Page 257 of 1865
DISASSEMBLY (CYLINDER BLOCK) 1 C
CYLINDER BLOCK—II
76G01C-093
1. Connecting rod cap
2. Connecting rod bearing
3. Connecting rod and piston
4. Piston ring
5. Snap ring
6. Piston pin
7. Main bearing cap
8. Crankshaft
9. Main bearing
10. Pilot bearing
11. Oil jet
12. Cylinder block
Disassembly Note
Connecting rod and cap
During disassembly, clean the bearing, connecting
rod, and crankpin, and measure the following:
1. Connecting rod side clearance. (Refer to page
1C-67.)
2. Crankpin oil clearance.(Refer to page 1C—66.)
76G01C-094
1C-45
Page 258 of 1865
1 C DISASSEMBLY (CYLINDER BLOCK)
Piston and connecting rod
1. Before disassembling the piston and connecting
rod, check the oscillation torque as shown in the
figure. If the large end does not drop by its own
weight, replace the piston or the piston pin.
76G01C-095
2. Remove the snap rings from the piston.
3. Remove the piston pin with the SST.
76G01C-249
76G01C-096
Main bearing cap
During disassembly, clean the bearings, main jour-
nals, and caps, and measure the following:
1. Crankshaft end play. (Refer to page 1C—65.)
2. Main journal oil clearance. (Refer to page 1C—64.)
Pilot bearing
Remove the pilot bearing from the crankshaft with the
SST.
76G01C-097
1C—46
Page 259 of 1865
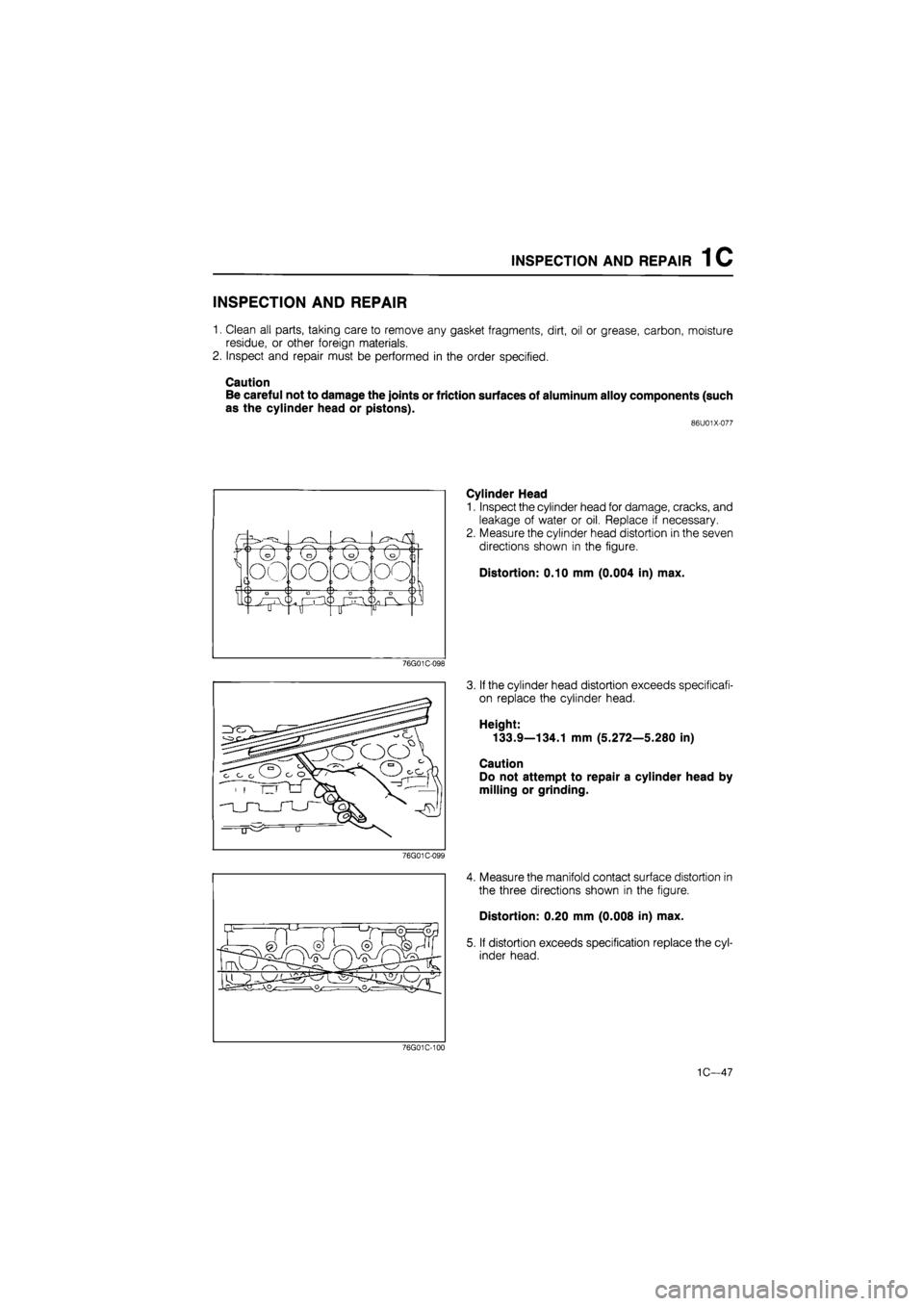
INSPECTION AND REPAIR 1C
INSPECTION AND REPAIR
1. Clean all parts, taking care to remove any gasket fragments, dirt, oil or grease, carbon, moisture
residue, or other foreign materials.
2. Inspect and repair must be performed in the order specified.
Caution
Be careful not to damage the joints or friction surfaces of aluminum alloy components (such
as the cylinder head or pistons).
86U01X-077
Cylinder Head
1. Inspect the cylinder head for damage, cracks, and
leakage of water or oil. Replace if necessary.
2. Measure the cylinder head distortion in the seven
directions shown in the figure.
Distortion: 0.10 mm (0.004 in) max.
76G01C-098
3. If the cylinder head distortion exceeds specificati-
on replace the cylinder head.
Height:
133.9—134.1 mm (5.272—5.280 in)
Caution
Do not attempt to repair a cylinder head by
milling or grinding.
76G01C-099
4. Measure the manifold contact surface distortion in
the three directions shown in the figure.
Distortion: 0.20 mm (0.008 in) max.
5. If distortion exceeds specification replace the cyl-
inder head.
76G01C-100
1C—47
Page 260 of 1865
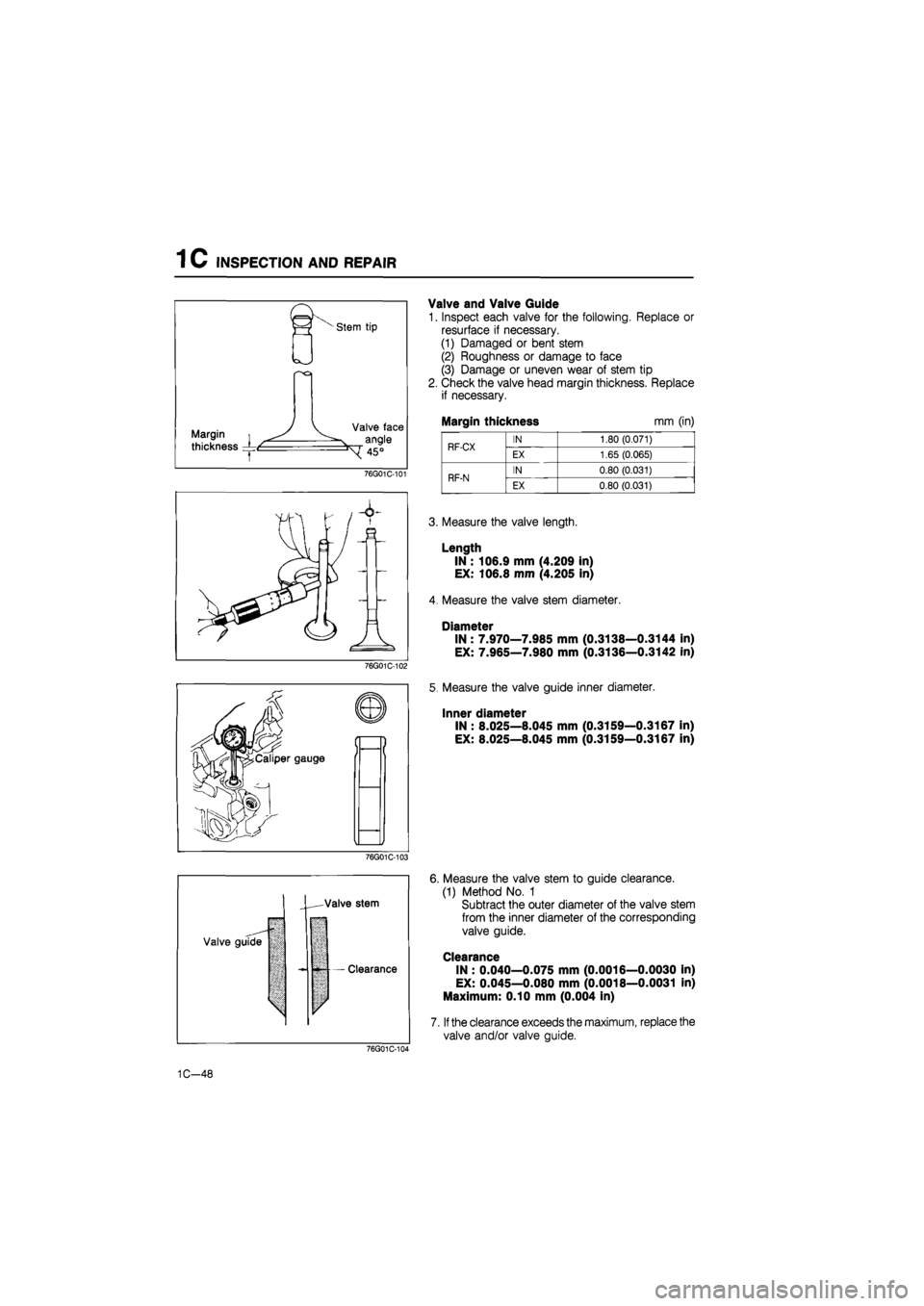
1C INSPECTION AND REPAIR
Stem tip
Margin i
thickness
T
Valve face
angle
^45°
76G01C-101
76G01C-102
" & ©
JMFc
•^Caliper gauge
^V^r "M
m
Valve and Valve Guide
1. Inspect each valve for the following. Replace or
resurface if necessary.
(1) Damaged or bent stem
(2) Roughness or damage to face
(3) Damage or uneven wear of stem tip
2. Check the valve head margin thickness. Replace
if necessary.
Margin thickness mm (in)
RF-CX IN 1.80 (0.071) RF-CX EX 1.65 (0.065)
RF-N IN 0.80 (0.031) RF-N EX 0.80 (0.031)
3. Measure the valve length.
Length
IN : 106.9 mm (4.209 in)
EX: 106.8 mm (4.205 in)
4. Measure the valve stem diameter.
Diameter
IN : 7.970—7.985 mm (0.3138—0.3144 in)
EX: 7.965—7.980 mm (0.3136—0.3142 in)
5. Measure the valve guide inner diameter.
Inner diameter
IN : 8.025—8.045 mm (0.3159—0.3167 in)
EX: 8.025—8.045 mm (0.3159—0.3167 in)
76G01C-103
-Valve stem
Valve guide
Clearance
V
6. Measure the valve stem to guide clearance.
(1) Method No. 1
Subtract the outer diameter of the valve stem
from the inner diameter of the corresponding
valve guide.
Clearance
IN : 0.040—0.075 mm (0.0016—0.0030 in)
EX: 0.045—0.080 mm (0.0018—0.0031 in)
Maximum: 0.10 mm (0.004 in)
7.
If
the clearance exceeds the maximum, replace the
valve and/or valve guide.
76G01C-111
1C-48
Page 261 of 1865
1C INSPECTION AND REPAIR
76G01C-105
Replacement of valve guide
Caution
When the valve guide is replaced, check the
gap between the valve and guide once again.
The valve seal should be installed after in-
spection and repair of the valve seat.
Don't misassemble the valve guides because
intake and exhaust valve guides have a differ-
ent seat.
Intake side valve guide longer
Exhaust side valve guide shorter
Removal
1. Gradually heat the cylinder head in water to ap-
prox. 90°C (194°F).
76G01C-106
2. Remove the valve guide from the side opposite the
combustion chamber with the SST.
86U01X-084
Installation
1. Gradually heat the cylinder head in water to ap-
prox. 90°C (194°F).
76G01C-111
1C-49
Page 262 of 1865
1C INSPECTION AND REPAIR
76G01C-103
76G01C-104
76G01C-110
2. Fit the clip onto the valve guide.
3. Tap the valve guide in from the side opposite the
combustion chamber with the SST until the clip
contacts the cylinder head.
4. Check the guide protrusion height (dimension A
in the figure) is as specified.
Height:
8.3—8.8 mm (0.327—0.346 in)
Valve Seat
1. Inspect the contact surface of the valve seat and
valve face for the following.
(1) Roughness
(2) Damage
2. If necessary, resurface the valve seat to the speci-
fied angle with valve seat cutter and/or resurface
the valve face.
Angle
RF-CX IN 60° RF-CX EX 45°
RF-N IN 45° RF-N EX 45°
3. Apply a thin coat of prussian blue to the valve face.
4. Check the valve seating by pressing the valve
against the seat.
(1) If blue does not appear 360° around the valve
face, replace the valve.
(2) If blue does not appear 360° around the valve
seat, resurface the seat.
76G01C-111
1C-50
Page 263 of 1865
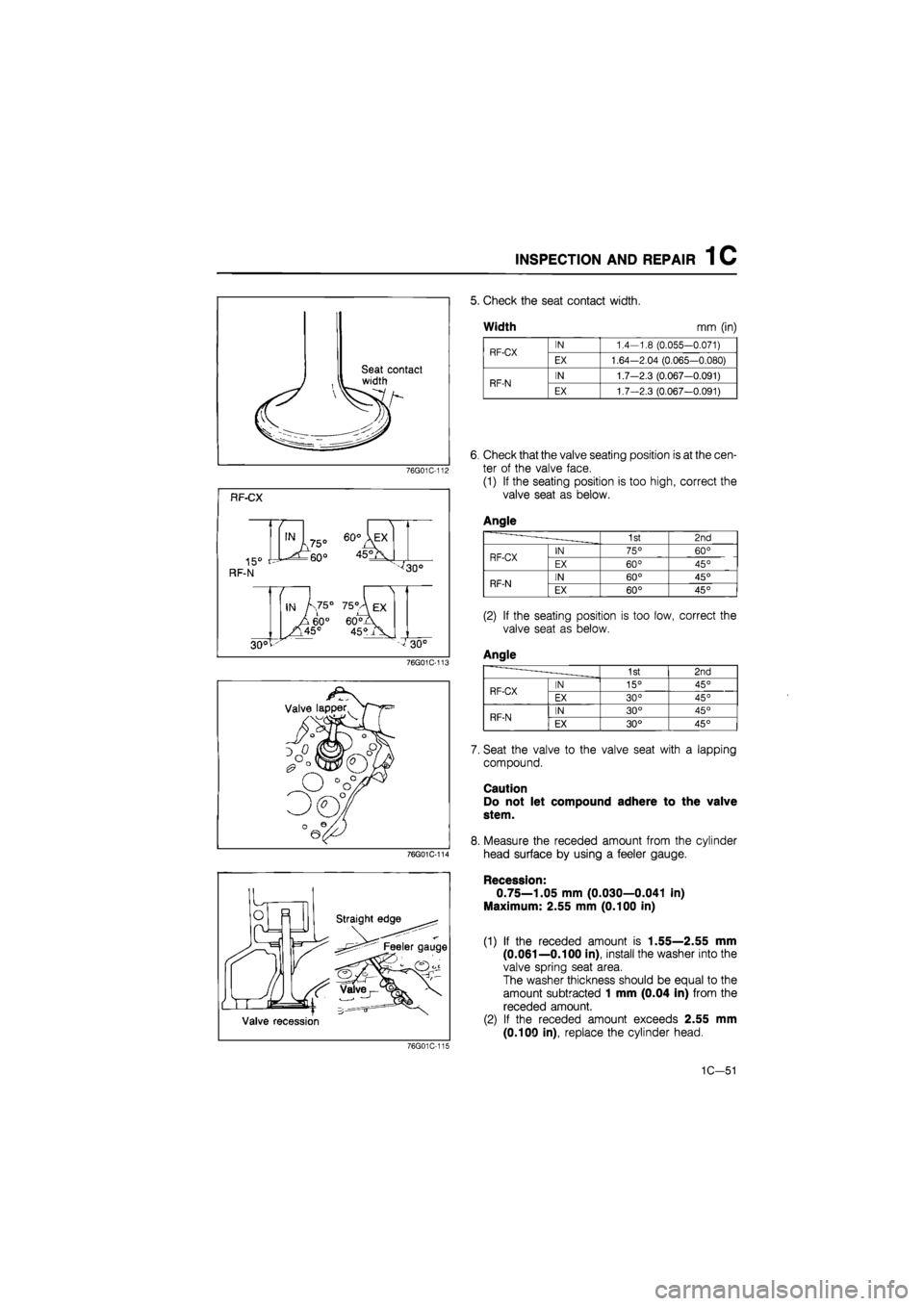
INSPECTION AND REPAIR 1C
76G01C-112
76G01C-113
76G01C-114
5. Check the seat contact width.
Width mm (in)
RF-CX IN 1.4-1.8 (0.055-0.071) RF-CX EX 1.64-2.04 (0.065-0.080)
RF-N IN 1.7—2.3 (0.067-0.091) RF-N EX 1.7—2.3 (0.067—0.091)
6, Check that the valve seating position is at the cen-
ter of the valve face.
(1) If the seating position is too high, correct the
valve seat as below.
Angle
- - • -1st 2nd
RF-CX IN 75° 60° RF-CX EX 60° 45°
RF-N IN 60° 45° RF-N EX 60° 45°
(2) If the seating position is too low, correct the
valve seat as below.
Angle
1st 2nd
RF-CX IN 15° 45° RF-CX EX 30° 45°
RF-N IN 30° 45° RF-N EX 30° 45°
7. Seat the valve to the valve seat with a lapping
compound.
Caution
Do not let compound adhere to the valve
stem.
8. Measure the receded amount from the cylinder
head surface by using a feeler gauge.
Recession-
0.75—1.05 mm (0.030—0.041 in)
Maximum: 2.55 mm (0.100 in)
(1) If the receded amount is 1.55—2.55 mm
(0.061—0.100 in), install the washer into the
valve spring seat area.
The washer thickness should be equal to the
amount subtracted 1 mm (0.04 in) from the
receded amount.
(2) If the receded amount exceeds 2.55 mm
(0.100 in), replace the cylinder head.
76G01C-144
1C-51
Page 264 of 1865
INSPECTION AND REPAIR 1C
76G01C-116
76G01C-117
—Angle limit
S//////A 777;////////
Combustion Chamber Insert
1. Inspect the combustion chamber insert for damage
or crack, replace if necessary.
2. Mesure the receded or projected amount of com-
bustion chamber insert from cylinder head surface.
Recession: 0.020 mm (0.0008 in) max.
Projection: 0.005 mm (0.0001 in) max.
If it exceeds the specification, replace the combus-
tion chamber insert and the cylinder head as an as-
sembly.
Valve Spring
1. Inspect each valve spring for cracks or damage.
2. Check the free length and angle. Replace if
necessary.
Free length: 45.11 mm (1.776 in)
Minimum: 44.8 mm (1.764 in)
Angle: 1.6 mm (0.06 in) max.
76G01C-118
Tappet
1. Check the tappet to tappet hole clearance.
(1) Measure the tappet outer diameter.
Diameter:
34.95—34.97 mm (1.3764—1.3768 in)
76G01C-144
1C-52