Page 1209 of 1463
5D2-2 TRANSFER CASE (TOD)
SCHEMATIC AND ROUTING DIAGRAMS
TOD
Page 1210 of 1463
TRANSFER CASE (TOD) 5D2-3
T.C.C.U
Page 1211 of 1463
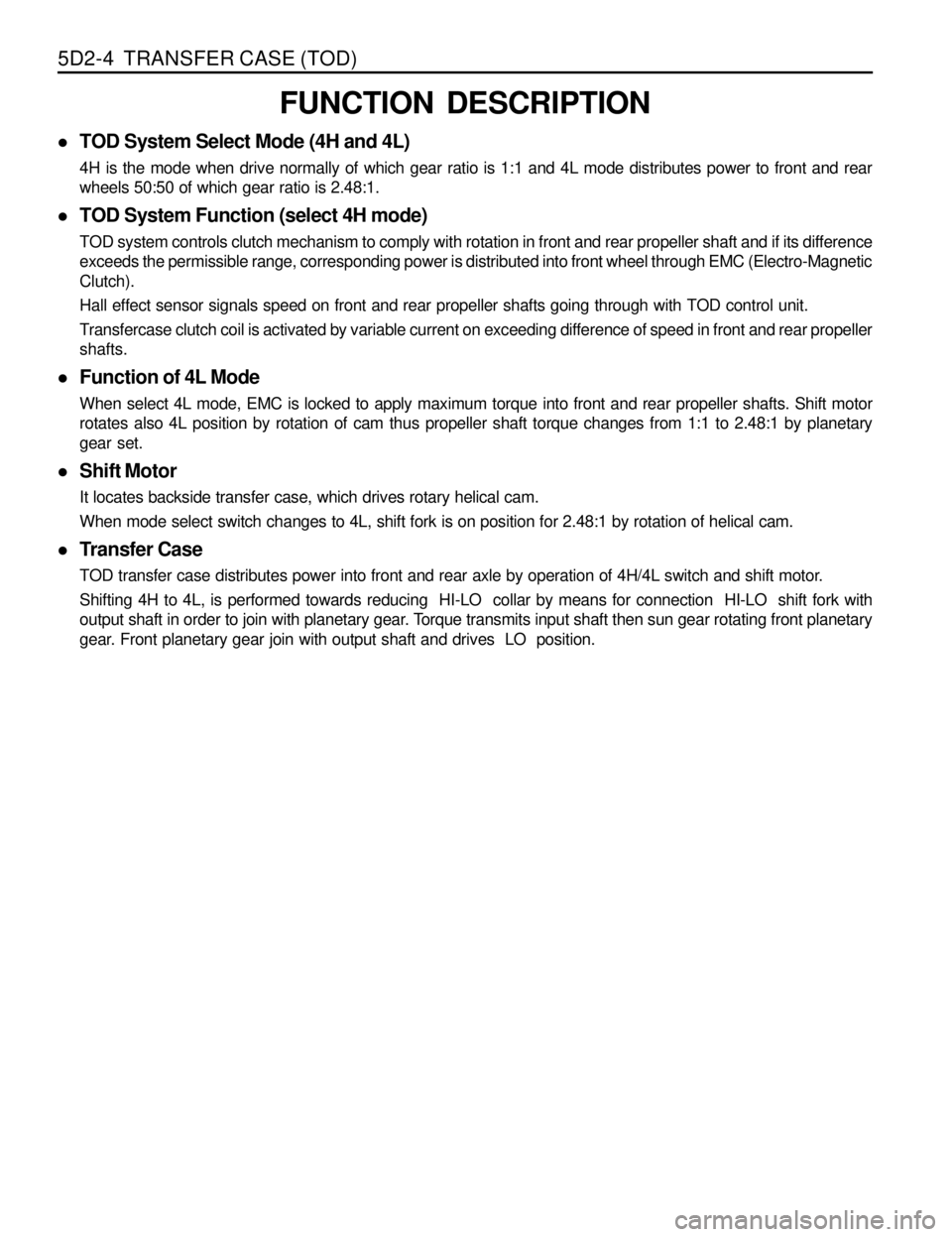
5D2-4 TRANSFER CASE (TOD)
FUNCTION DESCRIPTION
lTOD System Select Mode (4H and 4L)
4H is the mode when drive normally of which gear ratio is 1:1 and 4L mode distributes power to front and rear
wheels 50:50 of which gear ratio is 2.48:1.
lTOD System Function (select 4H mode)
TOD system controls clutch mechanism to comply with rotation in front and rear propeller shaft and if its difference
exceeds the permissible range, corresponding power is distributed into front wheel through EMC (Electro-Magnetic
Clutch).
Hall effect sensor signals speed on front and rear propeller shafts going through with TOD control unit.
Transfercase clutch coil is activated by variable current on exceeding difference of speed in front and rear propeller
shafts.
lFunction of 4L Mode
When select 4L mode, EMC is locked to apply maximum torque into front and rear propeller shafts. Shift motor
rotates also 4L position by rotation of cam thus propeller shaft torque changes from 1:1 to 2.48:1 by planetary
gear set.
lShift Motor
It locates backside transfer case, which drives rotary helical cam.
When mode select switch changes to 4L, shift fork is on position for 2.48:1 by rotation of helical cam.
lTransfer Case
TOD transfer case distributes power into front and rear axle by operation of 4H/4L switch and shift motor.
Shifting 4H to 4L, is performed towards reducing HI-LO collar by means for connection HI-LO shift fork with
output shaft in order to join with planetary gear. Torque transmits input shaft then sun gear rotating front planetary
gear. Front planetary gear join with output shaft and drives LO position.
Page 1212 of 1463
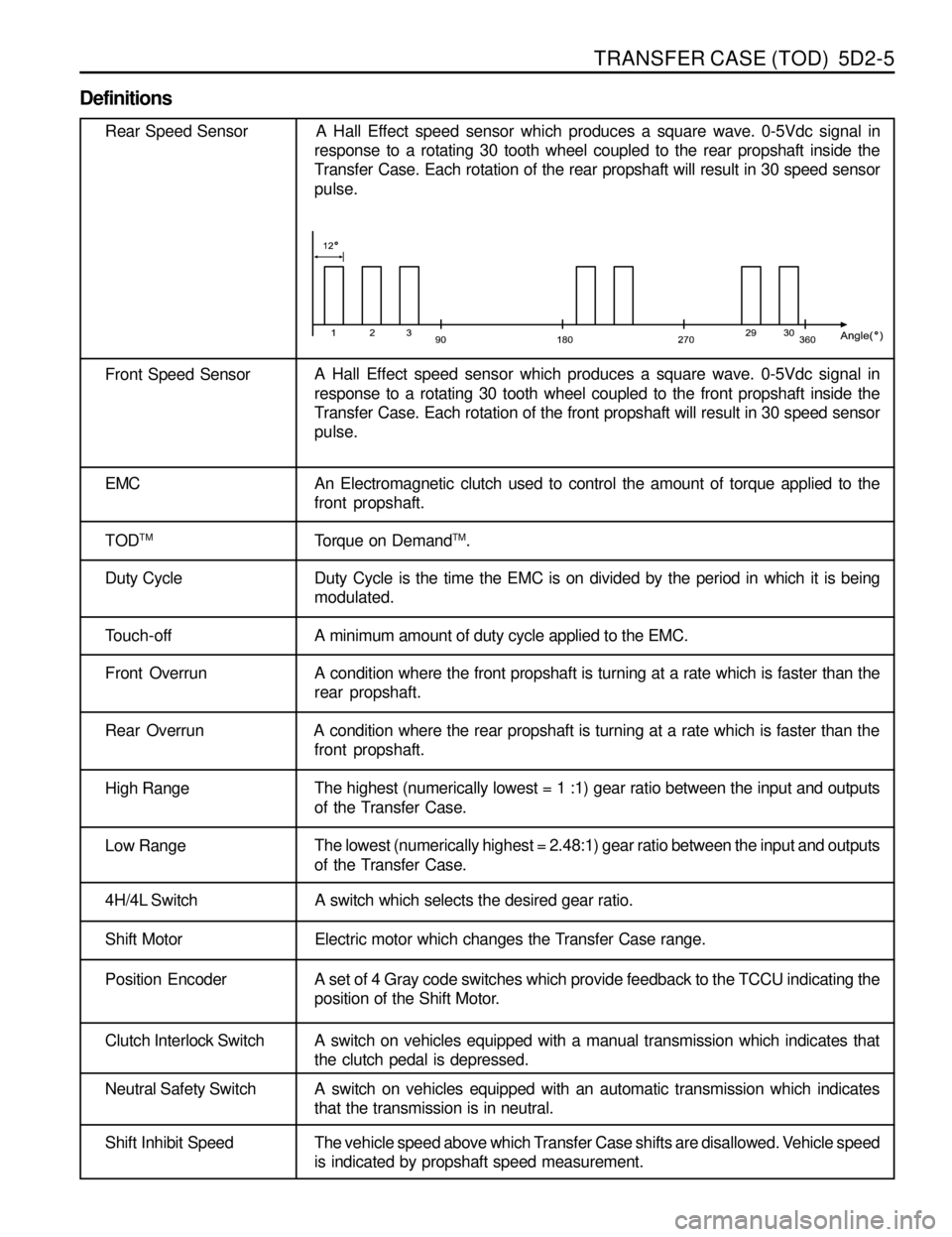
TRANSFER CASE (TOD) 5D2-5
Definitions
Rear Speed Sensor A Hall Effect speed sensor which produces a square wave. 0-5Vdc signal in
response to a rotating 30 tooth wheel coupled to the rear propshaft inside the
Transfer Case. Each rotation of the rear propshaft will result in 30 speed sensor
pulse.
Front Speed SensorA Hall Effect speed sensor which produces a square wave. 0-5Vdc signal in
response to a rotating 30 tooth wheel coupled to the front propshaft inside the
Transfer Case. Each rotation of the front propshaft will result in 30 speed sensor
pulse.
EMC An Electromagnetic clutch used to control the amount of torque applied to the
front propshaft.
TOD
TMTorque on DemandTM.
Duty Cycle Duty Cycle is the time the EMC is on divided by the period in which it is being
modulated.
Touch-off A minimum amount of duty cycle applied to the EMC.
Front OverrunA condition where the front propshaft is turning at a rate which is faster than the
rear propshaft.
Rear Overrun A condition where the rear propshaft is turning at a rate which is faster than the
front propshaft.
High RangeThe highest (numerically lowest = 1 :1) gear ratio between the input and outputs
of the Transfer Case.
Low RangeThe lowest (numerically highest = 2.48:1) gear ratio between the input and outputs
of the Transfer Case.
4H/4L Switch A switch which selects the desired gear ratio.
Shift Motor Electric motor which changes the Transfer Case range.
Position Encoder A set of 4 Gray code switches which provide feedback to the TCCU indicating the
position of the Shift Motor.
Clutch Interlock Switch A switch on vehicles equipped with a manual transmission which indicates that
the clutch pedal is depressed.
Neutral Safety Switch A switch on vehicles equipped with an automatic transmission which indicates
that the transmission is in neutral.
Shift Inhibit Speed The vehicle speed above which Transfer Case shifts are disallowed. Vehicle speed
is indicated by propshaft speed measurement.
Page 1213 of 1463
5D2-6 TRANSFER CASE (TOD)
Input/Output diagram
TOD control unit and main wiring harness is linked by 30 pin
connector. Each pin joins with switche and actuator whose
details refer to the below diagram.
Battery Power
Ignition ON/OFF
Position Encoder 1
Position Encoder 2
Position Encoder 3
Position Encoder 4
4H / 4L Switch Signal
A/T “N” Position Signal
Speed / TPS Supply
Front Speed Sensor Input
Rear Speed Sensor Input
ABS Operation Signal
Brake Switch Signal
4
5
27
10
28
30
9
24
16
11
29
25
26
19
CAN H
CAN L
Shift Motor output port
(LO-HI)
Shift Motor output port
(HI-LO)
EMC
'4L' Indicator
Position Return
'4WD CHECK' IND
TPS/speed Sensor Ground
(Speed / TPS Return)
2
1
3
21
6
7
13 15
14
K-Line20 22
23
17
18
Page 1214 of 1463
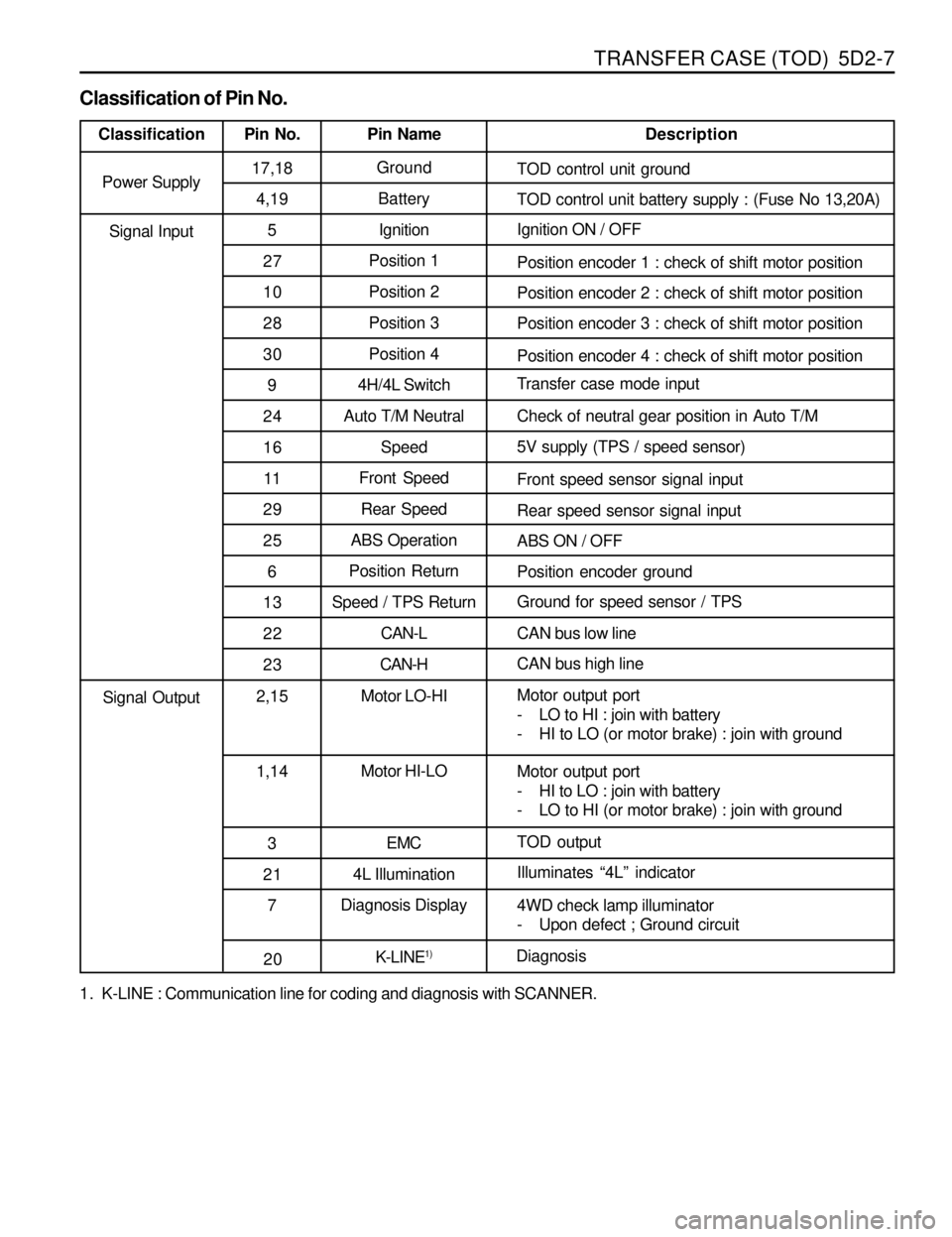
TRANSFER CASE (TOD) 5D2-7
1. K-LINE : Communication line for coding and diagnosis with SCANNER.
Classification of Pin No.
ClassificationPin No. Pin NameDescription
Power Supply17,18Ground
TOD control unit ground
4,19Battery
TOD control unit battery supply : (Fuse No 13,20A)
5IgnitionIgnition ON / OFF
27Position 1
Position encoder 1 : check of shift motor position
10Position 2
Position encoder 2 : check of shift motor position
28Position 3
Position encoder 3 : check of shift motor position
30Position 4
Position encoder 4 : check of shift motor position
94H/4L SwitchTransfer case mode input
24Auto T/M Neutral
Check of neutral gear position in Auto T/M
16Speed5V supply (TPS / speed sensor)
11Front Speed
Front speed sensor signal input Signal Input
29Rear Speed
Rear speed sensor signal input
25ABS Operation
ABS ON / OFF
6Position Return
Position encoder ground
13Speed / TPS ReturnGround for speed sensor / TPS
22CAN-LCAN bus low line
23CAN-HCAN bus high line
2,15Motor LO-HIMotor output port
- LO to HI : join with battery
- HI to LO (or motor brake) : join with ground
1,14Motor HI-LO
Motor output port
- HI to LO : join with battery
- LO to HI (or motor brake) : join with ground
3EMCTOD output
Signal Output
214L IlluminationIlluminates “4L” indicator
7Diagnosis Display
4WD check lamp illuminator
- Upon defect ; Ground circuit
20K-LINE1)Diagnosis
Page 1215 of 1463
5D2-8 TRANSFER CASE (TOD)
Position Code 1/2/3/4
111 0
1010
0010
0000
111 0
Initial Operation of TOD Control Unit
When ignition “ON”, “4L” and "4WD check" lamps illuminates
for 0.6second to check bulb in instrument panel, then perform
diagnosis of system.
Position Encoder
The Position Encoder is used by the TCCU to determine the
position of the Shift Motor. Each motor position is identified by
a position code as shown.
Notice
1. All other position codes are invalid
2. Position Input Open Circuit (> 4.5V) = 1
3. Position Input shorted to Speed/Position Return (< 0.5V) = 0
Motor Position
Left Stop
Left of High
High
Right of High
Zone 1Position Code 1/2/3/4
1001
0001
0101
0100Motor Position
Neutral
Zone 2
Low
Right Stop
Page 1216 of 1463
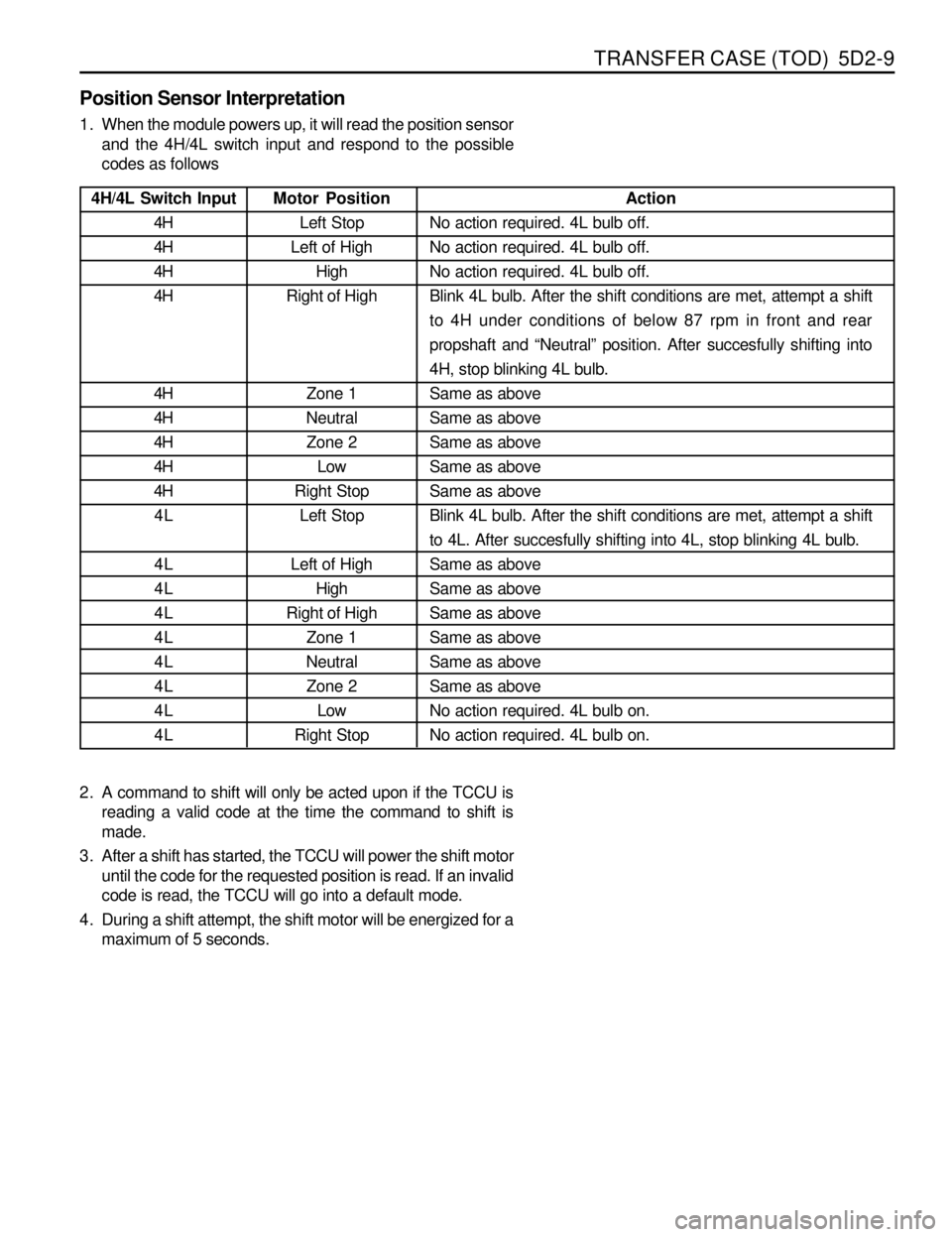
TRANSFER CASE (TOD) 5D2-9
4H/4L Switch Input
4H
4H
4H
4H
4H
4H
4H
4H
4H
4L
4L
4L
4L
4L
4L
4L
4L
4L
Position Sensor Interpretation
1. When the module powers up, it will read the position sensor
and the 4H/4L switch input and respond to the possible
codes as follows
2. A command to shift will only be acted upon if the TCCU is
reading a valid code at the time the command to shift is
made.
3. After a shift has started, the TCCU will power the shift motor
until the code for the requested position is read. If an invalid
code is read, the TCCU will go into a default mode.
4. During a shift attempt, the shift motor will be energized for a
maximum of 5 seconds.Motor Position
Left Stop
Left of High
High
Right of High
Zone 1
Neutral
Zone 2
Low
Right Stop
Left Stop
Left of High
High
Right of High
Zone 1
Neutral
Zone 2
Low
Right StopAction
No action required. 4L bulb off.
No action required. 4L bulb off.
No action required. 4L bulb off.
Blink 4L bulb. After the shift conditions are met, attempt a shift
to 4H under conditions of below 87 rpm in front and rear
propshaft and “Neutral” position. After succesfully shifting into
4H, stop blinking 4L bulb.
Same as above
Same as above
Same as above
Same as above
Same as above
Blink 4L bulb. After the shift conditions are met, attempt a shift
to 4L. After succesfully shifting into 4L, stop blinking 4L bulb.
Same as above
Same as above
Same as above
Same as above
Same as above
Same as above
No action required. 4L bulb on.
No action required. 4L bulb on.