Page 1017 of 1463
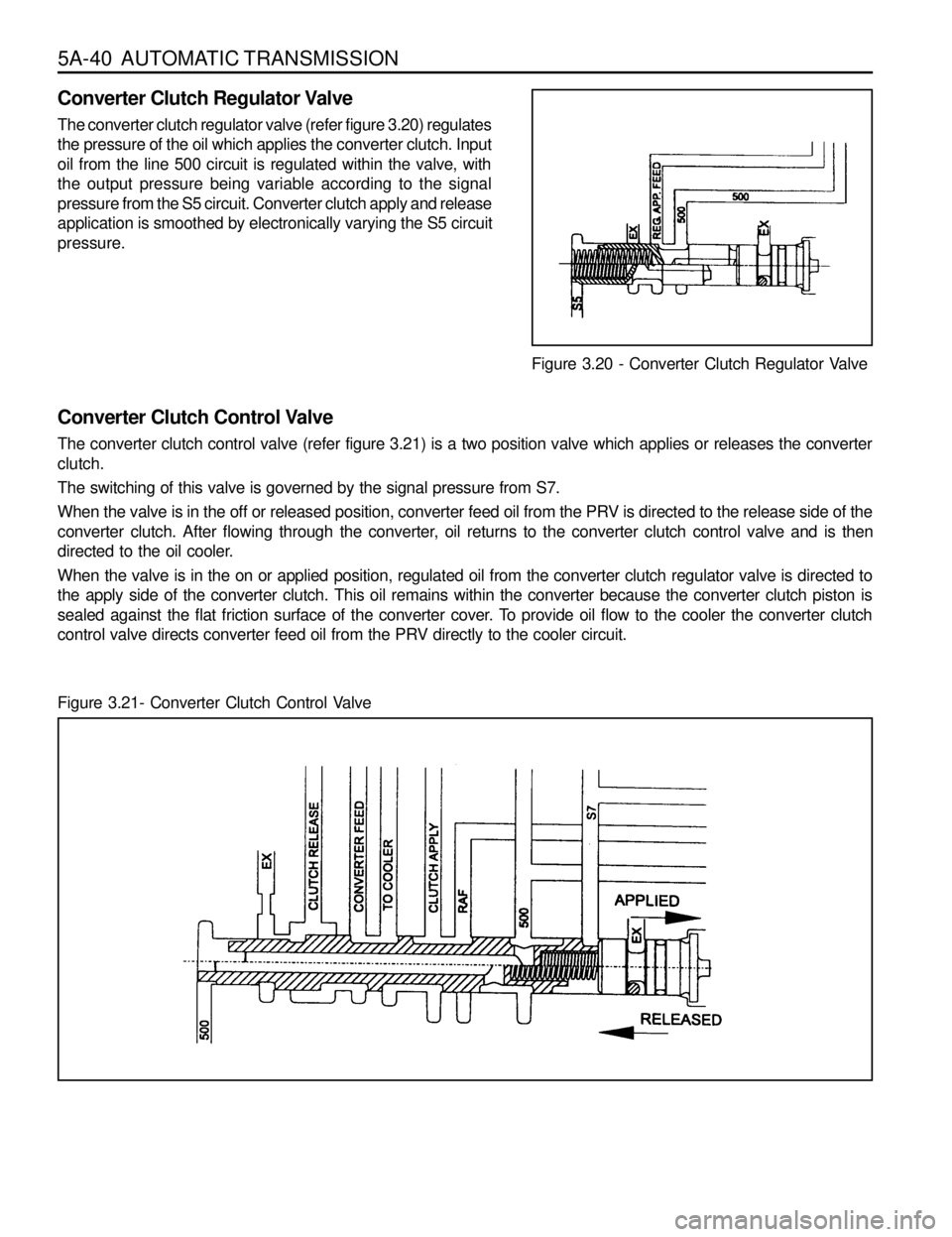
5A-40 AUTOMATIC TRANSMISSION
Converter Clutch Regulator Valve
The converter clutch regulator valve (refer figure 3.20) regulates
the pressure of the oil which applies the converter clutch. Input
oil from the line 500 circuit is regulated within the valve, with
the output pressure being variable according to the signal
pressure from the S5 circuit. Converter clutch apply and release
application is smoothed by electronically varying the S5 circuit
pressure.
Converter Clutch Control Valve
The converter clutch control valve (refer figure 3.21) is a two position valve which applies or releases the converter
clutch.
The switching of this valve is governed by the signal pressure from S7.
When the valve is in the off or released position, converter feed oil from the PRV is directed to the release side of the
converter clutch. After flowing through the converter, oil returns to the converter clutch control valve and is then
directed to the oil cooler.
When the valve is in the on or applied position, regulated oil from the converter clutch regulator valve is directed to
the apply side of the converter clutch. This oil remains within the converter because the converter clutch piston is
sealed against the flat friction surface of the converter cover. To provide oil flow to the cooler the converter clutch
control valve directs converter feed oil from the PRV directly to the cooler circuit.
Figure 3.21- Converter Clutch Control ValveFigure 3.20 - Converter Clutch Regulator Valve
Page 1018 of 1463
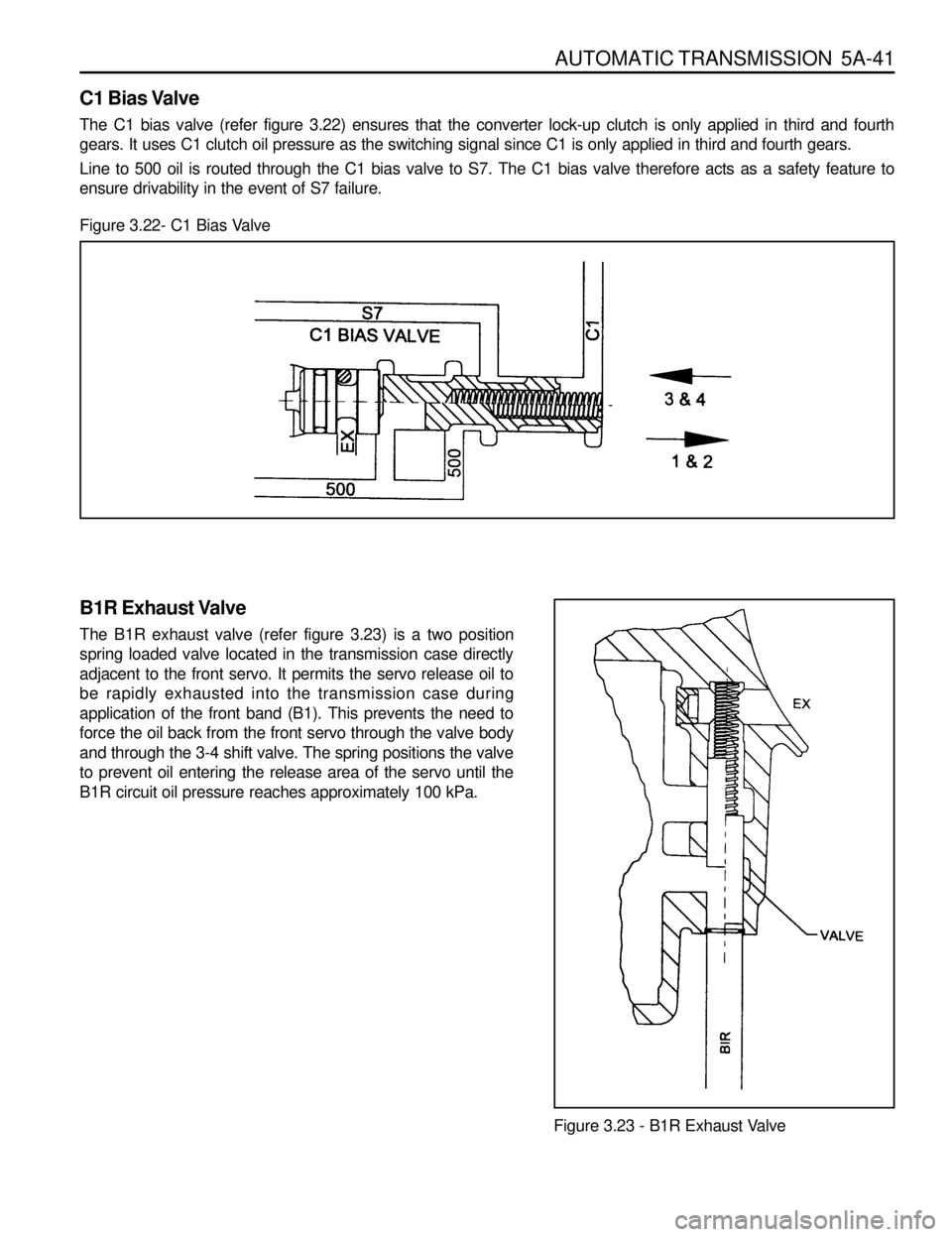
AUTOMATIC TRANSMISSION 5A-41
C1 Bias Valve
The C1 bias valve (refer figure 3.22) ensures that the converter lock-up clutch is only applied in third and fourth
gears. It uses C1 clutch oil pressure as the switching signal since C1 is only applied in third and fourth gears.
Line to 500 oil is routed through the C1 bias valve to S7. The C1 bias valve therefore acts as a safety feature to
ensure drivability in the event of S7 failure.
Figure 3.22- C1 Bias Valve
B1R Exhaust Valve
The B1R exhaust valve (refer figure 3.23) is a two position
spring loaded valve located in the transmission case directly
adjacent to the front servo. It permits the servo release oil to
be rapidly exhausted into the transmission case during
application of the front band (B1). This prevents the need to
force the oil back from the front servo through the valve body
and through the 3-4 shift valve. The spring positions the valve
to prevent oil entering the release area of the servo until the
B1R circuit oil pressure reaches approximately 100 kPa.
Figure 3.23 - B1R Exhaust Valve
Page 1019 of 1463
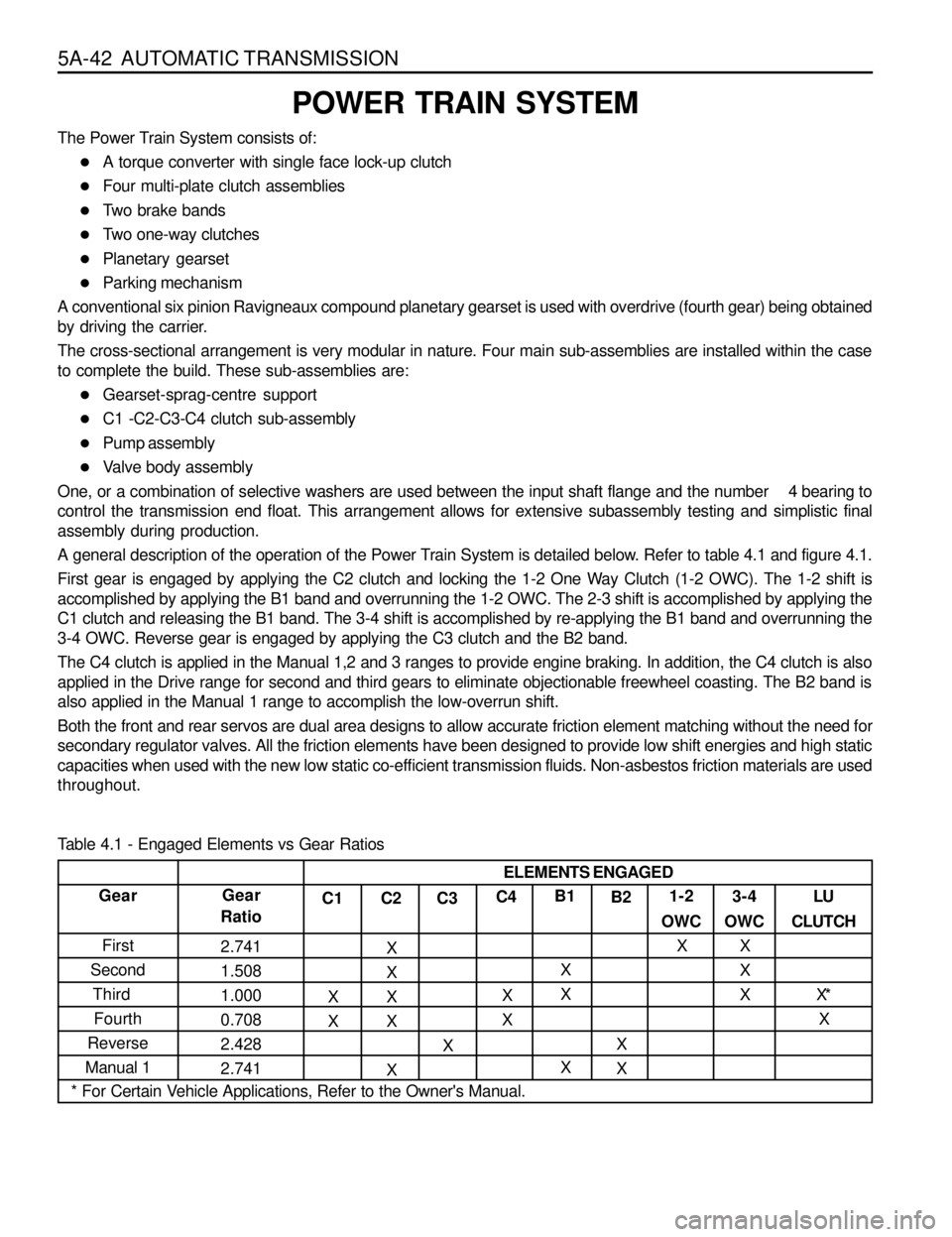
5A-42 AUTOMATIC TRANSMISSION
POWER TRAIN SYSTEM
The Power Train System consists of:
lA torque converter with single face lock-up clutch
lFour multi-plate clutch assemblies
lTwo brake bands
lTwo one-way clutches
lPlanetary gearset
lParking mechanism
A conventional six pinion Ravigneaux compound planetary gearset is used with overdrive (fourth gear) being obtained
by driving the carrier.
The cross-sectional arrangement is very modular in nature. Four main sub-assemblies are installed within the case
to complete the build. These sub-assemblies are:
lGearset-sprag-centre support
lC1 -C2-C3-C4 clutch sub-assembly
lPump assembly
lValve body assembly
One, or a combination of selective washers are used between the input shaft flange and the number 4 bearing to
control the transmission end float. This arrangement allows for extensive subassembly testing and simplistic final
assembly during production.
A general description of the operation of the Power Train System is detailed below. Refer to table 4.1 and figure 4.1.
First gear is engaged by applying the C2 clutch and locking the 1-2 One Way Clutch (1-2 OWC). The 1-2 shift is
accomplished by applying the B1 band and overrunning the 1-2 OWC. The 2-3 shift is accomplished by applying the
C1 clutch and releasing the B1 band. The 3-4 shift is accomplished by re-applying the B1 band and overrunning the
3-4 OWC. Reverse gear is engaged by applying the C3 clutch and the B2 band.
The C4 clutch is applied in the Manual 1,2 and 3 ranges to provide engine braking. In addition, the C4 clutch is also
applied in the Drive range for second and third gears to eliminate objectionable freewheel coasting. The B2 band is
also applied in the Manual 1 range to accomplish the low-overrun shift.
Both the front and rear servos are dual area designs to allow accurate friction element matching without the need for
secondary regulator valves. All the friction elements have been designed to provide low shift energies and high static
capacities when used with the new low static co-efficient transmission fluids. Non-asbestos friction materials are used
throughout.
Gear
First
Second
Third
Fourth
Reverse
Manual 1Gear
Ratio
2.741
1.508
1.000
0.708
2.428
2.741C1
X
XC2
X
X
X
X
XC3
XC4
X
XB1
X
X
XB2
X
X1-2
OWC
X3-4
OWC
X
X
XLU
CLUTCH
X*
X ELEMENTS ENGAGED
* For Certain Vehicle Applications, Refer to the Owner's Manual. Table 4.1 - Engaged Elements vs Gear Ratios
Page 1020 of 1463
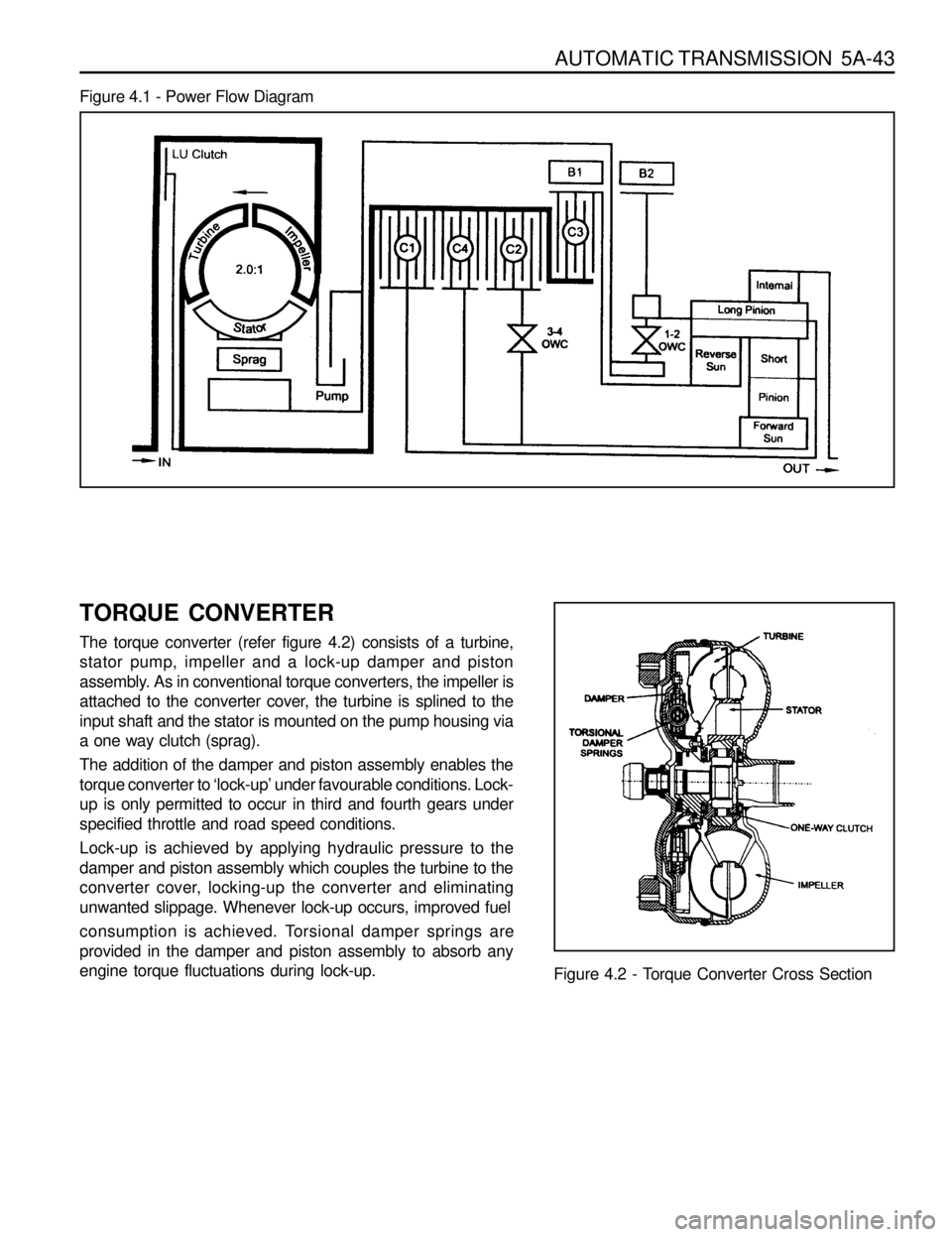
AUTOMATIC TRANSMISSION 5A-43
Figure 4.1 - Power Flow Diagram
TORQUE CONVERTER
The torque converter (refer figure 4.2) consists of a turbine,
stator pump, impeller and a lock-up damper and piston
assembly. As in conventional torque converters, the impeller is
attached to the converter cover, the turbine is splined to the
input shaft and the stator is mounted on the pump housing via
a one way clutch (sprag).
The addition of the damper and piston assembly enables the
torque converter to ‘lock-up’ under favourable conditions. Lock-
up is only permitted to occur in third and fourth gears under
specified throttle and road speed conditions.
Lock-up is achieved by applying hydraulic pressure to the
damper and piston assembly which couples the turbine to the
converter cover, locking-up the converter and eliminating
unwanted slippage. Whenever lock-up occurs, improved fuel
consumption is achieved. Torsional damper springs are
provided in the damper and piston assembly to absorb any
engine torque fluctuations during lock-up.
Figure 4.2 - Torque Converter Cross Section
Page 1021 of 1463
5A-44 AUTOMATIC TRANSMISSION
CLUTCH PACKS
There are four clutch packs (refer to figure 4.3). All clutch packs are composed of multiple steel and friction plates.
C1 CLUTCHWhen applied, this clutch pack allows the input shaft to drive the planet carrier.
This occurs in third and fourth gears.
C2 CLUTCHWhen applied this clutch pack allows the input shaft to drive the forward sun gear via the 3-4 OWC.
This occurs in all forward gears.
C3 CLUTCHWhen applied this clutch pack allows the input shaft to drive the reverse sun gear. This only occurs in
reverse gear.
C4 CLUTCHWhen applied this clutch provides engine braking on overrun. This occurs in Manual 1, 2 and 3 and
also Drive 2 and Drive 3 to prevent objectionable free wheel coasting.
Figure 4.3 - Clutch Packs
Page 1022 of 1463
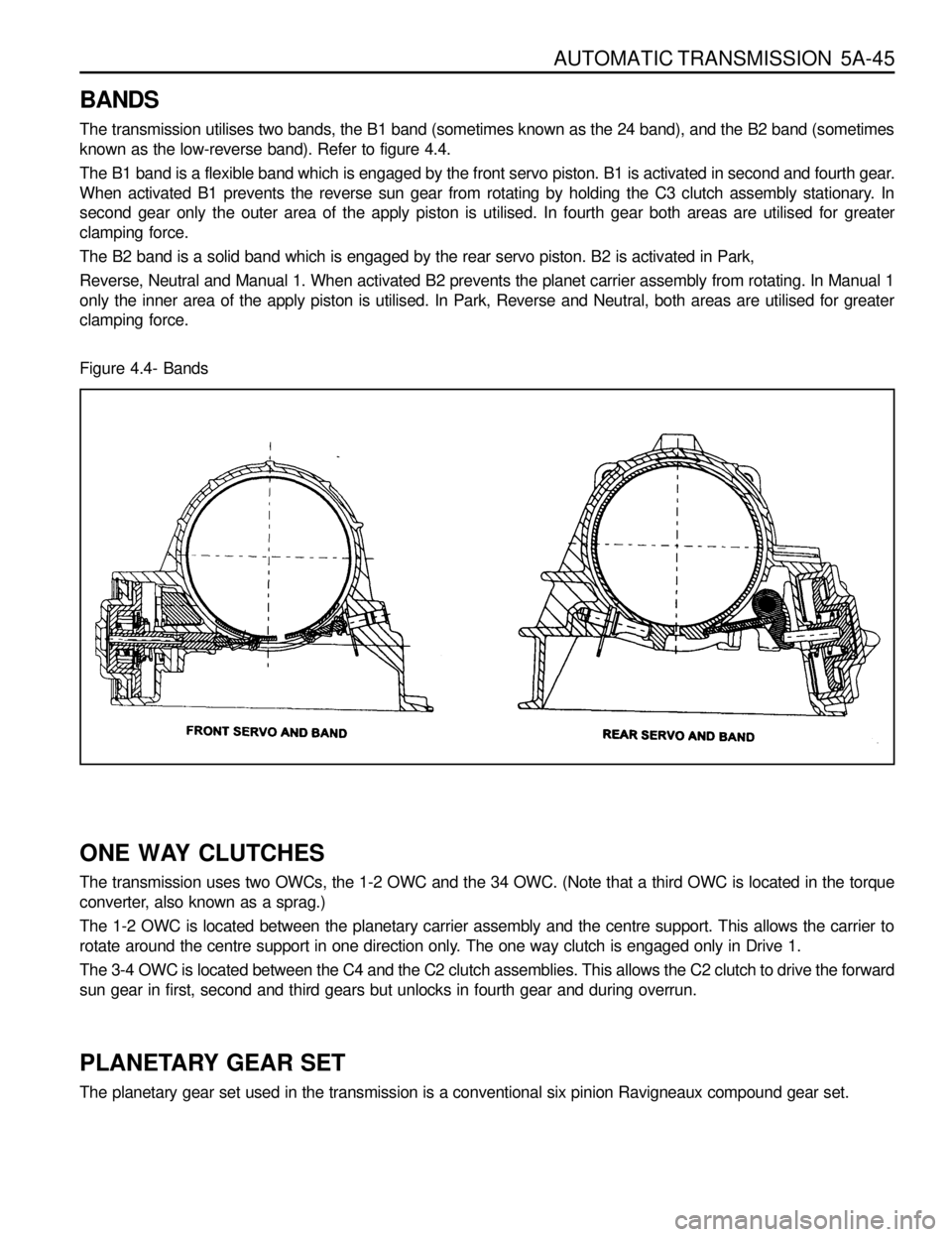
AUTOMATIC TRANSMISSION 5A-45
BANDS
The transmission utilises two bands, the B1 band (sometimes known as the 24 band), and the B2 band (sometimes
known as the low-reverse band). Refer to figure 4.4.
The B1 band is a flexible band which is engaged by the front servo piston. B1 is activated in second and fourth gear.
When activated B1 prevents the reverse sun gear from rotating by holding the C3 clutch assembly stationary. In
second gear only the outer area of the apply piston is utilised. In fourth gear both areas are utilised for greater
clamping force.
The B2 band is a solid band which is engaged by the rear servo piston. B2 is activated in Park,
Reverse, Neutral and Manual 1. When activated B2 prevents the planet carrier assembly from rotating. In Manual 1
only the inner area of the apply piston is utilised. In Park, Reverse and Neutral, both areas are utilised for greater
clamping force.
Figure 4.4- Bands
ONE WAY CLUTCHES
The transmission uses two OWCs, the 1-2 OWC and the 34 OWC. (Note that a third OWC is located in the torque
converter, also known as a sprag.)
The 1-2 OWC is located between the planetary carrier assembly and the centre support. This allows the carrier to
rotate around the centre support in one direction only. The one way clutch is engaged only in Drive 1.
The 3-4 OWC is located between the C4 and the C2 clutch assemblies. This allows the C2 clutch to drive the forward
sun gear in first, second and third gears but unlocks in fourth gear and during overrun.
PLANETARY GEAR SET
The planetary gear set used in the transmission is a conventional six pinion Ravigneaux compound gear set.
Page 1023 of 1463
5A-46 AUTOMATIC TRANSMISSION
PARKING MECHANISM
When Park is selected the manual lever extends the park rod rearwards to engage the parking pawl (refer to (figure
4.5). The pawl will engage the external teeth on the ring gear thus locking the output shaft to the transmission case.
When Park is not selected a return spring holds the parking pawl clear of the output shaft, preventing accidental
engagement of Park.
Figure 4.5 - Park Rod and Cross Shaft
Page 1024 of 1463
AUTOMATIC TRANSMISSION 5A-47
POWER FLOWS
INTRODUCTION
The power flows for the various transmission selections are listed below:
lPower Flow - Neutral and Park
lPower Flow - Reverse
lPower Flow - Manual 1
lPower Flow - Drive 1
lPower Flow - Drive 2
lPower Flow - Drive 3
lPower Flow - Drive 3 Lock Up
lPower Flow - Drive 4 (Overdrive)
lPower Flow - Drive4 Lock Up
Each power flow is described in the following sections.
Table 5.1 details the engaged elements versus the gear selected for all transmission selections.
Gear State
Park and Neutral
Reverse
Manual 1
Drive 1
Drive 2 and Manual 2
Drive 3 and Manual 3
Drive 3 Lock Up and
Manual 3 Lock Up
Drive 4 Overdrive
Drive 4 Lock UpC1
-
-
-
-
-
X
X
X
XC2
-
-
X
X
X
X
X
X
XC3
-
X
-
-
-
-
-
-
-C4
-
-
X
-
X
X
X
-
-B1
-
-
-
-
X
-
-
-
-B2
X
X
X
-
-
-
-
-
-1-2
OWC
-
-
-
X
-
-
-
-
-3-4
OWC
-
-
X
X
X
X
X
-
-LU
CLUTCH
-
-
-
-
-
-
X
-
X ELEMENTS ENGAGED Figure 5.1 - Engaged Elements vs Gear Selected
Planetary Gear Set