Page 1009 of 1463
5A-32 AUTOMATIC TRANSMISSION
Figure 3.7 - Hydraulic Control Circuit
Page 1010 of 1463
AUTOMATIC TRANSMISSION 5A-33
Figure 3.8 - Valve Body
Figure 3.9 - Pump Cover
Valve Body
Figure 3.8 depicts the valve body as a unit as viewed from the
transmission sump. Figure 3.9 depicts the pump cover.
Page 1011 of 1463
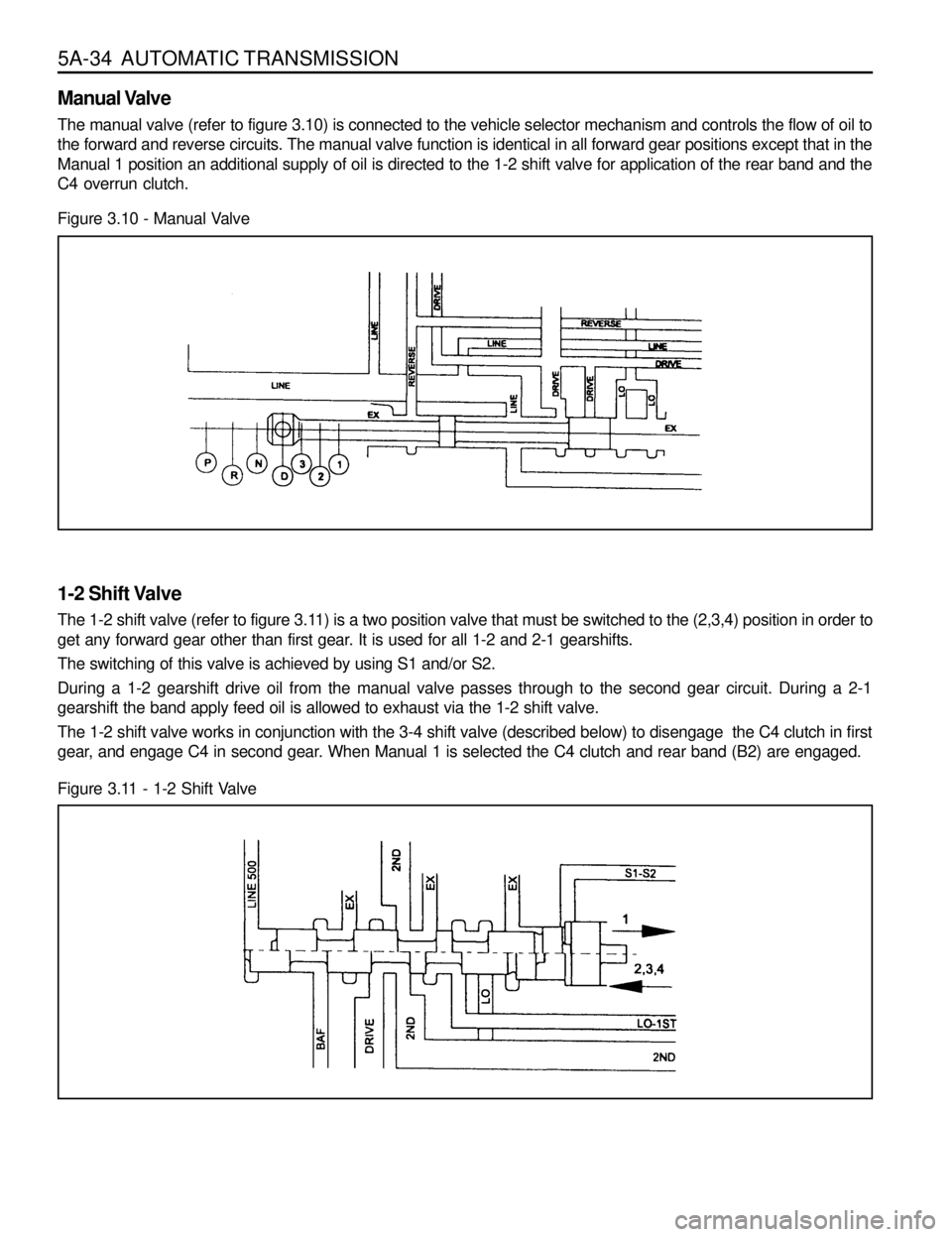
5A-34 AUTOMATIC TRANSMISSION
Figure 3.10 - Manual Valve
1-2 Shift Valve
The 1-2 shift valve (refer to figure 3.11) is a two position valve that must be switched to the (2,3,4) position in order to
get any forward gear other than first gear. It is used for all 1-2 and 2-1 gearshifts.
The switching of this valve is achieved by using S1 and/or S2.
During a 1-2 gearshift drive oil from the manual valve passes through to the second gear circuit. During a 2-1
gearshift the band apply feed oil is allowed to exhaust via the 1-2 shift valve.
The 1-2 shift valve works in conjunction with the 3-4 shift valve (described below) to disengage the C4 clutch in first
gear, and engage C4 in second gear. When Manual 1 is selected the C4 clutch and rear band (B2) are engaged.
Figure 3.11 - 1-2 Shift Valve
Manual Valve
The manual valve (refer to figure 3.10) is connected to the vehicle selector mechanism and controls the flow of oil to
the forward and reverse circuits. The manual valve function is identical in all forward gear positions except that in the
Manual 1 position an additional supply of oil is directed to the 1-2 shift valve for application of the rear band and the
C4 overrun clutch.
Page 1012 of 1463
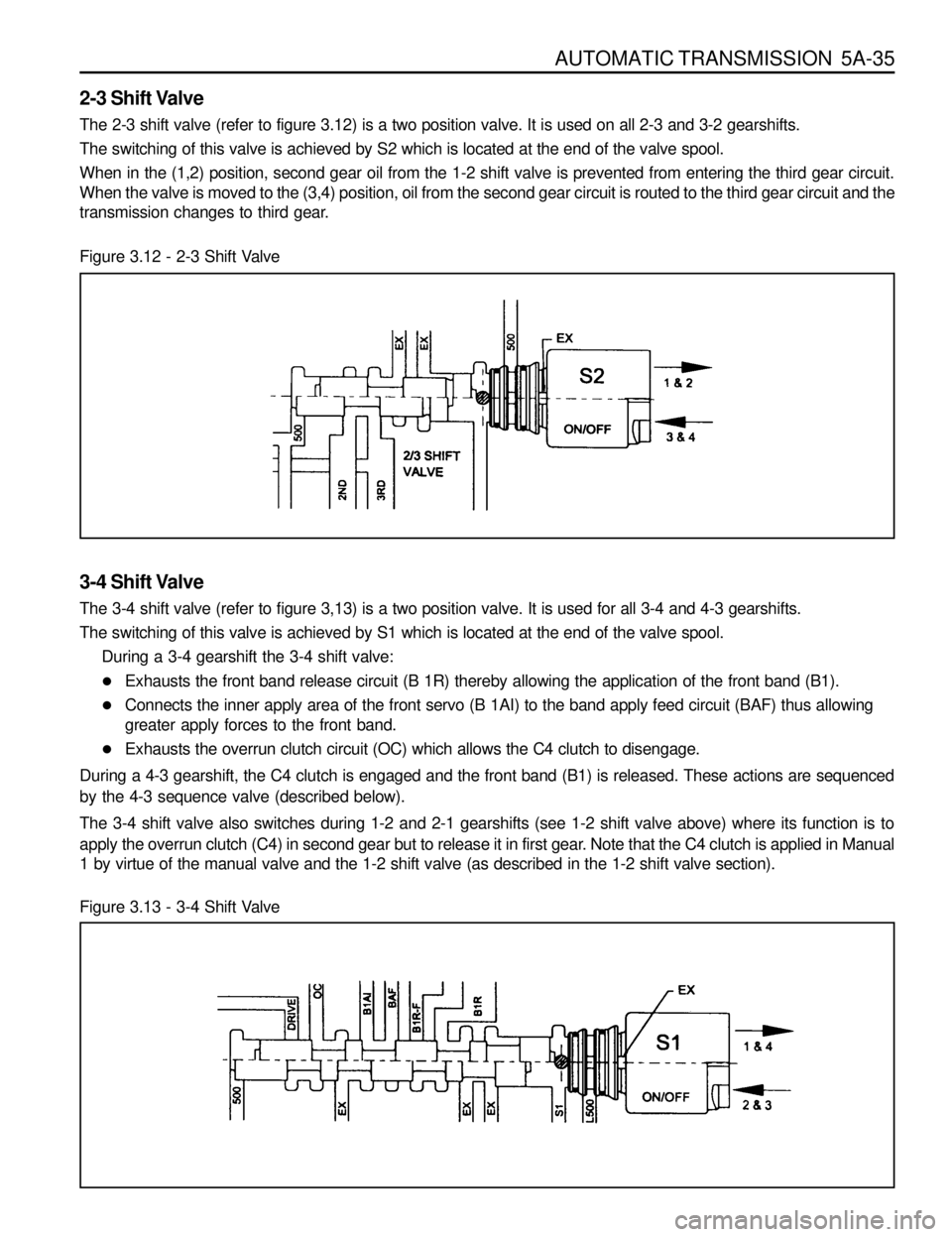
AUTOMATIC TRANSMISSION 5A-35
2-3 Shift Valve
The 2-3 shift valve (refer to figure 3.12) is a two position valve. It is used on all 2-3 and 3-2 gearshifts.
The switching of this valve is achieved by S2 which is located at the end of the valve spool.
When in the (1,2) position, second gear oil from the 1-2 shift valve is prevented from entering the third gear circuit.
When the valve is moved to the (3,4) position, oil from the second gear circuit is routed to the third gear circuit and the
transmission changes to third gear.
Figure 3.12 - 2-3 Shift Valve
3-4 Shift Valve
The 3-4 shift valve (refer to figure 3,13) is a two position valve. It is used for all 3-4 and 4-3 gearshifts.
The switching of this valve is achieved by S1 which is located at the end of the valve spool.
During a 3-4 gearshift the 3-4 shift valve:
lExhausts the front band release circuit (B 1R) thereby allowing the application of the front band (B1).
lConnects the inner apply area of the front servo (B 1AI) to the band apply feed circuit (BAF) thus allowing
greater apply forces to the front band.
lExhausts the overrun clutch circuit (OC) which allows the C4 clutch to disengage.
During a 4-3 gearshift, the C4 clutch is engaged and the front band (B1) is released. These actions are sequenced
by the 4-3 sequence valve (described below).
The 3-4 shift valve also switches during 1-2 and 2-1 gearshifts (see 1-2 shift valve above) where its function is to
apply the overrun clutch (C4) in second gear but to release it in first gear. Note that the C4 clutch is applied in Manual
1 by virtue of the manual valve and the 1-2 shift valve (as described in the 1-2 shift valve section).
Figure 3.13 - 3-4 Shift Valve
Page 1013 of 1463
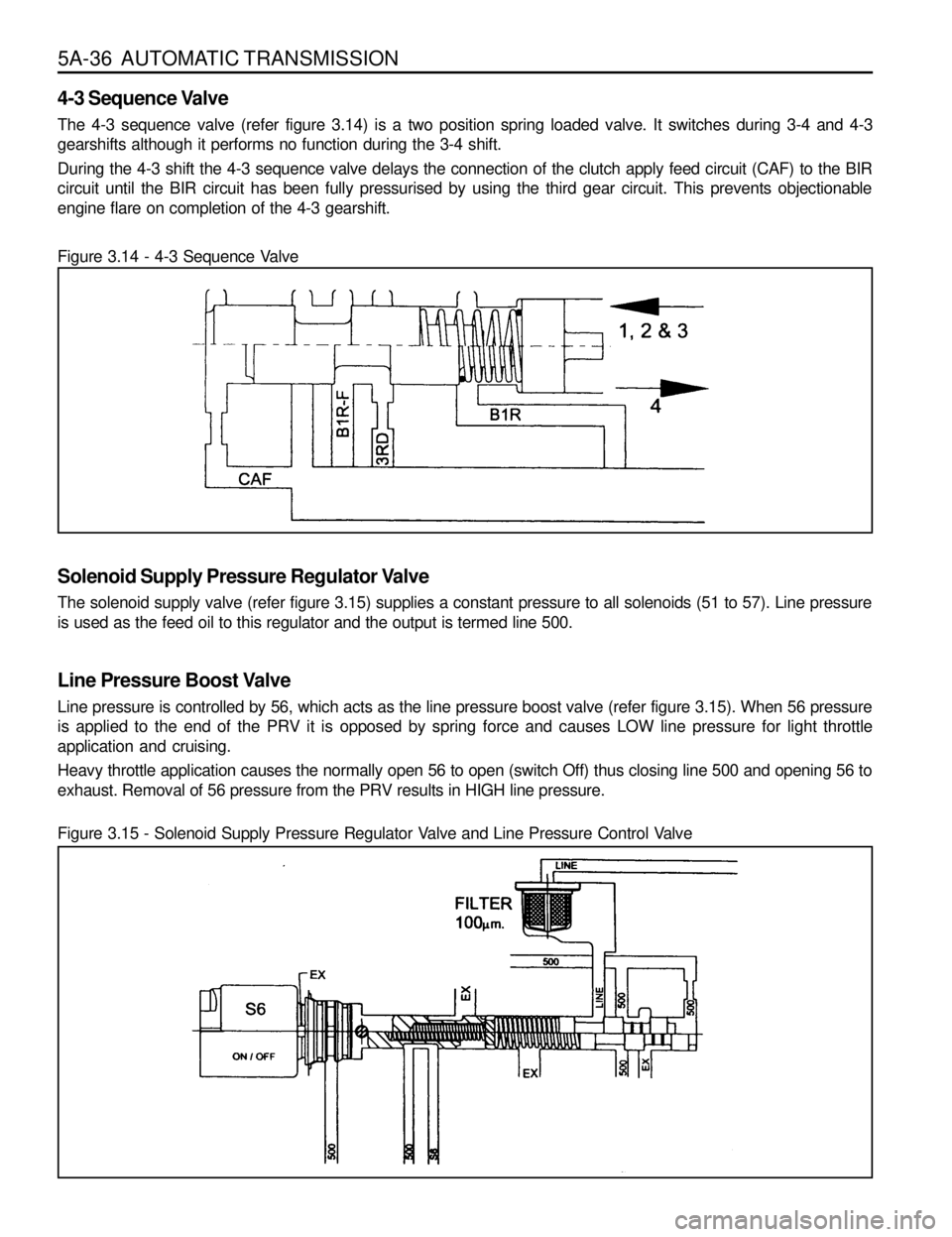
5A-36 AUTOMATIC TRANSMISSION
4-3 Sequence Valve
The 4-3 sequence valve (refer figure 3.14) is a two position spring loaded valve. It switches during 3-4 and 4-3
gearshifts although it performs no function during the 3-4 shift.
During the 4-3 shift the 4-3 sequence valve delays the connection of the clutch apply feed circuit (CAF) to the BIR
circuit until the BIR circuit has been fully pressurised by using the third gear circuit. This prevents objectionable
engine flare on completion of the 4-3 gearshift.
Figure 3.14 - 4-3 Sequence Valve
Figure 3.15 - Solenoid Supply Pressure Regulator Valve and Line Pressure Control Valve
Solenoid Supply Pressure Regulator Valve
The solenoid supply valve (refer figure 3.15) supplies a constant pressure to all solenoids (51 to 57). Line pressure
is used as the feed oil to this regulator and the output is termed line 500.
Line Pressure Boost Valve
Line pressure is controlled by 56, which acts as the line pressure boost valve (refer figure 3.15). When 56 pressure
is applied to the end of the PRV it is opposed by spring force and causes LOW line pressure for light throttle
application and cruising.
Heavy throttle application causes the normally open 56 to open (switch Off) thus closing line 500 and opening 56 to
exhaust. Removal of 56 pressure from the PRV results in HIGH line pressure.
Page 1014 of 1463
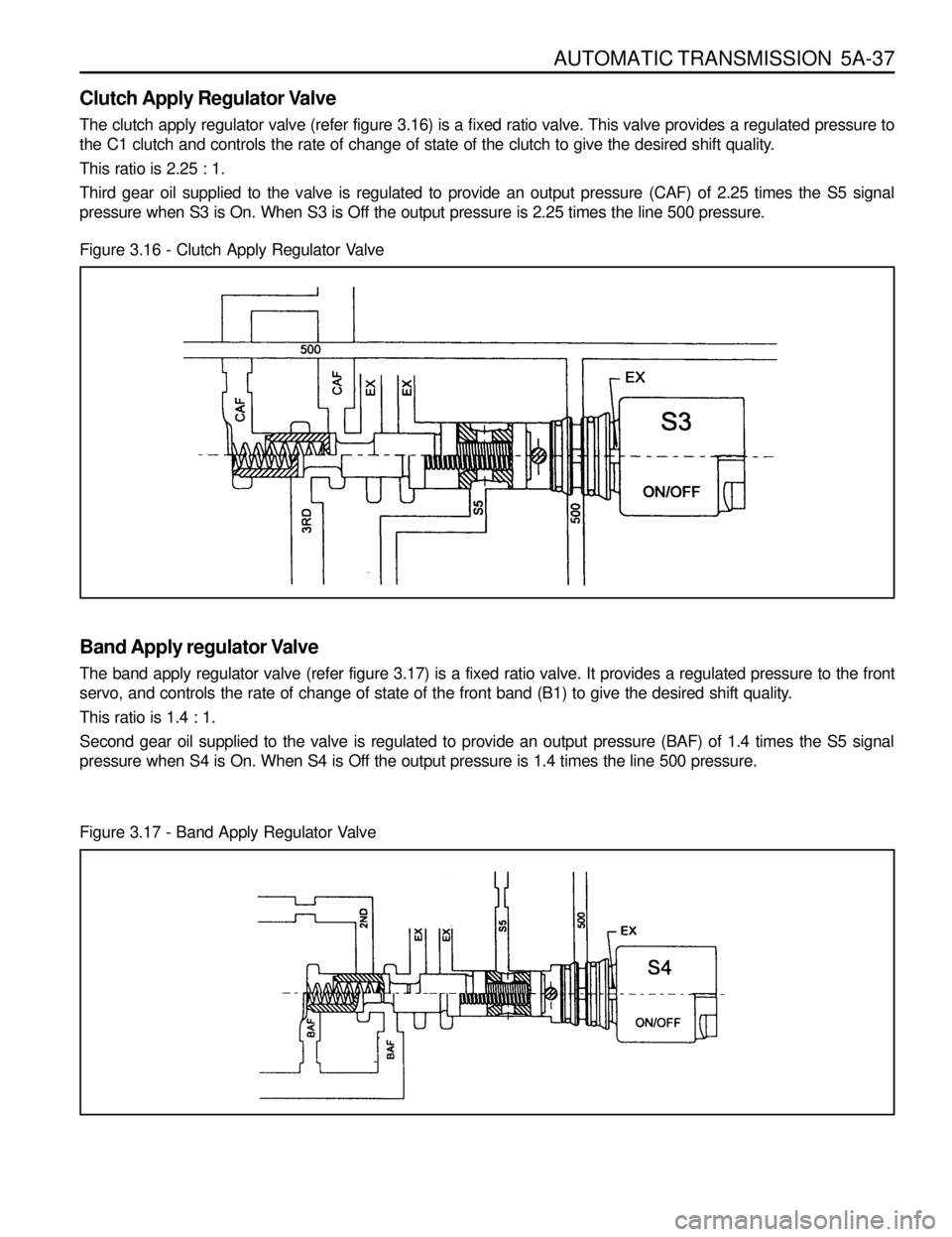
AUTOMATIC TRANSMISSION 5A-37
Figure 3.16 - Clutch Apply Regulator Valve
Clutch Apply Regulator Valve
The clutch apply regulator valve (refer figure 3.16) is a fixed ratio valve. This valve provides a regulated pressure to
the C1 clutch and controls the rate of change of state of the clutch to give the desired shift quality.
This ratio is 2.25 : 1.
Third gear oil supplied to the valve is regulated to provide an output pressure (CAF) of 2.25 times the S5 signal
pressure when S3 is On. When S3 is Off the output pressure is 2.25 times the line 500 pressure.
Band Apply regulator Valve
The band apply regulator valve (refer figure 3.17) is a fixed ratio valve. It provides a regulated pressure to the front
servo, and controls the rate of change of state of the front band (B1) to give the desired shift quality.
This ratio is 1.4 : 1.
Second gear oil supplied to the valve is regulated to provide an output pressure (BAF) of 1.4 times the S5 signal
pressure when S4 is On. When S4 is Off the output pressure is 1.4 times the line 500 pressure.
Figure 3.17 - Band Apply Regulator Valve
Page 1015 of 1463
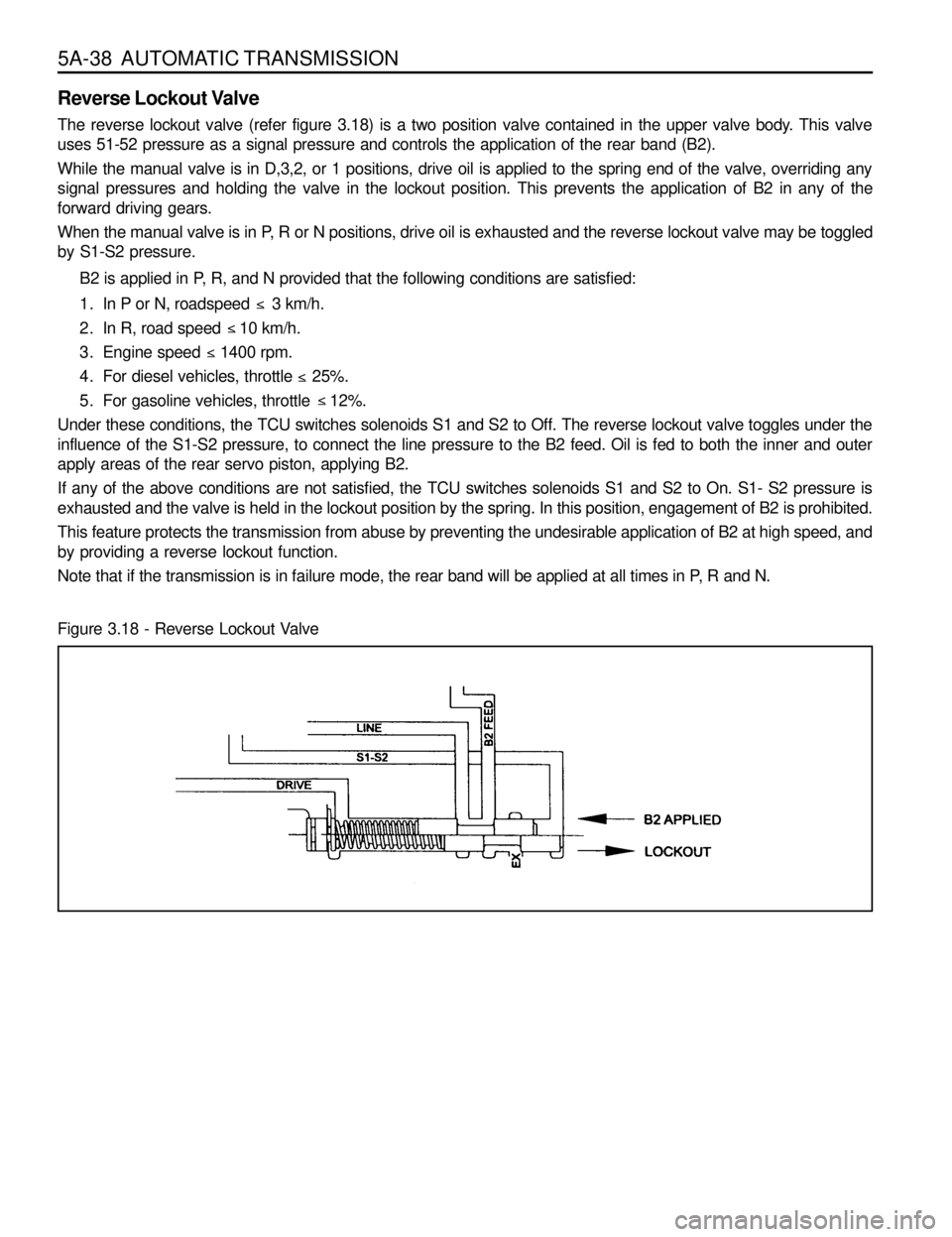
5A-38 AUTOMATIC TRANSMISSION
Reverse Lockout Valve
The reverse lockout valve (refer figure 3.18) is a two position valve contained in the upper valve body. This valve
uses 51-52 pressure as a signal pressure and controls the application of the rear band (B2).
While the manual valve is in D,3,2, or 1 positions, drive oil is applied to the spring end of the valve, overriding any
signal pressures and holding the valve in the lockout position. This prevents the application of B2 in any of the
forward driving gears.
When the manual valve is in P, R or N positions, drive oil is exhausted and the reverse lockout valve may be toggled
by S1-S2 pressure.
B2 is applied in P, R, and N provided that the following conditions are satisfied:
1. In P or N, roadspeed 3 km/h.
2. In R, road speed 10 km/h.
3. Engine speed 1400 rpm.
4. For diesel vehicles, throttle 25%.
5. For gasoline vehicles, throttle 12%.
Under these conditions, the TCU switches solenoids S1 and S2 to Off. The reverse lockout valve toggles under the
influence of the S1-S2 pressure, to connect the line pressure to the B2 feed. Oil is fed to both the inner and outer
apply areas of the rear servo piston, applying B2.
If any of the above conditions are not satisfied, the TCU switches solenoids S1 and S2 to On. S1- S2 pressure is
exhausted and the valve is held in the lockout position by the spring. In this position, engagement of B2 is prohibited.
This feature protects the transmission from abuse by preventing the undesirable application of B2 at high speed, and
by providing a reverse lockout function.
Note that if the transmission is in failure mode, the rear band will be applied at all times in P, R and N.
Figure 3.18 - Reverse Lockout Valve
<
<
<
<
<
Page 1016 of 1463
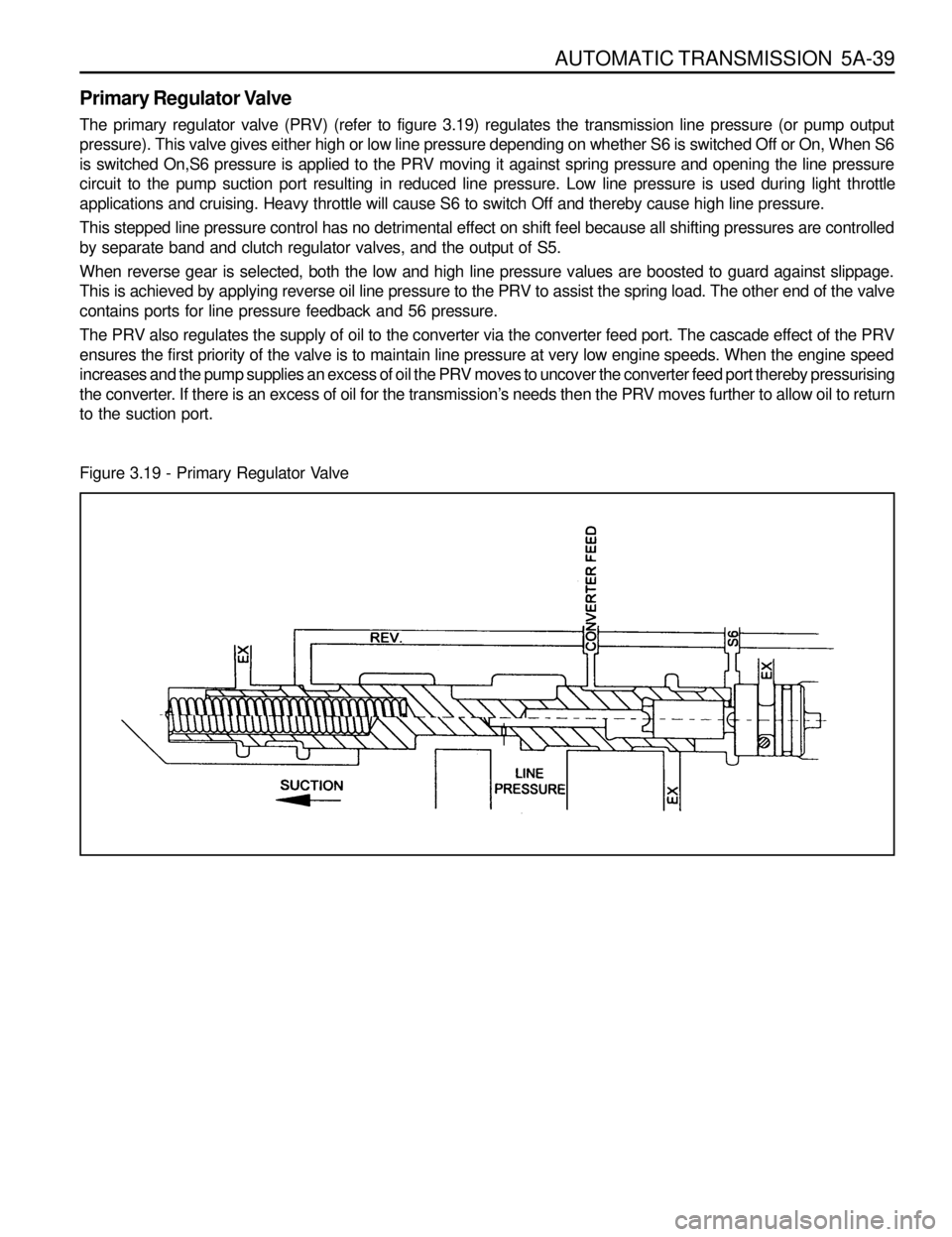
AUTOMATIC TRANSMISSION 5A-39
Primary Regulator Valve
The primary regulator valve (PRV) (refer to figure 3.19) regulates the transmission line pressure (or pump output
pressure). This valve gives either high or low line pressure depending on whether S6 is switched Off or On, When S6
is switched On,S6 pressure is applied to the PRV moving it against spring pressure and opening the line pressure
circuit to the pump suction port resulting in reduced line pressure. Low line pressure is used during light throttle
applications and cruising. Heavy throttle will cause S6 to switch Off and thereby cause high line pressure.
This stepped line pressure control has no detrimental effect on shift feel because all shifting pressures are controlled
by separate band and clutch regulator valves, and the output of S5.
When reverse gear is selected, both the low and high line pressure values are boosted to guard against slippage.
This is achieved by applying reverse oil line pressure to the PRV to assist the spring load. The other end of the valve
contains ports for line pressure feedback and 56 pressure.
The PRV also regulates the supply of oil to the converter via the converter feed port. The cascade effect of the PRV
ensures the first priority of the valve is to maintain line pressure at very low engine speeds. When the engine speed
increases and the pump supplies an excess of oil the PRV moves to uncover the converter feed port thereby pressurising
the converter. If there is an excess of oil for the transmission’s needs then the PRV moves further to allow oil to return
to the suction port.
Figure 3.19 - Primary Regulator Valve