Page 841 of 1865
ASSEMBLY 7A
8. Measure the clearance between the 1st gear and
differential drive gear.
Clearance: 0.05—0.28 mm (0.0020—0.0110 in)
Maximum: 0.33 mm (0.0199 in)
86U07A-081
9. Measure the clearance between the 2nd gear and
secondary 3rd gear.
Clearance:
0.175—0.455 mm (0.0069—0.0179 in)
Maximum: 0.505 mm (0.0199 in)
86U07A-082
7A-35
Page 842 of 1865
7A ASSEMBLY
STEP 3
Torque specifications
7A—36
Page 843 of 1865
ASSEMBLY 7 A
Bearing Preload
Adjust the bearing preload through the use of adjust shim(s).
83U07A-099
49 G030 381
Outer race
Differential
Outer races
Secondary shaft
assembly
49 G030 382A
Transaxle case
Outer rases
Primary shaft assembly
Outer rase
49 F401 382A
Clutch housing
83U07A-033
7A-37
Page 844 of 1865
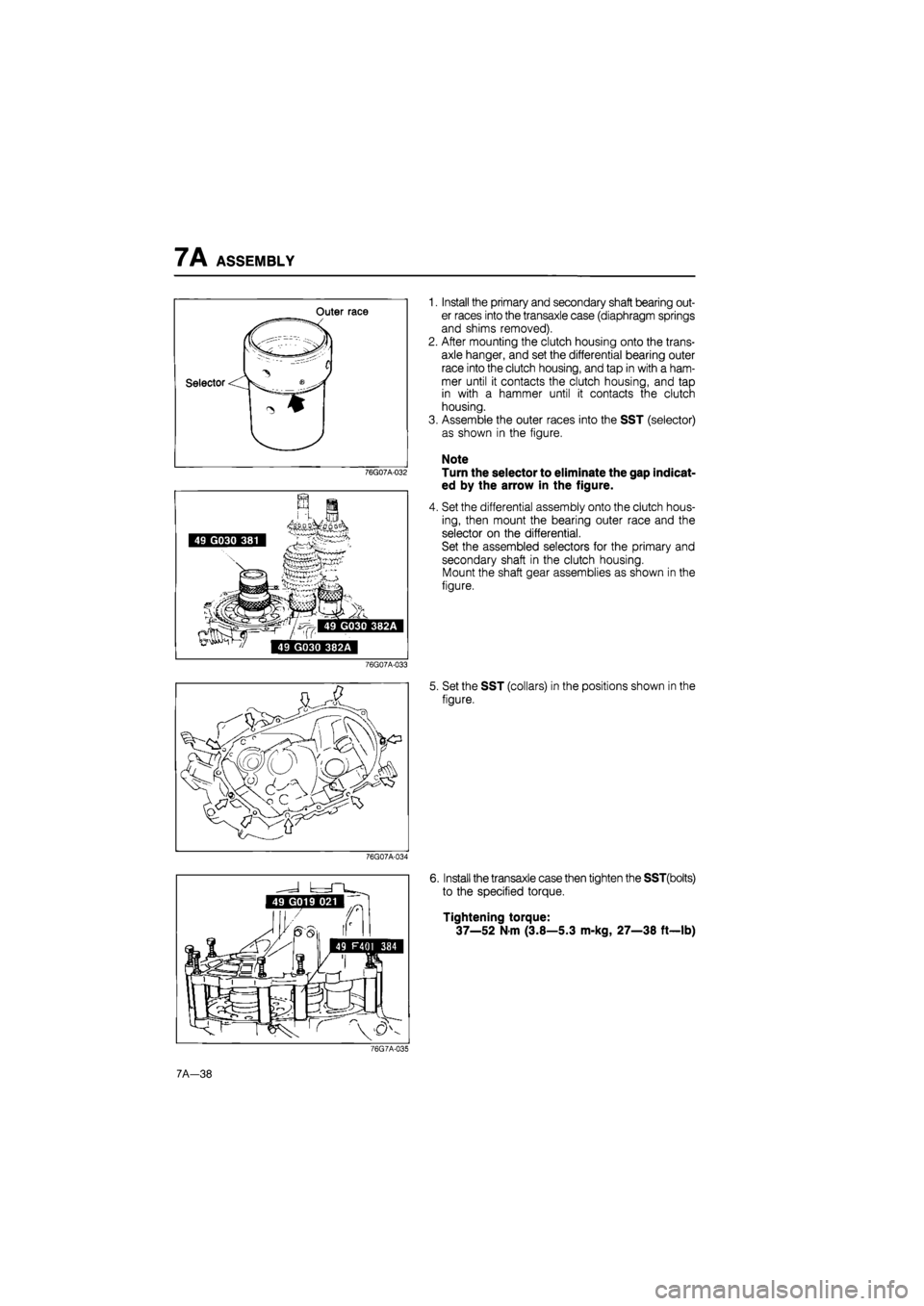
7 A ASSEMBLY
Outer race
Selector
76G07A-032
i "k
49 G030 381
49 G030 382A
49 G030 382A
76G07A-033
1. Install the primary and secondary shaft bearing out-
er races into the transaxle case (diaphragm springs
and shims removed).
2. After mounting the clutch housing onto the trans-
axle hanger, and set the differential bearing outer
race into the clutch housing, and tap in with a ham-
mer until it contacts the clutch housing, and tap
in with a hammer until it contacts the clutch
housing.
3. Assemble the outer races into the SST (selector)
as shown in the figure.
Note
Turn the selector to eliminate the gap indicat-
ed by the arrow in the figure.
4. Set the differential assembly onto the clutch hous-
ing, then mount the bearing outer race and the
selector on the differential.
Set the assembled selectors for the primary and
secondary shaft in the clutch housing.
Mount the shaft gear assemblies as shown in the
figure.
5. Set the SST (collars) in the positions shown in the
figure.
76G07A-034
6. Install the transaxle case then tighten the SST(bolts)
to the specified torque.
Tightening torque:
37—52
N
m (3.8—5.3 m-kg, 27—38 ft—lb)
76G7A-035
7A-38
Page 845 of 1865
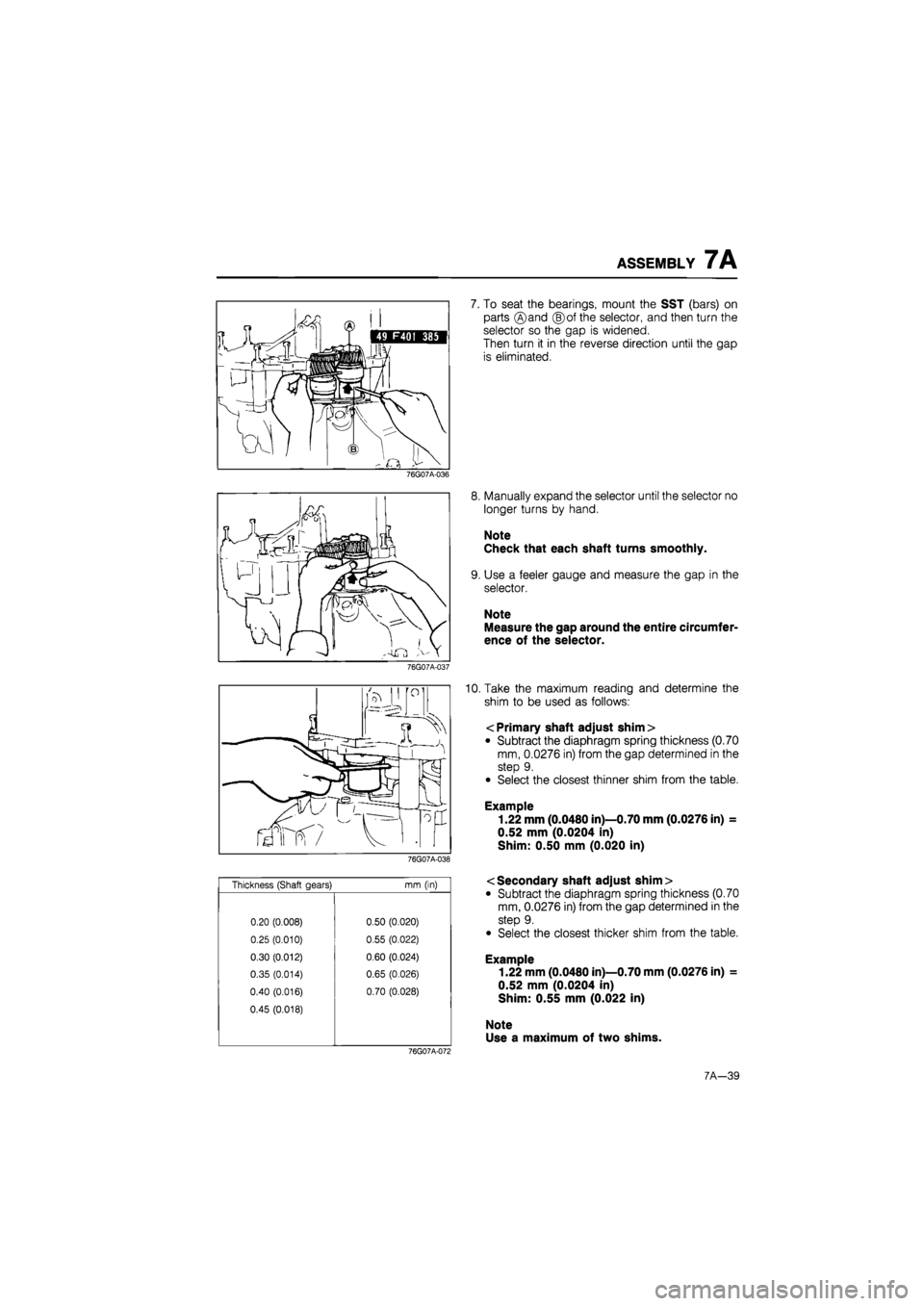
ASSEMBLY 7A
Thickness (Shaft gears) mm (in)
0.20 (0.008) 0.50 (0.020)
0.25 (0.010) 0.55 (0.022)
0.30 (0.012) 0.60 (0.024)
0.35 (0.014) 0.65 (0.026)
0.40 (0.016) 0.70 (0.028)
0.45 (0.018)
76G07A-072
To seat the bearings, mount the SST (bars) on
parts ©and (§)of the selector, and then turn the
selector so the gap is widened.
Then turn it in the reverse direction until the gap
is eliminated.
Manually expand the selector until the selector no
longer turns by hand.
Note
Check that each shaft turns smoothly.
Use a feeler gauge and measure the gap in the
selector.
Note
Measure the gap around the entire circumfer-
ence of the selector.
Take the maximum reading and determine the
shim to be used as follows:
< Primary shaft adjust shim >
• Subtract the diaphragm spring thickness (0.70
mm, 0.0276 in) from the gap determined in the
step 9.
• Select the closest thinner shim from the table.
Example
1.22 mm (0.0480 in)—0.70 mm (0.0276 in) =
0.52 mm (0.0204 in)
Shim: 0.50 mm (0.020 in)
< Secondary shaft adjust shim >
• Subtract the diaphragm spring thickness (0.70
mm, 0.0276 in) from the gap determined in the
step 9.
• Select the closest thicker shim from the table.
Example
1.22 mm (0.0480 in)—0.70 mm (0.0276 in) =
0.52 mm (0.0204 in)
Shim: 0.55 mm (0.022 in)
Note
Use a maximum of two shims.
7A—39
Page 846 of 1865
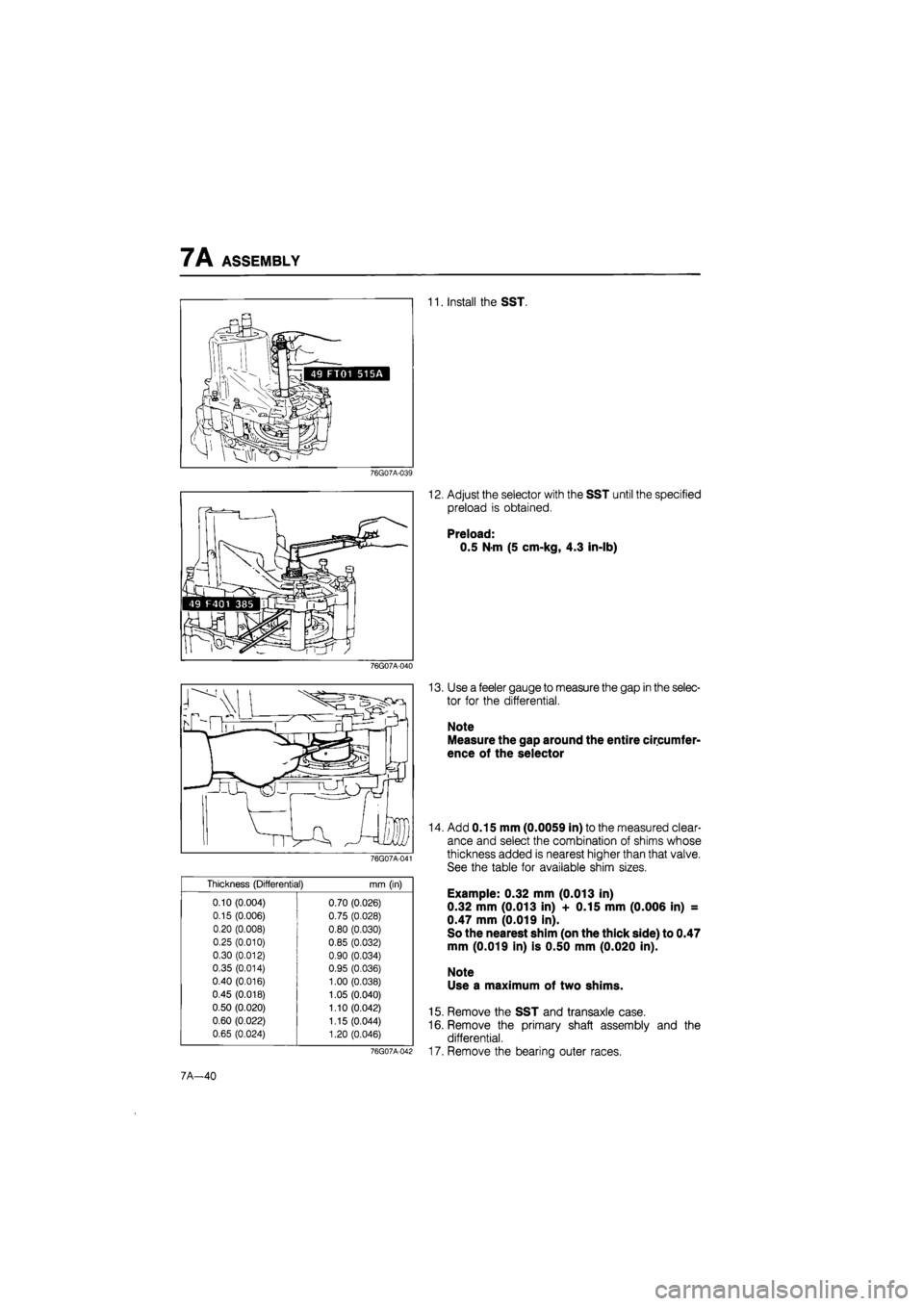
7A ASSEMBLY
11. Install the SST.
76G07A-039
76G07A-040
76G07A-041
Thickness (Differential)
mm
(in)
0.10 (0.004) 0.70 (0.026)
0.15 (0.006) 0.75 (0.028)
0.20 (0.008) 0.80 (0.030)
0.25 (0.010) 0.85 (0.032)
0.30 (0.012) 0.90 (0.034)
0.35 (0.014) 0.95 (0.036)
0.40 (0.016) 1.00 (0.038)
0.45 (0.018) 1.05 (0.040)
0.50 (0.020) 1.10 (0.042)
0.60 (0.022) 1.15 (0.044)
0.65 (0.024) 1.20 (0.046)
12. Adjust the selector with the SST until the specified
preload is obtained.
Preload:
0.5 N-m (5 cm-kg, 4.3 in-lb)
13. Use a feeler gauge to measure the gap in the selec-
tor for the differential.
Note
Measure the gap around the entire circumfer-
ence of the selector
76G07A-042
14. Add 0.15 mm (0.0059 in) to the measured clear-
ance and select the combination of shims whose
thickness added is nearest higher than that valve.
See the table for available shim sizes.
Example: 0.32 mm (0.013 in)
0.32 mm (0.013 in) + 0.15 mm (0.006 in) =
0.47 mm (0.019 in).
So the nearest shim (on the thick side) to 0.47
mm (0.019 in) is 0.50 mm (0.020 in).
Note
Use a maximum of two shims.
15. Remove the SST and transaxle case.
16. Remove the primary shaft assembly and the
differential.
17. Remove the bearing outer races.
7A—40
Page 847 of 1865
ASSEMBLY 7A
86U07A-102
86U07A-103
76G07A-043
Assembly
1. Install the neutral switch.
2. Install the drain plug.
3. Install the back-up lamp switch.
4. Install the new oil seals with the SST.
5. Install the differential adjust shim(s) and the bear-
ing outer race with a suitable pipe.
6. Install the adjust shims, diaphragm springs, fun-
nel, and bearing outer races.
Note
Install the diaphragm spring as shown in the
figure.
7. Install the bearing outer races with a suitable pipe.
86U07A-105
7A—41
Page 848 of 1865
7 A ASSEMBLY
86U07A-106
86U07A-107
86U07A-108
8. Install the new breather.
9. Install the new change rod oil seal.
10. Install the change rod ©, the boot the spring
(3),
the reverse gate @, and selector ©, as shown.
11. Install the new roll pin.
12. Install the change arm.
Tightening torque: 12—14 N-m
(120—140 cm-kg, 104—122 in-lb)
13. Install the guide plate.
Tightening torque:
©8—11 N-m
(80—115 cm-kg, 69—100 in-lb)
(1)22—33 N-m
(2.25—3.35 m-kg, 16—25 ft-lb)
14. Install reverse lever, and reverse lever shaft.
15. Install the new roll pin.
16. Install the speedometer driven gear assembly.
86U07A-109
7A-42