Page 393 of 1463
OM600 ENGINE MECHANICAL 1B3-91
Notice
If the max. length of bolts(L) exceed 63.8mm, replace them.
19. Coat the new crankshaft with engine oil and place it on the
crankcase.
20. Install the crankshaft bearing caps according to marking
and tighten the bolts.
Tightening Torque 55 Nm + 90°
Notice
Install from No. 1 cap.
22. Rotate the crankshaft with hand and check whether it
rotates smoothly.
23. Measure crankshaft bearing axial clearance.
Clearance 0.100 - 0.245mm
Notice
If the clearance is out of standard, adjust the axial clearance
of crankshaft bearing by replacing the thrust washers.
Dial Gauge 001 589 53 21 00
Dial Gauge Holder 363 589 02 21 00
Notice
The same thickness of thrust washers should be installed
on both sides of the thrust bearing.
Page 394 of 1463
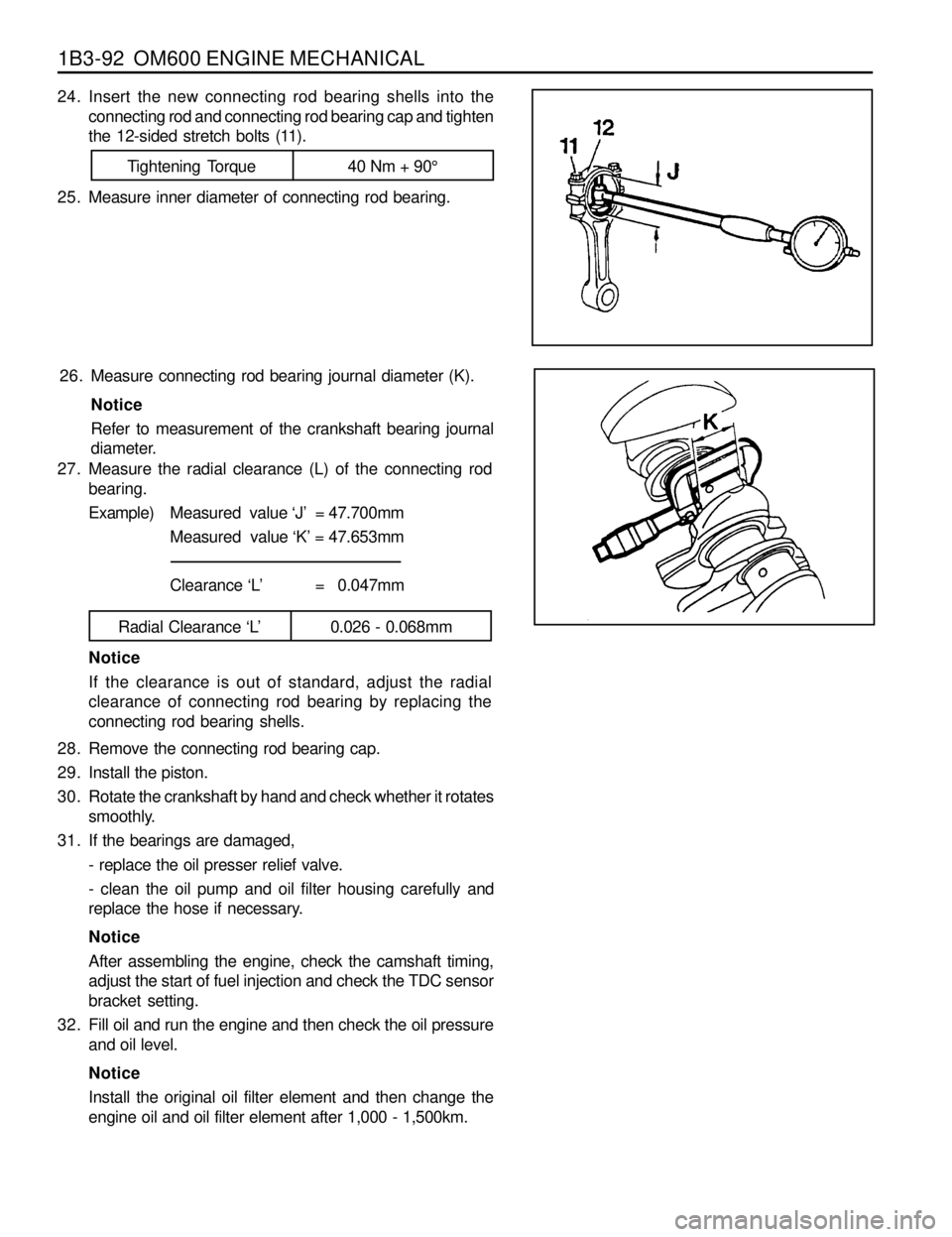
1B3-92 OM600 ENGINE MECHANICAL
28. Remove the connecting rod bearing cap.
29. Install the piston.
30. Rotate the crankshaft by hand and check whether it rotates
smoothly.
31. If the bearings are damaged,
- replace the oil presser relief valve.
- clean the oil pump and oil filter housing carefully and
replace the hose if necessary.
Notice
After assembling the engine, check the camshaft timing,
adjust the start of fuel injection and check the TDC sensor
bracket setting.
32. Fill oil and run the engine and then check the oil pressure
and oil level.
Notice
Install the original oil filter element and then change the
engine oil and oil filter element after 1,000 - 1,500km. 27. Measure the radial clearance (L) of the connecting rod
bearing.
Example)Measured value ‘J’ = 47.700mm
Measured value ‘K’ = 47.653mm
Clearance ‘L’ = 0.047mm
Radial Clearance ‘L’ 0.026 - 0.068mm
Notice
If the clearance is out of standard, adjust the radial
clearance of connecting rod bearing by replacing the
connecting rod bearing shells. 26. Measure connecting rod bearing journal diameter (K).
Notice
Refer to measurement of the crankshaft bearing journal
diameter.
24. Insert the new connecting rod bearing shells into the
connecting rod and connecting rod bearing cap and tighten
the 12-sided stretch bolts (11).
25. Measure inner diameter of connecting rod bearing.
Tightening Torque 40 Nm + 90°
Page 395 of 1463
OM600 ENGINE MECHANICAL 1B3-93
FLYWHEEL
Preceding Work : Removal of the transmission
Removal of the clutch
1 Oil Pan
2 Straight Pin
3 Flywheel4 12-Sided Stretch Bolt............Check, 45Nm + 90°
5 Drive Plate (Automatic Transmission)
6 Flywheel (Automatic Transmission)
Page 396 of 1463
1B3-94 OM600 ENGINE MECHANICAL
lManual transmission flywheel
lAutomatic transmission flywheel
OM661LA OM662LA
Page 397 of 1463
OM600 ENGINE MECHANICAL 1B3-95
3. Remove the flywheel (3), if equipped with manual
transmission.
Installation Notice
Correctly align the position of dowel pin (2).
Tools Required
602 589 00 40 00 Engine Lock
Removal & Installation Procedure
1. Install the engine lock.
Engine Lock 602 589 02 40 00
2. Remove the 12-sided stretch bolts (4).
Installation Notice
Tightening Torque 45 Nm + 90°
Notice
If the length ‘L’ of bolts exceeds 22.5mm, replace the bolts.
Page 398 of 1463
1B3-96 OM600 ENGINE MECHANICAL
4. Remove the flywheel (6) and driven plate (5), if equipped
with automatic transmission.
Installation Notice
Correctly align the position of dowel pin (2).
5. Installation should follow the removal procedure in the
reverse order.
Page 399 of 1463
OM600 ENGINE MECHANICAL 1B3-97
MACHINING OF FLYWHEEL
1 Flywheel
Machining of Flywheel
Notice
Flywheels which have scorch marks, scoring or cracks in
the clutch surface should be machined by grinding or
precision-turning. If the scores or cracks are severe than
permissible specifications, replace the flywheel.
lWhen machining the clutch surface ‘A’, the mounting
surface (B) for the clutch pressure plate should also be
machined in accordance with ‘A’ to keep the distance ‘a’.
lDo not machine under ‘b’ value.
lWhen machining, fix the flywheel exactly not to exceed the
standard runout.
OM662LA
OM662LA
Max. axial runout
Distance ‘a’
New
Repair up to19.3 - 19.5 mm16.6 mm
15.6 mm
0.05 mmDistance ‘b’
Page 400 of 1463
1B3-98 OM600 ENGINE MECHANICAL
FLYWHEEL RING GEAR
Preceding Work : Removal of flywheel
1 Ring Gear
2 Flywheel3 Centering Collar Diameter
Tools Required
001 589 53 21 00 Dial Gauge
363 589 02 21 00 Dial Gauge Holder