Page 70 of 1463
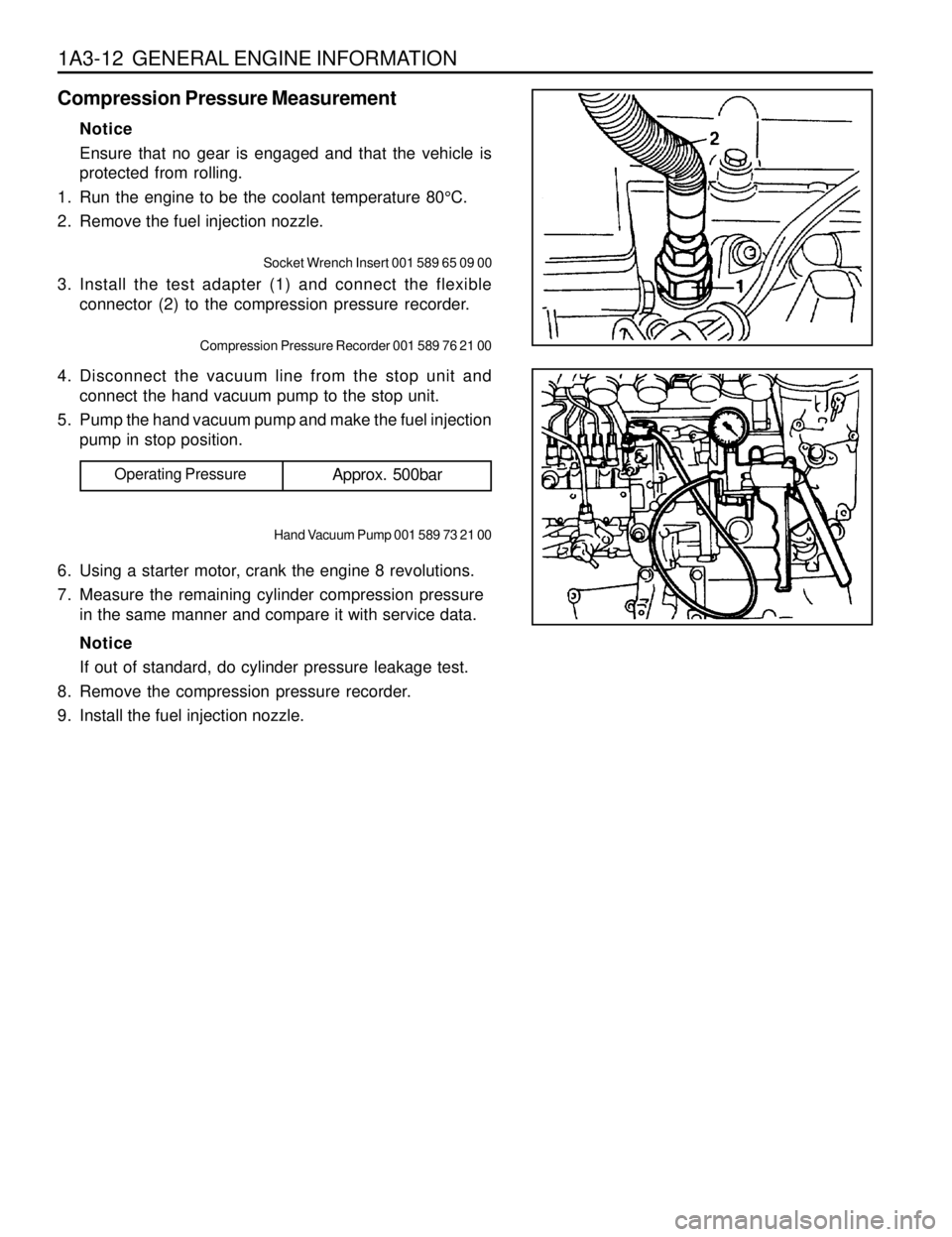
1A3-12 GENERAL ENGINE INFORMATION
Compression Pressure Measurement
Notice
Ensure that no gear is engaged and that the vehicle is
protected from rolling.
1. Run the engine to be the coolant temperature 80°C.
2. Remove the fuel injection nozzle.
Socket Wrench Insert 001 589 65 09 00
3. Install the test adapter (1) and connect the flexible
connector (2) to the compression pressure recorder.
Compression Pressure Recorder 001 589 76 21 00
4. Disconnect the vacuum line from the stop unit and
connect the hand vacuum pump to the stop unit.
5. Pump the hand vacuum pump and make the fuel injection
pump in stop position.
Operating PressureApprox. 500bar
Hand Vacuum Pump 001 589 73 21 00
6. Using a starter motor, crank the engine 8 revolutions.
7. Measure the remaining cylinder compression pressure
in the same manner and compare it with service data.
Notice
If out of standard, do cylinder pressure leakage test.
8. Remove the compression pressure recorder.
9. Install the fuel injection nozzle.
Page 169 of 1463
1B1-96 M162 ENGINE MECHANICAL
3 Oil Filler Cap
4 Dipstick Gauge
9. Fill up engine oil through the engine oil filler opening (3).
10. Check for oil leaks at normal engine temperature after
starting the engine.
11. Stop the engine and wait 5 minutes.
Check the oil level and fill up as specified if necessary.
Page 289 of 1463
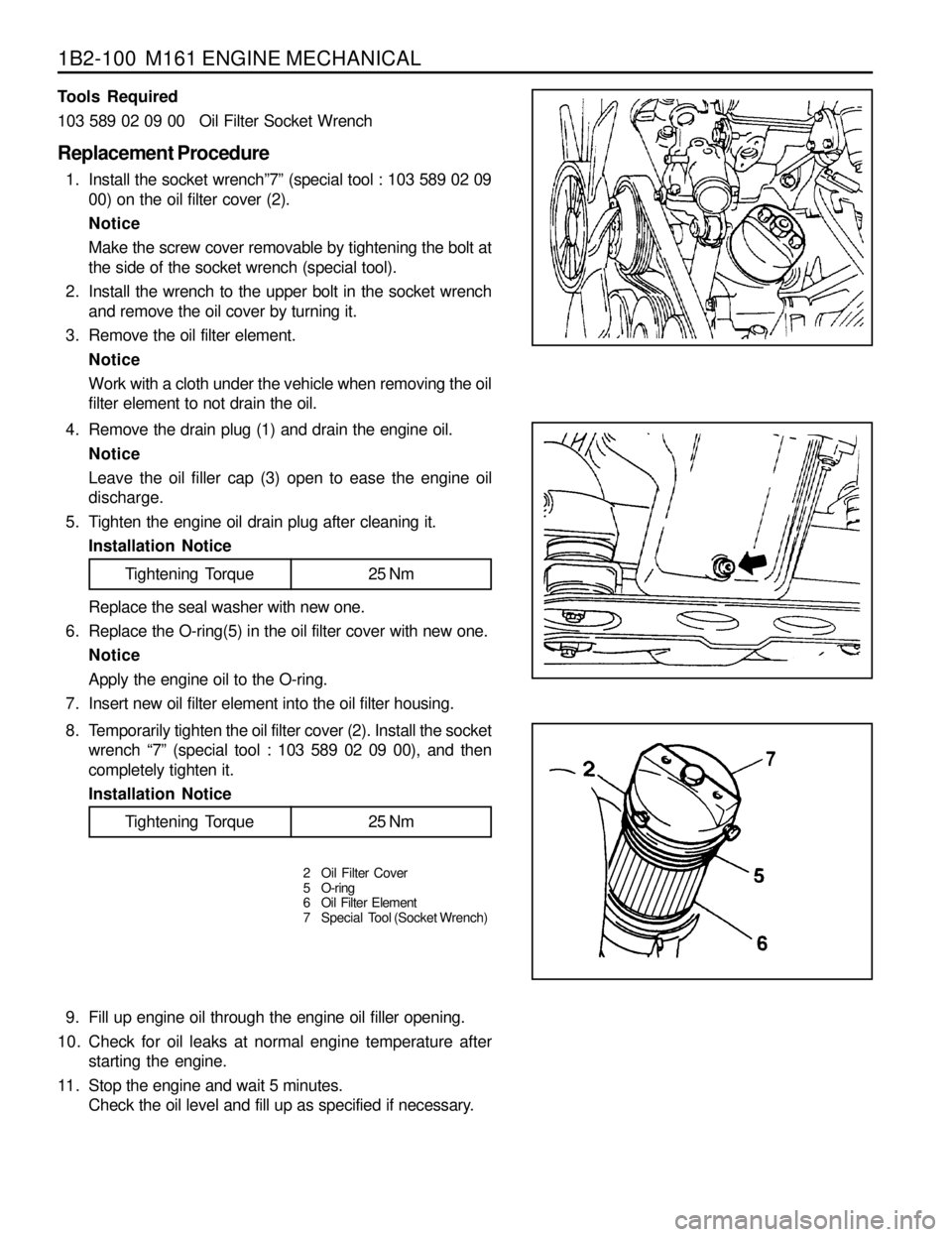
1B2-100 M161 ENGINE MECHANICAL
9. Fill up engine oil through the engine oil filler opening.
10. Check for oil leaks at normal engine temperature after
starting the engine.
11. Stop the engine and wait 5 minutes.
Check the oil level and fill up as specified if necessary. 4. Remove the drain plug (1) and drain the engine oil.
Notice
Leave the oil filler cap (3) open to ease the engine oil
discharge.
5. Tighten the engine oil drain plug after cleaning it.
Installation Notice Tools Required
103 589 02 09 00 Oil Filter Socket Wrench
Replacement Procedure
1. Install the socket wrench”7” (special tool : 103 589 02 09
00) on the oil filter cover (2).
Notice
Make the screw cover removable by tightening the bolt at
the side of the socket wrench (special tool).
2. Install the wrench to the upper bolt in the socket wrench
and remove the oil cover by turning it.
3. Remove the oil filter element.
Notice
Work with a cloth under the vehicle when removing the oil
filter element to not drain the oil.
Replace the seal washer with new one.
6. Replace the O-ring(5) in the oil filter cover with new one.
Notice
Apply the engine oil to the O-ring.
7. Insert new oil filter element into the oil filter housing.
Tightening Torque 25 Nm
8. Temporarily tighten the oil filter cover (2). Install the socket
wrench “7” (special tool : 103 589 02 09 00), and then
completely tighten it.
Installation Notice
2 Oil Filter Cover
5 O-ring
6 Oil Filter Element
7 Special Tool (Socket Wrench)
Tightening Torque 25 Nm
Page 404 of 1463
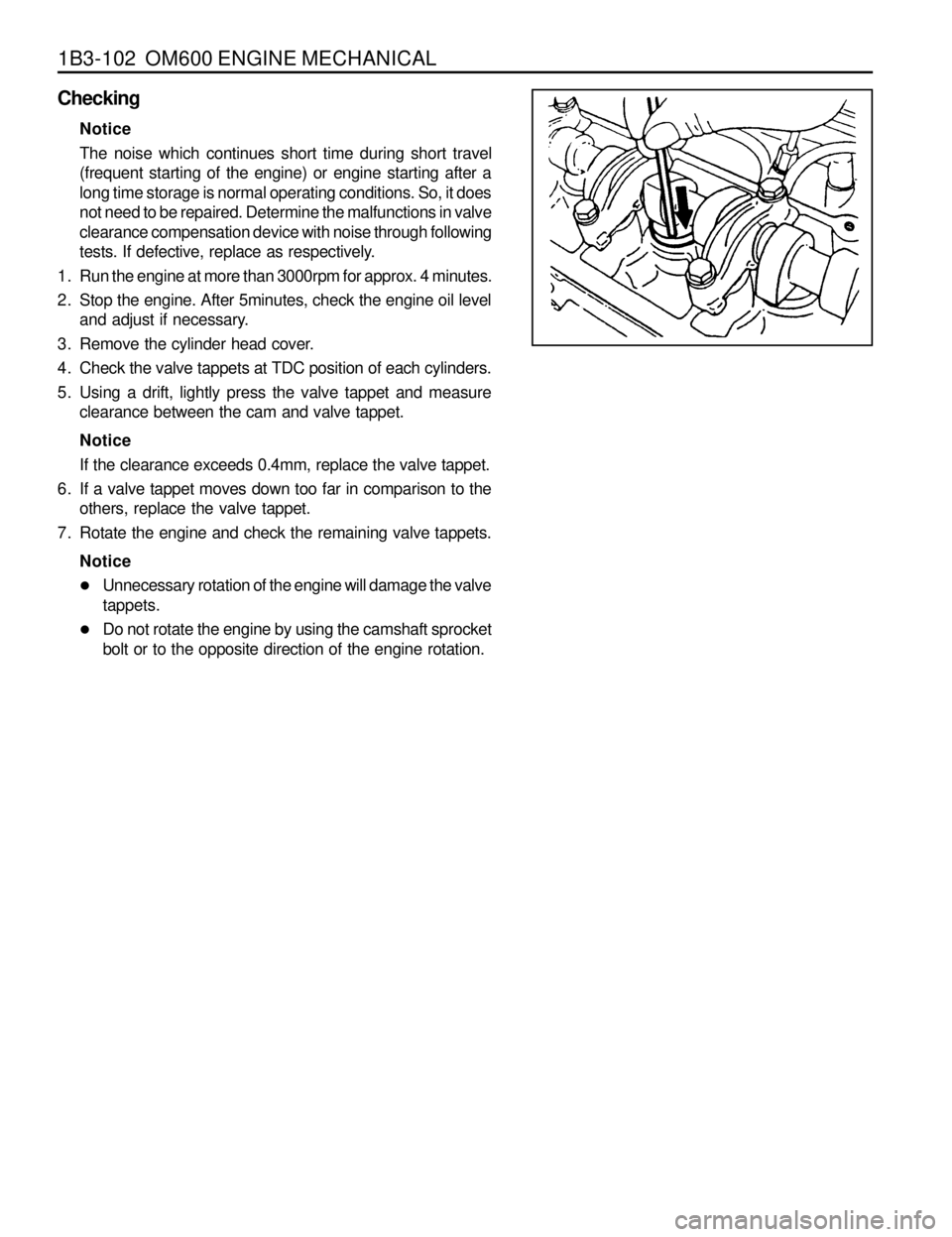
1B3-102 OM600 ENGINE MECHANICAL
Checking
Notice
The noise which continues short time during short travel
(frequent starting of the engine) or engine starting after a
long time storage is normal operating conditions. So, it does
not need to be repaired. Determine the malfunctions in valve
clearance compensation device with noise through following
tests. If defective, replace as respectively.
1. Run the engine at more than 3000rpm for approx. 4 minutes.
2. Stop the engine. After 5minutes, check the engine oil level
and adjust if necessary.
3. Remove the cylinder head cover.
4. Check the valve tappets at TDC position of each cylinders.
5. Using a drift, lightly press the valve tappet and measure
clearance between the cam and valve tappet.
Notice
If the clearance exceeds 0.4mm, replace the valve tappet.
6. If a valve tappet moves down too far in comparison to the
others, replace the valve tappet.
7. Rotate the engine and check the remaining valve tappets.
Notice
lUnnecessary rotation of the engine will damage the valve
tappets.
lDo not rotate the engine by using the camshaft sprocket
bolt or to the opposite direction of the engine rotation.
Page 656 of 1463
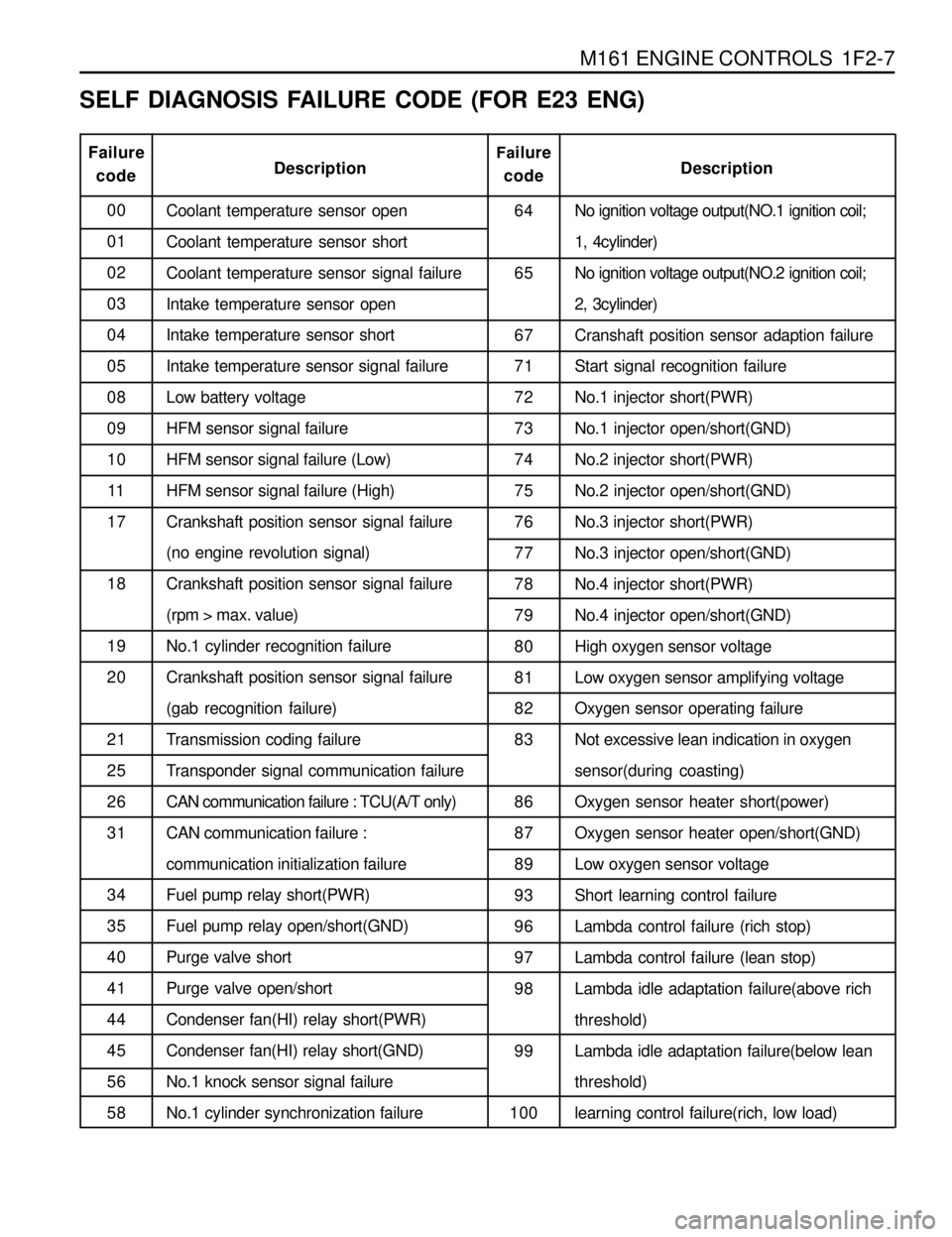
M161 ENGINE CONTROLS 1F2-7
No ignition voltage output(NO.1 ignition coil;
1, 4cylinder)
No ignition voltage output(NO.2 ignition coil;
2, 3cylinder)
Cranshaft position sensor adaption failure
Start signal recognition failure
No.1 injector short(PWR)
No.1 injector open/short(GND)
No.2 injector short(PWR)
No.2 injector open/short(GND)
No.3 injector short(PWR)
No.3 injector open/short(GND)
No.4 injector short(PWR)
No.4 injector open/short(GND)
High oxygen sensor voltage
Low oxygen sensor amplifying voltage
Oxygen sensor operating failure
Not excessive lean indication in oxygen
sensor(during coasting)
Oxygen sensor heater short(power)
Oxygen sensor heater open/short(GND)
Low oxygen sensor voltage
Short learning control failure
Lambda control failure (rich stop)
Lambda control failure (lean stop)
Lambda idle adaptation failure(above rich
threshold)
Lambda idle adaptation failure(below lean
threshold)
learning control failure(rich, low load) Coolant temperature sensor open
Coolant temperature sensor short
Coolant temperature sensor signal failure
Intake temperature sensor open
Intake temperature sensor short
Intake temperature sensor signal failure
Low battery voltage
HFM sensor signal failure
HFM sensor signal failure (Low)
HFM sensor signal failure (High)
Crankshaft position sensor signal failure
(no engine revolution signal)
Crankshaft position sensor signal failure
(rpm > max. value)
No.1 cylinder recognition failure
Crankshaft position sensor signal failure
(gab recognition failure)
Transmission coding failure
Transponder signal communication failure
CAN communication failure : TCU(A/T only)
CAN communication failure :
communication initialization failure
Fuel pump relay short(PWR)
Fuel pump relay open/short(GND)
Purge valve short
Purge valve open/short
Condenser fan(HI) relay short(PWR)
Condenser fan(HI) relay short(GND)
No.1 knock sensor signal failure
No.1 cylinder synchronization failure 00
01
02
03
04
05
08
09
10
11
17
18
19
20
21
25
26
31
34
35
40
41
44
45
56
58
Failure
codeDescriptionFailure
codeDescription
64
65
67
71
72
73
74
75
76
77
78
79
80
81
82
83
86
87
89
93
96
97
98
99
100
SELF DIAGNOSIS FAILURE CODE (FOR E23 ENG)
Page 747 of 1463
1F3-18 OM600 ENGINE CONTROLS
Min. volume 150cm for 30 seconds
FUEL PUMP TEST
Notice
Before test, replace the fuel filter cartridge and fuel prefilter.
Fuel Feed Test
1. Disconnect the fuel return line (1) and seal up it with plug.
2. Insert the plastic hose (5) and put the end into the measuring
beaker (6).
3. Disconnect the vacuum line (4) from vacuum unit (engine
stop) (5) and connect the vacuum pump (7) to the vacuum
unit.
4. To avoid the engine starting, build up vacuum (approx. 500
mbar).
5. Operate the starter motor for exactly 30 seconds and
measure fuel volume in the beaker.
3
Page 749 of 1463
1F3-20 OM600 ENGINE CONTROLS
Tools Required
617 589 04 21 00 Tester
1. Disconnect the fuel line (2) from the fuel filter.
2. Remove the banjo bolt (4) from the fuel injection pump and
remove the seals (3) and fuel line (2).
3. Connect the tester (5).
4. Start the engine and read off the fuel pressure on tester
(5).
Notice
If out of standard, replace the fuel feed pump.
Tester 617 589 04 21 00
5. Stop the engine.At Idle Speed
At Full load
> 0.3bar
> 0.5bar
6. Remove the tester.
7. Replace the seal and connect the fuel line (2).
Page 770 of 1463
OM600 ENGINE CONTROLS 1F3-41
With Pulse Generator Tools Required
617 589 09 21 00 Rl Sensor
617 589 10 21 00 Timing Tester
667 589 00 21 00 TDC Pulse Generator
Commercial Tools
Item
Digital Tester
Without Pulse GeneratorTools
Bosch, MOT 001.03
Hartmann & Braun, EOMT3
Bosch, ETD 019.00
Sun, DIT 9000
ALV, Diesel - Tester 875
Test Procedure
1. Remove the screw plug (7) and seal (8) collect oil in a suitable
vessel.
2. Install the Rl sensor into the governor housing of injection
pump (1).
Rl Sensor 617 589 10 21 00
3. Connect the digital tester and TDC pulse sender unit
according to connection diagram.
4. Run the engine at idle speed and check the Rl value on the
digital tester
Notice
If out of standard, adjust the start of delivery.
5. Stop the engine.
6. Remove the Rl sensor, digital tester and TDC pulse sender
unit.
7. Replace the seal and tighten the plug.
8. Check engine oil level and adjust if necessary.
Rl value ATDC 14° - 16°
Tightening Torque 30 Nm