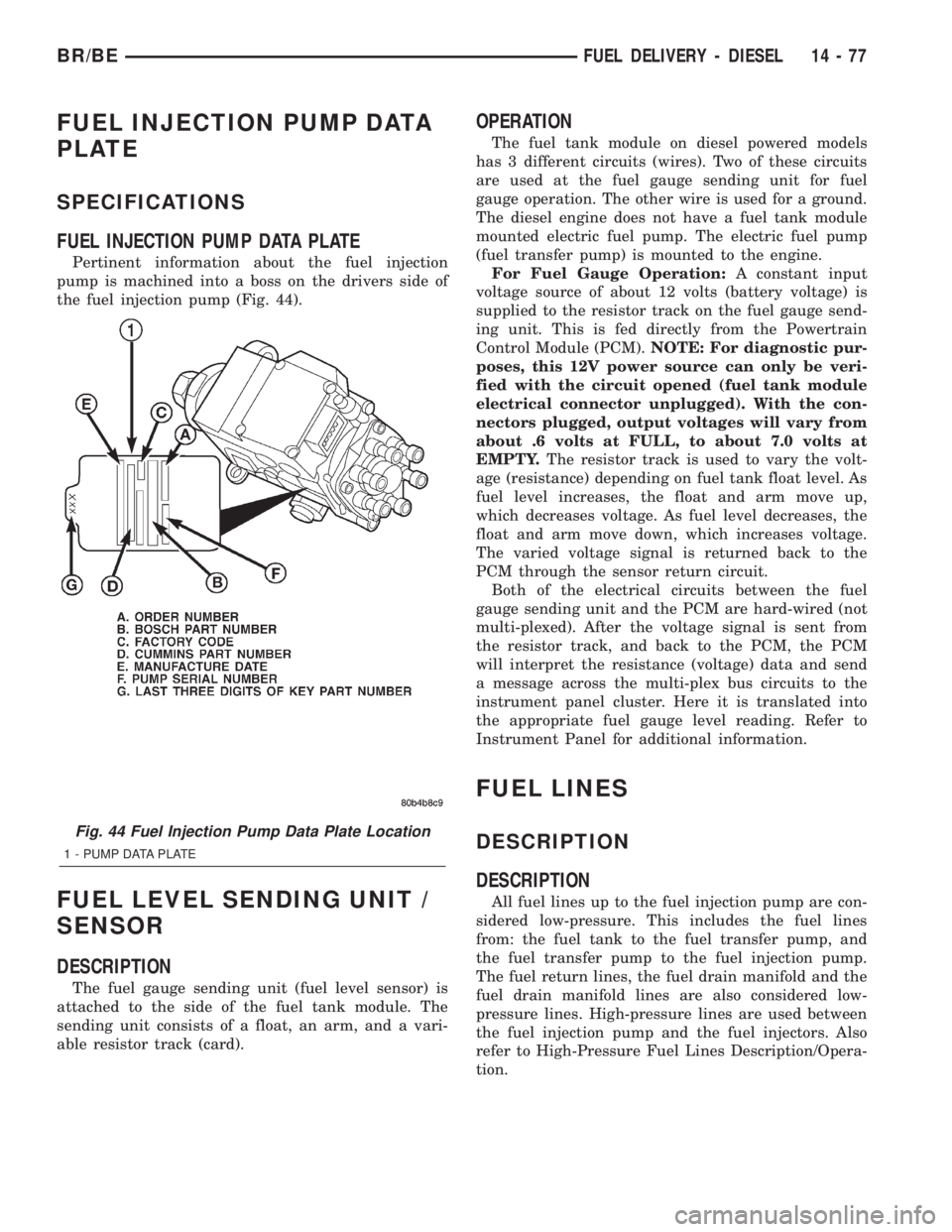
FUEL INJECTION PUMP DATA
PLATE
SPECIFICATIONS
FUEL INJECTION PUMP DATA PLATE
Pertinent information about the fuel injection
pump is machined into a boss on the drivers side of
the fuel injection pump (Fig. 44).
FUEL LEVEL SENDING UNIT /
SENSOR
DESCRIPTION
The fuel gauge sending unit (fuel level sensor) is
attached to the side of the fuel tank module. The
sending unit consists of a float, an arm, and a vari-
able resistor track (card).
OPERATION
The fuel tank module on diesel powered models
has 3 different circuits (wires). Two of these circuits
are used at the fuel gauge sending unit for fuel
gauge operation. The other wire is used for a ground.
The diesel engine does not have a fuel tank module
mounted electric fuel pump. The electric fuel pump
(fuel transfer pump) is mounted to the engine.
For Fuel Gauge Operation:A constant input
voltage source of about 12 volts (battery voltage) is
supplied to the resistor track on the fuel gauge send-
ing unit. This is fed directly from the Powertrain
Control Module (PCM).NOTE: For diagnostic pur-
poses, this 12V power source can only be veri-
fied with the circuit opened (fuel tank module
electrical connector unplugged). With the con-
nectors plugged, output voltages will vary from
about .6 volts at FULL, to about 7.0 volts at
EMPTY.The resistor track is used to vary the volt-
age (resistance) depending on fuel tank float level. As
fuel level increases, the float and arm move up,
which decreases voltage. As fuel level decreases, the
float and arm move down, which increases voltage.
The varied voltage signal is returned back to the
PCM through the sensor return circuit.
Both of the electrical circuits between the fuel
gauge sending unit and the PCM are hard-wired (not
multi-plexed). After the voltage signal is sent from
the resistor track, and back to the PCM, the PCM
will interpret the resistance (voltage) data and send
a message across the multi-plex bus circuits to the
instrument panel cluster. Here it is translated into
the appropriate fuel gauge level reading. Refer to
Instrument Panel for additional information.
FUEL LINES
DESCRIPTION
DESCRIPTION
All fuel lines up to the fuel injection pump are con-
sidered low-pressure. This includes the fuel lines
from: the fuel tank to the fuel transfer pump, and
the fuel transfer pump to the fuel injection pump.
The fuel return lines, the fuel drain manifold and the
fuel drain manifold lines are also considered low-
pressure lines. High-pressure lines are used between
the fuel injection pump and the fuel injectors. Also
refer to High-Pressure Fuel Lines Description/Opera-
tion.
Fig. 44 Fuel Injection Pump Data Plate Location
1 - PUMP DATA PLATE
BR/BEFUEL DELIVERY - DIESEL 14 - 77