Page 433 of 1463
OM600 ENGINE MECHANICAL 1B3-131
11. The distance ‘x’ (camshaft basic bore - valve stem).
‘x’ = ‘z’ - ‘y’.
Determine the valve to use according to this measurement
(See ‘matching valves’)
Example)Measured value ‘w’ = 38.2 mm
Measured value ‘z’ = 36.5 mm
Value ‘y’ = 15.5 mm
‘x’ = 36.5 - 15.5 = 21.0mm
In this case according to ‘Matching valves’ table, the
installed valve may be used.
Page 434 of 1463
1B3-132 OM600 ENGINE MECHANICAL
MACHINING OF VALVE SEAT
Preceding Work : Removal of prechamber
Removal and inspection of valve, replace if necessary
Inspection of valve guide, replace if necessary
1 Valve
2 Valve Seat Ring
3 Cylinder Head
4 Valve Guidea Valve Seat Angle
b Valve Seat Free Angle
Page 435 of 1463
OM600 ENGINE MECHANICAL 1B3-133
Service Data
Item
Valve Arrears ‘a’
Valve Seat Width ‘b’
Valve Seat Angle ‘
a’
Valve Seat Free Angle ‘
b’
Permissible Radial Runout
Valve Length ‘I’Intake
0.1 - 0.7 mm
1.2 - 1.7 mm
45°
65°
0.03 mm
106.20 - 106.60 mm
105.30 - 105.70 mmExhaust
0.1 - 0.7 mm
1.5 - 2.0 mm
45°
65°
0.03 mm
106.20 - 106.60 mm
105.30 - 105.70 mm
Standard
Repair
w = 38.0 ± 0.2 mm
Matching Valves
Camshaft cam basic dia.
Size (x)
Size (x)
Size (x)19.5 - 20.3mm
20.4 - 21.4mm
21.4 - 21.97mmw = 37.6 ± 0.2 mm Camshaft cam basic dia.
19.5 - 20.1mm
20.2 - 21.2mm
21.2 - 21.97mmValve to be used
Use machined valve,
if needed
use pair valve
1 = 105.5 ± 0.2mm
Reuse valve
Use standard size
valve
I = 106.4 ± 0.2mm
Commercial Tools
Hunger
D-8000 München 70
Type Ventilknecht K2000
Order No. 221 00 100
Hunger
D-8000 München 70
Type VDS 1A
Order No. 236 03 308
Hunger
D-8000 München 70
Order No. 217 93 601 Cylinder Head Clamping Devie
Valve Seat Turning Tool
Test Sat for Valves
Page 436 of 1463
1B3-134 OM600 ENGINE MECHANICAL
Machining Procedure
Valve machining is required :
- When the valve is leaking.
- When replacing the valve.
- When replacing the valve guide.
- When replacing the valve seat or valve seat ring.
1. Machine the valve seat (a=45°).
2. Measure valve seat width ‘b’.
Valve seat
width ‘b’1.2 - 1.7 mm
1.5 - 2.0 mm Intake
Exhaust
3. If the specification is exceeded, the valve seat width has to
be corrected at the lower free angle of ‘
b’=65°.
4. Measure radial runout.
Runout Max. 0.03mm
Page 437 of 1463
OM600 ENGINE MECHANICAL 1B3-135
38 ± 0.2mm
or 37.6 ± 0.2mm
5. Insert the valve (1) into the valve guide according to marking
and measure amount by which the valve arrears ‘a’.
Arrears ‘a’ 0.1 - 0.7mm
6. Measure camshaft cam basic circle diameter (w).
Diameter ‘w’
7. Measure distance ‘z’ (cylinder head cover parting surface
- valve stem).
Page 438 of 1463
1B3-136 OM600 ENGINE MECHANICAL
I Length of Valve
w Camshaft Cam Basic Circle Diameter
x Distance (Camshaft basic bore - valve stem)y Half Camshaft Basic Bore Diameter
z Distance (Cylinder head cover parting surface - .
valve stem)
8. Measure ‘x’ (Camshaft basic bore - valve stem).
‘x’ = ‘z’ - ‘y’
9. Determine the valve to be used.
(See ‘Matching valves’)
Example)Measured value ‘w’ = 38.2 mm
Measured value ‘z’ = 36.5 mm
Value ‘y’ = 15.5 mm
‘x’ = 36.5 - 15.5 = 21.0 mm
In the case of a camshaft cam basic circle diameter
‘w’ = 38.2mm and a distance ‘x’ = 21.0mm, the installed
valve may be used.
Page 439 of 1463
OM600 ENGINE MECHANICAL 1B3-137
CAMSHAFT TIMING TEST
Preceding Work : Removal of glow plug
1 Cylinder Head Cover
2 Bolt............................................................10Nm
3 Gasket ................................................... Replace4 Valve Tappet
5 Cylinder Head
Timing
Condition of camshaft
New
After approx. 20,000kmIntake valve
Open
ATDC 11.33°
ATDC 12°Close
ABDC 17°
ABDC 18°Exhaust valve
Open
BBDC 28°
BBDC 27°Close
BTDC 15.25°
BTDC 14°
«At 2mm of valve lifting stroke.
Page 440 of 1463
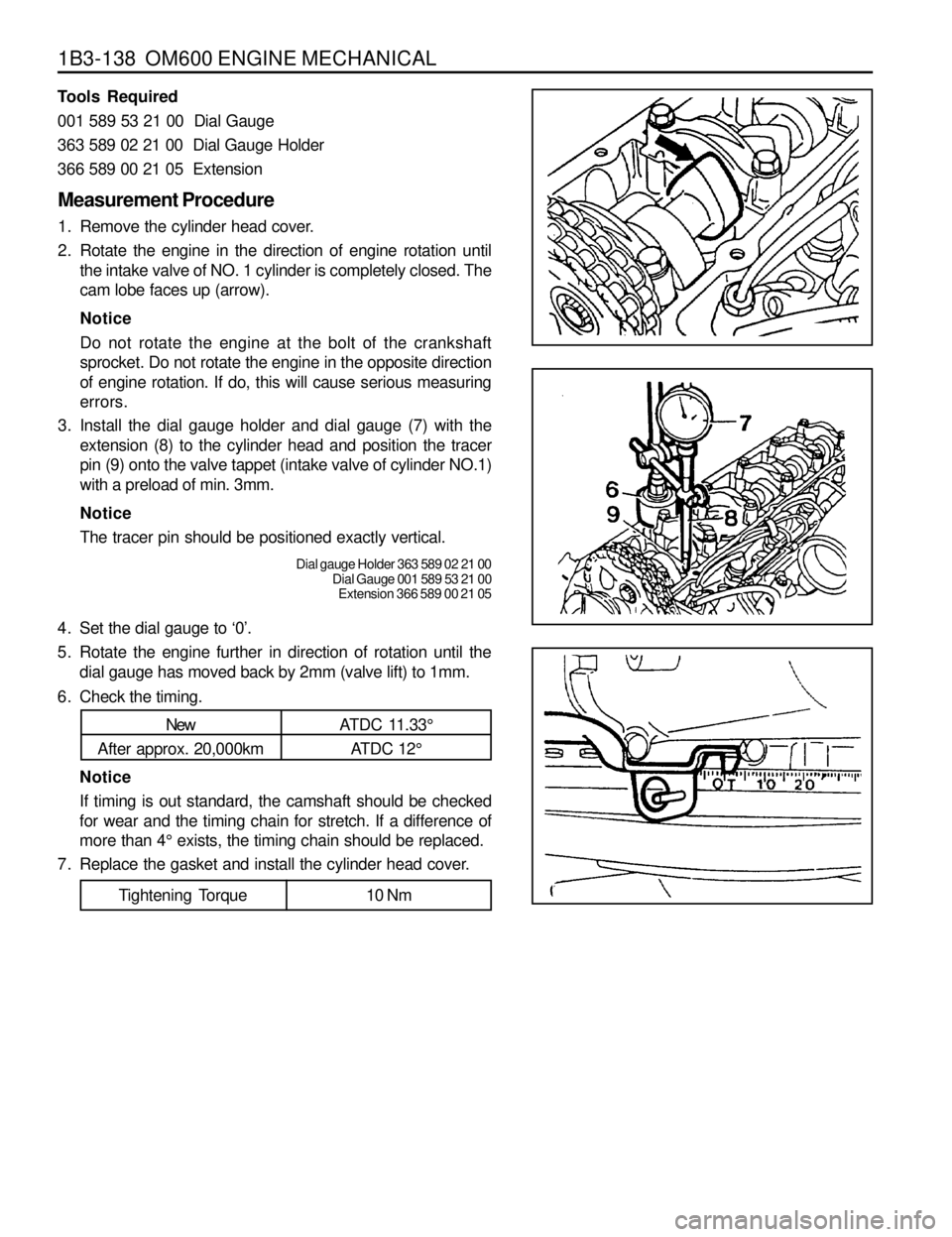
1B3-138 OM600 ENGINE MECHANICAL
6. Check the timing.
New
After approx. 20,000kmATDC 11.33°
ATDC 12°
Notice
If timing is out standard, the camshaft should be checked
for wear and the timing chain for stretch. If a difference of
more than 4° exists, the timing chain should be replaced.
7. Replace the gasket and install the cylinder head cover.
Tightening Torque 10 Nm
Measurement Procedure
1. Remove the cylinder head cover.
2. Rotate the engine in the direction of engine rotation until
the intake valve of NO. 1 cylinder is completely closed. The
cam lobe faces up (arrow).
Notice
Do not rotate the engine at the bolt of the crankshaft
sprocket. Do not rotate the engine in the opposite direction
of engine rotation. If do, this will cause serious measuring
errors.
3. Install the dial gauge holder and dial gauge (7) with the
extension (8) to the cylinder head and position the tracer
pin (9) onto the valve tappet (intake valve of cylinder NO.1)
with a preload of min. 3mm.
Notice
The tracer pin should be positioned exactly vertical.
Dial gauge Holder 363 589 02 21 00
Dial Gauge 001 589 53 21 00
Extension 366 589 00 21 05
4. Set the dial gauge to ‘0’.
5. Rotate the engine further in direction of rotation until the
dial gauge has moved back by 2mm (valve lift) to 1mm.
Tools Required
001 589 53 21 00 Dial Gauge
363 589 02 21 00 Dial Gauge Holder
366 589 00 21 05 Extension