Page 89 of 1865
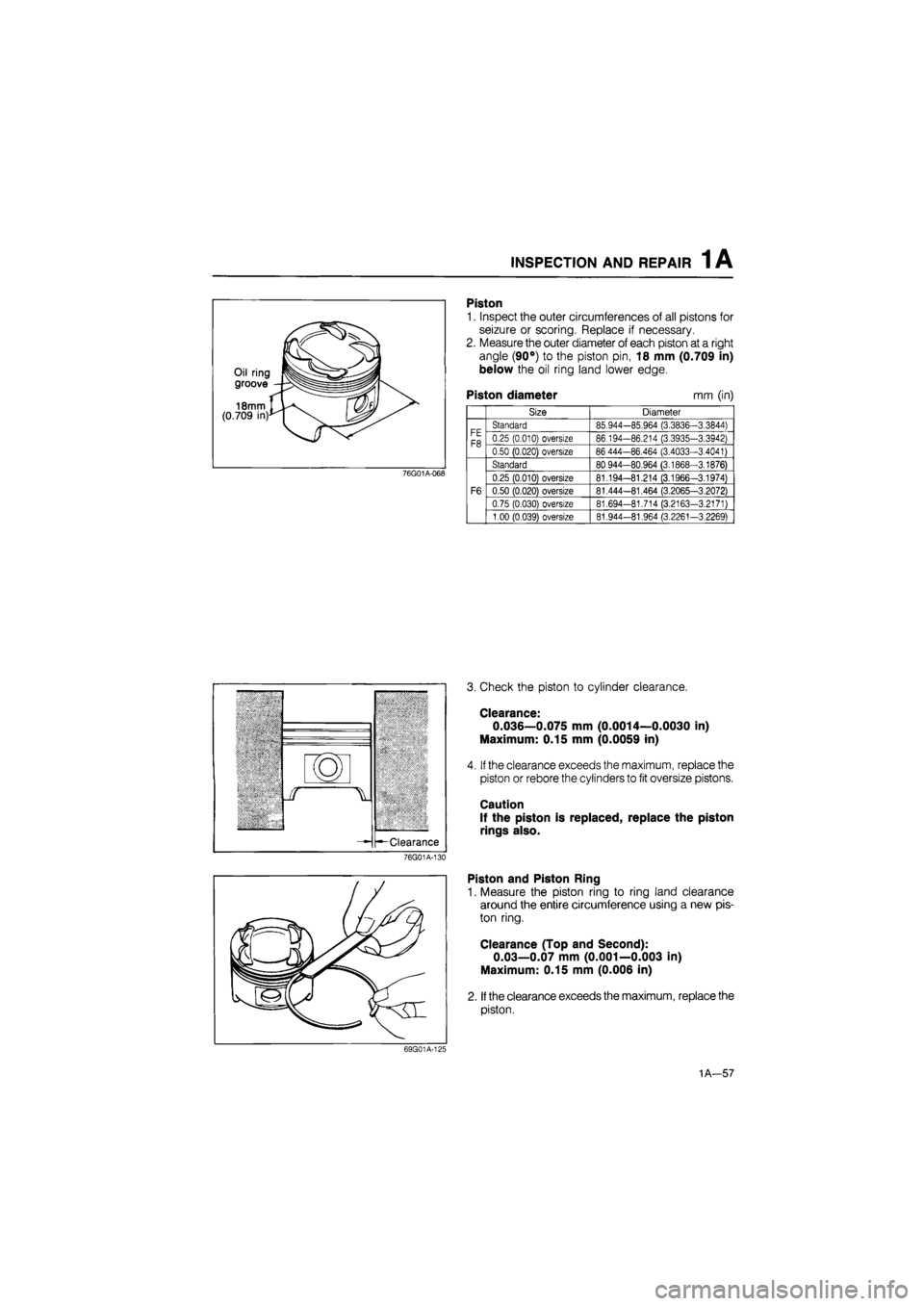
INSPECTION AND REPAIR 1A
76G01A-068
Piston
1. Inspect the outer circumferences of all pistons for
seizure or scoring. Replace if necessary.
2. Measure the outer diameter of each piston at a right
angle (90°) to the piston pin, 18 mm (0.709 in)
below the oil ring land lower edge.
Piston diameter mm (in)
Size Diameter
LU
OO LL LL Standard 85.944-85.964 (3.3836-3.3844)
LU
OO LL LL 0.25 (0.010) oversize 86.194-86.214 (3.3935-3.3942)
LU
OO LL LL
0.50 (0.020) oversize 86 444-86.464 (3.4033-3.4041)
F6
Standard 80 944-80.964 (3.1868-3.1876)
F6
0.25 (0.010) oversize 81.194-81.214 (3.1966-3.1974)
F6 0.50 (0.020) oversize 81.444-81.464 (3.2065-3.2072) F6
0.75 (0.030) oversize 81.694-81.714 (3.2163-3.2171)
F6
1.00 (0.039) oversize 81.944-81.964 (3.2261-3,2269)
3. Check the piston to cylinder clearance.
ClGdrsncG1
0.036—0.075 mm (0.0014—0.0030 in)
Maximum: 0.15 mm (0.0059 in)
4. If the clearance exceeds the maximum, replace the
piston or rebore the cylinders to fit oversize pistons.
Caution
If the piston is replaced, replace the piston
rings also.
76G01A-130
Piston and Piston Ring
1. Measure the piston ring to ring land clearance
around the entire circumference using a new pis-
ton ring.
Clearance (Top and Second):
0.03—0.07 mm (0.001—0.003 in)
Maximum: 0.15 mm (0.006 in)
2. If the clearance exceeds the maximum, replace the
piston.
69G01A-125
1A—57
Page 90 of 1865
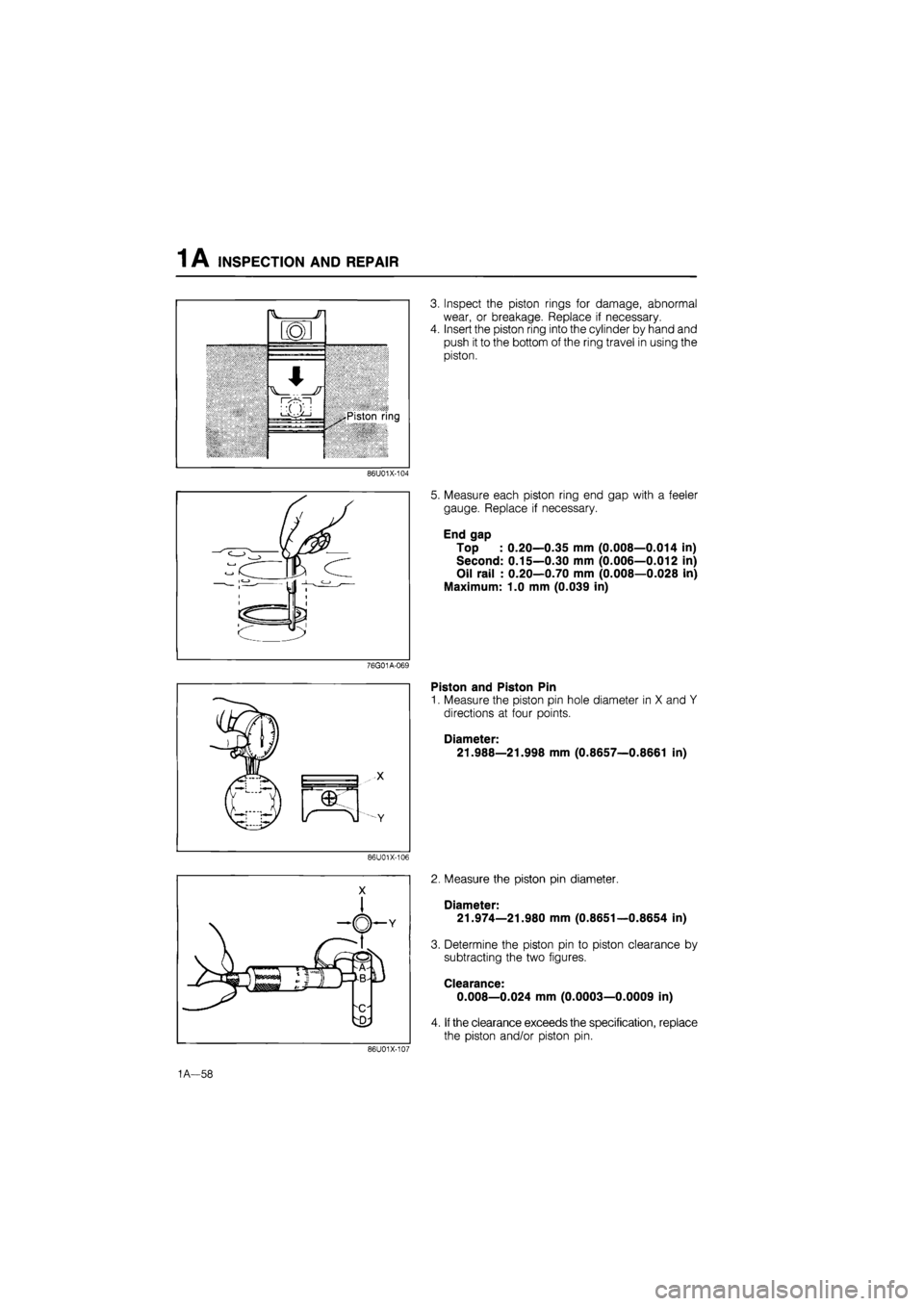
INSPECTION AND REPAIR 1 A
JT
I0J
'r-Sj&f-;:*::;^
.^Piston ring
'r-Sj&f-;:*::;^
.^Piston ring
'r-Sj&f-;:*::;^
.^Piston ring
86U01X-104
76G01A-069
86U01X-106
3. Inspect the piston rings for damage, abnormal
wear, or breakage. Replace if necessary.
4. Insert the piston ring into the cylinder by hand and
push it to the bottom of the ring travel in using the
piston.
5. Measure each piston ring end gap with a feeler
gauge. Replace if necessary.
End gap
Top : 0.20—0.35 mm (0.008—0.014 in)
Second: 0.15—0.30 mm (0.006—0.012 in)
Oil rail : 0.20—0.70 mm (0.008—0.028 in)
Maximum: 1.0 mm (0.039 in)
Piston and Piston Pin
1. Measure the piston pin hole diameter in X and Y
directions at four points.
Diameter:
21.988—21.998 mm (0.8657—0.8661 in)
2. Measure the piston pin diameter.
Diameter:
21.974—21.980 mm (0.8651—0.8654 in)
3. Determine the piston pin to piston clearance by
subtracting the two figures.
Clearance:
0.008—0.024 mm (0.0003—0.0009 in)
4. If the clearance exceeds the specification, replace
the piston and/or piston pin.
86U01X-117
1A—58
Page 91 of 1865
INSPECTION AND REPAIR 1 A
76G01A-070
76G01A-071
86U01X-109
Connecting Rod
1. Measure the connecting rod small end bore.
Diameter: 21.943—21.961 mm (0.8640—0.8646 in)
2. Check the interference between the small end bore
and piston pin.
Interference:
0.013—0.037 mm (0.0005—0.0015 in)
3. Check each connecting rod for bending or twist-
ing. Repair or replace if necessary.
Bend: 0.06 mm (0.0024 in) max.
Twist: 0.06 mm (0.0024 in) max.
Crankshaft
1. Check the journals and pins for damage, scoring,
or oil hole clogging.
2. Set the crankshaft on V-blocks.
3. Check the crankshaft runout at the center journal.
Replace if necessary.
Runout: 0.03 mm (0.0012 in) max.
4. Measure each journal diameter in X and Y direc-
tions at two points.
Main journal
Diameter:
59.937—59.955 mm (2.3597—2.3604 in)
Out-of-round: 0.05 mm (0.0020 in) max.
Crankpin journal
Diameter:
50.940—50.955 mm (2.0055—2.0061 in)
Out-of-round: 0.05 mm (0.0020 in) max.
76G01A-131
1A—59
Page 92 of 1865
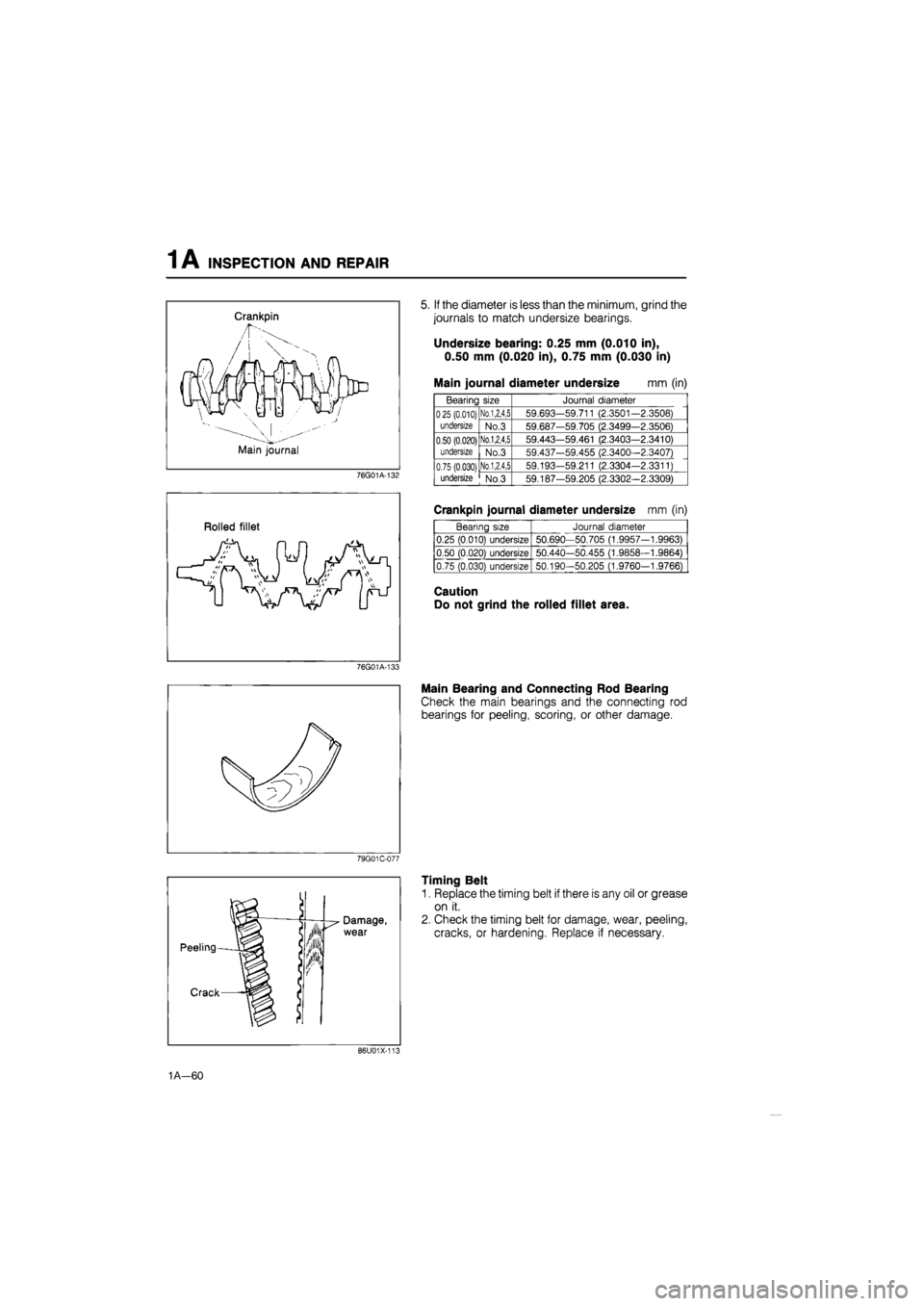
INSPECTION AND REPAIR 1 A
Crankpin
,/f
Main journal
76G01A-132
5. If the diameter is less than the minimum, grind the
journals to match undersize bearings.
Undersize bearing: 0.25 mm (0.010 in),
0.50 mm (0.020 in), 0.75 mm (0.030 in)
Main journal diameter undersize mm (in)
Bearing size Journal diameter
025 (0.010)
undersize
No.1,2,4,5 59.693-59.711 (2.3501-2.3508) 025 (0.010)
undersize No.3 59.687-59.705 (2.3499-2.3506)
0.50 (0.020)
undersize
No.1,2,4,5 59.443-59.461 (2.3403—2.3410) 0.50 (0.020)
undersize No.3 59.437-59.455 (2.3400—2.3407)
0.75 (0.030) undersize
No.1,2,4,5 59.193-59.211 (2.3304-2.3311) 0.75 (0.030) undersize No.3 59.187-59.205 (2.3302-2.3309)
Rolled fillet
Crankpin journal diameter undersize mm (in)
Bearing size Journal diameter
0.25 (0.010) undersize 50.690—50.705 (1.9957-1.9963)
0.50 (0.020) undersize 50.440-50.455 (1.9858—1.9864)
0.75 (0.030) undersize 50.190-50.205 (1.9760-1.9766)
Caution
Do not grind the rolled fillet area.
76G01A-133
Main Bearing and Connecting Rod Bearing
Check the main bearings and the connecting rod
bearings for peeling, scoring, or other damage.
79G01C-077
Timing Belt
1. Replace the timing belt if there is any oil or grease
on it.
2. Check the timing belt for damage, wear, peeling,
cracks, or hardening. Replace if necessary.
86U01X-117
1A—60
Page 93 of 1865
INSPECTION AND REPAIR 1 A
Caution
a) Never forcefully twist, turn inside out, or
bend the timing belt.
b) Be careful not to allow oil or grease on the
belt.
86U01X-114
Timing Belt Tensioner and Idler Pulley
Check the timing belt tensioner and idler pulley for
smooth rotation and abnormal- noise. Replace if
necessary.
Caution
Do not clean the tensioner with cleaning
fluids. If necessary, use a soft rag to wipe it
clean, and avoid scratching it.
86U01X-115
Timing Belt Tensioner Spring
Check the free length of the tensioner spring. Replace
if necessary.
Free length: 56.9 mm (2.240 in) FE
64.1 mm (2.524 in) F8, F6
76G01A-134
Timing Belt Pulley and Camshaft Pulley
Inspect the pulley teeth for wear, deformation, or other
damage. Replace if necessary.
Caution
Do not clean the pulley with cleaning fluids.
If necessary, use a rag to wipe it clean.
Timing Belt Cover (lower and upper)
Inspect the timing belt covers for damage or cracks.
Replace if necessary.
86U01X-117
1A—61
Page 94 of 1865
1 A ASSEMBLY (CYLINDER BLOCK)
ASSEMBLY
1. Clean all parts before reinstallation.
2. Apply new engine oil to all sliding and rotating parts.
3. Replace plain bearings if they are peeling, burned, or otherwise damaged.
4. Tighten all bolts and nuts to the specified torques.
Caution
Do not reuse gaskets or oil seals.
CYLINDER BLOCK—I
Torque Specifications
69G01A-139
1A—62
Page 95 of 1865
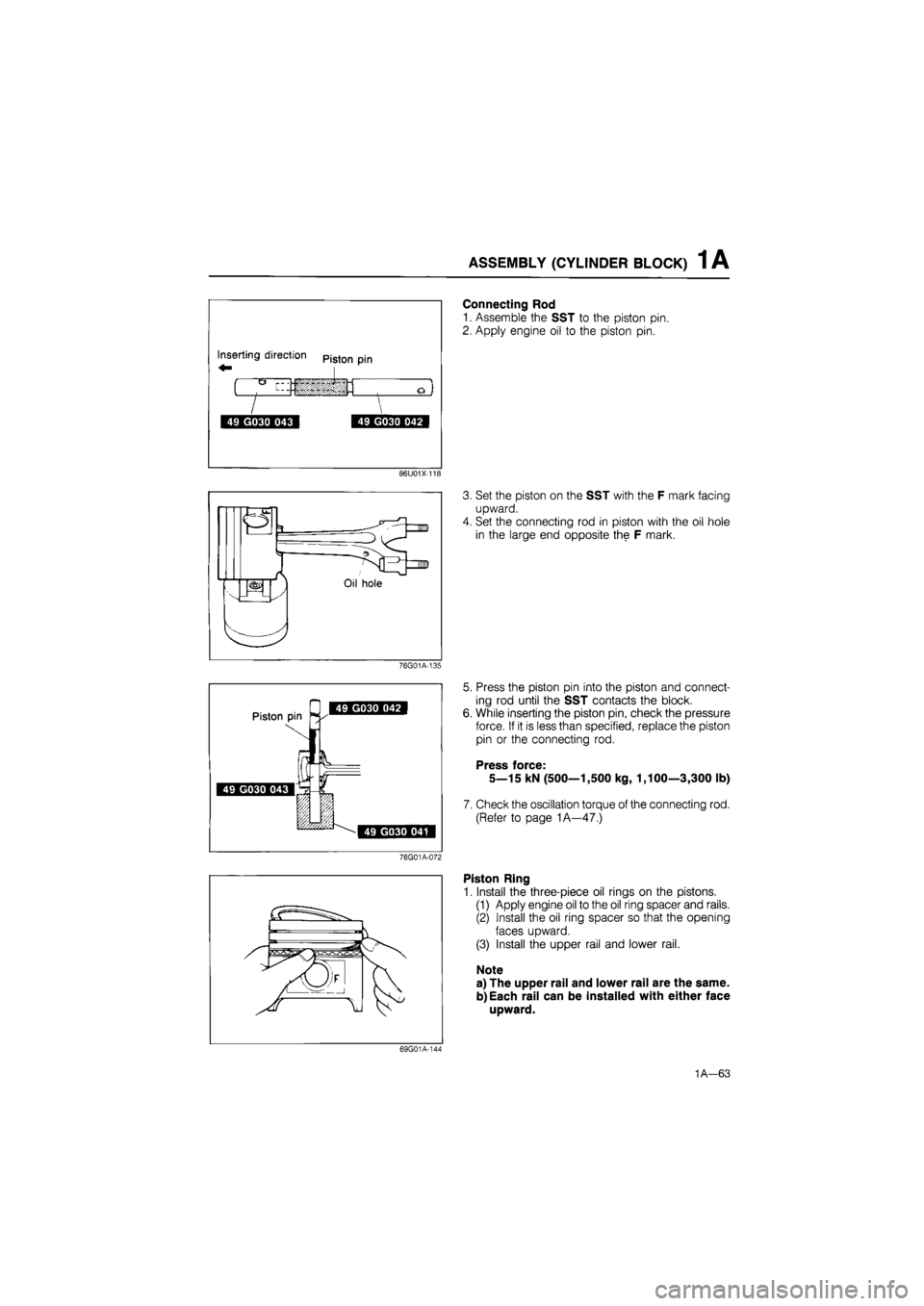
ASSEMBLY (CYLINDER BLOCK) 1 A
Connecting Rod
1. Assemble the SST to the piston pin.
2. Apply engine oil to the piston pin.
86U01X-118
3. Set the piston on the SST with the F mark facing
upward.
4. Set the connecting rod in piston with the oil hole
in the large end opposite the F mark.
76G01A-135
5. Press the piston pin into the piston and connect-
ing rod until the SST contacts the block.
While inserting the piston pin, check the pressure
force. If it is less than specified, replace the piston
pin or the connecting rod.
Press force:
5—15 kN (500—1,500 kg, 1,100—3,300 lb)
Check the oscillation torque of the connecting rod.
(Refer to page 1A—47.)
76G01A-072
Piston Ring
1. Install the three-piece oil rings on the pistons.
(1) Apply engine oil to the oil ring spacer and rails.
(2) Install the oil ring spacer so that the opening
faces upward.
(3) Install the upper rail and lower rail.
Note
a) The upper rail and lower rail are the same.
b) Each rail can be installed with either face
upward.
69G01A-144
1A—63
Page 96 of 1865
1 A ASSEMBLY (CYLINDER BLOCK)
Spacer iang
Oil ring
spacer ends
Upper rail
Piston
Lower rail
69G01A-145
86U01X-121
Oil ring —
upper rail f .Top ring
Oil ring (
spacer r \30° \ . Pistion
^-^/ao0F pin
Oil ring
lower rail /Second ring
69G01A-147
2. Check that both rails are expanded by the spacer
tangs as shown in the figure by checking that both
rails turn smoothly in both directions.
3. Install the second ring to the piston first, then in-
stall the top ring. Use a piston ring expander.
Caution
The rings must be installed with the "R"
marks facing upward.
4. Apply a liberal amount of clean engine oil to the
second and top piston rings.
5. Position the opening of each ring as shown in the
figure.
Crankshaft
1. Before installing the crankshaft, inspect the main
bearing oil clearances as described.
Note
The bearing with thrust shoulders is the cen-
ter bearing in the cylinder block.
86U01X-136
1A—64