Page 425 of 1463
OM600 ENGINE MECHANICAL 1B3-123
Cylinder Head Clamping Device
Valve Seat Turning Tool
Ring Seat Turning Tool
Pneumatic Removal / Installation Device
(Drift : 8mm, 9mm, 14mm)
Tensioning Head
Cutting Tool for Recessing Grooves
Test Set for Valves
Internal Dial Gauge (Range : 25 - 60mm)
External Micrometer (Range : 25 - 60mm)
Electrically Heated Water Tank
Commercial Tools
Hunger
D-8000 München 70
Type Ventilknecht K2000
Order No. 221 00 100
Hunger
D-8000 München 70
Type VDS 1A
Order No. 236 03 308
Hunger
D-8000 München 70
Type RDS 1
Order No. 219 00 100
Hunger
D-8000 München 70
Type PVM 1
Hunger
D-8000 München 70
Order No. 250 15 250
Hunger
D-8000 München 70
Order No. 217 93 601
Hunger
D-8000 München 70
Order No. 216 69 210
Mahr
D-7300 Esslingen
Order No. 844
Mahr
D-7300 Esslingen
Order No. 40 S
Otto Dürr
D-7123 Sachsenherm - Ochsenbach
Page 426 of 1463
1B3-124 OM600 ENGINE MECHANICAL
1. Measure dimension ‘A’.
Removal Procedure
Limit142.5mm
2. Clamp the cylinder head with clamping device.
3. Cut groove into the valve seat ring so that dimension ‘C’ is
approx. 2mm and dimension ‘E’ is approx. 6mm.
4. Remove the cylinder head from the clamping device and
place it onto wooden blocks.
5. Remove the valve guide (3).
Drift (Intake) 8mm
Drift (Exhaust) 9mm
6. Insert the tensioning head (4) and extracted wedges(arrow)
by turning the bolt (5).
Notice
Carefully tighten the bolt (5) otherwise the valve seat ring in
the cylinder head will be excessively tensioned.
7. Lock the bolt (5) with nut (6).
Page 427 of 1463
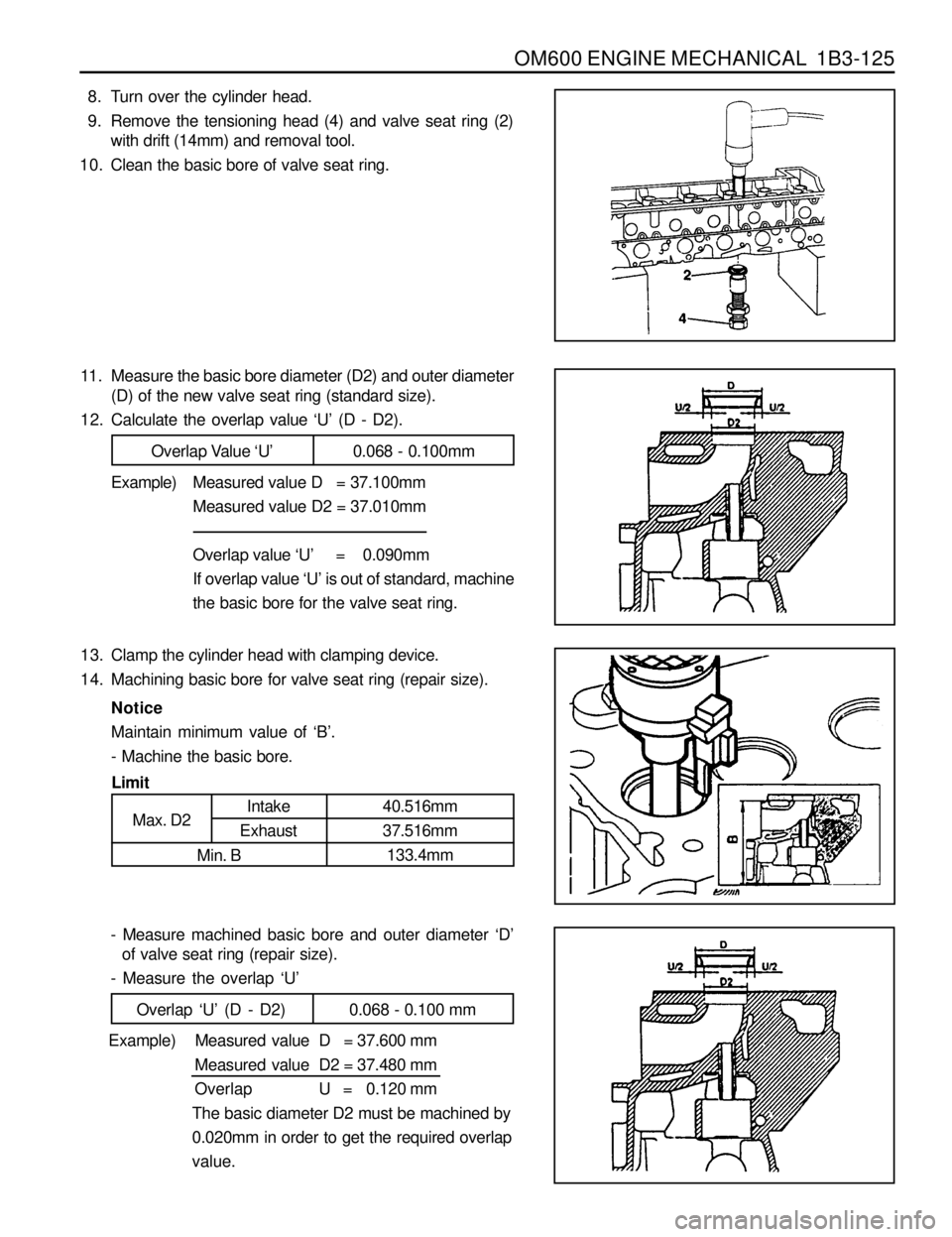
OM600 ENGINE MECHANICAL 1B3-125
8. Turn over the cylinder head.
9. Remove the tensioning head (4) and valve seat ring (2)
with drift (14mm) and removal tool.
10. Clean the basic bore of valve seat ring.
11. Measure the basic bore diameter (D2) and outer diameter
(D) of the new valve seat ring (standard size).
12. Calculate the overlap value ‘U’ (D - D2).
Overlap Value ‘U’ 0.068 - 0.100mm
Example)Measured value D = 37.100mm
Measured value D2 = 37.010mm
Overlap value ‘U’ = 0.090mm
If overlap value ‘U’ is out of standard, machine
the basic bore for the valve seat ring.
13. Clamp the cylinder head with clamping device.
14. Machining basic bore for valve seat ring (repair size).
Notice
Maintain minimum value of ‘B’.
- Machine the basic bore.
Limit
Intake
Exhaust
Max. D2
Min. B40.516mm
37.516mm
133.4mm
- Measure machined basic bore and outer diameter ‘D’
of valve seat ring (repair size).
- Measure the overlap ‘U’
Overlap ‘U’ (D - D2) 0.068 - 0.100 mm
Example) Measured value D = 37.600 mm
Measured value D2 = 37.480 mm
Overlap U = 0.120 mm
The basic diameter D2 must be machined by
0.020mm in order to get the required overlap
value.
Page 428 of 1463
1B3-126 OM600 ENGINE MECHANICAL
17. Drive in new valve seat ring (2) with a proper wooden drift.
18. Install the valve guide (3) with a proper drift and assembling
tool.
Notice
The valve guide must be driven in from the cylinder head
cover.
Drift (Intake) 8mm
Drift (Exhaust) 9mm
19. Machine the valve seats.
15. Hang the cylinder head (1) to the lifting device and heat in
a water tank to approx. 80°C.
16. Cool down new valve seat ring (2) into the cooling box with
liquid nitrogen.
Notice
Do not touch the cooled valve seat rings with hand.
Super Cooling Box 345 589 00 63 00
Page 429 of 1463
OM600 ENGINE MECHANICAL 1B3-127
CHECK AND MACHINING OF VALVES
Preceding Works : Removal of cylinder head
Removal of the vale spring
Removal of the valve
I Valve Length
W Camshaft Cam Basic Diameter
X Distance (Camshaft Basic Bore - Valve Stem)Y Half Camshaft Basic Bore Diameter
Z Distance (Cylinder Head Cover Parting Surface -
Valve Stem)
Page 430 of 1463
1B3-128 OM600 ENGINE MECHANICAL
Intake Valve Exhaust Valve
Item
Valve Disc Diameter ‘d’
Valve Disc Height ‘h’
Setting Angle “a” or Machining the Valve
Valve Stem Diameter ‘d1’
Valve Length ‘I’Intake Valve
37.90 - 38.10 mm
1.7 mm
45°
7.955 - 7.970 mm
106.20 - 106.60 mm
105.30 - 105.70
0.03 mmExhaust Valve
34.90 - 35.10 mm
1.7 mm
45°
9.945 - 8.960 mm
106.20 - 106.60 mm
105.30 - 105.70 mm
0.03 mm
Standard
Repair
Max. Permis Sible Runout at Valve Stem and Valve Seat
W = 38.0 ± 0.2mm
Matching Valves
Camshaft Cam Basic Dia.
Size (x)
Size (x)
Size (x)19.5 - 20.3mm
20.4 - 21.4mm
21.4 - 21.97mmW = 36.6 ± 0.2mm Camshaft Cam Basic Dia.
19.5 - 20.1mm
20.2 - 21.2mm
21.2 - 21.97mmValve to be Used
Use machined valve,
if needed
new repair valve
I = 105.5 ± 0.2mm
Reuse valve
Use standard size
valve
I = 106.4 ± 0.2mm
Page 431 of 1463
OM600 ENGINE MECHANICAL 1B3-129
Tools Required
001 589 32 21 00 Dial Gauge
Checking and Machining
1. Clean the valves and do visual check.
Valves with wobbled valve disc, with worn or scored valve
stem should be replaced.
2. Measure valve disc height ‘h’.
Service data
Intake
Exhaust1.7 ± 0.15 mm
1.7 ± 0.15 mm
3. Machine the valve.
Notice
Pay attention to setting angle ‘a’.
Commercial Tool
Valve corn grinding machine
4. Measure radial runout between valve stem and valve seat.
Limit Max. 0.03mm
Dial Gauge 001 589 32 21 00
Page 432 of 1463
1B3-130 OM600 ENGINE MECHANICAL
10. Measure distance ‘z’ (cylinder head cover parting surface
- valve stem). 5. Clean the vales, valve seats and valve guides.
6. Coat the valve stem with oil and insert it into valve guide.
7. Insert the valves (1) into the valve guides according to
marking.
8. Measure amount by which the valve arrears ‘a’.
Arrears ‘a’ 0.1 - 0.7 mm
Notice
If out of standard, replace the valve seat ring.
9. Measure camshaft cam basic diameter (w).
Diameter ‘w’38 ± 0.2 mm
or 37.6 ± 0.2 mm