Page 481 of 2339
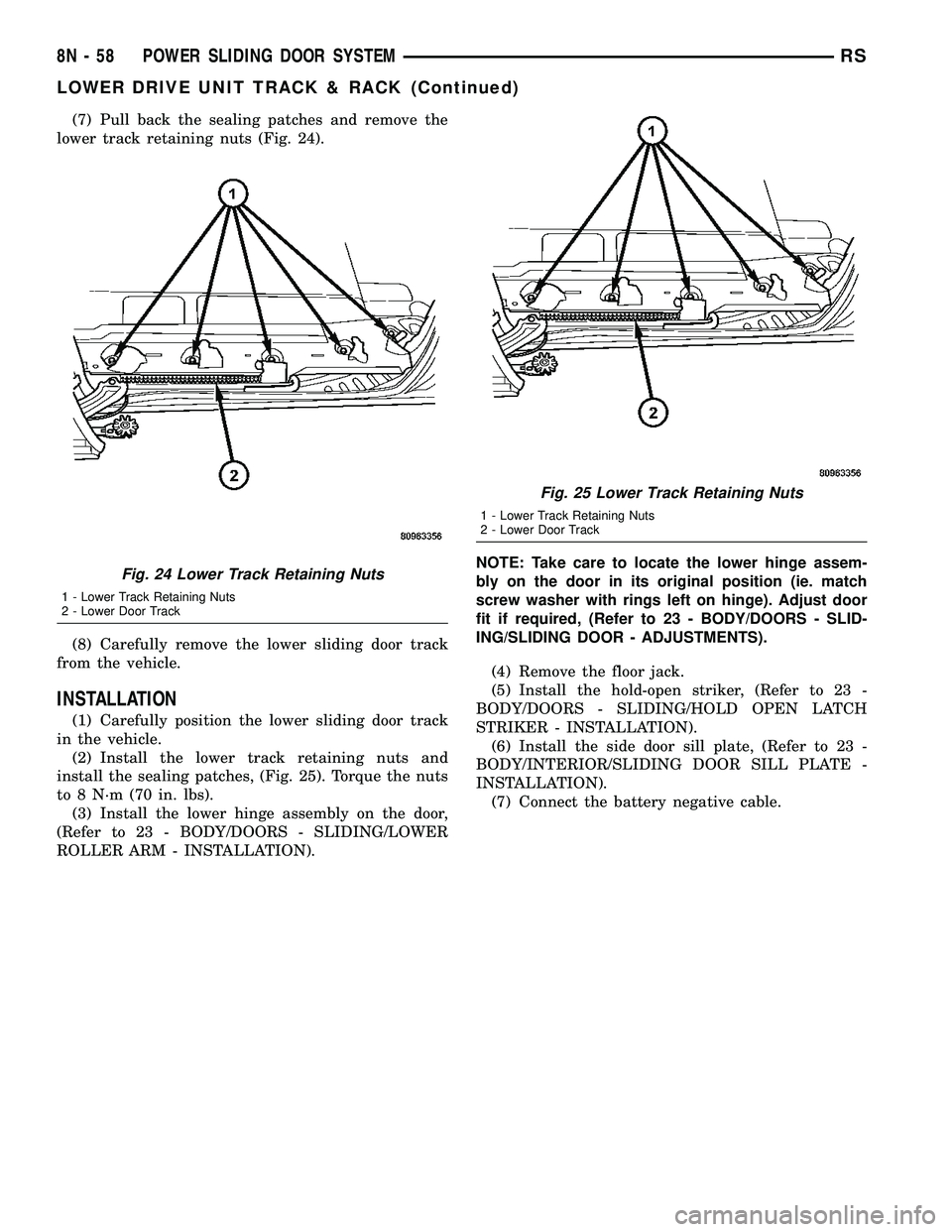
(7) Pull back the sealing patches and remove the
lower track retaining nuts (Fig. 24).
(8) Carefully remove the lower sliding door track
from the vehicle.
INSTALLATION
(1) Carefully position the lower sliding door track
in the vehicle.
(2) Install the lower track retaining nuts and
install the sealing patches, (Fig. 25). Torque the nuts
to 8 N´m (70 in. lbs).
(3) Install the lower hinge assembly on the door,
(Refer to 23 - BODY/DOORS - SLIDING/LOWER
ROLLER ARM - INSTALLATION).NOTE: Take care to locate the lower hinge assem-
bly on the door in its original position (ie. match
screw washer with rings left on hinge). Adjust door
fit if required, (Refer to 23 - BODY/DOORS - SLID-
ING/SLIDING DOOR - ADJUSTMENTS).
(4) Remove the floor jack.
(5) Install the hold-open striker, (Refer to 23 -
BODY/DOORS - SLIDING/HOLD OPEN LATCH
STRIKER - INSTALLATION).
(6) Install the side door sill plate, (Refer to 23 -
BODY/INTERIOR/SLIDING DOOR SILL PLATE -
INSTALLATION).
(7) Connect the battery negative cable.
Fig. 24 Lower Track Retaining Nuts
1 - Lower Track Retaining Nuts
2 - Lower Door Track
Fig. 25 Lower Track Retaining Nuts
1 - Lower Track Retaining Nuts
2 - Lower Door Track
8N - 58 POWER SLIDING DOOR SYSTEMRS
LOWER DRIVE UNIT TRACK & RACK (Continued)
Page 482 of 2339
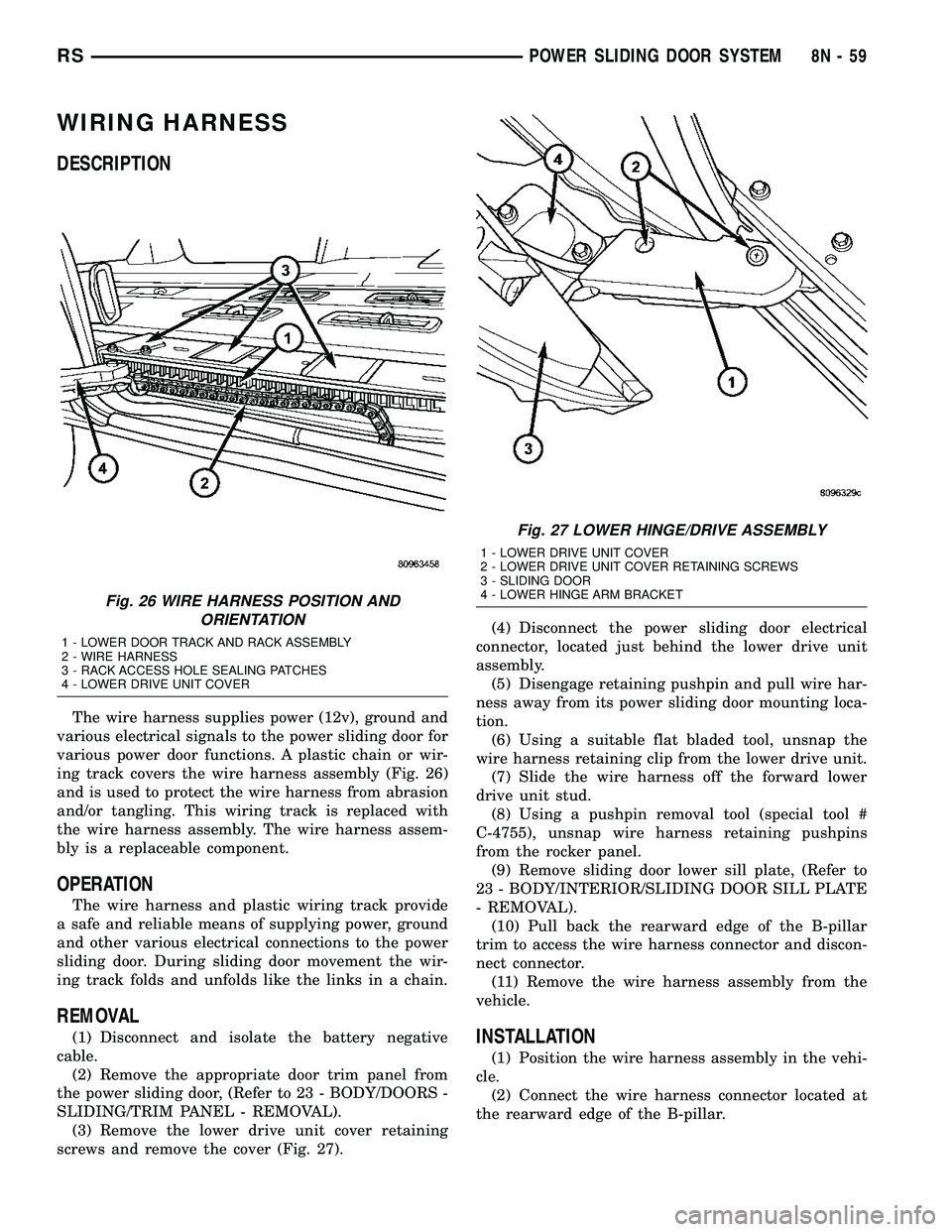
WIRING HARNESS
DESCRIPTION
The wire harness supplies power (12v), ground and
various electrical signals to the power sliding door for
various power door functions. A plastic chain or wir-
ing track covers the wire harness assembly (Fig. 26)
and is used to protect the wire harness from abrasion
and/or tangling. This wiring track is replaced with
the wire harness assembly. The wire harness assem-
bly is a replaceable component.
OPERATION
The wire harness and plastic wiring track provide
a safe and reliable means of supplying power, ground
and other various electrical connections to the power
sliding door. During sliding door movement the wir-
ing track folds and unfolds like the links in a chain.
REMOVAL
(1) Disconnect and isolate the battery negative
cable.
(2) Remove the appropriate door trim panel from
the power sliding door, (Refer to 23 - BODY/DOORS -
SLIDING/TRIM PANEL - REMOVAL).
(3) Remove the lower drive unit cover retaining
screws and remove the cover (Fig. 27).(4) Disconnect the power sliding door electrical
connector, located just behind the lower drive unit
assembly.
(5) Disengage retaining pushpin and pull wire har-
ness away from its power sliding door mounting loca-
tion.
(6) Using a suitable flat bladed tool, unsnap the
wire harness retaining clip from the lower drive unit.
(7) Slide the wire harness off the forward lower
drive unit stud.
(8) Using a pushpin removal tool (special tool #
C-4755), unsnap wire harness retaining pushpins
from the rocker panel.
(9) Remove sliding door lower sill plate, (Refer to
23 - BODY/INTERIOR/SLIDING DOOR SILL PLATE
- REMOVAL).
(10) Pull back the rearward edge of the B-pillar
trim to access the wire harness connector and discon-
nect connector.
(11) Remove the wire harness assembly from the
vehicle.INSTALLATION
(1) Position the wire harness assembly in the vehi-
cle.
(2) Connect the wire harness connector located at
the rearward edge of the B-pillar.
Fig. 26 WIRE HARNESS POSITION AND
ORIENTATION
1 - LOWER DOOR TRACK AND RACK ASSEMBLY
2 - WIRE HARNESS
3 - RACK ACCESS HOLE SEALING PATCHES
4 - LOWER DRIVE UNIT COVER
Fig. 27 LOWER HINGE/DRIVE ASSEMBLY
1 - LOWER DRIVE UNIT COVER
2 - LOWER DRIVE UNIT COVER RETAINING SCREWS
3 - SLIDING DOOR
4 - LOWER HINGE ARM BRACKET
RSPOWER SLIDING DOOR SYSTEM8N-59
Page 483 of 2339
(3) Install the sliding door lower sill plate, (Refer
to 23 - BODY/INTERIOR/SLIDING DOOR SILL
PLATE - INSTALLATION).
(4) Snap the wire harness retaining pushpins in
the rocker panel.
(5) Slide the wire harness on the lower drive unit
stud.
(6) Install the wire harness retaining clip on the
lower drive unit stud.
(7) Connect the power sliding door electrical con-
nector, located just behind the lower drive unit.
(8) Install the lower drive unit cover and retaining
screws (Fig. 28).
(9) Install the appropriate sliding door trim panel,
(Refer to 23 - BODY/DOORS - SLIDING/TRIM
PANEL - INSTALLATION).
(10) Connect the battery negative cable.
Fig. 28 LOWER HINGE/DRIVE ASSEMBLY
1 - LOWER DRIVE UNIT COVER
2 - LOWER DRIVE UNIT COVER RETAINING SCREWS
3 - SLIDING DOOR
4 - LOWER HINGE ARM BRACKET
8N - 60 POWER SLIDING DOOR SYSTEMRS
WIRING HARNESS (Continued)
Page 484 of 2339
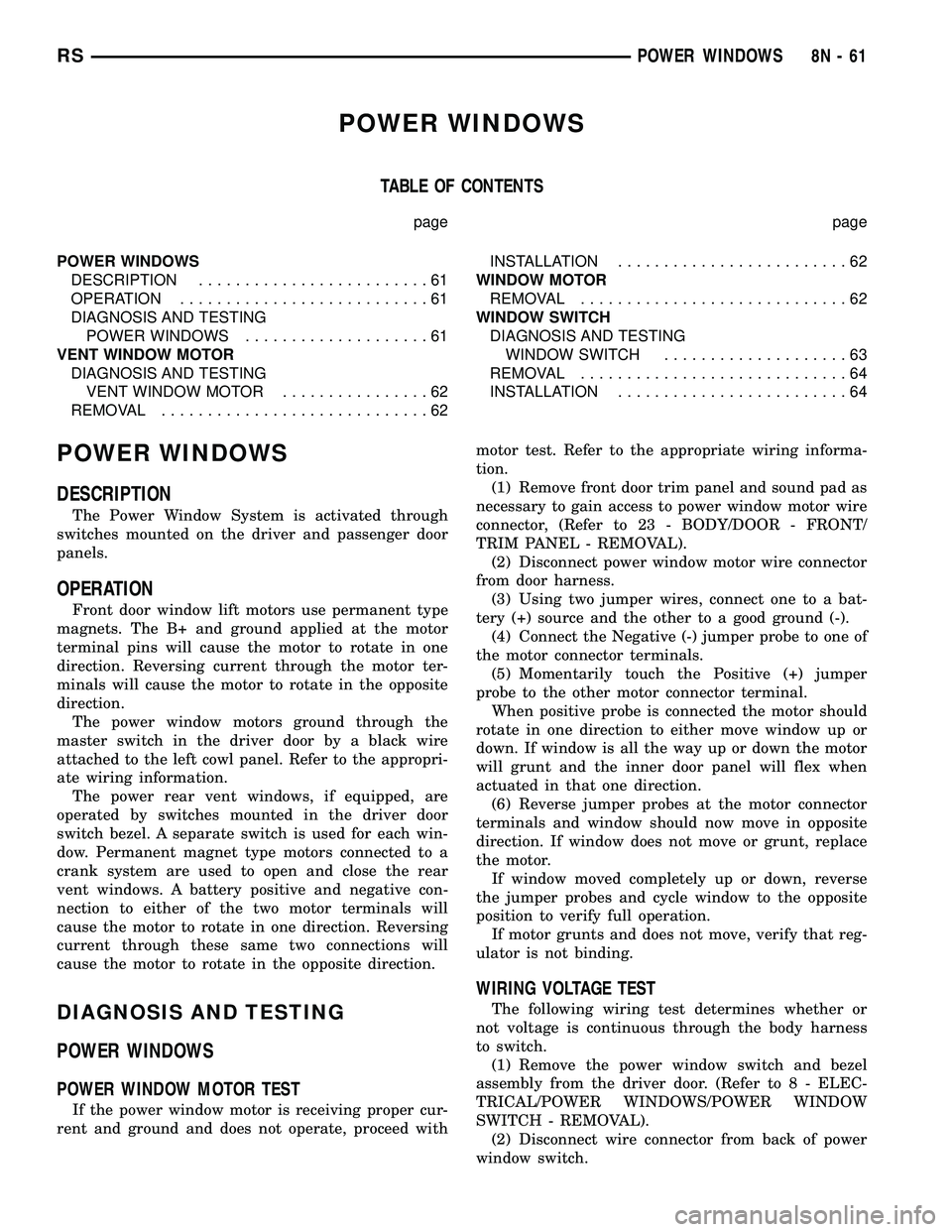
POWER WINDOWS
TABLE OF CONTENTS
page page
POWER WINDOWS
DESCRIPTION.........................61
OPERATION...........................61
DIAGNOSIS AND TESTING
POWER WINDOWS....................61
VENT WINDOW MOTOR
DIAGNOSIS AND TESTING
VENT WINDOW MOTOR................62
REMOVAL.............................62INSTALLATION.........................62
WINDOW MOTOR
REMOVAL.............................62
WINDOW SWITCH
DIAGNOSIS AND TESTING
WINDOW SWITCH....................63
REMOVAL.............................64
INSTALLATION.........................64
POWER WINDOWS
DESCRIPTION
The Power Window System is activated through
switches mounted on the driver and passenger door
panels.
OPERATION
Front door window lift motors use permanent type
magnets. The B+ and ground applied at the motor
terminal pins will cause the motor to rotate in one
direction. Reversing current through the motor ter-
minals will cause the motor to rotate in the opposite
direction.
The power window motors ground through the
master switch in the driver door by a black wire
attached to the left cowl panel. Refer to the appropri-
ate wiring information.
The power rear vent windows, if equipped, are
operated by switches mounted in the driver door
switch bezel. A separate switch is used for each win-
dow. Permanent magnet type motors connected to a
crank system are used to open and close the rear
vent windows. A battery positive and negative con-
nection to either of the two motor terminals will
cause the motor to rotate in one direction. Reversing
current through these same two connections will
cause the motor to rotate in the opposite direction.
DIAGNOSIS AND TESTING
POWER WINDOWS
POWER WINDOW MOTOR TEST
If the power window motor is receiving proper cur-
rent and ground and does not operate, proceed withmotor test. Refer to the appropriate wiring informa-
tion.
(1) Remove front door trim panel and sound pad as
necessary to gain access to power window motor wire
connector, (Refer to 23 - BODY/DOOR - FRONT/
TRIM PANEL - REMOVAL).
(2) Disconnect power window motor wire connector
from door harness.
(3) Using two jumper wires, connect one to a bat-
tery (+) source and the other to a good ground (-).
(4) Connect the Negative (-) jumper probe to one of
the motor connector terminals.
(5) Momentarily touch the Positive (+) jumper
probe to the other motor connector terminal.
When positive probe is connected the motor should
rotate in one direction to either move window up or
down. If window is all the way up or down the motor
will grunt and the inner door panel will flex when
actuated in that one direction.
(6) Reverse jumper probes at the motor connector
terminals and window should now move in opposite
direction. If window does not move or grunt, replace
the motor.
If window moved completely up or down, reverse
the jumper probes and cycle window to the opposite
position to verify full operation.
If motor grunts and does not move, verify that reg-
ulator is not binding.
WIRING VOLTAGE TEST
The following wiring test determines whether or
not voltage is continuous through the body harness
to switch.
(1) Remove the power window switch and bezel
assembly from the driver door. (Refer to 8 - ELEC-
TRICAL/POWER WINDOWS/POWER WINDOW
SWITCH - REMOVAL).
(2) Disconnect wire connector from back of power
window switch.
RSPOWER WINDOWS8N-61
Page 485 of 2339
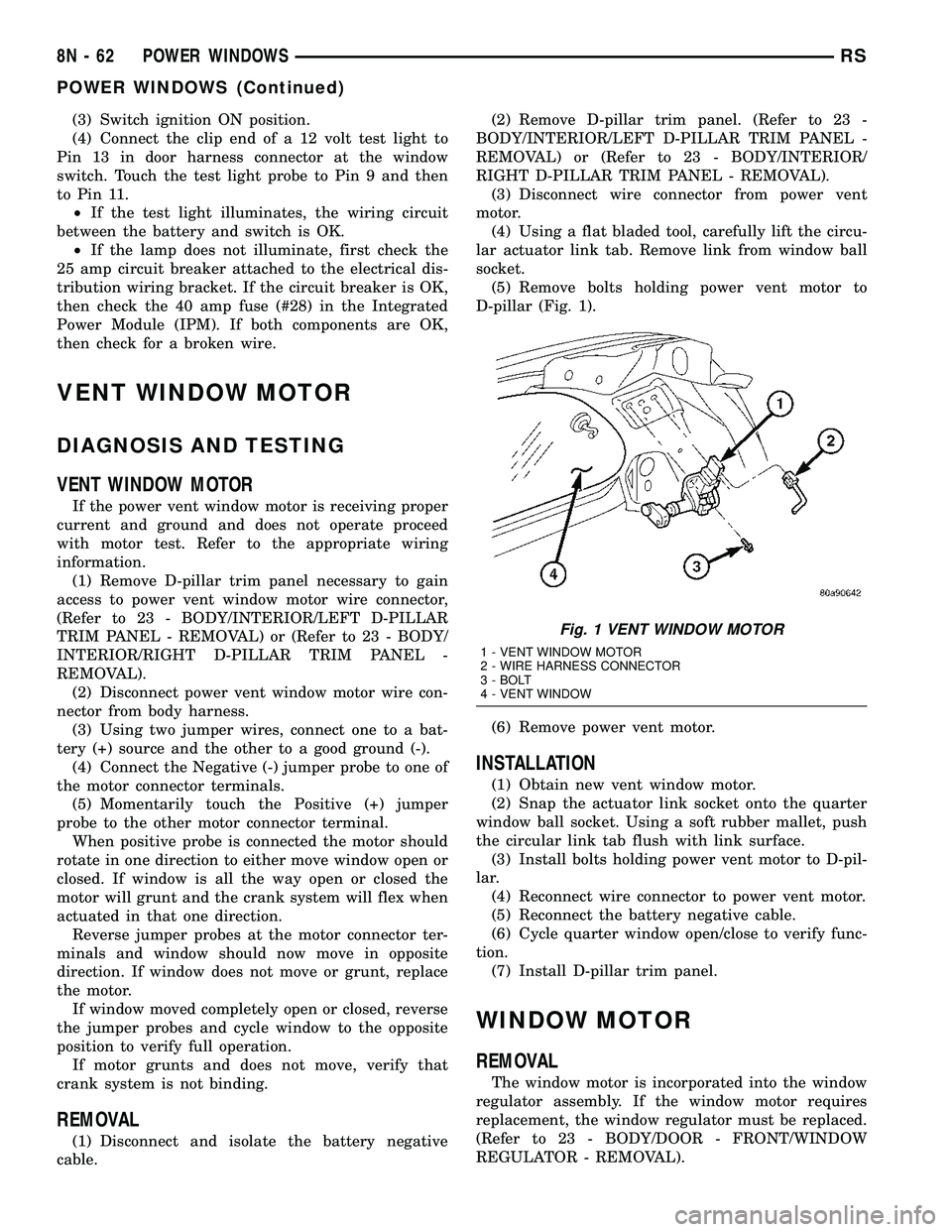
(3) Switch ignition ON position.
(4) Connect the clip end of a 12 volt test light to
Pin 13 in door harness connector at the window
switch. Touch the test light probe to Pin 9 and then
to Pin 11.
²If the test light illuminates, the wiring circuit
between the battery and switch is OK.
²If the lamp does not illuminate, first check the
25 amp circuit breaker attached to the electrical dis-
tribution wiring bracket. If the circuit breaker is OK,
then check the 40 amp fuse (#28) in the Integrated
Power Module (IPM). If both components are OK,
then check for a broken wire.
VENT WINDOW MOTOR
DIAGNOSIS AND TESTING
VENT WINDOW MOTOR
If the power vent window motor is receiving proper
current and ground and does not operate proceed
with motor test. Refer to the appropriate wiring
information.
(1) Remove D-pillar trim panel necessary to gain
access to power vent window motor wire connector,
(Refer to 23 - BODY/INTERIOR/LEFT D-PILLAR
TRIM PANEL - REMOVAL) or (Refer to 23 - BODY/
INTERIOR/RIGHT D-PILLAR TRIM PANEL -
REMOVAL).
(2) Disconnect power vent window motor wire con-
nector from body harness.
(3) Using two jumper wires, connect one to a bat-
tery (+) source and the other to a good ground (-).
(4) Connect the Negative (-) jumper probe to one of
the motor connector terminals.
(5) Momentarily touch the Positive (+) jumper
probe to the other motor connector terminal.
When positive probe is connected the motor should
rotate in one direction to either move window open or
closed. If window is all the way open or closed the
motor will grunt and the crank system will flex when
actuated in that one direction.
Reverse jumper probes at the motor connector ter-
minals and window should now move in opposite
direction. If window does not move or grunt, replace
the motor.
If window moved completely open or closed, reverse
the jumper probes and cycle window to the opposite
position to verify full operation.
If motor grunts and does not move, verify that
crank system is not binding.
REMOVAL
(1) Disconnect and isolate the battery negative
cable.(2) Remove D-pillar trim panel. (Refer to 23 -
BODY/INTERIOR/LEFT D-PILLAR TRIM PANEL -
REMOVAL) or (Refer to 23 - BODY/INTERIOR/
RIGHT D-PILLAR TRIM PANEL - REMOVAL).
(3) Disconnect wire connector from power vent
motor.
(4) Using a flat bladed tool, carefully lift the circu-
lar actuator link tab. Remove link from window ball
socket.
(5) Remove bolts holding power vent motor to
D-pillar (Fig. 1).
(6) Remove power vent motor.
INSTALLATION
(1) Obtain new vent window motor.
(2) Snap the actuator link socket onto the quarter
window ball socket. Using a soft rubber mallet, push
the circular link tab flush with link surface.
(3) Install bolts holding power vent motor to D-pil-
lar.
(4) Reconnect wire connector to power vent motor.
(5) Reconnect the battery negative cable.
(6) Cycle quarter window open/close to verify func-
tion.
(7) Install D-pillar trim panel.
WINDOW MOTOR
REMOVAL
The window motor is incorporated into the window
regulator assembly. If the window motor requires
replacement, the window regulator must be replaced.
(Refer to 23 - BODY/DOOR - FRONT/WINDOW
REGULATOR - REMOVAL).
Fig. 1 VENT WINDOW MOTOR
1 - VENT WINDOW MOTOR
2 - WIRE HARNESS CONNECTOR
3 - BOLT
4 - VENT WINDOW
8N - 62 POWER WINDOWSRS
POWER WINDOWS (Continued)
Page 486 of 2339
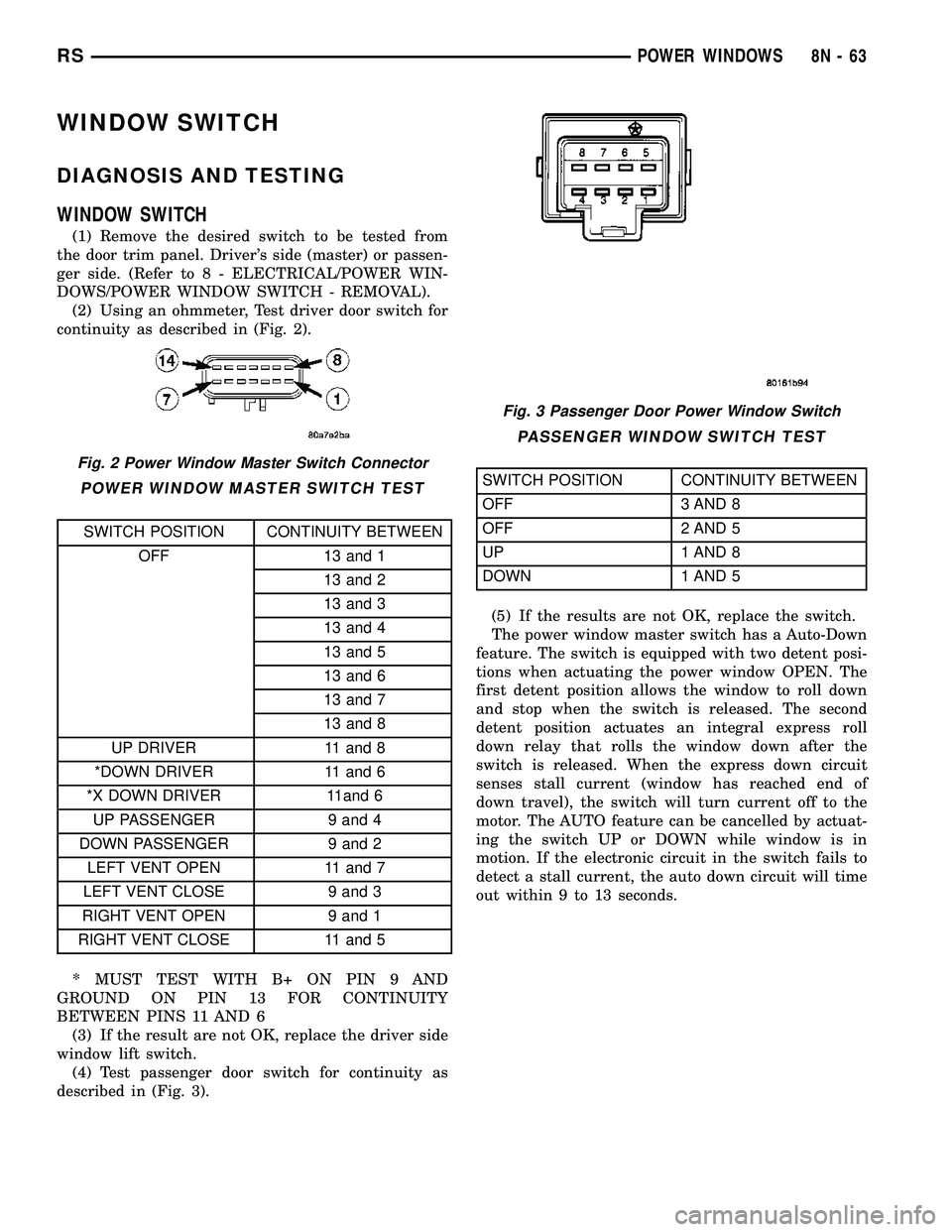
WINDOW SWITCH
DIAGNOSIS AND TESTING
WINDOW SWITCH
(1) Remove the desired switch to be tested from
the door trim panel. Driver's side (master) or passen-
ger side. (Refer to 8 - ELECTRICAL/POWER WIN-
DOWS/POWER WINDOW SWITCH - REMOVAL).
(2) Using an ohmmeter, Test driver door switch for
continuity as described in (Fig. 2).
POWER WINDOW MASTER SWITCH TEST
SWITCH POSITION CONTINUITY BETWEEN
OFF 13 and 1
13 and 2
13 and 3
13 and 4
13 and 5
13 and 6
13 and 7
13 and 8
UP DRIVER 11 and 8
*DOWN DRIVER 11 and 6
*X DOWN DRIVER 11and 6
UP PASSENGER 9 and 4
DOWN PASSENGER 9 and 2
LEFT VENT OPEN 11 and 7
LEFT VENT CLOSE 9 and 3
RIGHT VENT OPEN 9 and 1
RIGHT VENT CLOSE 11 and 5
* MUST TEST WITH B+ ON PIN 9 AND
GROUND ON PIN 13 FOR CONTINUITY
BETWEEN PINS 11 AND 6
(3) If the result are not OK, replace the driver side
window lift switch.
(4) Test passenger door switch for continuity as
described in (Fig. 3).
PASSENGER WINDOW SWITCH TEST
SWITCH POSITION CONTINUITY BETWEEN
OFF 3 AND 8
OFF 2 AND 5
UP 1 AND 8
DOWN 1 AND 5
(5) If the results are not OK, replace the switch.
The power window master switch has a Auto-Down
feature. The switch is equipped with two detent posi-
tions when actuating the power window OPEN. The
first detent position allows the window to roll down
and stop when the switch is released. The second
detent position actuates an integral express roll
down relay that rolls the window down after the
switch is released. When the express down circuit
senses stall current (window has reached end of
down travel), the switch will turn current off to the
motor. The AUTO feature can be cancelled by actuat-
ing the switch UP or DOWN while window is in
motion. If the electronic circuit in the switch fails to
detect a stall current, the auto down circuit will time
out within 9 to 13 seconds.
Fig. 2 Power Window Master Switch Connector
Fig. 3 Passenger Door Power Window Switch
RSPOWER WINDOWS8N-63
Page 487 of 2339
REMOVAL
(1) Disconnect and isolate the battery negative
cable.
(2) Using a trim stick, start at the bottom of the
switch and bezel assembly and pry up to remove the
switch and bezel assembly from the door trim panel
(Fig. 4).
(3) Unlatch the locking tab on the harness side
connector of the switch.
(4) Disconnect wire harness connectors from
switch.
INSTALLATION
(1) Reconnect wire harness connector to switch.
(2) Insert switch into door trim panel and press
into place.
(3) Reconnect battery negative cable.
Fig. 4 POWER WINDOW SWITCH
1 - DOOR TRIM PANEL
2 - POWER WINDOW SWITCH AND BEZEL ASSEMBLY
8N - 64 POWER WINDOWSRS
WINDOW SWITCH (Continued)
Page 488 of 2339
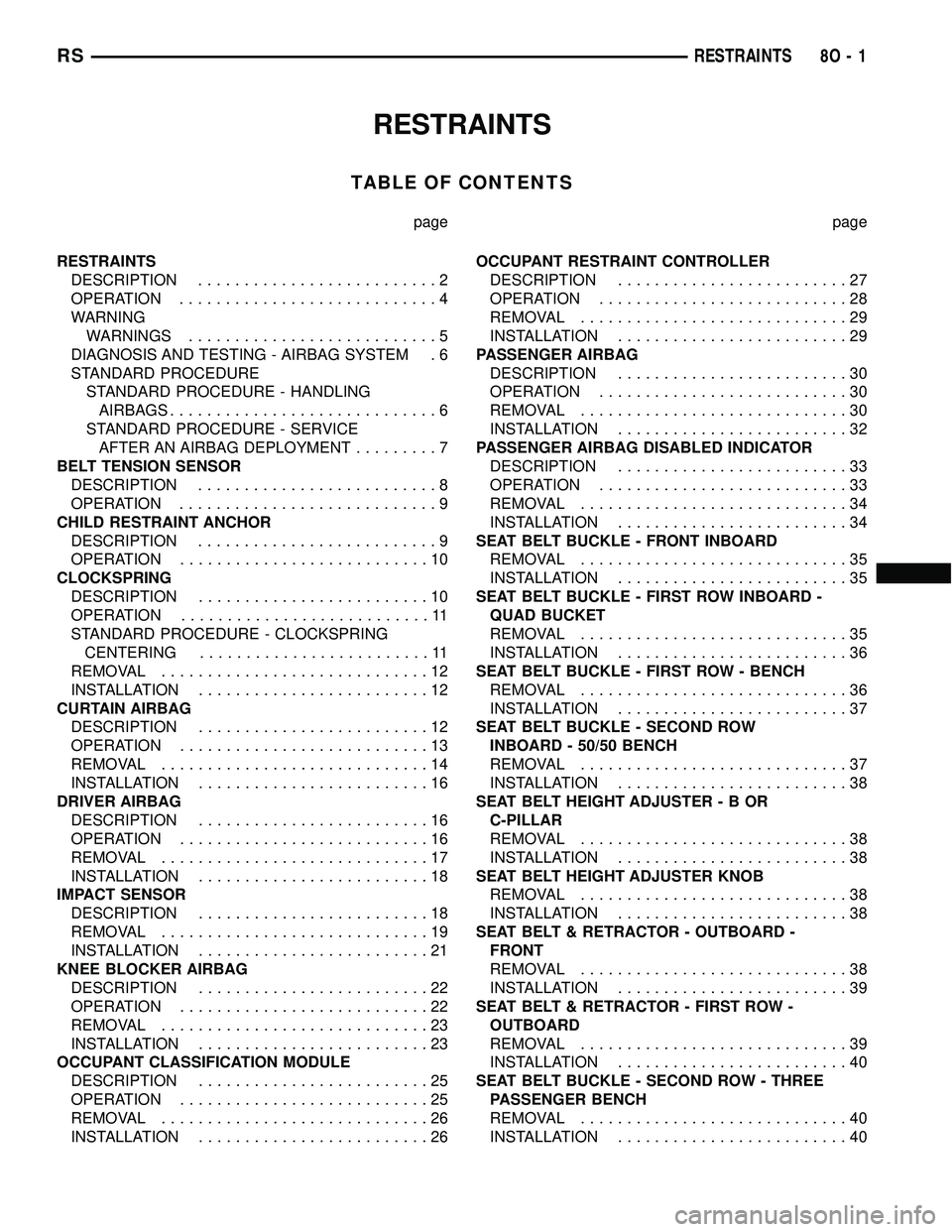
RESTRAINTS
TABLE OF CONTENTS
page page
RESTRAINTS
DESCRIPTION..........................2
OPERATION............................4
WARNING
WARNINGS...........................5
DIAGNOSIS AND TESTING - AIRBAG SYSTEM . 6
STANDARD PROCEDURE
STANDARD PROCEDURE - HANDLING
AIRBAGS.............................6
STANDARD PROCEDURE - SERVICE
AFTER AN AIRBAG DEPLOYMENT.........7
BELT TENSION SENSOR
DESCRIPTION..........................8
OPERATION............................9
CHILD RESTRAINT ANCHOR
DESCRIPTION..........................9
OPERATION...........................10
CLOCKSPRING
DESCRIPTION.........................10
OPERATION...........................11
STANDARD PROCEDURE - CLOCKSPRING
CENTERING.........................11
REMOVAL.............................12
INSTALLATION.........................12
CURTAIN AIRBAG
DESCRIPTION.........................12
OPERATION...........................13
REMOVAL.............................14
INSTALLATION.........................16
DRIVER AIRBAG
DESCRIPTION.........................16
OPERATION...........................16
REMOVAL.............................17
INSTALLATION.........................18
IMPACT SENSOR
DESCRIPTION.........................18
REMOVAL.............................19
INSTALLATION.........................21
KNEE BLOCKER AIRBAG
DESCRIPTION.........................22
OPERATION...........................22
REMOVAL.............................23
INSTALLATION.........................23
OCCUPANT CLASSIFICATION MODULE
DESCRIPTION.........................25
OPERATION...........................25
REMOVAL.............................26
INSTALLATION.........................26OCCUPANT RESTRAINT CONTROLLER
DESCRIPTION.........................27
OPERATION...........................28
REMOVAL.............................29
INSTALLATION.........................29
PASSENGER AIRBAG
DESCRIPTION.........................30
OPERATION...........................30
REMOVAL.............................30
INSTALLATION.........................32
PASSENGER AIRBAG DISABLED INDICATOR
DESCRIPTION.........................33
OPERATION...........................33
REMOVAL.............................34
INSTALLATION.........................34
SEAT BELT BUCKLE - FRONT INBOARD
REMOVAL.............................35
INSTALLATION.........................35
SEAT BELT BUCKLE - FIRST ROW INBOARD -
QUAD BUCKET
REMOVAL.............................35
INSTALLATION.........................36
SEAT BELT BUCKLE - FIRST ROW - BENCH
REMOVAL.............................36
INSTALLATION.........................37
SEAT BELT BUCKLE - SECOND ROW
INBOARD - 50/50 BENCH
REMOVAL.............................37
INSTALLATION.........................38
SEAT BELT HEIGHT ADJUSTER-BOR
C-PILLAR
REMOVAL.............................38
INSTALLATION.........................38
SEAT BELT HEIGHT ADJUSTER KNOB
REMOVAL.............................38
INSTALLATION.........................38
SEAT BELT & RETRACTOR - OUTBOARD -
FRONT
REMOVAL.............................38
INSTALLATION.........................39
SEAT BELT & RETRACTOR - FIRST ROW -
OUTBOARD
REMOVAL.............................39
INSTALLATION.........................40
SEAT BELT BUCKLE - SECOND ROW - THREE
PASSENGER BENCH
REMOVAL.............................40
INSTALLATION.........................40
RSRESTRAINTS8O-1