Page 1 of 513
1
s
I
I
P
r
r
i
J
I
I
Y
1
L
I
J
n
0I
f
0
F
c
o
v
I
il
I
I
r
V
I
II
i
t
I
l
C
J
L
E
7
c
vi
r
I
I
J
J
A
j
l
l
1
0
I
LJ
I
j
I
j
J
JL
y
I
J
l
Page 2 of 513
Page 3 of 513
A
e
@
wWD@
mQD
1
p
DATSUN
1200
MODEL
B
11
0
SERIES
l
NISSAN
I
4
l
l
f
t
NI
SSAN
MOTOR
CO
LTD
TO
Yi
lIAPAN
SECTION
AT
AUTOMATIC
TRANSMISSION
DESCRIPTION
HYDRAULIC
CONTROL
SYSTEM
REMOVAL
AND
INSTALLATION
MAJOR
REPAIR
OPERATION
TROUBLE
DIAGNOSES
AND
ADJUSTMENT
SERVicE1
DATA
AND
SPECIFICATIONS
t
i
fr
lr
lo
i
1
4
1
p
i
AT
2
AT
4
AT
33
AT
31
AT
49
Al
60
1
r
1
i
J
Page 4 of 513
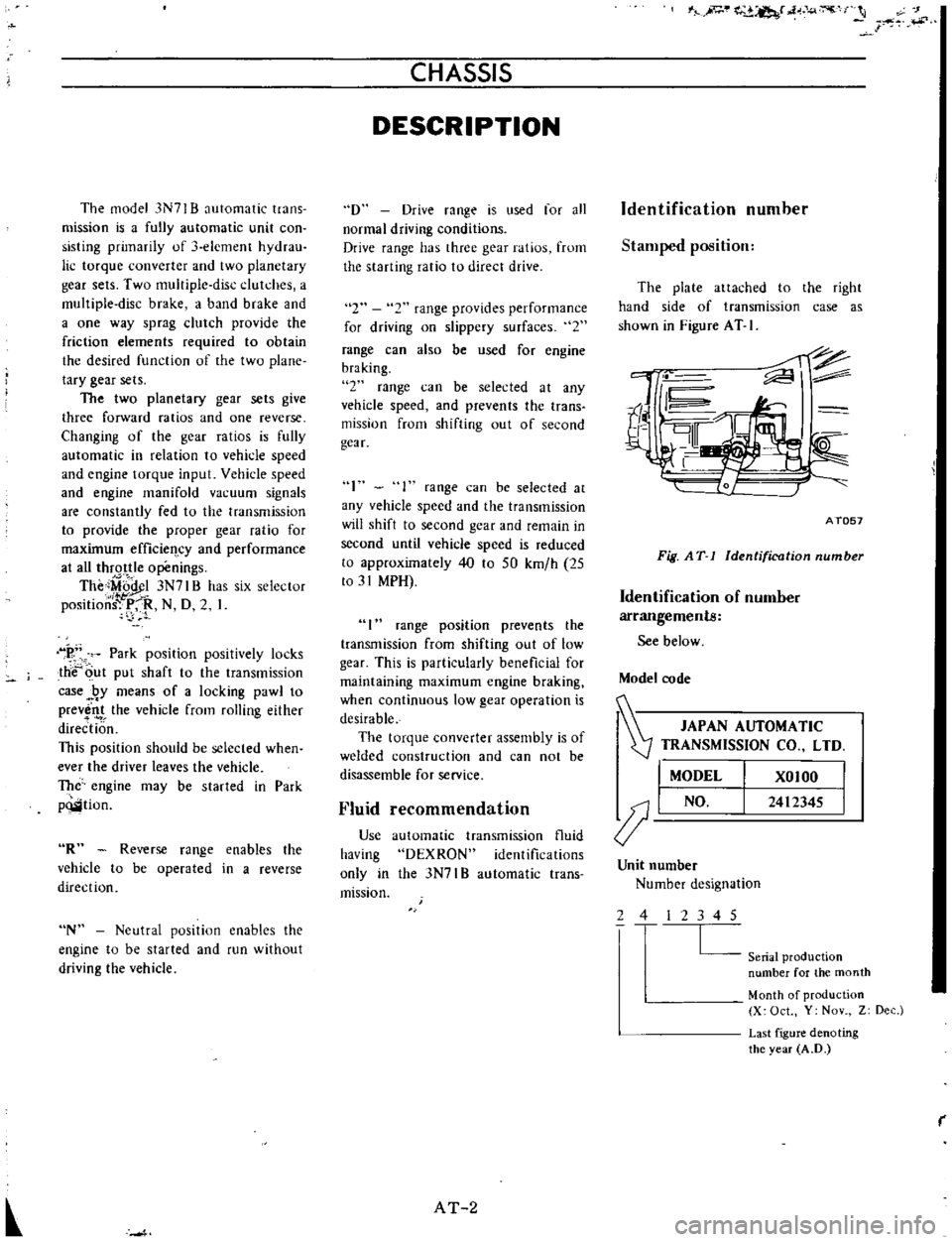
The
model
3N71
B
automatic
trans
mission
is
a
fully
automatic
unit
con
sisting
primarily
of
element
hydrau
lic
torque
converter
and
two
planetary
gear
sets
Two
multiple
disc
clutches
a
muItiple
disc
brake
a
band
brake
and
a
one
way
sprag
clutch
provide
the
friction
elements
required
to
obtain
the
desired
function
of
the
two
plane
tary
gear
sets
The
two
planetary
gear
sets
give
three
forward
ratios
and
one
reverse
Changing
of
the
gear
ratios
is
fully
automatic
in
relation
to
vehicle
speed
and
engine
torque
input
Vehicle
speed
and
engine
manifold
vacuum
signals
are
constantly
fed
to
the
transmission
to
provide
the
proper
gear
ratio
for
maximum
efficieq
cy
and
performance
at
all
thrqttIe
openings
The
iMiij
l
3N7I
B
has
six
selector
position
f
P
R
N
D
2
1
k
Park
position
positively
locks
the
c
ut
put
shaft
to
the
transmission
case
RY
means
of
a
locking
pawl
to
prev
nt
the
vehicle
from
rolling
either
direction
This
position
should
be
selected
when
ever
the
driver
leaves
the
vehicle
The
engine
may
be
started
in
Park
pQlition
OR
Reverse
range
enables
the
vehicle
to
be
operated
in
a
reverse
direction
N
Neutral
posItion
enables
the
engine
to
be
started
and
run
without
driving
the
vehicle
CHASSIS
DESCRIPTION
D
Drive
range
is
used
for
all
normal
driving
conditions
Drive
range
has
three
gear
ratios
frum
the
starting
ratio
to
direct
drive
2
2
range
provides
performance
for
driving
on
slippery
surfaces
2
range
can
also
be
used
for
engine
braking
2
range
can
be
selected
at
any
vehicle
speed
and
prevents
the
trans
mission
from
shifting
out
of
second
gear
I
range
can
be
selected
at
any
vehicle
speed
and
the
transmission
will
shift
to
second
gear
and
remain
in
second
until
vehide
speed
is
reduced
to
approximately
40
to
50
kmfh
25
to
31
MPH
I
range
position
prevents
the
transmission
from
shifting
out
of
low
gear
This
is
particularly
beneficial
for
maintaining
maximum
engine
braking
when
continuous
low
gear
operation
is
desirable
The
torque
converter
assembly
is
of
welded
construction
and
can
not
be
disassemble
for
service
Fluid
recommendation
Use
having
only
in
mission
automatic
transmission
fluid
DEXRON
identifications
the
3N7I
B
automatic
trans
AT
2
IA
e
l
csr
4o
J
r
s
Identification
number
Stamped
position
The
plate
attached
to
the
right
hand
side
of
transmission
case
as
shown
in
Figure
AT
I
ii
II
r
4
1
r
I
to
i
AT057
Fig
AT
1
Identification
number
Identification
of
number
arrangements
See
below
Model
code
JAPAN
AUTOMATIC
Z
TRANSMISSION
CO
LTD
I
MODEL
XOIOO
J
I
NO
2412345
Unit
number
Number
designation
2
4
2
3
4
5
L
Seriat
production
number
for
the
month
Month
of
production
X
Oct
Y
Nov
Z
Dec
Last
figure
denoting
the
year
A
D
r
Page 5 of 513
AUTOMATIC
TRANSMISSION
1
1
1
I
L
@
CD
@
@
ID
@
@
h
r
H
@
@
@
@
@
@
@
4
@
@
t
I
fA
TIl70
4
t
ill
pJrP
I
Transmission
ase
II
Governor
Tightening
torque
T
of
@T
0
5
to
0
7
2
Oil
pump
12
Output
shaft
bolts
and
nuts
kg
rn
ft
Ib
3
6
to
5
1
3
Front
clutch
13
Rear
xtcnsion
@T
0
8
to
1
0
@T
2
0
to
2
5
4
Band
brake
14
Oil
pan
@T
5
8
to
7
2
14
to
18
5
Rear
clutch
15
Control
valve
4
to
5
@T
1
3
to
1
8
6
Front
planetary
gt
ar
16
Input
shaft
@T
29
to
36
9
4
to
13
7
Rear
planetary
gear
17
Torque
converter
6
5
to
7
5
@T
0
55
to
0
75
8
One
way
clutch
18
Converter
housing
@T
47
to
54
4
0
to
5
4
9
Low
Reverse
brake
19
Drive
plate
0
6
h
Q
8
Q
T
0
25
to
0
35
10
Oil
distributor
4
3
to
5
8
1
9
to
2
5
Fig
AT
2
Cross
sectional
uiew
of
3N71
B
automatic
transmission
I
AT
3
l
t
Page 6 of 513
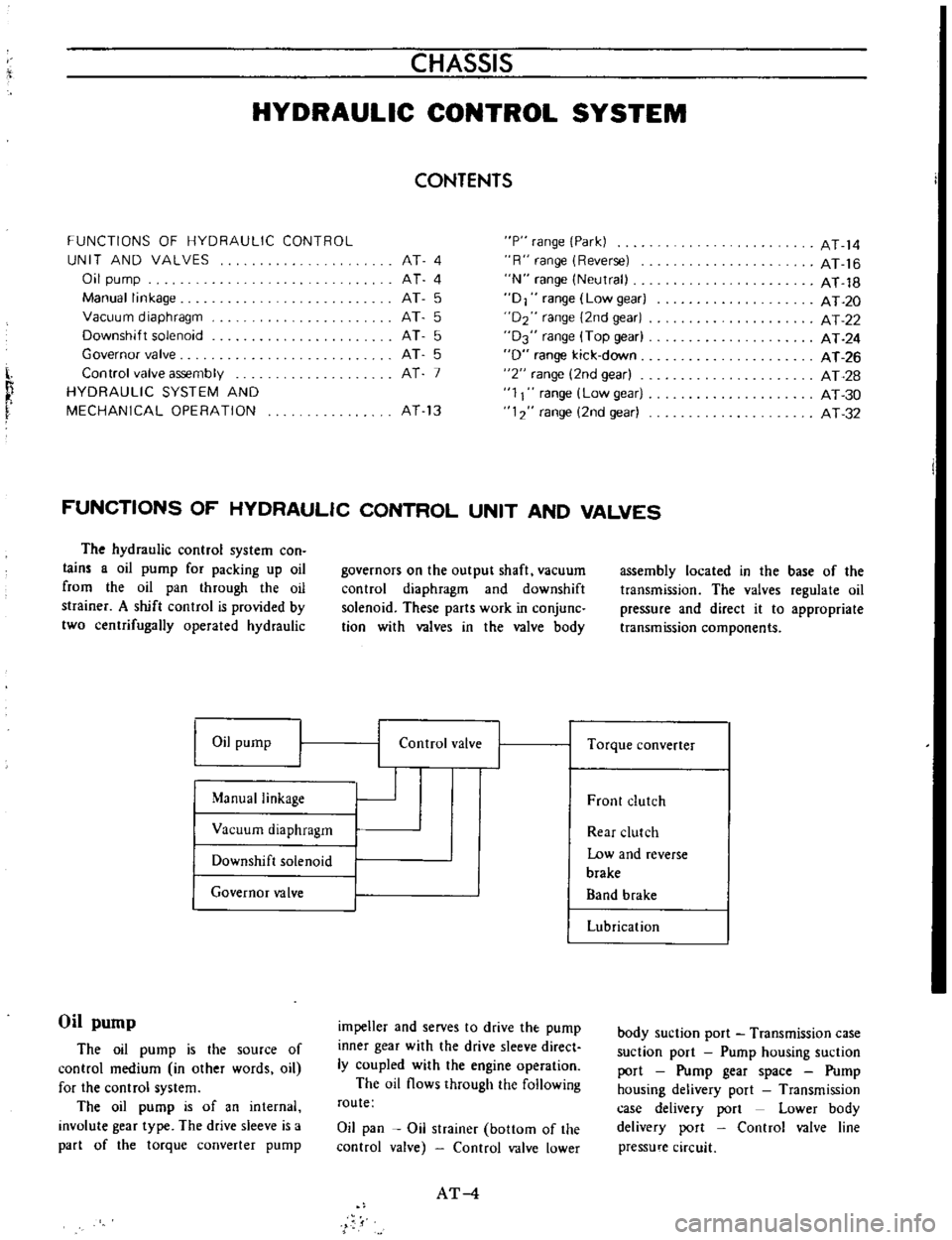
CHASSIS
HYDRAULIC
CONTROL
SYSTEM
l
FUNCTIONS
OF
HYDRAULIC
CONTROL
UNIT
AND
VALVES
Oil
pump
Manual
linkage
Vacuum
diaphragm
Downshift
solenoid
Governor
valve
Control
valve
assembly
HYDRAULIC
SYSTEM
AND
MECHANICAL
OPERATION
CONTENTS
P
range
Park
R
range
Reverse
N
range
Neutral
D
range
Low
gear
D2
range
2nd
gear
D3
range
Top
gear
D
range
kick
down
2
range
2nd
gear
1
range
Low
gear
12
range
2nd
gear
AT
4
AT
4
AT
5
AT
5
AT
5
AT
5
AT
7
AT13
AT
14
AT
16
AT
18
AT
20
AT
22
AT
24
AT
26
AT
28
AT
30
AT
32
FUNCTIONS
OF
HYDRAULIC
CONTROL
UNIT
AND
VALVES
The
hydraulic
control
system
con
lain
a
oil
pump
for
packing
up
oil
from
the
oil
pan
through
the
oil
strainer
A
shift
control
is
provided
by
two
centrifugally
operated
hydraulic
Oil
pump
Manual
linkage
Vacuum
diaphragm
Downshift
solenoid
Governor
valve
Oil
pump
The
oil
pump
is
the
source
of
control
medium
in
other
words
oil
for
the
control
system
The
oil
pump
is
of
an
internal
involute
gear
type
The
drive
sleeve
is
a
part
of
the
torque
converter
pump
governors
on
the
output
shaft
vacuum
control
diaphragm
and
downshift
solenoid
These
parts
work
in
conjunc
tion
with
valves
in
the
valve
body
I
I
Control
valve
impeller
and
serves
to
drive
the
pump
inner
gear
with
the
drive
sleeve
direct
ly
coupled
with
the
engine
operation
The
oil
flows
through
the
following
route
Oil
pan
Oil
strainer
bottom
of
the
control
valve
Control
valve
lower
AT
4
assembly
located
in
the
base
of
the
transmission
The
valves
regulate
oil
pressure
and
direct
it
to
appropriate
transmission
components
I
Torque
converter
Front
clutch
Rear
clutch
Low
and
reverse
brake
Band
brake
Lubrication
body
suction
port
Transmission
case
suction
port
Pump
housing
suction
port
Pump
gear
space
Pump
housing
delivery
port
Transmission
case
delivery
port
Lower
body
delivery
port
Control
valve
line
pressure
circuit
Page 7 of 513
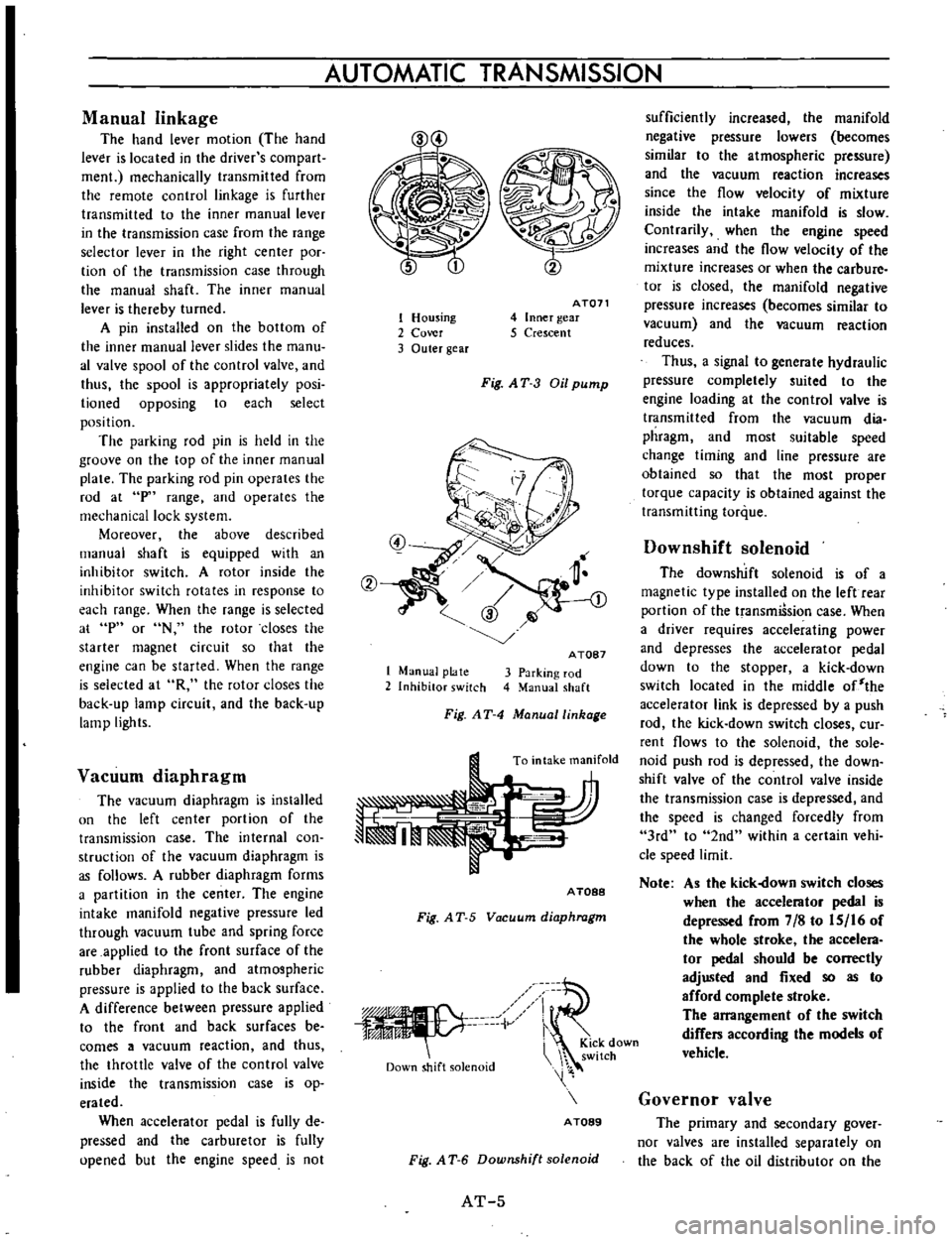
AUTOMATIC
TRANSMISSION
Manual
linkage
The
hand
lever
motion
The
hand
lever
is
located
in
the
driver
s
com
part
men
mechanically
transmitted
from
the
remote
control
linkage
is
further
transmitted
to
the
inner
manual
lever
in
the
transmission
case
from
the
range
selector
lever
in
the
right
center
poc
tion
of
the
transmission
case
through
the
manual
shaft
The
inner
manual
lever
is
thereby
turned
A
pin
installed
on
the
bottom
of
the
inner
manual
lever
slides
the
manu
al
valve
spool
of
the
control
valve
and
thus
the
spool
is
appropriately
posi
lioned
opposing
to
each
select
position
The
parking
rod
pin
is
held
in
the
groove
on
the
top
of
the
inner
manual
plate
The
parking
rod
pin
operates
the
rod
at
p
range
and
operates
the
mechanical
lock
system
Moreover
the
above
described
manual
shaft
is
equipped
with
an
inhibitor
switch
A
rotor
inside
the
inhibitor
switch
rotates
in
response
to
each
range
When
the
range
is
selected
at
p
or
N
the
rotor
closes
the
starter
magnet
circuit
so
that
the
engine
can
be
started
When
the
range
is
selected
at
R
the
rotor
closes
the
back
up
lamp
circuit
and
the
back
up
lamp
lights
Vacuum
diaphragm
The
vacuum
diaphragm
is
installed
un
the
left
center
portion
of
the
transmission
case
The
internal
con
struction
of
the
vacuum
diaphragm
is
as
follows
A
rubber
diaphragm
forms
a
partition
in
the
center
The
engine
intake
manifold
negative
pressure
led
through
vacuum
tube
and
spring
force
are
applied
to
the
front
surface
of
the
rubber
diaphragm
and
atmospheric
pressure
is
applied
to
the
back
surface
A
difference
between
pressure
applied
to
the
front
and
back
surfaces
be
comes
a
vacuum
reaction
and
thus
the
throttle
valve
of
the
control
valve
inside
the
transmission
case
is
op
erated
When
accelerator
pedal
is
fully
de
pressed
and
the
carburetor
is
fully
upened
but
the
engine
speed
is
not
1
Housing
2
Cover
3
Outer
gear
AT071
4
Inner
gear
5
Crescent
Fig
AT
3
Oil
pump
1
Manual
plate
2
Inhibitor
switch
A
TOB7
3
Parking
rod
4
Manual
shaft
Fig
AT
4
Manuallinhage
To
intake
manifold
A
TOBB
Fig
A
T
5
Vacuum
diaphragm
iV
Down
shift
solenoid
i
KiCk
down
switch
A
TOB9
Fig
A
T
6
Downshift
solenoid
AT
5
sufficiently
increased
the
manifold
negative
pressure
lowers
becomes
similar
to
the
atmospheric
pressure
and
the
vacuum
reaction
increases
since
the
flow
velocity
of
mixture
inside
the
intake
manifold
is
slow
Contrarily
when
the
engine
speed
increases
and
the
flow
velocity
of
the
mixture
increases
or
when
the
carbure
tor
is
closed
the
manifold
negative
pressure
increases
becomes
similar
to
vacuum
and
the
vacuum
reaction
reduces
Thus
a
signal
to
generate
hydraulic
pressure
completely
suited
to
the
engine
loading
at
the
control
valve
is
transmitted
from
the
vacuum
dia
phragm
and
most
suitable
speed
change
timing
and
line
pressure
are
obtained
so
that
the
most
proper
torque
capacity
is
obtained
against
the
transmitting
torque
Downshift
solenoid
The
downshift
solenoid
is
of
a
magnetic
type
installed
on
the
left
rear
portion
of
the
transmiSsion
case
When
a
driver
requires
accelerating
power
and
depresses
the
accelerator
pedal
down
to
the
stopper
a
kick
down
switch
located
in
the
middle
of
the
accelerator
link
is
depressed
by
a
push
rod
the
kick
down
switch
closes
cur
rent
flows
to
the
solenoid
the
sole
noid
push
rod
is
depressed
the
down
shift
valve
of
the
control
valve
inside
the
transmission
case
is
depressed
and
the
speed
is
changed
forcedly
from
3rd
to
2nd
within
a
certain
vehi
cle
speed
limit
Note
As
the
kick
own
switch
closes
when
the
accelerator
pedal
is
depressed
from
7
8
to
IS
16
of
the
whole
stroke
the
accelera
tor
pedal
should
be
correctly
adjusted
and
fixed
so
as
to
afford
complete
stroke
The
arrangement
of
the
switch
differs
according
the
models
of
vehicle
Governor
valve
The
primary
and
secondary
gover
nor
valves
are
installed
separately
on
the
back
of
the
oil
distributor
on
the
Page 8 of 513
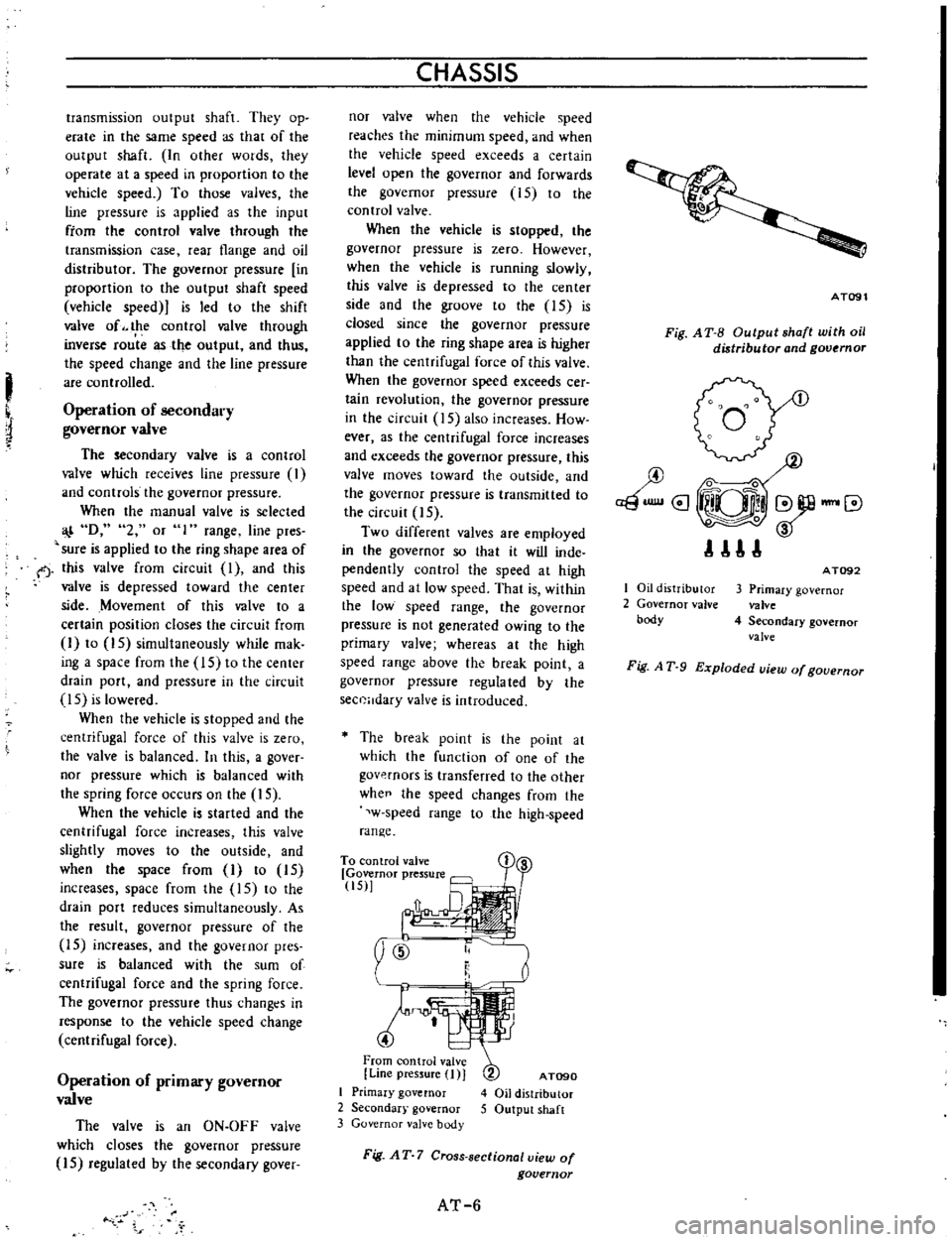
I
transmission
output
shaft
They
op
erate
in
the
same
speed
as
that
of
the
output
shaft
In
other
wotds
they
operate
at
a
speed
in
proportion
to
the
vehicle
speed
To
those
valves
the
line
pressure
is
applied
as
the
input
ftom
the
control
valve
through
the
transmission
case
rear
flange
and
oil
distributor
The
governor
pressure
in
proportion
to
the
output
shaft
speed
vehicle
speed
is
led
to
the
shift
valve
of
the
control
valve
through
inverse
rou
te
as
the
output
and
thus
the
speed
change
and
the
line
pressure
are
controlled
Operation
of
secondary
governor
valve
The
secondary
valve
is
a
control
valve
which
receives
line
pressure
I
and
controls
the
governor
pressure
When
the
manual
valve
is
selected
D
2
or
1
range
line
pres
sure
is
applied
to
the
ring
shape
area
of
f
this
valve
from
circuit
I
and
this
valve
is
depressed
toward
the
center
side
Movement
of
this
valve
to
a
certain
position
closes
the
circuit
from
I
to
15
simultaneously
while
mak
ing
a
space
from
the
15
to
the
center
drain
port
and
pressure
in
the
circuit
IS
is
lowered
When
the
vehicle
is
stopped
and
the
centrifugal
force
of
this
valve
is
zero
the
valve
is
balanced
In
this
a
gover
nor
pressure
which
is
balanced
with
the
spring
force
occurs
on
the
15
When
the
vehicle
is
started
and
the
centrifugal
force
increases
this
valve
slightly
moves
to
the
outside
and
when
the
space
from
I
to
15
increases
space
from
the
15
to
the
drain
port
reduces
simultaneously
As
the
result
governor
pressure
of
the
15
increases
and
the
governor
pres
sure
is
balanced
with
the
sum
of
centrifugal
force
and
the
spring
force
The
governor
pressure
thus
changt
s
in
response
to
the
vehicle
speed
change
centrifugal
force
Operation
of
primary
governor
valve
The
valve
is
an
ON
OFF
valve
which
closes
the
governor
pressure
15
regulated
by
the
secondary
gover
CHASSIS
nor
valve
when
the
vehicle
speed
reaches
the
minimum
speed
and
when
the
vehicle
speed
exceeds
a
certain
level
open
the
governor
and
forwards
the
governor
pressure
15
to
the
control
valve
When
the
vehicle
is
stopped
the
governor
pressure
is
zero
However
when
the
vehicle
is
running
slowly
this
valve
is
depressed
to
the
center
side
and
the
groove
to
the
IS
is
closed
since
the
governor
pressure
applied
to
the
ring
shape
area
is
higher
than
the
centrifugal
force
of
this
valve
When
the
governor
speed
exceeds
cer
tain
revolution
the
governor
pressure
in
the
circuit
15
also
increases
How
ever
as
the
centrifugal
force
increases
and
exceeds
the
governor
pressure
this
valve
moves
toward
the
outside
and
the
governor
pressure
is
transmitted
to
the
circuit
15
Two
different
valves
are
employed
in
the
governor
so
that
it
will
inde
pendently
control
the
speed
at
high
speed
and
at
low
speed
That
is
within
the
low
speed
range
the
governor
pressure
is
not
generated
owing
to
the
primary
valve
whereas
at
the
high
speed
range
above
the
break
point
a
governor
pressure
regula
ted
by
the
sec0Hdary
valve
is
introduced
The
break
point
is
the
point
at
which
the
function
of
one
of
the
govp
rnors
is
transferred
to
the
other
whee
the
speed
changes
from
the
w
speed
range
to
the
high
speed
range
To
con
trol
valve
Governor
pressure
tiS
y
ID
t
4
From
control
valve
Line
pressure
I
J
I
Primary
governor
2
Secondar
governor
3
Governor
valve
body
AT090
4
Oil
distributor
5
Output
shaft
Fig
AT
7
Cross
sectional
view
of
governor
AT
6
AT091
Fig
A
T
B
Output
shaft
with
oil
distributor
and
governor
I
Oil
distributor
2
Governor
valve
body
AT092
3
Primary
governor
valve
4
Secondary
governor
valve
Fig
A
T
9
Exploded
uiew
of
gouernor