Page 1217 of 1463
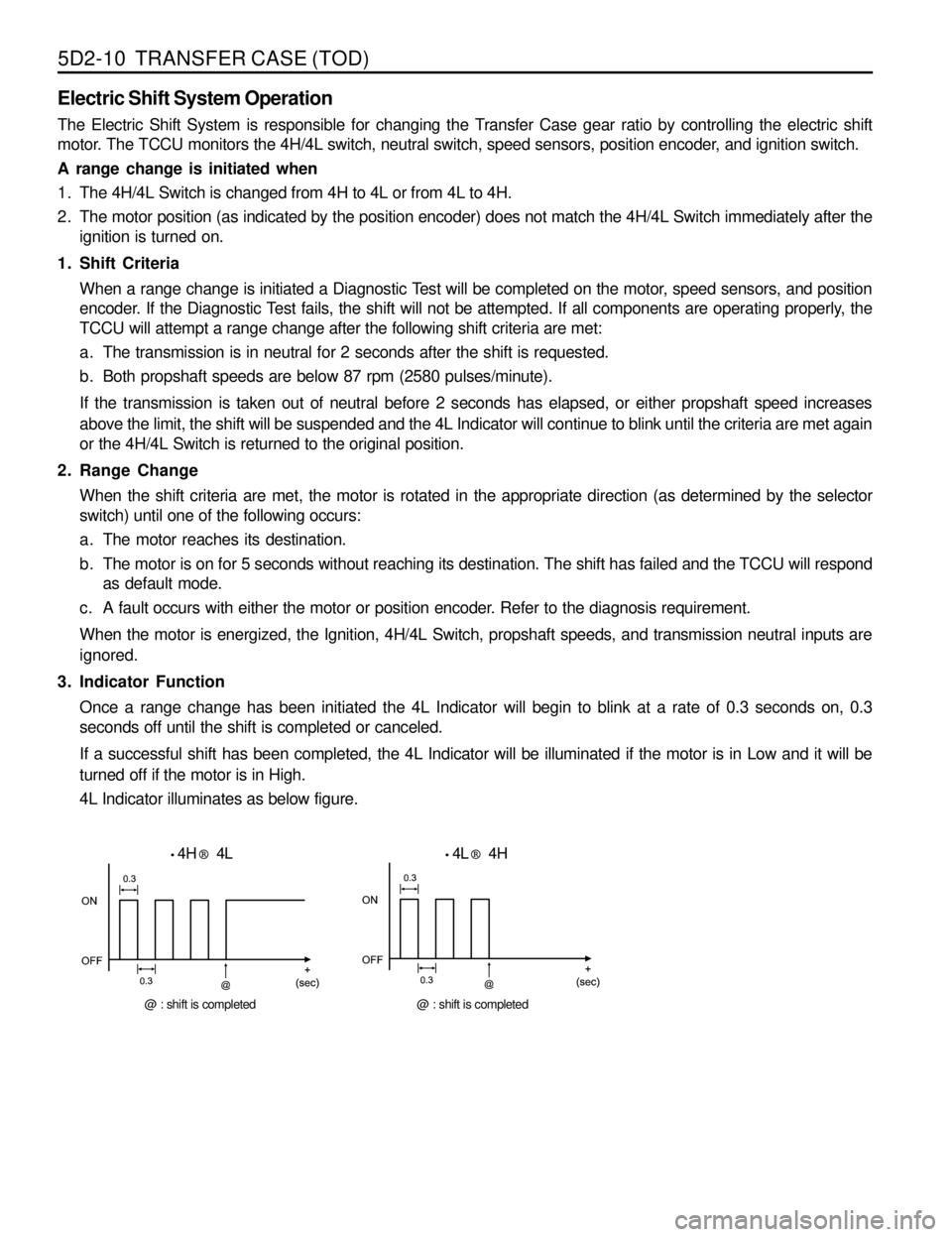
5D2-10 TRANSFER CASE (TOD)
Electric Shift System Operation
The Electric Shift System is responsible for changing the Transfer Case gear ratio by controlling the electric shift
motor. The TCCU monitors the 4H/4L switch, neutral switch, speed sensors, position encoder, and ignition switch.
A range change is initiated when
1. The 4H/4L Switch is changed from 4H to 4L or from 4L to 4H.
2. The motor position (as indicated by the position encoder) does not match the 4H/4L Switch immediately after the
ignition is turned on.
1. Shift Criteria
When a range change is initiated a Diagnostic Test will be completed on the motor, speed sensors, and position
encoder. If the Diagnostic Test fails, the shift will not be attempted. If all components are operating properly, the
TCCU will attempt a range change after the following shift criteria are met:
a. The transmission is in neutral for 2 seconds after the shift is requested.
b. Both propshaft speeds are below 87 rpm (2580 pulses/minute).
If the transmission is taken out of neutral before 2 seconds has elapsed, or either propshaft speed increases
above the limit, the shift will be suspended and the 4L Indicator will continue to blink until the criteria are met again
or the 4H/4L Switch is returned to the original position.
2. Range Change
When the shift criteria are met, the motor is rotated in the appropriate direction (as determined by the selector
switch) until one of the following occurs:
a. The motor reaches its destination.
b. The motor is on for 5 seconds without reaching its destination. The shift has failed and the TCCU will respond
as default mode.
c. A fault occurs with either the motor or position encoder. Refer to the diagnosis requirement.
When the motor is energized, the Ignition, 4H/4L Switch, propshaft speeds, and transmission neutral inputs are
ignored.
3. Indicator Function
Once a range change has been initiated the 4L Indicator will begin to blink at a rate of 0.3 seconds on, 0.3
seconds off until the shift is completed or canceled.
If a successful shift has been completed, the 4L Indicator will be illuminated if the motor is in Low and it will be
turned off if the motor is in High.
4L Indicator illuminates as below figure.
· 4H ® 4L
@ : shift is completed
· 4L ® 4H
@ : shift is completed
Page 1218 of 1463
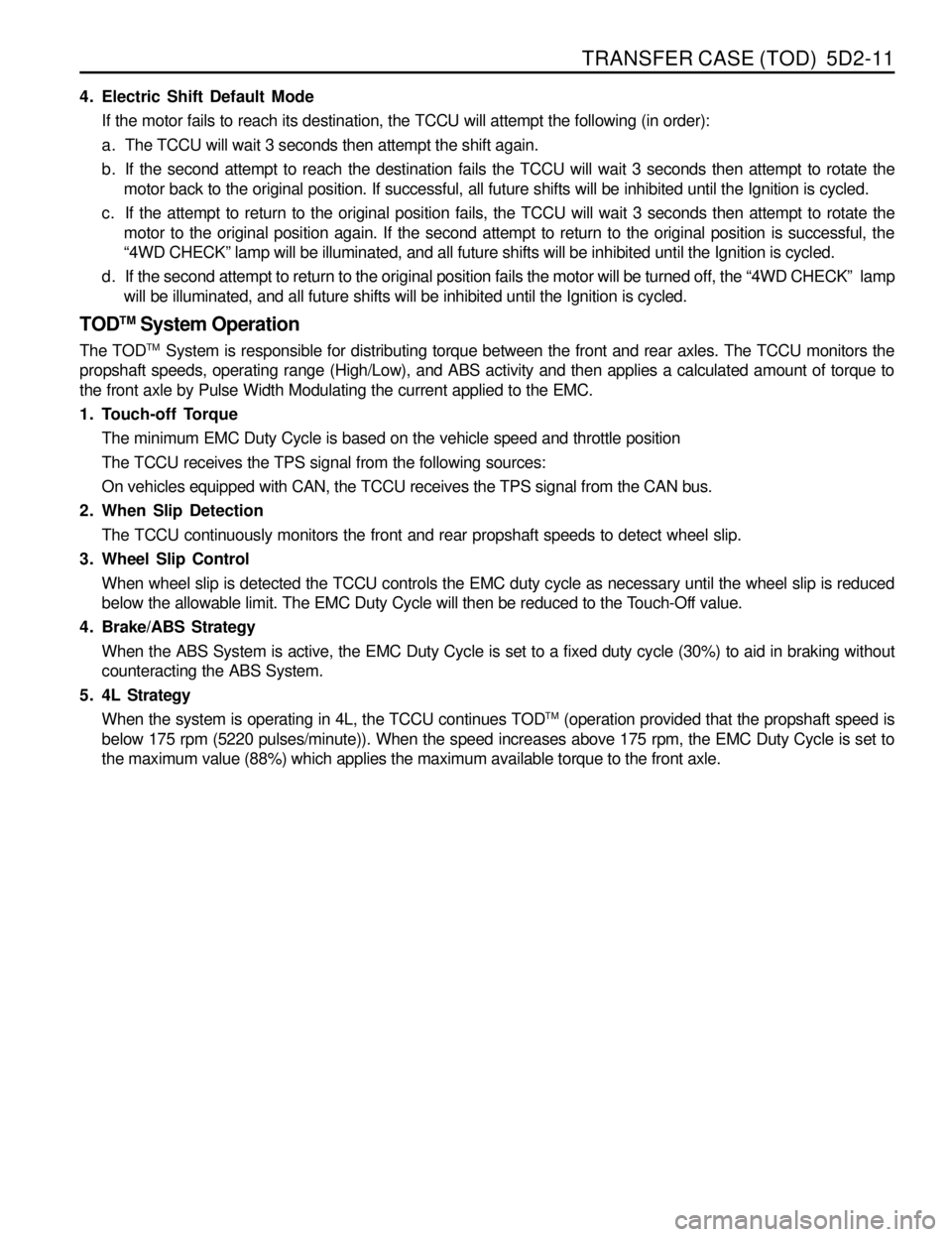
TRANSFER CASE (TOD) 5D2-11
4. Electric Shift Default Mode
If the motor fails to reach its destination, the TCCU will attempt the following (in order):
a. The TCCU will wait 3 seconds then attempt the shift again.
b. If the second attempt to reach the destination fails the TCCU will wait 3 seconds then attempt to rotate the
motor back to the original position. If successful, all future shifts will be inhibited until the Ignition is cycled.
c. If the attempt to return to the original position fails, the TCCU will wait 3 seconds then attempt to rotate the
motor to the original position again. If the second attempt to return to the original position is successful, the
“4WD CHECK” lamp will be illuminated, and all future shifts will be inhibited until the Ignition is cycled.
d. If the second attempt to return to the original position fails the motor will be turned off, the “4WD CHECK” lamp
will be illuminated, and all future shifts will be inhibited until the Ignition is cycled.
TODTM System Operation
The TODTM System is responsible for distributing torque between the front and rear axles. The TCCU monitors the
propshaft speeds, operating range (High/Low), and ABS activity and then applies a calculated amount of torque to
the front axle by Pulse Width Modulating the current applied to the EMC.
1. Touch-off Torque
The minimum EMC Duty Cycle is based on the vehicle speed and throttle position
The TCCU receives the TPS signal from the following sources:
On vehicles equipped with CAN, the TCCU receives the TPS signal from the CAN bus.
2. When Slip Detection
The TCCU continuously monitors the front and rear propshaft speeds to detect wheel slip.
3. Wheel Slip Control
When wheel slip is detected the TCCU controls the EMC duty cycle as necessary until the wheel slip is reduced
below the allowable limit. The EMC Duty Cycle will then be reduced to the Touch-Off value.
4. Brake/ABS Strategy
When the ABS System is active, the EMC Duty Cycle is set to a fixed duty cycle (30%) to aid in braking without
counteracting the ABS System.
5. 4L Strategy
When the system is operating in 4L, the TCCU continues TOD
TM (operation provided that the propshaft speed is
below 175 rpm (5220 pulses/minute)). When the speed increases above 175 rpm, the EMC Duty Cycle is set to
the maximum value (88%) which applies the maximum available torque to the front axle.
Page 1219 of 1463
5D2-12 TRANSFER CASE (TOD)
Pin
1
2
3
4
5
6
7
8Function
Motor HI-LO
Motor LO-HI
EMC
Battery (+)
Ignition
Position Return
Diagnosis Display
-Pin
9
10
11
12
13
14
15
16Function
HI / LO Switch
Position 2
Front Speed
TPS Supply (Diesel)
Speed/TPS Return
Motor HI-LO
Motor LO-HI
Speed ReferencePin
17
18
19
20
21
22
23
24Function
Ground
Ground
Battery (+)
K-LINE
4L Illumination
CAN-H
CAN-L
Auto T/M, NeutralPin
25
26
27
28
29
30
-
-Function
ABS Input
Brake Switch
Position 1
Position 3
Rear Speed
Position 4
-
-
TOD CONTROL UNIT
Shape and function of TOD Control Unit
Page 1220 of 1463
TRANSFER CASE (TOD) 5D2-13
Speed Sensor/Clutch Coil and Motor Connector
Speed senso /clutch coil and shift motor connector locate upper
backside transfer case (upper part of shift motor).
- Shift motor connector : Black
- Speed sensor and clutch coil connector : White
Shift Mtor Connector Speed Sensor/Clutch Coil Connector
Rear View for Connector
Pin
A
B
C
D
E
F
GFunction
Position 4
Motor (Counter-Clockwise)
Position 3
Position 2
Position 1
Position Retum
Motor (Clockwise)Pin
H
I
J
K
L
M
NFunction
Clutch Coil (EMC)
Front Speed Return
Front Speed
Front Speed Sensor Supply
Rear Speed Sensor Supply
Rear Speed
Rear Speed Return Rear View for Connector
Page 1221 of 1463
5D2-14 TRANSFER CASE (TOD)
Motor HI-LO(clockwise)
Motor LO-HI(counterclockwise)
PIN 13
CONTROL UNIT DIAGRAM
TOD CONTROL UNIT
14
Page 1222 of 1463
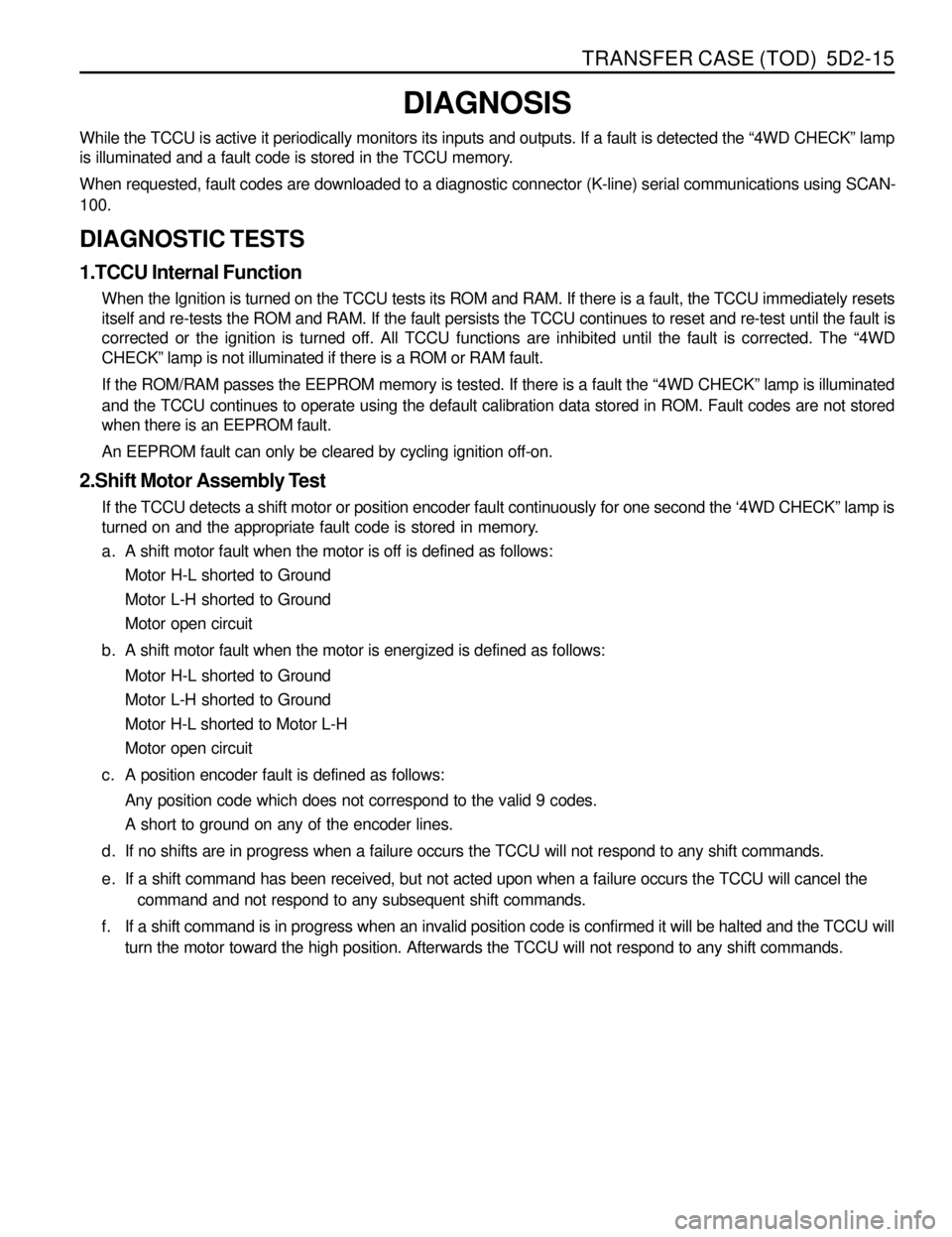
TRANSFER CASE (TOD) 5D2-15
DIAGNOSIS
While the TCCU is active it periodically monitors its inputs and outputs. If a fault is detected the “4WD CHECK” lamp
is illuminated and a fault code is stored in the TCCU memory.
When requested, fault codes are downloaded to a diagnostic connector (K-line) serial communications using SCAN-
100.
DIAGNOSTIC TESTS
1.TCCU Internal Function
When the Ignition is turned on the TCCU tests its ROM and RAM. If there is a fault, the TCCU immediately resets
itself and re-tests the ROM and RAM. If the fault persists the TCCU continues to reset and re-test until the fault is
corrected or the ignition is turned off. All TCCU functions are inhibited until the fault is corrected. The “4WD
CHECK” lamp is not illuminated if there is a ROM or RAM fault.
If the ROM/RAM passes the EEPROM memory is tested. If there is a fault the “4WD CHECK” lamp is illuminated
and the TCCU continues to operate using the default calibration data stored in ROM. Fault codes are not stored
when there is an EEPROM fault.
An EEPROM fault can only be cleared by cycling ignition off-on.
2.Shift Motor Assembly Test
If the TCCU detects a shift motor or position encoder fault continuously for one second the ‘4WD CHECK” lamp is
turned on and the appropriate fault code is stored in memory.
a. A shift motor fault when the motor is off is defined as follows:
Motor H-L shorted to Ground
Motor L-H shorted to Ground
Motor open circuit
b. A shift motor fault when the motor is energized is defined as follows:
Motor H-L shorted to Ground
Motor L-H shorted to Ground
Motor H-L shorted to Motor L-H
Motor open circuit
c. A position encoder fault is defined as follows:
Any position code which does not correspond to the valid 9 codes.
A short to ground on any of the encoder lines.
d. If no shifts are in progress when a failure occurs the TCCU will not respond to any shift commands.
e. If a shift command has been received, but not acted upon when a failure occurs the TCCU will cancel the
command and not respond to any subsequent shift commands.
f. If a shift command is in progress when an invalid position code is confirmed it will be halted and the TCCU will
turn the motor toward the high position. Afterwards the TCCU will not respond to any shift commands.
Page 1223 of 1463
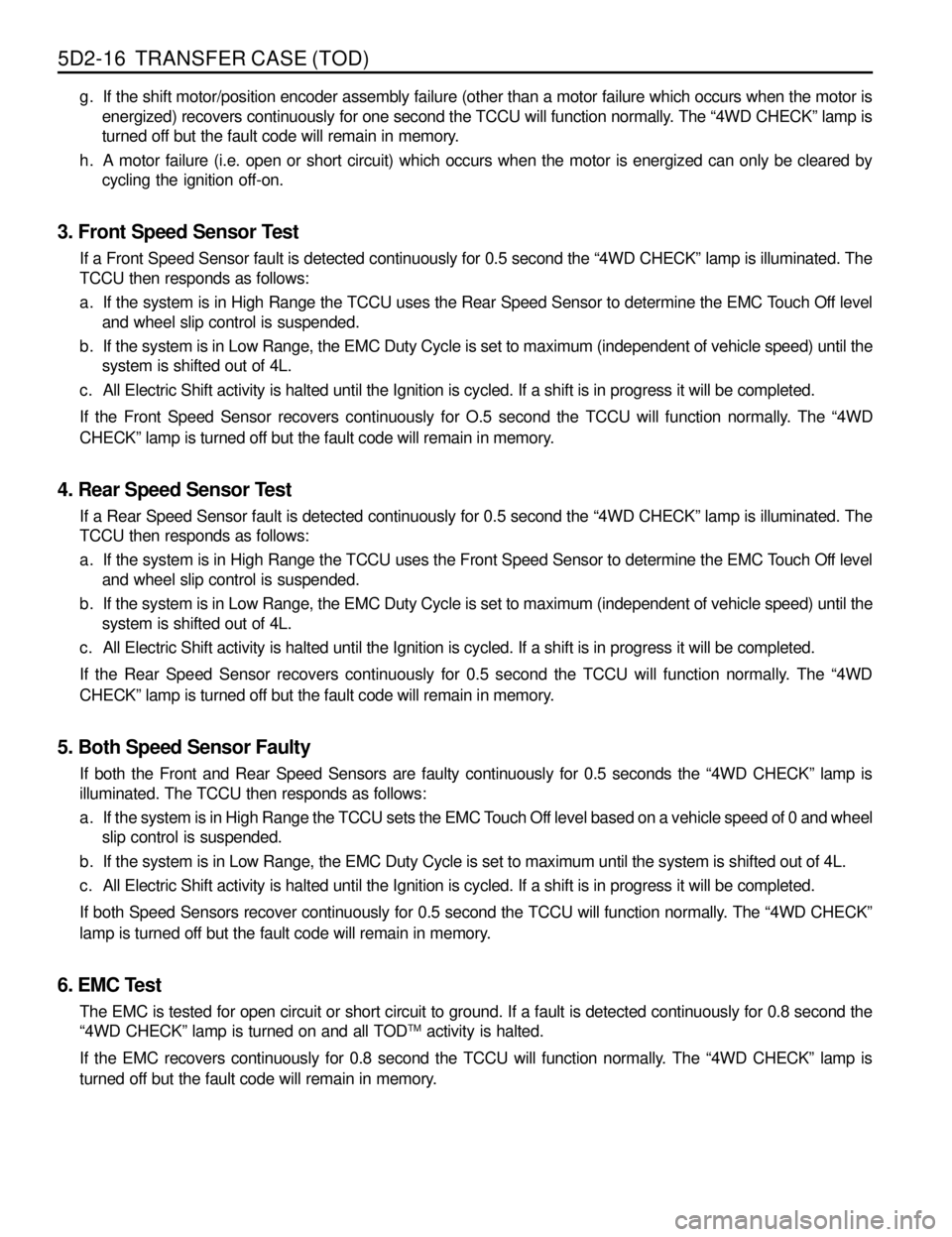
5D2-16 TRANSFER CASE (TOD)
g. If the shift motor/position encoder assembly failure (other than a motor failure which occurs when the motor is
energized) recovers continuously for one second the TCCU will function normally. The “4WD CHECK” lamp is
turned off but the fault code will remain in memory.
h. A motor failure (i.e. open or short circuit) which occurs when the motor is energized can only be cleared by
cycling the ignition off-on.
3. Front Speed Sensor Test
If a Front Speed Sensor fault is detected continuously for 0.5 second the “4WD CHECK” lamp is illuminated. The
TCCU then responds as follows:
a. If the system is in High Range the TCCU uses the Rear Speed Sensor to determine the EMC Touch Off level
and wheel slip control is suspended.
b. If the system is in Low Range, the EMC Duty Cycle is set to maximum (independent of vehicle speed) until the
system is shifted out of 4L.
c. All Electric Shift activity is halted until the Ignition is cycled. If a shift is in progress it will be completed.
If the Front Speed Sensor recovers continuously for O.5 second the TCCU will function normally. The “4WD
CHECK” lamp is turned off but the fault code will remain in memory.
4. Rear Speed Sensor Test
If a Rear Speed Sensor fault is detected continuously for 0.5 second the “4WD CHECK” lamp is illuminated. The
TCCU then responds as follows:
a. If the system is in High Range the TCCU uses the Front Speed Sensor to determine the EMC Touch Off level
and wheel slip control is suspended.
b. If the system is in Low Range, the EMC Duty Cycle is set to maximum (independent of vehicle speed) until the
system is shifted out of 4L.
c. All Electric Shift activity is halted until the Ignition is cycled. If a shift is in progress it will be completed.
If the Rear Speed Sensor recovers continuously for 0.5 second the TCCU will function normally. The “4WD
CHECK” lamp is turned off but the fault code will remain in memory.
5. Both Speed Sensor Faulty
If both the Front and Rear Speed Sensors are faulty continuously for 0.5 seconds the “4WD CHECK” lamp is
illuminated. The TCCU then responds as follows:
a. If the system is in High Range the TCCU sets the EMC Touch Off level based on a vehicle speed of 0 and wheel
slip control is suspended.
b. If the system is in Low Range, the EMC Duty Cycle is set to maximum until the system is shifted out of 4L.
c. All Electric Shift activity is halted until the Ignition is cycled. If a shift is in progress it will be completed.
If both Speed Sensors recover continuously for 0.5 second the TCCU will function normally. The “4WD CHECK”
lamp is turned off but the fault code will remain in memory.
6. EMC Test
The EMC is tested for open circuit or short circuit to ground. If a fault is detected continuously for 0.8 second the
“4WD CHECK” lamp is turned on and all TODTM activity is halted.
If the EMC recovers continuously for 0.8 second the TCCU will function normally. The “4WD CHECK” lamp is
turned off but the fault code will remain in memory.
Page 1224 of 1463
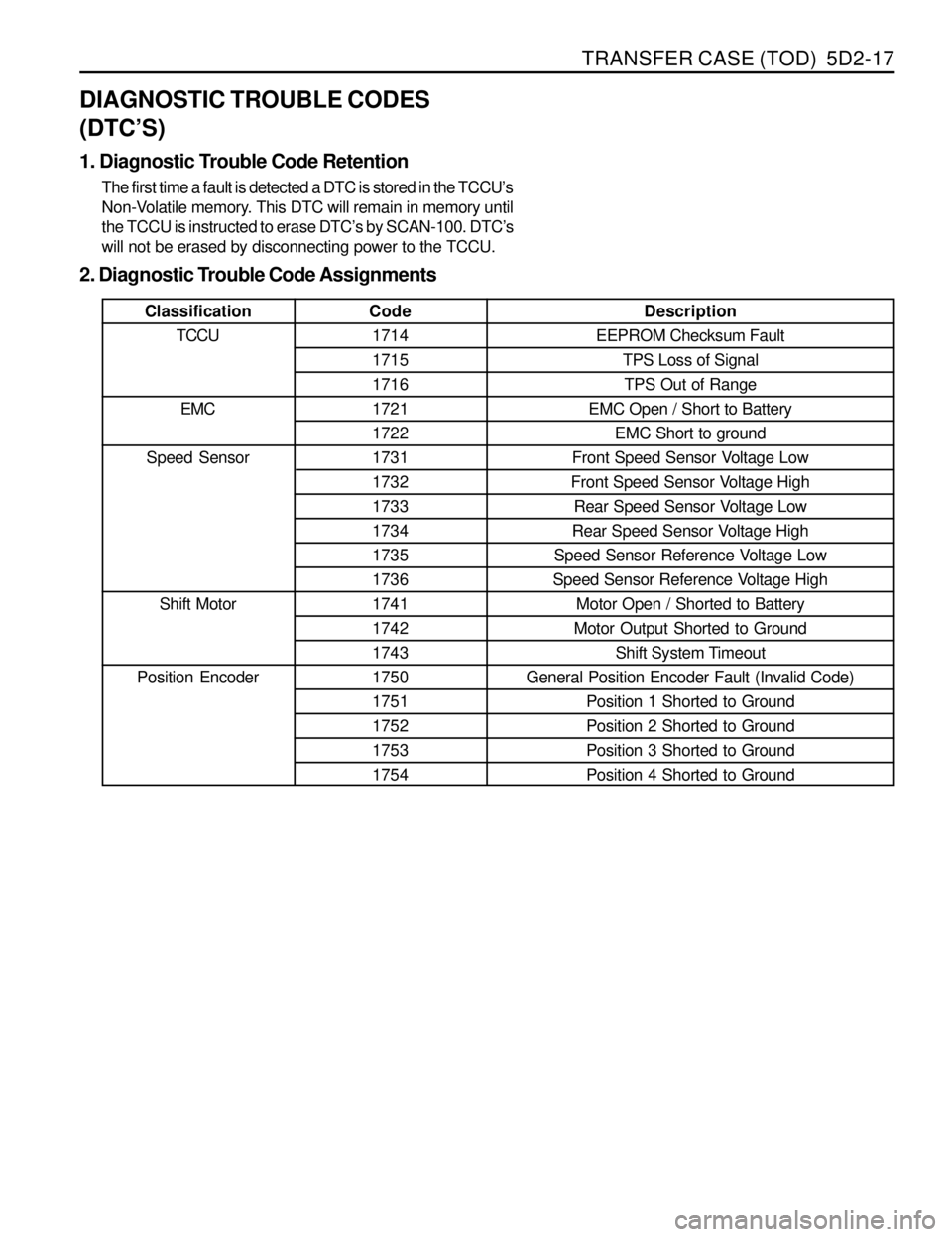
TRANSFER CASE (TOD) 5D2-17
Classification
TCCU
EMC
Speed Sensor
Shift Motor
Position Encoder
DIAGNOSTIC TROUBLE CODES
(DTC’S)
1. Diagnostic Trouble Code Retention
The first time a fault is detected a DTC is stored in the TCCU’s
Non-Volatile memory. This DTC will remain in memory until
the TCCU is instructed to erase DTC’s by SCAN-100. DTC’s
will not be erased by disconnecting power to the TCCU.
2. Diagnostic Trouble Code Assignments
Code
1714
1715
1716
1721
1722
1731
1732
1733
1734
1735
1736
1741
1742
1743
1750
1751
1752
1753
1754Description
EEPROM Checksum Fault
TPS Loss of Signal
TPS Out of Range
EMC Open / Short to Battery
EMC Short to ground
Front Speed Sensor Voltage Low
Front Speed Sensor Voltage High
Rear Speed Sensor Voltage Low
Rear Speed Sensor Voltage High
Speed Sensor Reference Voltage Low
Speed Sensor Reference Voltage High
Motor Open / Shorted to Battery
Motor Output Shorted to Ground
Shift System Timeout
General Position Encoder Fault (Invalid Code)
Position 1 Shorted to Ground
Position 2 Shorted to Ground
Position 3 Shorted to Ground
Position 4 Shorted to Ground