Page 1545 of 2339
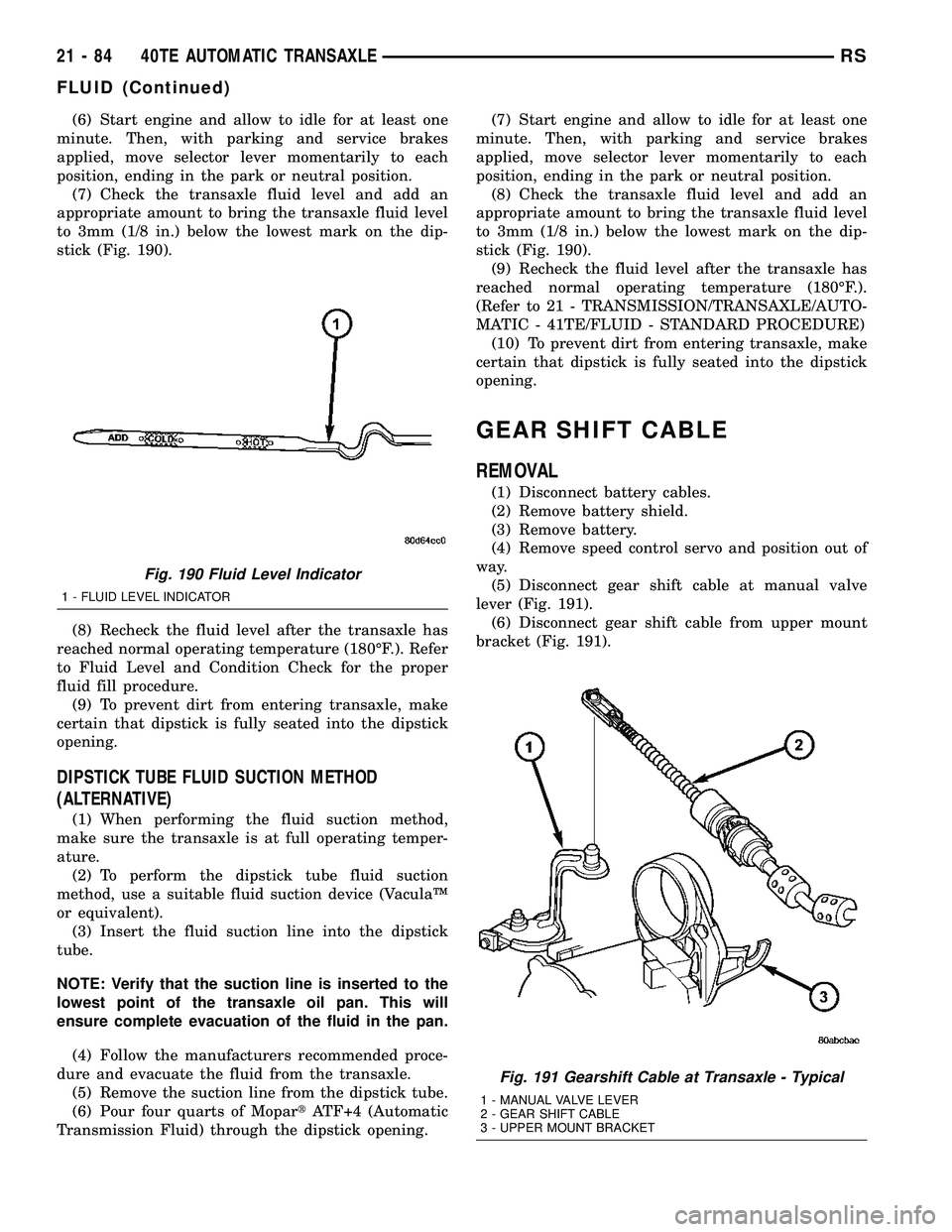
(6) Start engine and allow to idle for at least one
minute. Then, with parking and service brakes
applied, move selector lever momentarily to each
position, ending in the park or neutral position.
(7) Check the transaxle fluid level and add an
appropriate amount to bring the transaxle fluid level
to 3mm (1/8 in.) below the lowest mark on the dip-
stick (Fig. 190).
(8) Recheck the fluid level after the transaxle has
reached normal operating temperature (180ÉF.). Refer
to Fluid Level and Condition Check for the proper
fluid fill procedure.
(9) To prevent dirt from entering transaxle, make
certain that dipstick is fully seated into the dipstick
opening.
DIPSTICK TUBE FLUID SUCTION METHOD
(ALTERNATIVE)
(1) When performing the fluid suction method,
make sure the transaxle is at full operating temper-
ature.
(2) To perform the dipstick tube fluid suction
method, use a suitable fluid suction device (VaculaŸ
or equivalent).
(3) Insert the fluid suction line into the dipstick
tube.
NOTE: Verify that the suction line is inserted to the
lowest point of the transaxle oil pan. This will
ensure complete evacuation of the fluid in the pan.
(4) Follow the manufacturers recommended proce-
dure and evacuate the fluid from the transaxle.
(5) Remove the suction line from the dipstick tube.
(6) Pour four quarts of MopartATF+4 (Automatic
Transmission Fluid) through the dipstick opening.(7) Start engine and allow to idle for at least one
minute. Then, with parking and service brakes
applied, move selector lever momentarily to each
position, ending in the park or neutral position.
(8) Check the transaxle fluid level and add an
appropriate amount to bring the transaxle fluid level
to 3mm (1/8 in.) below the lowest mark on the dip-
stick (Fig. 190).
(9) Recheck the fluid level after the transaxle has
reached normal operating temperature (180ÉF.).
(Refer to 21 - TRANSMISSION/TRANSAXLE/AUTO-
MATIC - 41TE/FLUID - STANDARD PROCEDURE)
(10) To prevent dirt from entering transaxle, make
certain that dipstick is fully seated into the dipstick
opening.
GEAR SHIFT CABLE
REMOVAL
(1) Disconnect battery cables.
(2) Remove battery shield.
(3) Remove battery.
(4) Remove speed control servo and position out of
way.
(5) Disconnect gear shift cable at manual valve
lever (Fig. 191).
(6) Disconnect gear shift cable from upper mount
bracket (Fig. 191).
Fig. 190 Fluid Level Indicator
1 - FLUID LEVEL INDICATOR
Fig. 191 Gearshift Cable at Transaxle - Typical
1 - MANUAL VALVE LEVER
2 - GEAR SHIFT CABLE
3 - UPPER MOUNT BRACKET
21 - 84 40TE AUTOMATIC TRANSAXLERS
FLUID (Continued)
Page 1546 of 2339
(7) Remove instrument panel lower silencer (Fig.
192).
(8) Remove knee bolster (Fig. 193).
(9) Disconnect gear shift cable from gear shift
lever (Fig. 194).
(10) Remove gear shift cable from column bracket
(Fig. 194).
(11) Disengage grommet from dash panel (Fig.
195) and remove gear shift cable from inside vehicle.
Fig. 192 Instrument Panel Lower Silencer
1 - INSTRUMENT PANEL LOWER SILENCER
Fig. 193 Knee Bolster
1 - KNEE BOLSTER
Fig. 194 Gearshift Cable at Column
1 - GEAR SHIFT CABLE
Fig. 195 Gearshift Cable/Grommet at Dash Panel
1 - CABLE GROMMET
2 - DASH PANEL
RS40TE AUTOMATIC TRANSAXLE21-85
GEAR SHIFT CABLE (Continued)
Page 1547 of 2339
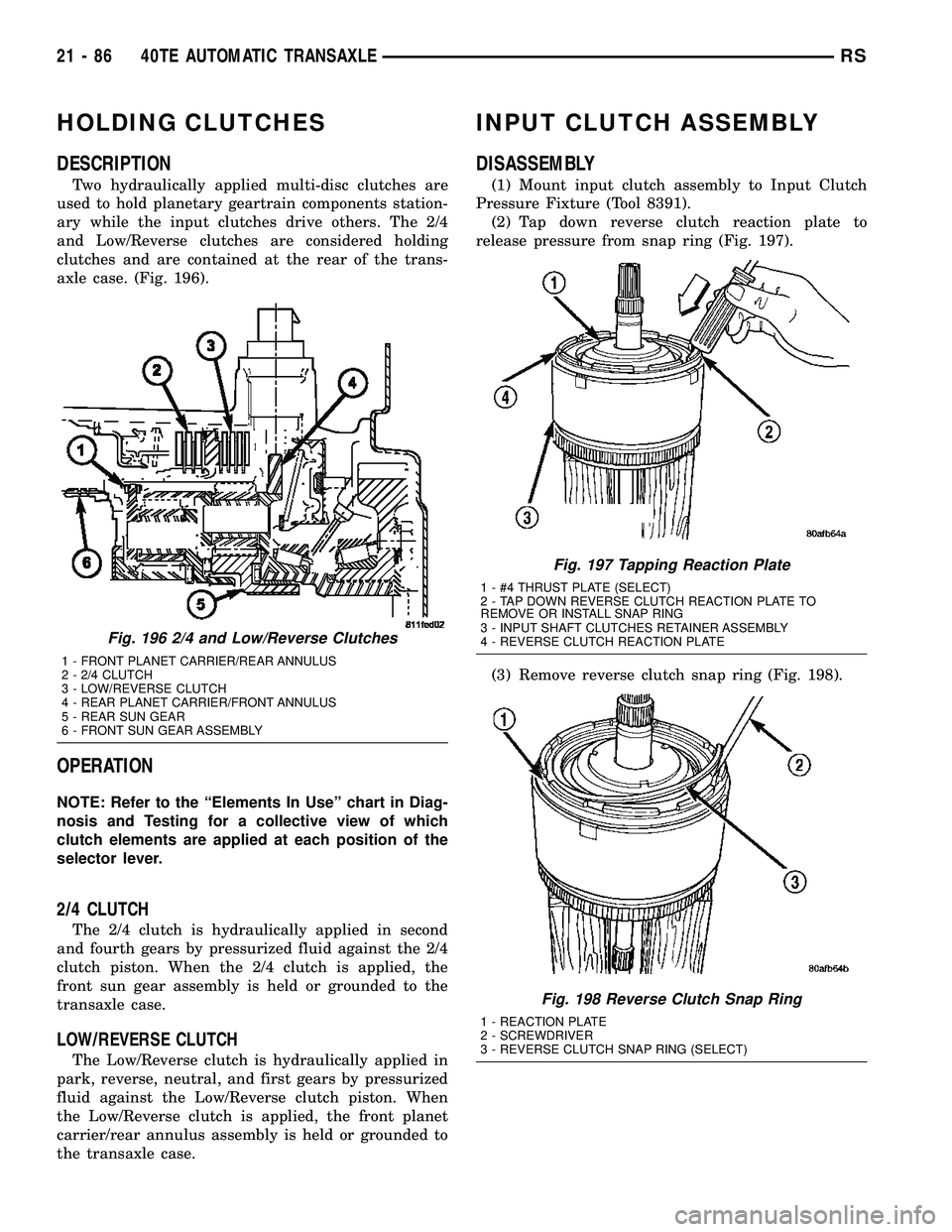
HOLDING CLUTCHES
DESCRIPTION
Two hydraulically applied multi-disc clutches are
used to hold planetary geartrain components station-
ary while the input clutches drive others. The 2/4
and Low/Reverse clutches are considered holding
clutches and are contained at the rear of the trans-
axle case. (Fig. 196).
OPERATION
NOTE: Refer to the ªElements In Useº chart in Diag-
nosis and Testing for a collective view of which
clutch elements are applied at each position of the
selector lever.
2/4 CLUTCH
The 2/4 clutch is hydraulically applied in second
and fourth gears by pressurized fluid against the 2/4
clutch piston. When the 2/4 clutch is applied, the
front sun gear assembly is held or grounded to the
transaxle case.
LOW/REVERSE CLUTCH
The Low/Reverse clutch is hydraulically applied in
park, reverse, neutral, and first gears by pressurized
fluid against the Low/Reverse clutch piston. When
the Low/Reverse clutch is applied, the front planet
carrier/rear annulus assembly is held or grounded to
the transaxle case.
INPUT CLUTCH ASSEMBLY
DISASSEMBLY
(1) Mount input clutch assembly to Input Clutch
Pressure Fixture (Tool 8391).
(2) Tap down reverse clutch reaction plate to
release pressure from snap ring (Fig. 197).
(3) Remove reverse clutch snap ring (Fig. 198).
Fig. 196 2/4 and Low/Reverse Clutches
1 - FRONT PLANET CARRIER/REAR ANNULUS
2 - 2/4 CLUTCH
3 - LOW/REVERSE CLUTCH
4 - REAR PLANET CARRIER/FRONT ANNULUS
5 - REAR SUN GEAR
6 - FRONT SUN GEAR ASSEMBLY
Fig. 197 Tapping Reaction Plate
1 - #4 THRUST PLATE (SELECT)
2 - TAP DOWN REVERSE CLUTCH REACTION PLATE TO
REMOVE OR INSTALL SNAP RING
3 - INPUT SHAFT CLUTCHES RETAINER ASSEMBLY
4 - REVERSE CLUTCH REACTION PLATE
Fig. 198 Reverse Clutch Snap Ring
1 - REACTION PLATE
2 - SCREWDRIVER
3 - REVERSE CLUTCH SNAP RING (SELECT)
21 - 86 40TE AUTOMATIC TRANSAXLERS
Page 1548 of 2339
(4) Pry up and remove reverse clutch reaction
plate (Fig. 199).
(5) Remove reverse clutch pack (Fig. 200).Ta g
components for assembly identification.
Fig. 199 Pry Reverse Clutch Reaction Plate
1 - REVERSE CLUTCH REACTION PLATE
2 - SCREWDRIVER
3 - SCREWDRIVER
Fig. 200 Reverse Clutch Assembly
1 - SNAP RING
2 - REACTION PLATE
3 - CLUTCH DISC (2)4 - CLUTCH PLATE (1)
5 - INPUT CLUTCH ASSEMBLY
RS40TE AUTOMATIC TRANSAXLE21-87
INPUT CLUTCH ASSEMBLY (Continued)
Page 1549 of 2339
(6) Remove the OD/Reverse pressure plate snap
ring (Fig. 201).
(7) Remove OD/Reverse pressure plate (Fig. 201).
(8) Remove OD/Reverse pressure plate wave snap
ring (Fig. 201).
(9) Remove OD clutch pack (Fig. 201).Tag com-
ponents for assembly identification.
Fig. 201 Overdrive Clutch Assembly
1 - SNAP RING
2 - OD/REVERSE PRESSURE PLATE
3 - SNAP RING (WAVE)4 - CLUTCH DISC (3)
5 - CLUTCH STEEL (2)
6 - INPUT CLUTCH ASSEMBLY
21 - 88 40TE AUTOMATIC TRANSAXLERS
INPUT CLUTCH ASSEMBLY (Continued)
Page 1550 of 2339
(10) Remove and inspect OD and UD Shafts, as
well as #3 thrust washer and plate, and #2 needle
bearing (Fig. 202).
Fig. 202 Overdrive/Underdrive Shafts
1 - OVERDRIVE SHAFT
2 - #3 THRUST PLATE (3 TABS)
3 - #3 THRUST WASHER (5 TABS)4 - UNDERDRIVE SHAFT
5 - #2 NEEDLE BEARING (3 TABS)
6 - INPUT CLUTCH ASSEMBLY
RS40TE AUTOMATIC TRANSAXLE21-89
INPUT CLUTCH ASSEMBLY (Continued)
Page 1551 of 2339
(11) Remove the OD/UD reaction plate tapered
snap ring, reaction plate, and first friction disc (Fig.
203).
(12) Remove the UD clutch flat snap ring and rest
of UD clutch pack (Fig. 203).Tag clutch pack for
assembly identification.
Fig. 203 Underdrive Clutch Assembly
1 - SNAP RING (TAPERED)
2 - OD/UD REACTION PLATE
3 - CLUTCH DISC (3)4 - SNAP RING (FLAT)
5 - CLUTCH PLATE (3)
6 - INPUT CLUTCH ASSEMBLY
21 - 90 40TE AUTOMATIC TRANSAXLERS
INPUT CLUTCH ASSEMBLY (Continued)
Page 1552 of 2339
CAUTION: Compress return spring just enough to
remove or install snap ring.
(13) Using Tool 5059A and an arbor press, com-
press UD clutch piston/spring enough to remove snap
ring (Fig. 204) (Fig. 205).
(14) Remove spring retainer, spring, and piston
(Fig. 205).
Fig. 204 UD Spring Retainer Snap Ring
1 - SNAP RING PLIERS
2 - ARBOR PRESS RAM
3 - SNAP RING
4 - SPECIAL TOOL 5059A
Fig. 205 Underdrive Clutch Piston, Spring and Retainer
1 - SNAP RING
2 - SPRING RETAINER
3 - SPRING
4 - UD CLUTCH PISTON5 - SEAL, OUTER
6 - SEAL, INNER
7 - INPUT CLUTCH ASSEMBLY
RS40TE AUTOMATIC TRANSAXLE21-91
INPUT CLUTCH ASSEMBLY (Continued)